Nitrogen+Syngas 363 Jan-Feb 2020
31 January 2020
Influence of flame velocity on secondary reformer design
SECONDARY REFORMER DESIGN
Influence of flame velocity on secondary reformer design
The different flame velocities of reactants in the combustion space of a secondary reformer have a significant impact on the gas inlet temperature of the catalyst and the methane conversion in front of the catalyst. Based on this fact, Hanno Tautz Engineering introduces an alternative secondary reformer design. Compared with the state-of-the-art-technology, the alternative design shows advantages for hydrogen production efficiency and product capacity.
Steam reforming and optional secondary reforming or auto thermal reforming in the second stage after the steam reformer is a well-established technology for syngas production for ammonia plants. The mass balance of these catalytic processes is normally close to equilibrium conditions.
The consideration of reaction kinetic effects in the combustion space of the secondary reformer shows that a significant amount of hydrogen from the steam reformer syngas is consumed by oxidation in the first reaction step. In the second step, hydrogen is produced again from the methane reforming reaction mainly in the catalyst space.
The principle influence of this fact on operation conditions, process design options and revamp conditions will be discussed in this article.
Flame velocity
The flame velocity is a characteristic value for the combination of reaction kinetics, diffusivity and heat conduction under experimental conditions. The values for laminar flame velocities of hydrogen, methane and carbon monoxide are shown in Table 1 1 .
The flame velocity of hydrogen in air is at least five times higher than for methane and carbon monoxide. The flame velocity is dependent on pressure, local temperature, gas mixture, air or oxygen atmosphere, turbulence degree and several other factors.
That means, if the distribution from an injection point and the reaction of hydrogen in a reaction space is much faster than for methane and carbon monoxide, the available oxygen will be consumed by hydrogen combustion as long as hydrogen or oxygen is available.
The principle influence of hydrogen combustion in the secondary reformer on gas inlet temperature in the catalyst and the methane conversion in front of the catalyst is shown in Fig. 1.
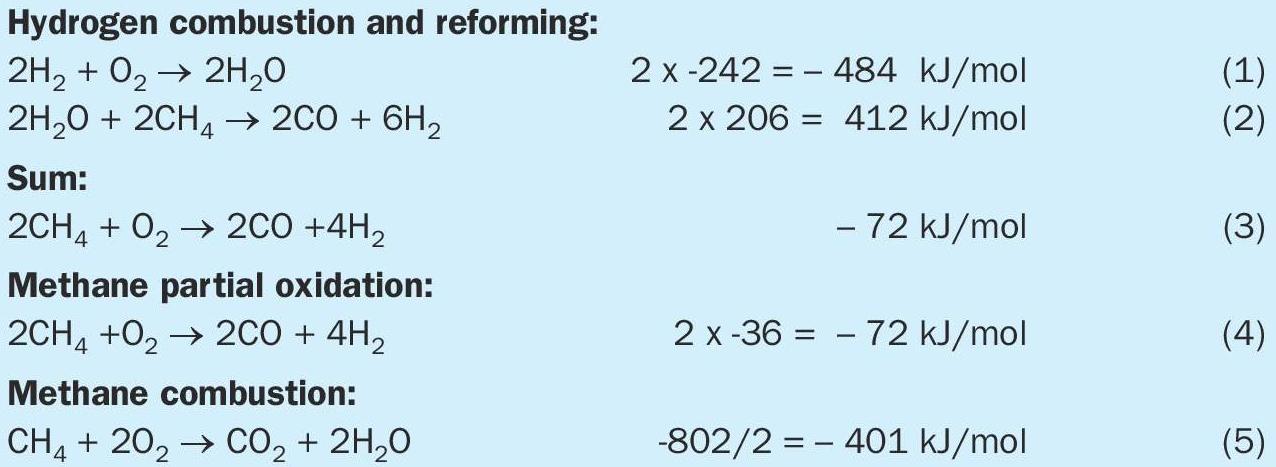
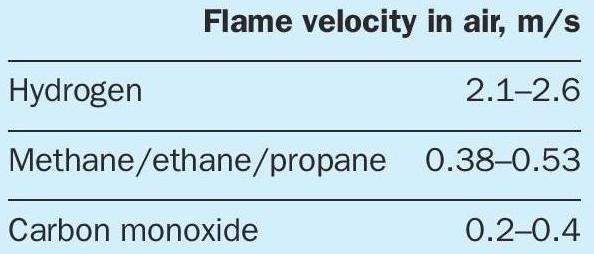
Heat formation
Reactions 1-4 in Fig. 1 show the main reactions for syngas production and reaction 5 shows the reaction for total combustion of methane.
The product stoichiometry of the main reactions (1)-(3) with hydrogen combustion and subsequent methane reforming is the same as for partial oxidation of methane (4), independent of the reaction pathway.
In reality the overall balance is determined by the reaction kinetics of all components for oxidation like methane, hydrogen and carbon monoxide.
The important observation is that the heat generation per mole oxygen consumed is about seven times higher with the oxidation of hydrogen (1) than with the partial oxidation of methane (4). And it is 20% higher than the total combustion of methane (5). That means with the higher flame velocity of hydrogen we can expect much higher local temperatures under current secondary reformer reaction conditions with hydrogen combustion than with the assumption of partial oxidation of methane for the whole amount of oxygen.
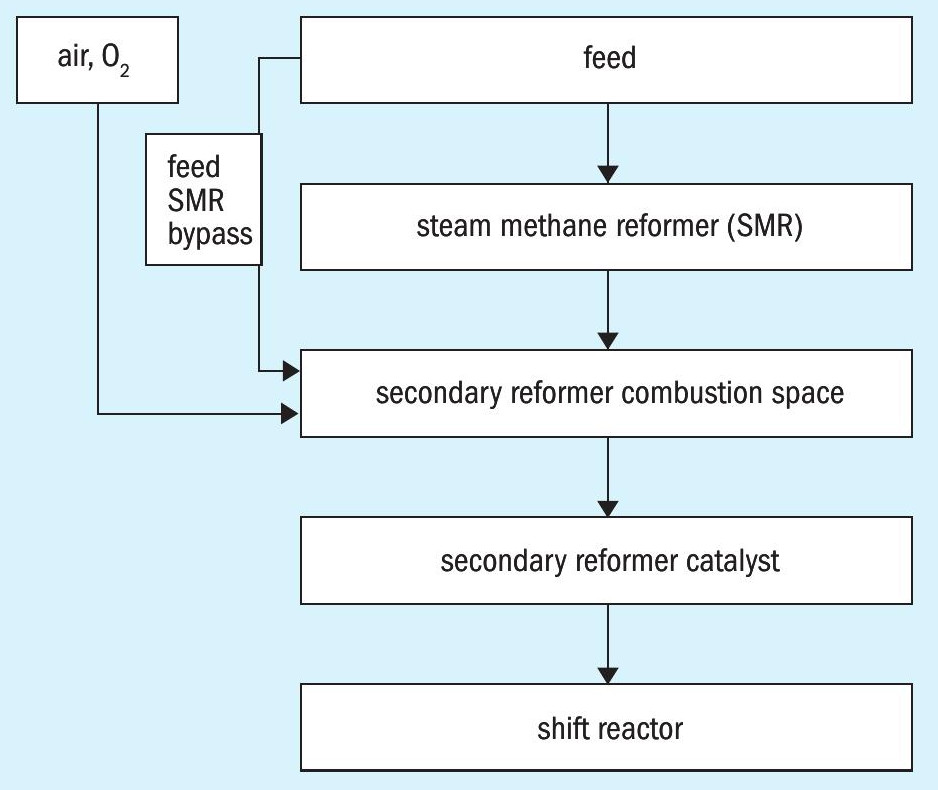
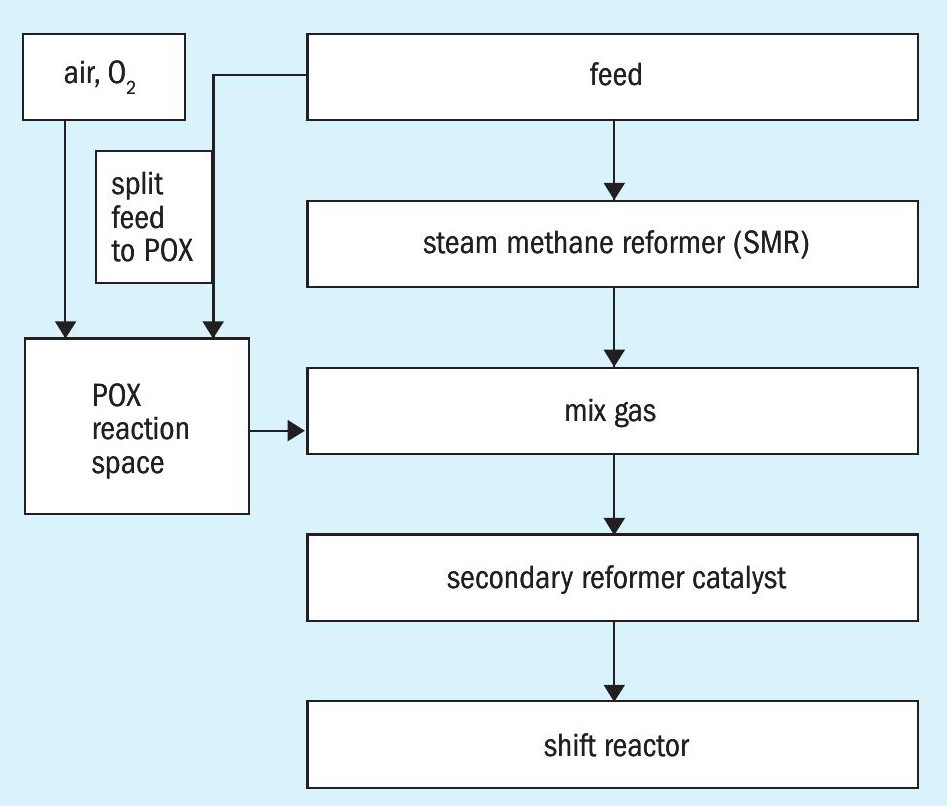
Process configurations
Typical process configurations for secondary reforming are summarised in Fig. 2, where in one case the whole feed gas is converted in the steam reformer 2,3 and in the other case the feed gas is split where one part is directed to the steam reformer and the other part bypasses the steam reformer and is routed directly to the secondary reformer 4 . In both cases the steam reformer syngas and optionally the mixture of steam reformer syngas and feed gas can be oxidised with air or pure oxygen in the combustion space of the secondary reformer or ATR to produce the heat for the reforming step in the catalyst. According to the higher flame velocity of hydrogen, a significant amount of hydrogen produced in the steam reformer is consumed for heat production in the secondary reformer.
The combustion of hydrogen from the steam reformer syngas gas in front of the catalyst and the related higher heat production can be avoided by an alternative process, shown in Fig. 3.
A part of the feed gas stream is directly contacted with oxygen or air before mixing with the steam reformer syngas gas, e.g. in a partial oxidation reaction (POX). Under these conditions no hydrogen from the steam reformer syngas can be oxidised and the heat from the product gas of the partial oxidation can be used for reforming of the methane in the secondary reformer catalyst after mixing with the steam reformer syngas.
Gas temperature and methane conversion
The principle effect of hydrogen oxidation in the combustion space in front of the secondary reformer catalyst is demonstrated for the following cases:
- Secondary reforming (SR): All feed gas is converted in a steam reformer and passed into a subsequent secondary reformer.
- Alternative secondary reforming (SR_A): Partial oxidation of feed gas from the split stream before mixing with syngas from the steam reformer.
- Bypass secondary reforming (SR_B): Oxidation of gas mixture from bypass flow together with syngas from the steam reformer in the secondary reformer combustion space.
These cases will be applied to a basic design of a new secondary reformer plant and a revamp design of an existing secondary reformer plant with a fixed steam reformer capacity.
There are at least two important parameters for the design:
- Catalyst inlet gas temperature – With rising temperature, problems with ruby formation, nickel evaporation and catalyst sintering and aging will increase.
- Methane conversion capacity of the catalyst – This determines the methane slip after the catalyst and is related to the catalyst inlet temperature.
In the basic design, 35% of the feed gas flow is routed as a split stream of the steam reformer to the POX reaction space or directly to the combustion space of the secondary reformer to react together with the steam reformer syngas and oxygen. With this configuration the size and capacity of the steam reformer can be reduced and the hydrogen efficiency can be increased for a certain product capacity.
In the revamp design, the feed gas flow is increased by 40% and the oxygen supply by 73% related to an existing steam reformer capacity. The parameters for standard secondary (SR) reforming are kept constant. The additional gas is routed directly to the POX reaction space (SR_A) or to the combustion space of the secondary reformer (SR_B).
To show the principle effect of hydrogen combustion in the secondary reformer space the proportion of oxygen consumption by hydrogen combustion is assumed for 40%, 70% and 100%. The remaining oxygen is assumed to be equally consumed by partial oxidation of methane and carbon monoxide oxidation.
The influence on the gas temperature with pure oxygen in front of the catalyst is shown in Figs. 4a and 4b.
For both design cases the alternative process shows significant lower gas inlet temperatures in front of the catalyst. For the revamp design, the bypass process (SR_B) shows gas temperatures with more than 1,400°C which are already critical. For the operation of the secondary reformer with air the maximum gas temperatures are about 100°C lower.
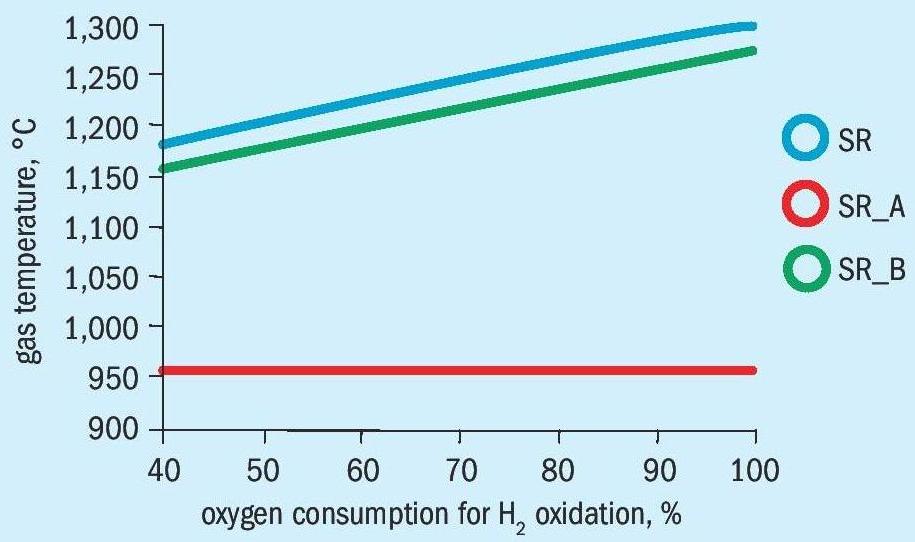
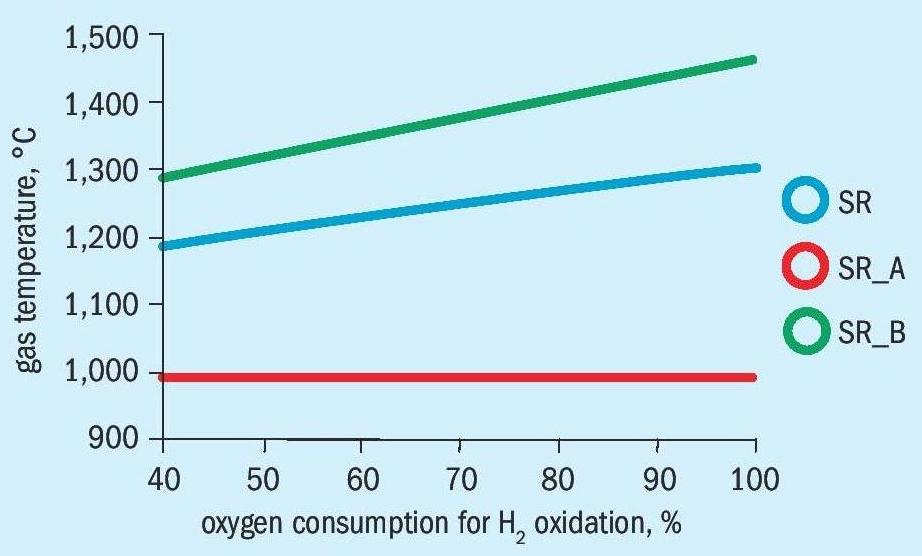
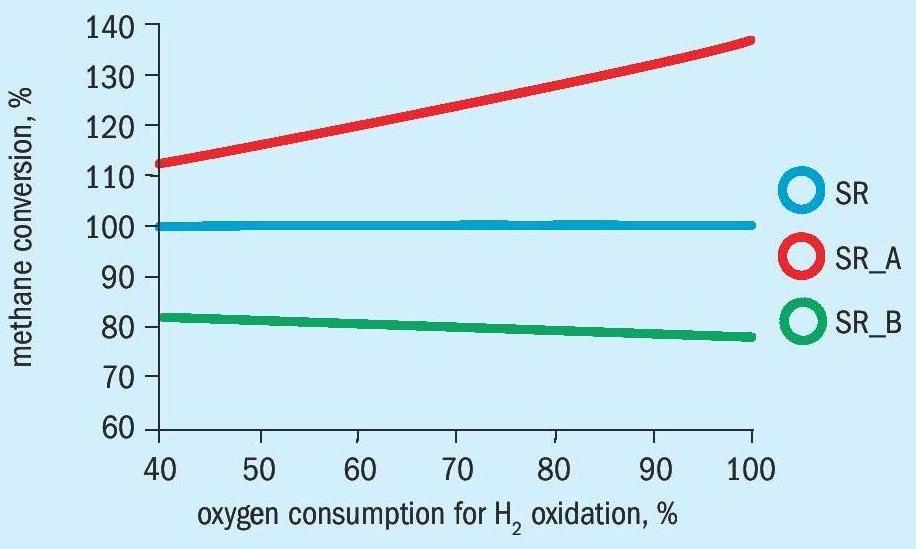
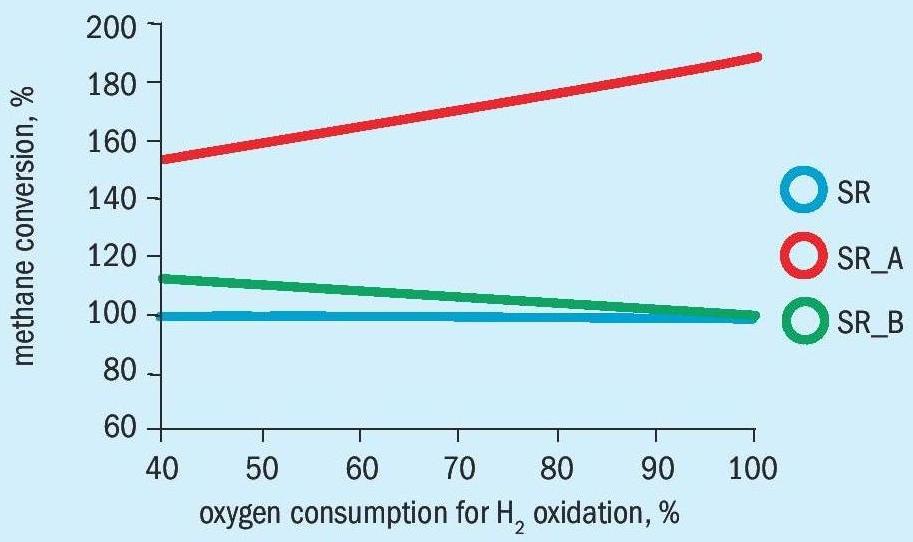
The methane conversion in front of the catalyst is related to methane conversion in the standard secondary reformer process (SR) with steam reformer and subsequent secondary reformer without bypass of a feed flow (Figs. 5a and 5b).
It can be seen, that the methane conversion is significantly higher for the alternative process than for the standard process SR and bypass process SR_B, because the oxygen for the heat formation is consumed by partial oxidation of methane and not for combustion of hydrogen from the steam reformer syngas.
Discussion
With a split feed gas stream with one part going to the steam reformer and the other part to the POX reaction or in the secondary reformer combustion space the hydrogen product capacity and the hydrogen production efficiency for a given steam reformer capacity can be increased.
For new plants, the steam reformer can be built smaller and for the revamp of existing plants the product capacity can be increased significantly. This means, that each secondary reformer (SR) is a source for additional hydrogen or ammonia feed gas.
The alternative process (SR_A) shows the following advantages related to the existing bypass process (SR_B):
- higher methane conversion in front of catalyst;
- lower gas inlet temperature in the catalyst and related lower ruby formation and aging of the catalyst;
- higher hydrogen efficiency than bypass process;
- no risk of burner damage and flame impingement on the catalyst;
- especially attractive for revamp activities because lower gas temperature in front of the catalyst and methane conversion capacity of the catalyst is kept within tolerable limits.
In the simplest case the alternative process can be operated with conventional proven technology with a standard reactor for partial oxidation, a gas mixing space for reformer syngas and POX syngas and a catalyst section for secondary reforming of the mixed syngas.
The design of a special POX burner which separates the POX reaction from the steam reformer syngas, which can be introduced in an existing secondary reformer can bring significant additional cost opportunities 6 . The application will need to be checked from case to case.
To evaluate the possible product increase and the related investments for existing secondary reformer plants an individual analysis related to the actual boundary conditions in respect of combustion conditions and tolerable capacity increase in downstream process units is necessary.
References