Sulphur 397 Nov-Dec 2021
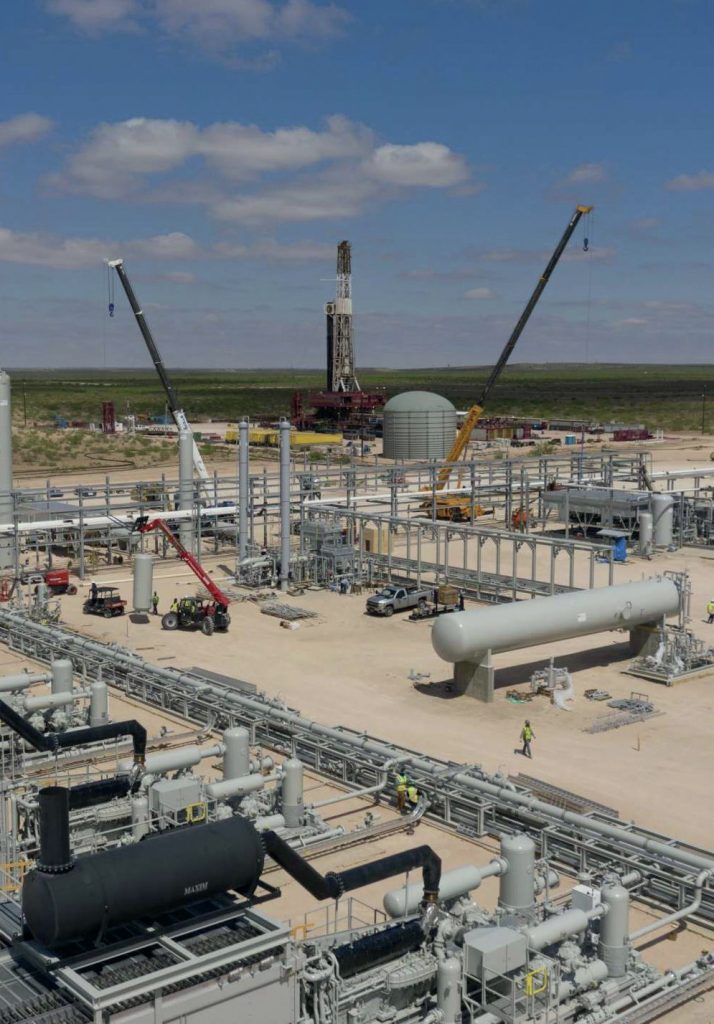
30 November 2021
Sulphur Industry News Roundup
Start-up imminent for Shenghong refinery
China’s private sector Shenghong Petrochemical refining complex is targeting a startup in late November, following the receipt of its first cargo of crude in October. The greenfield refining complex in the eastern Lianyungang petrochemical zone has a capacity of 16 million t/a, including a 320,000 bbl/d crude unit – the largest single stream CDU in China – and a 76,000 bbl/d naphtha reformer. Product capacities include 56,000 bbl/d of gasoline, 41,000 bbl/d of diesel and 32,000 bbl/d of jet fuel. Construction began in mid-2019, delayed from 2018 by late approval of its environmental impact assessment, but has been achieved within two months of the scheduled completion date in spite of the coronavirus pandemic. Shenghong Petrochemical is owned by Eastern Shenghong, a producer of petrochemical products and chemical fibres.
Like other major new greenfield refineries Rongsheng ZPC and Hengli Changxing, Shenghong is designed to use sour crude from the Arabian Gulf. The refinery’s sulphur recovery section has a capacity of 600,000 t/a.
POLAND
Tecnimont to build new hydrocracker
Maire Tecnimont says that its subsidiary KT – Kinetics Technology has been awarded a e200 million lump sum turnkey engineering, procurement and construction contract by LOTOS Oil, to build a new hydrocracking unit with associated logistic facilities for the LOTOS Gdansk refinery. Project completion with fully operational facilities is expected by the first half of 2025. This plant will be capable of treating better performing base oil groups, with a lower environmental impact. International environmental regulations are driving the need for higher quality base oils, especially in the automotive sector, where engine oil manufacturers are responding to increasing demand for low sulphur and energy-efficient products.
Pierroberto Folgiero, Maire Tecnimont Group CEO, commented: “We are delighted to continue our long-lasting, mutually beneficial cooperation with such a prestigious client, thanks to this third EPC project awarded to our Group and concerning the Gdansk Refinery. With this award we further strengthen our footprint in Poland as well as our strong commitment to support the LOTOS Group in ensuring the best environmentally performing processes and products”.
PAKISTAN
Axens to modernise Byco refinery
Axens has been selected to support Byco’s refinery upgrade project in order to meet Euro V gasoline and diesel specifications in Pakistan. The scope of Axens’ work includes the supply of a process design package for integration of three existing units into a FCC gasoline hydro-treating configuration using licensed Prime-G+ ® technology, as well as catalysts and adsorbents for the sulphur recovery unit and hydrotreaters, internals for the distillate hydrotreater, training and long term technical services. The upgrade is scheduled to be completed by Q2 2024. The award follows cooperation between the two companies that began in 2019 when Byco awarded Axens a study to evaluate the configuration of units for the modernisation. Byco operates Pakistan’s largest refinery, a 156,000 bbl/d facility at Mouza Kund, 20km west of Karachi.
COLOMBIA
Ecopetrol looking to green and blue hydrogen
Colombia’s state-owned Ecopetrol says that it is looking at a variety of green hydrogen pilot projects, including for its Cartagena and Barrancabermeja refineries, with a total investment cost of $200-300 million. The first step on the company’s hydrogen roadmap will be to import an electrolysis unit from Spain in 1Q 2022 to test integration with existing hydrogen production at its 165,000 b/d Cartagena refinery, on the Caribbean coast. Ecopetrol’s refineries consume 130,000 t/a of hydrogen as part of desulphurisation sections, most at Cartagena and around one third at its 250,000 bbl/d Barrancabermeja refinery. The company is also looking at producing up to 50,000 t/a ‘blue’ hydrogen, using carbon capture and storage, by 2030.
SWEDEN
Sandvik extends collaboration with Tenaris
Tenaris and long-standing business partner Sandvik Materials Technology say that they are extending their nearly 20-year alliance with the signing of a new fiveyear agreement for the supply of tubular products with premium connections and specialty steel alloys for the oil and gas market. The renewed agreement combines Sandvik’s expertise in material technology and the development of corrosion-resistant steel alloys with Tenaris’s excellence in the manufacture of high-quality, high-performing piping and connections.
KUWAIT
SRU fire at Mina al-Ahmadi
On October 18th a fire broke out in the sulphur recovery unit of the Mina Al-Ahmadi oil refinery in Kuwait, operated by the Kuwait National Petroleum Company (KNPC). There were no deaths but some minor injuries and several were treated for smoke inhalation. The fire occurred in the atmospheric residue desulphurisation unit (RDU), but forced the shutdown of one of the refinery’s two large 180,000 bbl/d crude distillation units. It was expected to take around three weeks to repair damage and restart production. The incident comes less than a month since full operations began at KNPC’s Clean Fuels Project (CFP). The project involved the upgrade and integration of the firm’s Mina al-Ahmadi and Mina Abdullah refineries, although the RDU was not part of the upgrade.
WORLD
HSFO market remains strong as ships switch to scrubbing
Platts reports that, contrary to initial expectations about the switch towards lower sulphur bunker fuels as part of the International Maritime Organisation’s low sulphur mandate, the high sulphur fuel oil (HSFO) market has remained relatively strong due to the uptake of exhaust scrubbing systems. Very low sulphur fuel oil (VLSFO) does represent 60-65% of global bunker demand at present, but in Singapore, the world’s largest bunkering port, HSFO demand has remained strong, with sales of HSFO up 2.7% year on year, as larger ships, which tend to be the ones with scrubbing systems, use the port. Users of VLSFO pay on average a $100/t premium over HSFO, which can make the cost of scrubbing systems attractive, especially for new build vessels.
UNITED STATES
Piñon sour gas facility nearing capacity
Piñon Midstream says that its greenfield sour gas treatment and carbon capture facility in New Mexico is near its initial capacity, and the company is installing its second facility. The 85 million cfd Dark Horse facility, in Lea County New Mexico, uses amines to strip carbon dioxide and hydrogen sulphide from natural gas and delivers sweet gas to third-party midstream operators. The sequestered acid gas is then reinjected into the well. A second, 170 million cfd treatment facility is expected to be completed before the end of the year. The company says that the first well has the capacity to permanently sequester up to 175,000 tonnes of CO2 and 75,000 tonnes of H2 S per year. The company is also adding a second well that will be completed in 2022 which will double this.
“We are excited to announce that our Dark Horse Facility is open for business,” said Piñon Midstream co-founder and president Steven Green. “The producers in our area have had a dire need for a long-term and environmentally friendly solution to the extreme acid gas concentrations that have previously challenged the region. By removing and sequestering these gases, the Dark Horse Facility makes it possible for operators to realise a single-source solution to CO2 and H2 S contaminants that are prevalent throughout the basin.”
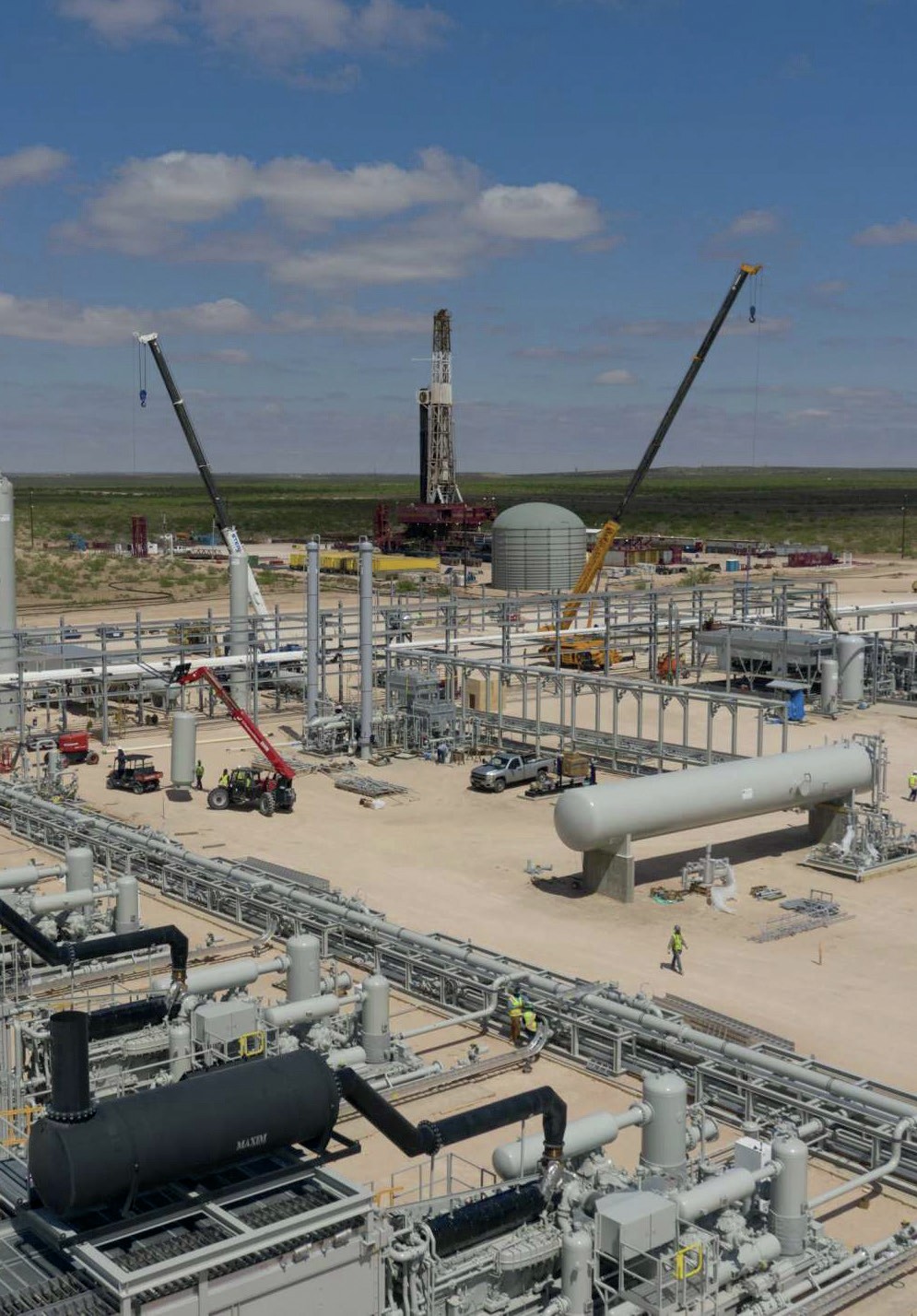
Flame retardant sulphur plastics
University of Arizona researchers say that they have developed a way to turn sulphur into a flame retardant, high-end plastic. The work comes at the end of 10 years of research by the team to find uses for elemental sulphur. Two years ago, Jeff Pyun, a professor in the Department of Chemistry and Biochemistry and his colleagues, created lenses made of sulphur for infrared detectors. Now, they have created a high-end thermoplastic elastomer out of sulphur. The material is rubbery, elastic and mouldable compared to stiffer plastics. Other types of thermoplastics are used to make the grips on items such as power tools, pens and toothbrushes. The sulphur plastic created by Pyun and his team is flame retardant; soon as it catches fire, it immediately self-extinguishes instead of burning and creating heat and smoke. The researchers’ work was funded by Eni, which partnered with the University of Arizona to develop and translate the technology.
“We are still in the early developmental stages, but this is the first demonstration of a polymer with these properties,” said Pyun. The team’s work is detailed in Angewandte Chemie, a journal of the German Chemical Society. “It really stands out.. because almost all plastics are flammable,” Pyun said. “Most plastics today are very cheap and have excellent mechanical properties that can be tunable over a broad range of products from automobile engine parts to rubber tires, but they’re flammable. Plastics that have really good properties and are flame retardant, such as this one, are very expensive. What we eventually want are plastics that are low-cost, with good properties, and are flame retardant.”
UNITED ARAB EMIRATES
ADNOC looks to huge LNG export terminal
The Abu Dhabi National Oil Company (ADNOC) is reportedly planning a huge LNG export terminal at Fujairah on the Gulf of Oman coast of the United Arab Emirates. Reports suggest that the company is considering 9.6 million t/a of LNG export capacity, aimed at markets in India, Pakistan, Japan and elsewhere in Asia. ADNOC has recently sought expressions of interest from several international engineering contractors for conceptual studies and for front-end engineering and design (FEED) work on the surface facilities required at the huge terminal. ADNOC currently can produce 11 bcf/d of natural gas and 1.3 bcf/d of sour gas, but is involved in several large developments to boost this capacity, including the Hail, Ghasha and Dalma projects. It is expanding its huge Shah gas project, developing the Umm Shaif gas cap reservoir and expanding into unconventional gas.
RUSSIA
Russia adding major new gas processing capacity
Russia is expected to dominate the Former Soviet Union (FSU) region in terms of the number of gas processing capacity projects expected to be planned or announced between 2021 and 2025, according to GlobalData. The leading data and analytics company notes that Russia will contribute around 77% of FSU additions by 2025. The huge increase in gas processing capacity, totalling up to 10.3 billion scf/d, will help Russia to meet growing domestic demand and export gas as LNG and through pipelines.
Teja Pappoppula, Oil and Gas Analyst at GlobalData, comments: “Ust-Luga is the largest upcoming gas processing plant in Russia and is expected to help the country meet demand for natural gas in the peak winter season. Operated by RusKhimAlyans, the processing plant is expected to start operations in 2024.”
Uzbekistan ranks second in terms of gas processing capacity additions, with a planned and announced gas processing capacity of 1.5 bcf/d by 2025. Mubarek II is the major gas processing plant during 2021 to 2025 with a proposed capacity of 580 million scf/d. The planned gas processing plant is expected to start operations in 2022. Third is Kazakhstan, which will have a planned and announced gas processing capacity of 1.06 bcf/d by 2025. Tengiz II is the largest upcoming gas processing plant in the country and is slated to begin operations in 2024 with a capacity of 937 million scf/d.