Sulphur 393 Mar-Apr 2021
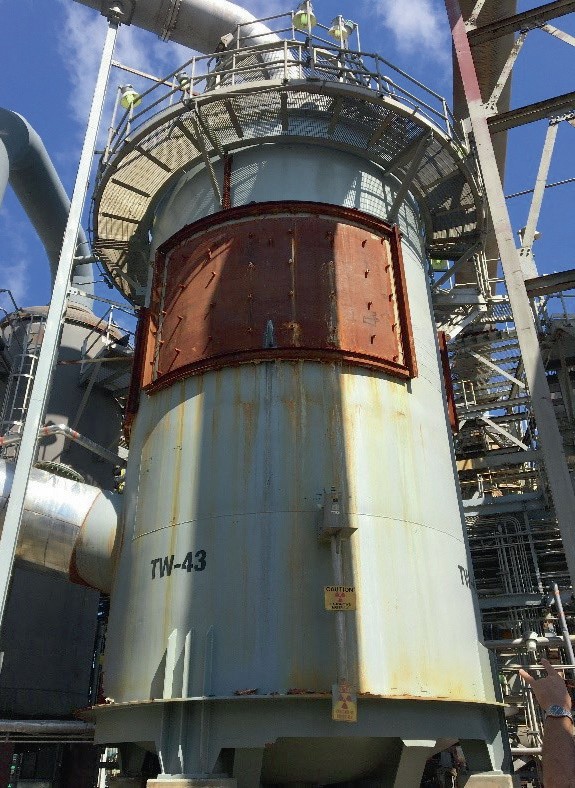
31 March 2021
A tale of two acid tower systems
ACID TOWER REPLACEMENT
A tale of two acid tower systems
All acid towers eventually require replacement. In this article, K. Sirikan, A. Mahecha-Botero et al of NORAM Engineering and Constructors Ltd discuss two recently executed acid tower replacement projects. The first project involved the replacement of a brick-lined tower by an alloy acid tower for a sulphur burning plant in North America. The second project involved the replacement of a brick-lined acid tower with a NORAM designed brick-lined tower for a smelter off gas acid plant in South America. The impacts of various design considerations on acid tower replacement projects are compared, including in-situ replacement versus a new location; brick-lined versus alloy shell, and selection criteria for mist eliminators.
The sulphuric acid plant typically consists of several strong acid towers utilising sulphuric acid between 93% and 99.5% w/w concentration with temperatures ranging from 50°C to 120°C.Within this operating range, the traditional design for acid towers uses brick-lined carbon steel for the bottom section of the tower with stainless steel 316L above the acid distributor. Over the last 25 years, the use of all-metal absorption towers, where high-silicon alloys such as NORAM SX® replaced the brick-lined carbon steel section, has gained popularity as the design offers several advantages such as reduced installation time for replacement towers.
This article discusses two of NORAM’s recent projects where acid towers were successfully replaced to upgrade the strong acid systems of existing acid plants, and compares some of the key tower design concepts, the selection of materials of construction and tower internals and execution strategies.
Reasons for tower replacement
Acid towers will eventually need to be replaced and upgraded due to a combination of factors including:
- plant operating conditions;
- mechanical integrity of equipment (endof-life, corrosion etc.);
- increasingly stringent environmental regulations;
- increased production requirements.
- reduce ammonia consumption (of a downstream scrubber system).
NORAM recently completed two different acid tower replacement projects as follows:
Project A required the replacement of an acid tower for a sulphur burning plant in North America. The existing acid tower had reached the end of its service life with numerous patches on the shell, necessitating replacement. The new tower needed to accommodate operation at the current capacity for the next five to ten years after which the plant capacity is expected to increase. The new tower was also designed to:
- reduce acid mist carryover;
- reduce SO3 slippage (based on absorption efficiency);
Project B consisted of the replacement of an acid tower for a smelter in South America. The existing acid tower had severe structural issues. The new tower was designed for:
- higher process gas flows and SO3 concentrations;
- higher absorption efficiency;
- increased acid circulation;
- reduced H2SO4 and SO3 emissions.
Fig. 1 shows the old acid towers which were replaced for the two projects.
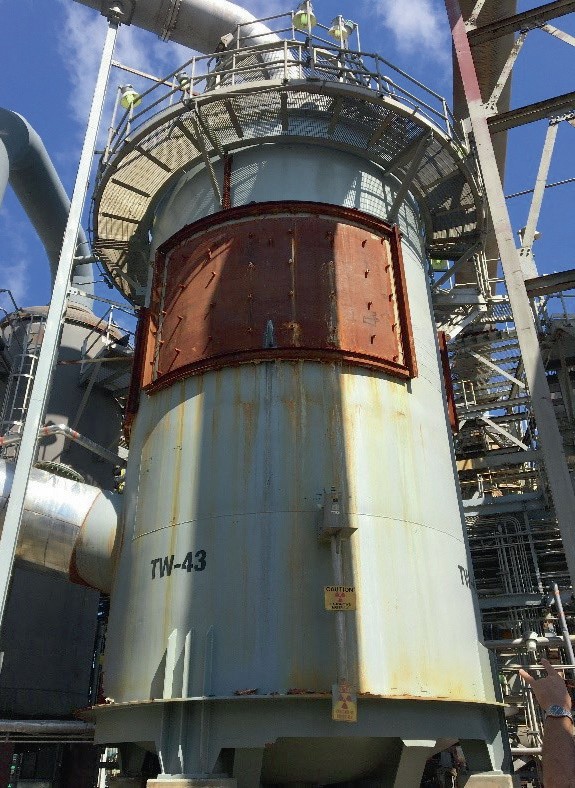
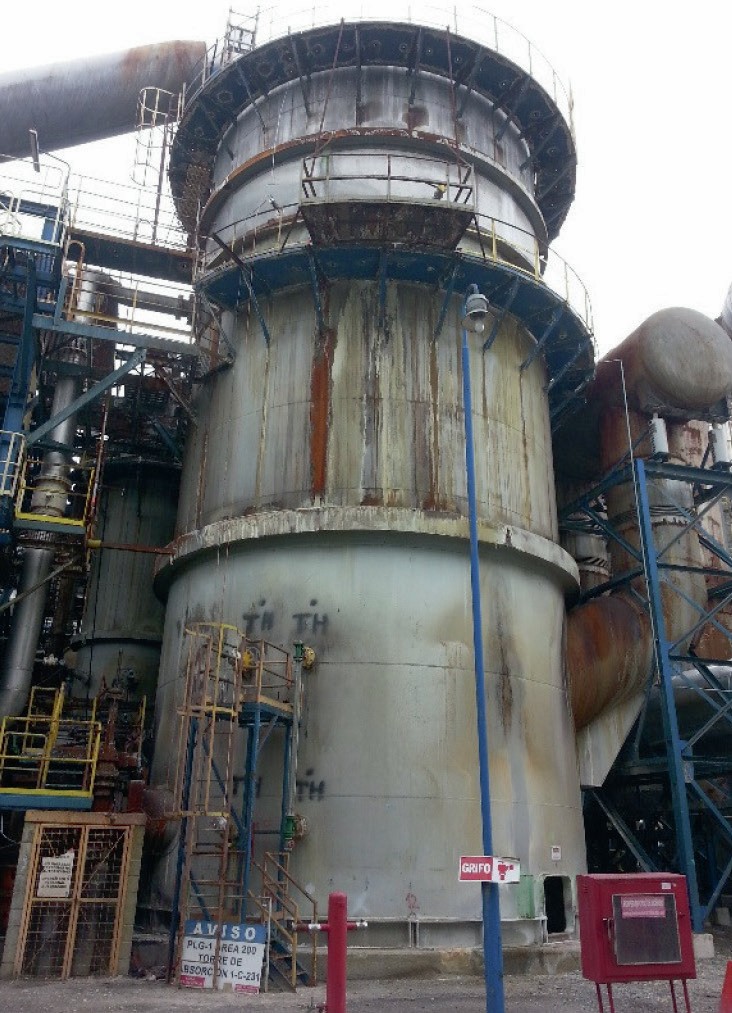
Design comparison
The design parameters and requirements of a replacement tower need to be agreed to and finalised at the start of any tower replacement project. There are many options for acid tower design including the selection of:
- materials of construction (brick-lined vs alloy);
- packing (type and height);
- mist eliminators (mesh pad vs candles; hanging vs standing candles; impaction candles vs Brownian diffusion candles);
- distributor (trough vs pipe);
- acid dilution (internal vs external);
- strainer (no strainer vs internal strainer vs external strainer);
- pumps (re-use vs new pumps; submerged vs external);
- piping (re-use vs new piping, alloy vs cast iron);
- ducting (re-use vs new, carbon steel vs stainless steel);
- supports and foundation (re-use vs new);
- instrumentation (re-use vs new).
The materials of construction and internals for both projects are summarised in Table 1.
Key features are described in more detail in the following sections.
Materials of construction
The materials of construction for acid absorption towers can be either carbon steel shell with brick-lined bottom section (below distributor) and stainless-steel top section or a combination of stainless steel and alloy for an entirely metal shell. The following requirements need to be considered:
- acid quality constraints;
- availability of specialised bricking contractors;
- available space at site for the new acid tower;
- installation time constraints and plant shut-down time;
- process design requirements (i.e. reduced emissions, increased capacity);
- project budget.
For Project A, a metal shell was selected to reduce the installation time as the on-site bricking component is eliminated. It was also designed to fit the existing foundation and to minimise modifications to the existing piping and ducting. For this alloy tower, the packing support was an alloy grid design spanning the entire tower diameter. These design decisions reduced the complexity and execution time of the project.
For Project B, a brick-lined carbon steel tower was chosen because it provides higher tolerance to acid quality variations in a smelter setting. For NORAM’s brick-lined tower, the packing was supported by a self-supporting ceramic dome with an open area of up to 60% providing a very low pressure drop.
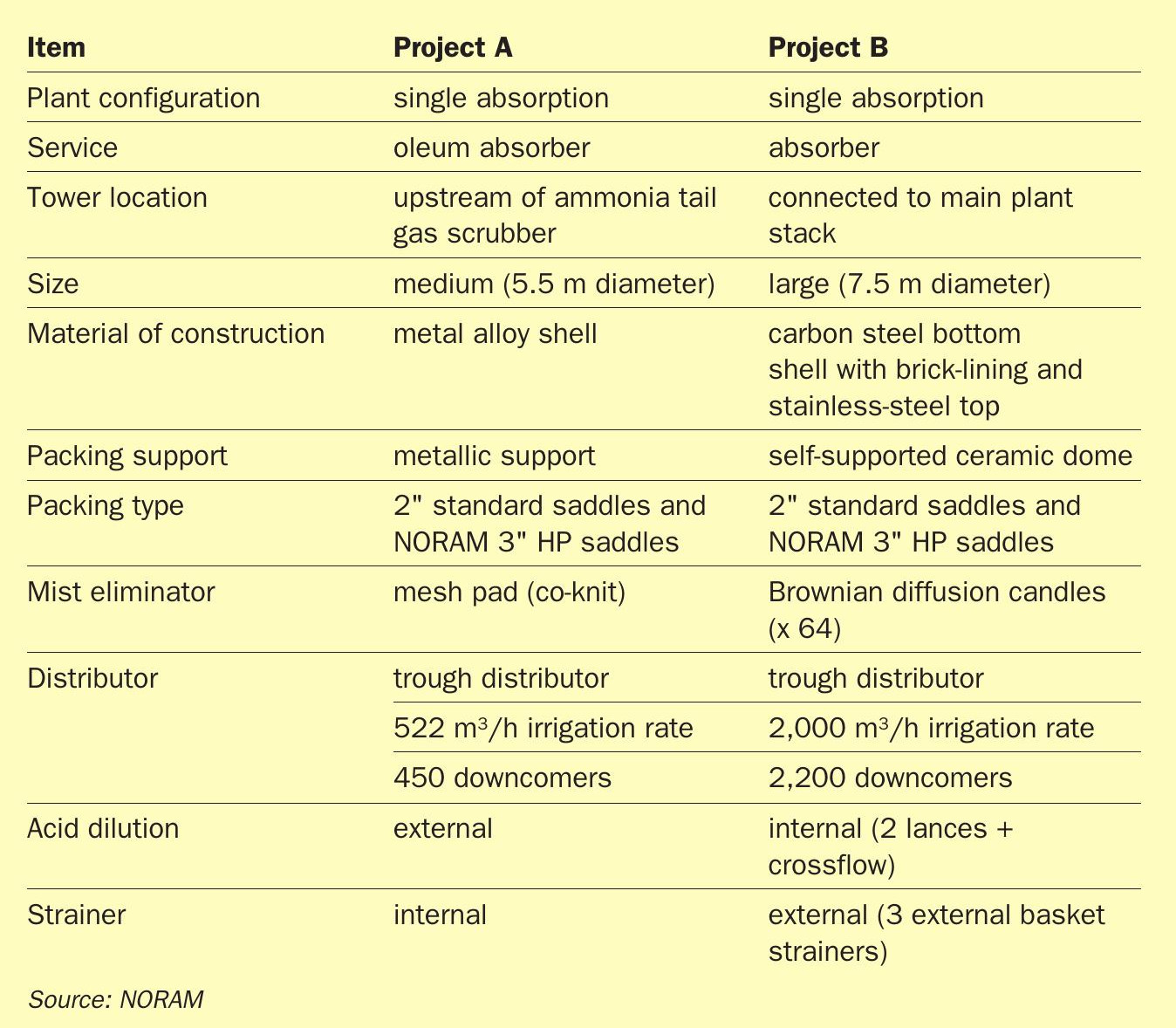
Fig. 2 shows different types of packing support utilised.
Mist eliminator
Acid towers are typically equipped with mist eliminators. The selection of the most suitable mist eliminator depends on:
- type of tower service;
- type of distributor;
- tower operating parameters;
- location of the tower;
- particle size of acid droplets.
Mesh-pads are typically used in drying tower service as the droplet size generated in drying towers is generally larger than ten microns and mesh-pads have high efficiencies for droplets larger than five microns.
Brownian diffusion (BD) candles are recommended for absorption tower service as the droplet size generated is mostly smaller than three microns in diameter.
For Project A, the old tower was equipped with a multi-layer mesh pad even though it is an absorption tower. High mist capture efficiency was not required as the tower is located upstream of an ammonia tail gas scrubber. One of the objectives of the replacement tower was to reduce ammonia consumption leading to the consideration of Brownian diffusion (BD) candles to improve mist capturing efficiency.
However, due to tower pressure drop requirements, a mesh pad (co-knit) was selected.
For Project B, Brownian diffusion (BD) candles were selected to provide the maximum practical acid droplet capture efficiency thereby eliminating acid mist emissions to the stack and to the environment.
Fig. 3 shows different types of mist eliminators.
Distributor
In both Project A and Project B, the client selected a NORAM trough acid distributor (see Fig. 4), which provides very uniform and well-dispersed acid distribution. Troughs with evenly spaced downcomer tubes distribute the acid by gravity into the packing for optimum performance and minimal spray formation. The design prevents debris in the acid from obstructing the downcomer tubes, and the acid flow in the troughs can be inspected during operation. It is particularly suitable for large and high-performance towers.
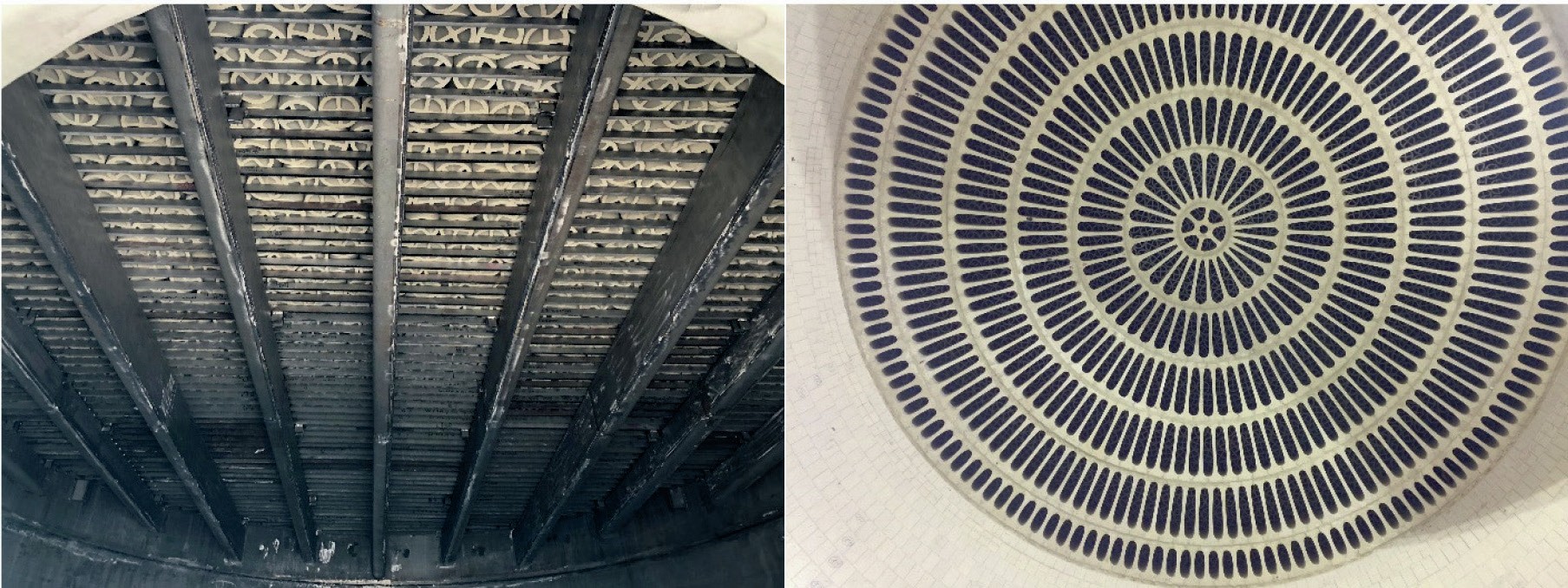
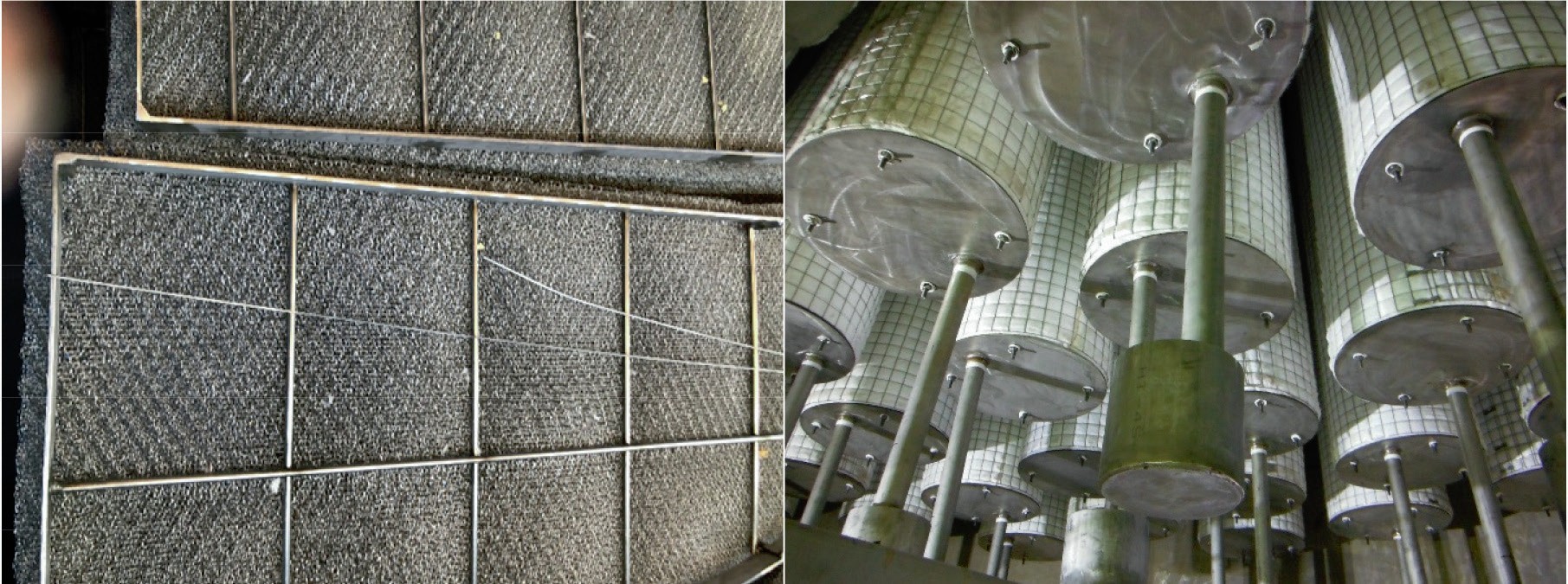
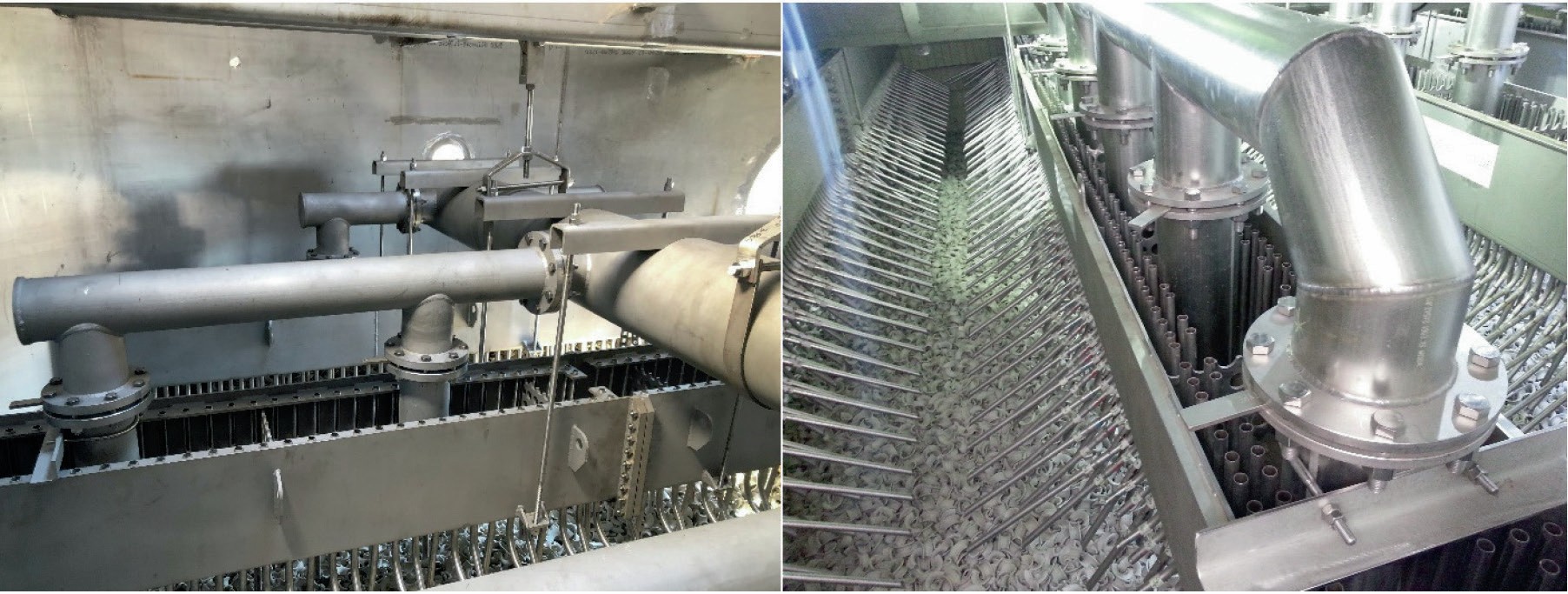
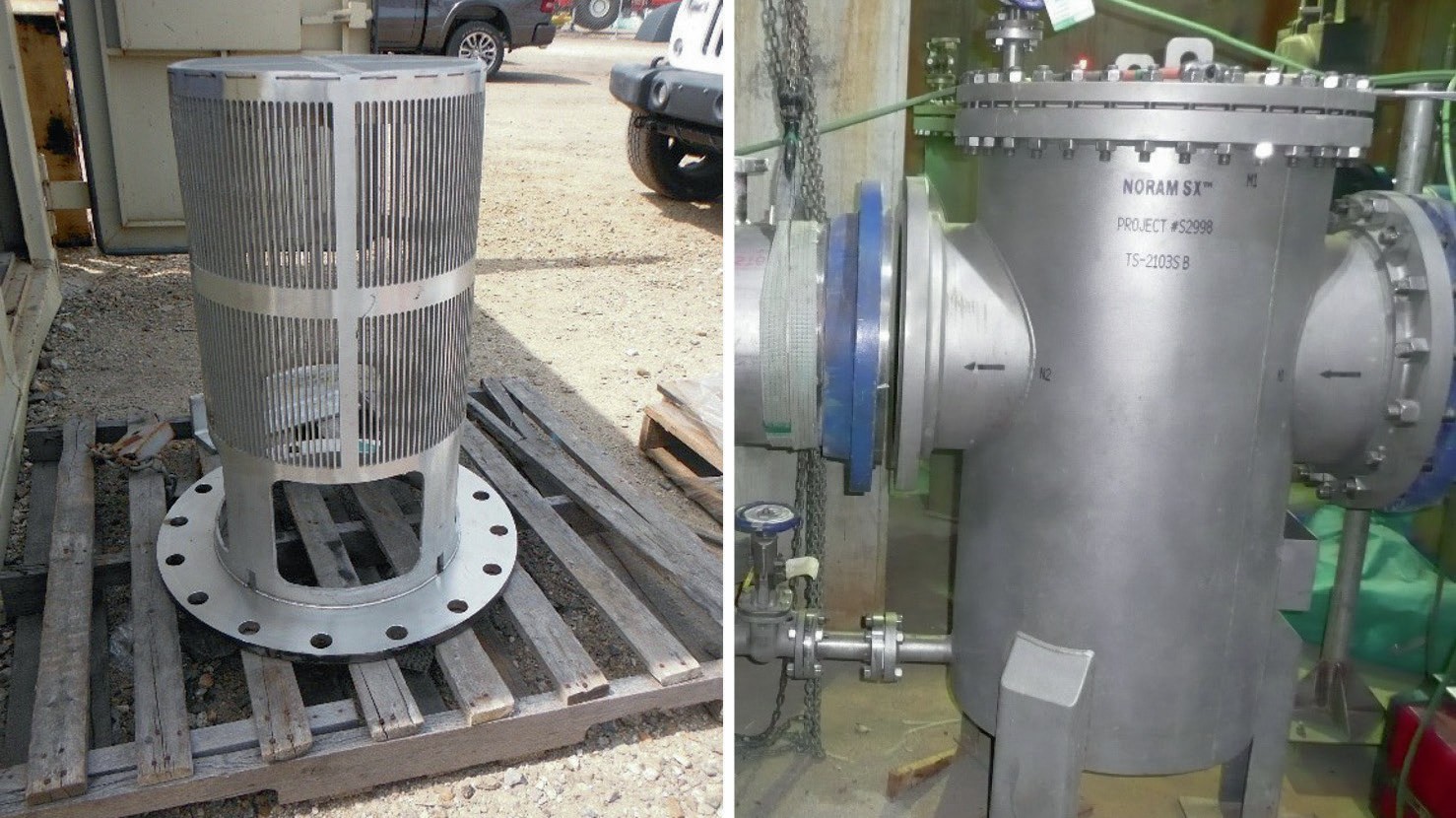
Pyrex™ sight glasses are installed above the distributor in the tower shell and permit viewing of distributor operation.
Strainer type
Installation of a strainer in the acid circuit is recommended as entrainment of solids, such as construction debris, ceramic packing chips, breakage from brick-lined equipment, and corrosion by-products, often cause problems in acid circulation systems. Two common types of strainer are (see Fig. 5):
- acid tower internal strainer;
- external in-line basket strainer.
For Project A, an internal strainer was installed inside the acid tower at the drain nozzle. This strainer was fitted into the drain nozzle.
For Project B, an external in-line basket strainer was installed in-line with the acid piping. This strainer was fitted with a removable metal basket located at ground level allowing for easy clean out, inspection and maintenance.
Execution strategy comparison
Several strategies can be considered to execute an acid system replacement project including the requirement to keep the plant running while the equipment is installed, equipment size and weight, available space at site, installation time constraints, plant shut-down time, crane capacity, layout and ducting considerations, etc. The execution strategies for the two NORAM acid towers replacement projects are summarised in Table 2.
Installation strategies
Both towers were supplied in rings and assembled on site.
For Project A, the tower was installed in the same location on the existing foundations which minimised the modification of platforms, ducting and piping. The tower was assembled, and the packing and distributor installed inside the tower on the temporary foundations and before lifting it into place. The overall installation time of this tower was relatively fast and was completed during the plant scheduled shutdown. The installation of the tower in the same foundation and re-use of ancillaries allowed for significantly simpler project execution.
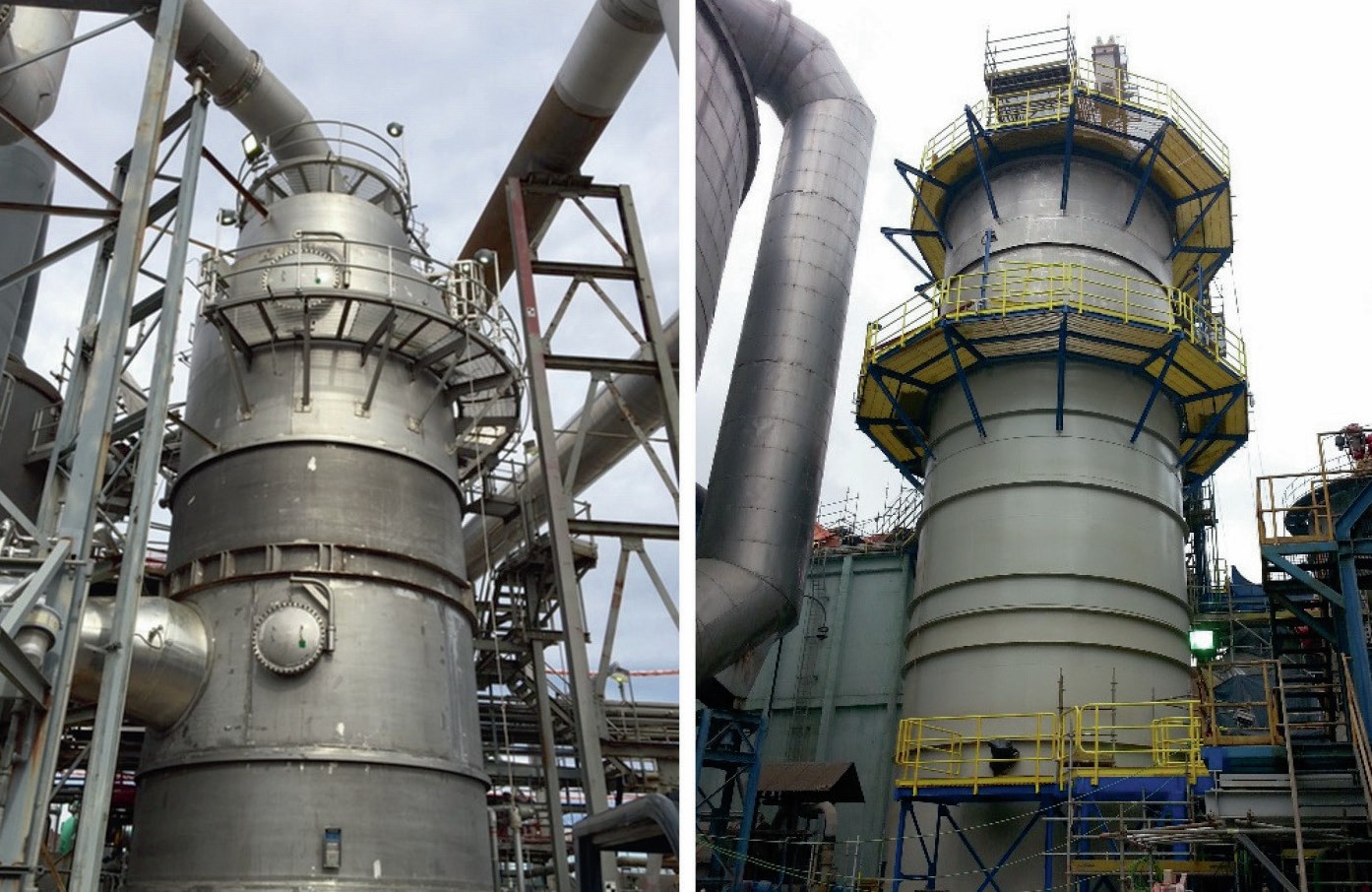
For Project B, the tower was assembled and installed on a new foundation, which required new platforms, ducting and piping as well as new acid pumps and external strainers. The brick lining and the installation of tower internals were completed at the tower final location. This strategy increased the overall project complexity and cost, but provided some technical advantages to meet the client requirements.
Commissioning and start-up
For Project A, the new system was commissioned during the plant scheduled shutdown. When the sulphur burning plant restarted, the acid tower and ancillaries were operated and monitored. The operation and performance of the system was confirmed as the plant was brought online.
For Project B, the new system was commissioned independently from the acid plant which was running normally using the existing tower. The new acid system including acid pumps, piping, strainers, acid circulation and distributor were operated to confirm all process parameters and to optimise the operation of the system. During a scheduled plant shutdown, the tie-ins to the new tower was completed and brought online to capture the SO3 gases from the smelter, while the environmental performance of the new system was confirmed.
Fig. 6 shows the NORAM acid towers for both projects.
Conclusions
This article compared the design and execution strategies of two acid system upgrade projects. Some of the early design decisions have a large impact on the overall project execution, capital costs and project schedule as illustrated by two markedly different projects. Working with an experienced engineering team is invaluable to acid producers to define the most suitable design and execution strategy to achieve higher performance, and reliability at most reasonable cost.
Acknowledgements
The authors Kam Sirikan, Andrés Mahecha-Botero, Igor Aksenov, C. Guy Cooper, Hongtao Lu, JP Sandhu, Brian Ferris, Brian Gilliland and Werner Vorster acknowledge colleagues and plant operators that have contributed to this paper. The paper was presented at CRU’s Sulphur + Sulphuric Acid 2020 Virtual Conference, 9-11, November 2020.
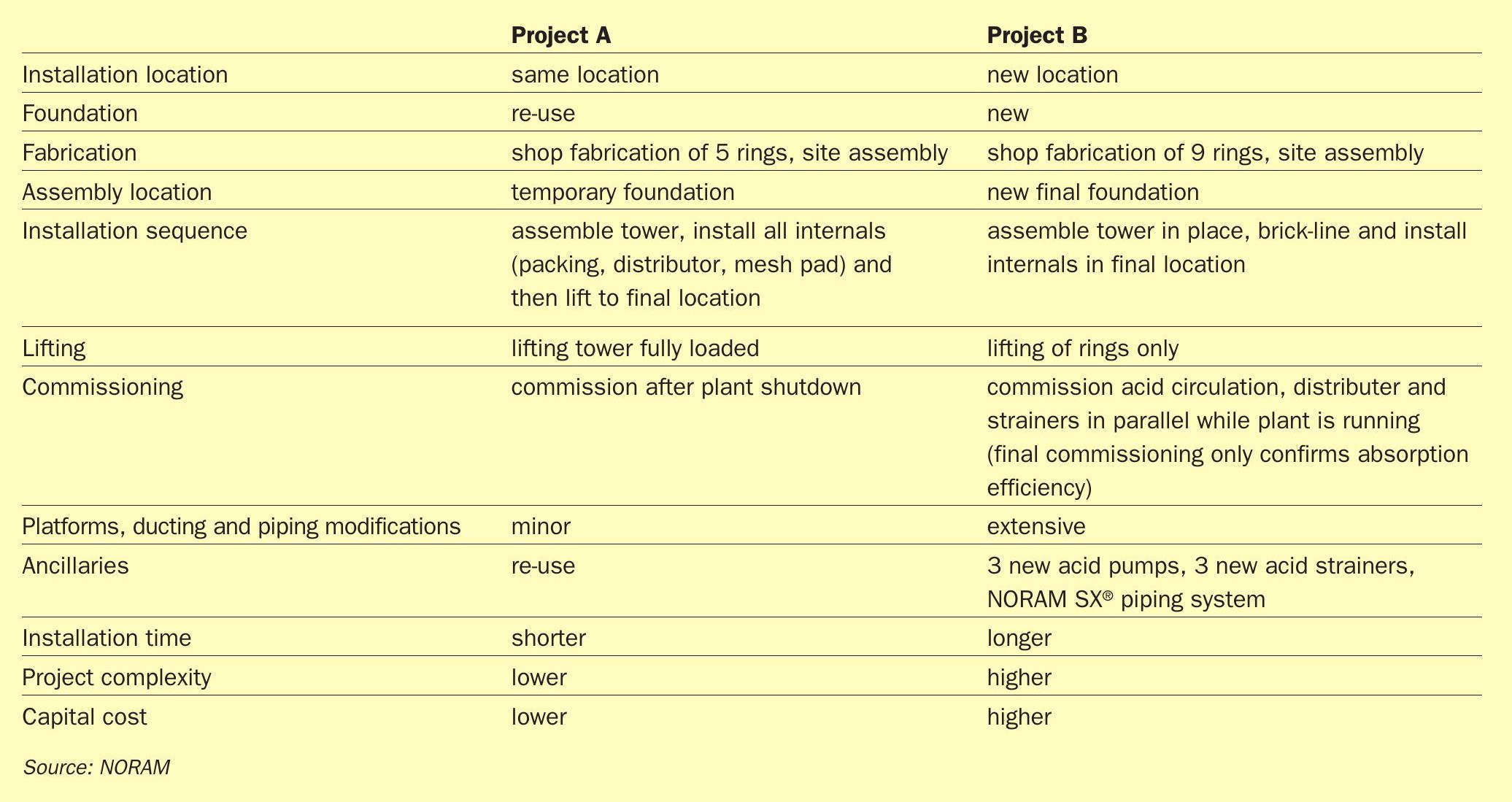