Sulphur 389 Jul-Aug 2020
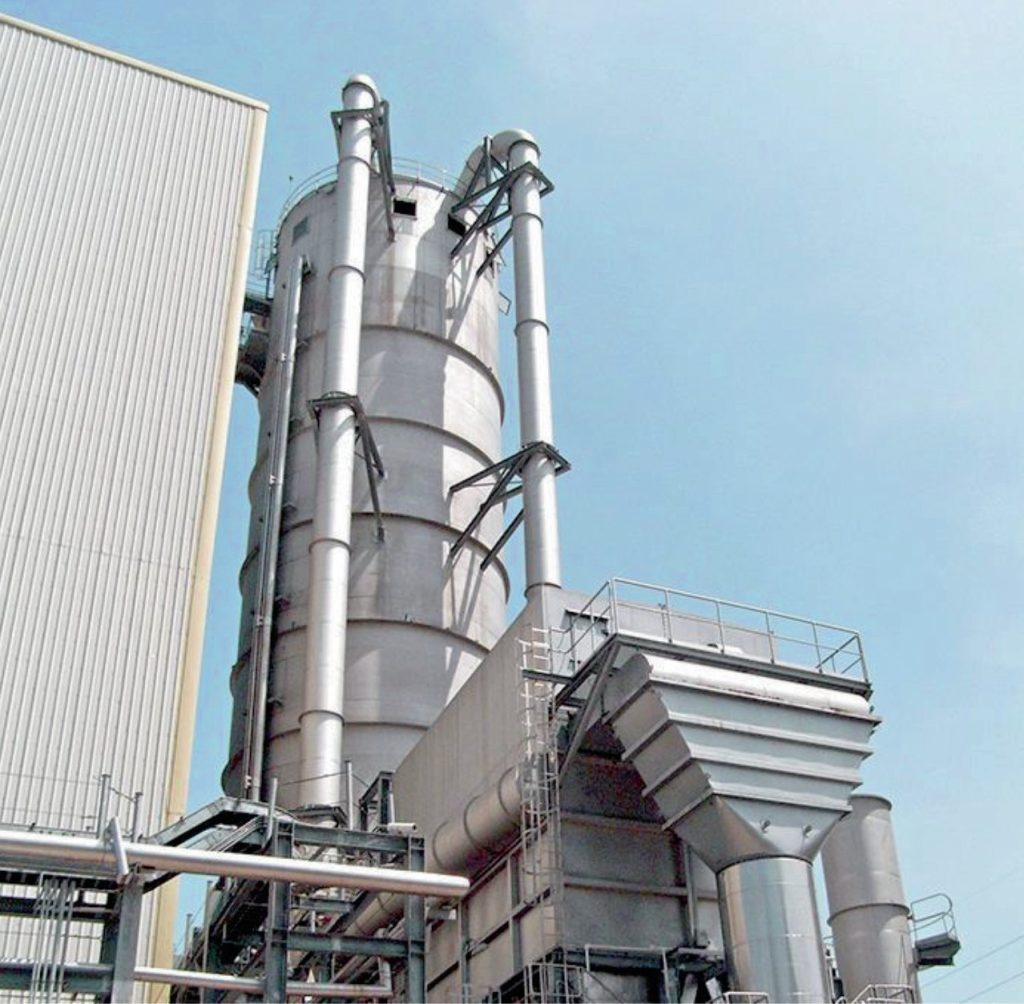
31 July 2020
Modernisation of an old sulphur forming technology
SULPHUR PRILLING
Modernisation of an old sulphur forming technology
Kreber’s R&D department has been researching the prilling of sulphur in pursuit of the ideal process. In this article, T. Nieboer of Kreber recounts the history of prilling up to today, tracing the developments and highlighting the challenges that still remain.
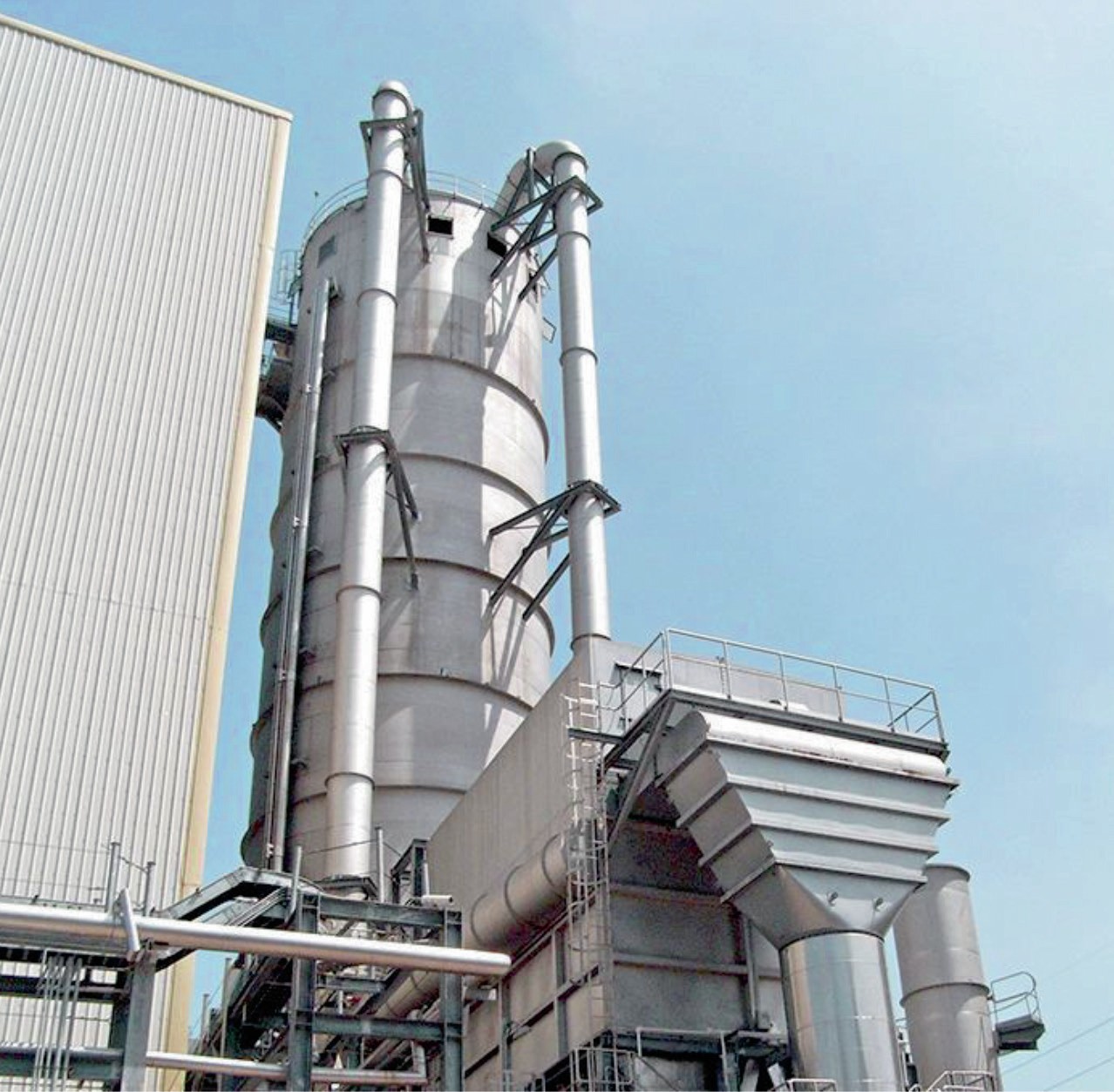
Legend has it that one night in 1782, William Watts, a plumber from the city of Bristol in the UK was walking home after a long night of drinking ale. On his way home he decided to take a rest near St Mary Redcliffe church, which he had worked on, helping to renovate the lead roof. As he lay on a bench thinking about his loving wife, who was home alone, he drifted into a sleep full of dreams in which his wife’s anger kept haunting him.
He saw her towering on top of the church, and in her anger she poured molten lead down the tower onto his face. The lead didn’t fall in a stream but instead formed perfect spherical droplets, which rained down upon him in the shape of solidified lead pellets. He woke up to find that it was only the Bristol rain falling down on him.
The next day he decided to experiment and together with his wife climbed the spiral stairs onto the roof of the church. They drilled holes in the bottom of a cooking pan, melted some lead and poured it through the holes. As in the dream, the molten lead formed droplets, which solidified into perfectly spherical lead pellets. These pellets became known as patent lead shot, which was used in shotguns for hunting1 . Previously, lead shot was produced in a slow and cumbersome moulding process, producing irregular (and expensive to produce) lead balls. Watts, a hobby hunter himself, was so convinced of this production method that he decided to build the world’s first prilling tower, right on top of his house2 .
Until this day, spherical products from the chemical industry are produced in very much the same way as it was invented by William Watts; although the process is now known as prilling.
The pan has been replaced with a prilling machine, where the melt is forced through nozzles. From these nozzles, a jet is ejected, which breaks up into spherical droplets and subsequently solidifies in the air. The priller provides greater control of the breakup of the liquid jet and therefore greater control of the process quality and product shape or size. The tower is optionally operated with forced convection and can be equipped with a filter installation or scrubber to counter dust emissions.
Prilling was, and still is, mainly utilised in the world of fertilizers and plastics finishing. These high capacity production processes demand an easy to use and stable finishing technology that can both handle production fluctuations and production of a free flowing product with a narrow particle size distribution (PSD). One of the main reasons prilling is utilised in the market, is that the process requires very few moving parts and is capable of processing very high quantities.
Prilling of sulphur
In the world of sulphur, converting molten sulphur into large quantities of solid particles has always been a challenge. Crushing a solid block into smaller chunks was formerly utilised as the main method of obtaining transportable sulphur pieces. Due to considerable dust formation while handling solid sulphur pieces in this form, the industry started looking for new technologies to form sulphur.
One of the adapted technologies was air prilling, which was already utilised by the fertilizer industry. The finished product from these prilling facilities was large quantities of small, yet perfectly spherical pellets with a polished surface and a relatively narrow PSD, leading to a free flowing product. At this point, when prilling was the most dominant method of producing solid sulphur, the well-known SUDIC specification (Sulphur Development Institute of Canada) was also introduced, leading to a market standard for all sulphur finishing technologies.
The industry developed new ways of production, such as granulation, (steel belt) pastillation and wet prilling, which took over the role of being the most dominant method of particle engineering in the sulphur industry.
This shift in production method was the result of two main concerns3 . Firstly, the prilling towers designed in the 1960s operated on an open air design. This meant that all cooling air used for solidifying the prills was immediately ejected into the environment. All the dust particles formed during the prilling process, as well as any vapours from the sulphur melt, were transported with the air stream into the environment. This led to environmental problems in the downwind areas of the prilling plant.
Secondly, a disastrous fire incident in the Middle East led to the conclusion that dry prilling should be considered as a high risk technology4 . The low ignition energy, combined with the potential build-up of static charge in the solidifying prills, can lead to dangerous sparks. The combination of these two aspects, coupled with a hot climate, led to the disastrous incident in the Middle East.

Safer and more sustainable future
In the last few years, prilling has been under development to handle a wide variety of products. The addition of an air treatment section was applied in the late 1980s, where either a dry filter or wet scrubber is utilised to drastically cut down on (dust) emissions from prilling towers. However, as the environmental impact of all industrial plants on their surroundings became more apparent, laws became more and more stringent on prilling towers. This resulted in a surge of new research on prilling with a closed loop process as one of the main achievements.
In the closed loop process, the cooling medium (in this case air) is first led to an air treatment section and then to a heat exchanger. The resulting cleaned and cooled air can be reused in the tower. The main benefit of closing the loop, is the fact that emissions are reduced to zero. In addition, the heat removed from the cooling medium can be reused elsewhere in the plant, leading to a higher degree of heat integration of the total plant.
Prilling is already widely applied in other industries, where the same hazards with regard to fire and dust explosions exists, mainly near the air treatment section. When applying the closed loop principle, all of the cooling medium is recycled, eliminating the need to use ambient air as the cooling medium. Practically any gas can be chosen as any wastage of the cooling medium will be very limited. Currently, the first prilling towers with inert nitrogen gas as cooling medium have started to emerge, leading to an intrinsically safe method of prilling with no emissions and low fire hazards.
These prilling towers provide a safe and high capacity production method of converting melt into a preferable finished product. These innovations are showing promise in the field of sulphur as well. It is already empirically proven that sulphur prills can be formed and that they have a range of benefits over other finishing technologies. The main challenge now is to alter the closed loop prilling system that is used in the world of plastic and fertilizer prilling, towards a system that can safely handle sulphur.
Future developments
From its origins in the 18th century until now, prilling has gone through many developments. The latest innovations are mainly in the off-gas section and a higher degree of control of the total process, which have led to a safe and trustworthy process to create prills from melt. With their narrow PSD, and free flowing properties, prills have unique product qualities compared to the other main finishing technologies.
Currently, the main challenge is to find a way to prill sulphur in a safe and economical way. Closed loop prilling with an inert cooling medium shows great promise in making this achievable. There are still a handful of challenges to overcome before this stage is reached. Kreber stands ready to pool its resources with any interested party in order to achieve the ideal prilling process that will result in benefits for all involved, whether economically or environmentally.
References