Fertilizer International 494 Jan-Feb 2020
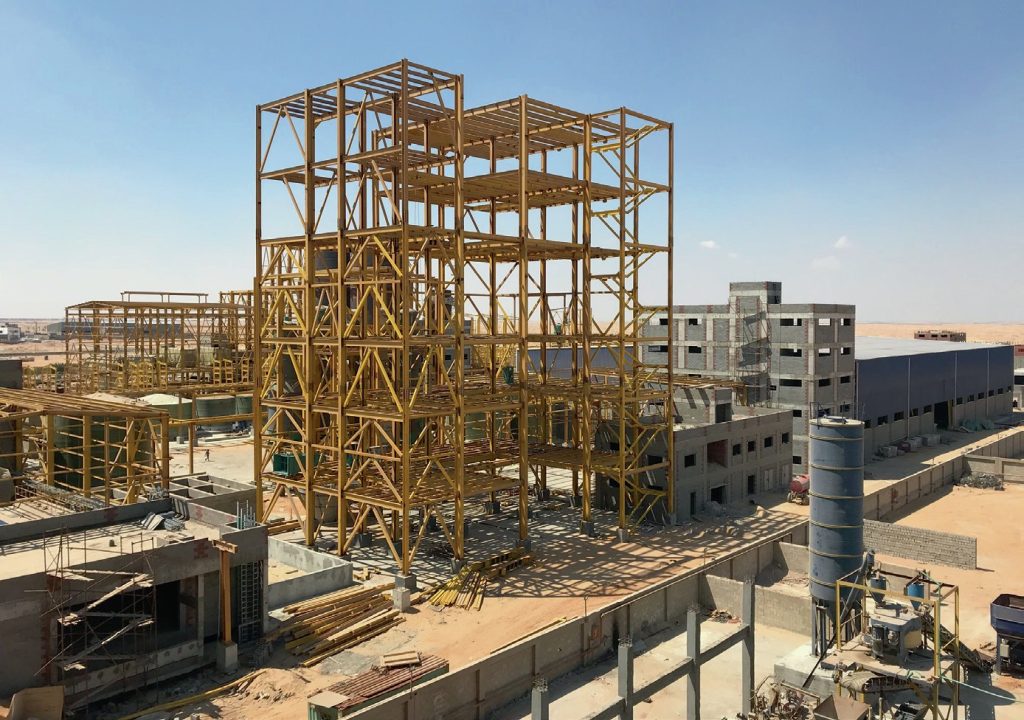
31 January 2020
EcoPhos ChemBe plant for Evergrow in Egypt
PHOS ACID PROCESS INNOVATION
EcoPhos ChemBe plant for Evergrow in Egypt
ChemBe process from EcoPhos merges beneficiation with chemical processing to generate high-quality phosphoric acid and dicalcium phosphate products. Mohamed Takhim, the CEO and founder of EcoPhos, describes how the ChemBe process is being implemented at the Evergrow project in Egypt.
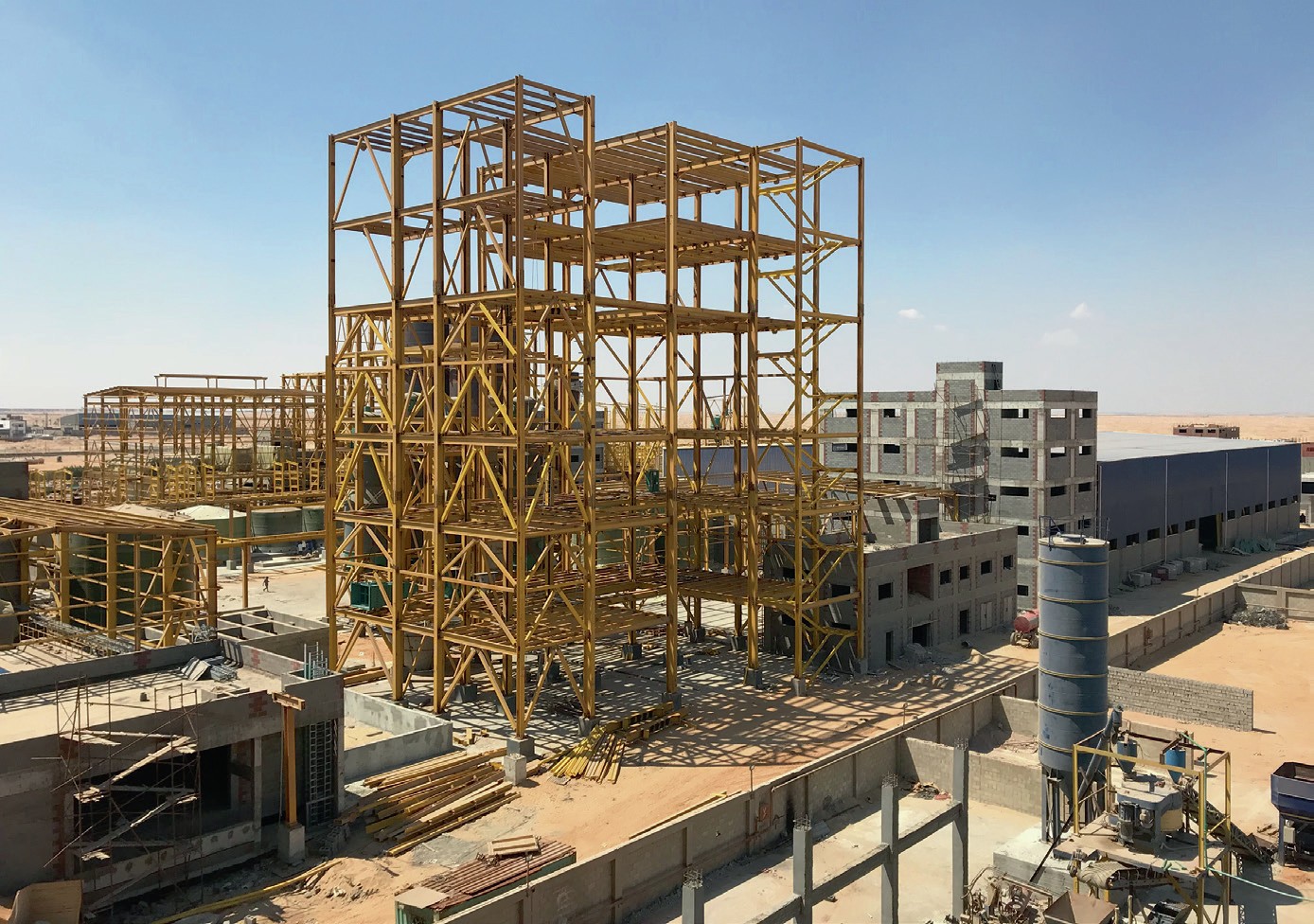
Conventional phosphate production
The production of phosphates is traditionally based on two distinct and separate processes: beneficiation and chemical processing.
Beneficiation aims to remove deleterious components from the phosphate rock raw material – sand, organic matter, magnesium salts etc. – to ensure it is suitable for chemical processing This is generally achieved by grinding, washing, de-sliming, sizing and froth flotation. Calcination is also used occasionally.
This complex beneficiation process consumes large amounts of energy and water and generates substantial volumes of waste and contaminated effluent. The efficiency of beneficiation is also low, typically because of large phosphate losses in waste materials such as pebbles, clay, oversize and tailings. Beneficiation is also becoming increasingly challenging due to the depletion of phosphate resources and the decline in the quality of phosphate rock ore.
After beneficiation, upgraded rock concentrates are transported to the chemical plant where they are reacted with sulphuric acid to produce dilute phosphoric acid. This is then concentrated and purified to obtain merchant grade acid (MGA). The quality of MGA obtained is directly linked to the composition of the phosphate rock used and can still contain heavy metals and other harmful impurities.
This wet phosphoric acid process also generates large quantities of gypsum. This phosphogypsum waste – which may be contaminated with heavy metals and radioactive elements – needs to be stored in stockpiles (stacks) or discharged to the sea. Phosphogypsum, whatever the disposal route, creates a costly environmental problem that needs to be managed.
The EcoPhos ChemBe process
The Belgian company EcoPhos was founded by Mohamed Takhim in 1996 with the specific aim of developing solutions to the economic and environmental challenges faced by the phosphate industry. The ChemBe process is one of the solutions successfully developed by EcoPhos. This innovative technology merges beneficiation with chemistry to create an optimised chemical beneficiation process.
In a ChemBe plant, the raw phosphate ore is gently digested in dilute hydrochloric acid solution. This ‘soft’ process selectively dissolves the soluble phosphate from the unwanted insoluble part of the ore. This insoluble fraction, which remains as a solid residue under the mildly acidic conditions, is washed and then disposed of or recycled.
The next step in the process is to precipitate the soluble phosphate obtained from acid digestion. This is achieved by adding calcium carbonate (or another source of calcium) to the soluble phosphate solution. This precipitates dicalcium phosphate (DCP) crystals and leaves a calcium chloride solution. The crystallised DCP created is then separated from the calcium chloride mother solution by filtration.
The leftover calcium chloride solution is fully recycled in the process by reacting with sulphuric acid. This results in the formation of hydrochloric acid and a gypsum by product. The gypsum obtained is highly pure as impurities from the phosphate rock were removed in the preceding digestion stage.
The DCP product generated by the ChemBe process is an ideal starting material for a wide range of other phosphate products, including:
- Single superphosphate (SSP)
- Triple superphosphate (TSP)
- NPKs
- All grades of phosphoric acid
- Feed-grade DCP and monocalcium phosphate (MCP) etc.
Indeed, the DCP obtained from the ChemBe production route contains much higher phosphate levels than beneficiated ore – typically 40-48 percent P2 O5 vs 30-39 percent for high-grade rock concentrates. The DCP end-product is also free of carbonate (CO2 ) and sand, contains less calcium, and has a low heavy metal content. The yield of the ChemBe process (typically 80-95 percent) is also much higher than standard beneficiation technologies (which typically range from 25 percent to 80 percent maximum depending on rock quality).
These significant yield and quality advantages means the ChemBe process can make new projects much more economically feasible. Because the process can happily consume much lower quality ore, it can also increase the operational life of a phosphate rock mine by a factor of up to four! Finally, because water is recycled, water consumption in the ChemBe process is much lower in comparison to traditional beneficiation.
In summary, the EcoPhos ChemBe process, by combining together chemistry with beneficiation, offers a practical, economic solution that overcomes a number of issues encountered when using conventional phosphate production technologies. It key advantages include:
- The efficient and highly flexible processing of phosphate ore
- Rock reserves are increased
- More mining projects are made economically feasible
- Process effluents are drastically reduced
- Higher quality products and co-products are obtained
- Less energy and water are consumed.
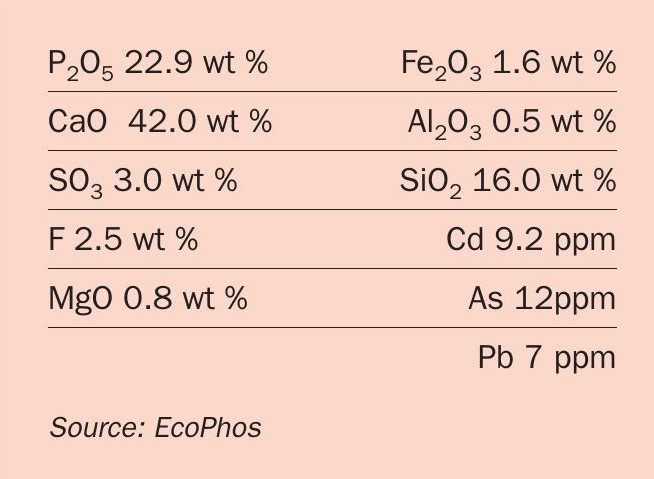
The Evergrow project, Egypt
Evergrow is a pioneering Egyptian company that produces speciality fertilizers to meet increasing demand from local and regional agriculture. Evergrow is positioning itself as the future leader in the fertilizer market in Egypt and the Middle East by optimising the value of locally-available resources.
As the company has grown, Evergrow has maintained a high level of operational excellence in fertilizer manufacturing – by investing in innovation and regularly upgrading its plants. This approach to business enables Evergrow to supply its customers with effective, reliable and safe products that meets international quality standards.
Evergrow was founded in 2006 with the opening of a production site in the Abo Rawash industrial zone of Egypt’s 6th October City. This is located in Giza Governorate around 32 kilometres from the capital Cairo. Evergow was the first Egyptian company to specialise in the production of water-soluble fertilizers such as potassium sulphate (SOP), monoammonium phosphate (MAP), granular and liquid urea phosphate (UP), solid and liquid NPKs and calcium ammonium nitrate (CAN).
In 2011, to meet increasing demand for its products, Evergrow established two new large-scale production complexes for phosphoric, nitric and sulphuric acid on an 180,000 m² site in the Sadat industrial zone. The site, ideally located in Sadat City, Monufia Governorate, between Alexandria and Cairo, is close to the Egyptian water-soluble fertilizer market.
The new acid production facilities will enable Evergrow to increase SOP capacity and produce CaCl2 for non-agricultural uses. Due to these manufacturing investments, Evergrow’s annual production capacity rose from 885,000 tonnes in 2016 to more than one million tonnes in 2017.
EcoPhos implemented a project for Evergrow at the Sadat industrial zone to consume waste hydrochloric acid (HCl) from the new complex. As well as being the best solution for HCl waste, the ChemBe process was selected by Ever-grow because it was capable of generating high profits from phosphates and phosphoric acid production.
The industrial process developed by Ecophos for Evergrow (Figure 1) converts phosphate rock into dicalcium phosphate (DCP) and calcium chloride (CaCl2 ). Hydrochloride acid (HCl) and calcium carbonate (CaCO3 ) are the other main raw materials.
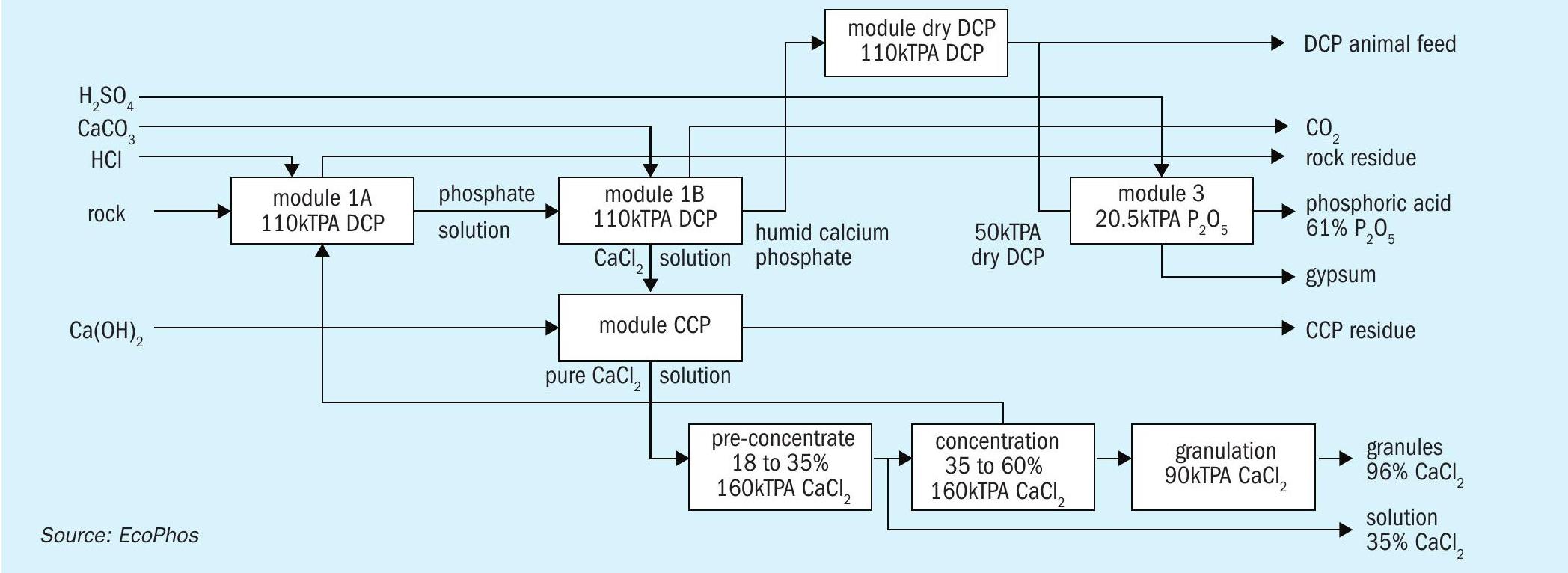
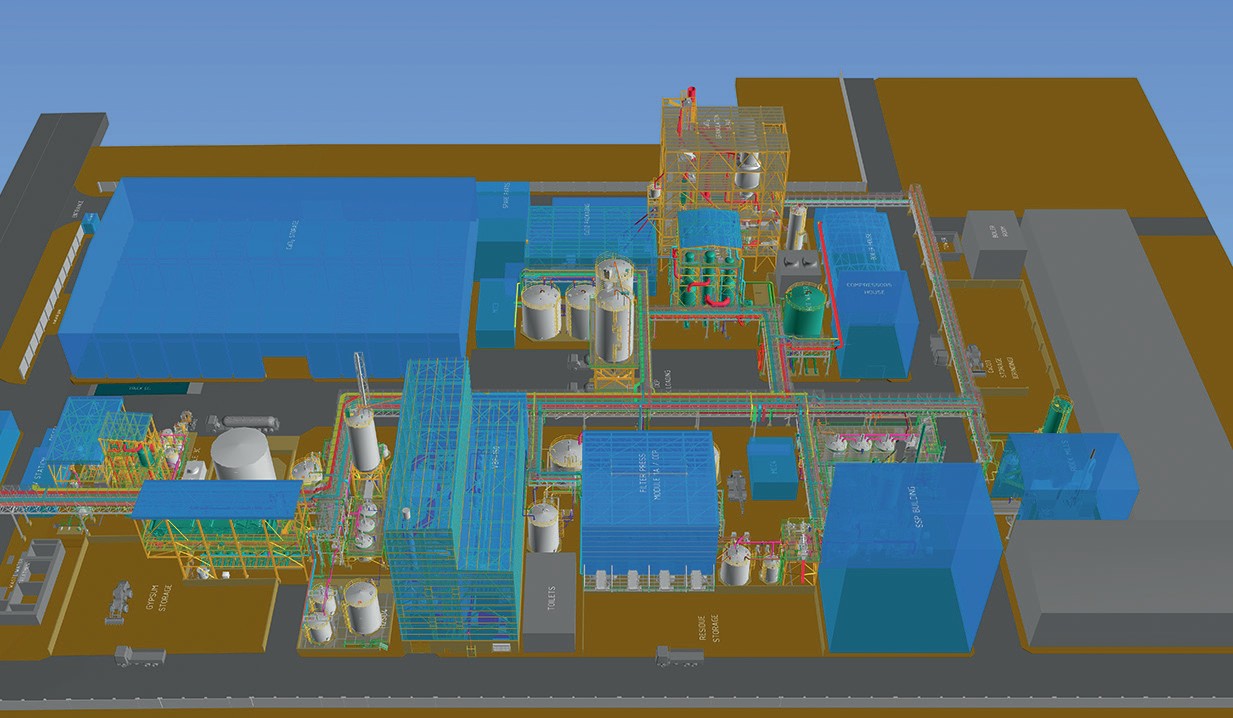
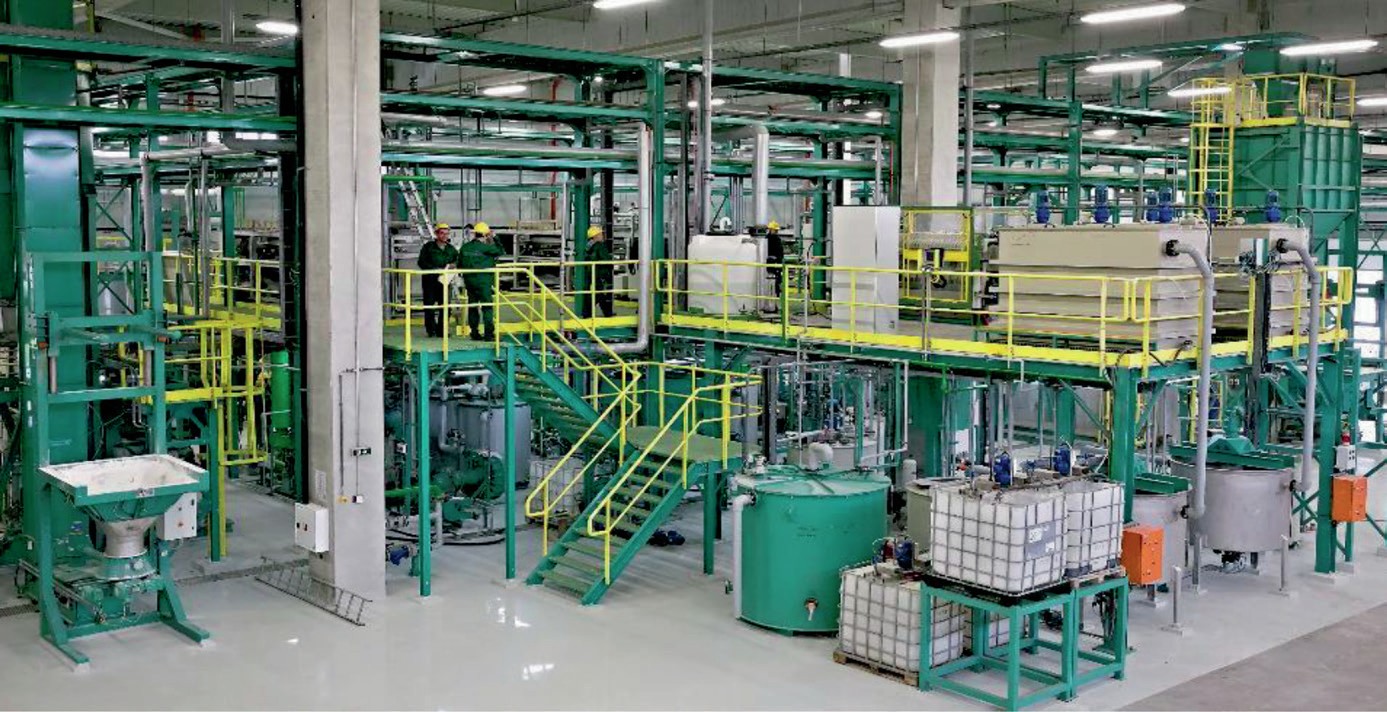
The DCP from the process is firstly dried. A portion of the dry DCP obtained is sold as final product, while the remainder is converted to purified phosphoric acid (H3 PO4 ) and gypsum (CaSO4 .2H2 O) using sulphuric acid (H2 SO4 ). The CaCl2 solution generated is concentrated to 35 percent. This is partly solidified to obtain a 96 percent pure calcium chloride by-product.
Construction of the e80 million Evergrow project began in 2015 with start-up currently scheduled for June 2020. The largescale project has involved:
- 12,000 man-hours of process development and tests
- 72,000 man-hours of engineering
- 12,000 man-hours of project management and procurement.
More than 80 Ecophos staff have worked on the Evergrow project since its inception. They have been involved in all aspect of the project, including laboratory work, detailed engineering, process validation, semi-industrial plant tests, project management and procurement.
Project raw materials
Analysis of the Egyptian phosphate rock raw material revealed a low P2 O5 content and high aluminium, iron and silica contents (Table 1). This composition – although unusable with conventional phosphate production processes – is ideal for Ecophos technology, which is perfectly capable of consuming low-grade phosphate rock.
The ChemBe process also consumes HCl, an unwanted by-product of Evergrow’s SOP plant. Calcium carbonate used in the process is sourced locally and ground to increase reactivity. The sulphuric acid (9698%) consumed by the process is also supplied locally.
Semi-industrial scale demonstration tests
The ChemBe process for the Evergrow project was validated by EcoPhos at Technophos, the company’s semi-industrial demonstration plant in Bulgaria (Figure 3). For validation purposes, this plant was operated continuously for 24 hours over a 10-day period.
The process stability of the following three ChemBe modules was validated during the 10-day test run at the Technophos demonstration plant:
- Module 1A: digestion of phosphate rock – first refining step
- Module 1B: crystallization of DCP – the second refining step
- Module 3: Phosphoric acid production using the EcoPhos TacHem process.
The phosphoric acid obtained from Module 3 is suitable for production of water-soluble fertilizers. However, an additional purification process developed by EcoPhos – known as PUMA (purification using membranes of acids) – is necessary to obtain technical- or food-grade phosphoric acid.
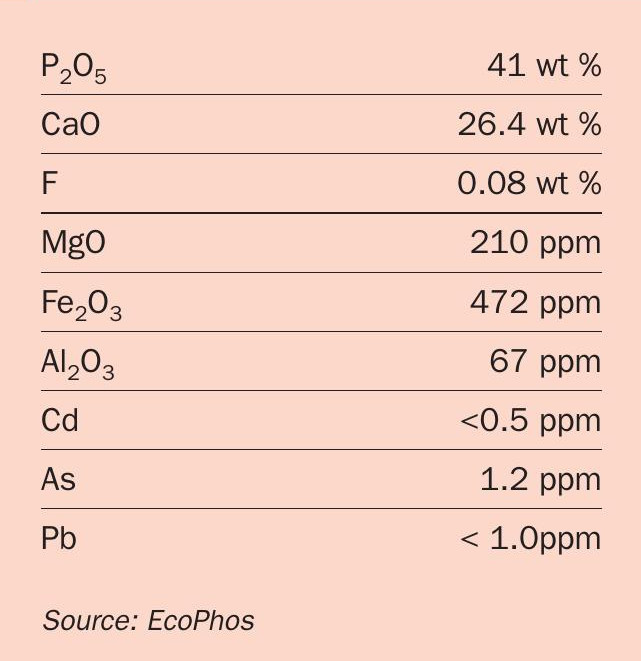
Products and co-products
The ChemBe process generates DCP, phosphoric acid and pure gypsum as products and co-products.
The ChemBe process, as well as delivering a high phosphate yield from low-grade Egyptian rock, generates DCP with a high P2 O5 content (around 41 percent), low calcium content (around 26 percent) and low levels of impurities (Table 2). Analysis of the phosphoric acid obtained from the semi-industrial tests confirmed a high-quality product with low impurity levels (Table 3). Finally, the gypsum by-product generated by the ChemBe process was also found to be extremely pure (99.8 percent, Table 4).
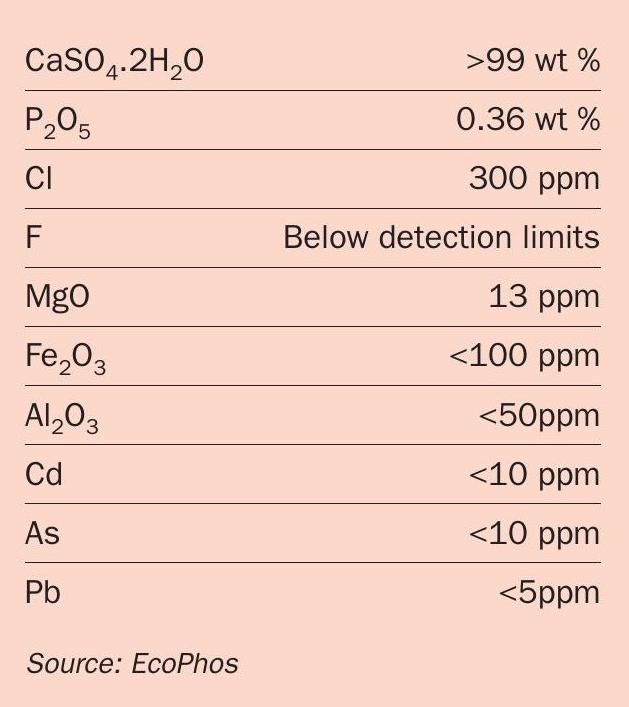
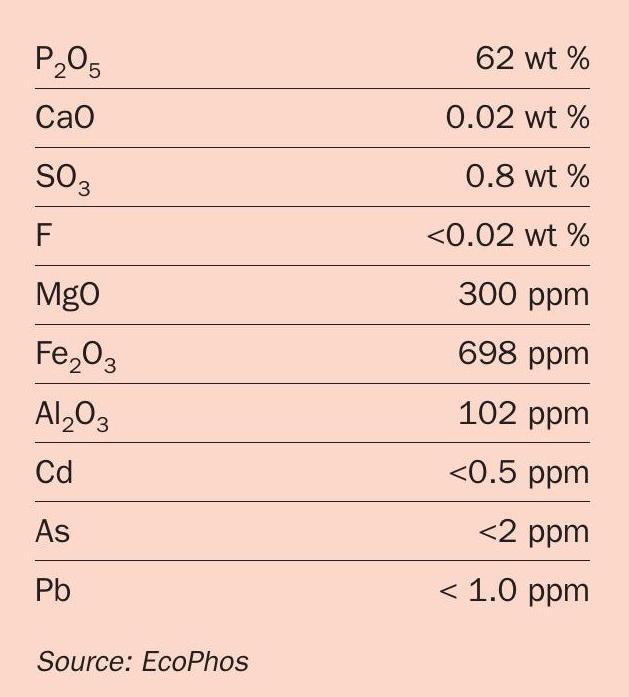
Conclusion
The innovative phosphates technology developed by EcoPhos leads to lower production costs due to its ability to consume low-grade phosphate rock as a raw-materials.
The company’s ChemBe process consumes phosphate rock, as-mined without any additional beneficiation, and successfully converts this to high-quality DCP. This intermediate product is a stepping stone for the production of phosphoric acid and several other phosphate products such as monosodium phosphate (MSP), TSP and NPKs.
EcoPhos is currently building a modern phosphate production plant in Egypt as a project for Evergrow. This plant will use low-grade Egyptian phosphate rock and hydrochloric acid waste generated by Evergrow’s SOP production plant. The Innovative ChemBe process developed by EcoPhos will use these raw materials to produce DCP, phosphoric acid and calcium chloride. The low cost of the rock and HCl raw materials, as well as the valorisation of co-products, will keep plant production costs very low and profit margins high. Last but not least, the ChemBe process guarantees that the Evergrow plant will operate to high ecological and environmental standards – as it avoids the generation of large quantities of phosphogypsum, and also keeps both energy and water consumption to a minimum.
The ChemBe process used in the Evergrow project has been validated by EcoPhos at semi-industrial scale. Demonstration tests carried out at the company’s Technophos site in Bulgaria confirmed the stability of the process and its ability to deliver high-quality products.
The Evergrow project is close to completion with start-up of the ChemBe plant currently scheduled for June 2020.