Nitrogen+Syngas 371 May-Jun 2021
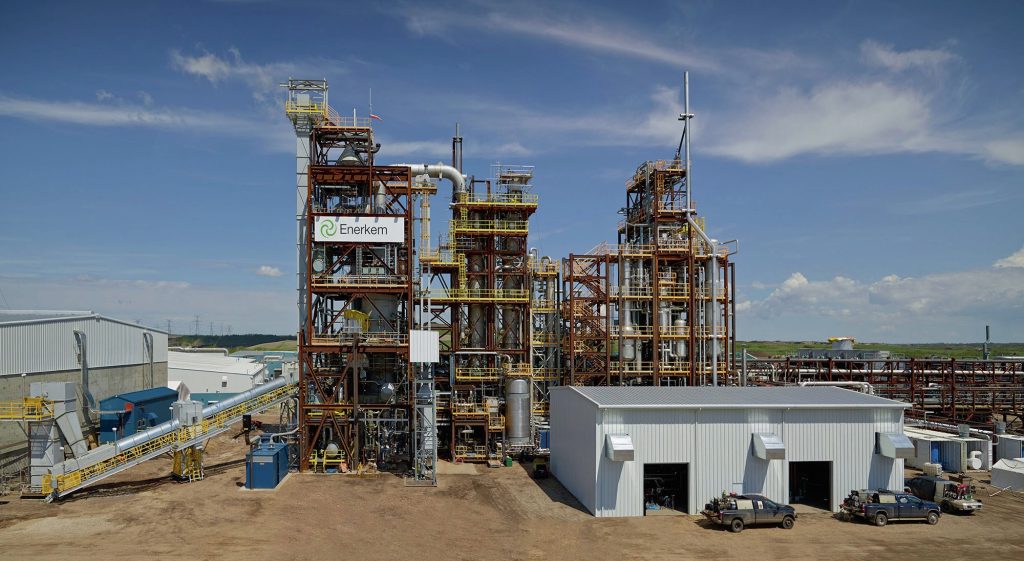
31 May 2021
Syngas from waste
GASIFICATION
Syngas from waste
Gasification technology offers the promise of being able to convert the increasing volumes of municipal waste generated by society into useful chemical products. In spite of a patchy commercial record, interest in the process remains high.
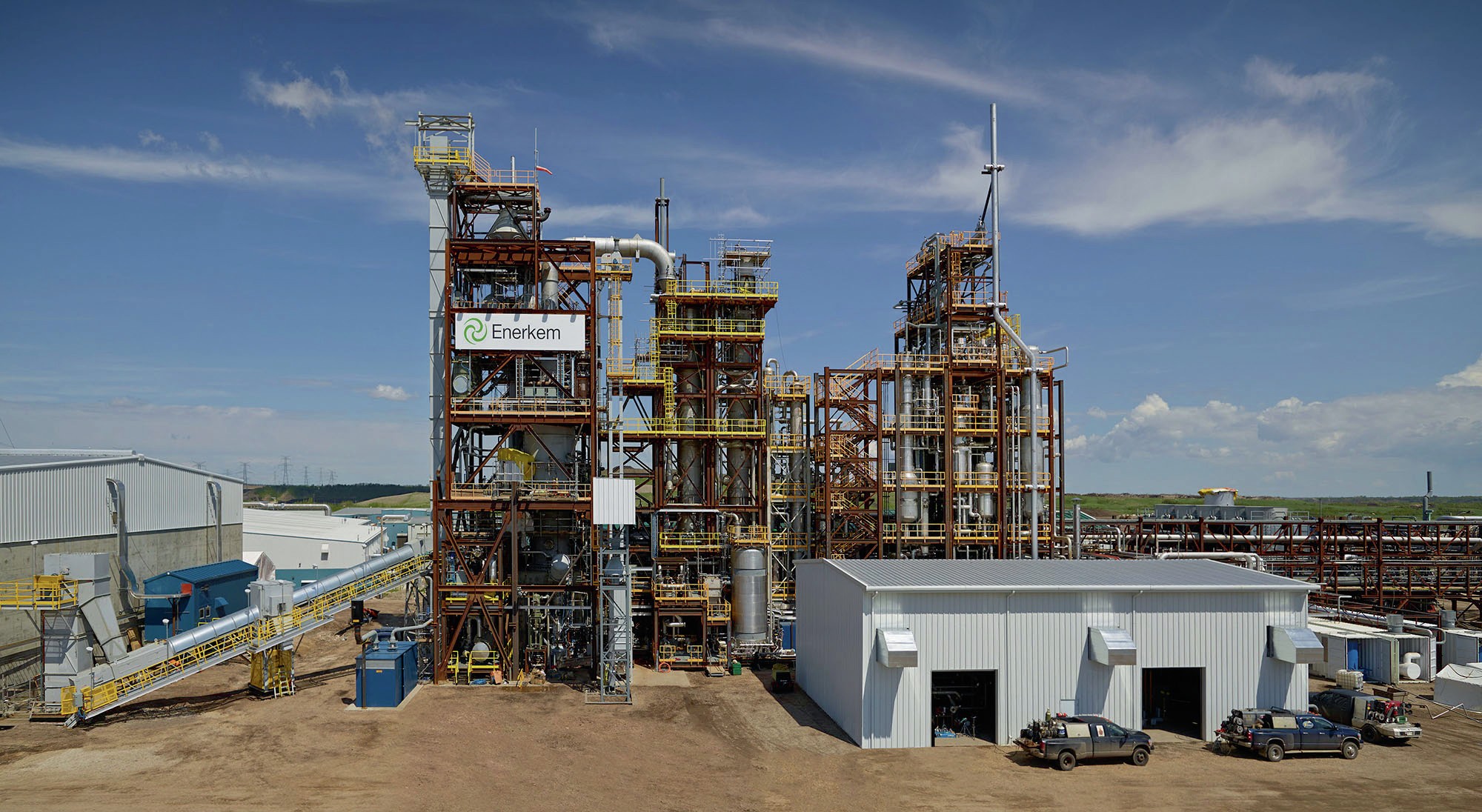
How to deal with the waste generated by modern society remains a vexed issue for governments all over the world. OECD figures indicate that the average citizen of a developed country produces 540 kg of so-called municipal solid waste (MSW) every year, and this has been a near constant figure over the past two decades. In spite of advances in recycling rates, the European Union reckons that only about 50% of all MSW is currently recycled, with the rest going to landfill or incineration. In the US the figure is only 35%. But landfill sites are filling up, and opportunities for export of waste to other countries to deal with are becoming more limited. China, which used to take large volumes of MSW, banned solid waste imports in 2018. Landfills also generate methane from the breakdown of organic matter, and there is an increasing focus these days on methane as a greenhouse gas. The US alone produces approximately 130 million t/a of CO2 equivalent in methane escapes from landfill.
Incineration allows the recovery of energy from MSW, which often contains products such as paper, food waste and plastics with a high calorific value, and when coupled to power generation can produce up to 550 kWh of electricity per tonne. However, the variable nature of MSW means that its incineration can also produce a number of toxic by-products including dioxins, furans, polycyclic aromatic hydrocarbons, and oxides of sulphur and nitrogen.
Combusting it in an enclosed system allows for easier removal of by-products, and also generates more energy – up to 1,000 kWh per tonne. Furthermore, waste gasification also generates syngas which can be used for the production of hydrogen or higher value downstream products such as ammonia, methanol and synthetic fuels or plastics. Gasification is also able to deal with some of the more intractable elements of MSW which cannot be recycled, including non-recyclable plastics like polycarbonates.
Commercial operation
In spite of its promise, the commercial history of waste gasification has been patchy to say the least, with a number of high profile project failures and bankruptcies, the most prominent of which was the Air Products and AlterNRG Tees Valley 1 and 2 plants in the UK, which were abandoned during construction and which cost Air Products a write down of a reported $1 billion. Companies involved are often small and cannot absorb the cost of often lengthy permitting delays – inevitable as the facilities are usually in or near urban areas. The variable quality of MSW can also be a challenge for gasifiers, and dealing with waste products like tar and ash contaminated with heavy metals can pose a technical challenge. For this reason there are often far more small scale pilot and demonstrator plants than large scale commercial operations. Nevertheless, progress has been made, and interest in the technology continues to increase.
Enerkem
One of the most prominent proponents of waste to chemicals has been Canada’s Enerkem. After successful pilot and demonstrator plant trials the company moved to a large scale 100,000 t/a waste gasification-based plant in Edmonton, Alberta. The plant was completed in 2014 at a cost of US$60 million and takes MSW from the city of Edmonton under a 25 year contract – the city also provided 40% of the funding. The plant deals with 30% of the city’s waste, and produces 33,000 t/a of methanol and ethanol.
The company has next moved to develop an even large waste to methanol plant at Varennes in Quebec. In the $670 million project it is partnered by Shell, Suncor and Proman, as well as the Quebec provincial and Canadian federal governments. The project aims to use more than 200,000 t/a of non-recyclable and wood waste to produce 100,000 t/a of methanol and ethanol. The project will also include an 87 MW electrolyser to generate renewable hydrogen and oxygen from hydroelectric power to feed the plant.
The company is also part of the W2C (Waste to Chemicals) methanol project in Rotterdam, along with Shell, Air Liquide, Nouryon and the Port of Rotterdam. The project originally envisaged processing 360,000 t/a of MSW into 220,000 t/a of methanol, with a start-up in 2022, although it is now evaluating biomass feeds as well and no final investment decisions has yet been taken. There is also a partnership with Suez to develop a 400,000 t/a waste to methanol plant at Tarragona in Spain. Again no final investment decisions has yet been taken.
United Kingdom
The UK is facing a shortage of landfill sites, and in the early 2010s became very interested in waste to syngas projects as a potential way of dealing with its solid waste problem. However, while several small biomass gasification plants processing waste wood have successfully started up in the past few years, municipal waste gasification plants have had a much more difficult history, as mentioned above, particularly the Tees Valley (TV) 1 and 2 plants at Billingham, developed by Air Products in conjunction with AlterNRG’s plasma gasification technology, which would have processed 700,000 t/a of waste from the northeast of England to generate 100 MW of power from syngas. However, technical difficulties with the gasification system led to the project being abandoned in 2016.
Likewise UK-based Energos, which developed a successful waste gasification demonstrator plant in Norway, planned three projects in the UK, but went into administration in 2016. The Milton Keynes project has since proceeded but abandoned the use of gasification in favour of incineration, the Derby project was abandoned in 2019 due to technical difficulties, and after some years in legal limbo the Glasgow project was finally denied planning permission in March 2021.
So far the only notable municipal waste gasification project in the UK has been a much smaller scale 40 t/d demonstrator plant has begun operations in the West Midlands, developed by Kew Technology, to produce 1.5 MW of electricity. However, there are still projects on the drawing board, as detailed below.
Velocys
Velocys, formerly the Oxford Catalysts Group, has developed a Fischer-Tropsch gas to liquids process which it is seeking to couple to renewable syngas generation from biomass or municipal waste. The company has had many ups and downs over the past few years, but in additional to a biofuel gasification plant in the US, says that it remains committed to a UK-based project to convert municipal waste into aviation fuel via Fischer-Tropsch conversion of waste-derived syngas, using technology licenses from Air Liquide, Linde and Haldor Topsoe. However, project timescales have now been put back to completion in 2025.
Fulcrum
Potentially stealing a march on Velocys is US-based Fulcrum BioEnergy, who have been operating in conjunction with BP and Johnson Matthey (JM). Fulcrum has been working on two projects. The first, at the Sierra BioFuels Plant in Storey, Nevada, is designed to convert 175,000 t/a of household waste into 37,000 t/a of Fischer-Tropsch derived fuel. The project has been delayed but is now in the late stages of construction, and is due to start up this year.
The other major Fulcrum project currently under development is based in the UK, and recently completed site selection – it will be based at the Essar Oil refinery at Stanlow near Liverpool. Construction on Fulcrum NorthPoint, as the project is known, is expected to begin in late 2023 and will be completed in 2025. It will process “several hundred thousand tonnes” of pre-processed waste into 30 million gallons per year of low-carbon aviation fuel.
Eastman
Eastman Chemicals has operated a coal gasification-based methanol plant at Kingsport, Tennessee for more than 25 years. However, in 2019 it decided to branch out into recycling unrecyclable plastics via two technologies. One, Polyester Renewal Technology, is a chemical breakdown of polyester using glycolysis. The other, Carbon Renewal Technology, effectively tips unrecyclable plastic waste into the gasifier as a co-feed to produce methanol, which can then be used to make acetic acid or formaldehyde and then downstream plastics. The company has set itself the target of recycling 250,000 t/a of plastics via these methods by 2030 and achieving net zero carbon emissions.
MGC
Mitsubishi Gas Chemical recently announced that it is developing technology to produce methanol by using CO2 emitted from factories and power plants, as well as gasified plastic waste. The company will modify an existing pilot facility in Japan for this, and intends to begin licensing the technology in 2022 or 2023.
MyRechemcial
In November last year, Maire Tecnimont launched a dedicated subsidiary dedicated to the processing of non-recyclable plastics and refuse derived fuel (RDF) and their conversion into downstream chemicals, which it calls MyRechemical. According to the company, MyRechemical will use a mixture of Tecnimont proprietary technologies with those licensed from other companies for the chemical conversion of carbon and hydrogen in waste via partial oxidation and subsequent purification, from which a low carbon syngas is obtained, able to be converted with process extension into hydrogen, methanol, ethanol and derivatives.
Plasma gasification
One of the issues with conventional gasification technologies is the variable quality of MSW, even after sorting and preprocessing. As well as ash, it also generates tars which must be cleaned from the gasifier. One solution is to increase the temperature drastically to break down molecules completely into a free plasma. This is achieved using an electric arc discharge to create a plasma torch which reduces tar formation (to around 0.1% of an autothermal gasification process) and converts all of the organic material into syngas. Arc discharges obtain thermal plasmas from DC or AC current or through radio frequency or microwaves. DC plasma technology is preferred for waste gasification plasma processes. Plasma is formed by high energy from AC or DC sources through the plasma torch close to the bottom of reactor and fuels are gasified through the plasma flames. The oxygen demand in this process is small compared to conventional gasification since most of the thermal energy is coming from an external energy source rather than exothermic reactions between the fuel and oxygen. There are several companies with pilot facilities, and some have proceeded to full commercialisation of the technology.
AlterNRG
AlterNRG market the Westinghouse plasma gasification system developed in the 1980s. AlterNRG and Westinghouse Gasification are now both co-owned by Chinese renewable energy developer Sunshine Kaidi New Energy Group Co., Ltd. In addition to running its demonstrator facility at Madison, Pennsylvania, USA, from 1995-2013, AlterNRG has built seven small scale waste gasification plants in Japan, China and India, with capacities from 24-220 t/d (8,000-73,000 t/a).
InEnTec
InEnTec (Integrated Environmental Technologies) was a spin-off from MIT in 1995, aiming to develop plasma gasification to convert waste into chemical products and clean fuels. The technology took many years of refinement before the first commercial plant was built in 2008. It has now concentrated on developing small scale modular plants which can process between 25 t/d to 150 t/d of waste or biomass.Impurities are trapped in a bath of molten glass and recovered as ingots, while lighter elements emerge as syngas. The company has six installations so far. In Japan, they process waste electronics, circuit boards and asbestos, mainly using the syngas to generate power, while in Taiwan a site processes batteries and medical waste. Dow Corning operates one at its Midland, Michigan site, which processes untreatable industrial waste and uses the hydrogen in hydrochloric acid production, and at Colombia Ridge, Oregon, InEnTec operates a plant processing MSW and produces 1.5 t/d of fuel cell grade hydrogen with the aim of using it to fuel 2,500 vehicles.
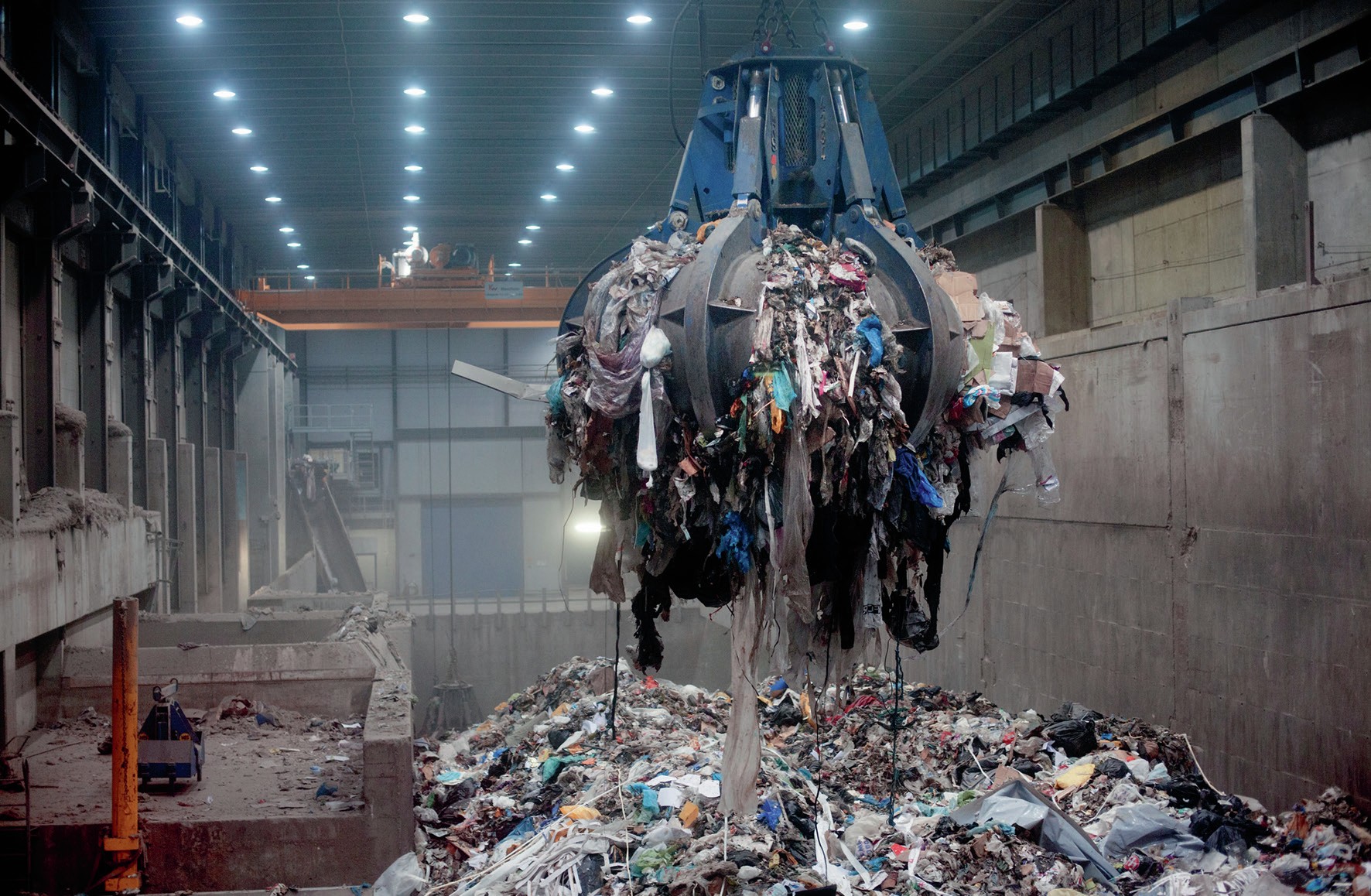
OMNI CT
The OMNI Conversion Technologies (CT) gasification and plasma refining system is the development of a Canadian company whose proprietary technology was demonstrated in a 135 t/d pilot facility built in 2007 in Austria. Like InEnTec, it is based around a modular system, although slightly larger at 200 t/d of waste input to produce 15 t/d of hydrogen or a larger equivalent volume of syngas. After feed preparation (shredding into 10cm chunks) the waste passes first into a horizontal moving grate gasifier and then a vertical fixed bed updraft gasifier. The plasma flame is only then applied in the presence of oxygen to refine the syngas and remove tars. A final gas cooling and conditioning section removes HCl, sulphur and heavy metals. Around 90% of the energy required to run the system comes from the waste itself, rather than consuming electricity, making it 80% more efficient than water electrolysis in production of hydrogen. In April 2021, OMNI CT announced its first commercial sale of the process, to the Larsen and Lam Climate Initiative in California, for $35 million.
A developing area
In spite of the technical and commercial hurdles, waste gasification is seen as a solution to an otherwise intractable problem of how to deal with large volumes of municipal waste that cannot be recycled, and potentially an element in the ‘circular economy’, as well as a way of eliminating or at least reducing methane emissions from landfill sites. If some of the steps have been faltering so far, the success of some installations, such as Enerkem in Edmonton, shows that it can be done at scale. Gasification of alternative feedstocks has often foundered on the issue of the cost of gathering together sufficient material to run a large-scale plant with associated economies of scale. This has particularly bedevilled biomass gasification projects, except those using waste streams from forestry, pulp and paper production, where the gathering has already been done. Municipal waste however already had had the gathering performed, and already represents 1.3 billion t/a of raw material globally, sufficient to generate more methanol, ammonia and hydrogen combined than current world demand. The entrance of players such as Mitsubishi Gas Chemicals and Maire Tecnimont into the arena shows that major licensors are taking this seriously.