Sulphur 393 Mar-Apr 2021
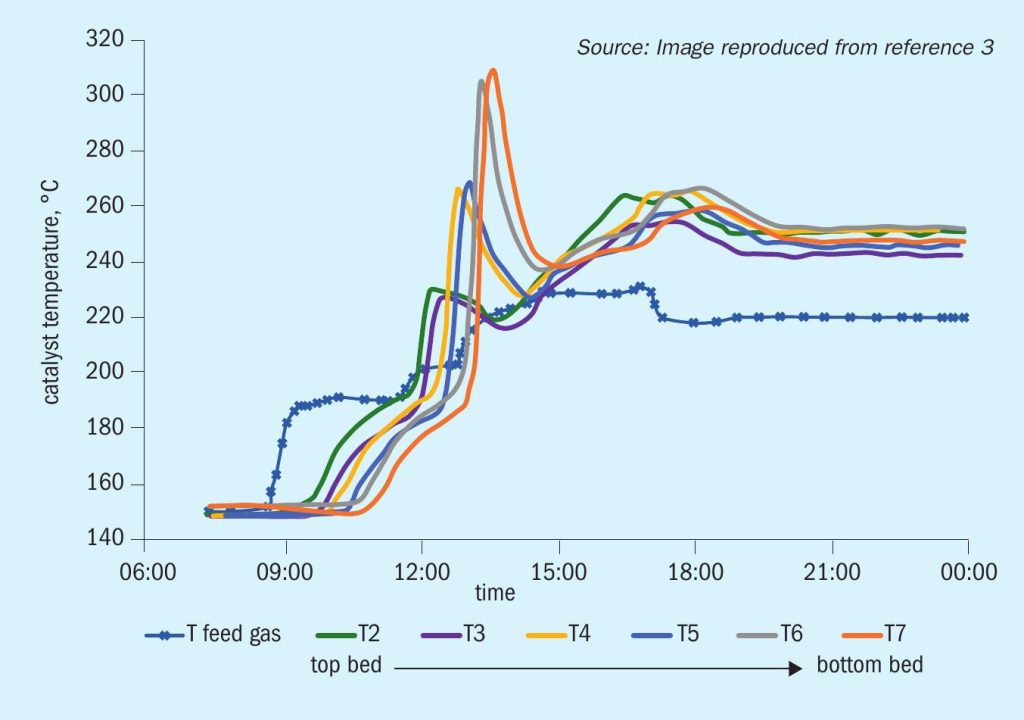
31 March 2021
The ease of titania-based tail gas catalysts start-up
TAIL GAS TREATING CATALYST
The ease of titania-based tail gas catalysts start-up
Euro Support’s new generation, titania-based low temperature tail gas catalyst shows a marked robustness to the start-up procedure compared to its common alumina-based counterparts. Dr B. Hereijgers of Euro Support discusses the promising lab results.
In Sulphur no. 369 Euro Support introduced its titania supported tail gas catalyst and highlighted the operational benefits on offer, especially for TGTU installations operated with steam reheaters at low temperature1 . Since then, Euro Support has received increasing signals from the field of users of low temperature tail gas treating units (LT-TGTU) loaded with traditional alumina-based LT catalysts that in-service operations are often fraught with hiccups. In particular, serious challenges exist to maintain the required low emissions over time.
When considering the operation of an LT-TGTU installation special attention to the catalyst start-up procedure is justified. As recently presented by Sulphur Experts, this involves a time-consuming and complex procedure whereby pristine catalyst is exposed to hydrogen and hydrogen sulphide containing gas to be transformed into the active sulphide phase2 . It has been shown multiple times in literature that a successful sulphidation is a measure of strict temperature control. For the high temperature application, the exothermic reaction should be curbed to prevent sintering of the catalyst, whilst under low temperature start-up conditions the main challenge is to make sure the exothermic reaction can heat up a sufficiently large portion of the catalyst bed to allow for deep sulphidation of the metals. Either way, the procedure requires tight process control and specific gas feed conditions, meaning that in the meantime the tail gas is routed to the incinerator leading to increased emissions. The big advantage of a high temperature system here is that a failed sulphidation can be restored by heating the bed in H2S/H2 to a temperature above 300°C. In case of a low temperature system the inlet temperature is simply limited to 240°C and once the catalyst is partially sulphided, an exothermic reaction is circumvented.
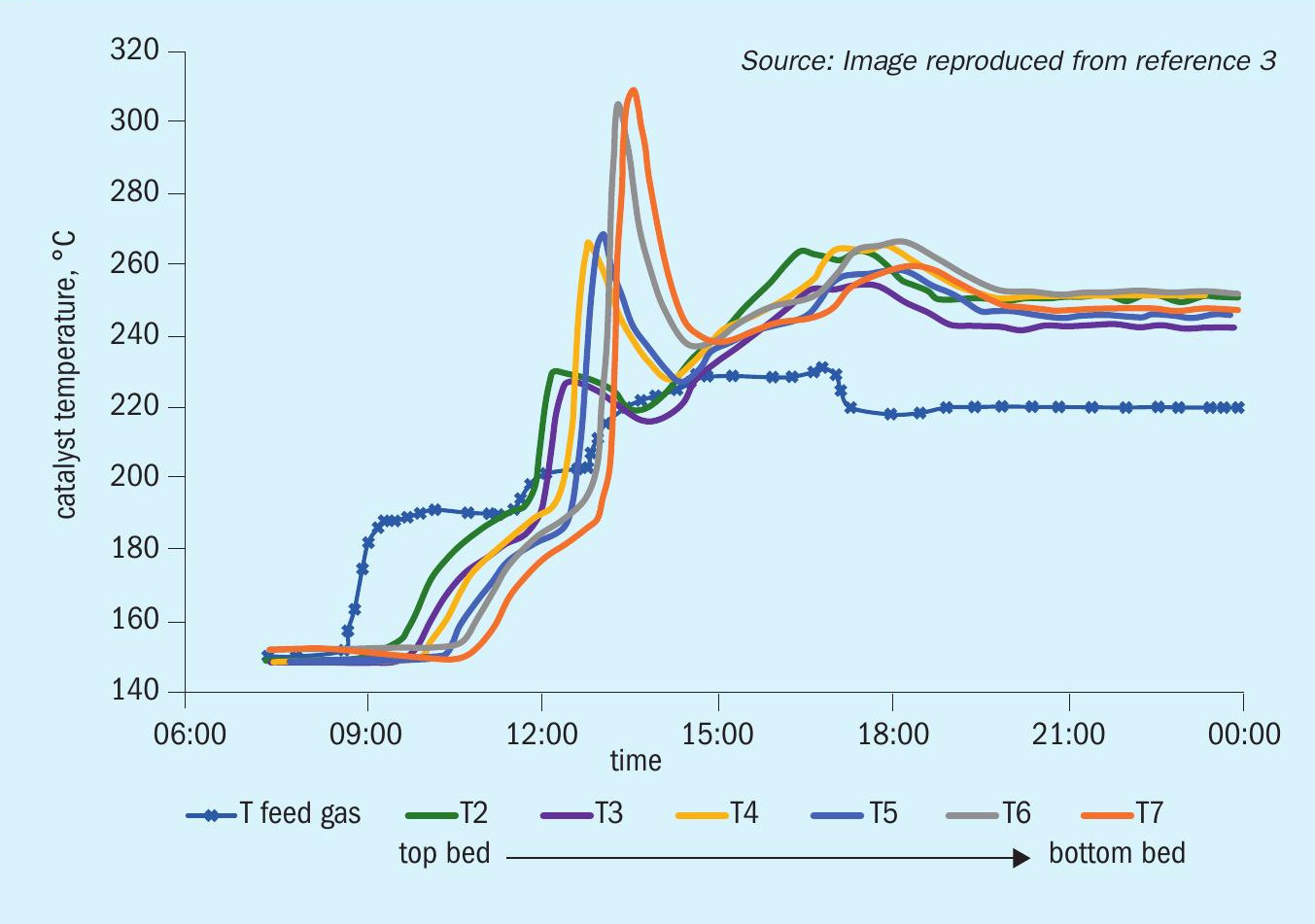
In a publication by Crevier et. al.3 from 2009, the actual temperature wave in an industrial reactor loaded with low temperature tail gas catalyst TG-107 was monitored in detail. A reproduction of the corresponding data is presented in Fig. 1. The conclusion was that about one third of the catalyst bed can reach a temperature above 300°C for a short time, whilst the remaining two thirds reached a maximum temperature around 260°C which could be sustained for 1-2 hours. This means that in practice, even when a perfect start-up procedure is performed, maximum one third of the loaded catalyst will be reasonably sulphided. Huffmaster et. al.4 reported that such a catalyst sulphided at 260°C can reach between 66-83% of the activity compared to the activity reached after start-up at 300°C and 10% hydrogen concentration. It should be stated though that even sulphidation of an alumina-based tail gas catalyst at 300°C is not as effective as a real high temperature sulphidation1 . In reality, the reduced activity that can be expected may cause a slip of sulphur compounds through the reactor. The nature of the different compounds can cause different operational problems for the TGTU as a whole; from increased SO2 emissions by COS and CS2 slip to the incinerator to sulphur fouling of the quench water and increased amine degradation by S8 and SO2 slip.
In this article Euro Support presents a new generation titania-based tail gas catalyst and shows the impact it has on the ease and robustness of the in-situ startup procedure compared to its traditional alumina-based counterparts.
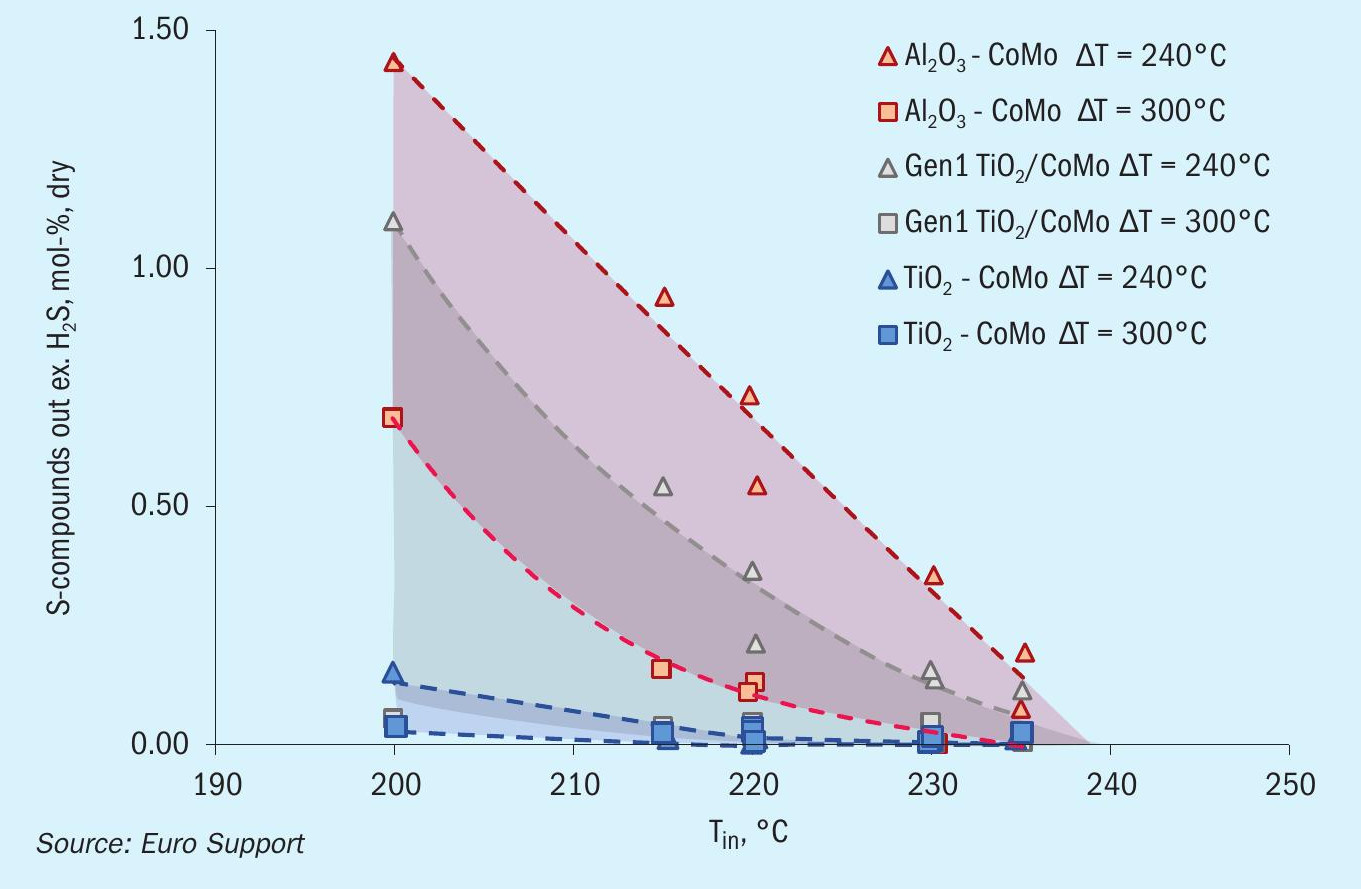
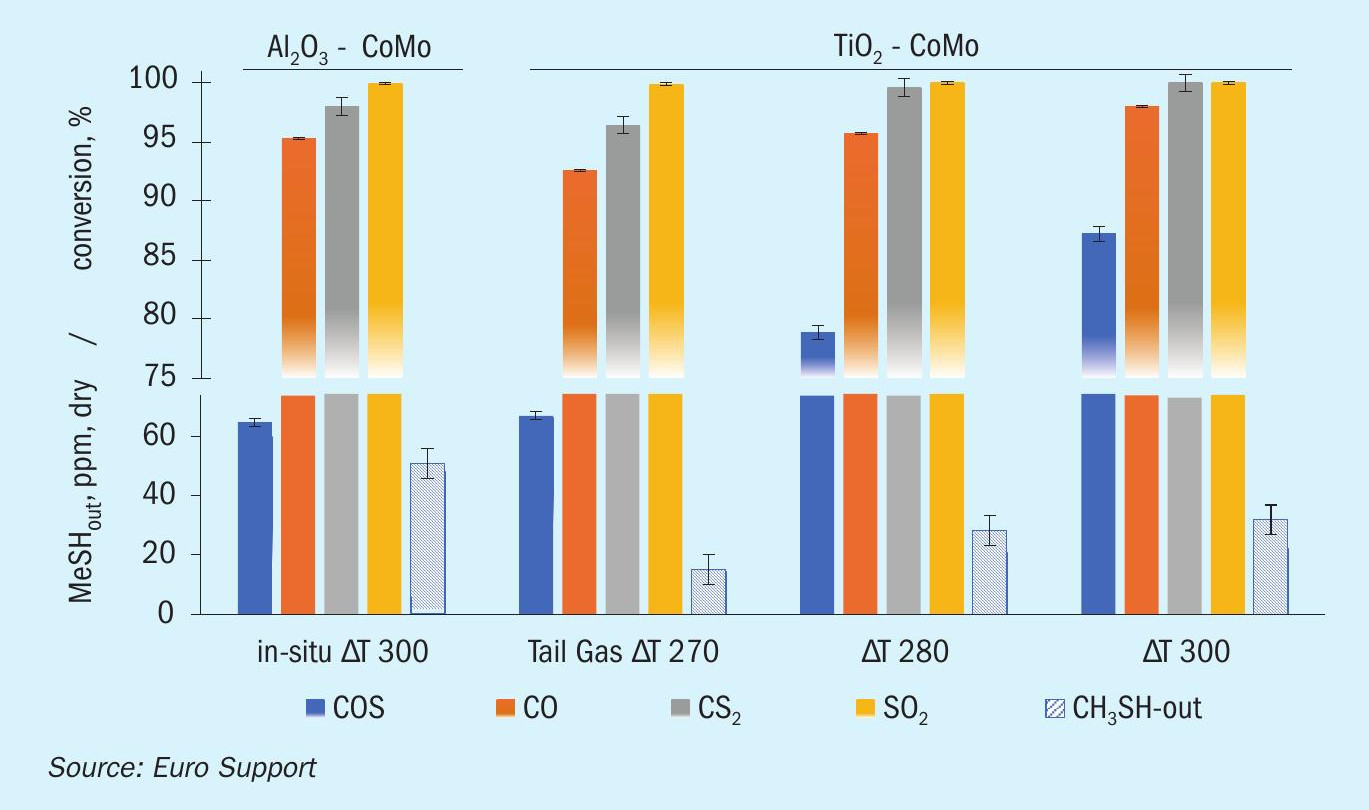
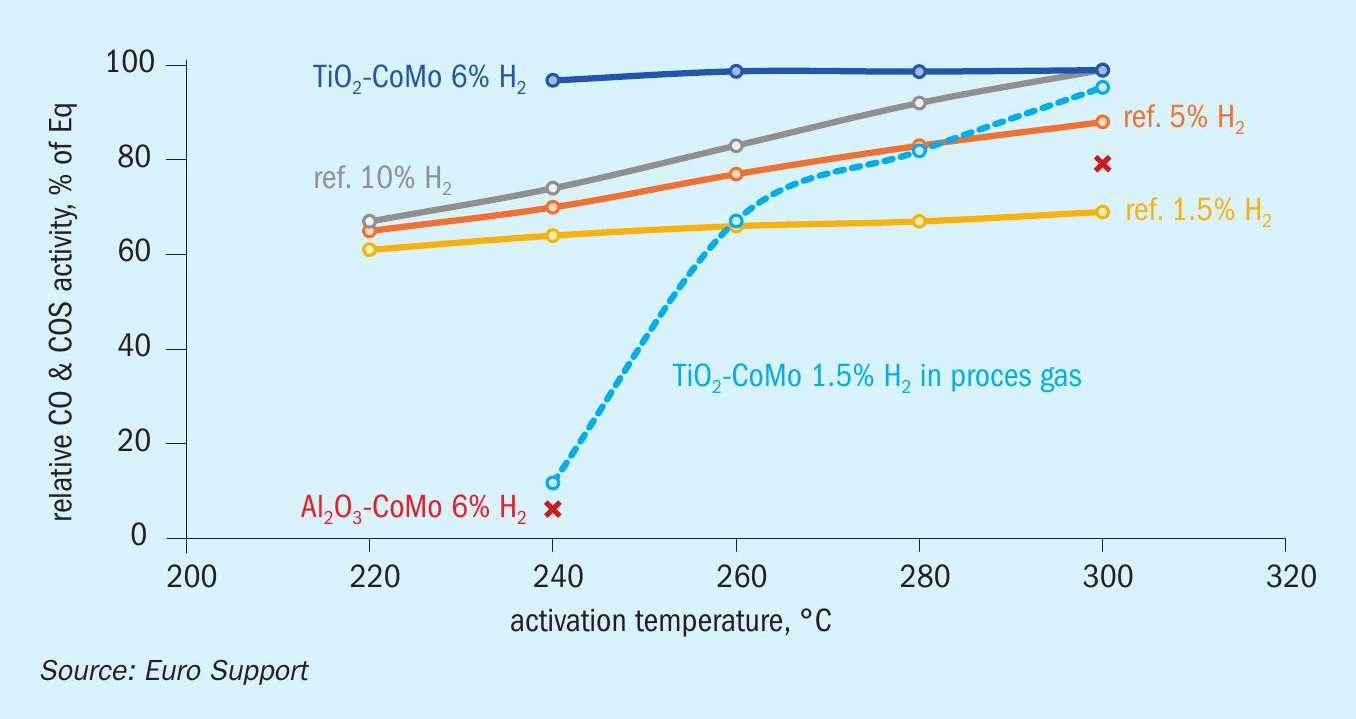
Results and discussion
Fig. 2 displays the total concentration of sulphur compounds (SO2 , CS2 , COS, methyl mercaptan and elemental sulphur, excluding H2 S) found in the reactor outlet of the TGTU catalyst as function of the reactor inlet temperature and maximum reached in-situ sulphidation temperature. This represents the total sulphur load that was not converted to H2S. The largest absolute contribution to the slip is in the form of elemental sulphur. The concentration of sulphur compounds was measured dry and free of elemental sulphur. The total sulphur load in the input gas was 2.0 mol-%.
In the graph, the performance of Euro Support’s new titania-based catalyst is compared to the alumina-based LT-TGTU catalyst and the 1st generation TiO2 /CoMo TGTU catalyst. Performance is plotted for two conditions where ΔT 240°C and ΔT 300°C indicate the maximum temperature that is reached by the heat wave from the exothermic reaction during in-situ sulphidation. These represent ‘worst-case’ (triangle) and ‘perfect’ (square) start-up procedures, respectively. The shaded area in between these lines (red for alumina and blue and grey for titania) represents the activity that can realistically be expected from the LT-TGTU catalyst. The graph for the alumina-based LT-TGTU catalysts shows that after perfect in-situ sulphidation an operation temperature of above 230°C is required to prevent slip of sulphur compounds already at start of run. The data suggests that a worst-case start-up makes it virtually impossible to operate at full conversion. In practice, the activity will fall in between in the shaded area, but in any event leaves limited room for the inevitable catalyst deactivation over time.
Although the first generation of TiO2 -CoMo catalyst readily outperforms an alumina-based catalyst under similar sulphidation conditions, the possibility to operate at start of run in the Tin < 230°C range still depends largely on the success of the sulphidation treatment, as indicated by the grey area in Fig. 2.
The new TiO2 -CoMo catalysts show a completely different picture. At inlet temperatures above 210°C both catalysts sulphided at 240°C or 300°C perform equally well and no slip in unconverted sulphur compounds was observed. This means that if the heat wave during in-situ start-up is lower than expected, because of not having the optimal conditions in the reactor, the catalyst will still be sulphided almost to its full potential, with no significant effect on catalyst activity.
From the data in Fig. 2 it can be concluded that TiO2 -CoMo shows a remarkable high activity towards sulphidation under mild conditions. This result raises the obvious question whether it would be feasible to successfully start-up a TGTU catalyst by simply exposing the pristine catalyst to Claus tail gas. After all, this would avoid the complex procedure and the chances of mishaps and permanent loss of catalyst activity.
Fig. 3 presents the performance of the TiO2 -CoMo catalysts at Tin = 240°C when no start-up treatment is performed. Activity is shown as a function of temperature (ΔT) that the catalyst was exposed to for four hours in the same Claus tail gas that was also used for the activity tests. The Al2 O3 -CoMo catalyst after best possible in-situ sulphidation at 300°C, is included in the figure for comparison.
It was found that when Euro Support’s new generation of TiO2 -CoMo catalyst is exposed to Claus tail gas at Tin = 270°C for four hours its performance roughly matches that of Al2 O3 -CoMo after the best possible in-situ start-up. When the temperature was increased slightly the performance could be enhanced even further. Although more research will be performed by Euro Support in the near future, these results already indicate that it is feasible to start a fresh TiO2 -CoMo TGTU catalyst without performing a specific start-up procedure. By optimising the gas composition to the right H2S:SO2 ratio and space velocity, performance may likely be enhanced further.
Recently Shell Catalysts & Technologies published a paper on effective activation of alumina-based low temperature tail gas catalysts4 . Although the reported sulphiding and test conditions are not identical to what are practiced at Euro Support’s labs, a useful benchmarking of results is provided. Generally speaking, the startup and test conditions in Euro Support’s tests are comparable, but somewhat more stringent to the catalyst, as compared to Shell’s reported stress test.
In Fig. 4 the data, as reported in the paper4 for a “representative low temperature TGU catalysts”, is compared with Euro Support’s test results for titania and alumina based catalysts under comparable start-up and operating conditions. Here activity is represented by the average CO and COS conversion as a fraction of the calculated equilibrium conversion5 .The data from Shell show a clear decrease in hydrogenation activity when sulphidation temperature or hydrogen gas concentration are decreased. Full conversion (99% of equilibrium) is only achieved after activation at 300°C in 10% H2 , which is not realistic under normal conditions. The best performing alumina-based catalyst only reached 79% of the equilibrium conversion under optimal sulphiding conditions, as applied in Euro Support’s tests. Euro Support’s new generation titania based CoMo catalysts compares favourably to all the alumina-based counterparts. Already at a sulphiding temperature of 240°C (meaning no exotherm in the bed), 97% of the equilibrium conversion is reached. If a minor exothermic reaction is experienced, that drives the temperature to 260°C, the catalysts reach full (99%) CO and COS conversion. Under all circumstances, the TiO2 -CoMo catalyst performs significantly better than any alumina based CoMo catalyst.
The dashed line in Fig. 4 represents the normalised CO and COS activity for this catalyst after exposing the catalyst to standard Claus tail gas with a H2S:SO2 ratio of 2, at the indicated temperature. Under these conditions the catalyst, albeit almost, cannot be sulphided to its full potential. On the other hand, considerably higher activity is still achieved compared to the alumina-based low temperature catalyst that is considered the market’s standard, in the same test. When a temperature above 280°C is reached in the catalyst bed with Claus tail gas, the activity is in the range of what would be considered as acceptable. If the start-up conditions were optimised to a higher H2S:SO2 ratio and increased H2 concentration the performance could likely be enhanced.
Conclusions
Euro Support’s new generation titaniabased low temperature tail gas catalyst shows a marked robustness to the startup procedure compared to its common alumina-based counterparts. Catalyst performance tests show that the alumina-based CoMo catalysts hardly get sulphided sufficiently under best possible in-situ start-up conditions to obtain an acceptable activity where no sulphur slip into the quench tower can occur, even at start of run. By contrast, the titania-based CoMo catalyst can be sulphided effectively in a worst-case scenario where virtually no exotherm in the catalyst bed is achieved.
Euro Support’s titania-based tail gas catalyst proved it is feasible that this kind of TGTU catalyst can exhibit sufficient activity even when no start-up procedure is applied. A simple activation in process gas under normal operation conditions has proven to be sufficient in the lab. More research is ongoing to map out the boundary conditions for successful operation.
Euro Support benchmarked the test data to literature performance data and although test and start-up conditions are different, the comparison underscores the superior performance of TiO2 -CoMo compared to its alumina-based counterparts under realistically applied start-up conditions.
Acknowledgements
Hana Svoboda, Michal Vesely, Dr. Oleg Bortnovskiy, Dr. Olga Gonsiorová and Jan Valenta (Euro Support Manufacturing Czechia s.r.o.) are kindly acknowledged for their indispensable contribution to these developments.
Experimental notes
All catalyst tests reported were performed in the test laboratories at Euro Support Manufacturing Czechia s.r.o. in a dedicated glass bench-scale test reactor of 30 mm I.D. loaded with 70 mL shaped catalyst.
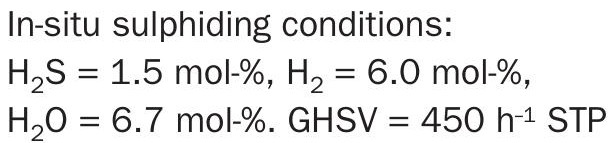
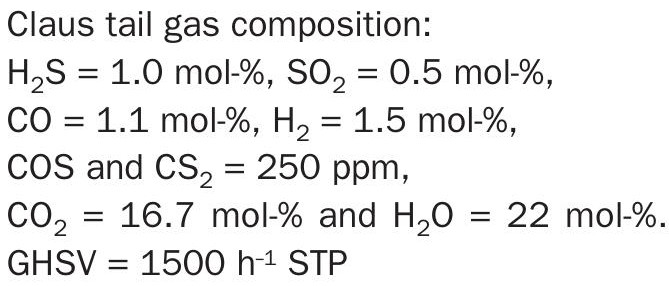
References