Nitrogen+Syngas 365 May-Jun 2020
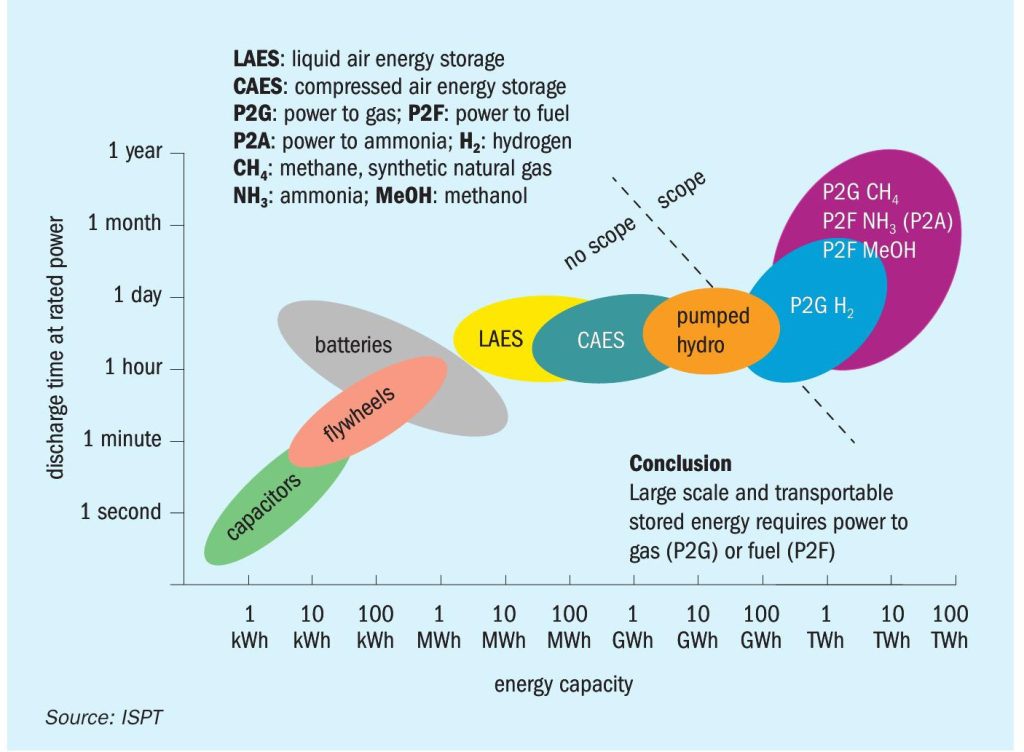
31 May 2020
Reducing industrial carbon footprint
GREEN AMMONIA COMBUSTION
Reducing industrial carbon footprint
Imagine an industry that only uses carbon-free fuels and does not have any carbon footprint. Assume this is feasible within a decade. Now wouldn’t that be an ambition worth pursuing? Duiker believes this is achievable. A. Lanser provides Duiker’s view on how its SCO technology can act as an enhancer for reducing industrial carbon footprint.
New application of SCO technology
Today the call for renewable forms of clean energy is increasing in order to reduce emissions of greenhouse gases (GHG) and to achieve the goals of the 2015 Paris Agreement. Many companies are striving to lower their carbon footprint during production. This creates the potential for a new application for Duiker’s patented Stoichiometry Controlled Oxidation (SCO) technology.
Duiker’s SCO technology was developed and commercialised in the early 2000s and is typically integrated in sulphur recovery units (SRUs) for processing ammonia (NH3 ) produced as a waste product in the refinery. Today, SCO technology is employed in several units in operation under various process conditions which have proven its ability to completely decompose NH3 . In stark contrast to uncontrolled ammonia combustion which can easily generate thousands of ppm of NOx emissions, the NOx emissions from the SCO unit can easily meet environmental regulations without further treatment. The SCO unit can realise NOx emissions in the range of 50-70 ppm @ 3% O2 dry.
Companies active in energy intensive and/or high temperature industries could benefit from SCO technology, because “green” or “sustainable” ammonia will be used as a carbon-free fuel, provided ammonia is produced from renewable sources.
This new application for Duiker’s SCO technology aims to replace fossil fuels (coal, oil, natural or refinery gas) by green ammonia, in so-called direct fired equipment applications and endeavours to contribute to a significant reduction of CO2 emissions.
Electrification and energy storage
One of the major efforts to reduce climate affecting gaseous emissions is the ongoing “electrification” of society and industry. This requires energy to be produced from renewable sources like wind, solar and hydro, or other methods. As the supply of renewable energy increases it is hoped this will reduce fossil fuel consumption.
The lack of long term storage options for electricity generated from renewable methods is a major disadvantage compared to traditional energy production. Special batteries, for example, could be a solution for short time storage in the magnitude of hours but are not optimum for seasonal storage (see Fig. 1).
Between the storage challenges of renewable energy and the daily or seasonal fluctuations in potential generation levels, the electrification of industry faces unique challenges. To meet the demands of certain industries, electrification will need to take a different approach, not using electricity directly from renewable sources. The use of “energy carriers” can provide long term storage and easier transportation options without creating economical barriers.
The chemicals in the blue and purple ellipses in Fig. 1 are currently labelled as potential “energy carriers”. Amongst other chemicals, ammonia has been identified as a highly suitable medium for the storage and long distance transport of hydrogen.
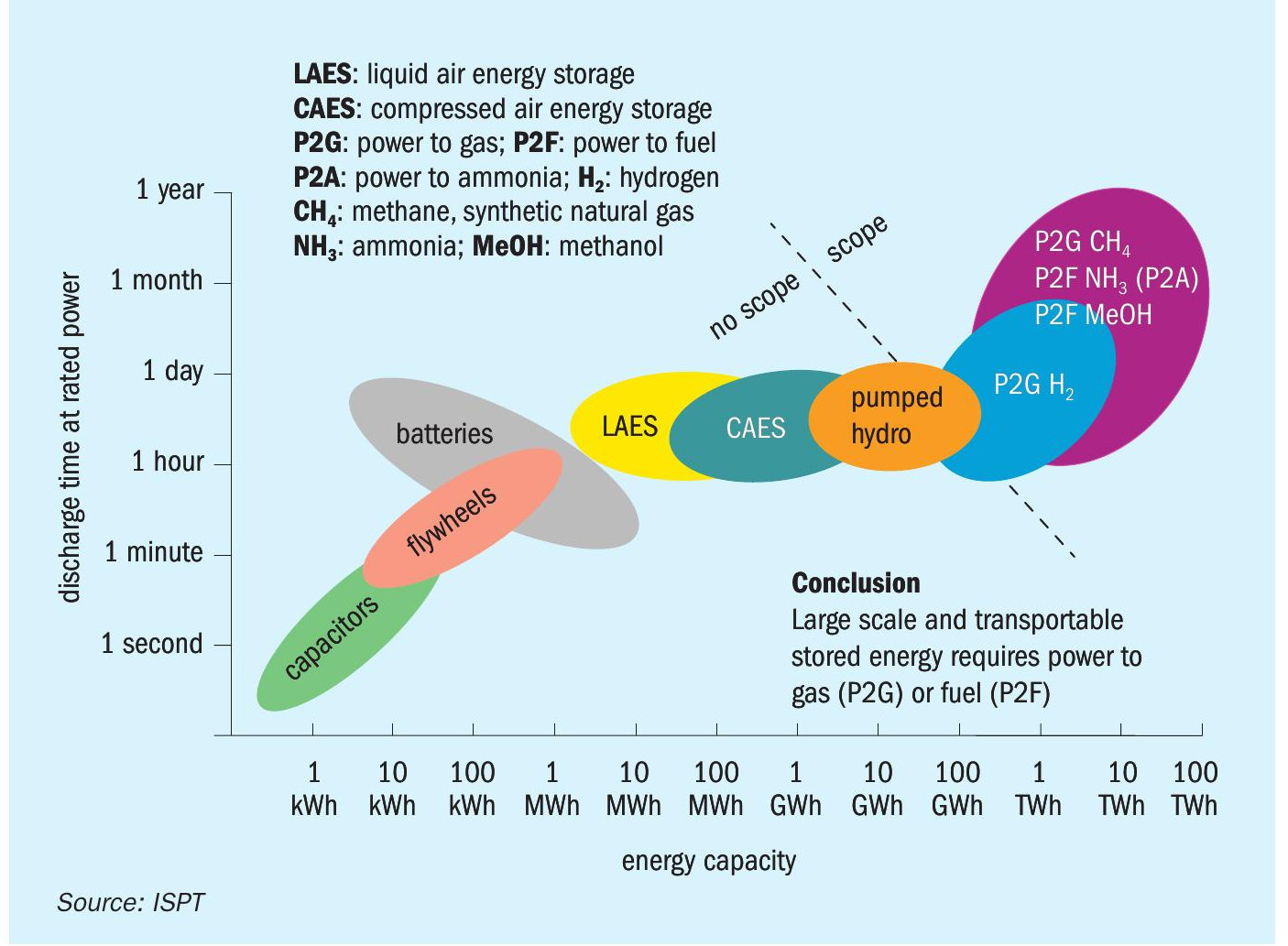
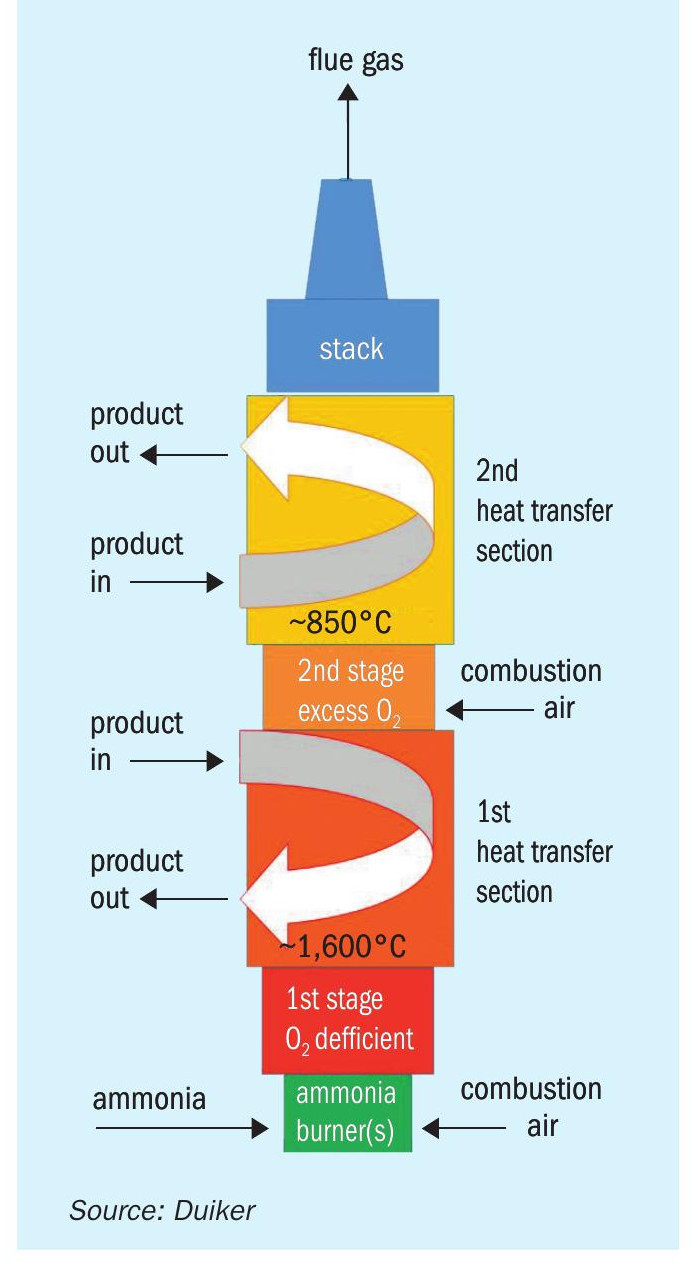
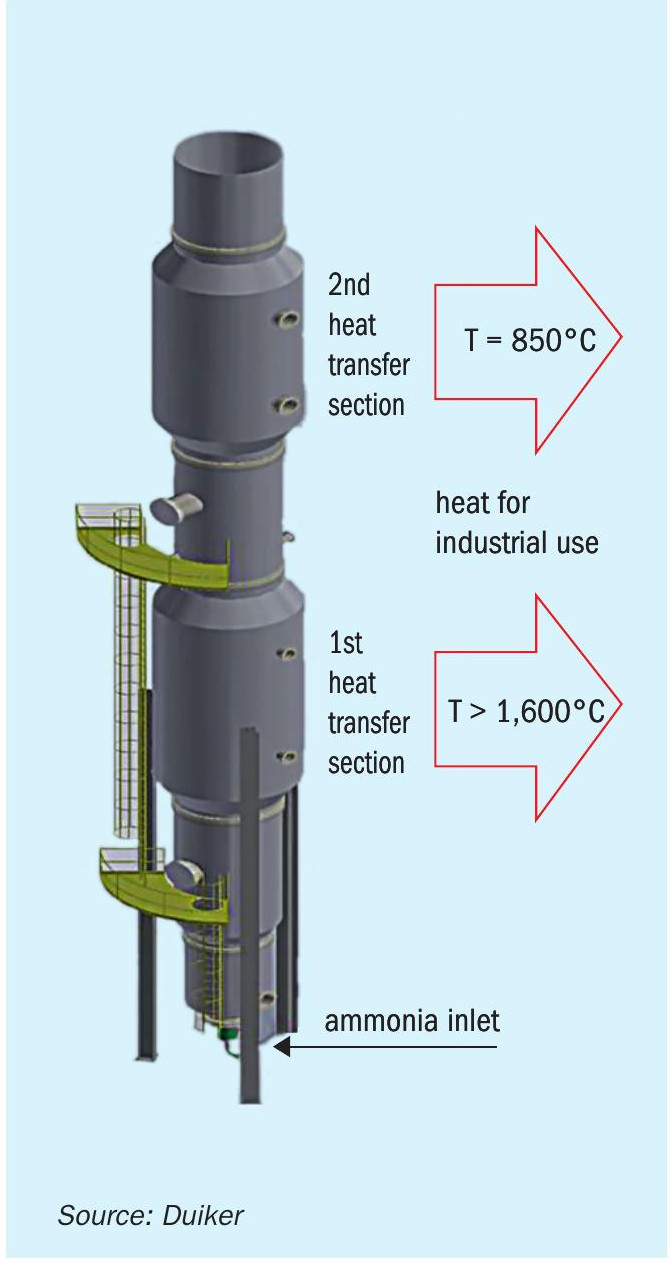
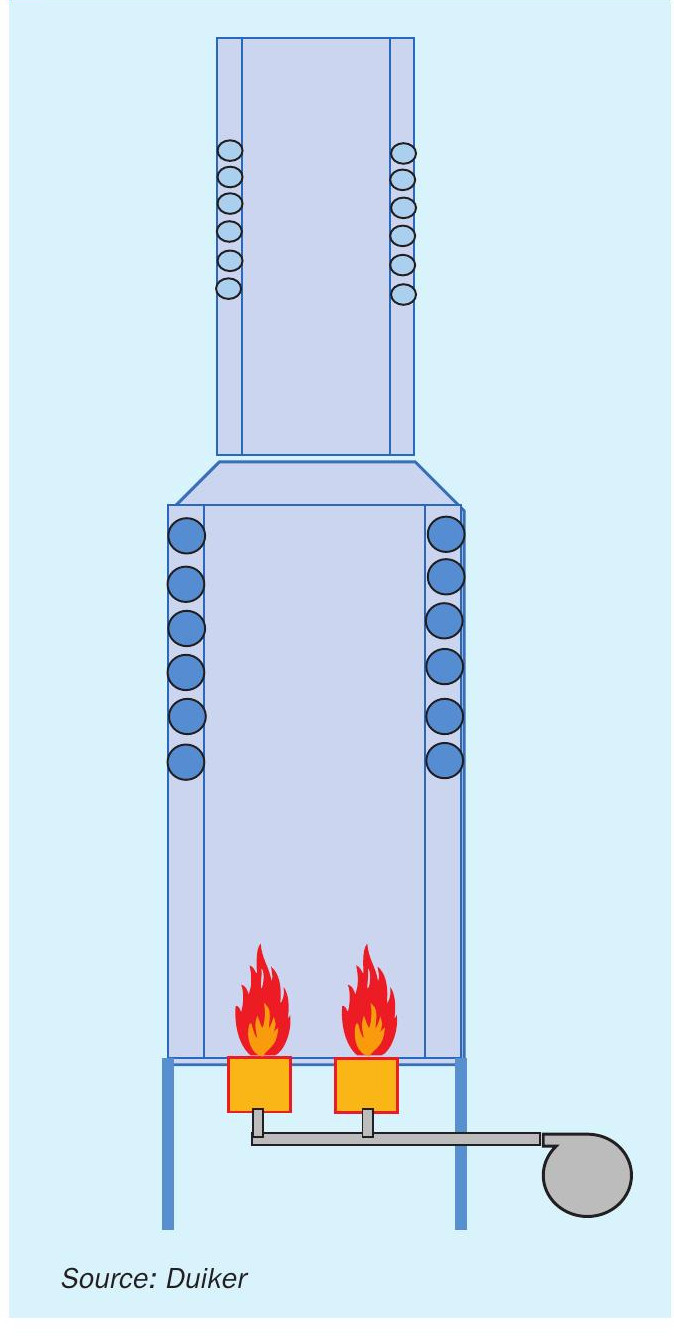
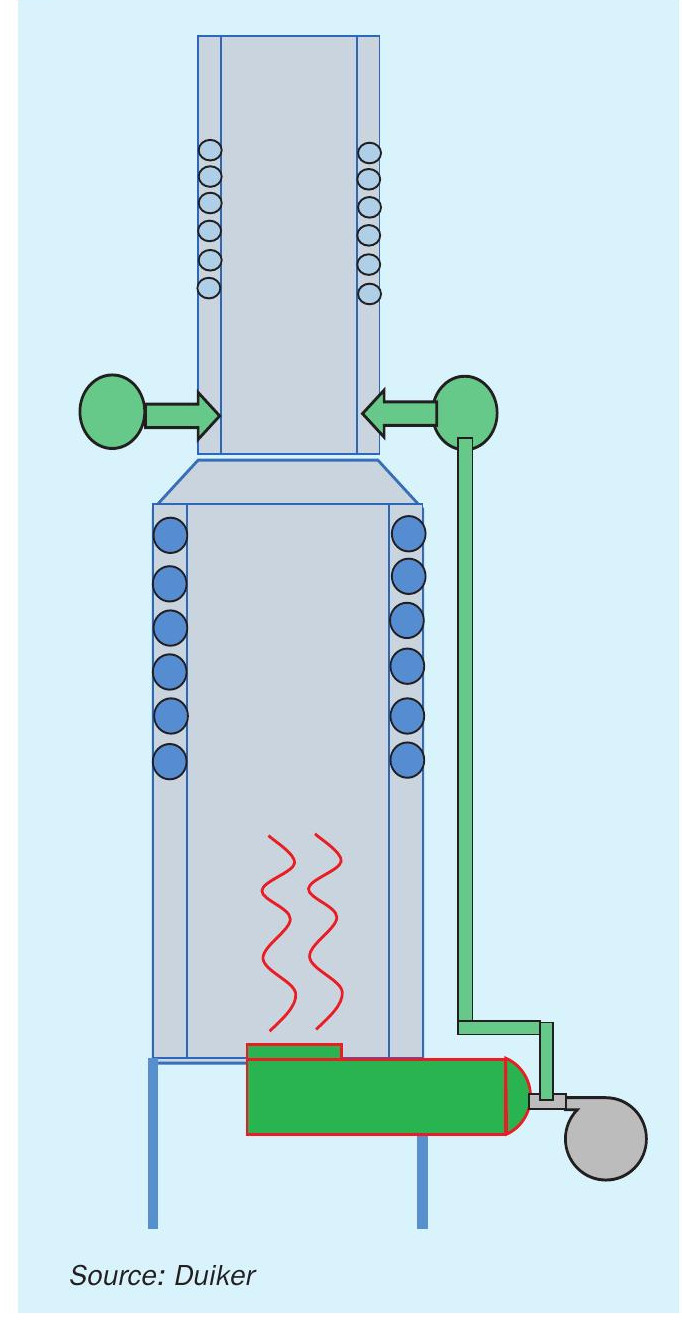
An important advantage of using ammonia as opposed to unbound hydrogen is that it can be stored and transported at room temperature at a pressure of 8.5 bar. Hydrogen on the other hand has to be stored and transported at a very low temperature and very high pressure. This not only makes it impractical but severely reduces the overall efficiency of the hydrogen-energy chain.
Ammonia as a sustainable green and carbon-free fuel
The ISPT report “Power to Ammonia”1 mentioned: “NH3 if produced from renewable electricity can be used as a high caloric energy carrier to store CO2 -free electricity. NH3 has a potential to be used as a chemical storage medium due to a relatively high round trip efficiency, energy density and low cost of nitrogen sourcing. Converting NH3 back into electricity can be done without CO2 emissions. The technology is scalable and not limited by scarcity of materials or storage space.”
Aside from the conversion of ammonia back into electricity it is feasible to use ammonia directly as a fuel. This might be an even more interesting option for certain industries. The maritime industry is already considering the use of ammonia as a fuel. A quote: “The decarbonisation by 2050 scenario shows a drastic switch to ammonia from 2040 onwards, with almost 100% of the fleet using ammonia by 2050”, published in a recent article2 from the Global Maritime Forum, shows serious consideration of green ammonia as a fuel.
From a technological point of view, sustainable or green ammonia as a fuel is a feasible solution for the electrification of industry. This can be realised with Duiker’s SCO technology that converts ammonia into flue gases of high temperature (>1,600°C). This will be further referred to as “high temperature heat”.
Energy release benefit of SCO technology
Fig. 2 illustrates how the heat released by the combustion of green ammonia could possibly be transferred to a potential production process by means of heat transfer equipment. After the first combustion stage the flue gas temperature may rise to a level above 1,600°C and these flue gases can be used as input for a high level temperature heat transfer section (1st heat transfer section).
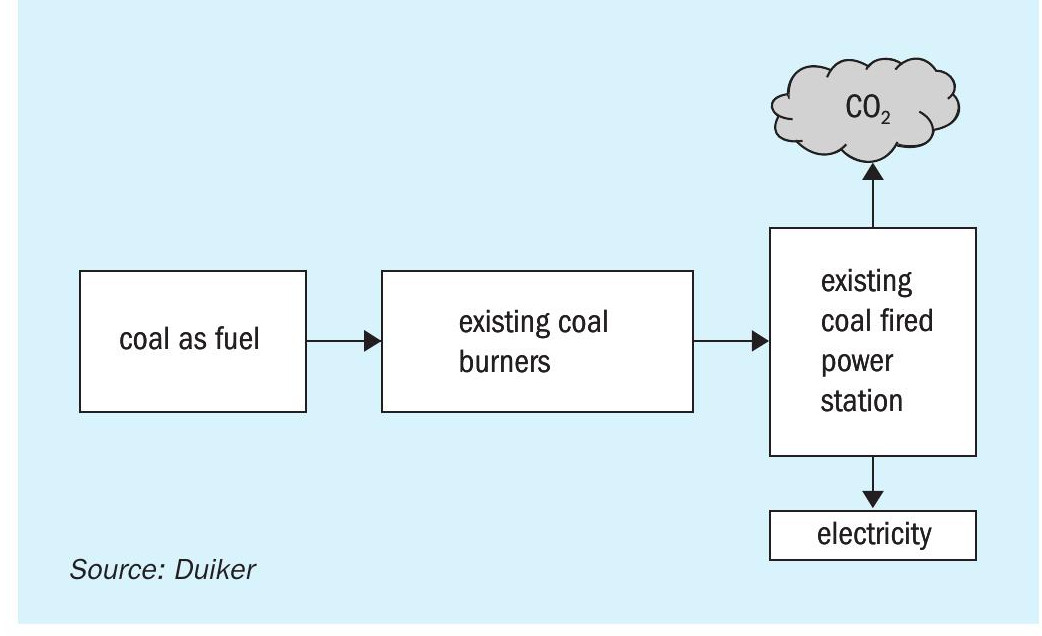
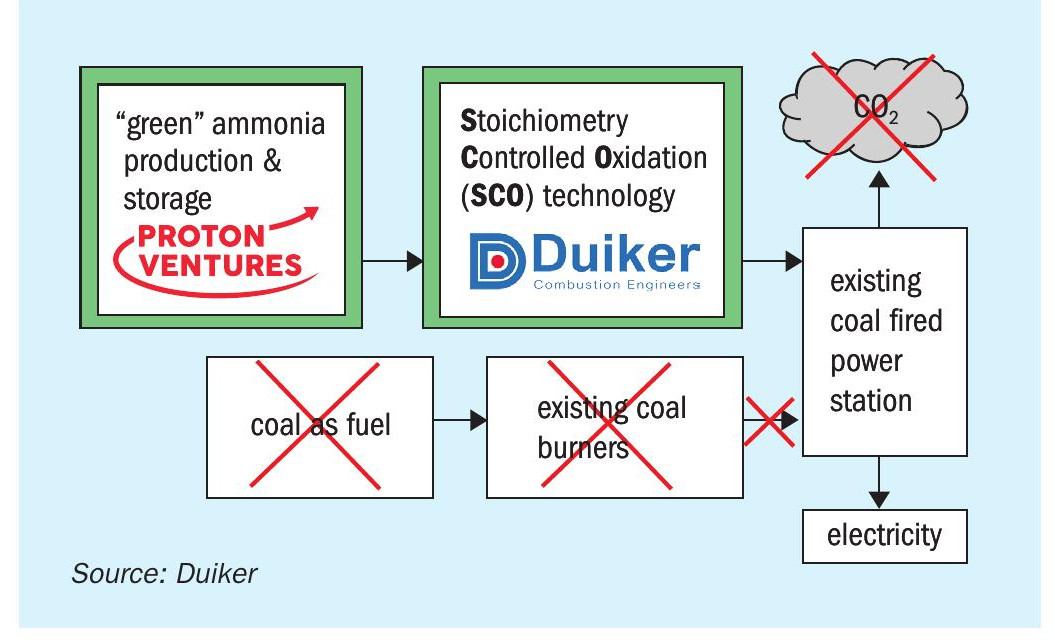
After the flue gases have passed through the 1st heat transfer section, another combustion process takes place in the second stage. Thereafter, the flue gases still contain enough energy to make energy recovery worthwhile. In the second stage the flue gases have a temperature of approximately 850°C so another heat transfer section can be used to harvest this energy (this takes place in the “2nd heat transfer section” in Fig. 2).
Fig. 3 shows a piece of imaginary equipment. This visualisation has been derived from the block scheme in Fig. 2. This is how Duiker envisages an example of direct fired equipment with “green or sustainable ammonia”.
The dimensions and configuration of the equipment may vary to a large extent, depending on the application. The exact heater configuration and dimensions will be determined in consultation with Duiker’s customers. Efforts will be made to minimise modifications to an existing (fossil fuel) fired heater/furnace.
Refer to Figs 4 and 5 for a brown field example. Fig. 4 shows a typical forced draft heater firing on fossil fuels and Fig. 5 shows the same heater after a typical revamp based on SCO technology, enabling green ammonia as a fuel.
From a combustion viewpoint, Duiker’s SCO technology is suitable for a variety of future applications in high temperature and energy intensive industries (i.e. steel, cement and power generation). The following equipment, amongst others, can be redesigned for ammonia as a green fuel:
- fired heaters / ovens;
- industrial gas fired furnaces;
- naphtha crackers;
- gas fired turbines;
- steam boilers;
- steam methane reformers (SMRs);
- (coal-fired) power plants.
Sustainable multifuel coal-fired power station
In general, CO2 emission reductions are a political and environmental topic. For example, in The Netherlands, the Dutch government decided that, in 2030, all coal-fired power stations for generation of electricity have to be either out of operation or rebuilt for carbon-free electricity generation.
This is not only a challenge from a viewpoint of CO2 emission reduction, but also from a power grid balancing perspective. The current Dutch coal-fired electrical power stations are also operating as a buffer for the preservation of the fine balance between supply and demand of electrical energy. Eliminating coal-fired power stations, which are relatively flexible, operating within a wide load range, stabilising the power grid, will be challenging, because generating electricity from renewables is less predictable and hardly determined by demand. Green ammonia as a fuel substitute for coal in a power station can take over this grid balancing role. This is another argument for considering ammonia as a flexible energy storage system.
Duiker Combustion Engineers, together with its partner Proton Ventures6 , are jointly working on a plan to convert existing coal-fired power plants into renewable multi fuel-fired power plants. The objective is to substitute coal by green ammonia combustion. The fuel conversion from coal to green ammonia will take place step by step and will, eventually, eliminate coal firing completely. The firing of green ammonia will be based upon Duiker’s SCO technology. The achievable reduction in CO2 emissions by this fuel change would be obvious and significant. Figs 6 and 7 visualise this process.
Economics vs environment
Let’s start with a couple of quotes about the perceived value or costs of ammonia: “Green ammonia is increasingly acknowledged as a valuable chemical for transportation and storage of hydrogen produced from renewable electricity.”1
Or: “The current price of green ammonia produced by renewable electricity, is about 18% more expensive than ammonia produced from fossil fuels”.
“So if brown ammonia goes to market at a price of, say, $450 per tonne (~15% mark-up over cost), and green ammonia could be available at a price of $530 per tonne, what effect might this have on national policy calculus? It’s one thing if the price of a green commodity is twice that of a brown one. But just 18% more? This could be a bargain policymakers may be willing to strike.”, according to a news item on the AEA website3 .
And: ”Ammonia fits well in a hydrogen based economy.”4
It is noteworthy that ammonia, in the current market, is predominantly used as a feedstock in the fertilizer industry and not as a fuel. If ammonia produced from renewable sources becomes cheaper than from fossil fuels, this will also reduce the cost of producing fertilizers. The largest cost driver for green ammonia is the electricity price to produce sustainable ammonia from green hydrogen. Thus, the lower the electricity price, the lower the price for green ammonia.
The Hydrogen Council expects that the cost of hydrogen: “is projected to decrease by up to 50% by 2030 for a wide range of applications.”5
The current economic feasibility of green ammonia versus fossil fuels, such as coal, is a challenge. However, the actual situation is most likely to change over time in favour of green hydrogen and ammonia. The price for CO2 emission rights is likely to increase in the next decade and the economies of scale will have a positive impact in bringing down the production costs for green hydrogen and ammonia. Today’s economics still rule over environment.
Duiker anticipates that it is only a matter of time before the business case for large-scale renewable energy production will favour renewable energy over fossil fuels.
The timing for economic breakeven for renewables will be greatly influenced by a higher price for CO2 emission rights, as a “penalty” for carbon emissions. Breakeven as soon as possible will be most beneficial for the environment.
Next steps
Coming back to the original ambition and question at the beginning of the article, Duiker’s conclusion is that the ambition is indeed worth pursuing and the answer to the question is a convincing “yes”. SCO technology has been proven and is scalable in SRUs and thus offers a feasible route to convert green ammonia into high temperature heat and to phase out industrial CO2 emissions.
The economic competitiveness for this path forward is only a matter of time. Large-scale green ammonia production in the near future, as well as extra carbon emission costs for using fossil fuels, will change the economic outlook for green ammonia in the coming decade.
The time taken for renewables to become an economic choice could be shortened significantly once a major industrial player or a consortium of different industrial players has the courage to invest considerably in green fuel production. This will prove that a large green fuel production plant is scalable and possible and it will have a very positive impact on the acceleration of the necessary infrastructure of green fuels.
Duiker Combustion Engineers is ready to act as an innovative partner for long-term solutions and is eager to explore the possibilities of its SCO technology with any potential customer who is interested in reduction of CO2 emissions and in applying green ammonia as a green solution for its (production) process.
References