Nitrogen+Syngas 365 May-Jun 2020
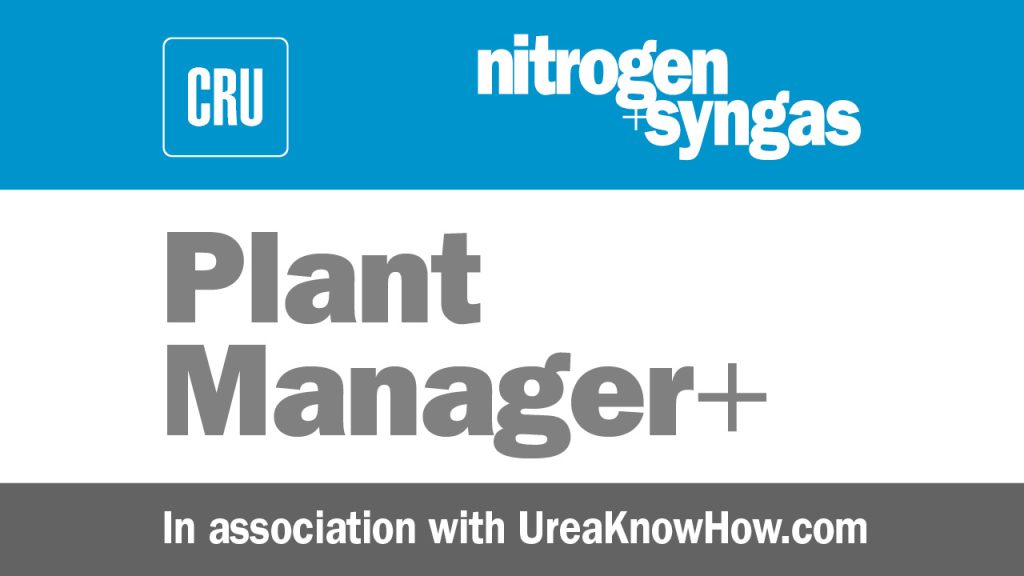
31 May 2020
Problem No. 60: Urea process passivation and heating rate
A Stamicarbon urea plant attempts to start up after a scheduled turnaround. Due to maintenance issues, it is necessary to shut down and block in the synthesis section several times. Although licensor’s procedures have been followed, several signs of active corrosion are noticed in the liner of the reactor. What could the cause be for this unexpected behaviour? Can sharing experiences from colleagues from other urea plants provide valuable support to find the root cause or even provide new insights into possible new causes? One observation is that the typical heating up rate of a liner in a reactor is much higher than recommended (refer to diagram). The condensation heat of steam heats up the liner much faster than the carbon steel pressure bearing wall. This creates stress on the liner and affects the lifetime of the liner. Another observation is a temperature rise in the reactor during a blocking in situation. This can be a cause for loss of oxygen required for passivation, resulting in higher corrosion rates.
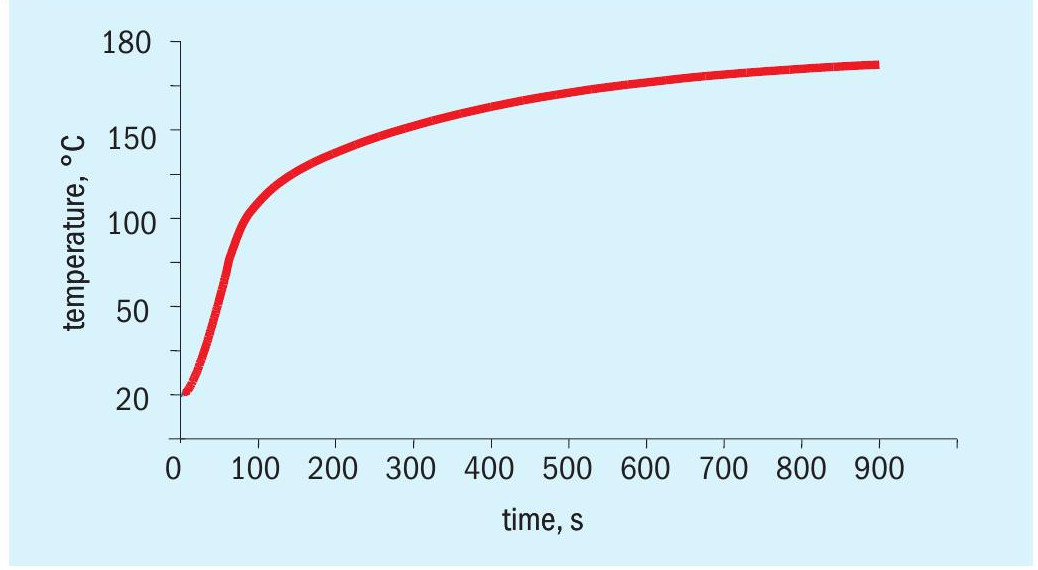
Cory Holt of CF Industries in Canada initiates the round table discussion: I was wondering if anyone could share their expertise with respect to urea process passivation and the possible modes of failure and if anyone has ever worked at a plant where passivation has failed. Our facility has recently shown physical signs of passivation failure in our reactor although all process data shows that we had oxygen in the system and proper passivation. We have recently come out of a scheduled shutdown and upon starting up we had a higher than normal N/C ratio as well as periods where we sat full in our HP loop while maintenance worked on some start-up issues.
Mark of UreaKnowHow.com in the Netherlands asks for some clarifications: Do I understand correctly from your story that you blocked in the synthesis section while dealing with some start-up issues? How long you did block in for? How many times did you block in and what was the time interval between block-ins?
Cory replies: There were a couple of issues and we attempted to start up three or four times. The longest period was a 22 hour period at which we know our ratio was greater than 4.
Mark asks another question: And how much time passed between the three or four blocking in periods?
Cory answers: For the first start-up we were nine hours into startup when we went down for six hours. Then we attempted the second start-up over a three hour period and went down for five hours. The third start-up was over a two hour period and then we went down for 22 hours. We attempted the fourth start-up over a 22 hour period when we were again forced to go down due to our leak detection system ringing in exposing a leak. When we shut down to look at the leak we realised that our vessel had been stripped of its regular iron oxide coating due to passivation. Upon vessel entry we realised we had many more pin holes and advised that they were the result of active corrosion at accelerated rates. This tends to point a finger at loss of passivation but our DCS trends show that we had oxygen in our system for the duration of the start-ups.
We are wondering if our high ratio had something to do with losing passivation in the reactor or if it was consumed by a contaminant, perhaps something from turnaround cleanings.
Mark replies: No, never heard that a high N/C ratio causes active corrosion. On the contrary, Saipem claims a high N/C ratio reduces corrosion rates.
Blocking in is always a situation where hot carbamate solution is in a vessel where no new fresh oxygen can enter. The existing oxygen will be consumed by the normal passive corrosion and a chromium oxide layer will form as a passive layer. When the blocking in time is too long, the amount of oxygen becomes insufficient and active corrosion starts. Stamicarbon and Saipem claim that blocking in times should be limited to max 72 hours.
Your remark of a contaminant consuming oxygen is interesting, although I have never heard of that phenomenon.
Does anyone else have similar experiences of blocking in right after start up and seeing active corrosion?
To observe so many new pinholes after such a short time seems strange to me. One should realise that a pinhole is an area of low oxygen refreshment even if the bulk liquid has sufficient oxygen. I find it hard to believe that its growth would be accelerated so much.
Further stop-start and start-stop situations cause big stresses on the liner due to temperature differences between the liner and the carbon steel wall and weaker areas could form a leak.
Cory replies: Thank you for your expertise, it does allow us to eliminate our ratio concern. We will continue our investigation into the exact cause of our accelerated corrosion and loss of oxide layer. The active corrosion is hard for us to imagine as well but we had the reactor inspected and some repairs during the turnaround which would not have missed these pinholes. We have found between 30 to 50 significant pinholes in just the bottom head alone and are inspecting the remaining zones now.
Muhammad Farooq of SAFCO in Saudi Arabia contributes to the discussion: I have some questions:
1. What is the lining material of your urea reactor and how long has it been in operation?
2. What is the inspection frequency?
3. What was the procedure applied for repair of previous pinholes and is it your annual practice or were these defects removed for the first time? Did you monitor the liner thickness yearly?
4. What is your feeding sequence and ammonia feeding temperature at start-up?
5. In the recent start-up, did you analyse the temperature profile for the urea reactor, especially at the reactor bottom?
Cory responds:
1. The lining material is a 316-SS and when we made repairs we used 25-22-2 SS as a weld material after grinding out the cavity. This liner is approx. 35 years old and the reactor was scheduled for re-lining in 2015.
2. We inspect during every scheduled maintenance outage which is every three to four years but due to other maintenance issues it has been every two years lately.
3. Repairs are always carried out in the same way as explained in point 1. As mentioned earlier, we were just coming out of a turnaround where minor repairs were being carried out and we had Stamicarbon do a pre-start-up inspection. They are currently doing our inspections now as well.
4. We usually warm the HP loop by feeding CO2 and steam (CO2 having oxygen from air blowers @ 0.6 vol-%) until we achieve 270°F at the top of the reactor. Then we feed in ammonia.
5. Yes, we looked at the temperature profile and actually realised we achieved the fastest heat up we have ever seen. Usually the heat up takes three to four hours but we almost achieved 270° within two hours. We are currently trying to prove whether the instrumentation was working properly as we cannot explain the accelerated temperature increase.
We are currently trying to narrow down our DCS data to see whether during our start-up attempts and block-ins we mismanaged the pulling of feed sequence or if somehow our instrumentation failed to show us loss of actual air. Initial data pulled has shown we were adding the right amount of air to our CO2 .
A question arising from this is whether circulating ammonia through the HP loop without CO2 (which means no oxygen) could have somehow disrupted the passivation layer?
Kashif Naseem offers his advice: I think your heating rate is much too high. Keep it at around 30°C per hour and use fresh air instead of a mix of CO2 and air for heating time passivation. I think the CO2 mix during heating with steam as water is creating the corrosion issues. Both your materials are OK as SS316-L UG and BC.05. I don’t think heating with a mixture of CO2 and air is a good idea. Add the air separately during heating and then follow the start-up procedure. Consult your licensor, who can provide you with better information to resolve the issue of your liner thickness and whether electrodes used during welding are of proper material. Furthermore contact the material specialist of your licensor. We are also operating a 30-year-old plant. We inspect the plant every two years and we have replaced the liner material. The highest corrosion rates are in the vapour area at the top of the overflow funnel. The original material was SS316-L UG and the top portion has been relined with BC.05. The condition is now very good.
Cory replies: I agree that the heat up rate is too high. We usually stay around 30 to 50°F per hour during the heat up. With our process it is impossible to have the heat up rate that we had with just steam or CO2 and we are not sure why it got as high as it did. We have our licensor involved but nobody knows yet how we got such a high heat up rate (almost 107°F per hour). We looked at our instrumentation to see if it was functioning properly and it looks like it was. Not sure if the heat up rate has anything to do with the active corrosion right now. It seems that all of our process data shows we had passivation (oxygen). We are now wondering whether we had a contaminant that might have given us an exothermic reaction of some kind that could have disrupted the passivation and produced a lot of heat? This theory seems unlikely to us now, but we cannot explain what happened.
Mark rejoins the discussion: Heat can be generated via: 1) condensation of steam and 2) formation of carbamate from NH3 and CO2 . What were the pressures during the high temperature increase? Did you see temperature increase at all the thermowells or only certain ones?
I don’t believe that circulating ammonia without CO2 would cause problems with the passive layer. Is there any chance that chlorides or sulphur may have entered the synthesis? These components have an adverse effect on the passivation layer.
Cory replies: When the temperature took off, the loop pressure was roughly 20 psi (80°F) and increased to approx. 60 psi (240°F) within 1.5 hours. We have seen the temperature increase on all four thermowells in the reactor as well as the overhead gas line. I should also mention that the CO2 flow was around 2,500 lb/hr during this time. At this time we have not found any indication of chloride or sulphur contamination.
Mark responds: Do you have graphs of the various temperatures versus time? Is 2,500 lb/hr the same amount of CO2 you applied earlier? Passivation of stainless steels can be hindered by heat tints (as a result of welding) or by fouling caused by corrosion product (iron and chromium oxides) or metal parts (grinding).
Once active corrosion of carbamate starts it cannot be stopped and one needs to stop the plant, drain and re-passivate the surface. Is it possible that heat tints and/or fouling is playing a role?
Easa Norozipour of Khorasan Petrochemical in Iran shares his experiences: Please note that for passivation of all equipment in the synthesis section, one needs at least two hours injection of oxygen. That means if the plant was started and then stopped before two hours passivation had been achieved, in this case, the plant cannot be blocked in. In this scenario the synthesis section must be drained completely and re-passivated.
Did you check the interval of the start-up, shutdown and blocking in of your plant?
Cory replies: We do have trends, I have been trending every relevant DCS tag looking for discrepancies. Grinding or welding contaminants may be a possibility as we did do some repairs during the scheduled turnaround before these start-up events. This has been discussed and we are looking into that. What baffles us still is the significant heat up rate. We have looked at the intervals and discussed them with our licensor and everything looks like it was in place and confirmed with our DCS data showing we had oxygen.
Mark adds some further comments: It is not easy to control the temperature rise at the beginning, i.e. between 20 and 100°C. I don’t think it’s uncommon for plants to have a temperature increase higher than the recommended 30°C per hour during this range. Can anyone confirm this? Does anyone have actual temperature curves available?
Muhammad replies: I agree with Mark that the temperature rise during start-up when pressure is 20 kg/cm 2 and temperaure is more than 100°C (after passivation and heating) increases quickly especially during the first hour. However it is normal start-up behaviour at many plants. My other observations are:
- The reactor lining is very old and needs early replacement.
- The issue of passivation and heating up of the synthesis loop needs to be sorted out with the licensor’s help. The impact on other equipment like the stripper, carbamate condenser and scrubber liner is not clear.
- The inspection frequency needs to be increased to yearly.
Muhammad comes back with a question: Have you analysed the CO2 purity and concentration of H2 in the CO2 feed stream?
Cory replies: We have two oxygen analysers on the CO2 compressor that were working fine and showed between 0.6 and 1 vol-%, which is normal. We have also trended the hydrogen content which was also normal (around 0.5 vol-%).
Mark replies: After evaluating the problems, this case has taught us that during blocking in of the synthesis section it is important to check the temperatures in the synthesis loop. These should show a downward trend. In case of upward trends it may mean some CO2 or NH3 is leaking into the synthesis section causing higher temperatures due to the exothermic carbamate formation reaction. In this case higher corrosion rates and active corrosion can occur.
Bob Edmondson, Technical Consultant in Canada shares his valuable experiences: I imagine highly improbable but a question to all is: with the reactor blocked in, “normal” oxygen would be about 0.02 wt-% in the reactor liquid. If, in one of the outages, the liquid level was above the funnel and steam was on the stripper at the normal pressure of some 11 bar, is it possible that a circulation loop is set up in which vapours are generated by the stripper and go to the reactor via the HPCC and over time drive off the dissolved oxygen which would be vented from the scrubber via a partially open vent (at minimum stop or worse, further open)?
If it is possible, somehow, to drive oxygen to below the level required for passivation it would be important to find the mechanism since it would be a risk for all 316L liners. It is a credit to CF Industries and to UreaKnowHow.com, that incidents like this can be made known and studied by other producers.