Nitrogen+Syngas 373 Sept-Oct 2021
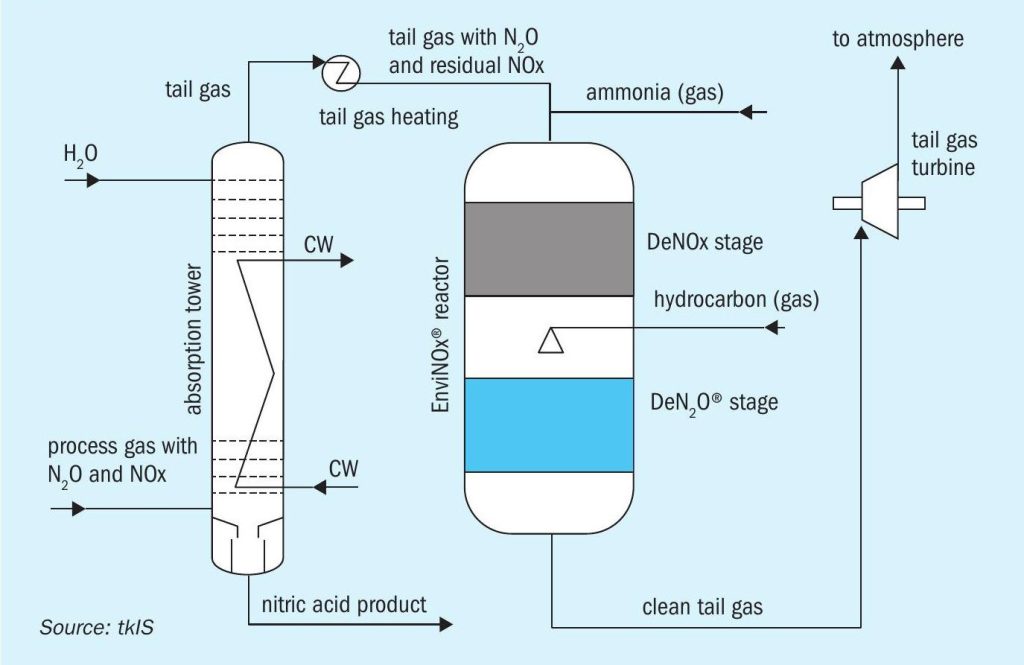
30 September 2021
Sustainable nitric acid and ammonium nitrate production
EMISSIONS ABATEMENT AND LIQUID WASTE REDUCTION
Sustainable nitric acid and ammonium nitrate production
By utilising state-of-the-art technologies, nitric acid and ammonium nitrate producers are able to reduce the environmental impact of their production plants and make a key contribution to climate protection.
Nitric acid plants are a significant producer of nitrogen oxides (NOx) and nitrous oxide (N2 O) emissions that have a radical impact on the environment, contributing to acid rain, the greenhouse gas (GHG) effect and ozone layer depletion. In the production of nitric acid, the main combustion product during the oxidation of ammonia over platinum gauzes is nitric oxide (NO), that is further oxidised to nitrogen dioxide (NO2 ), which reacts with water in the absorber to form nitric acid.
Unfortunately, the process also generates unwanted nitrous oxide (N2O) which passes unchanged through the plant and enters the atmosphere in the plant’s tail gas. Some residual NOx, not turned into nitric acid, is also emitted with the N2O. While limits on NOx emissions have long been in force because of concerns about acid rain and smog, N2 O emissions have not been subject to effective restrictions until fairly recently, but are now recognised as the powerful climate killer it truly is.
Nitrous oxide (N2O) is a potent greenhouse gas, 265 times worse than carbon dioxide, due to its longevity in the earth’s atmosphere and its infrared radiation absorption properties. Emissions of N2O have made nitric acid plants one of the world’s largest sources of greenhouse gas emissions amongst industrial manufacturing facilities.
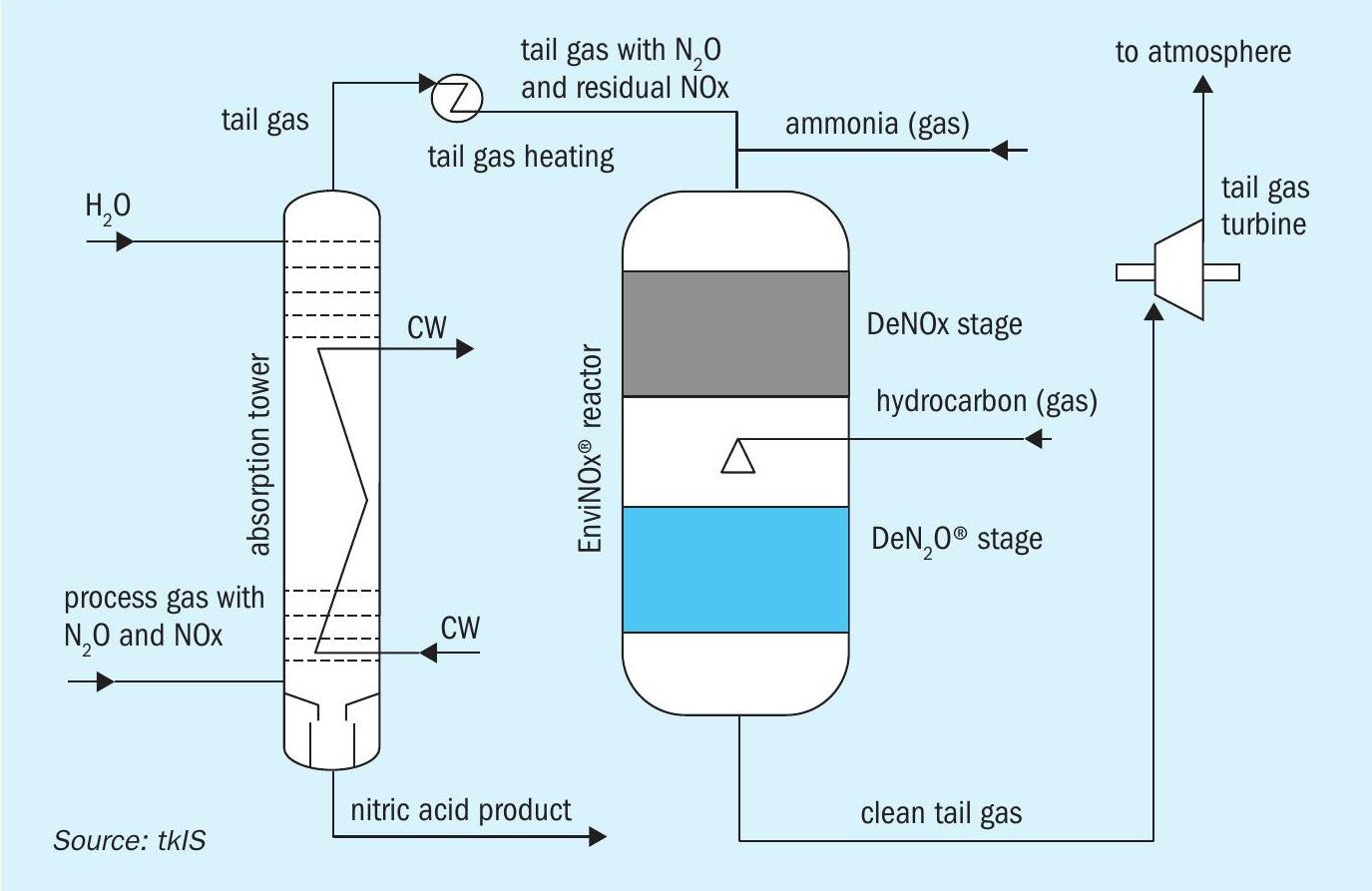
Emission rules and limits adopted by different countries are quite varied: NOx emissions are normally regulated in all countries worldwide, but emission limits in developing countries can be as much as 100 times higher than in stricter jurisdictions. As regards N2 O, most countries do not impose any emission limits. Only about a quarter of the nitric acid plants worldwide enforce a programme to reduce nitrous oxide emissions. Many of these nitric acid plants are located in Europe, where emissions trading supports plants to reduce their emissions.
N2 O/NOx abatement technologies are available to solve both emission problems.
thyssenkrupp EnviNOx® abatement process
The thyssenkrupp EnviNOx® abatement process provides an effective solution to reduce both NOx and N2 O emissions. It is an end-of-pipe technology because it is installed in the waste gas stream of the plant and thus entails no risk of product contamination, production loss or fouling of equipment (Fig. 1). Its multiple installations in nitric acid plants worldwide show N2 O removal rates of 99% and above, and elimination of NOx down to nearly zero ppm. It is also a highly practical solution as abatement of both pollutants can be combined in a single reactor vessel.
Operators can gain advantage from installing an EnviNOx® system as a greenhouse gas emission reduction project under any emission trading scheme.
Using thyssenkrupp’s wealth of experience and expertise the solutions can be optimised for particular process conditions and temperature ranges. With this proven technology to remove harmful greenhouse gases, thyssenkrupp is helping nitric acid plant operators make a key contribution to climate protection.
Use of green ammonia
In addition to the use of an abatement technology, further reduction of greenhouse gas emissions can be achieved by using green ammonia. Using green ammonia for nitric acid production, results in a much smaller carbon footprint. By partly replacing the process air in the nitric acid plant by the oxygen which is an otherwise unused by-product of the water electrolysis, or by adding this oxygen stream the plant can be significantly increased in capacity and efficiency.
Nowadays the syngas-based industry is under increased pressure, driven by low product prices on the one hand and higher environmental standards on the other hand. Producers are faced with increasing CO2 quotas or politically driven greenhouse gas reduction programs, which have caused several plant shutdowns in established markets such as China. The key objectives for the syngas industry are obvious – further increase production to serve market requirements driven by a growing world population and increasing wealth, but find process solutions with the lowest carbon footprint. The solution to stop climate change is the reduction of greenhouse gas emissions.
In order to achieve these ambitious long-term goals, different measures can be taken such as improvements in energy efficiency, an increased share of renewable energy, carbon capture and increased carbon utilisation.
Sustainability and energy efficiency are two of the key drivers for thyssenkrupp Industrial Solutions AG (tkIS). tkIS offers key elements which are important for more sustainable production processes with the target to reduce GHG emissions:
- Green hydrogen production based on alkaline water electrolysis technology provided by thyssenkrupp’s Uhde Chlorine Engineers (tk-UCE) being a Joint Venture of tkIS and Industrie De Nora either as standalone solution or as revamp option.
- Application of this to ammonia, methanol or other hydrogen-based production processes like synthetic natural gas (SNG, by methanation) and Fischer-Tropsch synthesis.
- Catalyst-based N2 O emission reduction in nitric acid plants by EnviNOx® technology.
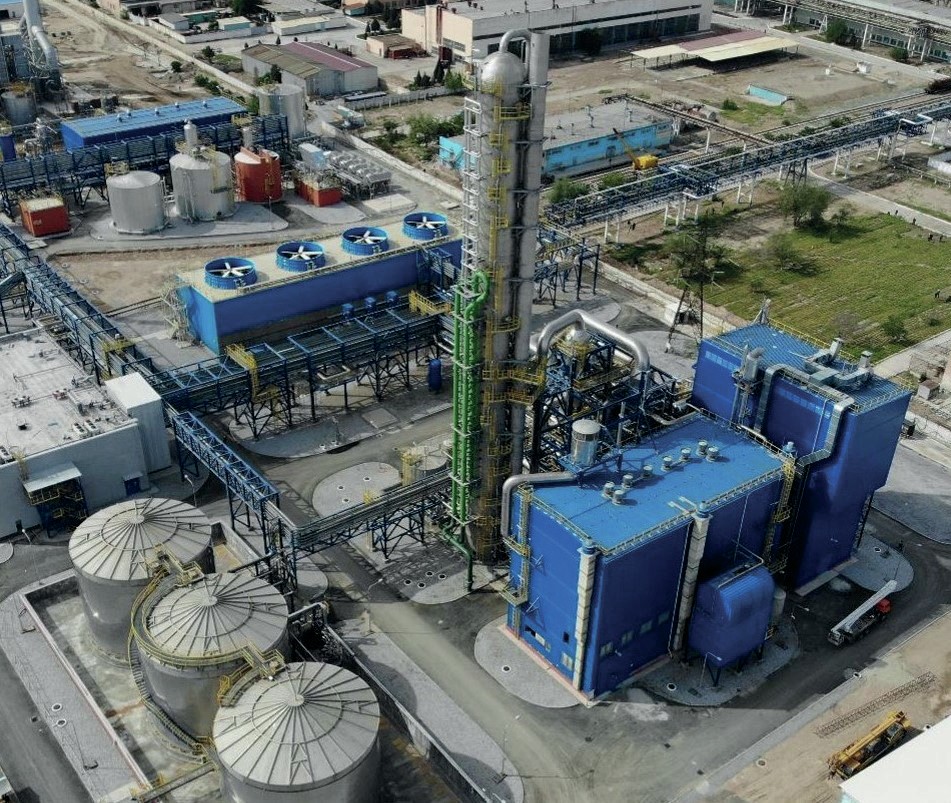
Casale nitric acid and ammonium nitrate plants
Casale is able to provide the full production line from nitric acid (HNO3 ) to ammonium nitrate solution (ANS) in compliance with the most stringent emission and liquid waste regulations. The following Uzbek case study provides an example that shows that emission reduction programmes are being progressively applied even in countries where no local emissions limits on N2O are imposed.
Uzbek nitric acid case study
In 2020, Casale completed an EPC project for a new 1,500 t/d nitric acid plant based on the dual pressure technology for JSC Navoiyazot in Uzbekistan (Fig. 2). Casale’s scope of work extended beyond the nitric acid production unit to include all the required utilities such as the start-up boiler, nitric acid storage tanks, cooling water facilities, demi water unit and the water treatment plant.
Casale provided JSC Navoiyazot with an innovative combination of know-how and technological solutions for the 1,500 t/d new nitric acid plant (based on the Casale NA2000™ process scheme), as well as an effective emission abatement system.
The JSC Navoiyazot nitric acid plant has been designed to reduce emissions in line with limits imposed by the client: NOx <50 ppmv, NH3 <5 ppmv, N2O <50 ppmv. These limits are more severe than the Uzbek limit requirements. The actual reductions achieved exceeded by far any expectations as the abatement system was able to achieve N2O and NOx slip lower than 10 ppmv and 25 ppmv respectively.
The JSC Navoiyazot catalytic system consists of the combined integration of secondary and tertiary abatement. Different catalyst arrangements can be provided depending on client requirements and emissions limits.
The burner basket design in JSC Navoiyazot is made with the provision to accommodate enough deN2O secondary catalyst to ensure substantial N2O abatement underneath the gauzes. The Casale tertiary catalyst, named GPRN20, is then installed directly upstream of the tail gas expander, where it operates at 430°C to ensure the decomposition of both the residual N2O slipping from the secondary catalyst and NOx residue from the absorber (Fig. 3).
Besides catalyst, no specific reactant is required for the DeN2 O reaction since N2O dissociation is promoted by temperature in the presence of the NOx that is naturally present in the tail gas, according to the following reaction:

NOx is decomposed by ammonia gas that is mixed with the tail gas upstream of the catalyst bed and reacts over catalyst according to the following SCR reactions:
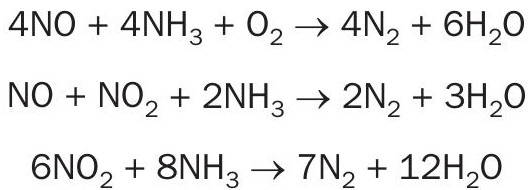
Special operating procedures and control loops are implemented in the Uzbek plant to achieve the emissions targets and ensure the accurate feeding of ammonia to the tertiary catalyst to avoid ammonia slip or overdosing. Ammonia slippage is minimised (concentration below 2 ppmv is achieved) to ensure that ammonium nitrate is not formed during start-up preventing unsafe operations. In addition, NOx concentration in the tail gas is kept below the limit of stack plume visibility during normal operation as well as during start-up.
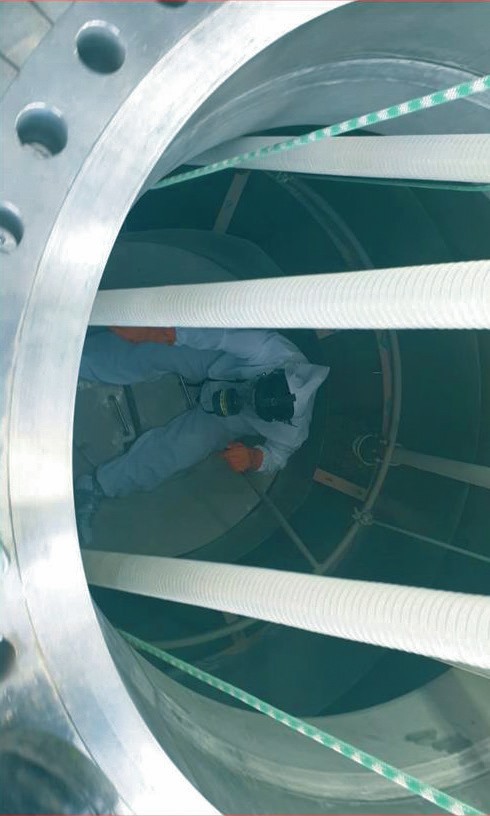
The proposed tertiary catalyst GPRN20 is industrially proven in a large variety of similar application and worldwide successfully applied with a record of long and trouble-free performances.
Casale has long experience in the design of catalytic reactors, mainly in ammonia synthesis, that has also contributed to its achievements in nitric acid applications:
- maximum abatement efficiencies with low emission levels;
- optimal gas distribution within the catalyst bed to ensure longer service life;
- reduced pressure drops over the reactor and minimized compressor energy loss.
Thanks to the remarkably high N2 O conversion, the tail gas treatment system provided by Casale was potentially able to ensure a shorter return of investment due to the higher carbon trading payback.
Casale ammonium nitrate solution process
Casale’s know how in designing ammonium nitrate plants dates back to the early 1980s, when the first ammonium nitrate plant was started-up in France by Grande Paroisse. Since then, Casale has designed more than 40 ammonium nitrate units with capacities ranging from 250 to 2,000 t/d.
Ammonium nitrate solution (ANS) is produced by the reaction of ammonia with nitric acid, which is strongly exothermic:

The main goal is to optimise the process to make the best use of the released energy and to obtain the highest ANS concentration possible. This is the base concept for the pipe reactor (Fig. 4), the distinctive Casale ammonium nitrate solution technology named AN2000™ , where neutralisation operates at nearly atmospheric pressure and maximises the use of the generated heat to achieve a high ANS concentration.
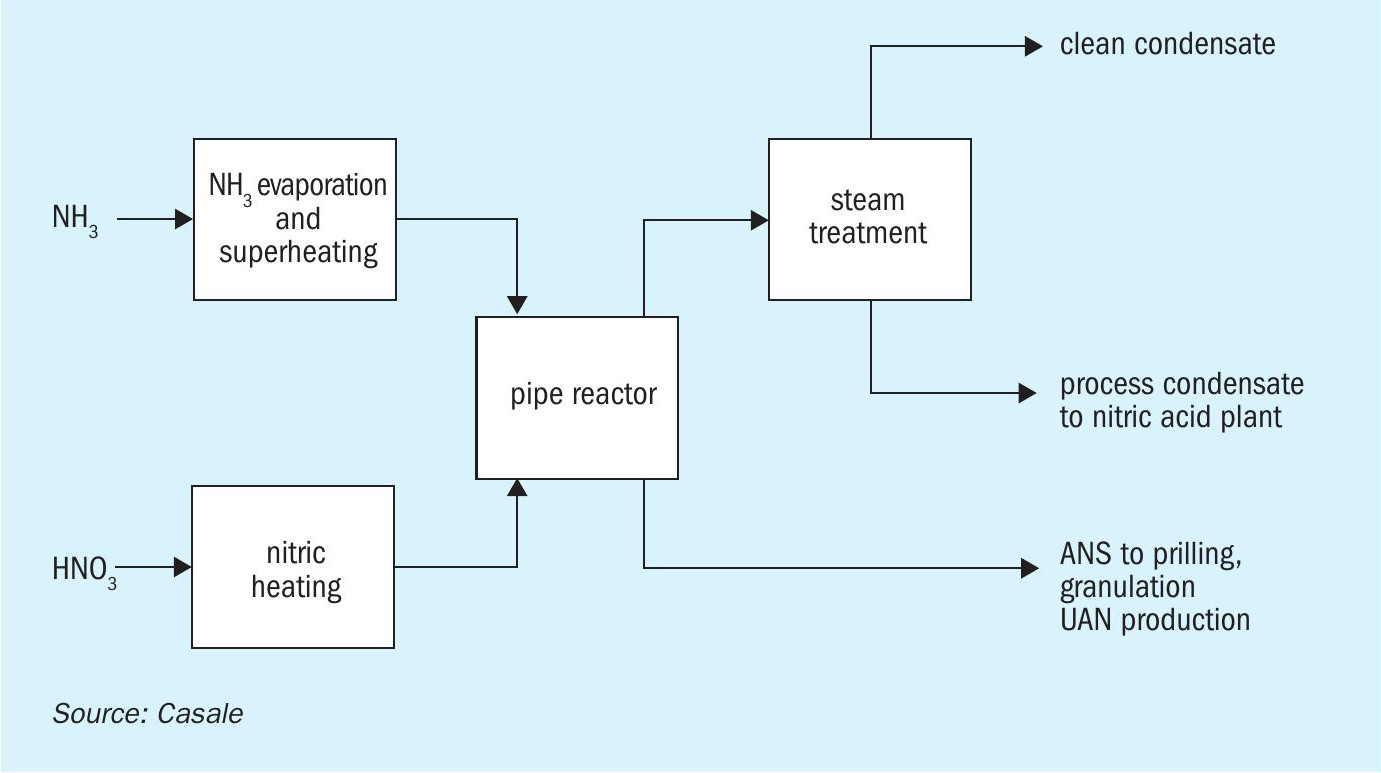
The heart of the process is the pipe reactor, where raw materials are efficiently mixed and react to produce ANS (Fig. 5). The formation of ammonium nitrate occurs almost instantaneously, releasing a significant amount of heat that is used to partially vaporise the water fed with the nitric acid. The resulting ANS product flashes into a separator, where ANS is collected at the bottom and the vaporised water is released as process steam.
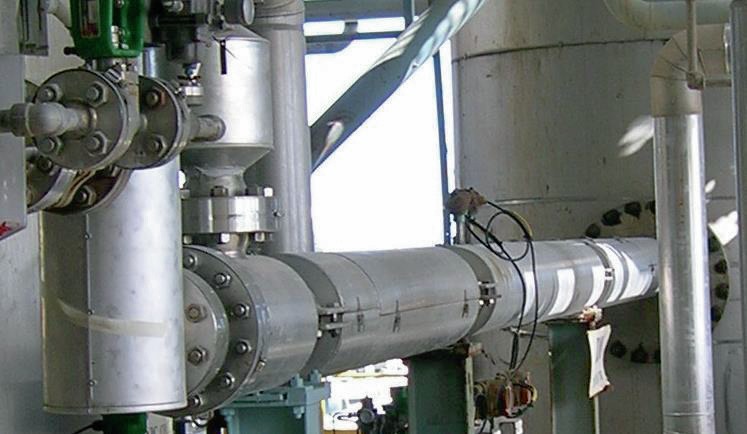
The AN2000™ pipe reactor design has undergone a series of improvements to accommodate a large range of operational requirements, while maintaining the simplicity and easy maintenance as well as the following advantages.
Safety
Safety is of paramount importance in ammonium nitrate solution production. In a pipe reactor, raw materials are mixed in an extremely small space, eliminating the need for large reaction volumes which would exacerbate the consequences of an uncontrolled decomposition. For example, the reaction volume required by a 2,000 t/d ANS plant is 0.2 m3 for the pipe reactor versus a threshold value of 20 m3 for a conventional neutraliser process.
Low capex
The process is extremely simple, thus requiring relatively few items of equipment as well as a limited footprint area. In addition, because it is an atmospheric-pressure process, it has the major benefit of a minimised capital cost.
Start-up and shutdown
Thanks to the limited reaction zone volume, the plant can be started up to from scratch to nominal capacity in less than 30 minutes. Shutdown is almost immediate once the raw material feed valves are closed.
Condensate purification
The AN2000™ pipe reactor process is intrinsically designed to have a low contaminated liquid stream (< 30 ppmw) but can be easily upgraded to a no waste effluent discharge plant.
The AN2000™ process and effluent treatment is relatively simple: steam released from the pipe reactor separator contains traces of ammonia, nitric acid, and ammonium nitrate, which are removed in a venturi scrubber, and a cyclonic column. Process steam can be further purified to the most stringent limits without requiring any external energy stream using the Casale Purifier Exchanger.
This Purifier Exchanger re-evaporates part of the process condensate in the shell side through the condensation of the process steam from the cyclonic column in the tube side (Fig. 6).
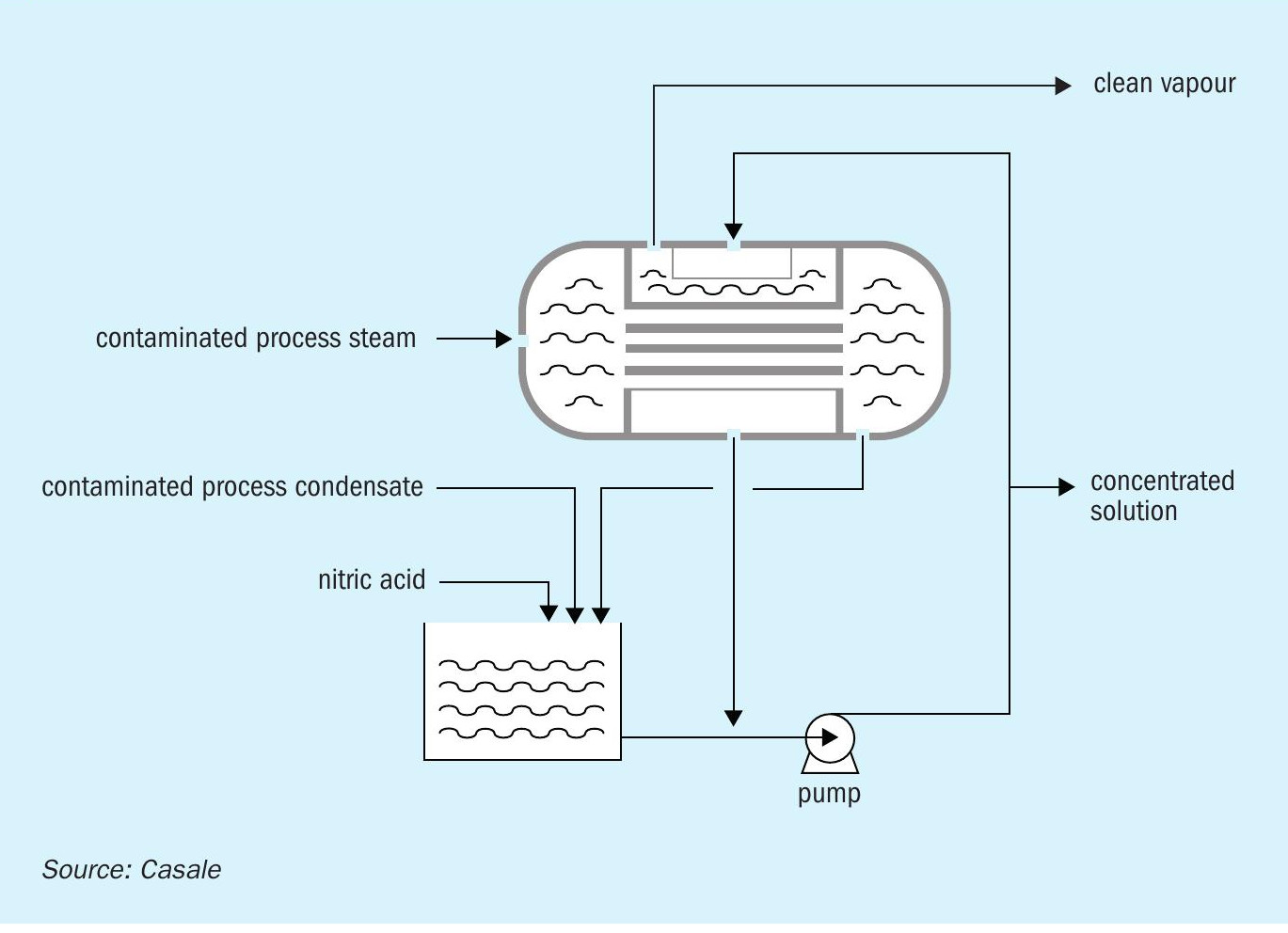
This simple operating step makes it possible to concentrate the contaminants in a single stream while the clean stream is purified up to a level (<30 ppmw) allowing it to be reused as DW or cooling water make-up within the fertilizer complex.
The concentrated condensate stream is then partially reused internally in the cyclonic column and the resulting amount is recycled to the absorption tower of the nitric acid unit. In this way it is possible to prevent environmental impact from the ammonium nitrate solution plant.
The typical mass ratio between the clean and concentrate condensates is 2:1 respectively, ensuring a substantial reduction of the waste liquid, resulting in more economic management of the liquid effluents.
In some cases, this latest option may not be viable in the client complex set-up, e.g. when the nitric acid plant is not available at the site or the nitric acid produced has a dual use as raw material for fertilizers and chemicals preventing the recycle of the concentrated condensate. To overcome such issues, the purification capacity can be doubled by installing two Purifier Exchangers in series (Fig. 7) to boost the clean steam generation, additionally combined with a reverse osmosis package to further improve recovery of the concentrated condensate stream.
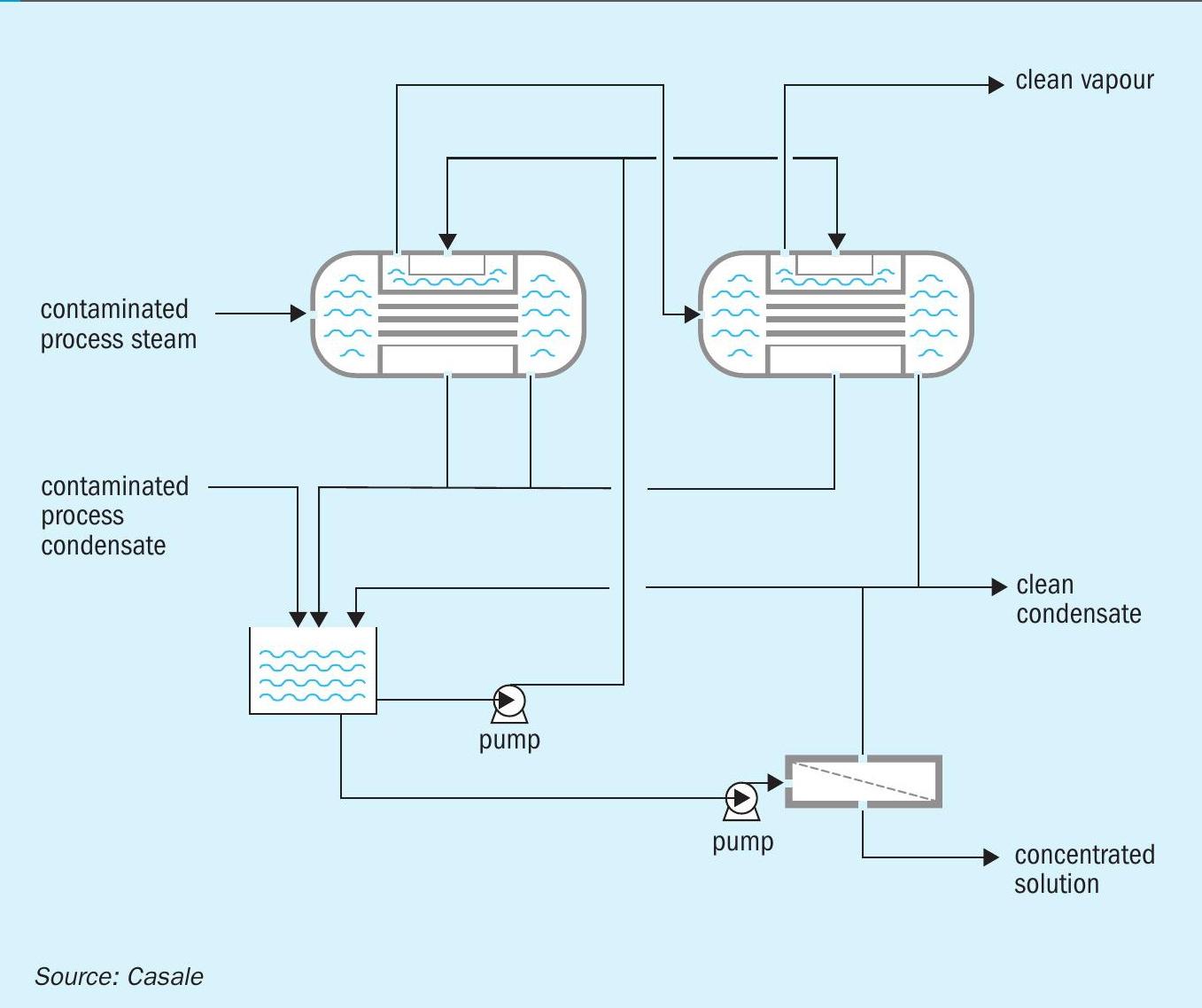
In this way, the concentrate condensate can be reduced to an amount suitable for internal reuse in the ANS scrubbing and cyclonic unit, making the entire ANS plant virtually a no liquid effluent plant.
The AN2000™ pipe reactor process is also intrinsically designed to have no gaseous emissions since the steam generated is fully condensed either as heating steam for the raw materials or in the Casale Purifier and later in a cooling water condenser, with substantially no vapour streams released to the atmosphere.