Fertilizer International 496 May-Jun 2020
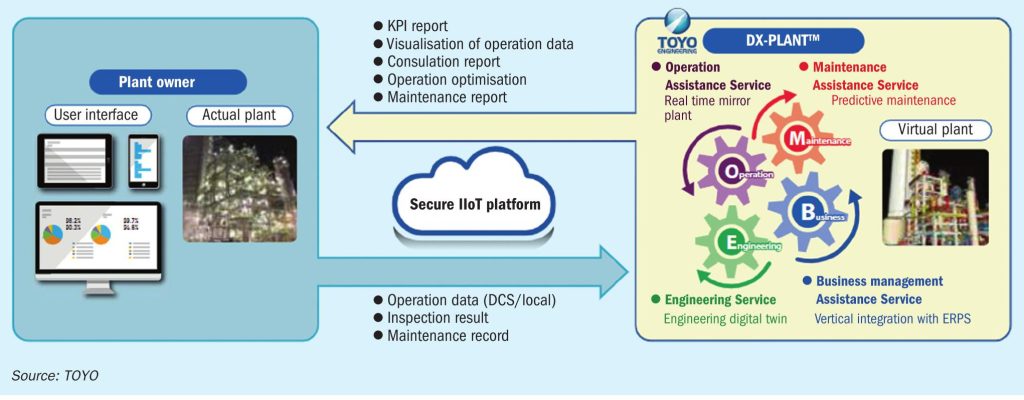
31 May 2020
Digitalisation and big data
PRODUCTION TECHNOLOGY
Digitalisation and big data
Digitalisation and the analysis of big data are playing an increasing role in fertilizer production. Innovative digital and cloud-based services are being offered by a range of technology companies, including Casale, tkIS, Topsoe and TOYO.
Chemical plants generate huge amounts of data every single day. Raw data needs to be analysed and converted into useful and actionable knowledge to get the full benefit from this wealth of information. Most of the time, however, only the most critical and prominent performance indicators are generally analysed by plant operators due to lack of internal resources and/or specific expertise.
Fortunately, digital technology now exists to capture, transfer and analyse huge amounts of data. This transition from the analogue to the digital – digitalisation – is opening up new opportunities for chemical plants, such as remote plant monitoring, remote plant operation and the real-time interpretation of plant data.
A raft of new digital technologies are currently being introduced by businesses as part of the so-called fourth industrial revolution – also known as ‘Industry 4.0’. These include the internet of things (IoT) artificial intelligence (AI), machine learning and cloud computing.
One digital innovation in particular – the IIoT (industrial internet of things) – holds great potential for the chemical industry. Cloud-based IIoT systems, when securely connected to chemical plants, can generate algorithms for process optimisation and predictive maintenance.
In this article we report on the digital services being offered by a number of leading technology providers to the fertilizer industry. These are designed to improve both plant efficiency and reliability.
TOYO’s digital approach –DX-PLANT™
TOYO believes the IIoT will be at the core of the fourth industrial revolution that looks set to usher in a range of exciting new changes to the way fertilizers and basic chemicals are manufactured. The Japanese company – a leading global engineering contractor and urea process licensor – has developed a system for the digital transformation of plants known as DX-PLANT(Nitrogen+Syngas ™ 360, p50). This system leverages TOYO’s unrivalled engineering expertise in chemical process technology and industrial plant operations. DX-PLANT™ is designed to maximise customer revenues and minimise their costs. It achieves this by providing services via a secure digital platform (Figure 1).
DX-PLANT™ works by creating a ‘digital twin’ – a virtual plant synchronised with an actual plant – based on big data captured from industrial plants. The DX-PLANT™ system enables TOYO to provide services and solutions to plant operators in four specific areas (Figure 2):
- Engineering (E): information management via an engineering ‘digital twin’. This 3D model platform uses augmented reality (AR) and virtual reality (VR) applications.
- Operations (O): this offers real-time process prediction/optimisation, including plant conditions monitoring and anomaly detection, using both real instruments (for pressure, temperature, flow etc.) and ‘soft’ sensors.
- Maintenance (M): this substitutes conventional periodic maintenance at set times with a more responsive conditions-based digital maintenance regime. Maintenance frequency and intervals are set by real-time monitoring and the prediction of abnormal conditions, for both rotating machines and static equipment.
TOYO offers a corrosion simulator, online ultrasonic (UT) monitoring and online metallic ion (Fe, Cr and Ni) monitoring as part of its digital maintenance package.
- Business (B): this company-wide approach combines corporate and factory management using stored operation and maintenance information. This service integrates DX-PLANT™ with enterprise resource planning (ERP) and asset performance management (APM).
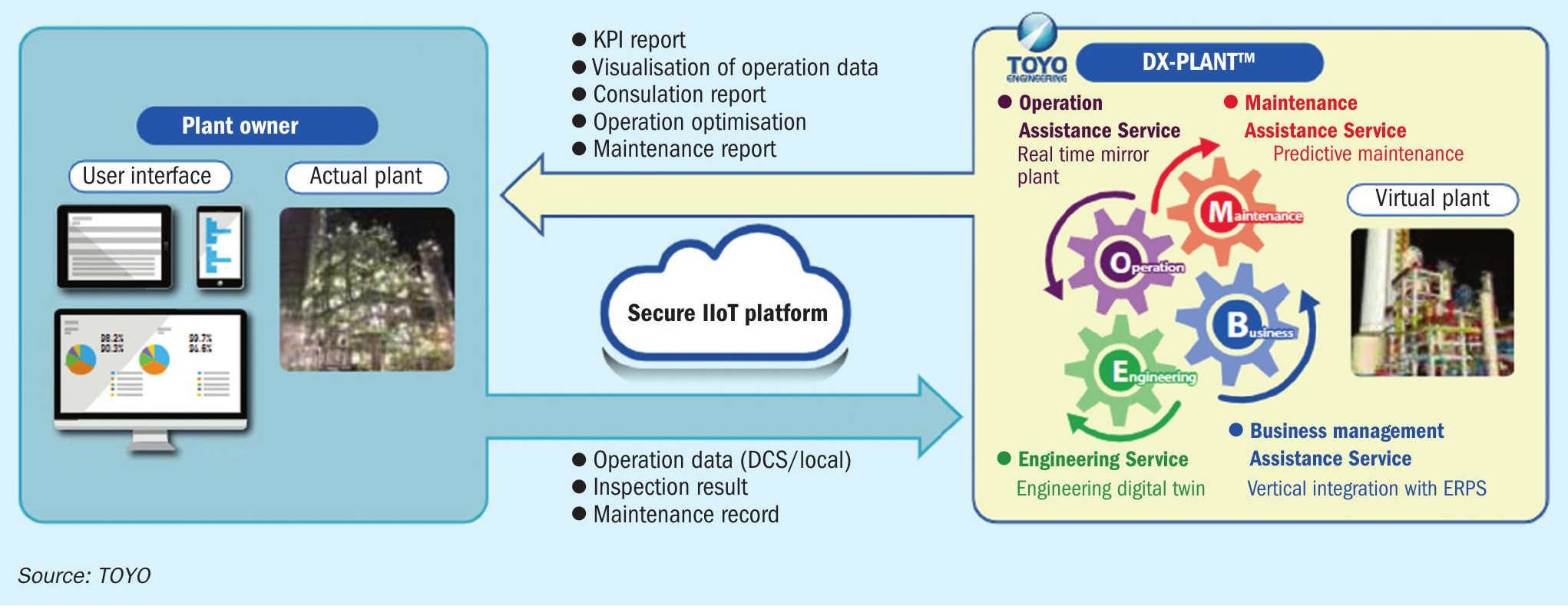
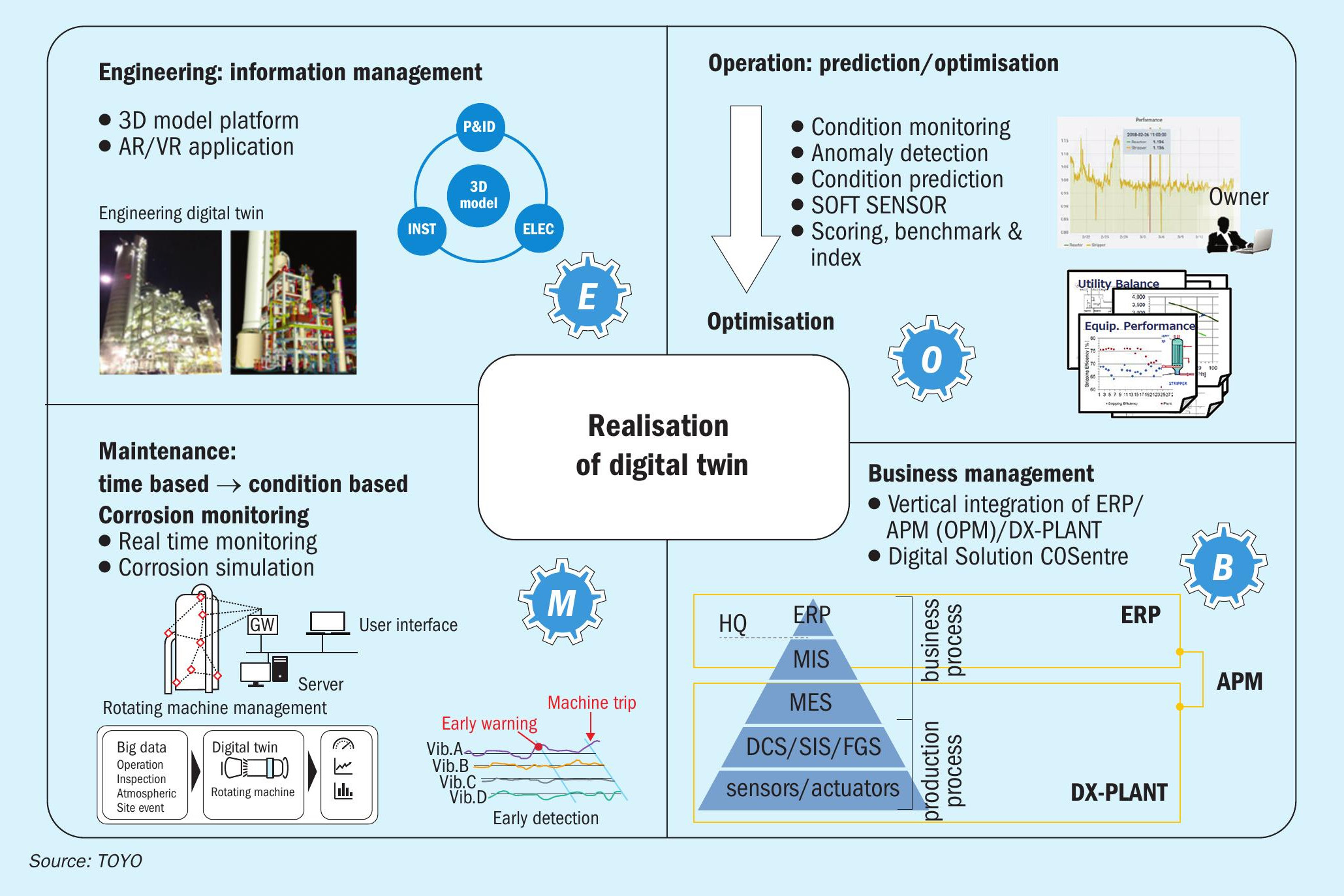
TOYO began development of DX-PLANT™ in November 2016 in collaboration with GE (now Baker Hughes, a GE company). TOYO’s system was originally based on an evolution of GE’s Predix cloud-based platform for industry.
However, following a dialogue with several plant owners – and to help satisfy end-user requirements – TOYO decided to expand the DX-PLANT™ line-up by developing its own self-made and in-house additions to the existing GE Predix platform. These new add-ons allow end-users to modify the system. This flexibility is valued, according to TOYO, as it permits clients to adapt and manage DX-PLANT™ more easily.
Further development of DX Plant™
TOYO launched DX-PLANT™ on the market in December 2017 by installing the system at the operations of Indonesian urea producer PT Pupuk Sriwidjaja Palembang (PUSRI). Further deployments of DXPLANT™ are imminent at several other plants during the next phase of its development, Looking ahead, TOYO plans to expand DX-PLANT™ applications to encompass other types of petrochemical plants and other industries. TOYO also intends to establish a ‘Digital Solution Centre’ once several plants are connected on the DX-PLANT™ platform. By connecting together multiple plants, this will provide a total solution to end-users. TOYO’s believes its integrated IIoT-based service sets a new benchmark for fertilizer plant governance.
tkIS – big data analysis at ammonia-urea plants
The control of manufacturing plants via a mobile phone is not generally the aim of fertilizer producers. Yet mobile devices do enable engineering employees to access plant data from remote locations so they can check the plant’s status and provide recommendations to operators inside the plant.
The same plant data being selectively accessed by production workers on mobile devices could also be transmitted as a whole to a process licensor like thyssenkrupp Industrial Solutions (tkIS). Such licensors have the necessary technology know-how and expertise to analyse and interpret the plant data and generate a detailed report about the status of the plant. These reports can provide fertilizer producers with recommendations and targets for improving plant reliability, increasing production or improving energy and water efficiency.
tkIS has experience and expertise in big data analysis covering several industries (Nitrogen+Syngas 354, p32). This has enabled the German engineering giant to improving plant performance and output for their customers, and solve specific process problems on their behalf. thyssenkrupp’s approach to big data analysis has been successfully tested at an ammonia-urea plant in Egypt. Based on the positive results obtained, tkIS says it will continue offering analytical services for process data to its own customers – and expand this to include other ammonia-urea plants that use third-party technology.
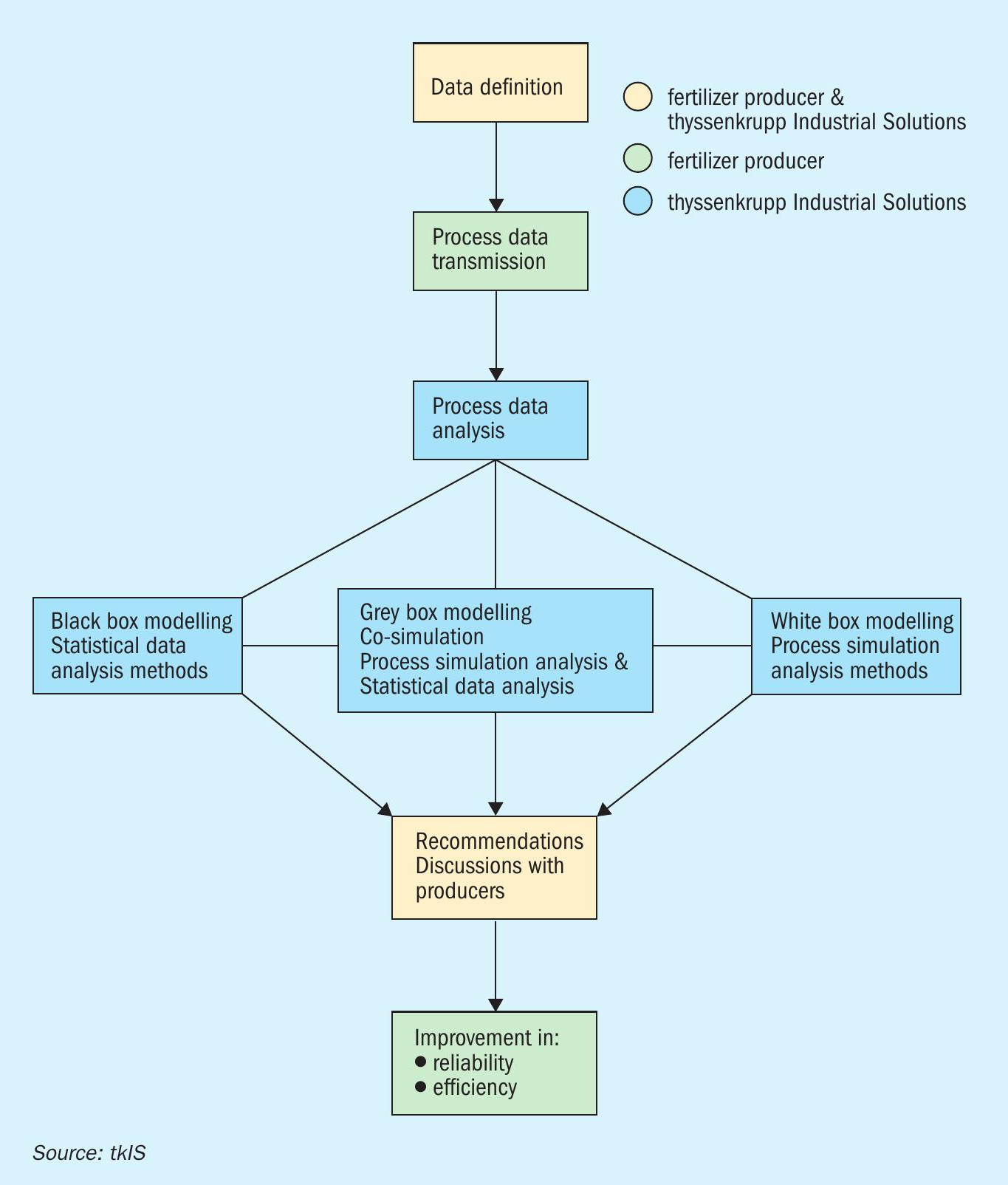
tkIS offers several options for big data analysis at industrial plants (Figure 3):
- White box modelling: a detailed plant simulation (e.g. Aspen Plus® ) collates and interprets a large amount of process data from the plant and uses this to create a ‘digital twin’.
- Black box modelling: this is a process simulation carried out without any deep knowledge of the plant. This approach can also be used for process optimisation and to detect process abnormalities It can also set targets in terms of efficiency and reliability, e.g. by finding critical parameters which might cause a plant to trip and so prevent this from happening.
- Grey box modelling: This third option for plant analysis is a co-simulation that combines both white and black box modelling approaches. The results of the detailed plant simulation, run to match the real-time plant data, are transferred back into the process simulation.
ClearView™ from Topsoe
The ClearView™ software system offered by Topsoe is based on the automatic upload of plant operating data to an IIoT platform (Figure 4). This system is designed to help ammonia producers harvest data and realise the full potential of their plants. ClearView™ creates a ‘digital twin’ of the ammonia plant in the cloud and uses this to provide plant personnel with best-practice knowledge on a daily basis (Nitrogen+Syngas 360, p46).
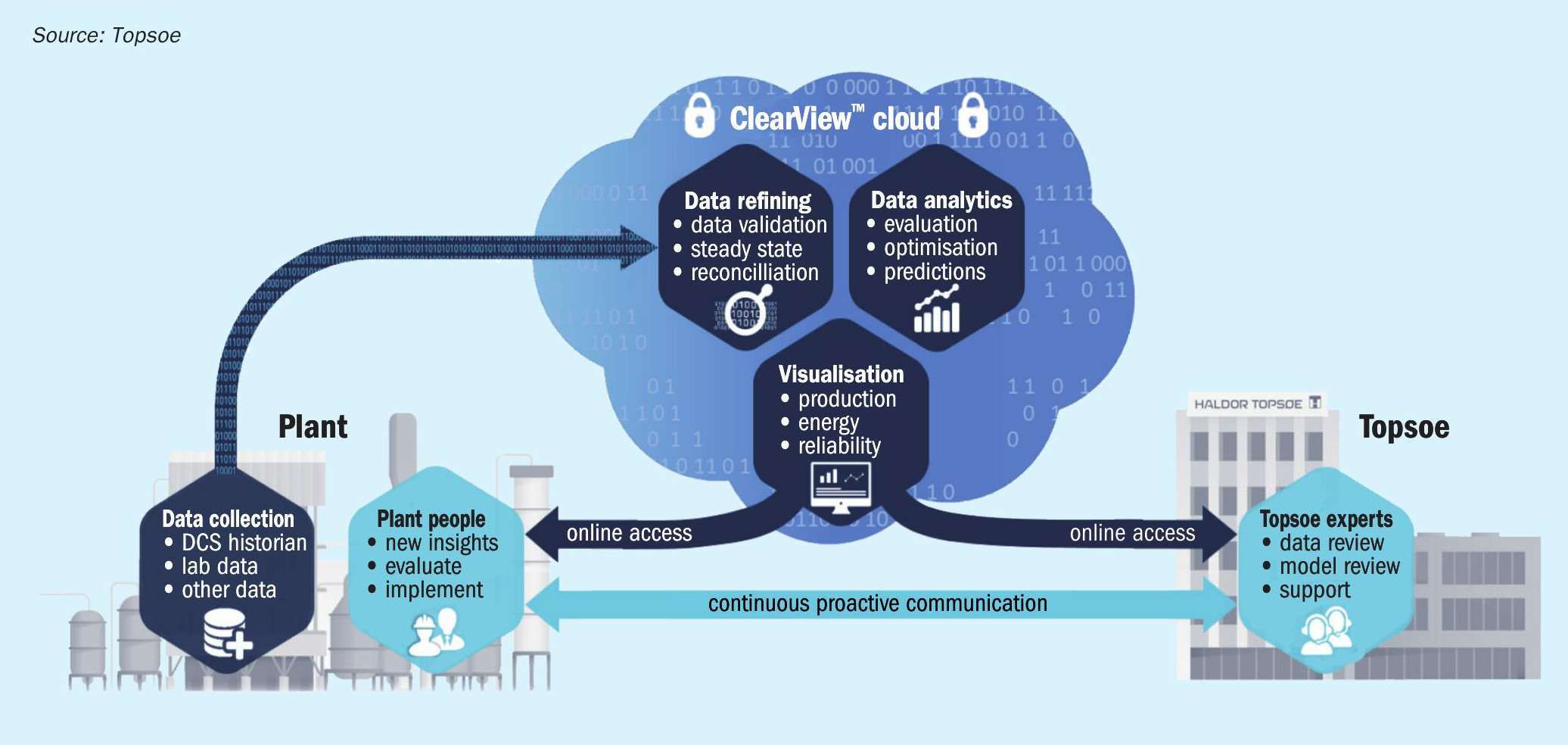
ClearView™ combines data validation with cloud-based simulation tools and data analytics software to evaluate and optimise plant operations. The system also benefits from a vast library of technical information held by Topsoe. This includes rigorous proprietary models, deep domain knowledge and the company’s extensive experience of catalysis and process design.
The results obtained from ClearView™ are visualised through online dashboards, these giving plant personnel a clear overview of how to optimise plant operations. The dashboards show, for a given operating variable, shortfalls between the current level and the optimal setting for that variable. Optimisation is achieved by monitoring catalyst and equipment performance, and by tracking and improving the plant’s overall key performance indicators (KPIs). Additionally, an early event detection feature helps to avoid downtime from unplanned outages. The software is easy to use and does not require extensive training.
The online dashboards are designed to deliver up-to-date information and insights directly to the relevant personnel. Usefully, they can be customised to match the roles and responsibilities of particular staff. They can provide the CEO and plant manager with a summary of the plant’s overall status and KPIs, for example, or show at-aglance alerts for the daily shift engineer, or give a more detailed optimisation update to the technical department. Plant performance data is also monitored by Topsoe experts so they can provide continuous support to plant personnel. This helps company engineers to pursue optimisation opportunities, and respond to reliability-related alerts, as early as possible.
The best practice guidance, background information and theory embedded in Clear-View™ software can also be used to develop the competency of operators and engineers. The software can give less experienced personnel a more fundamental and better understanding of how the plant operates.
What ClearView™ can do
ClearView™ is able to identify achievable opportunities for plant optimisation. The software flags up what operating parameters need to be adjusted (feedstock parameters, production output, energy consumption etc.) for the plant to reach optimum performance. It also provides short-term monitoring of plant performance and health, e.g. by detecting hydrocarbon cracking, condensation on catalysts, large exchanger leaks etc. Similarly, it can also monitor long-term performance degradation issues such as catalyst deactivation, equipment fouling, pressure drop, turbine inefficiency etc. In doing so, the software avoids costly downtimes by detecting and solving process issues before they become critical.
Topsoe-Honeywell alliance
Topsoe has entered into a strategic alliance with Honeywell, a company with considerable expertise in developing software for the oil and gas industry. Honeywell already provides cloud-based software services – Honeywell Connected Plant Services – to more than 70 refinery units globally. Topsoe’s ClearView™ service uses the same IIoT platform and user interface as Honeywell. The lessons learned by Honeywell from the first 2-3 years of commercial operation of its platform are also being incorporated into ClearView™ . This will allow Topsoe to improve and maximise the service offered to its ammonia and syngas plant customers.
Easy implementation and low maintenance
Topsoe offers ClearView™ to its customers as a complete end-to-end service. This removes responsibility from plant operators for implementing and managing a large, complex IT project. The hassle of maintaining models, software and IT infrastructure is also avoided. Everything related to system maintenance, migration, updates, backups and recovery is covered by the ClearView™ service.
Time and plant resources are also saved as only a limited on-site commitment and no large initial investment is required to get the service up and running. This enables plant personnel to instead focus on the information and support provided by ClearView™ and take full advantage of the service offered.
ClearView™ is kept up-to-date and its functionality maintained by continuous improvements to the online dashboards and underlying calculations. The latest enhancements are provided through online updates as they become available.
Innovative digital solutions from Casale
Casale has developed two best-in-class digital products for industrial plant operations. Casale remote engineering services (CARES) analyses and interprets plant operating data to enhance its value. Model predictive control (MPC), meanwhile, is a real-time advanced control system for improving plant performance (Nitrogen+Syngas 354, p32).
Both digital products are built around customer needs. CARES allows operators to remain the pilot of their plant, combining full control of operations with expert advice from Casale at their disposal. Casale’s fully automated MPC system, in contrast, is essentially a trusted auto-pilot that offers maximum plant performance at all times. Both CARES and MPC can be applied to any fertilizer industry process and methanol production.
Casale remote engineering services (CARES)
CARES is an innovative digital offering designed to help plant operators and managers achieve their daily production targets – by boosting plant production or minimising consumption and emissions. CARES employs sophisticated numerical methods and proven proprietary simulation technology to provide the following benefits to plant owners:
- Operational advice from Casale experts on improving plant performance.
- Better performance indicators for the whole plant and for single equipment items.
- Prevention of shutdown and equipment failures by early detection of malfunctions.
CARES acts as a personal advisor for operators when they troubleshoot process upsets. When looking at the operational data, it can also advise operators on when to carry out mechanical inspections, as part of a pro-active maintenance programme. Monitoring the close relationships between process operations and mechanical reliability is one of CARES key functions and main priorities.
In-depth analysis of plant data by CARES creates a ‘virtuous circle’, according to Casale. Raw plant data are processed at the Casale Data Center – where it gets cleaned, corrected and augmented – creating valuable information that is then placed at the disposal of clients.
“One of CARES main strengths is that it combines the digital and the human – by integrating powerful algorithms with the experience of Casale’s team.”
One of CARES main strengths is that it uniquely combines the digital and the human – by integrating powerful algorithms with the experience of Casale’s team. The service is based on four separate components (Figure 5):
- Data transfer: This takes place between the plant and the Casale Data Center via a modern seamless one-way connection. This allows plant operators to profit from the plant data without compromising operational security.
- CARES Analytics: the raw plant data undergoes deep and professional analysis to reveal its true value. This is accomplished through the uses of proprietary thermodynamic and kinetic models. Data robustness is enhanced (by mass and e nergy data reconciliation) to reduce the effects of measurement errors or lack of instrumentation. A meaningful and unique set of key performance indicators (KPIs) is computed – these being tailored to each plant and individual customer needs.
- CARES Monitoring: CARES is much more than a remote monitoring software – it offers a true remote engineering service. Behind the scenes, a dedicated team of Casale engineers closely monitor plant performance. Monitoring is followed up by the necessary next steps arising from the data analysis, with suggested actions encompassing plant optimisation, proactive maintenance or troubleshooting.
- CARES Reporting: The ability to provide the plant’s operational team with effective feedback is an essential function of a remote engineering service. CARES does this by offering two-fold reporting. Firstly, a web dashboard provides a quick and effective visualisation of plant performance. Secondly, reports issued to operators on a regular basis provide a much more detailed engineering analysis. The dashboard comes equipped with ‘assistance chat’. This allows operators to immediately link up with Casale specialists, whenever necessary. On top of this, conference calls are also regularly organised for in-depth discussion of process optimisation. Finally, plant events, such as extra-routine operations, are recorded and tracked in chronological sequence by the system’s ‘plant event notification’ interface.
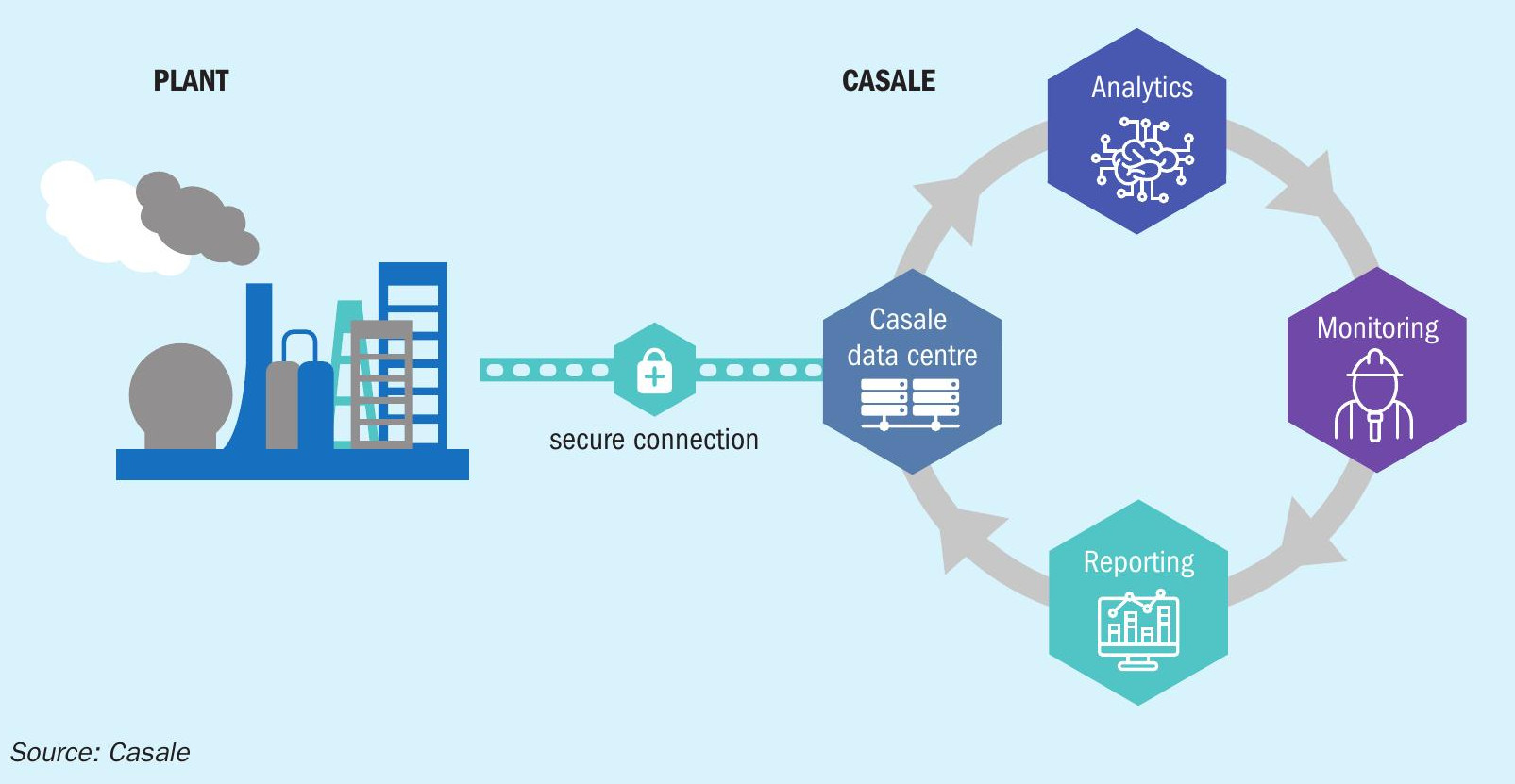
Model predictive control (MPC)
Casale’s model predictive control (MPC) system was developed in response to a growing demand from plant operators to increase production, maintain stability, and reduce energy consumption and emissions.
Even the most experienced operator is not able to adjust plant parameters rapidly enough to respond to plant fluctuations or external disturbances. As a result, plants are often operated far below their maximum achievable performance.
According to Casale, MPC “pushes the process out of the comfort zone of the plant operators”. The aim is to move the plant as close as possible to its optimum performance – while always respecting operating limits/constraints, particularly process and mechanical safety.
MPC is an automated system that complements the plant’s distributed control system (DCS). MPC continuously calculates the optimum set point of a number of chosen variables to keep plant performance at maximum at all times. Once stabilisation is achieved, MPC can safely push the plant’s performance, achieving higher production while reducing its energy consumption.
By partnering with accomplished and recognised software providers, including Honeywell, Yokogawa and Rockwell Automation, Casale is able to offer a dedicated MPC product for all fertilizer industry process technologies.
MPC is able to interpret the complex phenomena observed in fertilizer plants by incorporating customised thermodynamic and kinetic models. Fertilizer plants – including those used to produce urea, melamine, nitric acid, ammonium nitrate, ammonia, etc. – exhibit large recycle streams. These affect the performance of the synthesis section and the operational stability of the plant.
MPC has been designed to handle these strongly non-linear types of system, being able to identify and target the optimum values of critical process control variables. These optimum values are not steady-state figures. They dynamically change at each plant, depending on the real-time capabilities of the recycling system. MPC pays attention to each and every need of an operational plant at any time. It therefore offers a highly efficient service without any real compromises.