Fertilizer International 495 Mar-Apr 2020
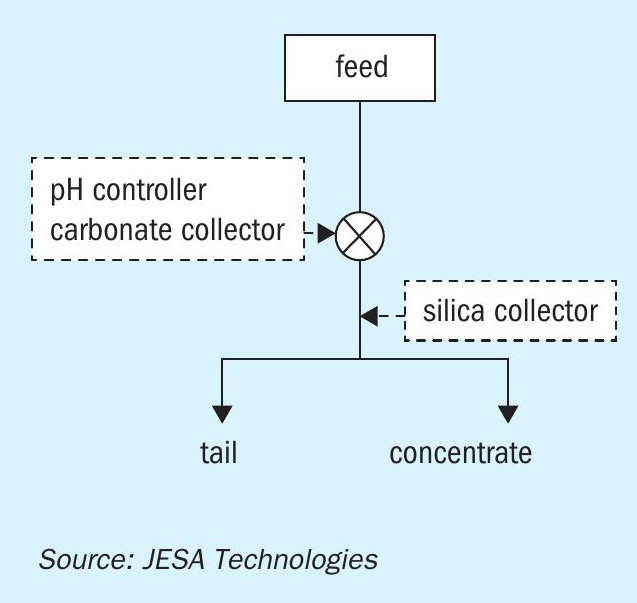
31 March 2020
Innovations in froth flotation
MINERAL BENEFICIATION
Innovations in froth flotation
Newly-developed froth flotation schemes, equipment and reagents are improving selectivity and the grade and recovering of phosphate concentrates
JESA TECHNOLOGIES
Two-stage flotation optimises performance
Reverse double flotation
Most sedimentary and igneous phosphate ores contain unwanted impurities that need to be removed prior to chemical processing. Froth flotation is currently the most economical beneficiation technique for separation and removal of impurities from phosphates around the world.
Many phosphate reserves beneficiated today are associated with carbonates and silica. Upgrading this type of phosphate ore can be costly and requires many beneficiation processing steps – such as crushing, scrubbing, classification, milling, de-sliming, attrition, direct or reverse flotation, etc. – to produce a phosphate rock concentrate suitable for the production of phosphoric acid.
The separation of carbonate from phosphate has long been recognised as one of the most challenging tasks in phosphate ore beneficiation. This is due to similarities in the physical and chemical properties of phosphate and carbonate minerals. Processing a phosphate ore that contains finely disseminated carbonate, as well as silica impurities, therefore requires a carefully designed flotation scheme. The selection of the correct reagents is also extremely important – to maximize phosphate recovery and ensure reagent consumption is optimised.
Single-stage vs two-stage reverse flotation
Single-stage reverse flotation is used to upgrade ore in many current phosphate beneficiation plants. This simultaneously floats carbonate and silica as tailings, leaving the phosphate sink as the final concentrate. Although this type of flowsheet benefits from simplicity, in practice, it can limit phosphate recovery for those ores that contains significant fine material. For these ore types, double reverse flotation is often preferable and recommended because it can improve P2 O5 recovery, reduce foaming, and lower reagent consumption and cost. In this two-stage process, carbonate is floated first, to remove all fines and slime carbonates from phosphate, followed by a second flotation stage to remove silica and clays.
Pilot plant tests
Flotation tests were conducted on a North African phosphate ore at JESA’s pilot plant, in Lakeland, Florida. The main purpose of the test work was to evaluate flotation performance using two flotation schemes. The first scheme used a single reverse flotation stage to float carbonates and silica together in one step. Whereas, in the second scheme, carbonate and silica were floated separately in two stages.
For both schemes, the ore was firstly scrubbed and classified at 160 microns to generate oversize and undersize products. The +160-micron product was then milled in closed circuit. The -160-micron material obtained from milling was then combined with the sample’s original -160-micron undersize. This combined product was then attrition scrubbed and deslimed at 40 microns to generate flotation feed for testing. The resulting -160 + 40 micron feed contained approximately:
- 27 percent P2 O5
- 7 percent insoluble material
- 1.3 percent MgO.
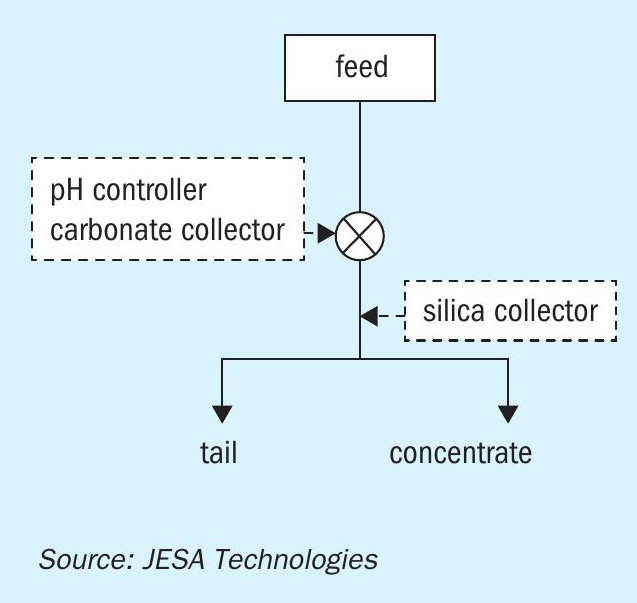
Calcite and dolomite were the main gangue minerals present. Both of these carbonate minerals together with silica needed to be removed from the feed to achieve a target grade of more than 30 percent P2 O5 in the phosphate concentrate.
Flotation tests were conducted using a Denver D12 laboratory flotation machine. The solids were pulped with Lakeland city tap water at ambient temperature. The feed was conditioned at a slightly acidic pH (less than 5.3) with phosphoric acid.
For single-stage flotation, the carbonate and silica were floated in one step as a tailing product, leaving the phosphate sink as a final concentrate (Figure 1). The slightly acidic feed was conditioned with a carbonate collector (phosphate ester) for two minutes, and a silica collector (amine) for 30 seconds, prior to flotation.
For two-stage flotation, carbonate and silica were floated separately. A fatty acid type carbonate collector was added in the first stage and an amine collector for silica in the second stage (Figure 2). The sink material from the carbonate flotation stage was de-slimed at 40 microns prior to silica flotation.
Pilot plant results
The flotation results for single- and two-stage reverse flotation are shown in Tables 1 and 2, respectively. These demonstrated that double reverse flotation in two stages separated carbonate and silica from phosphate very effectively. Carbonate flotation is more selective when performed separately from silica flotation – with about 58 percent of the MgO being removed in the carbonate tail compared to 45 percent using one flotation stage. The two-stage flotation scheme also achieved a higher concentrate grade (31.0% P2 O5 ) and phosphate recovery (91.5%) compared to the one-stage scheme (29.8% and 87%, respectively).
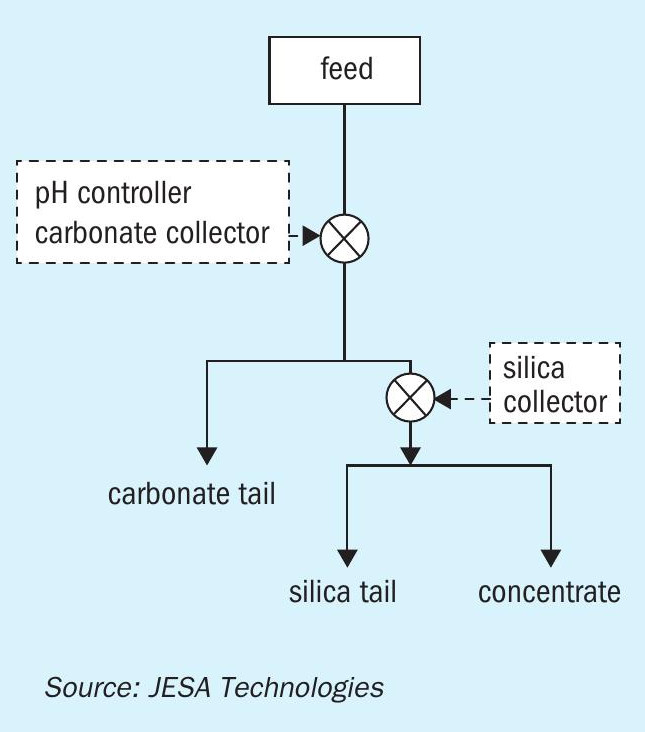
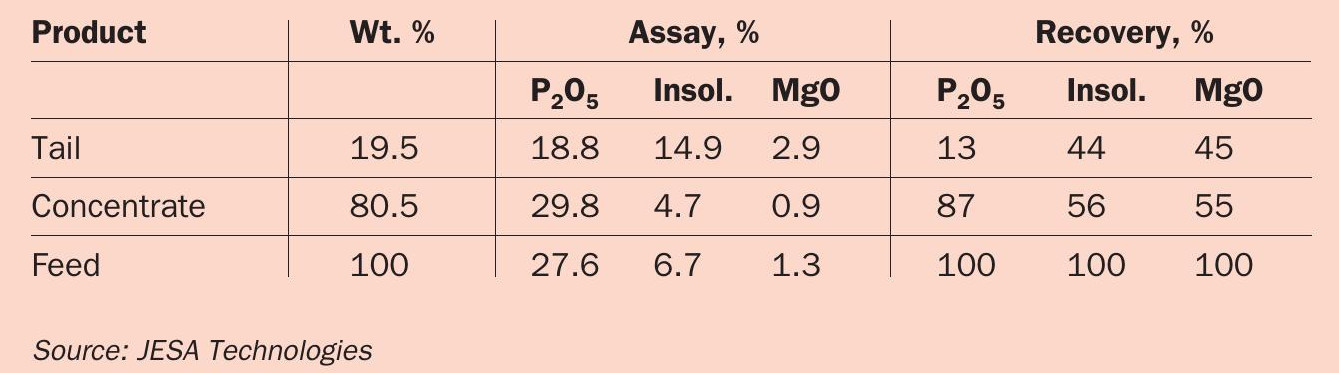
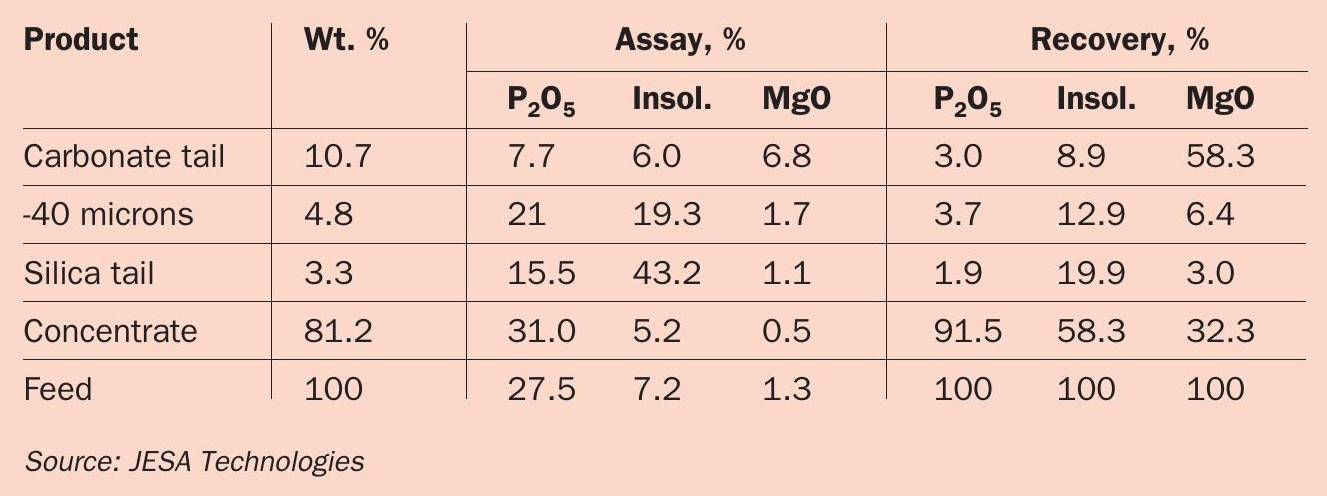
Summary
Flotation studies on a North African phosphate ore at JESA’s pilot plant in Lakeland, Florida, have demonstrated that separating carbonate and silica in two different stages results in better flotation performance. Overall, the test results show that removing fines and slimes, using a separate carbonate flotation before silica flotation, improves phosphate recovery, reduces the carbonate content in the final product, as well as minimising problematic foaming.
Reference
ERIEZ FLOTATION DIVISION
Column flotation of ultra-fine phosphate ore
Due to decreases in phosphate prices and the development of low-grade, finely liberated phosphate deposits, efforts are being made to maximize global phosphate recovery and grade within existing and prospective phosphate flotation circuits. Such improvements are essential when treating a low-grade ore where processing costs are highest, operating margins are lowest, and a near zero-waste approach is necessary.
Innovative Eriez Flotation Division (EFD) technology
Column flotation has been successfully adopted as a commercial mineral beneficiation technology due to its proven ability to improve ore separation performance and meet some of the above challenges. Typically, column flotation cells are capable of producing higher grade concentrates, with lower levels of impurities, compared to other types of flotation machines.
A key characteristic of column flotation cells is their ability to operate effectively while maintaining and washing a deep froth zone. Eriez Flotation Division (EFD) has developed its own proprietary industrial sparging system (Figure 1) for column flotation called the cavitation-tube (cav-tube for short). This improves fine particle recovery and maximizes the generation of bubble surface area.
The cav-tube system operates by recycling a portion of column underflow slurry through one or more specially-designed bubble generators – known as cav-tube spargers – while air is also introduced to the system upstream of the sparger. This two-phase air/slurry mixture is then passed through the cav-tube spargers causing hydrodynamic cavitation to take place. Cavitation ensures maximum collection of particles by promoting two simultaneous mechanisms:
- The generation of tiny ‘picobubbles’ that adhere to the surfaces of hydrophobic minerals
- Intense mixing within the remaining slurry.
Case study: the Três Estradas project
The Três Estradas greenfield phosphate project is being developed by Aguia Resources (Aguia) in the state of Rio Grande do Sul in southern Brazil. Beneficiation trials with EFD column flotation technology have been an integral part of efforts to develop the project.
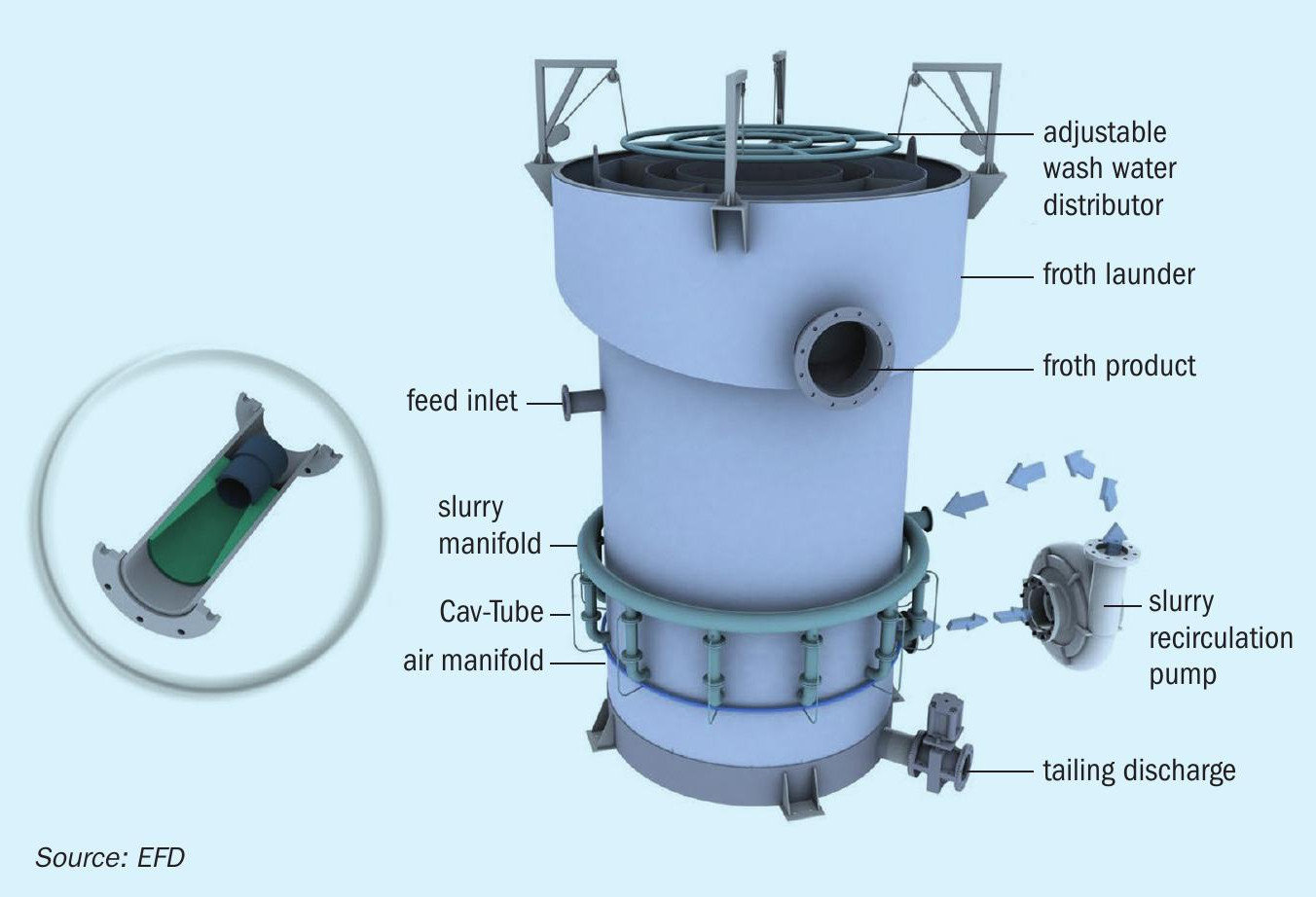
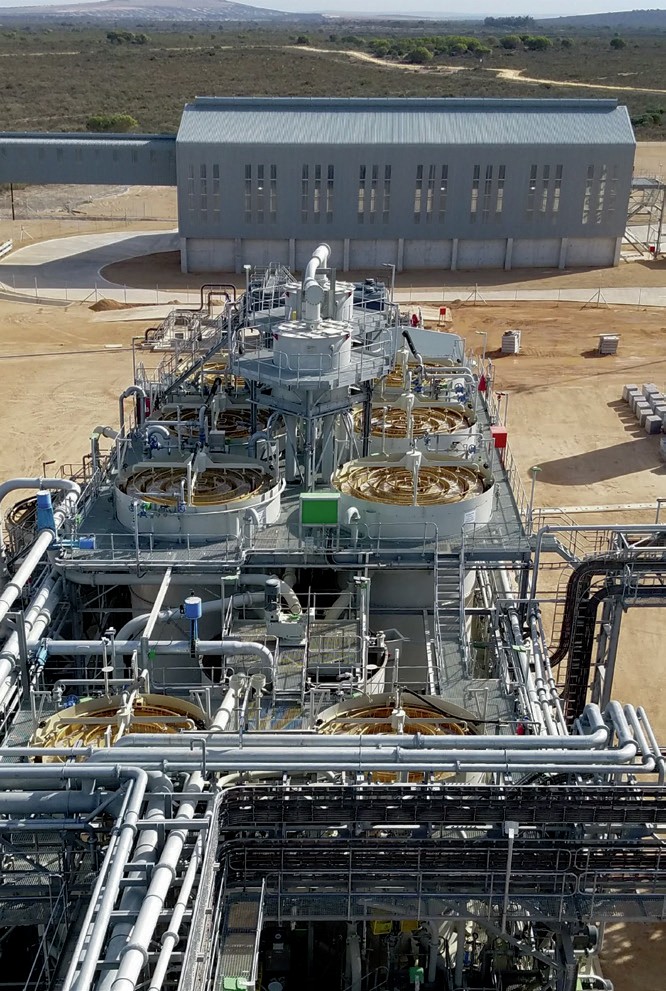
Initial bench-scale metallurgical test work on the Três Estradas ore indicated that a substantial portion of the apatite is contained in fine and ultra-fine fractions of the phosphate rock – and that, consequently, losses of apatite using conventional mechanical flotation machines could limit the commercial viability of the project. It was therefore concluded that column flotation should be considered for the Três Estradas project due to its inherent advantages over conventional flotation when treating fine and ultra-fine ores.
Using EFD’s automated multi-stage column flotation circuit, a series of steady-state flotation tests were conducted to determine the flotation response of fresh carbonatite and oxidised carbonatite (saprolite) ore samples provided by Aguia. Nearly one-third of the phosphate content of the fresh carbonatite sample was contained in the minus 25-µm fraction, while one-quarter of the phosphate in the saprolite sample was contained in this fraction. For both samples, this meant recovery and selectivity of ultra-fines during the flotation process was extremely important for maximising the global phosphate recovery and grade. Results obtained for both samples, using a rougher-scavenger-cleaner-cleaner reverse flotation circuit, are discussed below and shown graphically in Figure 2.
Column flotation results for the fresh carbonatite ore:
- Sample upgraded from 3.6-4.1 percent P2 O5 to 30-32 percent P2 O5 – at a P2 O5 recovery of 71-80 percent.
- Recovery increase of 2-3 percent, at equivalent concentrate grade, compared to results obtained by bench-scale mechanical flotation with five cleaning stages.
- Collector dosage requirement lowered from 600-800 g/t in bench-top mechanical flotation tests to 400-600 g/t in the steady-state column flotation tests.
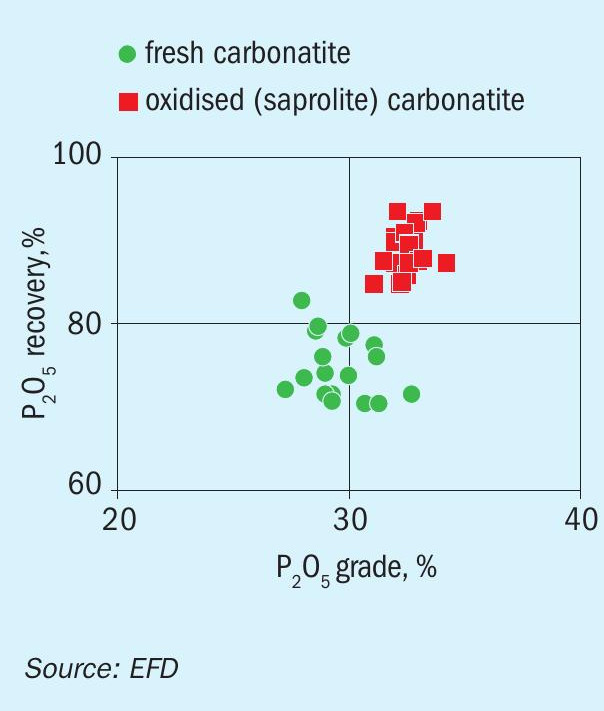
- Sample upgraded from 10.0-11.5 percent P2 O5 to 32-33 percent P2 O5 – at a P2 O5 recovery of 85-90 percent.
- Recovery increase of 5 percent, at equivalent concentrate grade, compared to results obtained by bench-scale mechanical flotation results obtained with three cleaning stages.
- Collector dosage requirement lowered from 800-1,200 g/t in bench-top mechanical flotation tests to 450 g/t in the steady-state column flotation tests.
In summary, test work with EFD’s column flotation technology for the flotation of ultra-fine phosphate ores realised a number of distinct benefits. These included a higher degree of selectivity, increased recovery and reduced collector dosage, in comparison to bench-scale mechanical flotation cells. Specifically, column flotation increased phosphate recovery from fresh carbonatite and oxidised carbonatite ore (saprolite) by 2-3 percent and 5 percent, respectively, while collector dosage was reduced by 20-40 percent. At the same time, the required number of cleaning stages to achieve the target concentrate grade was reduced.
Reference
ALLMINERAL
Pneumatic flotation: the breakthrough technology
Flotation technologies fall into one of three groups – mechanical, pneumatic and column flotation. Conventional Denver type mechanical flotation cells are currently the most well-established in phosphate processing plants worldwide.
The German company EKOF manufactured the first pneumatic cell for coal flotation in 1987. The innovative design incorporated an energy saving, self-aspirating, venturi-based aerator.
The allflot® pneumatic flotation machine from Düsseldorf-based manufacturer Allmineral (Figure 1) offers several potential benefits for phosphate ore flotation. It can either function as a scavenger cell to increases recovery and/or as a cleaner cell to improve grade.
The most important conditions necessary for pneumatic flotation are:
- Efficient reagent conditioning prior to flotation
- Creating the perfect size range and amount of air bubbles
- Efficiently attaching the air bubbles to mineral particles.
Essentially, the allflot® machine behaves as a high-intensity flotation cell – with a flotation throughput 2-4 times greater than an equivalent mechanical flotation cell. The machine brings mineral particles into close contact with fine bubbles within an external aerator/ contactor. The external contactor uses either pressurised air or air entrained in a fluid jet. The contactor/aerator functions as the primary collection zone while the main tank acts as the disengagement zone.
The allflot® machine’s unique vertical pneumatic flotation design has been successfully demonstrated for coal, industrial minerals and other ore types. Phosphate flotation experience with the machine dates back to 1996 and includes detailed test work at JPMC in Jordan, Simplot in the US and Kazphosphate in Kazakhstan. Results demonstrated the ability of the allflot® machine to produce marketable phosphate grades and achieve high recoveries.
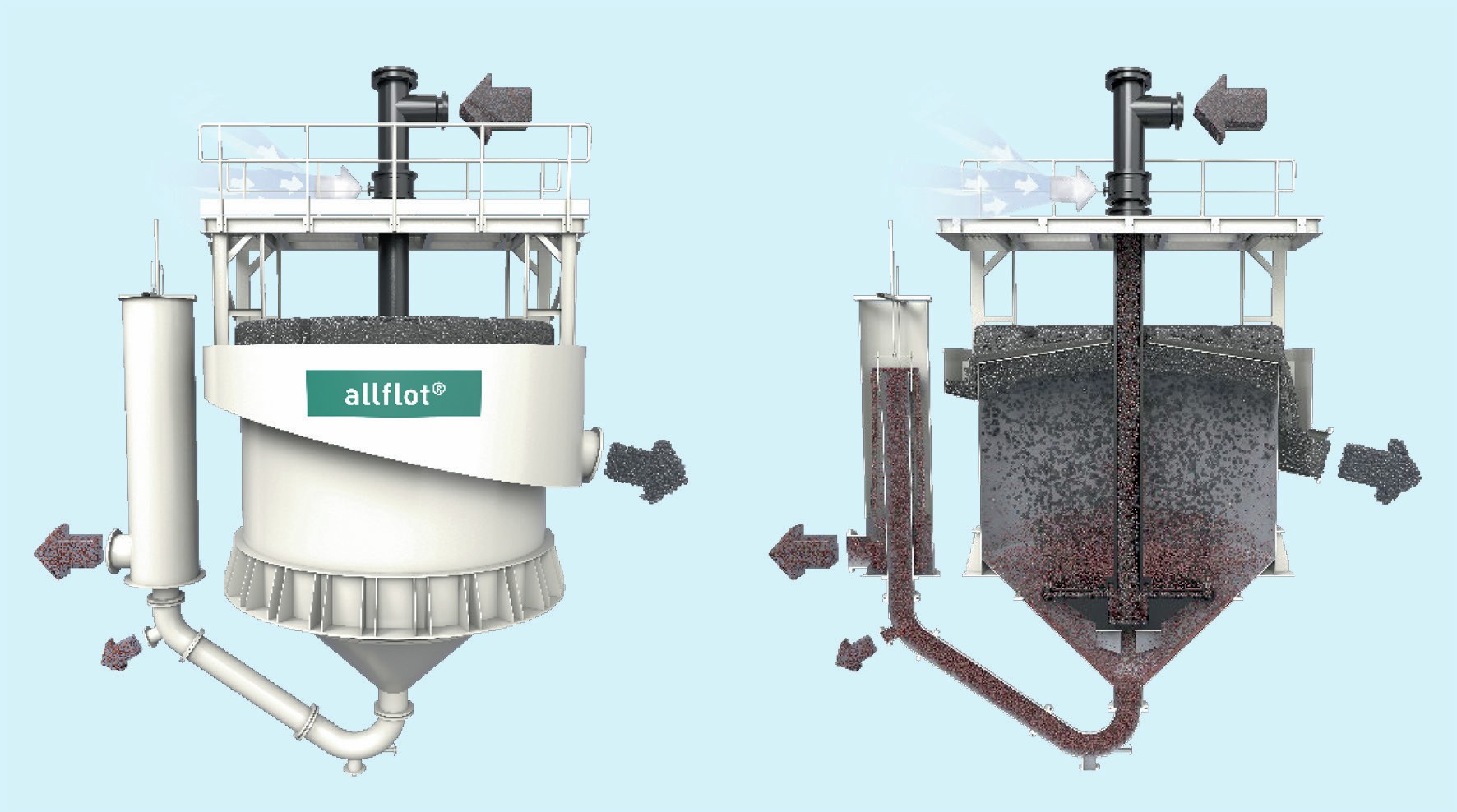
Allmineral designed a new froth channel discharge system for its pneumatic flotation machine in 2015. This allow both fine and coarse particles to be floated simult[aneously.
To maximise efficiency during phosphate flotation, Allmineral recommends a flotation scheme that combines different flotation technologies. The company suggests the following two-stage scheme based on its operational experience:
- First stage: a rougher flotation stage using mechanical agitator banks/tank cells.
- Second stage: a scavenger stage using allflot® pneumatic machines.
Using allflot® machines as a scavenger cell in this way improves phosphate recovery by capturing and floating fine phosphate particles that would otherwise be lost by the turbulent rougher cell. (Conversely, when installed as a cleaner cell, allflot® technology is also able to deliver higher grade phosphate concentrates.)
The power consumption of allflot® pneumatic flotation cells are 40 percent lower than conventional mechanical agitator cells. Their installation footprint is also smaller. Furthermore, allflot® machines improve recovery and concentrate grade, as the flotation takes place without rotational parts and turbulence. Allmineral recommends a de-sliming hydrocyclone stage prior to flotation. Process water also needs to be cleaned using a thickener before being re-used in the flotation circuit.
Reference
NOURYON
Highly selective Gemini flotation collectors from Nouryon
Nouryon manufactures and markets a large portfolio of flotation reagents for the worldwide mining industry, including collectors for the flotation of calcite, iron, phosphate, potash, niobium, silicates, graphite and sulphide ores.
The company is a leading global provider of customised collectors for the phosphate flotation market. Nouryon’s wide range of collectors are specifically tailored and optimised for different phosphate ore types (Table 1).
Complex ores are starting to dominate the mining industry due to the fast diminishing availability of high-quality rock deposits. The beneficiation of these complex ores requires advanced technologies. In response to this, Nouryon’s research and development teams have worked intensively to develop highly sophisticated collectors for phosphate flotation – developing unique products and product blends able to deliver the required grade and recovery levels.
For phosphate ores containing only apatite and silicates, beneficiation using straightforward and proven technology is generally effective. The same is not true for more complex ores with high carbonate contents. Historically, obtaining high-quality phosphate concentrates from these difficultto-process ores has been highly problematic. This is because traditional fatty acid collectors float apatite – also a calcium-bearing mineral – alongside calcite and dolomite, unless an effective depressant is available. However, following a recent breakthrough, Nouryon is now able to provide collectors which are highly selective for apatite only, so eliminating the need for a depressant.
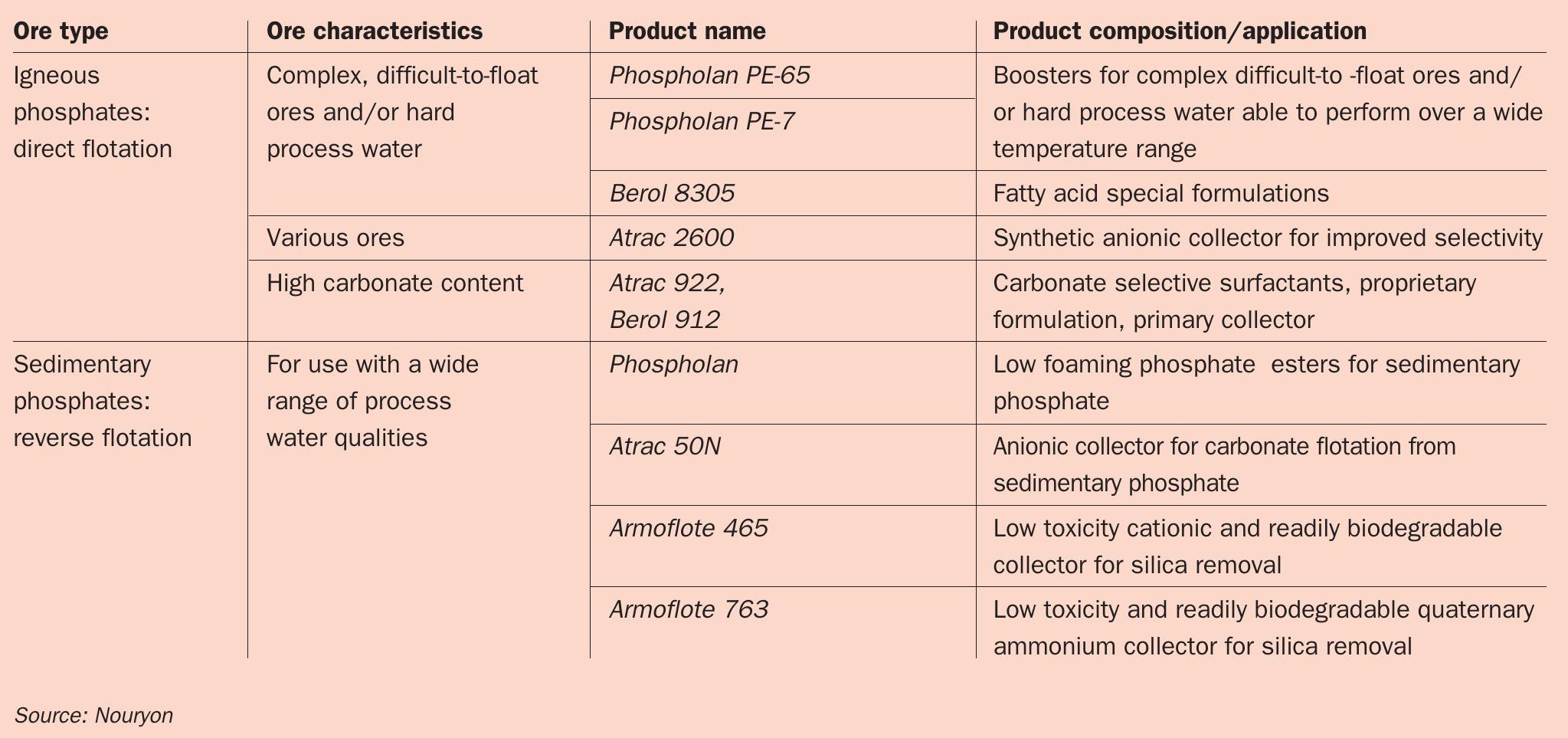
Nouryon, in close collaboration with its customers around the world, is developing improved process reagents for phosphate producers, especially those applied in mineral beneficiation and flotation. Nouryon recently introduced the Gemini family of environmentally-friendly apatite collectors. These novel reagents are based on anionic surfactant technology and are effective collectors for the flotation of phosphate ores containing carbonaceous and/or siliceous gangue minerals. Compared to benchmark collectors currently used within the industry, Nouryon’s Gemini range show outstanding selectivity towards apatite at a much lower dosage.
As a company, Nouryon is strongly committed to creating safer and more sustainable products. The Gemini family of novel apatite collectors, for example, combines high flotation performance and efficiency with high standards for product and environmental safety.
“To meet customers’ challenging requirements, we are focusing on developing sustainable solutions for the mining industry,” said Natalija Smolko Schwarzmayr, one of Nouryon’s senior scientists in mining R&D. “We identify these as sustainable solutions due to the environmental profile of the surfactants and the improved efficiency and performance of our collectors.”
Reference