Fertilizer International 494 Jan-Feb 2020
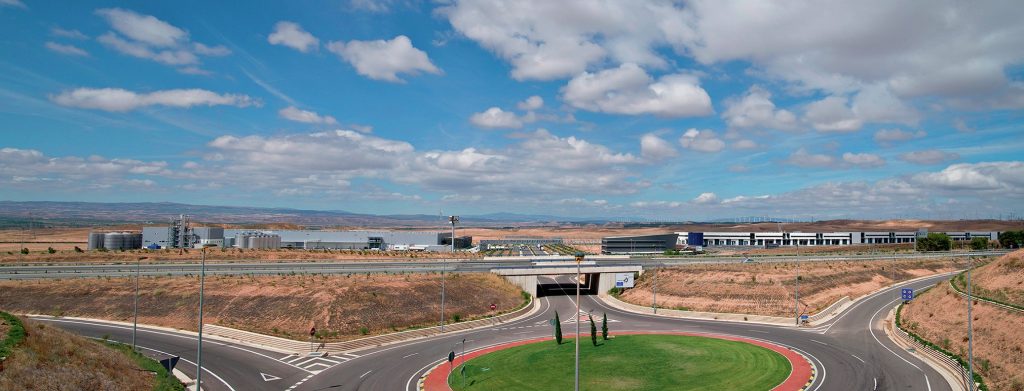
31 January 2020
Fertilizers go circular
GLOBAL STEWARDSHIP
Fertilizers go circular
Antonio Sancho, Incro’s managing director, gives a personal view on the circular economy and shares his experience of manufacturing high-quality liquid fertilizers from food industry wastewater.
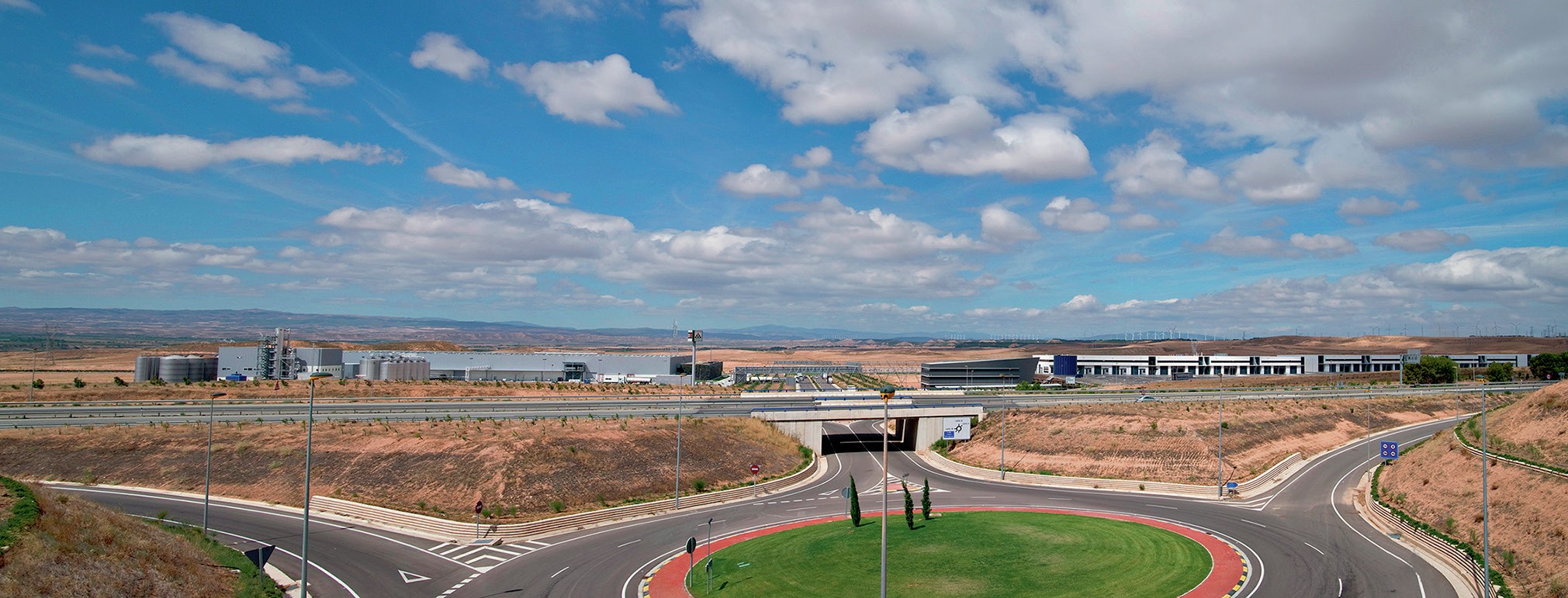
That was then…
Only a decade ago, this article would have been highly theoretical and, lacking a receptive audience, have probably gone largely ignored.
No doubt I would have needed to start with a reminder of basic school biology – the essential role phosphorus plays in all living things. The article would also have explained how phosphorus ends up in a wide range of waste generated by farming, food production and industry.
It would also have been necessary to point out some regrettable facts – that millions of tonnes of phosphorous end up in landfill each year or, even worse, polluting our rivers and ecosystems. Exactly the type of green language that makes many uncomfortable.
Finally, I would turn to my central proposition:
- That, in future, the fertilizer industry should recover nutrients as highly valuable products
- And, by doing so, would improve our environment, increase the contribution our sector makes to the economy, and empower fertilizer production from local sources.
Of course, that would probably have been the exact moment when many readers would have skipped to the next article. The only readers left – possibly one in a hundred – would be those interested in looking at a few laboratory test results!
This is now
Fortunately, those days are long gone. Nowadays, the fertilizer industry’s pursuit of the circular economy has turned from a leftfield idea into a cold, concrete fact. We have been compelled to act due to our sustainability needs as an industry, and by new legislation driving reforms in this direction.
Crucially, the EU finally published its new fertilising products regulation in 2019. This introduces legislation covering fertilizers derived from secondary raw materials for the first time. If you can ignore its jargon and somewhat patronising language, this highly positive regulation opens the gate to producing and placing on the market a whole new generation of safe and effective fertilizers.
Subsequently, the Joint Research Centre (JRC) of the European Commission, an independent science and knowledge service located in Seville, published a proposed legal framework for these new types of waste-derived fertilizer products. This covers precipitated phosphate salts and materials generated by thermal oxidation, pyrolysis and gasification.
The good news is that I am now confident that you – today’s reader – will be much more eager to learn about this subject. That’s because I bring to you, not just a few lab test results, but an actual industrial case instead.
A leadership role
Spanish industrial group Fertiberia has taken a leadership role in turning the circular economy concept of high-quality innovative fertilizers into a reality. In particular, its engineering company, Incro, S.A., has been instrumental in carrying out the flagship Oleofat project. Valuably, this pioneering project has successfully transformed industrial wastewater into a liquid fertilizer (almost 13% P2 O5 , cadmium-free), at the same time generating recycled water for farming and industrial purposes.
The Oleofat company is located in Tudela food-industrial park, Spain. It valorises (obtains value from) vegetable oil by-products and bio-wastes by transforming these into sustainable biodiesel and valuable compounds such as tocopherols, squalene and phytosterols. The by-products utilised include oil tank bottoms, degumming sludge and fatty acid waste from vegetable oil refining (soapstocks).
At Oleofat’s premises, these raw materials are treated with sulphuric acid and then, at a later stage, decanted to separate fatty acids from wastewater. High added-value products, derived from the subsequent processing of fatty acids, are delivered for animal feeding, cosmetics and the emerging ‘nutraceutical’ industry.
Wastewater, the Achilles’ heel
This entrepreneurial success story does, however, have one Achilles’ heel: difficult to dispose of wastewater.
Oleofat’s wastewater is strongly polluted with a low pH, high organic matter content (not biologically treatable) and a large amount of salts, mainly sulphates (Table 1).
Oleofat’s wastewater, because of its phosphate load, used to be sent to a local biogas plant. But after plant corrosion became a problem it was temporarily sent for disposal to the local sewage treatment plant instead.
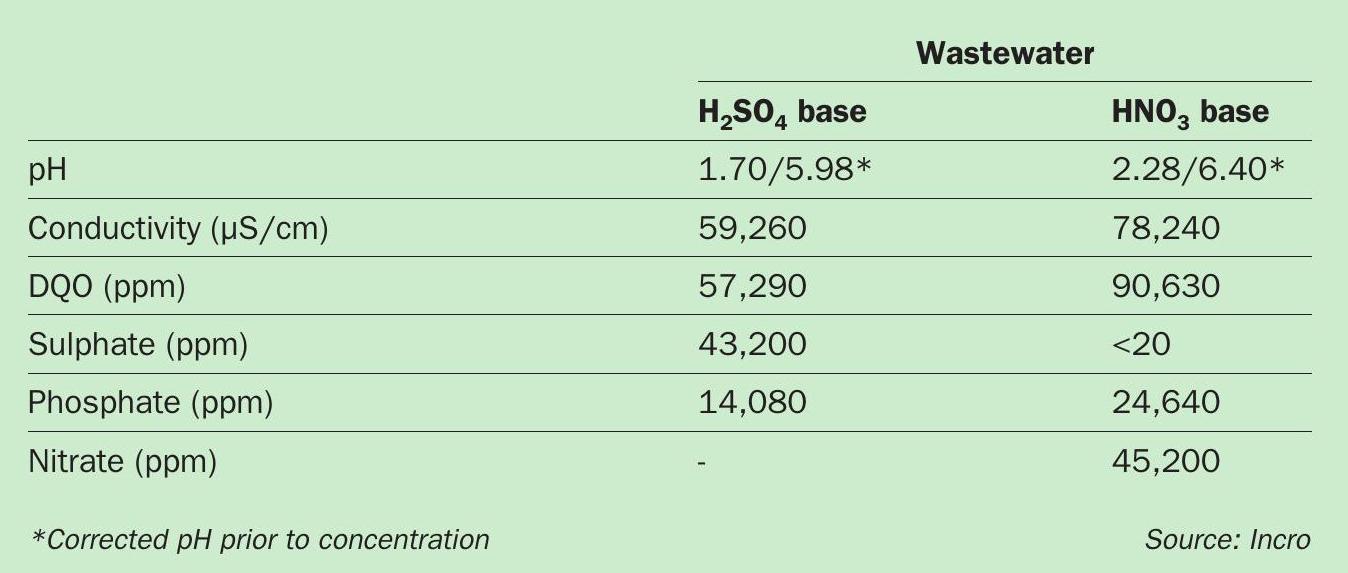
The lack of a long-term wastewater solution threatened Oleofat’s viability as a company. Because of this, Incro was asked to intervene and come up with a suitable wastewater treatment option. Early on we identified a definite opportunity to implement a circular economy approach involving the fertilizer industry.
Incro proposed concentrating wastewater to enrich its P2 O5 content. The liquid concentrate obtained would then be delivered to Fertiberia’s liquid fertilizer plant at Agralia where it would be valorised (transformed into a valuable product).
Furthermore, by switching from sulphuric acid to nitric acid in the Oleofat process, it was possible to improve the quality of the wastewater by replacing sulphates with nitrates. The resulting change in composition generated a liquid fertilizer with even higher added-value. In an additional benefit, the water obtained as a distillate during the concentration process was suitable for reuse elsewhere in the food-industrial park.
From wastewater to liquid fertilizer
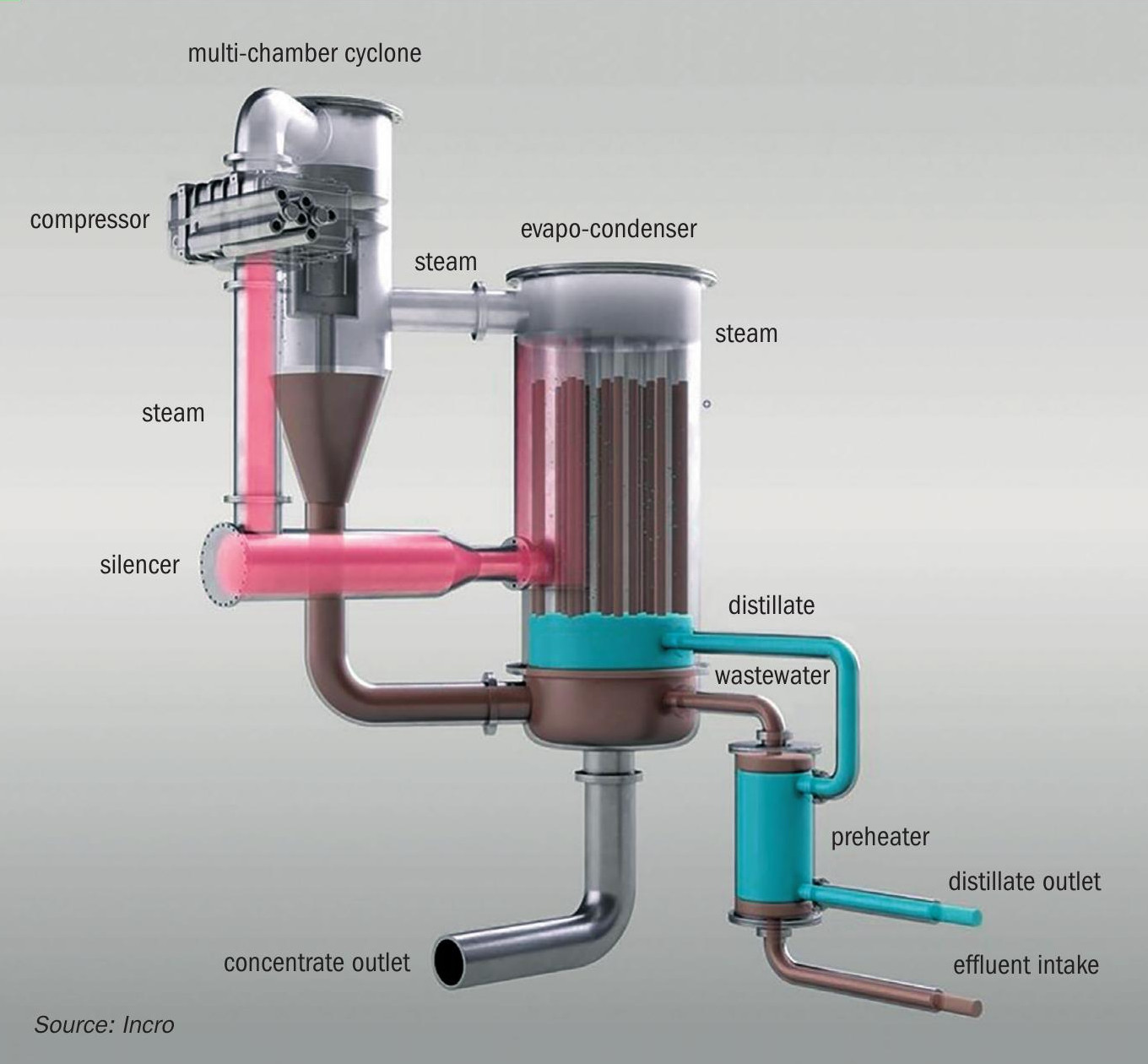
Incro employed its proprietary mechanical vapour compression (MVC) technology to obtain a concentrate and distillate from the wastewater (Figure 1). This unit incorporates a highly efficient and low operating cost evaporator that concentrates the wastewater close to its precipitation point. Its dual-use design allows treatment with either sulphuric or nitric acid, depending on acid market prices and/or the end-destination of the concentrate.
The concentrate obtained is suitable for use as a liquid NPK fertilizer, containing 4.0 percent nitrogen (as nitrate), 12.9 percent phosphorus (P2 O5 ), 0.7 percent potassium (K2 O) and 17.3 percent organic carbon, while also being free of heavy metals and pathogens (Table 2). Its nitrate content is, of course, derived from the nitric acid used to extract the phosphate from the bio-waste. Annually, Incro’s MVC unit has the capacity to handle around 10,000 tonnes of wastewater and produce 3,000 tonnes of liquid fertilizer from this.
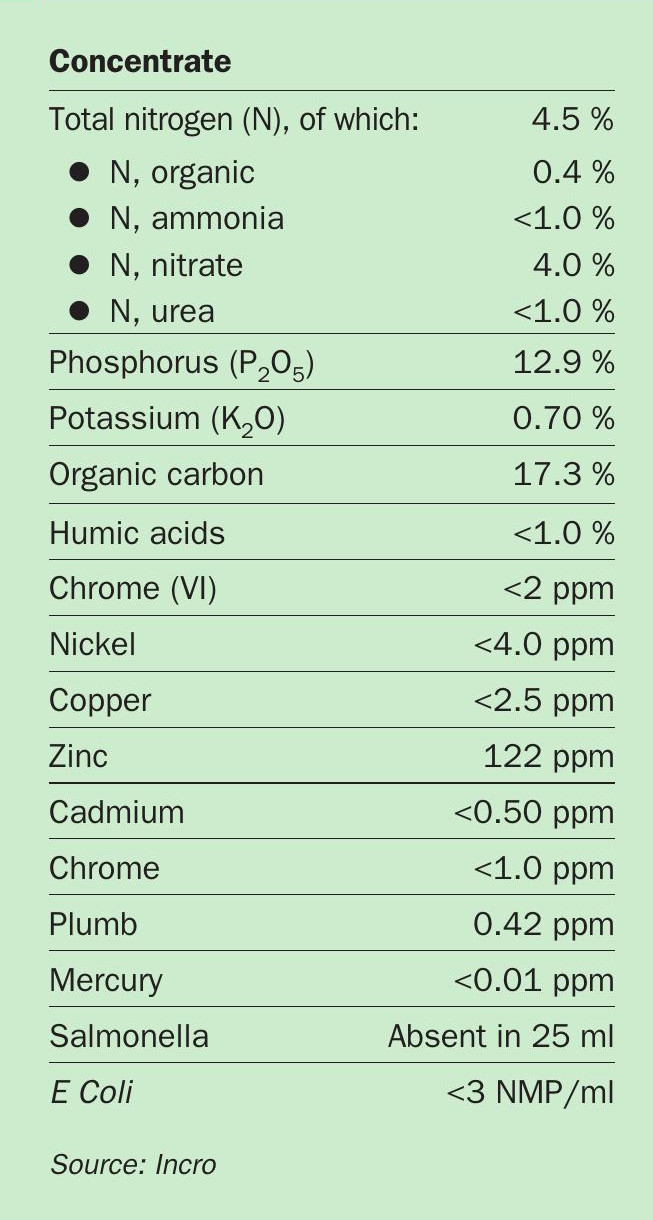
Conclusion
The Incro-Oleofat project shows how secondary raw materials – to use EU jargon – can be transformed into high quality, saleable products. But, above all, it symbolises a real, actual example of phosphate recovery by the fertilizer industry and the circular economy in action.