Sulphur 388 May-Jun 2020
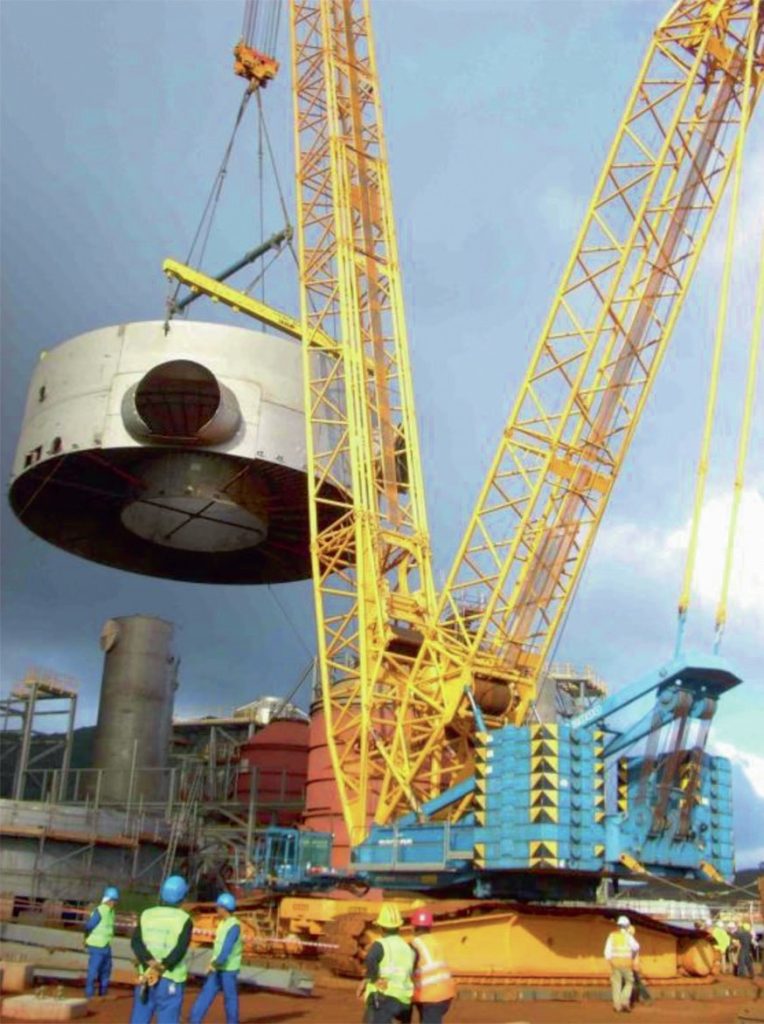
31 May 2020
Design challenges of mega acid plants
SULPHURIC ACID PLANT DESIGN
Design challenges of mega acid plants
What are the limits for future single stream sulphuric acid plant capacities? H. Storch, C. Bartlett, and S. Mohsler of Outotec discuss design considerations for large capacity sulphuric acid plants with reference to the world’s largest acid plants built to date.
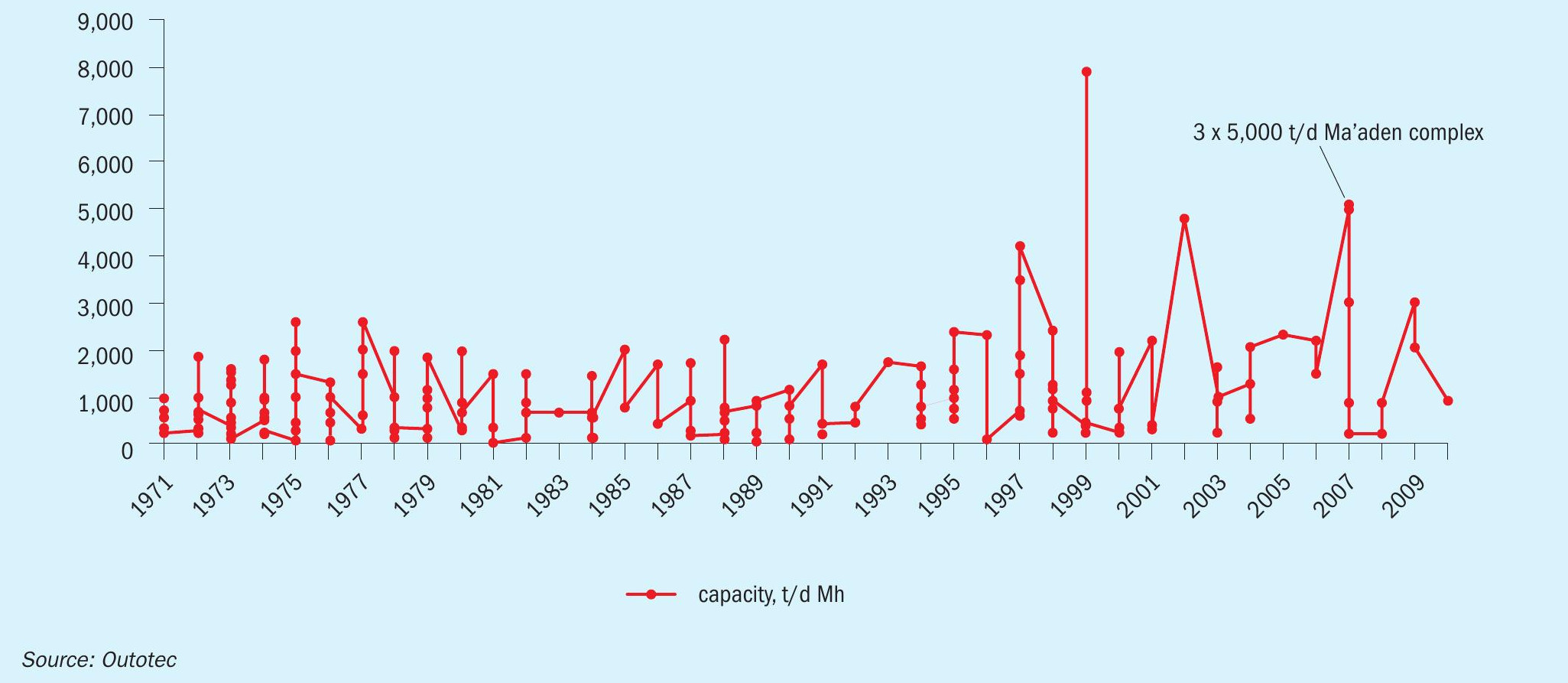
Historical data of the capacity of sulphuric acid plants built by Outotec within the last 40 years reveal a trend to larger capacity plants. Fig. 1 shows the capacity of Outotec designed plants since 1971, displaying an obvious growth in average plant capacity over the years.
Among the reasons for the upward trend are a general growth of project dimensions, e.g. mega fertilizer complexes such as the Ma’aden project, which have a high demand of sulphuric acid as a base component of the final product. Further reasons for the increase in requested plant size can be found in economic requirements based on the economies of scale. The cost impact of plant size cannot be considered to be linear, but rather follows a power function with exponents between 0.6 and 0.85, as shown in Fig. 2. This easily demonstrates why more and more plants are constructed with a larger capacity, as the specific costs are lowered.
Obviously, one main driver is economy of scale and even this goes in hand with certain operational limitations, the financial benefit of these “mega” plants triggered the industry to install such units. One prominent example for mega-plants is the Ma’aden/Saudi Arabia acid plant complex where three plants of 5,000 t/d capacity each have successfully passed their performance testing in 2012 and since then have been in operation at full capacity. These are the world’s largest single train sulphuric acid plants running at consistent capacity and thus can be regarded as state of the art for Outotec technology and the industry benchmark at large.
It has been noted that the industry is now asking for capacities beyond the proven 5,000 t/d capacity and Outotec as designer of such plants is of the firm opinion, that larger single stream capacities are possible. Yes, there will be technical challenges and some new thinking will be required, but some of the solutions for key issues are already invented and some of these aspects are discussed below. The level of digitalisation of such plants will also play a vital part of operational feasibility of this kind of plant.
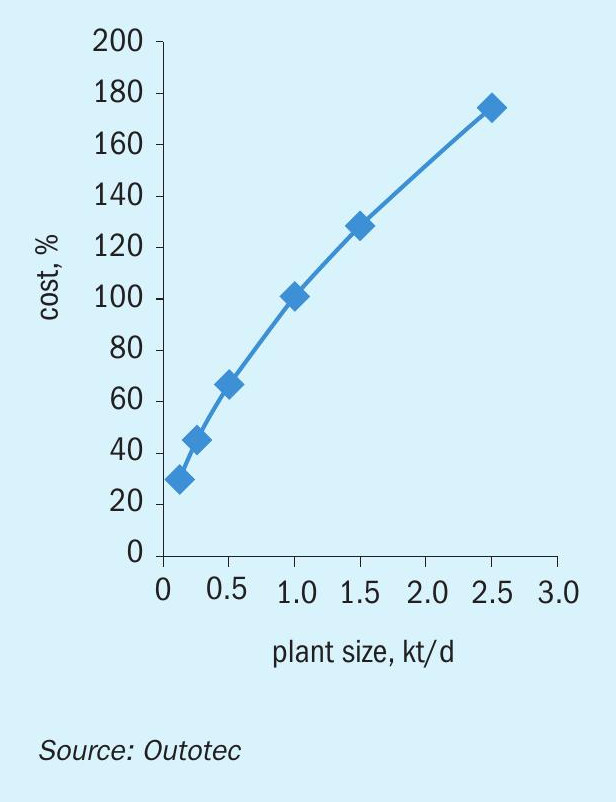
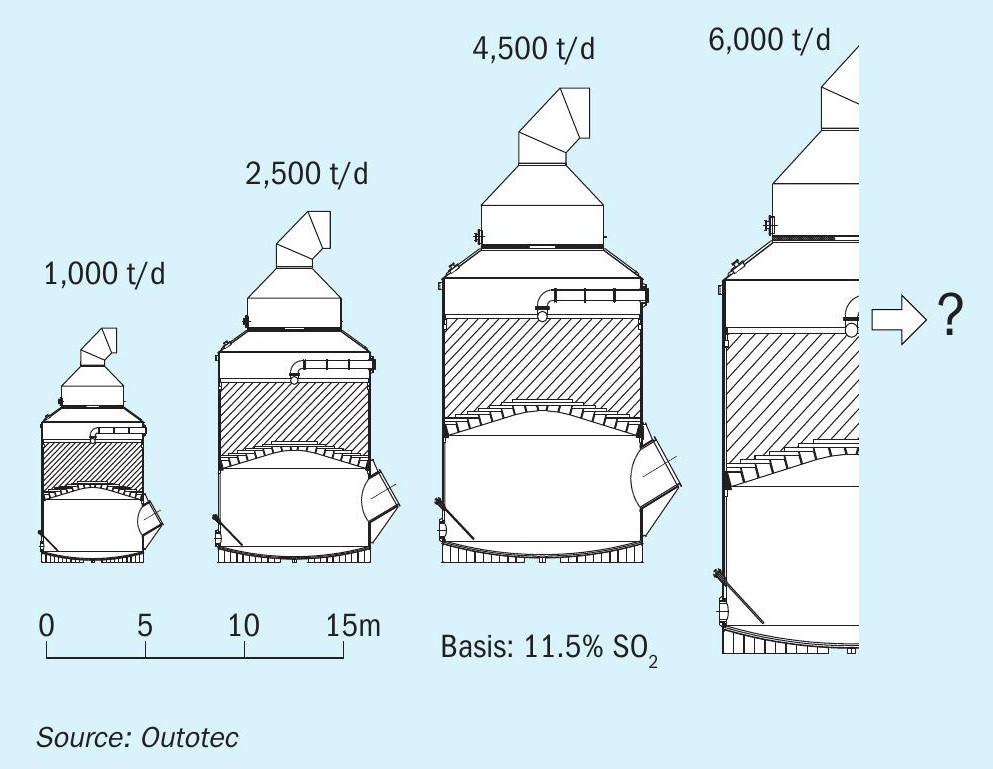
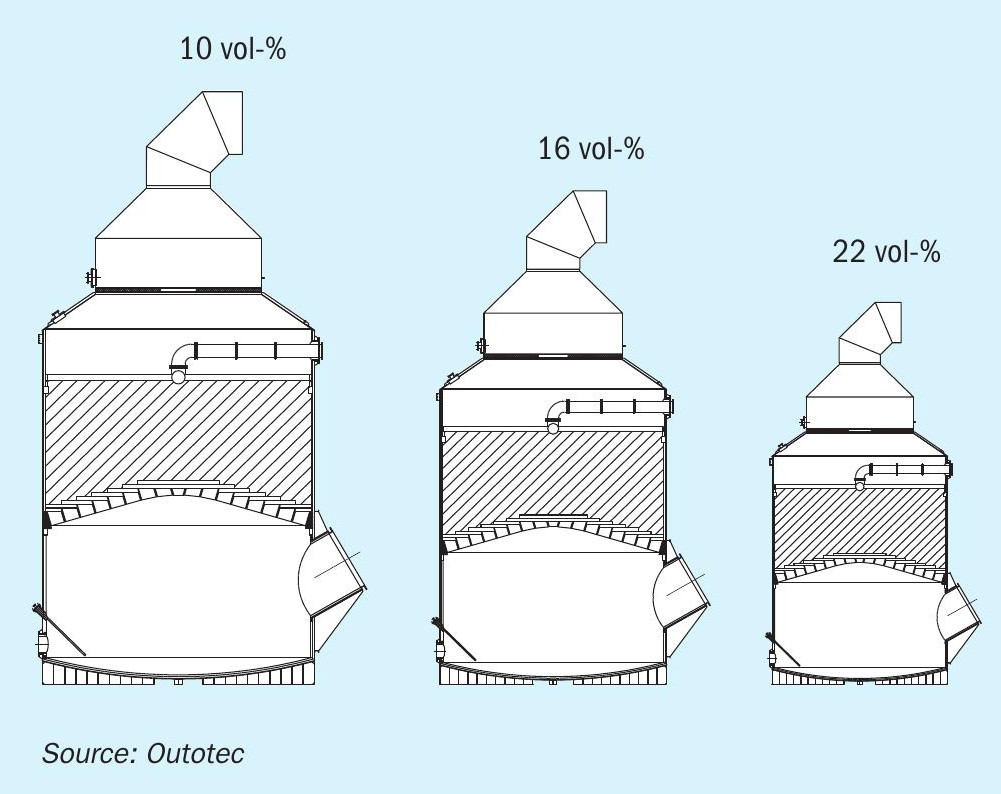
Process and mechanical considerations
The process design, as a first step, is the basis for the subsequent engineering phases and various project execution stages. With the process parameters fixed, it is possible to proceed with equipment sizing and design, which again impacts the following steps of construction, fabrication and transportation. Of course, there are limits to be kept in mind such as size limitations of certain equipment which essentially can be traced back to mechanical stability or gas and liquid distribution challenges. Another valid point is the changing characteristic of flow dynamics which can differ vastly for different equipment sizes. These issues are presenting a connection between process and mechanical design, which has to be in constant information exchange to prevent any of the aforementioned problems.
The initial challenges for even larger capacities are related to key aspects, such as gas distribution, mechanical integrity of equipment and ultimately OEM supply of process equipment, such as blowers, etc. There is however a secondary level of challenges that are not considered as the industry drives towards an ever lower investment cost per tonne of acid produced. These issues relate to the operability, turndown/ fluctuating load conditions, particularly relating to metallurgical acid plants, which historically have proven to be solved.
For the process design of sulphuric acid plants, two of the main parameters available to react to these requirements are gas velocities in the process equipment and ducts, as well as the SO2 concentration of the process gas. The effect of equipment dimension increase for different plant capacities is shown in Fig. 3.
Based on the trend to larger plants, it is shown how the size of e.g. an absorption tower is expected to evolve for larger capacity plants. It is obvious that there is a limit to equipment size increasing as a reaction to the increasing capacities requested. For further increases in capacity it might be necessary to adjust other process values or refine mechanical designs. As an example for mechanical design customisation, the number of gas inlet nozzles to the towers can be regarded as a variable. With increasing air flows it may be preferential to facilitate the gas distribution in the lower part of the towers by adding a second gas inlet nozzle. Further measures can include a design change to a combi-absorber, with a two-staged absorption, first in a venturi and then in a packed bed.
Fig. 4 shows the effect of changing one of the process design means available. With rising SO2 concentrations it is again possible to drastically reduce equipment sizes. Of course, not all the equipment in a sulphuric acid plant allow for such high SO2 concentrations, unless a special process is selected, such as Outotec’s LUREC™ process. Nevertheless, with the “standard” double absorption process it is at least possible to reduce equipment dimensions in certain plant areas.
Future considerations
When considering larger units, some restrictions must be observed, which potentially constitute major hurdles, but subject to the design, can be overcome. Some examples are discussed below:
There are no restrictions in the wet gas cleaning section, as multiple parallel units are already common practice in the industry.
Two parallel main SO2 blowers are currently used in large plants. Larger single blowers are available on the market and hence this is not a restriction to design larger capacity acid plants even beyond 8,000 t/d.
As the gas throughput increases with acid output capacity, the vessels, particularly the SO2 converter, will significantly increase in size. While the impact on the mechanical design of very large vessels can be managed using modern design tools, the uniform distribution of gas to the individual catalyst beds becomes a more challenging issue. Outotec’s radial flow converter with integrated heat exchangers is perfectly suitable for such enlargement in capacity. In Fig. 5 an outline of a modern five bed converter for processing of metallurgical off-gas is presented and the radial gas distribution from the centre to each bed is shown. Each of the converter beds is thus fed radially with the gas originating from the converter core. Thus the gas must not “travel” the entire diameter of the converter, as is the case with a conventional lateral gas inlet, but only the radius and hence the superior distribution quality. Nevertheless, in “mega” plants gas distribution is a challenge and that will become ever greater, requiring additional measures in the converter design.
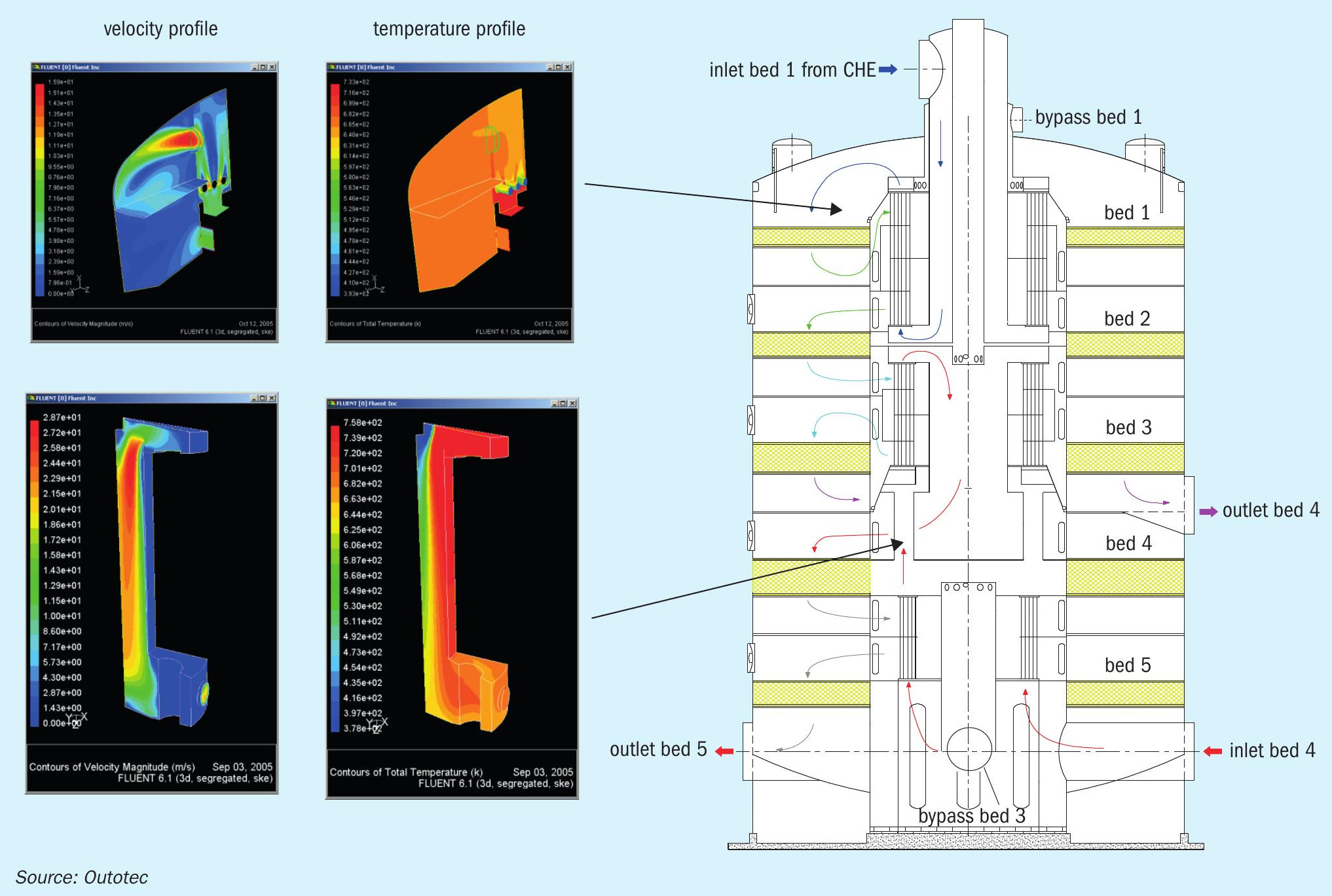
Large absorption towers of conventional design have been built up to 12 m diameter, which would theoretically be suitable for acid plant capacities around the 6,000 t/d level. However, also here the issue of uniform gas and liquid distribution becomes paramount.
While a variety of liquid distributors designs are available and well proven, the gas distribution has been widely disregarded as a critical issue in the past and was overcome by conservatively designed tower packing. CFD simulations have demonstrated that larger towers with high efficiency internals cannot tolerate the conventional single lateral gas inlet, even when this is split into two nozzles. Since the 1970s, Outotec has built a number of towers using the same principle as applied for the converter, i.e. radial gas distribution. Fig. 6 illustrates the schematic design of such a unit (the design can be one or two stage).
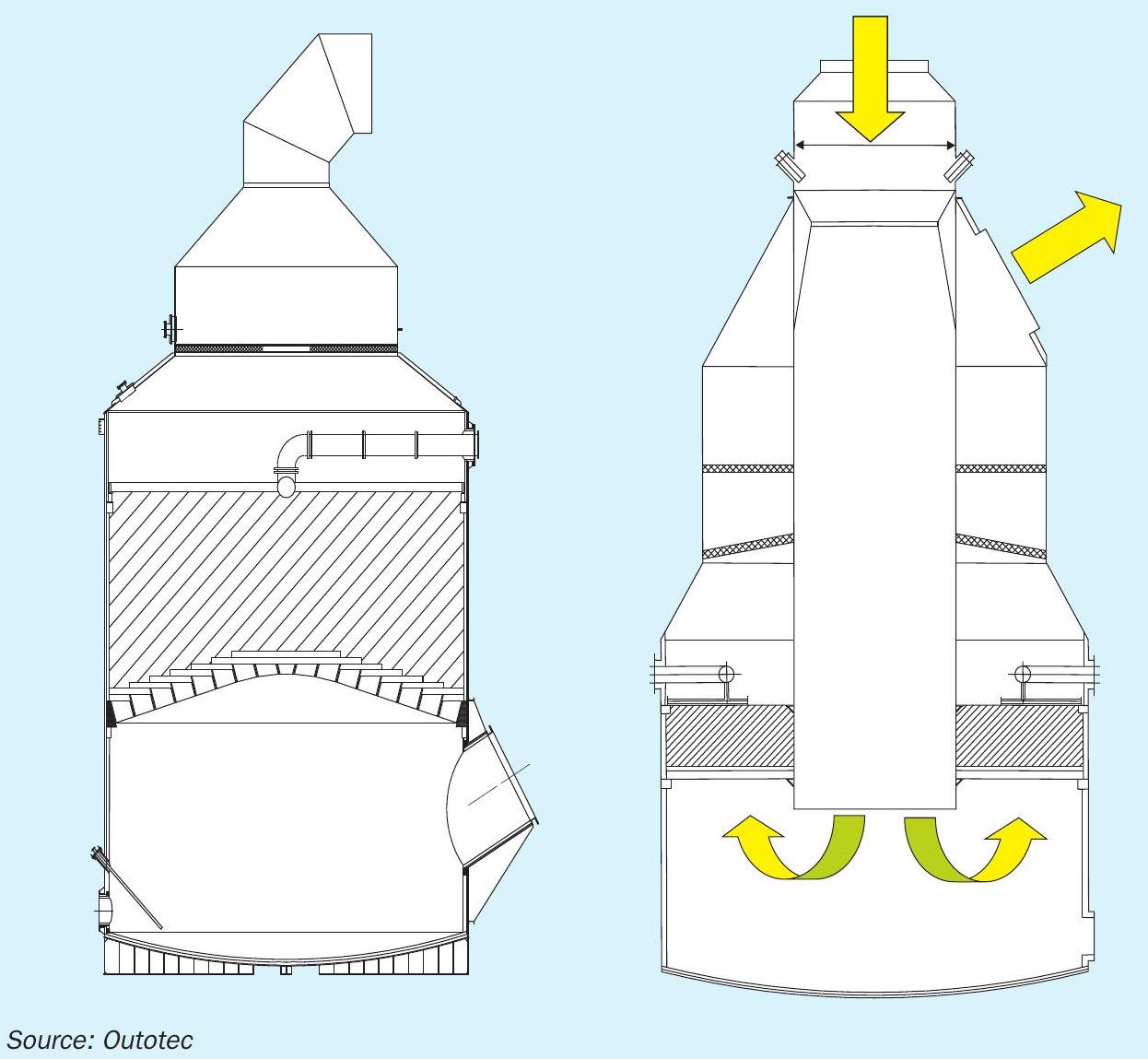
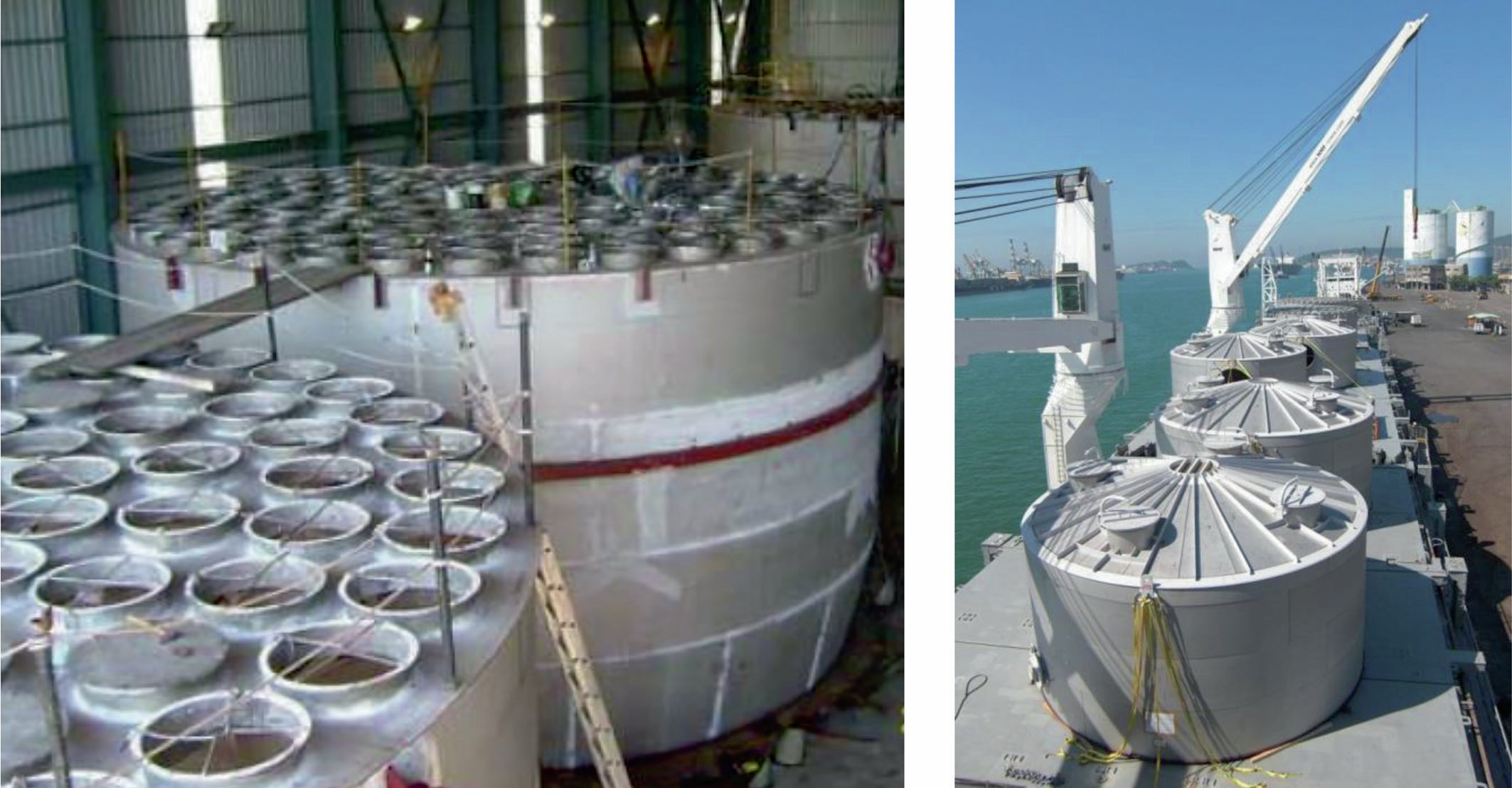
Fabrication, transport and construction
The degree of pre-fabrication of equipment generally has to be considered according to the final equipment size, weight and plant location (including cost/availability of logistics).
Pre-fabrication is often limited by the size of equipment parts, in order to still allow for later transport to site. Fig. 7 shows the shop fabrication of the upper part of absorption towers including the candle filter tube sheet, with transportation to site after being joined with the upper part of the towers.
Another aspect apart from size and weight limitations for transport to be considered when prefabricating equipment, is the decrease of structural integrity with growing equipment dimensions. It is often necessary to include additional reinforcements for the transport and construction phase to maintain the exact equipment dimensions, e.g. the sphericity as shown in the converter construction in Fig. 8.
Generally, it should be considered that fabrication tolerances increase with increasing part dimensions. This fact might lead to a higher workload on site when parts to be joined are at their tolerance extremes and need additional site fitting to allow for the proper erection of the equipment. Further aspects of large prefabricated equipment include higher cost for transport due to oversized loads and exceptional convoys, as the equipment is usually not fabricated in the country of destination.
Many plants are situated at locations without a direct connection to freight ports, further adding to the transport/logistical costs. Longer transport durations are therefore to be expected compared to shipment of semi-finished products, which might fit into standard transport containers. This time critical aspect needs special attention, particularly in connection with lead times of material which is needed for the preceding fabrication step.
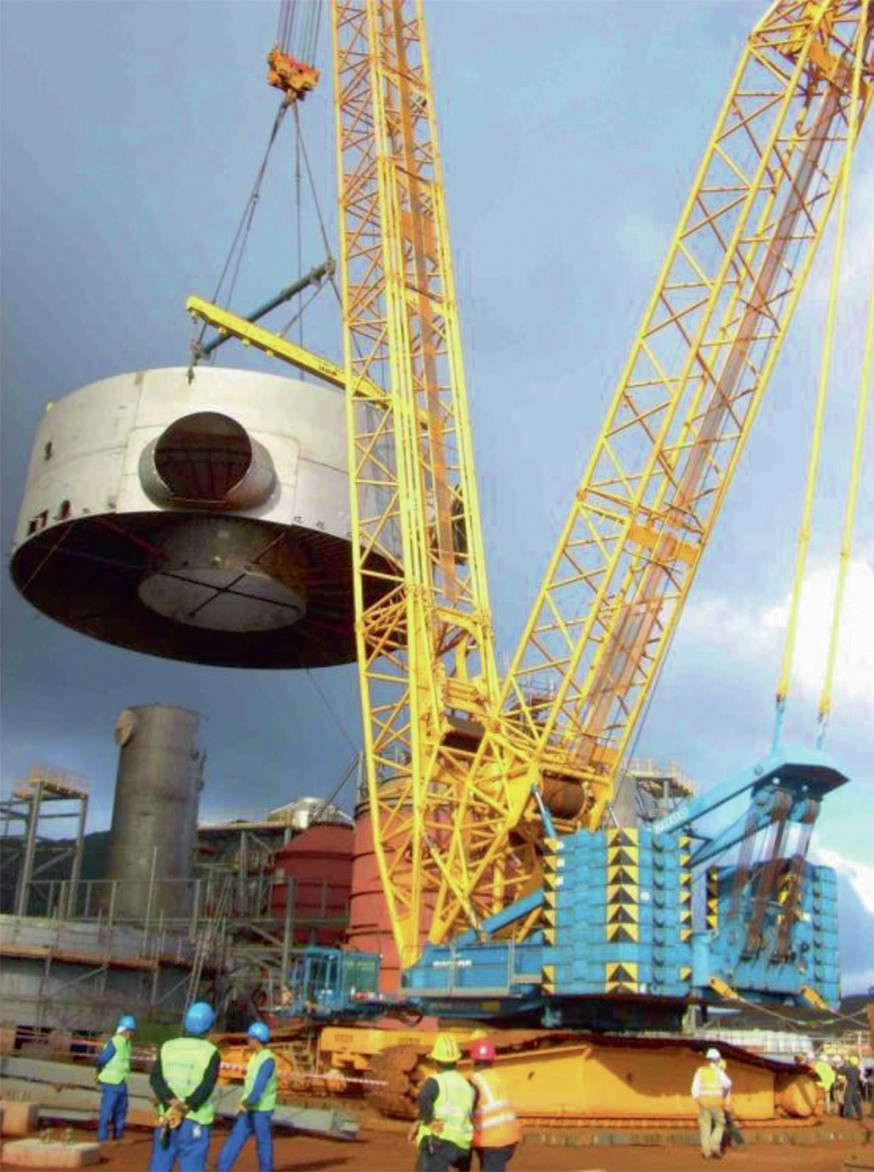
All these arguments seem to indicate that on-site fabrication is superior to prefabrication of equipment, but it has to be taken into consideration that often a lack of skilled workers is to be expected on site. Together with missing or inferior production facilities this may lead to quality deficiency or time losses due to e.g. repetition of faulty work. The availability of supervisors and skilled workers for mega projects is often above normal standards due to the impact and importance of such projects for the plant supplier. That said, there is competition between plant suppliers within the complex development for the best resources. Prefabrication and site work must therefore be carefully balanced according to existing experience to maximize the benefits arising from these two approaches.
Summary
In summary, Outotec is of the firm opinion that the current largest units with 5,000 t/d capacity do not constitute a limit for future single stream acid plant capacities. Obviously certain design principles will need to be re-introduced into the sulphuric acid industry, but lots of the required elements are already available. If the market demands the next generation of “new mega” plants, plant designers will be ready to offer this next step in technological development.