Sulphur 387 Mar-Apr 2020
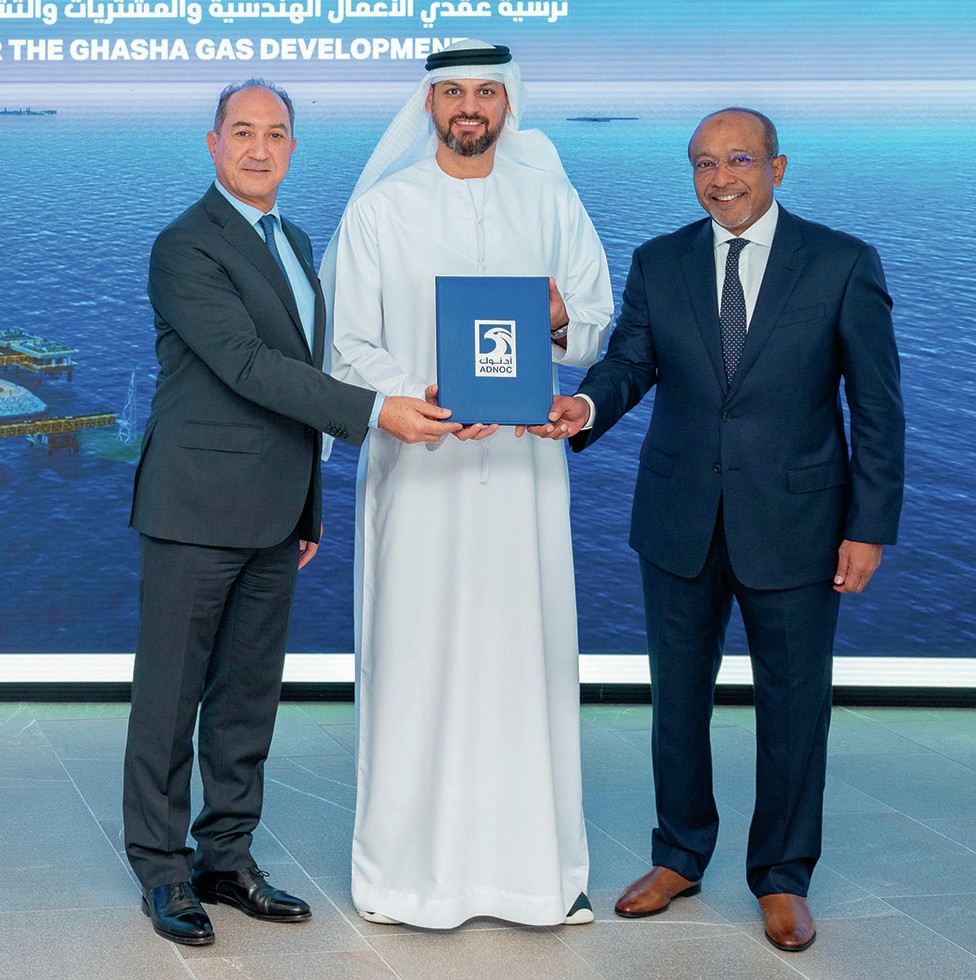
31 March 2020
Sulphur Industry News Roundup
Sulphur Industry News
UNITED ARAB EMIRATES
ADNOC issues Dalma offshore sour gas contracts
The Abu Dhabi National Oil Co. (ADNOC) has awarded two EPC contracts with a total value of more than $1.65 billion for the offshore Dalma sour gas development, 190 km northwest of Abu Dhabi city. Dalma is one of the fields in the offshore Ghasha ultra-sour gas concession, which ADNOC views as central to the UAE achieving self-sufficiency in domestic gas supplies.
The contracts went to Petrofac Emirates LLC and a joint venture between Petrofac and Sapura Energy. Both are due to be completed in 2022, with 70% of the total value set to flow into the UAE’s economy under ADNOC’s In-Country Value (ICV) programme.
Under the first contract, valued at $591 million over 30 months, Petrofac/Sapura Energy will engineer, procure, and construct three new wellhead platforms, removal and replacement of existing topsides, new pipelines, subsea umbilicals, composite and fibreoptic cables at the Hair Dalma, Satah, and Bu Haseer fields. The second, $1.065 billion contract, will see Petrofac become responsible for new gas conditioning facilities for gas dehydration, compression and associated utilities in Arzanah Island, 80 km from Abu Dhabi city. The treated gas will then be routed to the Habshan complex for further processing to deliver sales gas, condensate, and sulphur.
Dalma will produce 340 million cf/d and the Ghasha megaproject more than 1.5 bcf/d, when the latter comes onstream during the mid-2020s. According to ADNOC, Ghasha could supply close to 20% of the UAE’s gas demand by the second half of this decade, and more than 120,000 bbl/d of oil and condensates once fully operational.
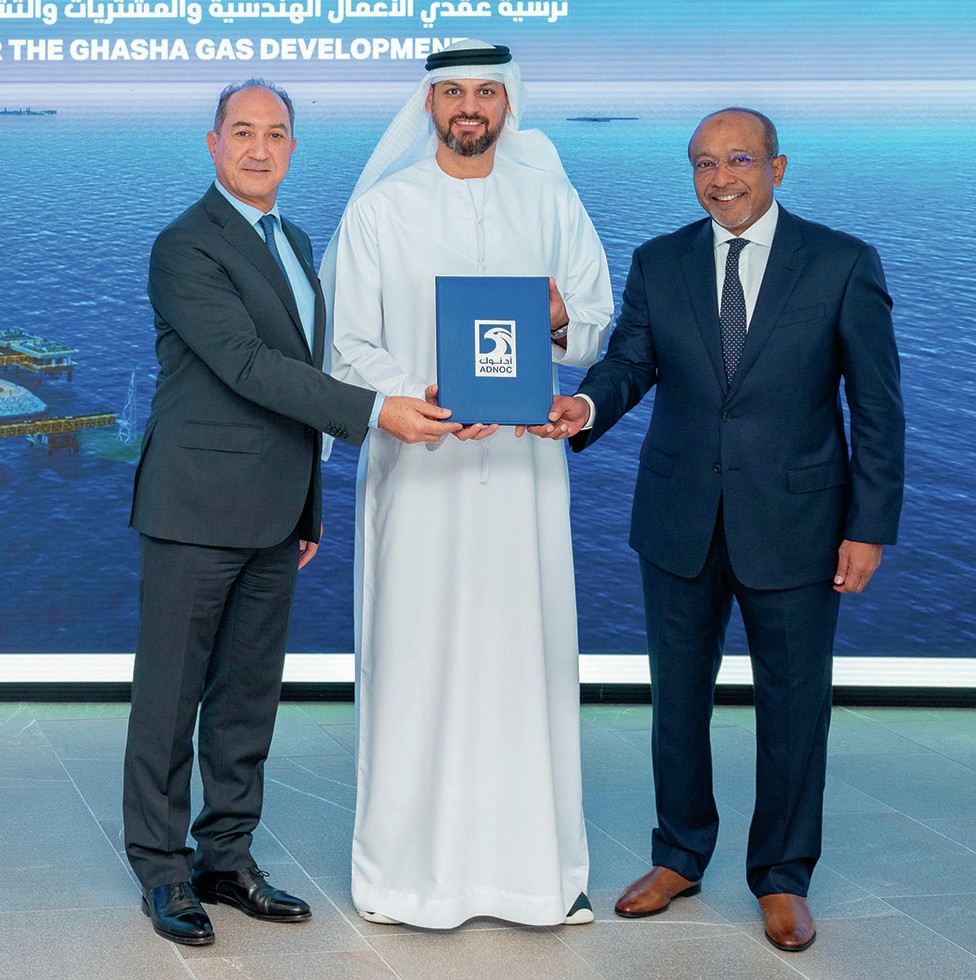
Major discovery at Jebel Ali
A new gas discovery in the UAE will boost domestic supplies, although it is expected that the UAE will continue to be a gas importer via LNG and the Dolphin pipeline from Qatar. The huge shallow gas reservoir at Jebel Ali is estimated to hold up to 0 trill ion cubic feet of gas, and is the world’s biggest gas find since the discovery of the Galkynysh field in Turkmenistan in 2005. It covers an area of around 5,000 km 2 and is still in the early stages of appraisal. ADNOC made the discovery on the border between the Emirates of Dubai and Abu Dhabi, and will develop it jointly with the Dubai Supply Authority (DUSUP), with gas from the field to flow to Dubai via DUSUP to feed utilities and industrial companies. Dubai has no gas of its own and imports 2 bcf/d of gas from Qatar as well as additional volumes imported as LNG, although the start-up of new coal and solar power projects will lower gas requirements in 2021. Total gas production in the UAE (mainly from Abu Dhabi) is around 6.2 bcf/d, while gas consumption is around 7.4 bcf/d, although exploitation of the new reserve could see gas self-sufficiency by 2030.
The discovery comes after Eni and the UAE’s Sharjah National Oil Corp. made another find recently, with gas and condensates flowing from a test well in Sharjah, the first onshore Sharjah discovery in 37 years.
ROMANIA
Petrom switches to LSFO production
Romania’s OMV Petrom has started production of 0.5% sulphur content low sulphur fuel oil (LSFO)at its Petrobrazi refinery in Romania to meet the new IMO 2020 fuel specifications. The production follows a e3 million ($3.2 million) upgrade of the refinery for it to produce70,000 t/a of low sulphur bunker fuel, relieving a Romanian market heavily reliant on imports.
“The new marine fuel oil obtained at the Petrobrazi refinery has only up to 0.5% sulphur content, in line with the IMO global sulphur limit applicable to the shipping industry starting from this year,” OMV Petrom stated. “OMV Petrom supports the maritime transport industry with a sustainable solution, both economically, as well as from the perspective of environmental protection. According to IMO, by limiting the sulphur content in ships’ fuel oil to 0.5%, an annual 77% drop in sulphur emissions can be achieved, which means a reduction of 8.5 million metric tonnes of sulphur dioxide per year globally. This will have a positive impact on quality of life in the communities of the port and coastal cities.”
SPAIN
IPCO buys Ingeniera de Procesos
IPCO has acquired Spanish company Ingeniera de Procesos SA (IdP), a supplier of processing equipment and spare parts, primarily to the chemical and sulphur industries. For the past 30 years, IdP had had an existing agreement with IPCO giving them the exclusive right to sell chemical and sulphur equipment in Spain based on IPCO’s steel belts and Rotoform machines.
“The acquisition is well in line with IPCO’s long-term strategy for profitable growth. With this, we strengthen our presence in the Spanish market and get access to a large installed base and direct contact with the customers”, says Johan Sjögren, Managing Director IPCO Equipment Division.
CANADA
Strategic Oil and Gas goes into receivership
Alberta-based Strategic Oil and Gas Ltd had gone into receivership after failing to agree a restructuring plan. The company owns gas wells in the Northwest Territory, including the Cameron Hills sour gas field, which is subject to ongoing end of life clean-up costs, including a remediation order because of leaks of hydrogen sulphide from the I-73 well. Strategic had installed a sour gas scrubber as a temporary measure prior to a permanent fix being in place by the deadline of April 1st. It is part of an ongoing issue for provincial authorities in Canada, where ‘financially fragile’ operators are trying to deal with the clean-up costs of spent oil and gas wells and oil sands patches, potentially amounting to billions of dollars. There is a continuing concern that companies will buy up good assets from struggling owners, leaving clean-up costs for the poor assets as a liability for the taxpayer.
UNITED STATES
Online platform for improved plant performance
ExxonMobil has launched an online platform called InFocus to help customers optimise plant performance, increase operational efficiency and minimise production interruptions. The company says that, using secure, near-real-time data, operators will be able to make faster, more informed decisions and collaborate more easily with ExxonMobil technical support. The platform has been tested and piloted with early adopters and has already been fully deployed in multiple facilities.
The platform provides two solutions; the predictive tool enables users to test the impact of feedstock and operational changes on lube product yields and quality. Developed from years of ExxonMobil expertise and experience, the tool can also be tuned to match actual unit performance, delivering valuable data enabling users to evaluate feed flexibility, optimise product mix and maximise operational value. The InFocus unit monitoring tool enables timely technical insights to improve process performance.
“Our customers are under increasing pressure to improve profitability and be more efficient,” said Dan Moore, president of ExxonMobil Catalysts and Licensing. “Our InFocus Platform will provide deeper insight into their operations and will enable concrete recommendations on ways to optimise plant performance and minimise interruptions.”
Plume suppression system for wet scrubbing
DuPont Clean Technologies has introduced a new steam plume suppression solution for its MECSDynaWave® ® scrubbers in sulphur recovery unit (SRU) applications. The Sennuba™ plume suppression technology employs two heat exchangers and a heat transfer medium to heat stack gas from the wet scrubbers that are used to remove pollutants from flue gases, with steam produced with the heat of the gas at the inlet of those scrubbers. This avoids the high operating costs associated with other methods of steam plume control, as it recovers otherwise lost heat from the process to generate the necessary steam to suppress the visible plume. Sennuba is designed with a heat transfer medium so there is no chance of leakage of the process gas directly to the stack gas. In this design, there is no forced circulation of the heat transfer medium.
Weir Minerals launches three new pumps
Weir Minerals has launched three additions to its Lewis® range of pumps and valves for the sulphur, sulphuric and phosphoric acid industries. The three pumps have been designed to maximise wear life in some of the most corrosive industrial applications while simplifying maintenance through their streamlined designs. This has significantly reduced the number of parts compared to previous pumps, without compromising their performance.
“Although they’re designed to address different challenges, these three new pumps were guided by the same core design principles: using advances in material technology to achieve increased performance and wear life, while reducing complexity to simplify equipment maintenance and give us the flexibility to deliver more engineered to order features that benefit our customers,” said Jerry Ernsky, Lewis product manager, Weir Minerals.
The first is the new Lewis horizontal process pump, which combines the corrosion and wear resistance of Lewmet® alloys with the robust performance, efficiency and ease of maintenance associated with centrifugal pumps. This single stage, end suction horizontal process pump is suitable for a wide variety of chemical processing applications.
The new Lewis VL Axial Flow Pump has heavy duty construction for use in corrosive, high temperature chemical processing applications such as evaporator and crystalliser circulation. Its innovative design can be customised to suit a wide variety of industrial applications, while its low component count makes servicing quicker and easier.
Finally, the Lewis vertical high pressure molten salt pump has been designed to meet the needs of the burgeoning concentrated solar power (CSP) industry. A multi-stage vertical turbine pump, it has been designed to handle the multifaceted challenges associated with the extremely high pressures and temperatures associated with pumping molten salt for thermal energy storage. It can be expanded from 3 to 14 stages, and has an integrated protective thermal barrier, a non-contracting shaft seal and a low NPSH first stage.
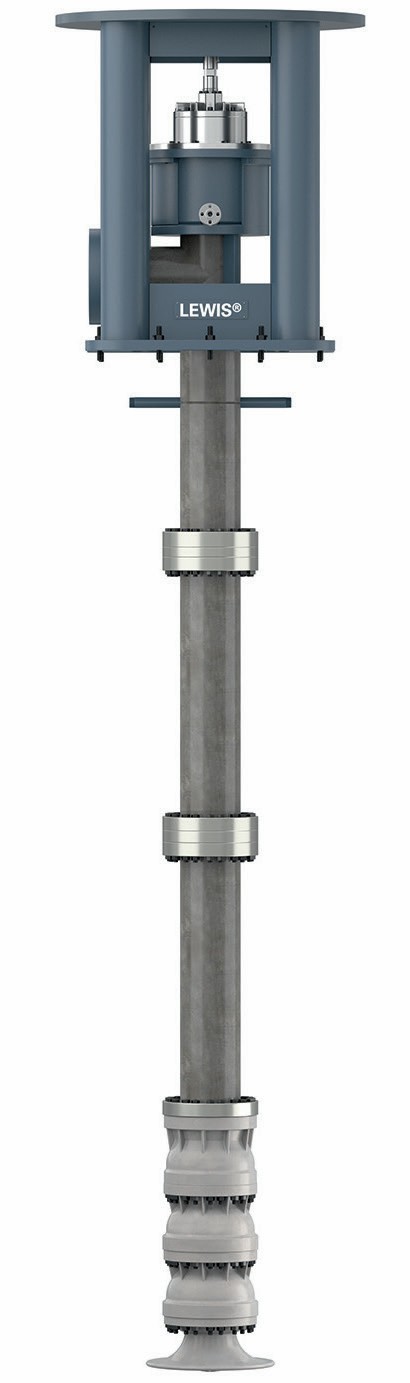
All three pumps are constructed with Weir Minerals’ Lewmet alloys, which incorporate specialised metallurgy designed to survive in the most corrosive industrial applications involving sulphur, sulphuric and phosphoric acids.
Alkylation unit contract awarded
DuPont has also been awarded the contract to supply Next Wave Energy Partners with licensing, engineering and proprietary equipment for a STRATCO® alkylation unit near the Houston Ship Channel in Pasadena, Texas, known as Project Traveler. In order to meet North America’s growing octane demand and desire for cleaner-burning gasoline, Next Wave commissioned DuPont to supply a 28,000 bbl/d alkylation unit from an ethylene feedstock. Start-up is targeted for mid-2022. STRATCO alkylation technology is a sulphuric acid catalysed process with over 100 units licensed worldwide and more than 915,000 bbl/d of installed capacity.
“DuPont is excited to provide Next Wave with our STRATCO alkylation technology in the world’s first stand-alone alkylation complex,” said Kevin Bockwinkel, Global Licensing Business Manager, STRATCO Alkylation Technology. Dan Fahey, Next Wave Vice President, Engineering & Technology, commented; “We value the relationship and technical contributions by DuPont over the last several years to progress our project to final investment decision.”
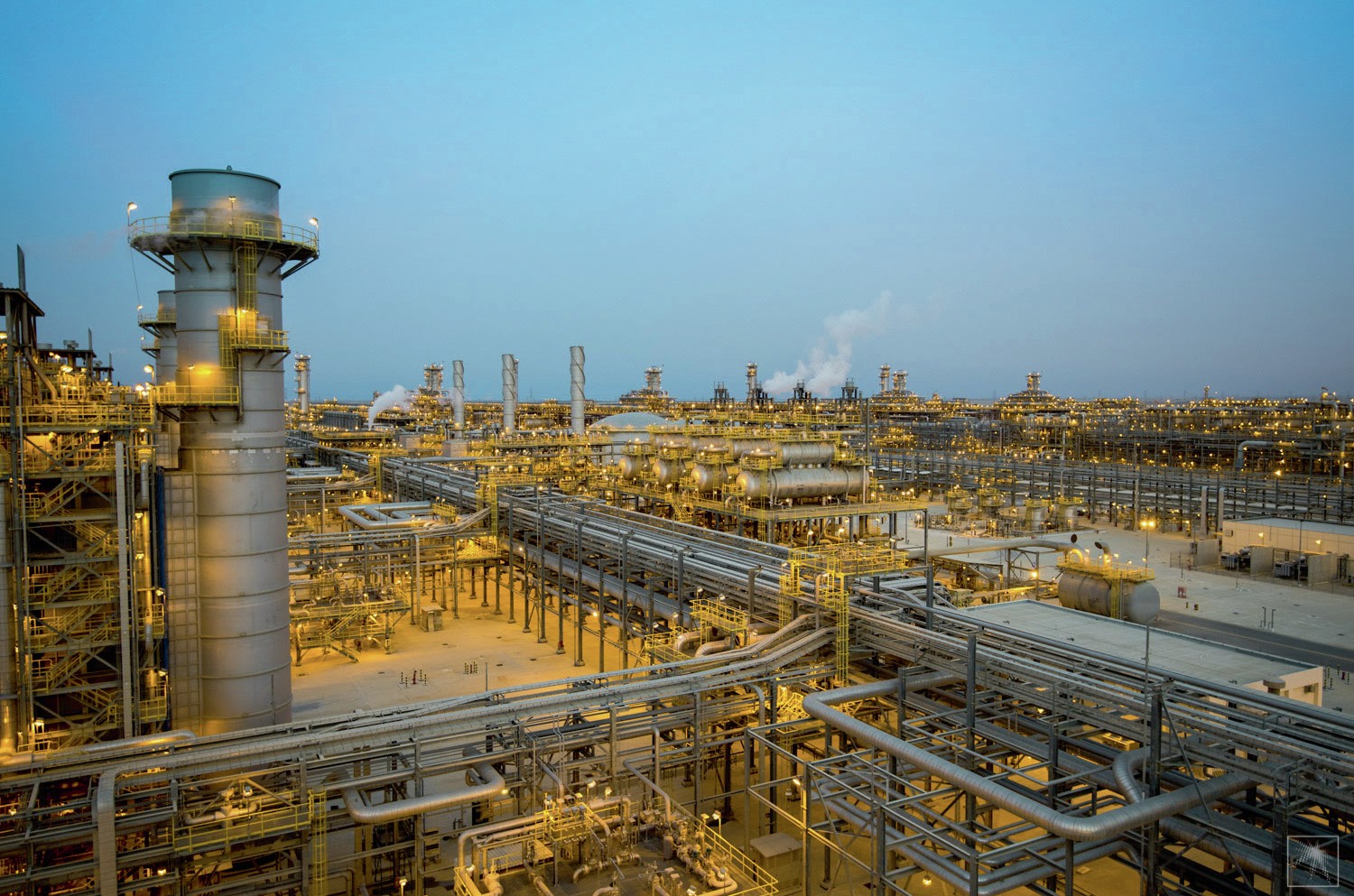
SAUDI ARABIA
Construction complete on Fadhili gas plant
Press reports say that engineering, procurement and construction (EPC) work on Saudi Aramco’s Fadhbili sour gas processing plant were completed in December 2019. The plan, located 30km southwest of the Khursaniyah gas plant in the east of Saudi Arabia, has been built at a cost of $6.5 billion. Tecnicas Reunidas built the central gas processing facility, and the utilities and interconnecting systems, with UK-based Petrofac constructing six sulphur recovery trains with associated facilities for sulphur and heavy duty oil handling, loading, unloading and storage, as well as a sour water stripper, flare system and waste water treatment plant. Pipelines and other utilities were built by Larsen & Toubro, Arkad Engineering & Construction, Denys Arabia and Al-Muhaidib Contracting. The front-end engineering and design (FEED) work was carried out by the UK-headquartered Wood Group, which was also the project management consultant.
When at capacity the Fadhili plant will process 2 billion scf/d of non-associated gas from the Hasbah offshore fields and 0.5 billion scf/d of non-associated gas from the Khursaniyah onshore fields to produce 1.5 billion scf/d of sales gas and 4,000 t/d of recovered sulphur.