Fertilizer International 508 May-Jun 2022
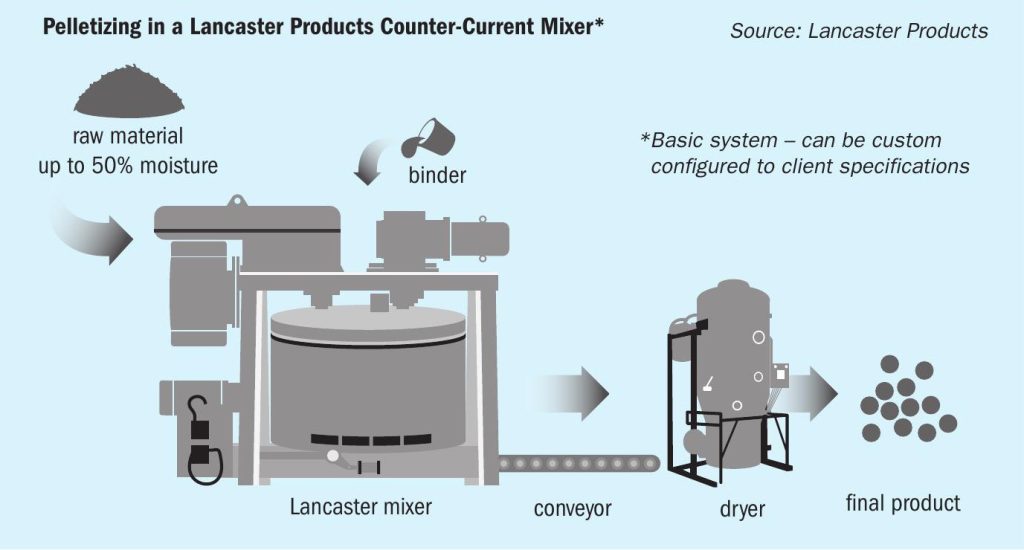
31 May 2022
Enhanced mix-granulation in a single machine
FERTILIZER FINISHING
Enhanced mix-granulation in a single machine
The precision mixing and granulation of mineral and organic fertilizer ingredients are essential to meet growing market demand for high-value, complex crop fertilizers. Furthermore, the ability to mix and granulate in a single machine offers fertilizer manufacturers both operational and product quality advantages over traditional granulation methods.
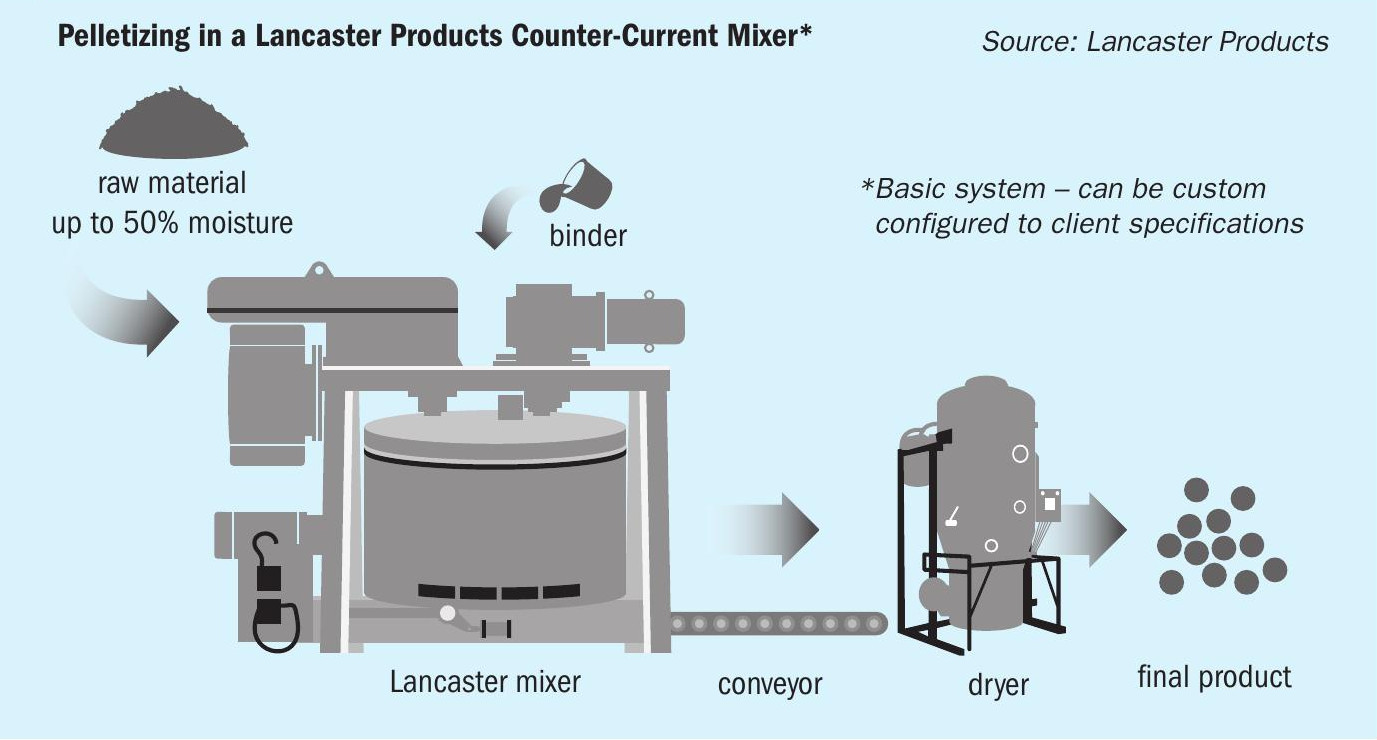
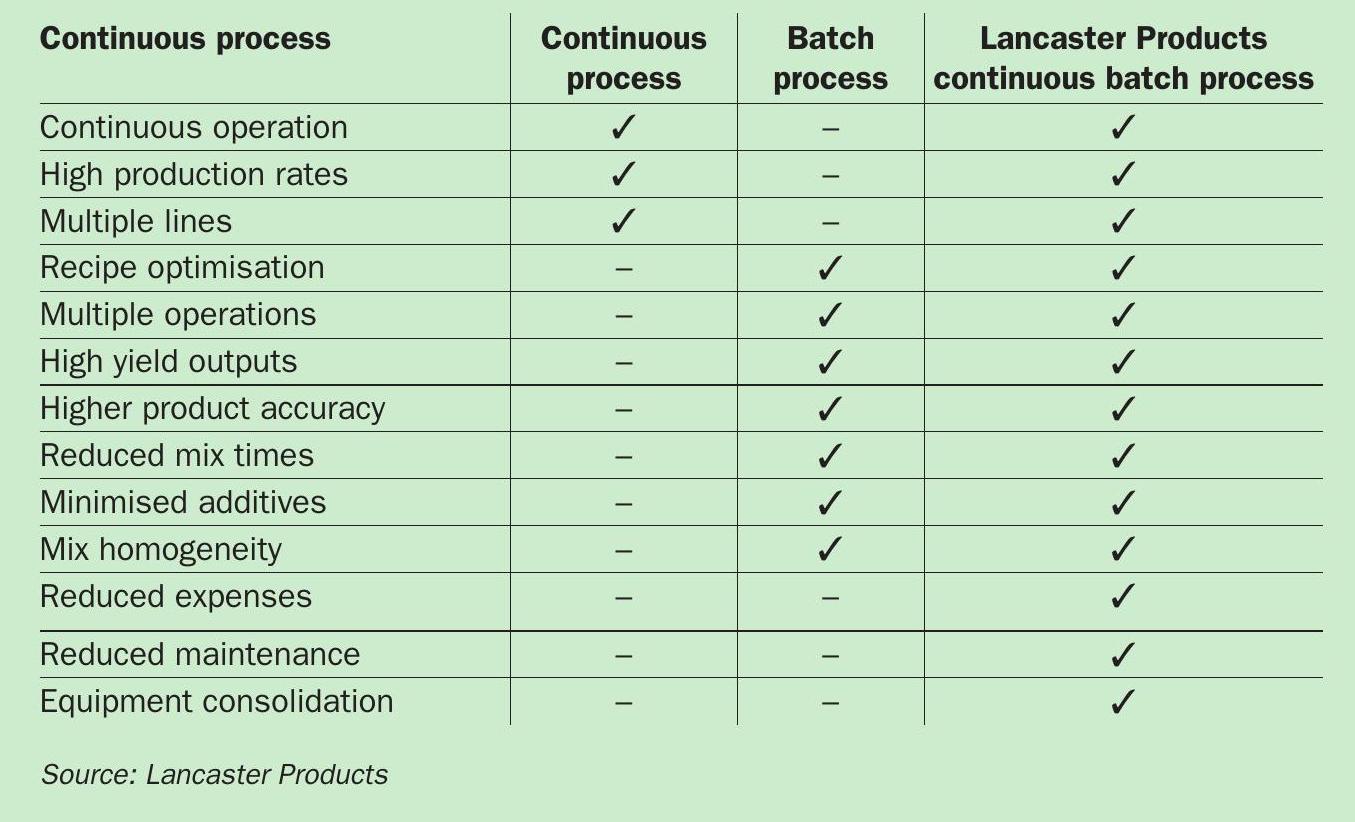
Disc granulation vs mix-granulation
Disc granulation is the method commonly used to produce fertilizer granules. This two-stage process typically employs a pin mixer (or similar mixer type) to pre-mix powdered materials to provide the feed for the disc pelletiser. The process generally requires the addition of large amounts of binder and water to create the finished product. This traditional type of granulation process is often not ideal as it generates lower yields of on-size pellets (1-3 mm) leading to high recycle loads.
In comparison, high shear, countercurrent mixers – unlike most granulation options – can rapidly mix and granulate materials in the same machine as a single-stage process. In mix-granulation equipment, such as those offered by Lancaster Products, the pan rotates in a clockwise direction, while the mixing tools rotate counter-clockwise direction. This design results in efficient counter-current mixing by creating the necessary shearing action within the mixing cavity.
The mixing tool’s variable speed capability achieves the desired output by enabling different sized granules and densities to be created. A wide spectrum of granule sizes – from the micron range to as large as 8-10 millimetres – are possible depending on the feed materials. Mix-granulation is completed in batches and excels at producing highly repeatable homogeneous mixes and granules (Figure 1).
Reduced system complexity
Traditional fertilizer manufacturing typically requires multiple steps and many different pieces of machinery for drying, milling, mixing and agglomeration. Additionally, initial drying of high moisture raw materials is often required prior to processing – adding extra time and energy costs to the manufacturing process. Mixing and granulating in the same step in a high shear, counter-current mixer is advantageous as it reduces system complexity in several ways (Table 1):
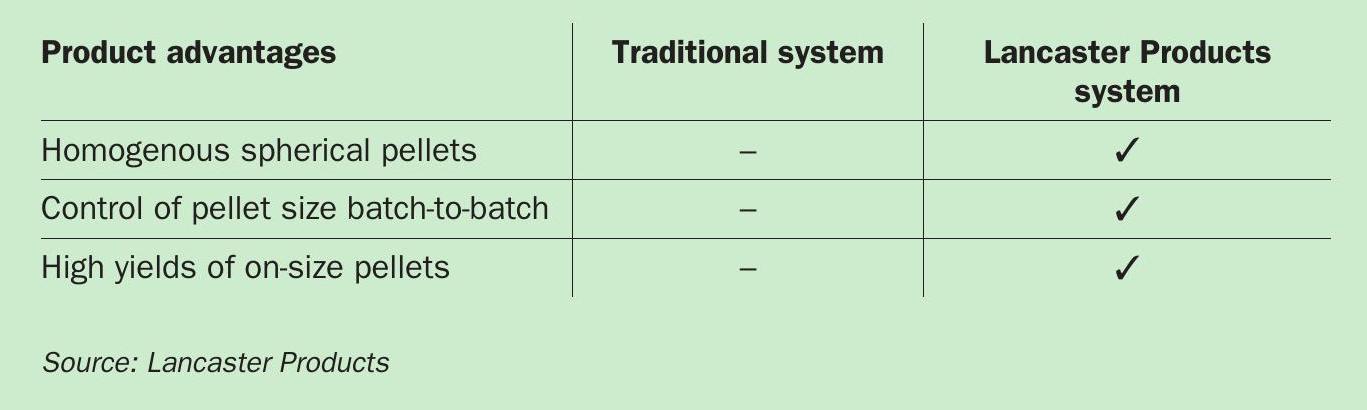
- Reduced physical footprint. The continuous batch process offered by Lancaster Products requires very little square footage due to its vertical design which employs gravity for material transport.
- Operates with high moisture materials. Initial drying and subsequent milling in the manufacturing process can also be eliminated or greatly reduced as the mix-granulation process handles raw materials with up to 50 percent moisture.
- Less maintenance and energy use. The replacement of multiple machines typically found in traditional pelletising process lines with a single high shear, counter-current mixer translates into less maintenance, fewer points of failure and reduced energy usage. l Optimised ingredients and lower operating costs. Precise batch recipes eliminate the ingredient waste that results from uneven mix distribution. Instead, much less binder and water is required because counter-current mixing technology is highly effective at thoroughly dispersing such additives throughout the main ingredients.
Enhanced product characteristics and reproducibility
In complex fertilizers, thorough mixing of individual nutrients (e.g., N, P and K macro-nutrients plus secondary nutrients and micronutrients) is required to ensure maximum agronomic effectiveness without over/under application to the field. The multi-tool mixing action in counter-current technology delivers this, providing homogeneous mixing with rapid mix times.
Because the pan, high speed rotor and plow are individually controlled, the mixer can create exact and repeatable conditions within the mixing cavity to produce specific products – e.g., granules of a specific size within a tight tolerance. Valuably, even slight adjustments to tooling speeds can produce different sized granules, shapes, densities, and yields.
Mix-granulation also offers the following product quality advantages (Table 2):
- Homogeneous pellets with improved ingredient distributions
- High yields of on-size pellets with substantially less need to reprocess off-size product
FERTILIZER GRANULATION CASE STUDIES
Methodology
Proof of concept testing optimises mix design by identifying product and process goals. Mix-granulation tests using a Lancaster Products mixer provide the opportunity to demonstrate granulation improvements over other mixing and/or agglomeration equipment. Design objectives can include:
- Mixing cycle times
- Binder and ingredient optimisation
- Homogeneity l Particle hardness, moisture and air entrainment
- Particle-size distributions and yields.
- In the following two fertilizer product case studies, the test metrics for mix-granulation included:
- Input moisture
- Operation cycle time (mix-granulation)
- On-size percentage yield.
Case study 1: potash-based fertilizer
Mix-granulation of a potash-based formula (see photo 1) in a Lancaster Mixer resulted in very effective granulation to the target size (2-4 mm) with an exceptional yield of 92.3 percent. Efficient mix-granulation occurred in a cycle time of 540 seconds (9 minutes).
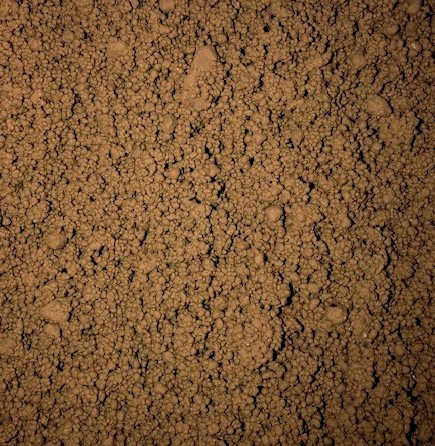
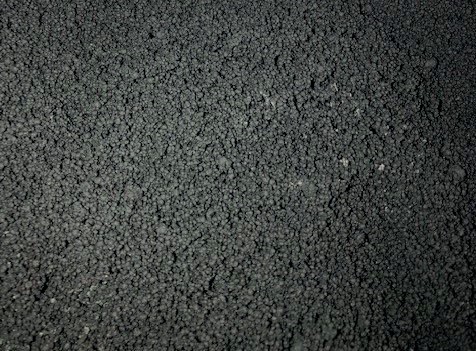
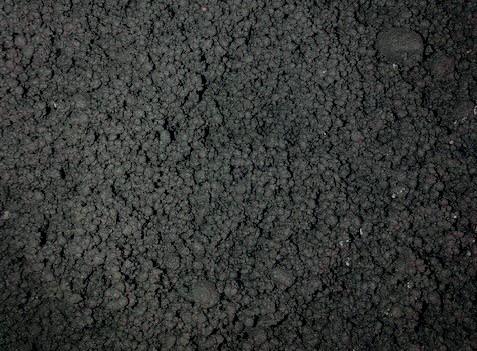
Case study 2: carbon char-based fertilizers
Mix-granulation was performed on two carbon-char based blends (see photos) with the following results:
- Experimental blend 1: water only. Mix-granulation of dry ingredients (34% input moisture) with water resulted in exceptional yield (90.8%) within a tight pellet size range (1-4 mm) for a cycle time of eight minutes.
- Experimental Blend 2: organic waste by-product used a binder. This blend (28% input moisture) eliminated the need for any water addition. Target sized pellets (1-4 mm) were achieved at a high yield (88.5%) for a 10-minute cycle time.
Other organic and inorganic materials
Lancaster Mixers are being used to granulate both fertilizers and soil amendments using a variety of raw materials. These include:
- Organic raw materials: manure, chicken litter, biochar, animal meal, humic acid, compost, biosolids.
- Inorganic materials: lime, synthetic gypsum, phosphates, potash, humates.
- Versatility to control pellet size and characteristics on a batch-by-batch basis.
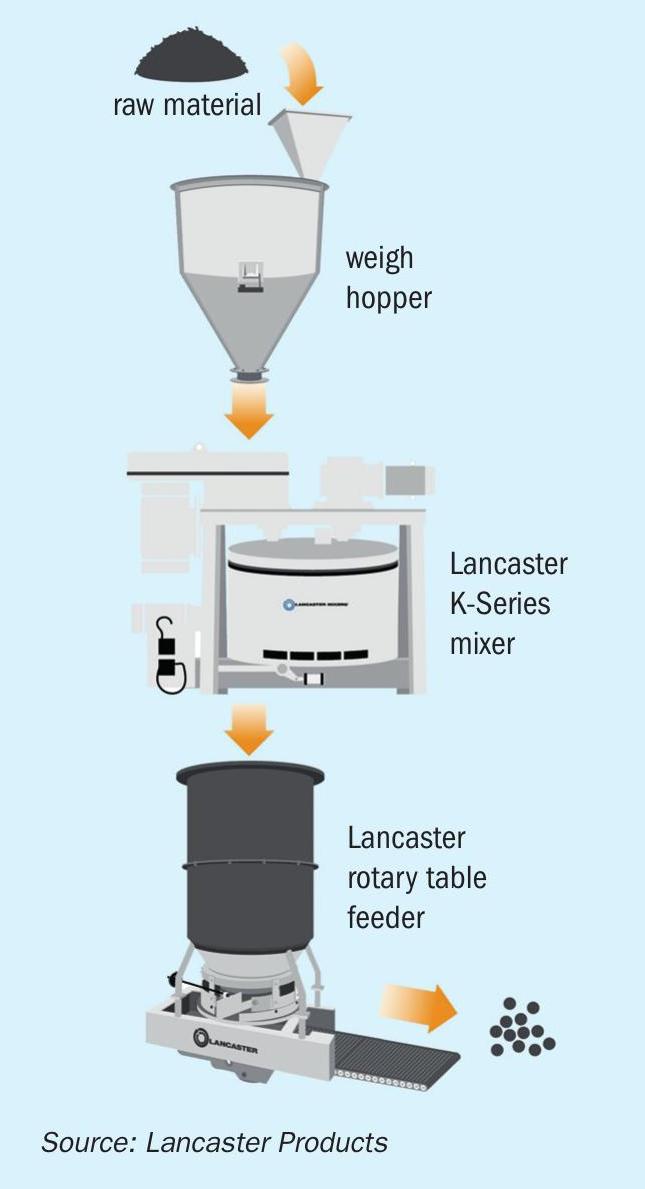
Increasing throughput with continuous batch processing
Batch processing of complex fertilizers offers both greater product accuracy and high yield outputs. The other key advantages of a batch process are recipe optimisation and mix homogeneity. In fact, there are no real downsides because – with a continuous batch configuration – these important benefits can be realised simultaneously with the consistent throughput and high production rates of a continuous production line.
A continuous batch processing system (Figure 2) is configured sequentially as follows:
- The process begins with pre-weighed raw materials and binders l These are delivered to the mixer via a weigh hopper
- The high shear mixer runs through a dry mix, a wet mix and then continues to a granulation cycle
- The material is then discharged from the mixer to a conveyor or table feeder – this converting the batch process into a continuous flow of materials
- Parallel lines for redundancy, or systems with multiple mixers, can also be utilised to increase output capacities.
Conclusions
Rapid growth in worldwide agriculture markets is driving up demand for complex fertilizers. This increasing requirement for products with specific and/or novel ingredient formulations means fertilizer producers are in urgent need of efficient and flexible granulation techniques. Simplifying the fertilizer granulation process, while simultaneously increasing throughput and lowering costs, all contribute to delivering high value fertilizer products to customers, at increased profitability. Advanced technologies such as mix-granulation offer fertilizer manufacturers opportunities to achieve these objectives – by combining high shear, counter-current mixing with continuous batch processing.