Nitrogen+Syngas 380 Nov-Dec 2022
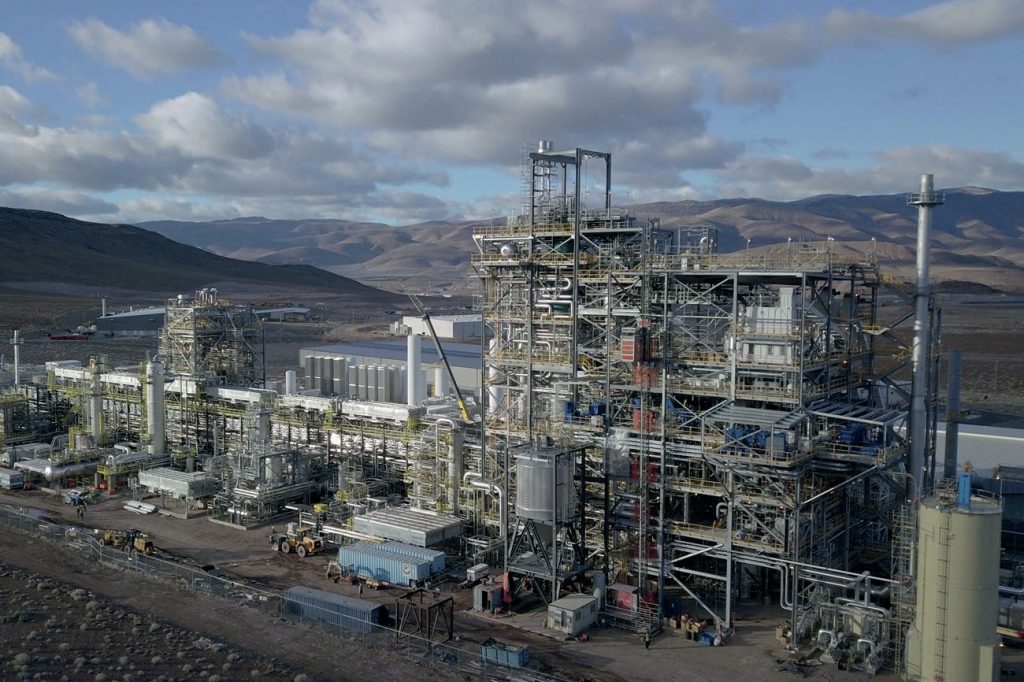
30 November 2022
Green Fischer-Tropsch technology routes
FISCHER-TROPSCH
Green Fischer-Tropsch technology routes
Fischer-Tropsch technology has long offered alternative production routes to synthetic fuels, but has struggled to make a use case outside of some niche applications. Could the greening of the chemical industry offer another way forward for the technology?
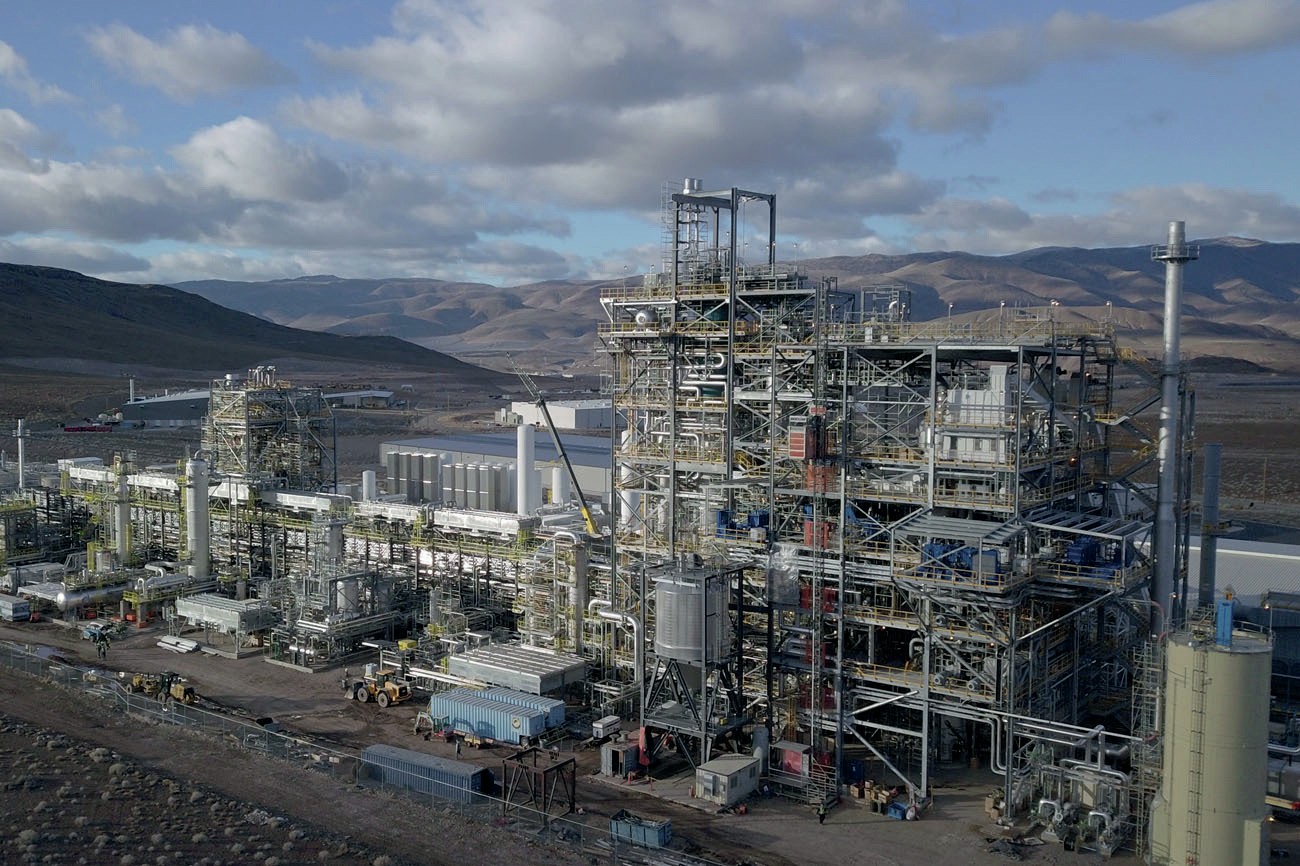
The Fischer-Tropsch polymerisation reaction converts synthesis gas into longer chain hydrocarbons. It was first developed by Franz Fischer and Hans Tropsch at the Kaiser Wilhelm Institute for Coal Research in Mülheim, Germany, in 1925. It effectively allows for the production of synthetic fuels and waxes from any feedstock that can generate syngas. Initially it was seen as a means of converting coal into liquid fuels for countries that were short of oil supplies. The reaction is catalysed by iron or cobalt-based catalysts, though due to the lack of selectivity, a wide variety of side reactions occur allowing for significant variation in end product between feed mixes and catalyst types. Cobalt-based catalysts give a higher yield of middle distillate products and show higher selectivity for paraffinic derivatives at low temperatures; hence, they can be used to produce sustainable aviation fuel (SAF). Iron-based catalysts are suitable for synthesis with low H2 /CO ratio syngas such as derived from low-quality feedstock such as biomass.
During the Second World War, the process was extensively developed by Germany for domestic fuel production, but fell into abeyance after the war when oil became readily available again. It enjoyed a second wind under Sasol in South Africa during the 1970s when South Africa was under sanctions, and gained further momentum when Sasol developed the process to work from a natural gas feed. Gas to liquids (GTL) production did not require the pre-treatment and gasification sections required by coal to liquids (CTL) production, and seemed to offer the possibility of being able to arbitrage cheap natural gas and high oil prices, and led to the building of Sasol’s Mossel Bay plant in South Africa in the 1990s and Shell’s Middle Distillate Synthesis (SMDS) plant at Bintulu in Malaysia. But natural gas went through a period of being relatively more expensive compared to oil during the 1990s, and so the process did not see another wave of interest until the 2000s, when rising oil prices encouraged another look at alternative feedstocks. This period led to the building of the successful Pearl and Oryx GTL plants in Qatar, but similar projects in Nigeria and Trinidad suffered from long delays and cost overruns.
A major issue for GTL has also been one of opportunity cost – where a large source of natural gas has been available, LNG has often been a more profitable way of monetising it, and therefore the most recent wave of GTL projects has come from central Asian countries that are not able to export gas as GTL and which have occasionally had problems win developing export pipelines. The largest project has been Uzbekistan’s 38,000 bbl/d Oltin Yo’l (‘Golden Road’) GTL plant, though development took more than a decade, and covid delays meant that start-up did not occur until this year. Other routes to synthetic gasoline production are also available, and next door Turkmenistan built what it describes as a 15,500 bbl/d ‘GTL’ plant using methanol/DME production and downstream methanol to gasoline conversion using Topsoe’s TIGAS (Topsoe Improved Gasoline Synthesis) process instead.
Environmental concerns
Perhaps the largest looming issue for CTL and GTL production is the carbon footprint not only of production, but also of the finished product. For this reason, coal-based production is now essentially ruled out in the developed world unless carbon capture and storage is used, and GTL plants could only be considered in the context of stranded or flared natural gas. However, rising costs of oil and gas and falling costs of electrolysis could help tip the balance towards greener production. In this regard, a green Fischer-Tropsch synthetic diesel could offer advantages over molecules such as green ammonia or methanol – both now widely touted as future alternative fuels – in that a complete distribution and sales infrastructure already exists for it.
Municipal waste
One potential green, or perhaps ‘pseudogreen’ feedstock for green F-T production is municipal solid waste (MSW). The growing lack of landfill space in developed countries is becoming a pressing problem in spite of increased recycling rates. In 2017 China stopped accepting imports of waste from other countries, a particular concern to the US, which exported much unprocessed waste to China, and where landfills and incinerators are running at capacity. This has led to a number of projects to generate power from waste incineration, using the heat generated to drive combined cycle turbines to produce electricity or to heat water or steam for local district heating. However, the wide variety of waste that finds its way into MSW means that there are concerns about emissions, including dioxins and furans, sulphur dioxide and nitrous oxides, heavy metals such as mercury, and so there has been increasing interest in the use of gasification to deal with such waste, allowing for easier clean-up of waste streams, and the generation of power or production of chemicals via syngas.
So far the largest and most successful installation has been Enerkem’s waste to fuels plant in Edmonton Alberta. The plant takes 100,000 t/a of Edmonton’s MSW under a 25-year supply agreement, amounting to about 30% of the solid waste that the city generates. The plant mainly converts the syngas generated from gasification into 33,000 t/a of methanol and ethanol, though there has been a pilot side plant producing synthetic diesel via Fischer-Tropsch conversion. A similar plant is now under construction at Varennes, Quebec, with completion due in 2023. Enerkem is also pursuing even larger projects in Rotterdam in the Netherlands and Tarragona in Spain, both of which are awaiting a final investment decision.
BP and Davy Process Technology (now Johnson Matthey/JM) jointly developed a Fischer-Tropsch process for GTL production in the 1990s, building a 300 bbl/d demonstrator plant in Alaska in 2002, but were not able to overcome commercial hurdles to its deployment. However, they have improved the process using ‘cans’ of catalyst in a fixed bed reactor, and via BP-backed US start-up company Fulcrom Bioenergy, they have developed the Sierra Biofuels plant near Reno in Nevada, USA. The plant, which began operations in May 2022, will convert at capacity 175,000 t/a of MSW into 11 million gallons per year (37,000 t/a) of ‘sustainable aviation fuel’ (SAF). They claim the new process delivers three times the productivity of a conventional multi-tubular fixed bed reactor and halves capital expenditure when compared to traditional FT reactors.
“It is finding most traction in the aviation industry, which otherwise believes it will struggle to move to a lower carbon model.”
UK-based Velocys has also developed a Fischer-Tropsch process, first demonstrated at the Envia Energy plant in Oklahoma City, producing 200 bbl/d of synthetic fuel for a few months from MSW before technical issues with the gasifier forced the shutdown of the project. The company is now focusing on SAF projects using the process. The Altalto project at Immingham in northeast Britain will use MSW feedstock to produce up to 1,300 bbl/d of SAF. Planning permission has been granted, and financial closure for the project is currently “targeted for 2024”. In the US, it is also developing a project based on woody biomass gasification with carbon capture and storage (CCS). The Bayou Fuels project in Mississippi is aiming to produce 1,600 bbl/d of SAF as well as naphtha.
Biomass
Gasification of biomass waste is another potential source of ‘green’ Fischer-Tropsch diesel and forms the basis of a number of biomass to liquids (BTL) projects. In addition to the Bayou Fuels plant above, there is another biomass to fuels plant under development using Fischer-Tropsch technology; Red Rock Biofuels, based at Lakeview, Oregon, USA. When at capacity, the plant will produce 1,100 bbl/d of F-T liquids based on forestry and sawmill residues, using a process developed by Frontline BioEnergy and proven at a demonstrator plant in Nevada. However, like many such projects it has had a somewhat tortured path to operation. In spite of the receipt of an estimated $350 million of public funding, the plant is not quite complete, and construction is currently paused while Red Rock is said to be looking for a development partner to help it finish construction.
Gasification of alternative feedstocks has often foundered on the issue of gathering together sufficient material to run a large-scale plant with associated economies of scale. This has particularly bedevilled biomass gasification projects, except those using waste streams from forestry, pulp and paper production, where some of the gathering has already been done, and illustrates one of the advantages of using MSW, where collection at large scales has already been accomplished by the local municipal authority.
Biogas
Biogas is formed from the anaerobic digestion of waste biomass by natural bacteria, either directly recovered from landfill sites, generated from wastewater treatment, or made via deliberate processing of biomass in biodigester reactors. It is mostly methane, carbon dioxide and water, and needs to be dehydrated, with a number of other impurities which also need to be treated during purification. While there are a large number of biogas producing sites, most are small scale, and collecting it for use as a chemical feedstock has not so far been attempted on a commercial scale, though flowsheets for F-T fuel production have been developed. Biogas is usually fed into local natural gas networks instead, earning the producer carbon credits.
Green hydrogen
The explosion of interest in water electrolysis using renewable energy as a way of producing green hydrogen has led to a fourth potential feed for green F-T production, in what is sometimes called ‘Power to Liquids’ (PtL). As with the BTL and waste to fuels alternatives above, it is finding most traction in the aviation industry, which otherwise believes it will struggle to move to a lower carbon model going forward because of the difficulty of using proposed alternative vehicle fuels or battery power in an aircraft.
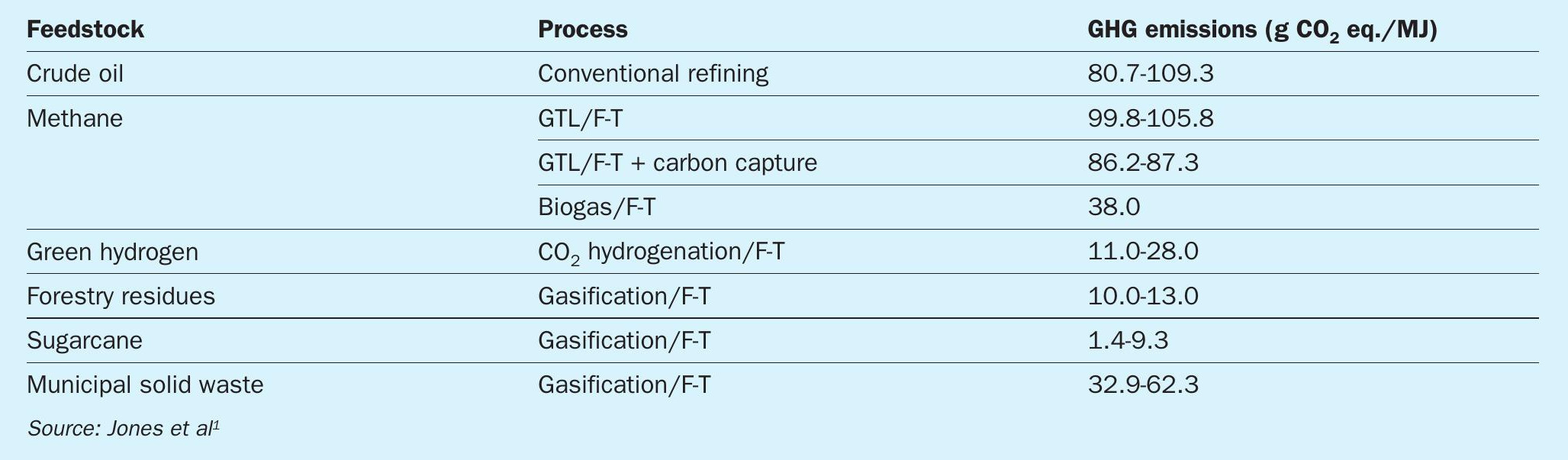
However, so far demonstrator units based on the technology have been at very small scales. In August 2019, the German government funded the Power-to-X (P2X) project within the Kopernikus initiative and produced kerosene via hydrogen from electrolysis and F-T synthesis, but at only 10 litres/day, though the P2X project plans to scale up capacity to 2,000 litres per day. In Norway, Norsk e-fuel aims to be Europe’s first large-scale commercial plant to produce SAF from renewable electricity, water and a combination of atmospheric CO2 and point sources at Herøya, Norway, with 12.5 million litres per year planned from 2024. The Green Fuels for Denmark consortium is attempting something similar in Denmark with a mix of green hydrogen and methanol alongside SAF. In the UAE, Masdar expects to have a PtL demonstrator plant operational by the end of 2022, and there are other initiatives, mainly in Europe.
As Table 1 shows, green hydrogen potentially offers a low carbon route to SAF, though in fact well to wheel emissions are not much lower than for MSW gasification and can be higher than BTL production. Cost issues also of course bedevil alternative fuel development, though in the current oil and gas price environment, hydrogen electrolysis can look very attractive for regions such as Europe.
A new lease of life?
At present, power to liquids schemes using Fischer-Tropsch conversion are still very much in their infancy, though they have benefited from the huge upsurge in interest in using renewable energy to produce chemicals that has occurred across the board. The application that is looking most favourable is in production of sustainable aviation fuels, where alternatives to kerosene and similar hydrocarbons are much fewer. But for the interim, gasification of municipal waste seems to be leading as a feedstock for its production, and PtL may require more research and development, lowered costs of production and more financial incentives from governments. Norsk e-fuel seems to be the project that is furthest forward towards production at a commercial scale, and it will be interesting to see how it develops over the next few years.
References