Nitrogen+Syngas 374 Nov-Dec 2021
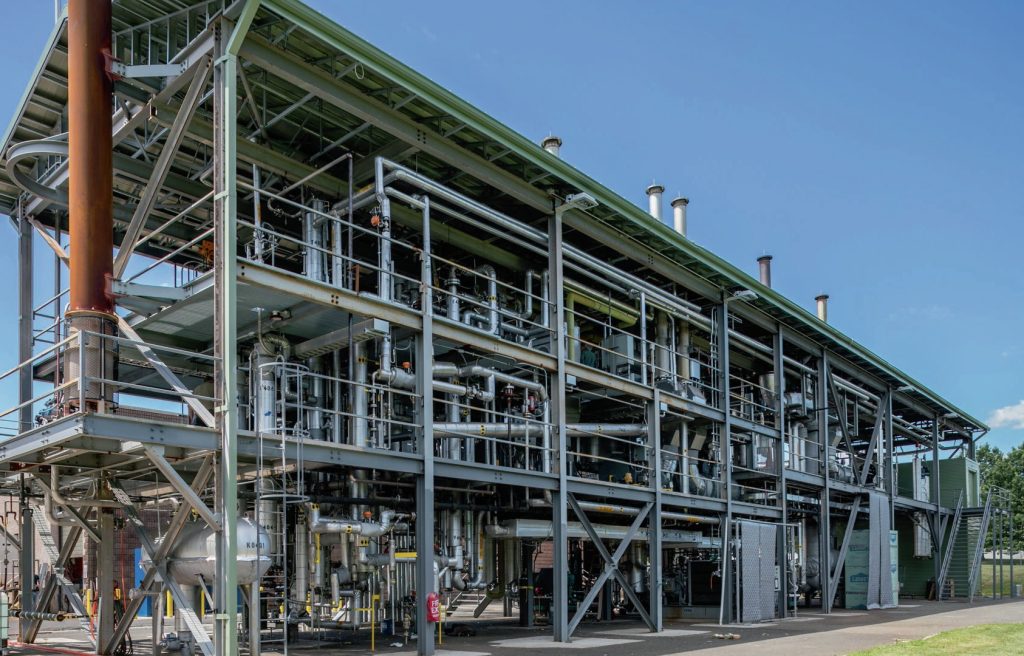
30 November 2021
Modular plant design
MODULAR CONSTRUCTION
Modular plant design
A move towards smaller scale feedstocks such as renewable energy and waste and biomass gasification is leading to increased focus on improving the efficiency of small-scale, modular plants.
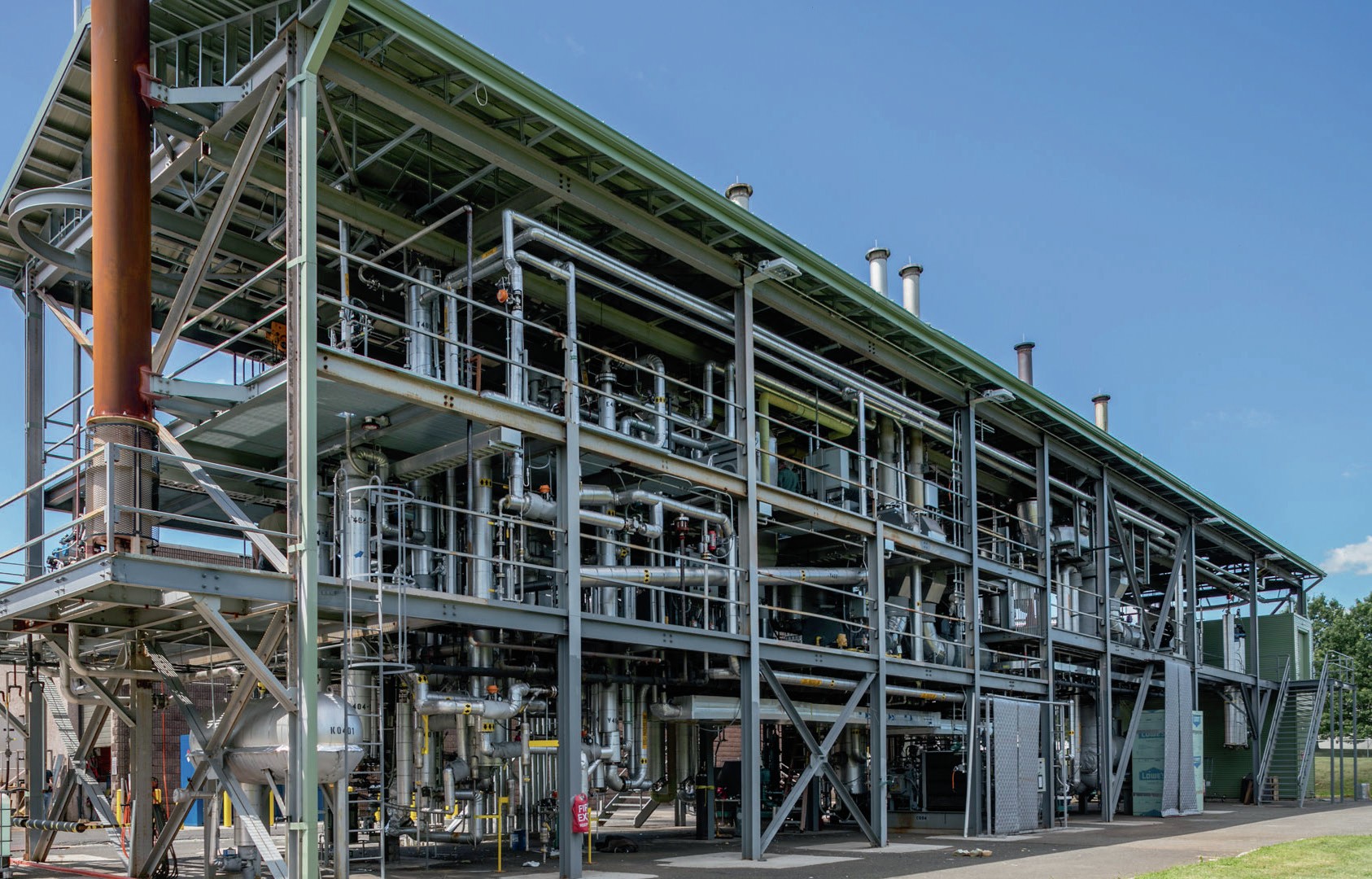
Construction of a chemical process plant as several pre-built modules which are then transported separately to a final site and assembled is not a new concept. However, modularisation is seeing an increase in interest in the ammonia and methanol industries for a variety of reasons.
Primary among these is the move to smaller scale feeds for a syngas plant. Previously the industry had moved towards large scale plants to capture economies of scale, and plants are still offered and (at least on the methanol side) built with capacities of up to 7,000 t/d. But these rely upon access to either large coal deposits – an increasingly untenable option in today’s world without some form of associated carbon capture and storage – or large scale natural gas feeds. But large gas feeds are becoming scarcer; the growth of the global LNG market means that large gas deposits usually prioritise LNG export where possible. Where ‘stranded’ gas is still available, it is often from either flared gas from oil deposits or isolated shale gas wells, where the amount of gas available is much smaller.
And then there is the move towards more environmentally friendly production, either through gasification of municipal waste or waste biomass, or from hydrogen generated by electrolysis using renewable energy. All of these operate on much smaller scales than would be required to feed a modern world-scale ammonia or methanol plant.
Smaller scale production makes plant financing easier, and also opens up the option of modularisation. This can offer a number of potential advantages compared to conventional construction. To begin with, it means that most of the construction work can be carried out in a carefully managed environment, reducing risks and leading to increased construction safety and productivity, leading to lower costs and shorter lead times. It minimises site preparation such as foundation laying and reduces the time needed to rent large cranes and the like. It also reduces the number of skilled workers required to assemble the plant, which can be a limiting factor, and can reduce the difficulty of transport of large equipment items to remote areas. At the very smallest scales, modules can be built to standard ISO container sizes, making transport very cheap and easy.
There are drawbacks as well. Module construction requires more steel than traditional construction, because each module needs to be designed and built to stand independently and to withstand the stresses of being transported, lifted, and erected. The units are therefore structurally stronger than conventional units constructed onsite, but more expensive.
Furthermore, without the advantages of large throughput, the capital intensity of each tonne of ammonia or methanol produced is usually higher for a smaller scale plant. However, if it offers the possibility of being produced closer to an end use market because it is using more environmentally friendly technologies, rather than a remote low gas cost location, then what it loses in capital cost it may recoup in reduced transport costs and potentially lower operating costs. Most major plant licensors now offer modular options for small scale (less than about 300 t/d) plant design and construction, and where modularisation offers the possibility of building multiple copies of the same equipment item, then this may also bring overall costs down. Small scale production can require a rethink of the entire process, but in so doing also open up the possibilities of using, e.g. microchannel reactors, plasma flames, semi-permeable membranes and other innovative design features which can bring costs down, by lowering temperatures or pressures required to achieve synthesis.
At the moment, many of these small scale modular plants are at the pilot or demonstrator plant stage, and there has not been a large-scale take-up. However, the current push to decarbonise chemical production may just provide the impetus that the industry needs to adopt widespread use of smaller scale, modular production.