Fertilizer International 494 Jan-Feb 2020
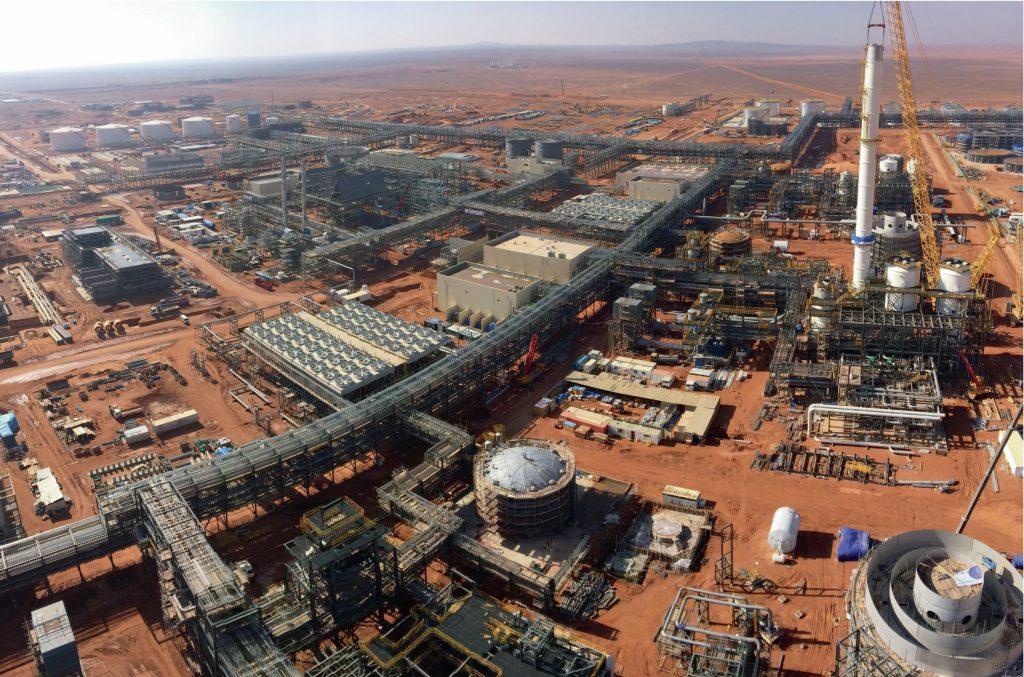
31 January 2020
Phosphoric acid plants for the 2020s
PHOS ACID PROCESS INNOVATION
Phosphoric acid plants for the 2020s
James Byrd of JESA Technologies (Worley, formerly Jacobs), Florida, looks at upcoming innovations in di-hydrate (DH) phosphoric acid plants for the 2020s.
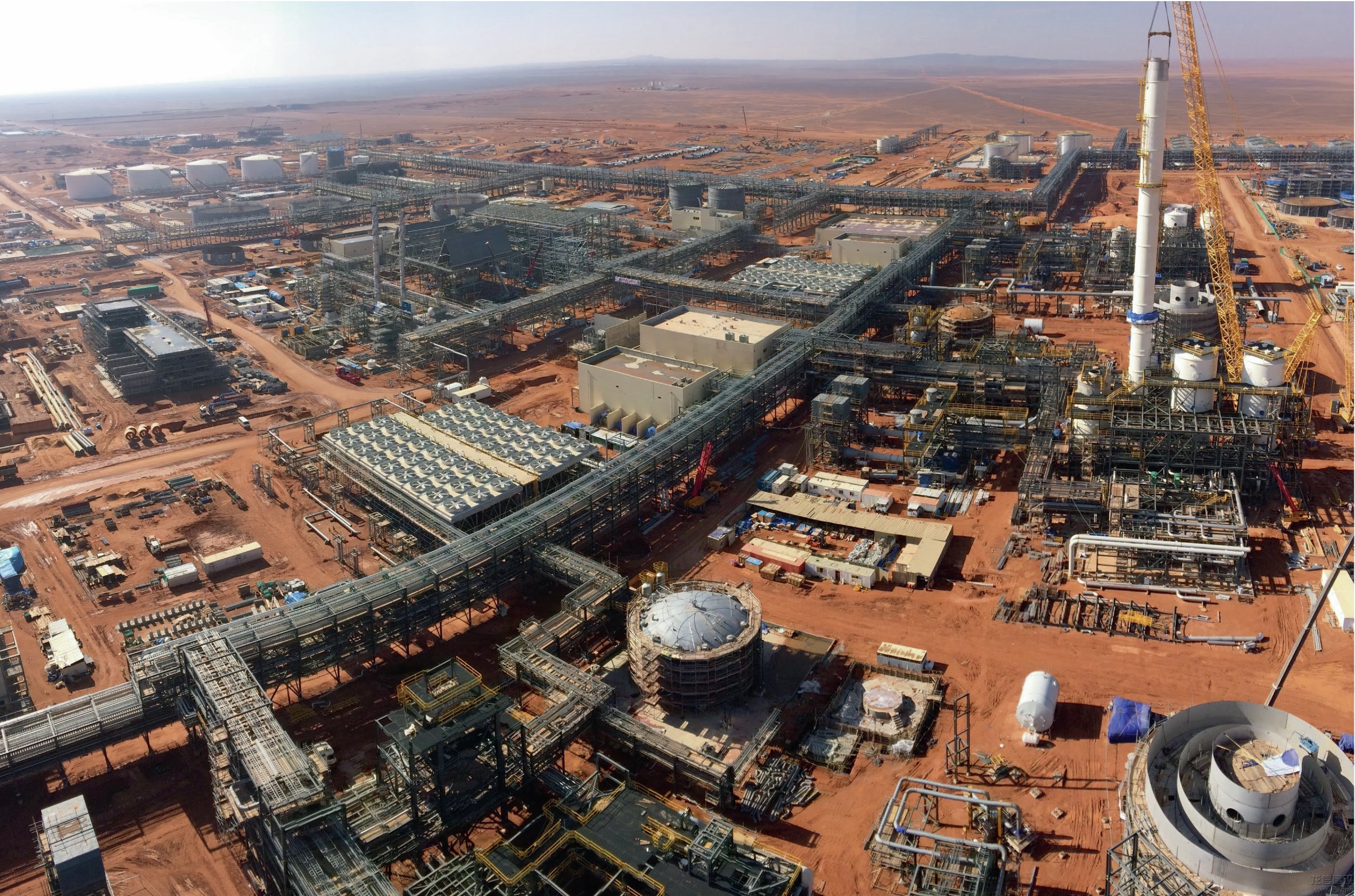
“The legacy of previous engineers is an amazing wealth of information we can learn from.”
Technological innovation, by introducing improvements to processes or products, offers new efficient ways of achieving the same or more ambitious production goals. In mature industries, innovations generally serve to bring down the unit cost of products. In a situation where small incremental improvements can cumulatively deliver large returns, it is not surprising that innovations are perpetually under study.
The importance of the process
The product being manufactured in a DH phosphoric acid plant is usually merchant grade acid (MGA). This can be the ultimate end-product or, in a vertically-integrated complex, consumed on-site as an intermediate in the manufacture of phosphate fertilizers. Because MGA is generally produced as a fixed and defined product, it is often the process that becomes the main focus for innovation at phosphoric acid plants.
Innovations can come in many forms. Equipment improvements have certainly changed how phosphoric acid plants are configured. But other more subtle process improvements can also provide dividends. Optimisation is possible at almost any phos acid facility, for example, even when the process is left largely unchanged.
The trick is to build these optimisations into the design phase of a project. This avoids the inefficiencies – in terms of cost or implementation – that invariably occur with retrofits. That is not downplaying the value of retrofits. It is just a recognition that, in engineering, the money is best spent early on.
This article will focus on innovations in di-hydrate (DH) technology for phosphoric acid production, as this process comprises over 80 percent of the market worldwide. Other production technologies, of course, do have merit. Indeed, matching individual technologies with the different production circumstances found across the world allows each process to find a place where it is the best fit.
The article is split into two sections. In Part 1, we look at the current state of the art and previous industry innovations. We then take a look at future innovations and trends that will influence the design of phosphoric acid plants over the next decade in Part 2.
Learning lessons from the past
No look forward is complete without a look back. Interestingly, over the decades, well-respected pioneers in our industry have written articles about future innovations more than once. Previous predictions are valuable as – by revealing how market forces influenced the industry in the past – they can tell us about our own path to the future. After all, the imprint of forces that influenced what our industry looks like today will also partly shape what it will look like tomorrow.
It is important to note that the general approach to improving phosphoric acid plants has been largely the same for many decades. Many significant improvements have been made in the past with undoubtedly more to come in future. In a world where the operating environment is constantly changing, the industry’s technology providers must evolve as well. Inevitably, those that stand still will actually lose ground due to the progress of their competitors.
Many talented engineers have made important contributions throughout the history of this mature industry. We owe them a debt as the current state of the industry is built on the lessons of the past. Yet technology has progressed to a point where it is sometimes easy to overlook or forget those past lessons.
Often, supposedly new ideas that are raised and dicussed have actually been thoroughly explored some decades earlier. Sometimes, these ideas may have newfound merit due to changes in the economic climate. Furthermore, no single idea is universally applicable as operators in different parts of the world have different concerns. While many phosphoric acid producers globally have superficial similarities, a deeper dive often reveals that their economic drivers are different.
In certain production situations, even driving down the unit cost per tonne may not be the primary driver. Where revenues and demand are both high, for example, production output may be more valued than production efficiency.
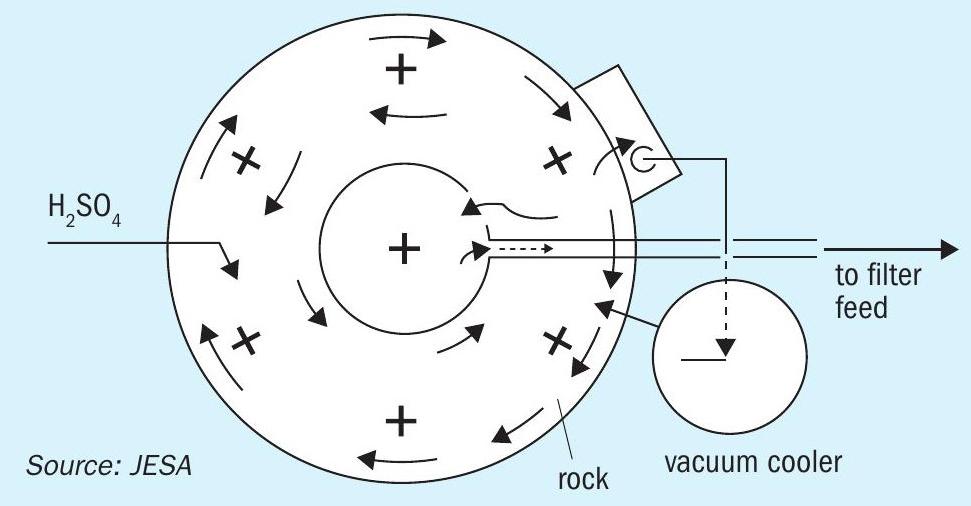
Many decades ago, the need for output over efficiency was recognised as an economic imperative that could be exploited under certain conditions. The danger comes in losing such institutional knowledge when the tide turns and highly efficient operation once again becomes the main objective. The value in using experienced operators and engineers, therefore, cannot be overestimated. The engineering literature states that phosphoric acid plants typically provide a six percent annual net return on annual production. Yet production losses can easily be higher in real operating conditions – a possibility that should be allowed for in plant design by ensuring the right balance is struck between design simplicity and flexibility.
The general point here is that there is a lot of merit in understanding how design principles have come to be applied. This is because a continuation of these principles is often the basis for current innovation and plant optimisation. But it also needs to be understood and appreciated that the same design principles are not always applicable in every circumstance. Indeed, from an engineer’s perspective, one of the things that makes this industry so interesting is that a bespoke approach is necessary – as there are few solutions that are universally applicable to every operation.
PART 1: Current state of the art
Ball mills
Very few DH phosphoric acid plants across the world can operate efficiently without first reducing the size of the ore they consume. Ball mills have been the traditional method for grinding phosphate rock concentrates for many decades, and are still the favoured method today. While dry grinding was preferred initially, wet grinding has become favoured for DH processes. This is due in large part to the power savings and operational reliability of wet grinding. The switchover from dry to wet grinding which began in the 1970s continues today. There are, however, industry circumstances where dry grinding is still warranted.
Ball mills require a substantial power load. A closed-circuit design improves their efficiency, in terms of both power usage and grinding consistency. It is important to recognise that the size distribution of the feed, and not just its chemistry, affects process parameters in the phosphoric acid reactor. Because phosphate concentrates make inherently unstable feeds, any improvements in grind consistency will therefore improve control of the phosphoric acid reactor.
Savvy operators will sluice phosphate rock in the ball mill with process water. Indeed, many plants have been retrofitted in this way from the 1990s onwards. The process water can come from gypsum stack decant water or from cooling pond water. Regardless of the source, sluice water usually contains P2 O5 that can be recovered to the process. While there are side effects – acidity, gas evolution, and gas entrainment in the slurry – these can be designed around.
Reactors: feed control, design and heat load
Rock slurry blend systems are used to mitigate variations in feed to the phosphoric acid reactor. This is critical in situations where slurries from different sources are blended together. Due to the water balance, it is desirable to supply the phosphoric acid reactor with a high solids feed. Because of this, rheology modification is one area that may become a focus for innovation in the future.
The use of nuclear density meters to monitor the reactor feed has improved solids control. The accuracy of these meters is unrivalled, allowing the automation of solids feedback loops. Future goals could include online chemical analysis of the rock slurry. Knowing the calcium feed to the reactor, the operator can more precisely add sulphuric acid to optimise reactor control.
Furthermore, while many have attempted online analysis for excess sulphates in the reactor slurry, this is not commercially successful at present. Jacobs did develop a method using conductivity meters many years ago. These meters have been used with moderate success, albeit primarily as trend indicators. Other methods have tried using slip streams, with one operator reporting moderate success, but scaling remains an inherent problem.
For reactors, much of our current understanding of internal recirculation properties and the benefits of sulphate control were first established back in the 1970s. At the time, agitation and flow schemes were identified as areas for future improvement in reactor design, as is still the case today. Computational fluid dynamics (CFD) has become accepted as the agitation design tool in modern times. CFD can improve reactor efficiencies and optimise capex and opex.
In the industry’s early days, the reactor heat load was controlled by air cooling. Then, in the late 1960s, flash coolers were introduced to control heat loads and increase reactor capacities. Low level flash coolers were subsequently designed and introduced in the early 1980s to improve cooler reliability.
Further improvements in the pumping capacity and direction of the recirculation pumps have been made since then. With increasing pumping capacities, the heat load removal for a given delta T has increased, particularly in the last ten years.
Plant capacity
Another trend was apparent between 1961 and 1978: phosphoric acid plant capacities were increasing (Figure 2).
One of the primary advantages of DH technology is economies of scale. To some degree, this is due to its relative simplicity and stability of operation. It was only natural that plant capacities would rise to keep pace with increasing equipment capacities.
Larger phosphoric acid plants are inherently more forgiving and flexible than smaller plants. The throughput to wetted surface area ratio increases with capacity. This reduces scale formation as there is less area available for scale nucleation per unit of production. With lower relative scale rates, plant run times can be extended between required turnarounds, allowing a higher relative specific reaction volume (SRV) to be realised over time. In turn, higher volumes improve reactor control resulting in higher overall yields and rates on an annualised basis.
Generally, the potential for improving annual production is greater at plants with higher nameplate capacities. Putting a precise figure on this higher annualised production, for project justification purposes, is problematic. Similar to investing in safety, the events that don’t occur justify the return on investment.
The trend for larger reactors continued through the 1990s culminating with the design and installation of a 2,650 tonne/day nameplate capacity plant in Paradeep, India, in 2000 (Figure 2). The plant, currently operated by IFFCO, routinely produces 3,000 t/d of phosphoric acid.
The obvious advantage of larger plants is their economies of scale for capex (capital expediture). The positive impact of plant capacity on opex (operational expenditure) is less pronounced. This is because opex is largely driven by raw material consumption and, to a lesser degree, labour and utility costs.
Filter design and operation
One logistical issue encountered with larger reactors has to do with filtration. Managing the return acid and mixing tee(s) is critical. Moderate strength acid is returned from the filter and introduced into the mixing tee alongside high strength sulphuric acid. Relative quantities are adjusted to control the dilution of the acid entering the reactor. The heat of dilution is significant as it provides a major source of heat in the reactor. Dispersing heat homogeneously is paramount to reactor control.
The use of multiple filters per reactor has been another practice that has evolved as plant capacity has increased. The primary goal here is to keep the reactor running. Every time a reactor shuts down mechanical losses occur during start up, shut down and the time it takes for the reactor to return to equilibrium. In addition, oversizing filtration – i.e. providing more filtration area than strictly necessary – by a larger margin than for other plant equipment allows higher relative production rates during routine washing of a filter. As a measure, oversizing also provides a way of mitigating against system upsets. Taken as a whole, these filter working practices should provide additional product tonnes on an annualised basis and help simplify operations.
Filter design has also advanced. The central valve, for example, has become more efficient in preventing entrainment losses and increasing filtration rates. It can even accommodate a dual vacuum system to increase overall control. Duct sizing has been optimised and vacuum pumps are also more efficient. Filtrate pumps can now be self-regulating too. This eliminates the need for filtrate tanks – bringing down the structural costs of the filter building and its elevation.
Another process advance has been in mixing tee placement. CFD has shown that placement makes a difference in how sulphates are dispersed. In an annular reactor, results showed that the position of the tee, relative to an agitator, controls whether the majority of sulphates move forward or backward in the reactor (Figure 3). This discovery can be exploited to improve process conditions, depending on the phosphate rock source. Advances in mixing tee design have also improved operational stability. JESA Technologies (JT) offers a proprietary tee to maximize dissolution and reliability.
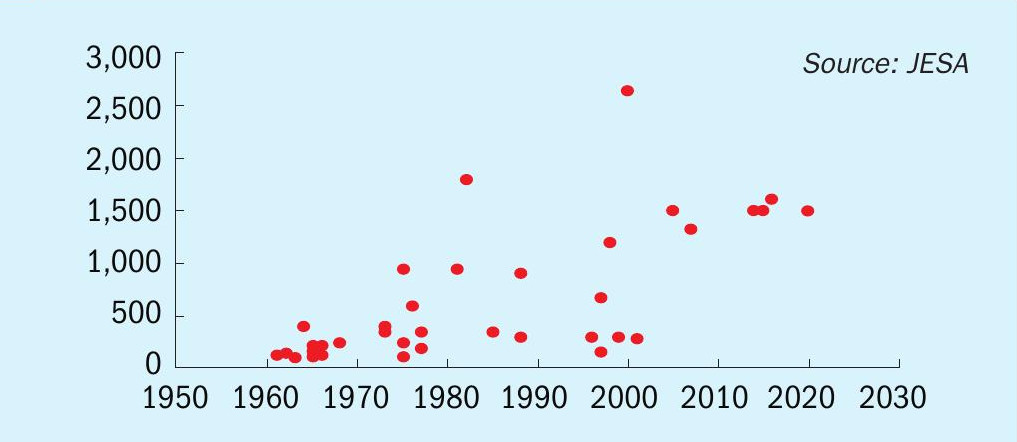
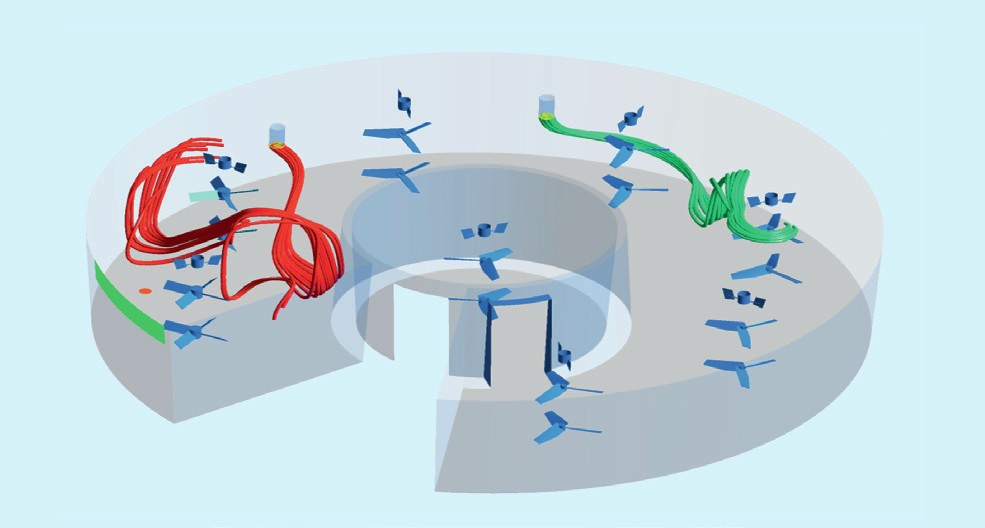
PART 2: Future innovations
Plant capacity and scale
Since 2000, no plant has been designed that approaches the nameplate capacity of the 2,650 t/d IFFCO plant in India. Nevertheless, with technological advances in filter capacities, flash cooler capacities and agitation, there is high confidence that even larger phosphoric acid plants can be designed and built. For example, a 3,000 t/d design with today’s technology could comprise of three filters and two flash coolers. This is a mark of progress as twenty years ago such a design would require five filters and three flash coolers.
Even a nameplate capacity of 3,000 t/d capacity should not be considered the upper limit for the size of phosphoric acid plants. Multiple filters, in excess of two, have been proven to operate successfully. It has also been proven that multiple flash coolers, again more than two, can be installed and operated in a single reactor.
In fact, a design exists in the JT archives for a 5,000 t/d plant. Although this was never built, the technical challenges in designing and building a larger scale plant have been overcome. It is likely there will be a time in the future where a 1,500 t/d plant will no longer be considered world-class. Economics dictate that this point will be reached, although precisely when this will occur is open to question. Given that the primary advantage of the DH process is economics and mass production, largescale plants are an easy prediction, as they allow these advantages to be further exploited.
Gypsum reuse
Gypsum, the by-product of the DH process, has received more attention, particularly as plant sizes have increased. Storage and/or reuse of gypsum has always been an issue because of the large volumes generated during phosphoric acid production. Environmental constraints are also becoming more and more prevalent throughout the world.
Other phosphoric acid technologies produce a slightly purer gypsum than the DH process, and is therefore one of the primary selling points for those technologies. Nevertheless, DH gypsum is being used in certain parts of the world, albeit on a limited basis. Developments enabling the ubiquitous reuse of gypsum look likely in the future. In fact, the inevitable shift to the gypsum reuse was predicted in a 1991 article by Dave Leyshon (see references).
Water balance
The phosphoric acid plant design is driven by the water balance. Any coherent design needs to take all local water constraints into account. Because water is a primary driver, and water concerns differ as much as the rock itself does, phosphoric acid plant designs also differ significantly between various locales.
Off the shelf plant design
Project teams typically want to copy plant designs, taking them off the shelf and then applying them to the next location to save time on the project schedule. While it is true that there is a time saving in quickly getting to the first drop of acid produced, this can be costly subsequently if start-up problems and delays occur in reaching full production potential – in essence there is a failure to realise project economics.
The economics of a plant that achieves its full potential late, versus early, is not something anyone wants to present to management. But it is a real issue nevertheless. It is quite impossible, except in retrospect, to quantify the production tonnes lost, the reductions in yields or the lower efficiencies that result from building and operating a plant with a copied, off the shelf design. Savvy operators will, however, take this point into account in future, so ensuring project economics will reach their full potential. In the overall scheme of things, developing a bespoke design early in the project does not require much additional time or cost.
Global losses
It is also useful to incorporate the concept of global losses into the coherent plant design. These can be significant even if many operators do not even track these. One operator, after seeking help, reported global P2 O5 losses of 15-20 percent of everything fed to the plant. This compares to 1-5 percent mechanical losses for a well-run plant cited in the literature. (Mechanical losses are equivalent to the global losses less filter losses). Management in a well-run plant will be aware of these losses and will be proactive in minimising them. It is not unusual for losses to exceed 5 percent, and even 10 percent, if mechanical losses are not a focus of operations.
Global losses therefore look set to remain a critical issue, looking ahead, as each operator takes steps to reduce the cost per tonne of product. Certainly, reducing global losses will be a focus of plant design in the future and, being a potential low hanging fruit, will also be the target of efficiency improvements in existing plants.
Acid concentration
Improvements in concentrating acid are closely linked to equipment advances. For example, recirculation pumps have become more reliable with higher capacities, while instrumentation and interlocks have also made operation much more reliable and efficient. Concentrator vessel construction has trended larger over the years too, albeit with the same design.
Entrainment separation has played an essential role in concentrator efficiency improvements as well, with several high efficiency designs currently commercially available. With proper design, the separator return can be merged with the product stream, improving throughput by about one percent.
Unit capacities have risen over time, although the heat exchanger bundle is a current limitation. Graphite is commonly used in the industry, but metal heat exchangers are becoming more economic. In monolithic heat exchanger designs, there is a limit on the graphite tube length. Metal heat exchangers, in contrast, could possibly break this barrier and be the basis for even larger unit capacities. Metal exchangers are well known by the phosphate industry in some parts of the world, while in others there is concern about corrosion being a life limiting factor.
Fluorosilicic acid (FSA) can be recovered from the process. Several design options are commercially available depending on the reasons for capturing fluorine and its end-use. Environmental designs that recover low-quality FSA, for example, have a much lower capex than designs that deliver product quality FSA.
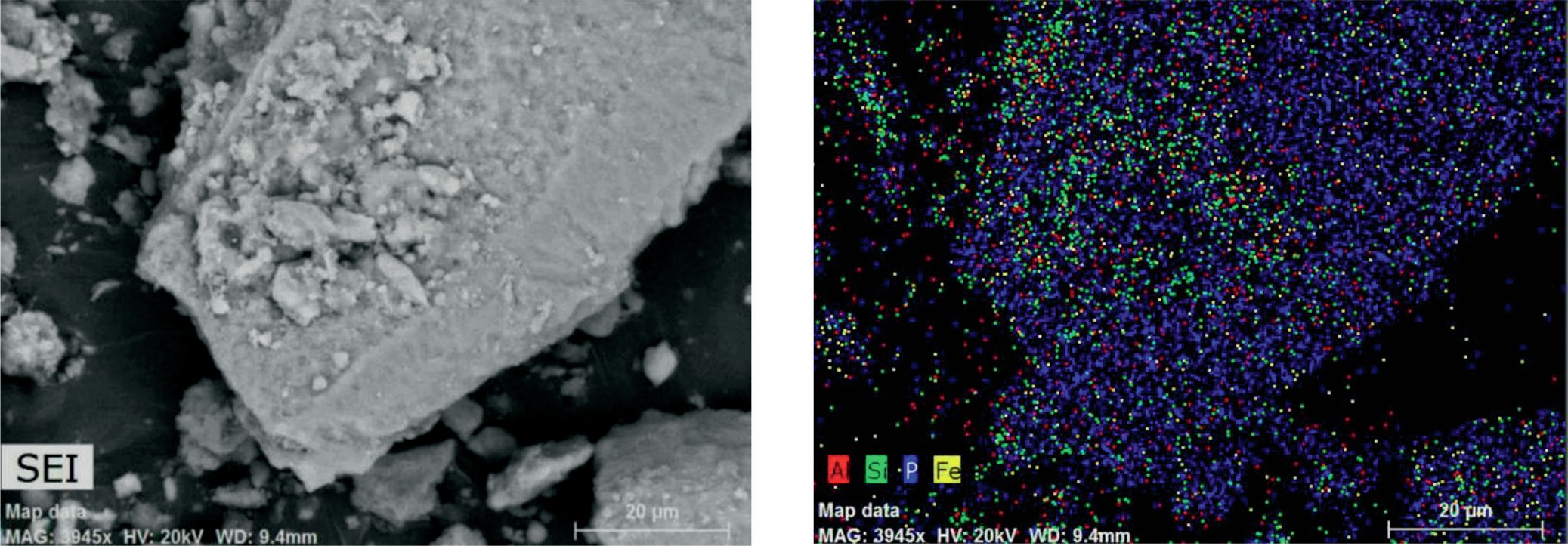
JESA Technologies (JT)
JESA recently rebranded its technology arm as JESA Technologies (JT). The renamed company is pursuing a number of specific innovations in response to current industry concerns.
JT has developed a modified flash cooler design. This new integrated flash cooler design is specific to the JESA reactor. The redesign is intended to save capex and minimise the plant footprint. Minor energy savings and improvements in process stability may also be realised. In this concept, the flash cooler sits on top of the reactor’s central compartment. Accommodations are also provided for cleaning. The design eliminates the need for an agitator in the central compartment. It does not alter the annulus geometry yet increases the open area of the annulus. A better recirculation ratio is anticipated as CFD has shown that the internal recirculation gains momentum in the open area.
Fluorine sequestration remains problematic for virtually every operator worldwide. JT has developed a new relatively low capex technique for neutralising fluorine. It is also an economically and environmentally attractive solution. Details of this process cannot be disclosed at present as the patent has not been filed as yet. Nevertheless, JT hopes to make the process commercially-available in the near future.
JT offers a patented iron removal technique. This can make some deposits commercially viable by removing iron and improving global losses. The associated equipment, because a slip stream is used, is small relative to the rest of the plant.
Operators are driving down their cost per ton of product produced, with process efficiencies being integral to this trend. JT offers a high yield mode for DH operations termed DH+. The goal is to provide an incremental improvement in filter losses. DH+ is expected to deliver increases in yields in the range of 1-2.5 percent. However, test work is required in all cases, with results being directly dependent on the source of phosphate ore.
JT is pursuing innovations in a number of other areas, including
- Upgrading coarse rejects for producing concentrate
- Flotation recovery for low-grade phosphate
- Refining flotation techniques
- Iodine recovery from phosphoric acid
- Cadmium removal
- Recovering rare earth minerals
- Chromium removal from phosphoric acid
- Sulphur recovery from gypsum.
Many more additional areas of investigation have also been identified. JT’s research and development activities are therefore expected to produce more results in the future.
Conclusion
The future is predicated on the past and present. Some great engineers and scientists have contributed a lot to this industry in many areas over time. Not recognising their achievements, which form the foundations for our own achievements, would be remiss. Foretelling the future is almost impossible – as can be seen when looking at the present from the past. Nevertheless, the legacy of previous generations of engineers is an amazing wealth of knowledge which we can draw on and learn from.
As we already know what the constraints will be, some forthcoming innovations for the 2020s seem like common sense – including efficiency improvements, cost reductions and advances in technology. These are all changes that have been predicted in the past. But how we execute such changes is likely to be what is different moving forward.
Larger scale phosphoric acid plants certainly seem likely over the next decade or so. In the future, the focus will also be on coherent plant designs. These will need to encompass the maximisation of global recovery, equipment refinements and consumption improvements.
A significant opportunity also exists for the comprehensive reuse of DH gypsum. It will be interesting to see what technology is either revived or developed to turn gypsum waste into a resource.
Only one thing is for sure, the future is coming, and – as a technology and engineering company – if we are not moving forward, we will be watching others overtake.
References