Nitrogen+Syngas 363 Jan-Feb 2020
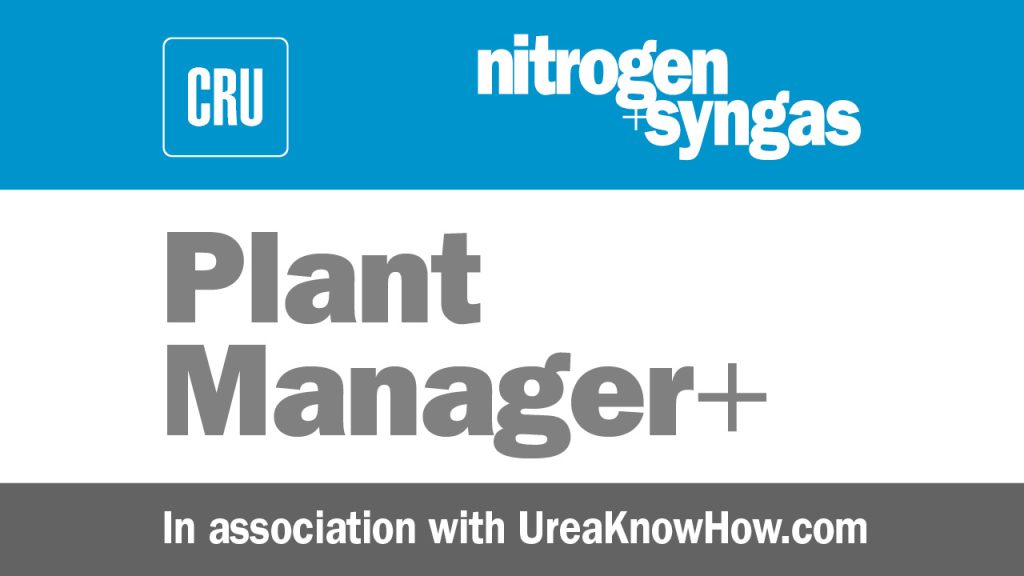
31 January 2020
Problem No. 58: Should liquid ammonia be drained to the ammonia water tank or vent stack?
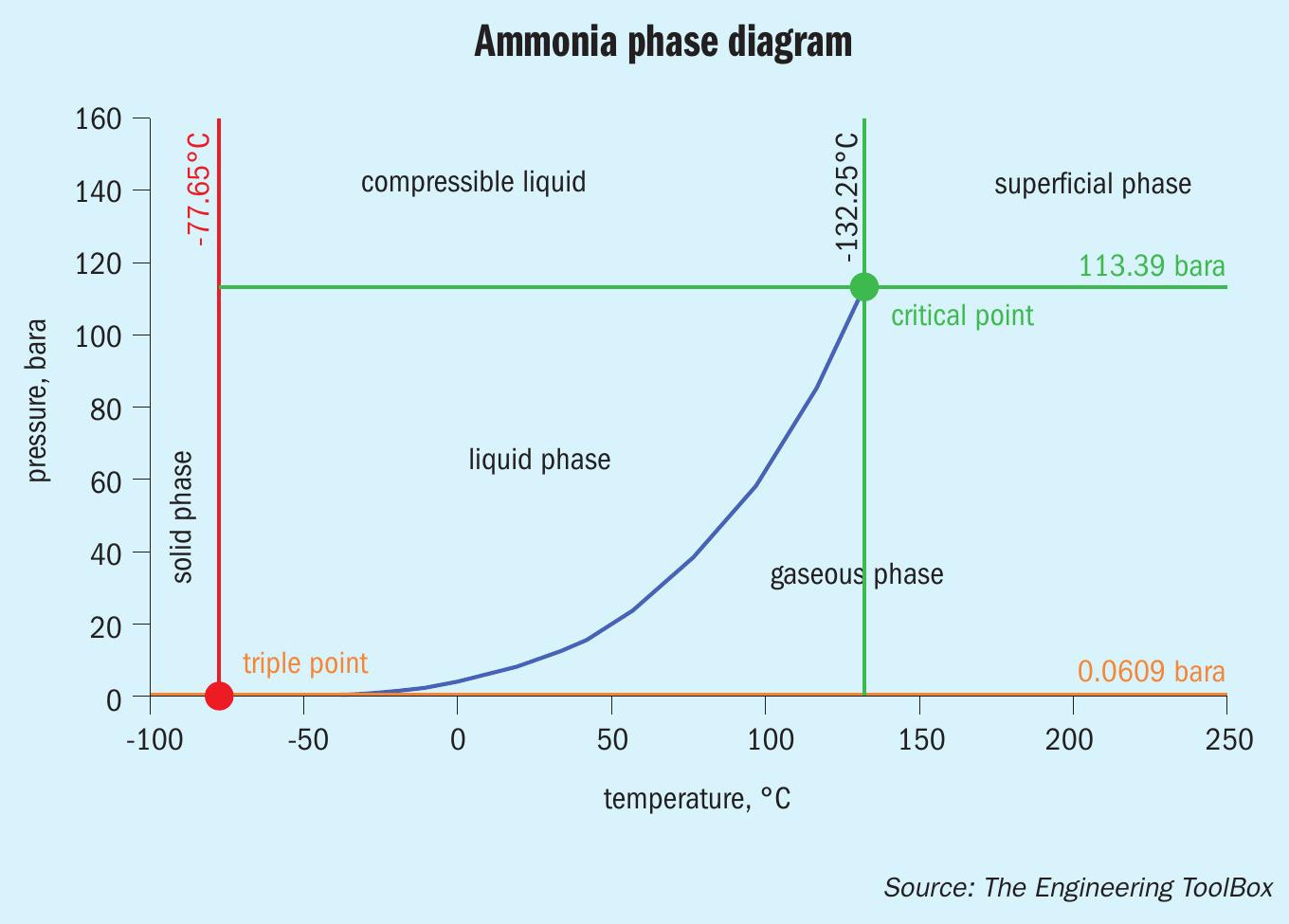
Ebrahim Mohamad Kamal of Abu Qir Fertilizers Company in Egypt starts this interesting discussion: What are the potential hazards from draining liquid ammonia to the ammonia water tank as some people prefer to drain it to the vent stack, which in turn directs ammonia to the ammonia water tank? Is there a difference between draining liquid ammonia from the ammonia pump or ammonia filters to the ammonia water tank or the vent stack?
Ahmed Selim of AlexFert in Egypt replies: In our plant, the vent stack is not supposed to receive pure liquid ammonia such as that present in the liquid ammonia system.
Ebrahim replies: We suppose that draining liquid pure ammonia to the vent stack is less hazardous than to drain it to the ammonia water tank as there is no hammering and the ammonia ends up in the ammonia water tank after overflow from the vent stank but at a lower pressure.
Muhammad Umar Riaz of Fatima Fertilizer company Ltd in Pakistan joins the discussion: Normally the liquid ammonia circuit piping is designed to cater for the impact of cold embrittlement while filling the ammonia circuit and draining/venting ammonia (at lower pressure when ammonia evaporates it causes sudden cooling i.e. cold embrittlement). That is why the ammonia circuit filling is carried out by first pressurising the ammonia circuit with nitrogen gas in order to avoid exposure of ammonia piping at a very low pressure, similarly during depressurisation of the ammonia circuit when the ammonia pressure falls below that of the nitrogen (utility header) pressure, any further depressurisation of ammonia will be carried out under nitrogen pressure due to the effects mentioned earlier.
Ammonia circuit piping is also protected against these sudden cooling shocks by using a suitable material of construction such as killed carbon steel. First, if you drain liquid ammonia into the ammonia water tank it will cause sudden cooling and may lead to cracks in the pipeline downstream of the ammonia circuit. Secondly when liquid ammonia evaporates in the ammonia water tank it will ultimately increase the pressure and release into the atmosphere and pose a safety concern. That is why it is preferred not to drain liquid ammonia directly into the ammonia water tank but to evaporate it to the vent header, from where it can be absorbed in showering water/condensate and finally recovered in the ammonia water tank.
Ebrahim replies again: In our plant design all the drains of the piping system for liquid ammonia are directed to the ammonia water tank and not to the vent stack. This is also the case for the drains of the high pressure ammonia pumps and the candle filter on the suction of theses ammonia pumps. So if it more safe to drain liquid ammonia to the vent stack why are all drains are directed to the ammonia water tank?
Ahmed Selim replies: Draining liquid ammonia directly to the ammonia water tank has been applied for several years in many plants, including ours and we have not suffered from any damage to the ammonia drainage system. Don’t you think that draining directly to the vent stack will actually increase the possibility of venting more ammonia vapour to the atmosphere compared to draining directly to the ammonia water tank? We know that drainage to the ammonia water tank from the ammonia system should be carried out slowly due to hammering and the impact of temperature and concentration on the tank after drainage. Also, can the material of construction used in the vent stack handle direct drainage of liquid pure ammonia and withstand the drop in temperature (cooling shocks).
Norozipour of Khorasan Petrochemical Company in Iran gives his opinion: I think the following arguments can be considered:
1. In our plant (Stamicarbon) the flow and quantity of liquid ammonia for draining to the ammonia water tank is usually very low.
2. From an environmental point of view it is important to collect any ammonia and hazardous material.
3. The production of ammonia requires energy consumption, therefore it is better to recycle it to the process instead of venting it to the atmosphere.
Mr Bhupen Mehta of IFFCO Kalol in India adds another consideration to the argument: A huge water volume will be required to collect the ammonia in the ammonia-water tank due to the ammonia-water saturation point at ambient conditions.
Prem Baboo of Dangote Fertilizers Projects in Nigeria shares his valuable experience: Good discussion and contribution by everyone. In addition, I think ammonia venting through the vent stack is very dangerous for the environment. Atmospheric ammonia has long been recognised as a key air pollutant contributing to the eutrophication and acidification of ecosystems. The advantages of draining through a closed drain into the ammonia water tank are:
1. Having a closed system for draining the ammonia into the water tank prevents ammonia escape to the atmosphere.
2. There will be some increased load in the waste water section (i.e. the steam requirement will be increased in the distillation tower/desorber), but the ammonia will be recovered (note ammonia is more costly than steam).
3. Most processes are typically total recycle processes so the ammonia must be recycled.
4. Nowadays advanced processes have some buffer tank to hold up the solution like ammonium carbonate and are also designed for shutdown solution hold up (e.g. carbonate solution tank (V-10 in Snamprogetti plants).
5. This is the routine practice to hand over HP ammonia pumps, filters, and ammonia booster pumps, all ammonia must be recovered through the ammonia water section. Some laws on pollution and for the environment to not allow ammonia to be vented.
This series of discussions is compiled from a selection of round table topics discussed on the UreaKnowHow. com website. UreaKnowHow.com promotes the exchange of technical information to improve the performance and safety of urea plants. A wide range of round table discussions take place in the field of process design, operations, mechanical issues, maintenance, inspection, safety, environmental concerns, and product quality for urea, ammonia, nitric acid and other fertilizers.