Nitrogen+Syngas 367 Sept-Oct 2020
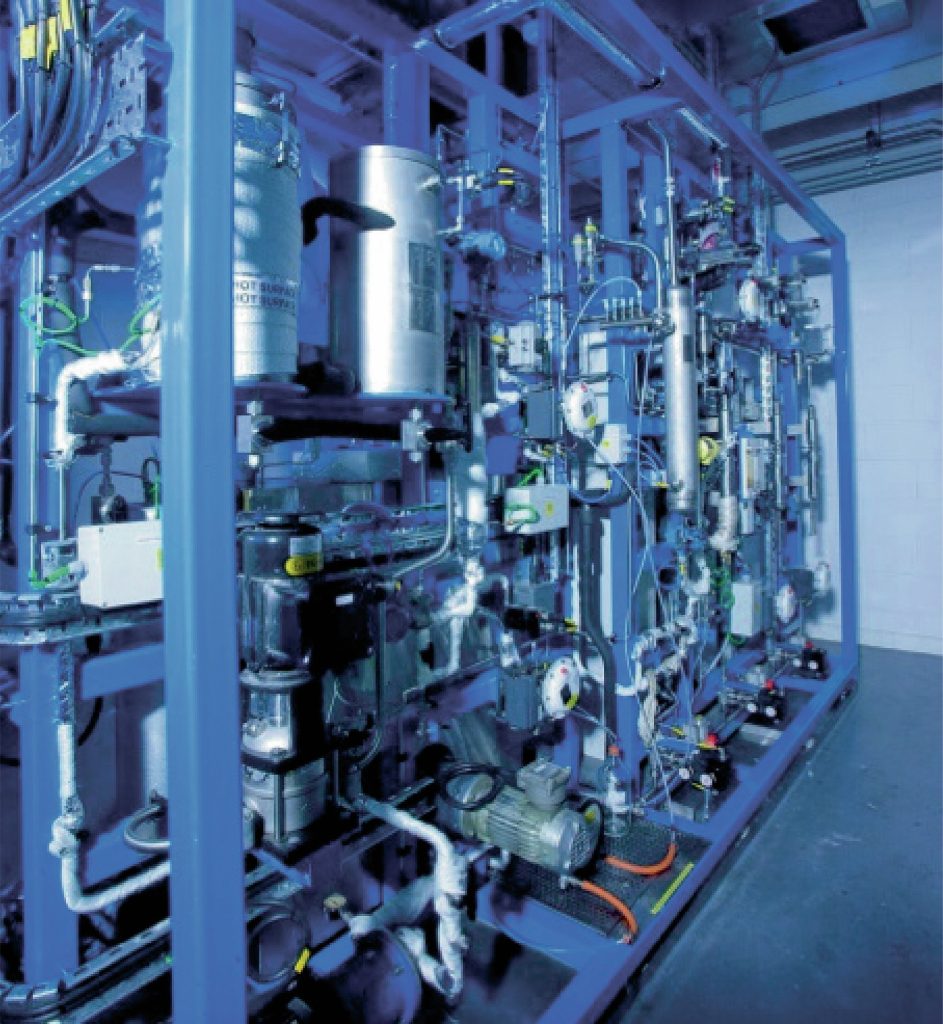
30 September 2020
MEG from methanol and syngas
PRODUCT SLATE DIVERSIFICATION
MEG from methanol and syngas
New technology makes it possible for methanol producers to diversify their product portfolio and participate in the high growth mono ethylene glycol market. A. Shah of Johnson Matthey reports on the development of the new technology and its commercialisation.
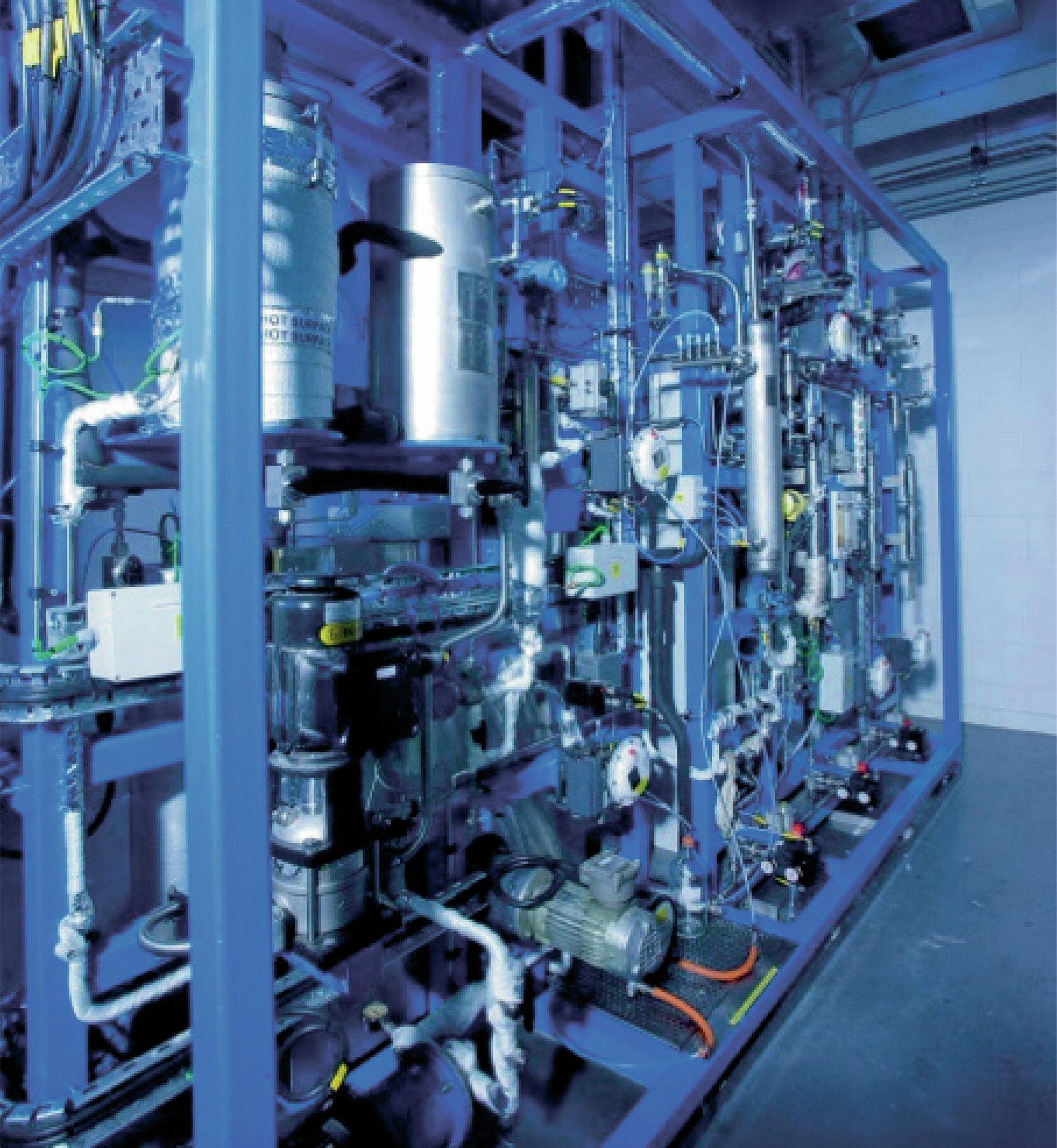
Mono ethylene glycol (MEG) is the most common industrial diol and is used in the manufacture of polyester fibre, fabrics and polyethylene terephthalate (PET) resin used for production of plastic bottles. Other industrial uses are as a coolant, heat transfer agent, antifreeze and a hydrate inhibitor in gas pipelines.
New process technology using a proprietary catalyst developed by Johnson Matthey Davy Technologies Limited (a fully owned subsidiary of Johnson Matthey Plc) and Eastman Chemical Company (Eastman) enables the production of MEG from methanol and syngas. This offers a unique and exciting opportunity for methanol producers who are interested in diversifying their product slate.
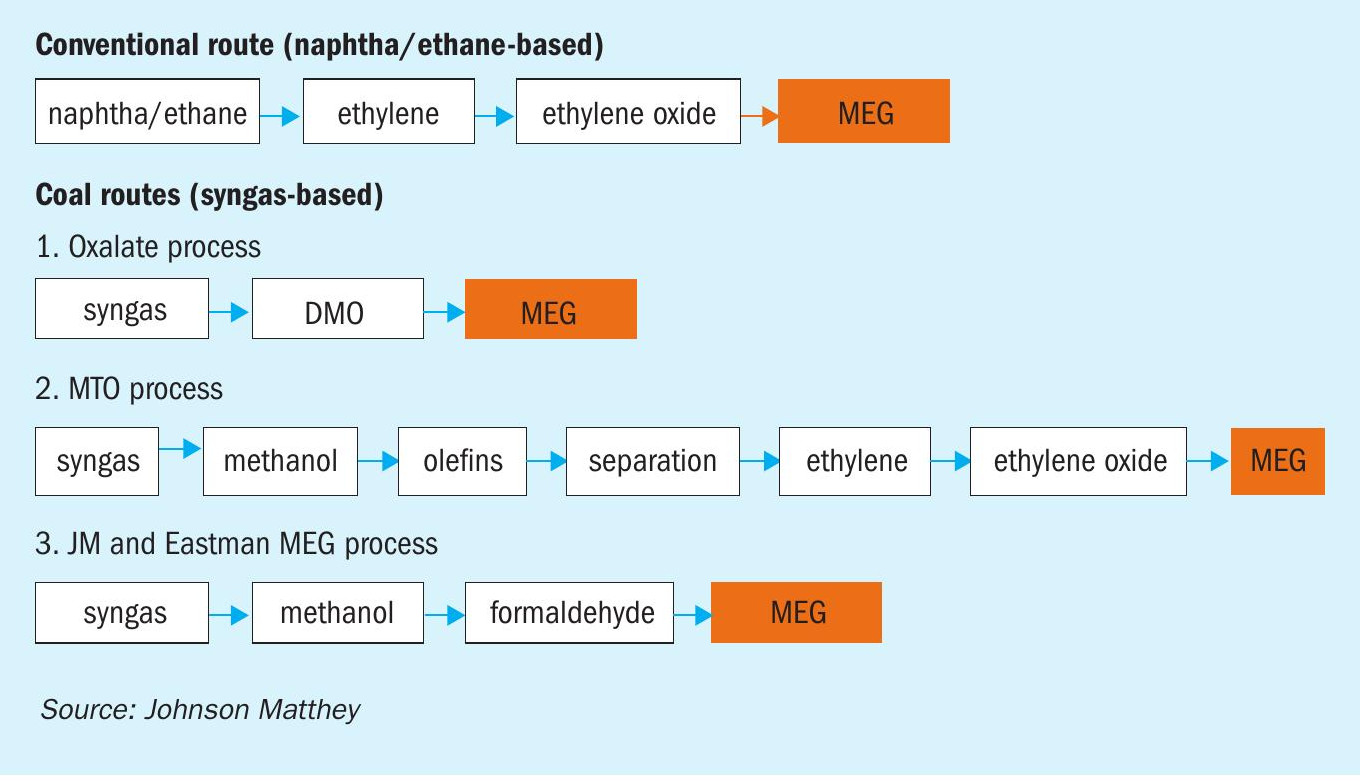
First licence for new MEG technology
The first licence for this new MEG technology was granted in September 2018 to Inner Mongolia Jiutai New Material Company who are building a major coal to MEG complex in Inner Mongolia, China which will use the new MEG technology to produce 1,000,000 t/a of MEG. This will be the first commercial plant using the new technology and is a result of development by Johnson Matthey (JM) and Eastman which started in 2006.
Market opportunity and production routes
Current worldwide consumption of MEG is approximately 30 million t/a and has grown by over 5% per year over the last decade. With a growing middle class, particularly in Asia, over ten million t/a of new MEG capacity will be required over the next ten years.
Fig. 1 shows the main production routes for MEG. Until 2012, nearly all the MEG in the world was produced by the conventional route from ethylene, which is produced by cracking natural gas or naphtha. In Asia, ethylene is produced mainly from naphtha and the increase in the oil price in the 2000s encouraged the development of the Oxalate process in China, using syngas produced from coal as the feedstock and several plants in China use this technology today. This route has an explosive intermediate and there have been reported issues with product quality where the MEG quality deteriorates within a few days of production. Another syngas-based route is the production of methanol from syngas followed by conversion of methanol to ethylene in a methanol to olefins (MTO) plant. MEG is then produced by the conventional process making it a long process.
Finally, there is the JM and Eastman process where methanol and syngas are converted to MEG. The process uses well proven unit operations with new proprietary catalyst technology with high conversion and selectivity enabling efficient use of raw materials. This process is more economic compared to the conventional ethylene-based route when the oil price is above $55 per barrel.
The novel MEG process
A simplified block diagram of the novel process is shown in Fig. 2. The key feedstocks are methanol, carbon monoxide and hydrogen and besides MEG, the process produces a small amount of valuable diethylene glycol (DEG). If required, the formaldehyde plant can be designed to also provide an export formaldehyde stream.
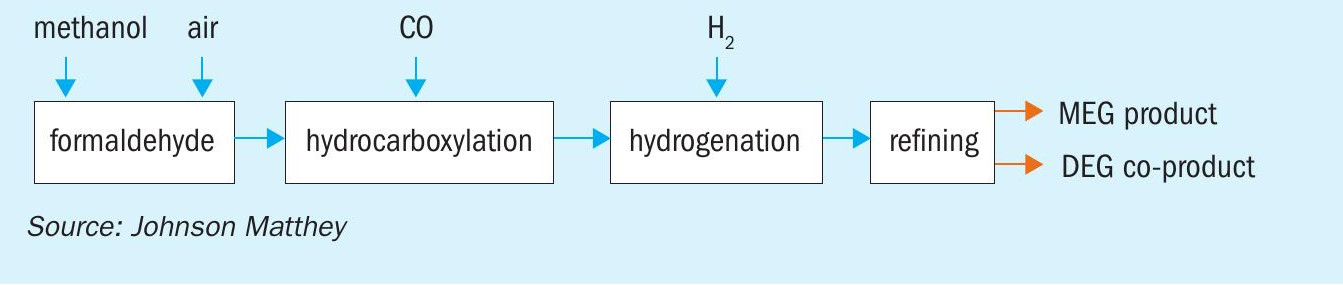
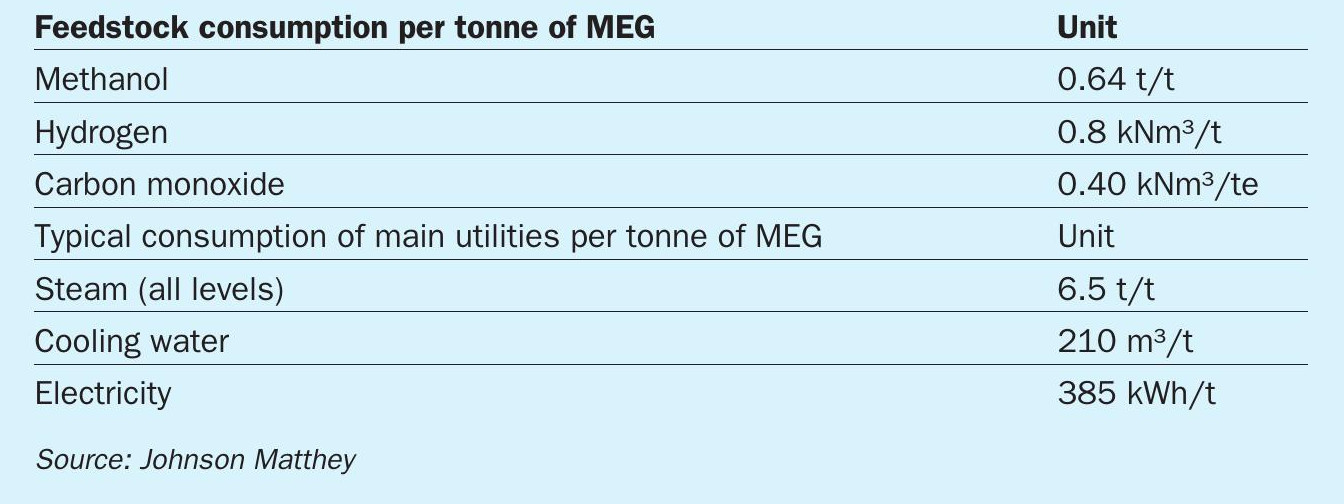
In the formaldehyde plant, methanol from battery limit reacts with air over a catalyst to produce formaldehyde. The first MEG plant reaction stage is hydrocarboxylation, where aqueous formaldehyde reacts with carbon monoxide to produce glycolic acid. The glycolic acid is then reacted with an alcohol to form esters, which are then hydrogenated to form mono ethylene glycol and diethylene glycol.
Feed and product specifications
The feedstock specifications are AA grade methanol, high purity carbon monoxide (99 vol-% min) and hydrogen (99.9 vol-% min).
The MEG product specification meets ASTM E2470-09 and the new Chinese National Standard GB/T 4649/2018. The key parameter for purity of the product is ultra violet (UV) transmittance and the MEG produced by the JM and Eastman process has been demonstrated to meet the specification in all UV transmittance wavelengths. The DEG product purity meets the ASTM D2694-05 specification.
Performance data
The key performance data is summarised in Table 1. DEG is a valuable by-product and approximately 19 kg of DEG is produced per tonne of MEG. The process has low waste water emissions and there are no hazardous intermediate products or by-products.
Technology development
JM has used the mini plant concept to develop and commercialise new DAVY™ technologies for nearly 50 years. It started with oxo alcohols in the 1970s.
Some of the new technologies commercialised over the last 50 years include the following:
- oxo alcohols – since 1970s;
- butanediol – since 1980s;
- tetrahydrofuran – since 1990s;
- ethyl acetate – 2000;
- detergent alcohols – 2002;
- octanol – 2007; l 2-propyl heptanol – 2014;
- hexanediol – 2018.
Efforts are now focused on MEG technology.
The development of new technologies is undertaken at the state-of-the-art technology centre in Stockton, UK. The mini plants are designed, built and operated by teams of chemists, chemical engineers and specialists working together combining their respective expertise to develop the optimum process flowsheet by selection of appropriate catalysts in conjunction with optimum reaction systems. The mini plants are designed to ensure all the fundamental design parameters can be scaled to commercial size. Besides mini plants extensive use is also made of other tools such vapour/liquid equilibria testing equipment, hydraulic rigs, and simulation and plant modelling tools.
Every part of the MEG flowsheet was replicated in the several mini plants which were operated over several thousands of hours to generate comprehensive data covering reaction kinetics, catalyst performance, separation equilibria and where appropriate the recycle streams were closed.
The mini plants were also used to produce the final product MEG and DEG. Using comprehensive data collected from long term operation of the mini plants, designs have been developed for commercial scale plants with MEG capacity ranging from 200,000 to 500,000 t/a.
JM and Eastman collaboration
Another key aspect in the MEG development has been the benefit of the collaboration with Eastman who have a strong background in coal gasification, syngas chemistry and derivatives. Eastman operates the USA’s first coal gasification plant and produce a range of high value chemicals. Eastman has expertise in material testing, product quality analysis and significant operating experience. A dedicated team of highly experienced chemists, scientists and engineers from both JM and Eastman worked together for over ten years during the development of the new MEG technology. Between JM and Eastman, a process design package and support during detailed engineering, plant start-up and post plant start ‐up can be provided.
Integration with methanol plant
JM can also offer designs which would integrate the methanol and MEG plants. Such a complex would benefit from common syngas production based on either coal gasification or steam reforming of natural gas with sharing of offsites and utilities. Such a facility would also offer the opportunity to produce methanol and formaldehyde as export streams.
Summary
The novel MEG technology from JM and Eastman enables production of MEG using methanol and syngas as feedstocks and has the following attributes:
- a competitive investment and operating cost;
- economies of scale with single train capacities up to 500,000 t/a;
- Demonstrated MEG product quality meeting the fibre grade application requirements.