Fertilizer International 501 Mar- Apr 2021
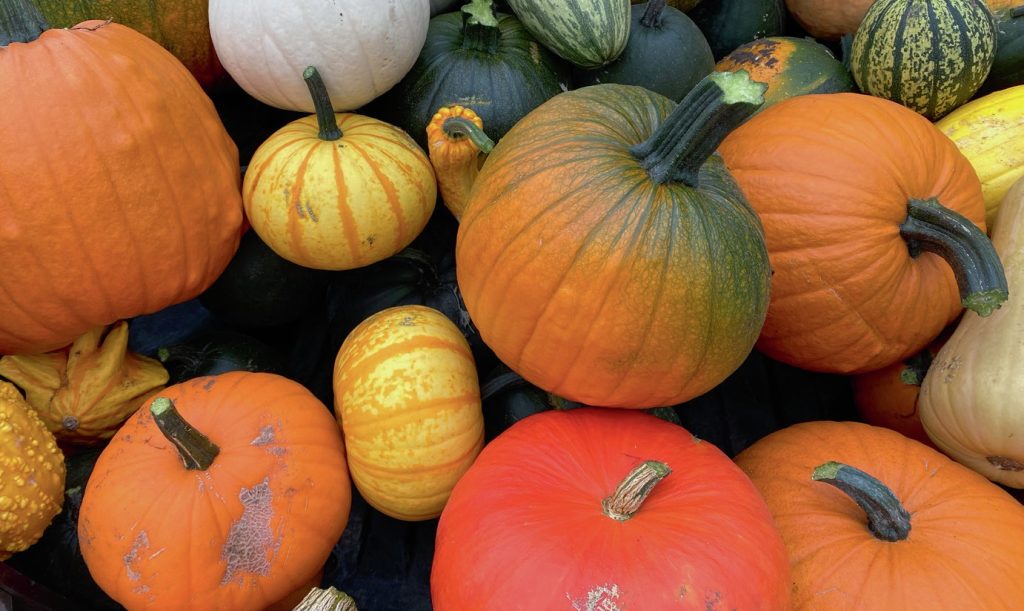
31 March 2021
Valuing phosphogypsum
PHOSPHOGYPSUM USE
Valuing phosphogypsum
Phosphogypsum is finding increasing use in plaster and cement manufacture, roadbed construction and afforestation. We look at how previously unwanted solid waste generated by the phosphate industry is being turned into a valued resource.
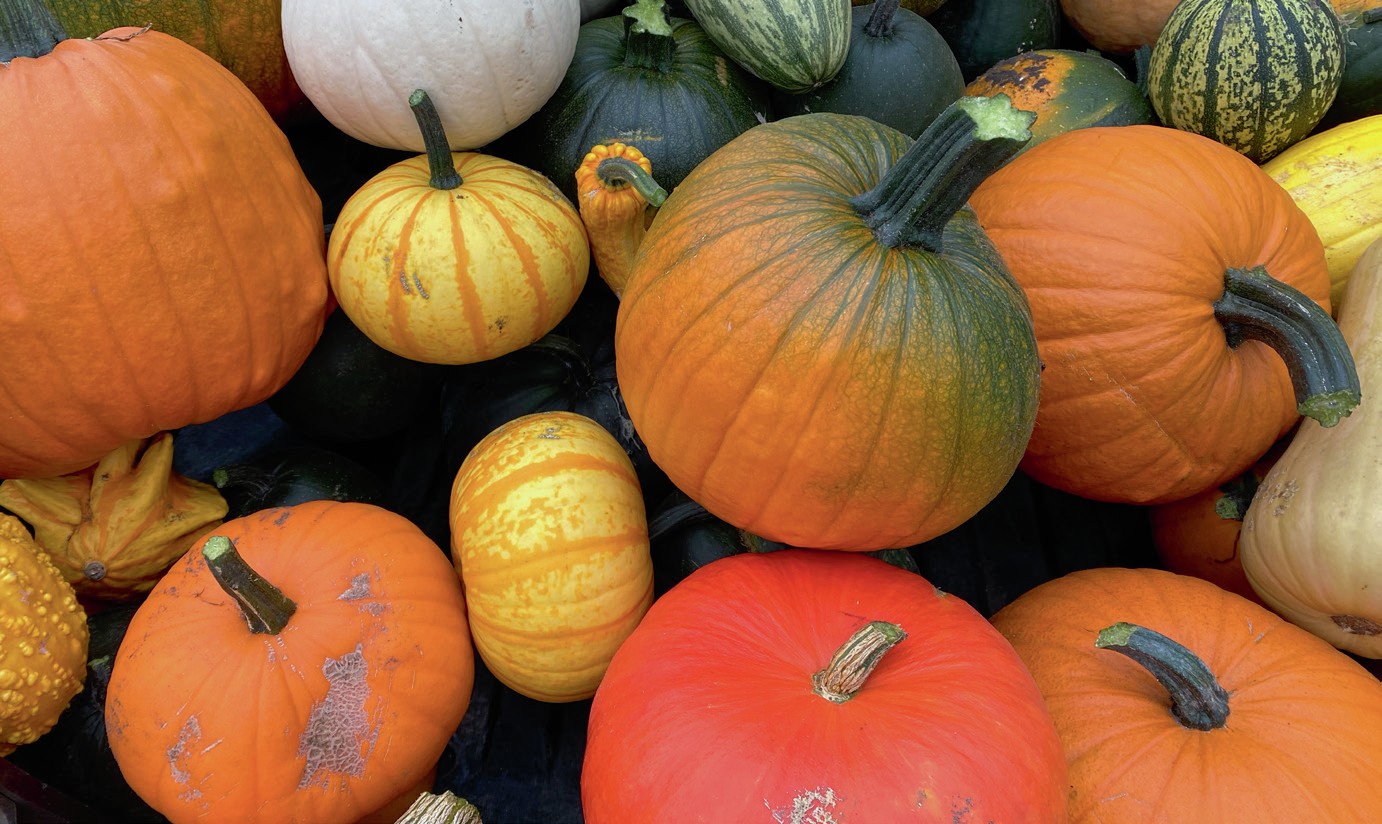
Greater commercialisation
As it expands globally, phosphate fertilizer manufacturing is generating ever larger volumes of phosphogypsum waste. Billions of tonnes of this material are currently being managed at great cost within giant waste stacks.
Nevertheless, phosphogypsum is finding increasing use as a co-product in agricultural, building and construction applications, particularly outside of the United States. This is a sign that the previously unwanted solid waste generated by the phosphates industry is becoming a valued resource (Fertilizer International 478, p58).
In recent years, there has been a clear shift away from desk studies and R&D towards commercialisation. Indeed, it is estimated that some 50-60 million tonnes of phosphogypsum is now being utilised worldwide1 . Notable examples of commercial phosphogypsum (PG) use include:
- Belgium (Prayon): sells high-quality PG for the cement and plaster market.
- Brazil: most PG now goes to agriculture (5 million t/a) following its reclassification.
- Canada (Nutrien): PG for agriculture and, working with forestry service, afforestation using man-made ‘anthrosols’ – PG mixed with soil in a 9:1 ratio.
- China (Wengfu Group): more than half of PG output is used in agriculture and construction, or recycled as ammonium sulphate/calcium carbonate.
- Kazakhstan (UN): large-scale remediation of saline/sodic soils.
- India: PG reclassified as a co-product, not waste, in 2008. Widely sold for construction, agriculture, soil additive, cement and as bagged fertilizer. Examples include afforestation for green energy (Coromandel) and road construction (Paradeep).
- Russia (PhosAgro): use of PG in agriculture, construction and road building
- Tunisia (GCT): remediation and return of land to productive use in Sfax, brick-making, road construction and housing.
The phosphate industry globally has also benefitted from a growing evidence base on phosphogypsum usage. The International Fertilizer Association (IFA), through its PG Working Group, has played a leading role in promoting phosphogypsum reuse. The association published a comprehensive landmark report on the sustainable management and use of phosphogypsum in 20162 . This was followed last year by a compilation of peer-reviewed case studies written by IFA member companies on the use of phosphogypsum in agriculture/forestry, construction and road building3 . The 10 diverse case studies presented, together with four national overviews, were global in scope, covering developments in Belgium, Brazil, Canada, India, Morocco and Russia.
The impressive evidence assembled in IFA’s latest report provides examples of current best practice, together with core principles for phosphogypsum management and use. Three exemplary case studies illustrating the value of phosphogypsum in agricultural/forestry, construction and road building are provided below.
Construction: Prayon leads the way
Prayon provides a leading example of a successful circular economy approach to phosphogypsum use. The leading technology licensor, phosphates producer and equipment manufacturer has actually been selling gypsum as a co-product for more than forty years4 .
The company sells virtually all of the phosphogypsum it produces at its phosphoric acid plant in Engis, Belgium, compared with 80-90 percent 4-5 years ago3 . In 2018, for example, Prayon sold 708,000 tonnes of phosphogypsum for plaster and cement manufacture, with a further 60,000 tonnes sold for agronomic use, from output totalling 790,000 tonnes.
When it comes to selling phosphogypsum, Prayon attributes its successful track record to several factors: notably the quality of its product, which in turn is attributable to the Central Prayon Process (CPP) used at its Engis plant, and the company’s long-term partnerships with its gypsum customers4 .
The CPP, with its double crystallisation process and two filtration steps, is exceptionally efficient (Fertilizer International 481, p49). The process is, however, only responsible for about one percent of total phosphoric acid production globally. Key feature of the CPP include:
- Flexibility: process can accommodate a wide range of phosphate rock types.
- High recovery: reduces phosphate rock consumption and generates a saleable gypsum co-product.
- High P2 O5 content in the filtered acid: reduces steam and therefore energy consumption.
- Self-drying gypsum: phosphogypsum from the CPP process naturally cures from wet hemihydrate (HH) to dry dihydrate (DH), meaning less fuel oil is required to process gypsum.
- Environmentally-friendly interim storage: neutralised phosphogypsum with a low P2 O5 content is stored as a temporary ‘gypsum quarry’ not as a waste stack.
Prayon’s commercial end-customer Knauf established a plaster production plant close to Engis in Belgium on the opposite bank of the River Meuse. Phosphogypsum from Prayon’s production plant is transported by conveyor belt across the river to a discharge point where it is temporarily stored.
Over a period of several weeks, the phosphogypsum cures naturally in-situ, reverting from wet hemihydrate (HH) cake (18% free water, 6% crystalline water) to rehydrated dry dihydrate (DH, 5% free water, 19% crystalline water). The resulting gypsum product requires no further treatment prior to its shipment down river by barge to Knauf’s stucco plaster factory.
In 2018, some 90 percent of phosphogypsum generated by Prayon at Engis met Knauf’s HH feedstock specifications, while eight percent was used in agriculture, leaving just a minor volume in the interim storage area.
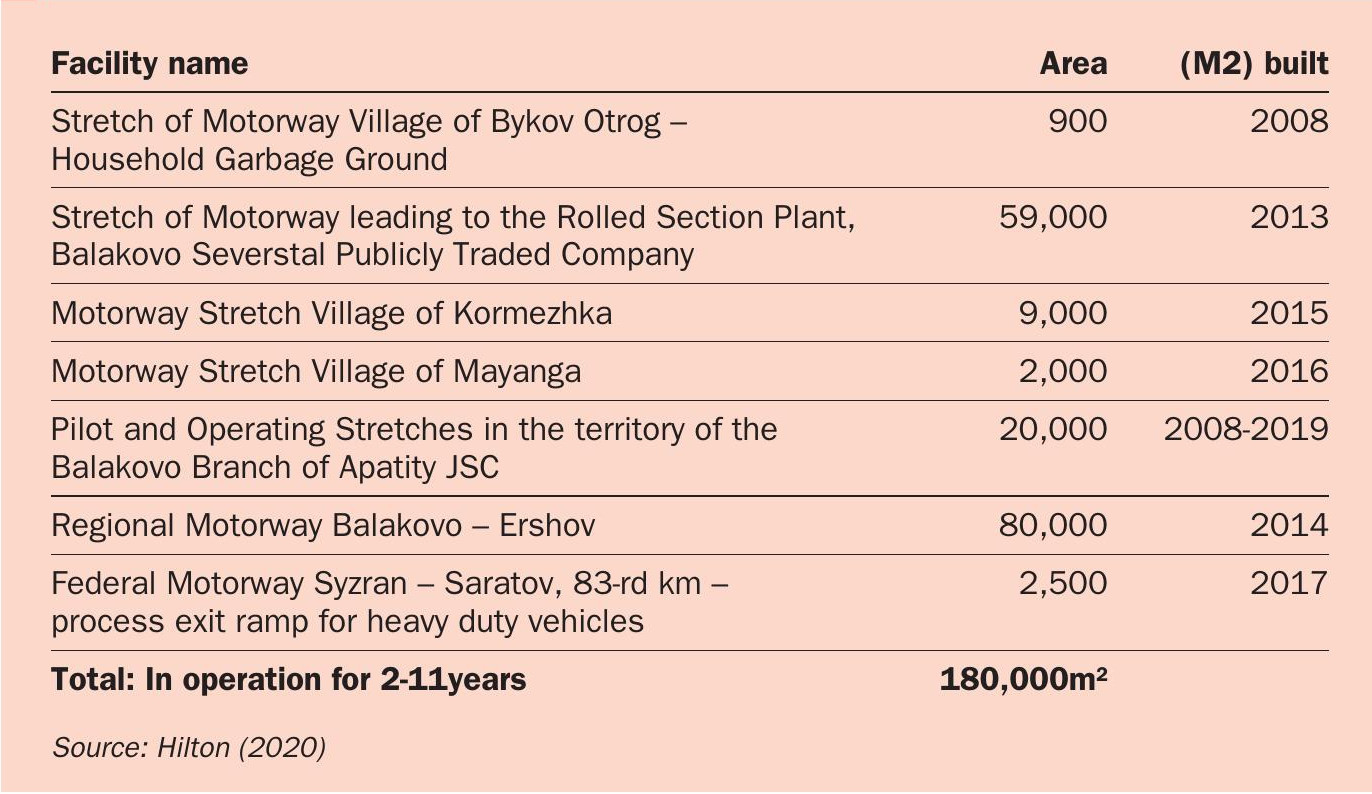
Prayon is currently collaborating with the British company Carbon Cycle on the innovative PureGYP process4 . This novel purification technology is designed to clean phosphogypsum so that it can be sold, rather than stacked, and offers the following advantages:
- Extracts fluoride and phosphate making phosphogypsum suitable for cement and plasterboard manufacture
- Typically removes 96 percent fluoride and 99 percent phosphate
- Widens the range of usable phosphate rock sources
- Has the potential to convert phosphogypsum stacks into valuable raw material quarries.
Roadbuilding: examples from Russia
Roadbed phosphogypsum (RBPG) is an innovative material for road construction produced by the Balakovo Branch of Apatit, a wholly-owned PhosAgro subsidiary3 .
The product’s specifications were approved by Russia’s Federal Road Agency in 2018 for three years. This authorises the use of RBPG in road construction and repair. To date, the total area of roads constructed using RBPG, including experimental pilot stretches, is around 180,000 m2 , these having a service life of between two and 11 years.
Notably, a 2,500 m2 stretch of the Syzran–Saratov motorway (83rd kilometre) was built in 2017 using RBPG, with the approval of local federal authorities in Povolzhupravtodor. This was part of seven road stretches constructed in Russia using RBPG between 2008 and 2017 (Table 1).
RBPG combines large volume availability, affordability, simplicity and safe handling with high operational performance and environmental safety. Its key advantages include:
- Tensile strength up to 10 times higher than required benchmarks
- Elasticity modulus up to two times higher than required benchmarks
- Eliminates the need for a sand drainage layer in road construction
- Road performance maintained in marshy terrain l Low propensity to heave during winter (freeze-thaw)
- An operational warranty as a road base of not less than 12 years l No detectable negative environmental impacts.
Overall, RBPG has proven economically viable as a secondary resource for road construction due to its ability to substitute for primary raw materials without compromising roadway performance. Indeed, cost-benefit analysis suggests that replacing conventional materials with RBPG in road construction could deliver cost savings of 21-35 percent3 .
Technology: helping phosphogypsum join the circular economy
Technology has a key role to play in generating commercially valuable and saleable ‘clean’ gypsum as a co-product of phosphoric acid manufacture. Germany’s thyssenkrupp Industrial Solutions, for example, is developing a viable treatment process for phosphogypsum, based on the OSW-Krupp method (see accompanying article on p48).
The dihydrate (DH) process from Tech-nip Energies also generates good quality phosphogypsum suitable for industrial reuse. In our forthcoming May/June issue, Philippe Malsan, the company’s Fertilizer Consulting & Technology Manager, will present industrial cases studies from Senegal and Austria – to show how phosphogypsum from this process has been successfully recycled on a large scale for cement, plaster and other end uses.
References
Using phosphogypsum to create soil and combat climate change
The conventional way of reclaiming phosphogypsum (PG) stacks is to cover their surface with a thick layer of soil. When Nutrien began researching alternative methods of PG stack reclamation in Alberta, Canada, in 2005, the company discovered that reclamation could be improved by mixing small amounts of soil directly into weathered PG. This created a man-made soil known as an ‘anthrosol’. Nutrien’s Connie Nichol explains more about this highly beneficial discovery.
Creating healthy soils for trees
“It was found that any amount of soil mixed into weathered PG grew larger, healthier biomass than plants grown in soil alone. Nutrien then investigated the possibility of growing trees in the PG mix to reduce long term maintenance costs and increase sustainability – while also creating value and sequestering carbon.
“Approximately a thousand hybrid poplar (Populus spp) and hybrid willow (Salix spp) cuttings were planted into a PG/soil mix in 2015 and found to grow extremely well. Based on this success, approximately twenty hectares of PG stacks were reclaimed and planted to high yield afforestation plantations in 2016 and 2017 following the protocols developed by the Canadian Wood Fiber Center, Natural Resources Canada.”
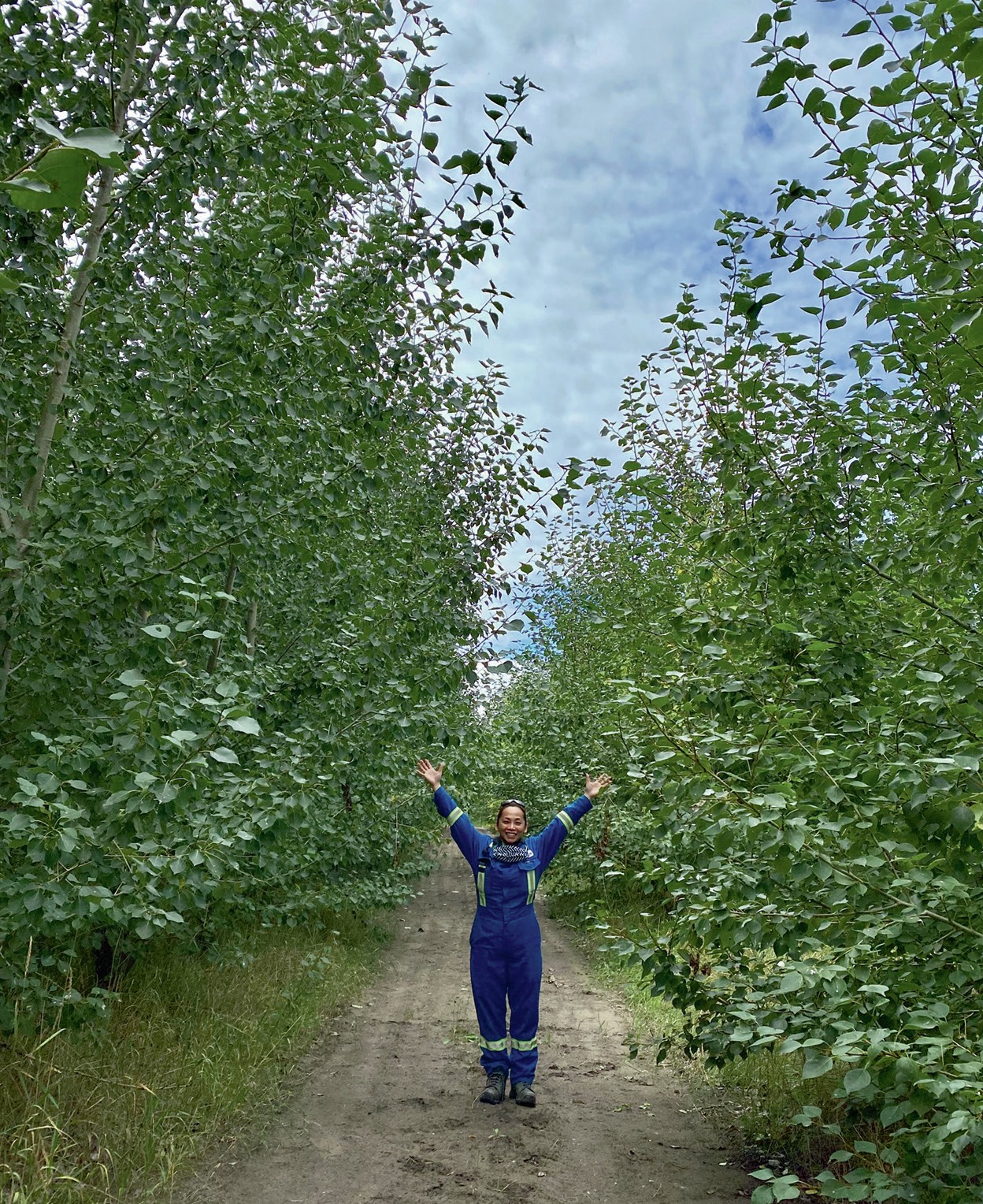
Rapid tree growth
“These trees are growing very quickly. As an example, between 2016 and 2017, the hybrid poplar cultivar Tristis grew from an average height of 85 cm to 280 cm, a height gain of almost two metres in a single year. Crown closure has been observed in some species after less than three years. This inhibits vegetation growth beneath the trees, with the site essentially left in a free-to-grow state without any need for maintenance.
“Trees are observed to be growing much faster on the gypsum stacks than the same trees growing on regular soil. This is likely because the PG has excellent water holding capacity and some residual plant nutrients.”
Carbon sequestration and biomass for energy
“The tree plantations established at Nutrien are predicted to sequester 30 tonnes CO2 equivalents per hectare per year. Thus, in 20 years, the gypsum stack area reclaimed to date will sequester 12,000 tonnes of CO2 equivalents. This same area is also predicted to produce 10 oven dry tonnes/ha/year of above ground woody biomass.
“It is therefore estimated that 4,000 green tonnes will be produced in this area over the next 20 years. These numbers will continue to increase as Nutrien continues to reclaim and establish concentrated woody plantations on their PG stacks.”
Myriad environmental benefits
“Establishing a forest on top of PG stacks has many positive impacts on the environment. The afforestation approach to PG stack reclamation will increase carbon sequestration and generate carbon dioxide offsets as well as produce biomass for energy production. Trees are also capable of phytoremediation of any excess nutrients and water within their rooting zone, thereby improving long term groundwater quality.
“University research indicates that there is little or no water infiltration into the gypsum stack under the concentrated tree plantations in the semi-arid climate of the Canadian prairies. Incorporating trees into the reclamation plan will also improve the long term sustainability and ecological diversity while also reducing long term maintenance costs. Increased wildlife such as deer, rabbits, foxes, small rodents and many birds have been observed in the forested areas.”
Food production
“The phosphogypsum/soil (anthrosol) can also be used to grow many other types of high value crops. Nutrien has established a small research garden on top of the PG stack and has tested various flowers, fruits and vegetables such as raspberries, potatoes, tomatoes and pumpkins (see photo).
“Analytical results indicate that the quality of the vegetables are the same or better than plants grown on regular soil. Future research will include expanding pollinator habitats and working with local beekeepers to investigate other opportunities to create value in situ.”