Fertilizer International 504 Sept-Oct 2021
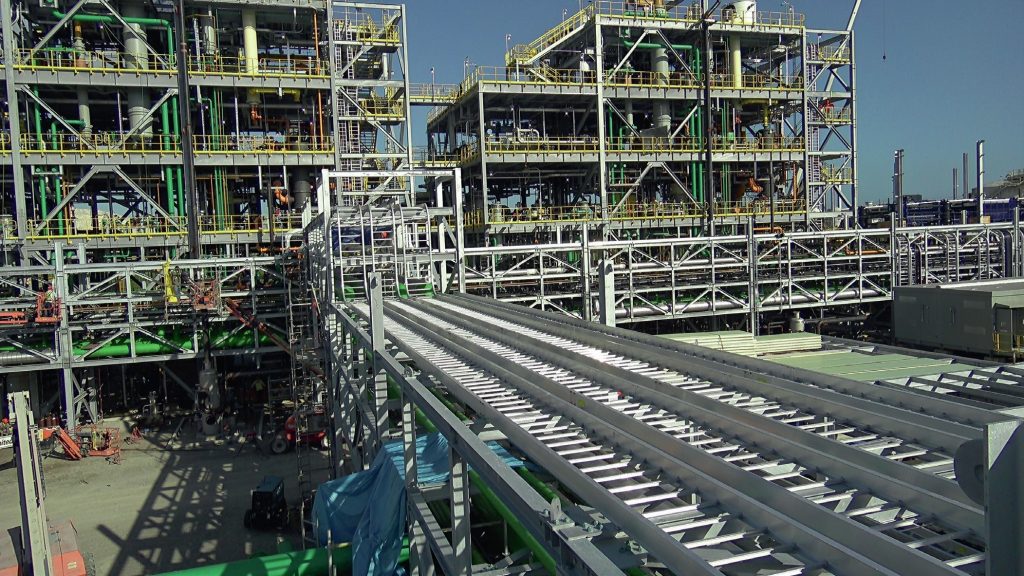
30 September 2021
Phosphoric acid co-products
SUSTAINABLE PHOSPHATE PRODUCTION
Phosphoric acid co-products
The latest developments in the recovery and commercialisation of fluorosilicic acid, rare earth elements (REEs) and uranium co-products associated with phosphoric acid production.
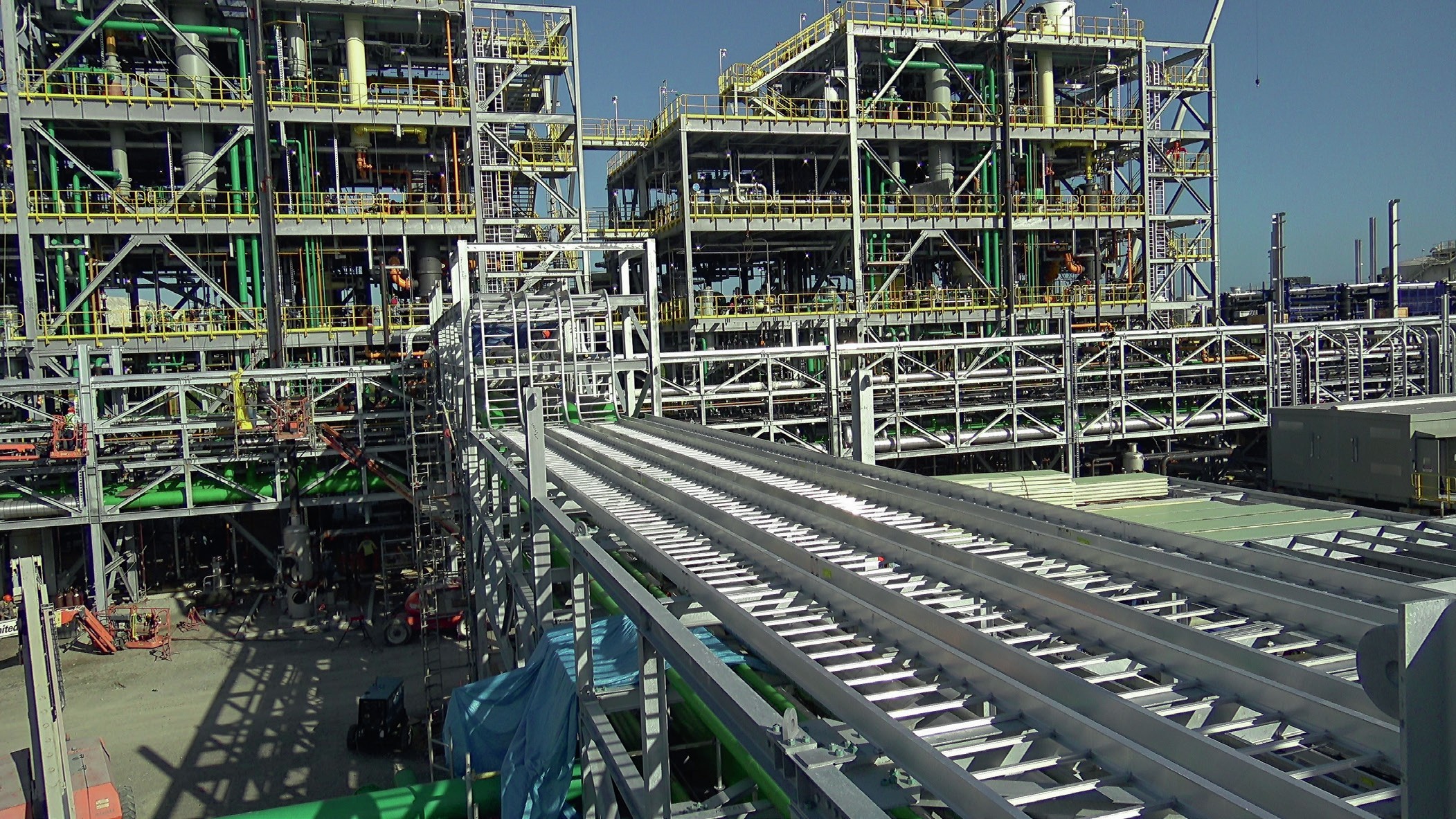
Cost and waste reduction have become increasingly important imperatives in phosphate fertilizer production. Greater resource efficiency has also risen up the industry’s agenda with the emergence of the circular economy and policies on waste prevention.
This has resulted in renewed interest in the commercial recovery of rare earth elements (REEs), uranium and fluorosilicic acid (FSA) during the phosphate manufacturing process. As well as improving process efficiency and reducing costs, the sale of such co-products can generate extra revenues for phosphate producers.
Rare earth elements
The rare earth elements (REEs) consist of the group of 15 lanthanide elements, with atomic numbers 57 to 71, together with yttrium and sometimes scandium. REEs are generally classified as heavy, medium or light according to their atomic number and relative abundance (Table 1).
These 17 elements commonly occur together and, as a consequence, are typically mined and processed collectively to produce an initial rare earth oxide (REO) product. Individual REEs, due to their similar physical and chemical properties, then need to be painstakingly and expensively separated from this REO intermediate for their different end uses via multi-stage solvent extraction1 .
Global rare earth oxide (REO) production has risen strongly over the last decade, increasing from 132,000 tonnes to 210,000 tonnes between 2017 and 2019, for example2 .
Rising production in recent years has been spurred by growing demand for REEs from three distinct end-use markets – the low-carbon, automobile catalyst and digital technology sectors – as follows2 :
l Neodymium (Nd), dysprosium (Dy), and praseodymium (Pr) are used in the manufacture of temperature-resistant permanent magnets, while Pr, gadolinium (Gd), europium (Eu) and erbium (Er) are used in nanoparticle-based materials which enhance power conversion efficiency
- Lanthanum (La), cerium (Ce), and Nd are commonly used as stabilisers in vehicle catalysts
- Eu, terbium (Tb), and yttrium (Y) are also used to manufacture video displays.
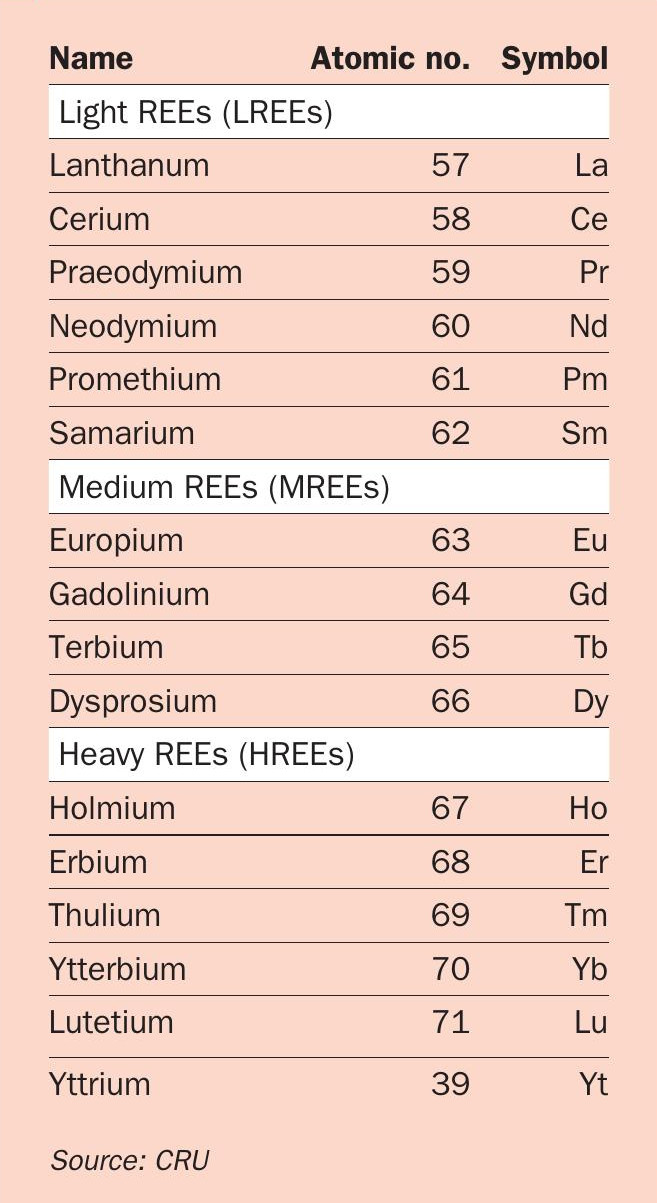
K-Technologies, Inc.
Florida’s K-Technologies, Inc. has developed a range of proprietary recovery technologies for uranium, REE and fluoride recovery at bench, pilot plant and commercial scale. These cover the following phosphate industry applications:
- Uranium recovery from phosphoric acid using conventional solvent extraction (SX) or advanced extraction methods such as impregnated substrates (IS) and/or ion exchange (IX)
- Recovery and purification of rare earths from wet process phosphoric acid using ion exchange and continuous chromatographic techniques.
- Fluoride recovery from phosphogypsum pond water or barometric cooling water systems via ion exchange.
K-Tech has been involved with REE recovery and separation since the early 1980s. The company offers technologies able to recover REEs from wet process phosphoric acid and, more importantly, purify these to produce individual rare earth products. In the initial process step, non-solvent extraction methods concentrate REEs in a low volume intermediate solution. A continuous process is then used to separate individual REEs from each other and produce purified materials such as europium oxide, terbium oxide, yttrium oxide, etc.
K-Tech possesses extensive in-house expertise on uranium (U3 O8 ) recovery from phosphoric-acid. The company was instrumental in the development and commercialisation of the so-called ‘second generation’ solvent extraction technology implemented from the 1970s onwards.
Following the closure of second-generation systems in the 1990s, due to economic pressures, K-Tech subsequently developed advanced third generation recovery techniques for uranium. These are based on the application of continuous non-solvent extraction – such as modified solid sorbent systems. This new simplified process results in a smaller plant footprint and lower capital and operating costs.
Adopting third generation uranium recovery technology can cut operating costs by 25-35 percent, according to K-Tech. It is also likely to be applicable to more concentrated phosphoric acid streams, such as those originating from the hemi-hydrate process.
Simultaneous recovery of both REEs and uranium makes economic sense, according to K-Tech, by providing phosphate producers with the option to diversify and add-value to their production processes.
REEs are mined from various mineral deposit types. The majority of global REE production comes from China, which produced 132,000 tonnes of REO in 2019, equivalent to almost two-thirds (63%) of total world output. Other important REE production centres include the US, Myanmar and Australia, which account for around 12 percent, 11 percent and 10 percent of global production, respectively2 .
While there is some variation from mine to mine, most orebodies comprise of1 :
- Large proportions of light ‘industrial’ rare earths (Ce and La) – which typically make up 60-75 percent of the final product volume
- Moderate amounts of light ‘magnetic’ rare earths (Nd and Pr) – typically 15-30 percent by product volume
- Small fractions of medium/heavy rare earths such as dysprosium, samarium, europium, terbium etc – although levels can be much higher in some exotic orebodies, as well as for specific elements such as yttrium.
When it comes to the economic feasibility of REE mine projects, the emphasis is on cerium, lanthanum, neodymium and praseodymium recovery. That is because, for an average orebody, these four elements collectively account for 94 percent of production volumes and generate 90 percent of mining revenues1 .
A tale of two markets
In recent times, two element pairs – the ‘industrial’ REEs Ce/La and the ‘magnetic’ REEs Nd/Pr – have operated as parallel, separate markets due to their contrasting end uses. Demand for Ce/La, for example, is concentrated in polishing powders, steelmaking and alloy manufacture, and as a support bed for catalysts. Usage of Nd/Pr, meanwhile, is mainly for the high-powered permanent magnets (NdFeB type) found in wind turbines, electric vehicles (EVs), portable electronics and many other applications.
Demand growth in the separate Ce/ La and Nd/Ps markets has diverged in recent years. Annual growth in NdFeB magnet demand, for example, grew at around 5-6 percent annually between 2012-2020, according to CRU, due to the widespread installation of wind turbines and rapid growth in EV sales. Growth in Ce/La demand, in contrast, has languished at just one percent per annum over the same period1 .
This divergence has created marked differences in REE prices and revenues. Nd/Pr prices are now 250-300 percent higher in real terms than they were in 2008, while Ce/La prices have declined by 20 percent on their 2008 levels. This has had a knock-on effect on REE mining revenues in recent years – with the extraction of La/Ce now generating just 10 percent of revenues, down from around half of total revenues previously1 .
REE recovery from phosphates
The history of REE recovery from phosphate rock, phosphoric acid and phosphogypsum waste dates back decades. Notable landmarks include3 :
- The commercial recovery of REEs from phosphate rock in Finland by Kemira Oy in the late 1960s and early 1970s
- Solvay’s extensive experimental work on uranium and REE extraction from phosphoric acid in the late 1970s and early 1980s, culminating in the establishment of an industrial-scale pilot plant in Rouen
- The pilot-scale recovery of REEs from phosphoric acid evaporation sludges, via nitric acid leaching and solvent extraction, trialled in South Africa in the late 1980s and 1990s.
More recently, the Florida Industrial and Phosphate Research Institute has carried out systematic studies of REE recovery from phosphate mining and production streams, including:
- Waste clay
- Amine flotation tails
- Phosphoric acid
- Phosphogypsum
- Sludge from phosphoric acid concentration and clarification.
To date, however, most pilot scale trials have failed to translate into viable commercial REE recovery from phosphate sources. This has mainly been attributed to technical challenges and the prohibitive recovery costs linked to the low REE content of phosphate rock3 .
Arkema and Nutrien’s innovative partnership
Arkema and Nutrien have teamed up on an innovative new project. Construction is well underway at Nutrien’s phosphate complex in Aurora, North Carolina, on a new plant that will produce anhydrous hydrogen fluoride (AHF) from fluorosilicic acid (FSA). This will be sold as a raw material to Arkema and used to produce a variety of materials at the company’s facility in Calvert City, Kentucky.
The world’s primary source of fluorine is fluorspar, a mineral mined in Mexico, South Africa and China, but the second-mostavailable source is phosphate rock. The fluorine in phosphate ore is extracted as FSA through the phosphoric acid production process. New technology – the first of its kind to be commercialised in the Americas – will allow Nutrien to use this FSA as feedstock to produce AHF.
The AHF produced at the new plant will be used as a key raw material for Arkema’s fluorogas and fluoropolymer product lines. This family of products includes Forane® foam blowing agents as well as Kynar® polyvinylidenefluoride (PVDF) resins and co-polymers.
Forane® is used in a variety of applications that reduce energy consumption of both residential and commercial buildings. They include Forane® refrigerants for stationary air conditioning, chillers and refrigeration. Kynar® is used in several of the world’s most challenging applications. These include binders for lithium-ion batteries, flame resistant wire and cable jacketing, inert piping and fittings for corrosive chemicals, back sheets for long life solar panels, and high durability coatings for skyscrapers.
The design and engineering of the AHF plant was completed in October 2020. Construction is due to be completed by the end of this year, with the plant up and running by the first half of 2022. Long-term partners Arkema and Nutrien are excited about the many benefits of this project.
“It is very gratifying to see this project with our strategic partner Nutrien near commissioning,” said Anthony O’Donovan, Regional Group President, Fluorochemicals Americas at Arkema. “Replacing the use of mined fluorspar with a co-product of an existing process for our fluorinated products platform reflects Arkema’s continued focus on sustainable growth and reducing the environmental footprint of the raw materials that are required to make our key products.”
Arkema is committed to sustainable growth and has made corporate social responsibility (CSR) an integral part of its strategies and activities. External stakeholders have recognised the company’s CSR approach and achievements. This notably includes Arkema’s listing in the FTSE4Good non-financial global index. The partnership with Nutrien is also well-aligned with Arkema’s ambitious targets to reduce its environmental footprint, and develop technologies and solutions that can help address major societal challenges.
With this new process, Arkema will be significantly reducing its dependence on a mined product produced in a much more resource-intensive fashion. The long-term supply agreement with Nutrien will also provide Arkema with a stable, secure and competitive supply chain for this vital material. In Nutrien’s recent Feeding the Future plan, the company committed to achieving a 30 percent reduction in its greenhouse gas (GHG) emissions intensity by 2030. The partnership with Arkema helps Nutrien double down on this target and other efforts to reduce its environmental footprint.
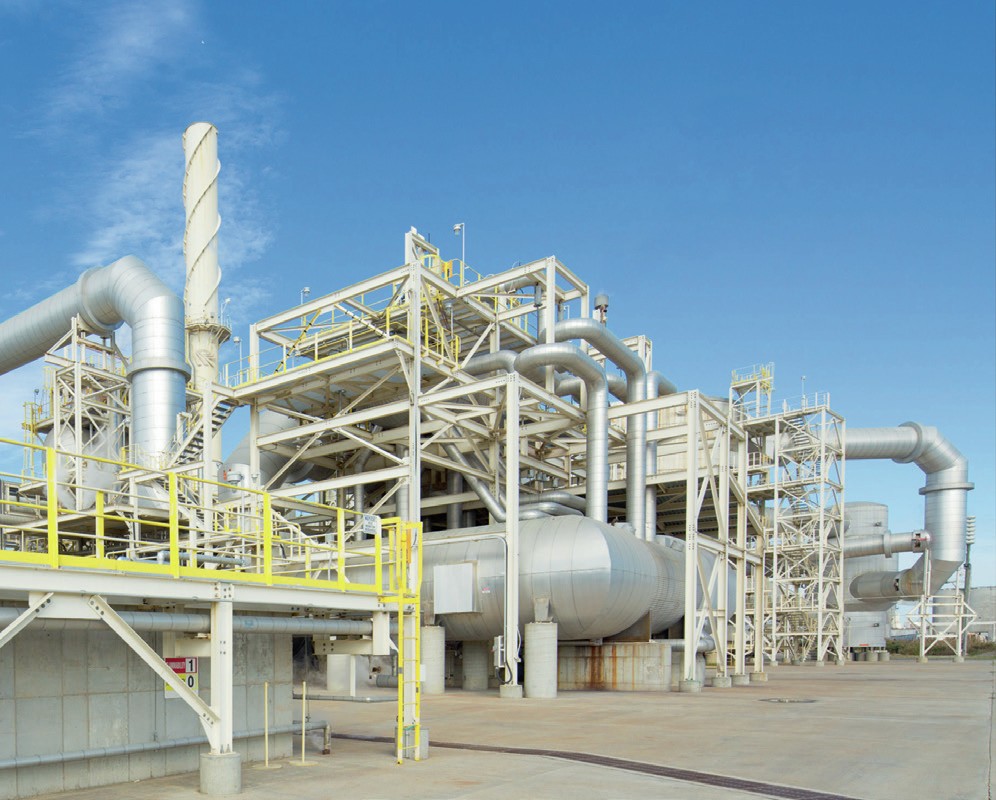
Phosphate rock is the largest global source of fluoride, and the new technology will allow Nutrien to convert a greater amount of fluorine. It’s also a more sustainable process for producing AHF compared to the more typical route, which converts it from fluorspar. And with higher utilisation of the existing mining operation at Aurora, it reduces overall energy consumption and GHG emissions.
The high-quality equipment and materials used in the new plant will feature proven technology that ensures comprehensive environmental protection and safe operation.
Safety is a top priority for Nutrien, and the company’s high safety standards and long-term operational experience will provide a solid foundation of safety at the new plant. The Aurora site has 55 years of operational excellence, and Nutrien’s project management team has more than 150 years of construction management experience. Likewise, Buss ChemTech AG, the project’s technology provider, has six decades of experience in construction of hydrofluoric acid and derivatives plants around the world.
As part of their agreement, Arkema is funding construction of the new plant at the Aurora site and Nutrien will operate and manage it. The strong relationship formed between the two companies – and the hard work of the many teams involved on both sides – were instrumental in bringing about this ground-breaking deal and innovative project.
“It is very exciting to get this project across the line,” said Raef Sully, Nutrien’s Executive Vice President and CEO, Nitrogen & Phosphate. “This strategic partnership with Arkema demonstrates our commitment to innovation and finding solutions that not only use co-products for industrial use, but also drive reductions in GHG emissions intensity. “
Nevertheless, the potential for REE recovery from phosphates remains high. The global phosphates industry consumes in excess 250 million tonnes of phosphate rock annually. This could translate into potential yearly REE production of around 125,000 tonnes, based on an average rock concentration of 0.046 percent, although this tonnage is skewed upwards by the presence of heavy REEs3 .
Below, we highlight some of the most promising current REE recovery projects.
Phalaborwa rare earth project
Rainbow Rare Earths Limited is developing the Phalaborwa rare earths project in South Africa. This aims to recover REEs from approximately 35 million tonnes of phosphogypsum waste, a historic legacy of the country’s igneous phosphate mining and processing industry. This PG waste has an average in situ REO grade of 0.6 percent, some 30 percent of this comprising high-value Nd/ Pr. Rainbow is co-developing the Phalaborwa project with Bosveld Phosphates Limited.
The company is also trialling REE mining operations at its Gakara project in Burundi. Gakara is currently Africa’s only active REE production site and, according to Rainbow, produces one of the highest-grade REE concentrates in the world – typically 54 percent total rare earth oxide (TREO). The Gakara concentrate is also heavily weighted towards Nd/Pr. This accounts for around 20 percent of overall TREO content, while representing 80 percent of its value.
In a technical update released in November last year, Rainbow announced that the Phalaborwa project’s pilot plant, developed by Sasol Limited, had successfully produced three tonnes of mixed rare earth carbonate and associated cerium oxide. The grade of the rare earth carbonate product obtained was found to be significantly higher than conventional mining concentrates, such as that produced at the company’s Gakara project in Burundi.
Initial estimates suggest that the proposed full-scale process to treat two million t/a of Phalaborwa phosphogypsum could deliver 10,000 t/a of mixed rare earth carbonate. This REE concentrate would, in turn, contain around 3,100 tonnes of Nd/Pr.
Rainbow expects Phalaborwa’s beneficiation costs to be significantly lower than those of a conventional REE mining project.
George Bennett, Rainbow’s CEO, said: “We are delighted by the initial results… which… reaffirm our confidence in the considerable potential of the project and support our expectation that it will represent a significant source of NdPr for Rainbow. Sasol’s processing flow sheet demonstrates the viability of the project, which is further validated by the proven ability to extract REEs from the gypsum, as displayed by the successful operation of its pilot plant.”
Pilot plant results suggest that the Phalaborwa project could deliver a high value product at low processing opex and capex, according to Bennett. “The value of the mixed rare earth carbonate will not only be higher than a traditional rare earth mineral concentrate, due to the chemical form… in the stacks, but also [because] of [its] underlying value, which at 30 percent NdPr, compares very favourably with other rare earth projects globally,” he said.
CaMona project
The recently completed German-Brazilian CaMona project investigated the industrial-scale extraction of REEs from phosphogypsum waste generated by the phosphate fertilizer industry in Brazil’s Catalão region. The project targeted the recovery of rare earth monazite concentrates from phosphogypsum using a cost-effective physical separation process. Its ultimate aim was to produce a rare earth concentrate from a continuously operated pilot plant and further process this – via chemical leaching and digestion – into highly pure and marketable rare earth products.
The e1.2 million, three-year, German government-funded project was coordinated by rare earths exploration company Ceritech. Partners included Brazilian phosphate producer CMOC and three German and Brazilian universities. The project first received funding at the start of 2018 and ended in June 2020. Preliminary results published last year concluded that industrial REE recovery from Brazilian phosphogypsum looked feasible, although further optimisation and scale-up of the process was still necessary.
Florida start-up recovers REEs from phosphoric acid
In 2019, Precision Periodic, an incubator company based at the University of Central Florida, successfully extracted and separated REEs from phosphoric acid using a reusable nano-filtration system called Thor. According to the company, the Thor filter can be reused for thousands of cycles and is highly scalable for all size applications.
In an extraction project for the Florida Industrial and Phosphate Research Institute, Thor captured 40-60 percent of the REEs and radioactive elements from wet-process phosphoric acid in a five-minute single pass-through. The innovative filter can handle up to 9,000 gallons an hour, allowing it to hold and recover around 0.5-1.2 kg of REEs, precious metals, or heavy metals.
“The successful test projects proved that the Thor nano-filtration technology could be a game-changer for US production of its own rare earth elements supply,” said Brian Andrew, CEO of Precision Periodic. “The phosphoric acid contains 150 ppm of total rare earths. Based on our extraction capabilities, we could extract 75 grams of total rare earths out of every 1,000 litres of phosphoric acid from a phosphate mine. This equates to one Florida phosphate mine being able to produce 230 tonnes of total rare earths per year – which would supply an estimated 25 percent of annual US military needs.”
Uranium
Interest in uranium recovery from phosphates is on the rise again – thanks to increased environmental awareness, energy security and rising uranium prices. Phosphate fertilizer producers could provide more than 15 percent of the world’s non-military uranium requirements, according to some estimates4 .
On a national basis, it has also been calculated that uranium as a by-product of phosphate production could meet 8-9 percent of Argentina’s demand, two percent of EU requirements and 10 percent of US needs. Amounts recovered could even exceed current domestic uranium production in some instances. The US phosphate industry, for example, could potentially provide 5.5 million pounds (2,495 tonnes) of uranium (U3 O8 ), versus US domestic production of 4.9 million pounds (2,223 tonnes) in 20144 .
Commercial techniques to recover uranium from phosphoric acid are well-known (see K-Technologies box) and were used on an industrial scale in the United States – and to a lesser extent elsewhere – up until the late 1990s, when plummeting uranium prices made recovery uneconomic for fertilizer producers4 .
Prayon’s fluoride recovery technology
Prayon’s Thomas Henry and Hadrien Leruth provide an overview of fluorine recovery at phosphoric acid plants – and explain how the many technical challenges can be overcome.
For phosphoric acid producers, fluorine is often considered as a bulky by-product to be neutralised and discharged along with the gypsum.
This chemical element is often regarded as an obstacle to meeting ambitious P2 O5 production objectives, whereas it should be the focal point of a lot more attention, both for environmental and economic reasons.
Fluorine, bonded to apatite, usually occurs as 10 weight percent of the P2 O5 content of sedimentary rocks and 2.5-5 weight percent of igneous rocks. It reacts with either soluble silica to produce fluorosilicic acid (H2 SiF6 ) or alumina to produce soluble AlF3 or AlF6 3– during the weak phosphoric acid production stage (28-42% P2 O5 ). Some of the fluorine dissolved in the phosphoric acid acidifies the plant’s off-gases through the formation of volatile SiF4 or HF, while another fraction precipitates as fluosilicates, being discharged with the gypsum cake. At the phosphoric acid concentration stage (48%-60% P2 O5 ), almost all the remaining liquid fluorine present in the acid is released as SiF4 and/or HF in the evaporated water.
Therefore, all the untreated gaseous effluent from phosphoric acid plants can represent a significant source of atmospheric pollution. This is as hazardous for the people working in the plant as it is for the nearby environment.
The technical challenge presented by fluorine recovery from those gaseous effluents lies in the important formation of solid silica. This is generated from gaseous silicon tetrafluoride when it is adsorbed in water to form fluorosilicic acid:

This reaction shows that an efficient fluorine recovery system results in high silica precipitation. However, the solid silica forms hard scaling in tanks and piping, creating some difficulties in the recovery system. Over the years, Prayon has adapted the design of its fluorine absorption system to meet the needs of producers and achieve the desired recovery performance, meet environmental objectives, and tackle silica scale formation.
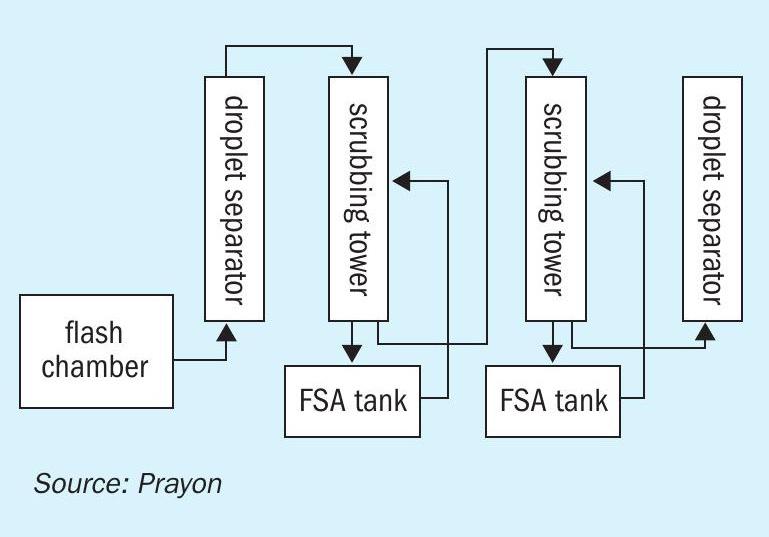
Prayon’s vacuum fluorine recovery and atmospheric gas cleaning systems both avoid the use of easily clogged packed bed towers and instead use simple but robust void towers equipped with high-efficiency sprayers and droplet separators. Prayon’s sprayers are especially designed without inserts to maximise the liquid-gas contact surface and simultaneously avoid clogging thanks to their large free passageways.
At the phosphoric acid concentration stage, the operating principle is as follows (Figure 1): the fluorinated gas to be cleaned flows through one or several absorption stages where the gaseous fluorine is absorbed in a fluorosilicic acid solution of decreasing concentration. If required, a final wash stage with pure water is carried out.
The operation of each absorption stage in batch mode is preferred to maximise the fluorine recovery. Firstly, the fluorosilicic acid tank is filled with pure water with a high capacity for fluorine absorption. Over time, fluorine slowly accumulates in the loop to reach the required fluorosilicic acid grade. Finally, the concentrated liquor is emptied to the storage area and the cycle starts again.
The design of the fluorine absorption tower (Figure 2) is focussed on two targets:
- Highest fluorine recovery (gaseous + liquid) to limit the fluorine conveyed to the next stage
- Self-cleaning of the piping with a mechanical washing provided by efficient sprayers implemented at the right locations.
Any remaining fluorosilicic acid droplets escaping the absorption tower are separated by passing the gas flow through Prayon separators (Figure 3) – Praysep – where, just as in a regular cyclone, droplets are separated using centrifugal forces. However, the special feature of this proprietary equipment is a static impeller that creates a vortex in the gas flow without the need for a change of direction. This feature greatly improves the compactness of the system and reduces its pressure drop to a few millimetres of water column.
In summary, production teams at phosphate plants find Prayon’s fluorine recovery system a comfortable solution that is easy to operate. At the same time, it avoids fluorine being released at the stack, or being recycled back to the plant where it results in scaling and presents a solids handling and removal challenge. Finally, producers simultaneously save money on maintenance and increase their revenues, especially if the fluorosilicic acid generated is sold for the manufacture of hydrofluoric acid or aluminium fluoride.

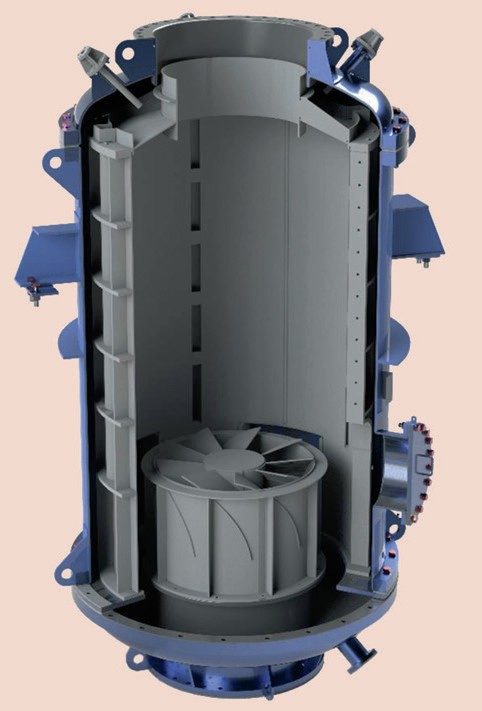
In the US, current costs for uranium recovery from phosphoric acid using industrially proven solvent-extraction technology are within the range $44-61 per pound (U3 O8 ). This is on the verge of being economically profitable, given that US nuclear reactor operators purchase uranium from foreign suppliers at an average cost of $38.81 per pound4 .
Ion exchange technology for uranium recovery from phosphoric acid, although as yet unproven at commercial scale, could drive down costs further. Pilot-plant scale ion exchange trials in the US by the Australian company PhosEnergy have reported costs of $33-54 per pound. Even greater cost savings could eventually be realised if uranium was leached directly from beneficiated phosphate rock prior to digestion. This would have the added benefit of making both the final fertilizer product and the phosphogypsum waste virtually uranium-free4 .
Fluorosilicic acid
Hexafluorosilicic acid (H2 SiF6 ), commonly known as fluorosilicic acid or fluosilicic acid (FSA), is generated as a by-product of phosphoric acid production. This originates from the natural levels of fluorine present in sedimentary (0.10-0.14 kg F per kg P2 05 ) and igneous (0.06-0.08 kg F per kg P2 05 ) phosphate rock.
Production of phosphoric acid (H3 PO4 ) and phosphate fertilizers creates silicon tetrafluoride (SiF4 ) as a toxic off-gas. Currently, this problem is mainly resolved by absorbing SiF4 in water to form fluorosilicic acid (FSA) and then storing it in ponds, neutralising it or disposing into the sea.
World phosphoric acid production, and by association FSA, is on the rise. Assuming phosphoric acid contains three percent fluorine on average, around 1.4 million tonnes of by-product FSA was produced globally in 2019, according to some estimates, being roughly distributed regionally as follows5 :
- 560,000 tonnes in East Asia
- 230,000 tonnes in Africa
- 225,0000 tonnes in North America
- 130,000 tonnes in East Europe and Central Asia
- 100,000 tonnes in West Asia.
Use of by-product FSA remains comparatively low, however, and most FSA produced by the phosphate industry, in general, continues to be either neutralised, ponded or discharged to the sea. Nevertheless, around 200,000 tonnes (fluorspar equivalent) is consumed annually in aluminium fluoride (AlF3 ) manufacture, meeting some 11 percent of global industry’s fluoride needs. Water fluoridation and fluoride salt manufacture consume a further 200,000 t/a of by-product FSA. Some FSA is also used during phosphoric acid production as a sulphuric acid substitute, reducing the latter’s usage by about five percent5 .
Currently, FSA generation is produced by at least 30 companies worldwide. Yet only one-third of these business obtain their FSA as a phosphate industry by-product, with the majority preferring to make FSA from fluorspar. Phosphate-derived FSA is, however, a negative cost raw material – as it must be neutralised and disposed of at extra cost if it cannot be used5 .
Another factor that has limited the widespread use of FSA as a source of fluorine has been its high capital and processing costs, together with logistical constraints, although these have been reduced by the technology advances made by Buss ChemTech and others (see companion feature on p50). A further complication is that HF plants must be configured to use either fluorspar or FSA, not both, as the associated chemical processing systems are unable to accept variations in feedstock quality5 .
More positively, the Chinese government has acted to encourage the use of by-product FSA in Guizhou, Hubei and Yunnan, the country’s the three main phosphate provinces. As a consequence, several FSA-consuming anhydrous hydrogen fluoride (AHF) plants have been set up by Guizhou Wengfu Lantian Fluorine Chemical, a subsidiary of Wengfu Group. Other Chinese HF producers, such as Do-Fluoride, are investigating whether producing HF from FSA looks economically feasible. Wengfu is also reported to be planning a joint venture to produce AHF from FSA in Morocco5 .
In the USA, an estimated 40,000 tonnes of FSA – equivalent to about 64,000 tonnes of pure fluorspar – was recovered from five phosphoric acid plants during 2019. This was mostly used in water fluoridation. North America’s first industrial-scale FSA-to-HF plant is currently under construction (see Arkema-Nutrien box).
References