Nitrogen+Syngas 380 Nov-Dec 2022
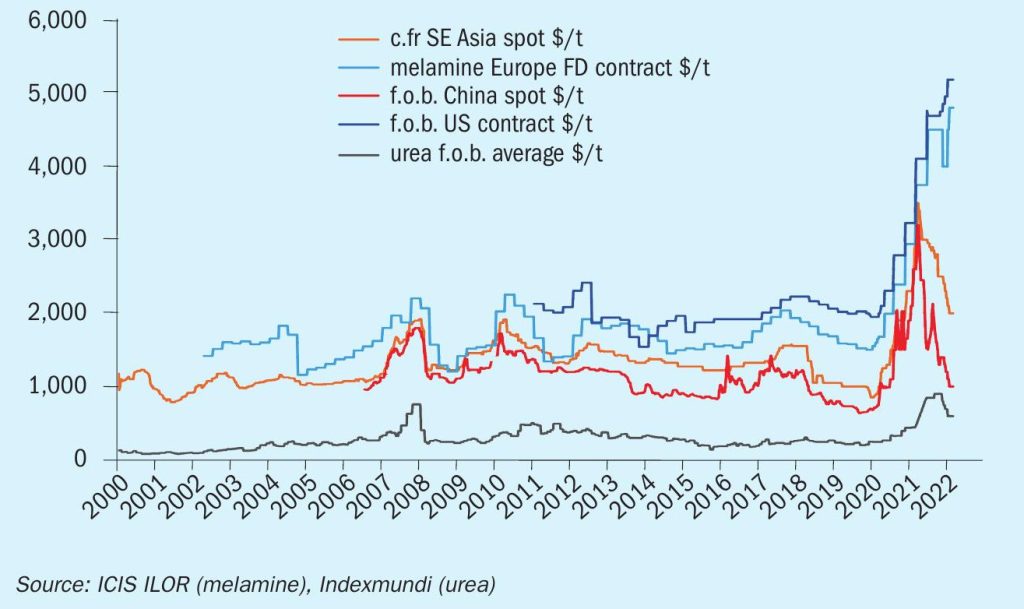
30 November 2022
Melamine integration in a fertilizer complex
PROCESS INTEGRATION
Melamine integration in a fertilizer complex
The latest improvements to melamine process technology now make it even easier to integrate a melamine plant with an ammonia and urea fertilizer complex. Guido Canti of Eurotecnica and Marc Wieschalla of thyssenkrupp Uhde discuss the benefits of plant integration.
The use of mineral fertilizer is an essential component of sustainable agriculture. Mineral fertilizers are applied in order to balance the gap between the nutrients required for optimal crop development and the nutrients supplied by the soil and available organic sources. One of the most widely used mineral fertilizers is urea, obtained from carbon dioxide and ammonia. Both reactants are brought together under high pressure where they form carbamate as an intermediate product and subsequently urea and water in the second step. Finally, urea is concentrated and solidified either by prilling or granulation.
Ammonia plants are typically designed to produce market grade ammonia, having at the same time a side stream of carbon dioxide. This latter stream is sometimes vented to the atmosphere or, more often, used as a feedstock for urea production. The amount of ammonia and carbon dioxide provided by an ammonia plant is not usually balanced for the stoichiometric production of urea. In most cases, ammonia is present in excess.
Additional sources of carbon dioxide are present in most ammonia/urea plants, namely, the reformer flue gases and boiler flue gases. Using the excess ammonia together with the additional carbon dioxide source allows the urea plant capacity to be increased by 10 to 15%. This capacity increase can be executed by modifying the synthesis loop either by adapting the existing equipment or adding a section, depending on the technology of the plant and its size or age. Should a urea capacity increase be required, concepts like debottlenecking without licensor involvement, “more in – more out” or the MP add-on based on Stamicarbon technology are suitable to comply with end-user desires. Capacity increases above 10% to even 100% can be achieved. However, in this case the ammonia plant requires revamping as well in order to provide higher amounts of ammonia. If the higher demand of steam needs to be mitigated, older Stamicarbon plants can be equipped with an MP flash using the low energy technology of Stamicarbon which reduces the steam consumption of the urea melt process. In the event that a different licensor technology is applied in the existing urea melt plant, different concepts are available that can be used to reduce energy consumption.
As the demand for urea grows by 2-3% per year and thus at a slower pace than the capacity increase achievable from plant debottlenecking, it can be useful to consider the production of alternative products to solidified urea fertilizer, such as Ad Blue® (diesel exhaust pollution control) or melamine. While the modifications to an existing urea melt plant are relatively simple the same upgrade on the finishing section (either prilling or granulation) can prove difficult: a prilling tower cannot be modified and a granulation section is rather limited in terms of acceptable flow-rates. However, granulation plants are usually designed with additional margin for recovery after washing e.g. up to 10%. With a capacity increase of the urea melt plant the recovery capability reduces.
Melamine, a direct derivative of urea melt, can be considered for debottlenecking, ensuring the complete utilisation of any excess ammonia/carbon dioxide and producing a valuable compound.
To produce melamine, urea molecules are joined under pressure in an endothermic non-catalytic reaction that generates melamine, ammonia and carbon dioxide. These off-gases are sent back to the urea plant to be recovered as fresh urea. Fig. 1 shows a simplified block diagram of the two plants.
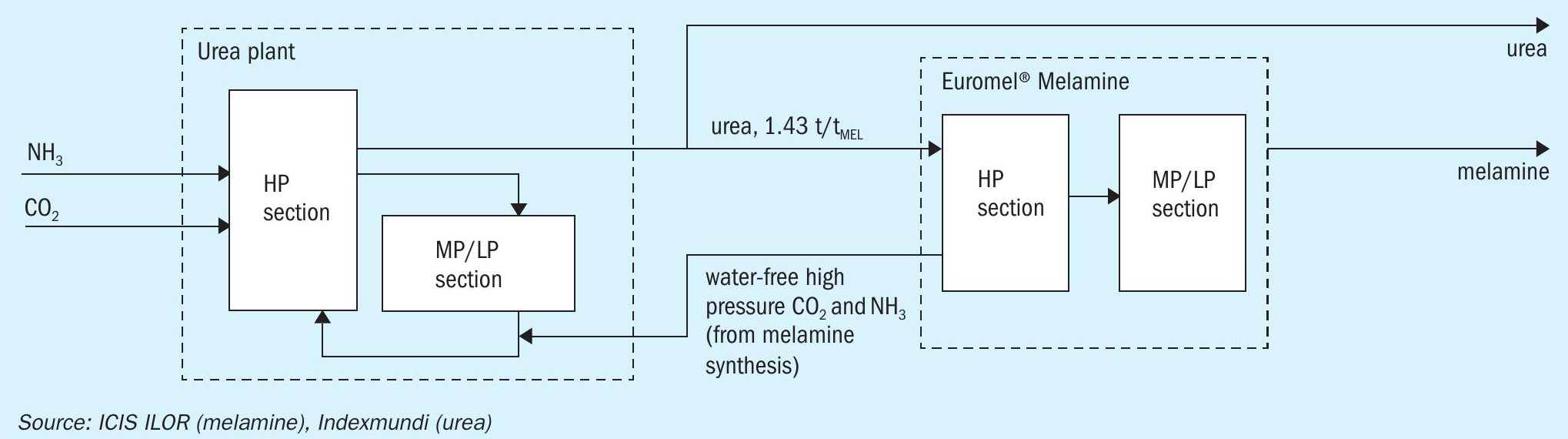
A second feed stream of ammonia ensures the complete transformation of urea to melamine and guarantees that no by-products are formed. All ammonia is fully recovered in the urea plant, with no modification of the ammonia balance of the complex.
Leading melamine licensor Eurotecnica SpA has recently marketed its fifth generation (G5) technology which improves the process by minimising the energy consumption and ensuring its long-standing no solid, no liquid effluent policy, thus ensuring, as per previous generations, a total zero-pollution plant.
One of the main features of this technology is its ability to simplify the integration of the melamine plant with its urea counterpart by means of a single liquid carbamate tie-in.
An existing urea plant can be safely and smoothly modified for the connection to a melamine plant; at the same time an increase in capacity can be achieved by using, for example, the existing excess ammonia.
This results in several positive effects on the urea plant such as:
- higher ammonia plant utilisation;
- no need to revamp the prilling or granulation section;
- guarantees on urea quality unaffected;
- no loss of ammonia and carbon dioxide, they are fully recovered in the urea plant;
- easy integration with the existing facilities;
- no changes to the water balance (scrubbing water for the melamine plant is taken from the waste-water system of the urea plant).
The same advantages can be obtained for a new urea plant under design or an existing facility to be revamped.
For both new and existing urea plants the modifications required to link the melamine and urea plant can be easily implemented and are briefly described in Table 1.
As the carbon dioxide captured in melamine production is stored in this compound for the long term, melamine production can also be regarded as a means to mitigate climate change. Melamine production, in itself, has a negative carbon footprint and its economic exploitation benefits the complex end-user without any impact on the environment in terms of greenhouse gases release.
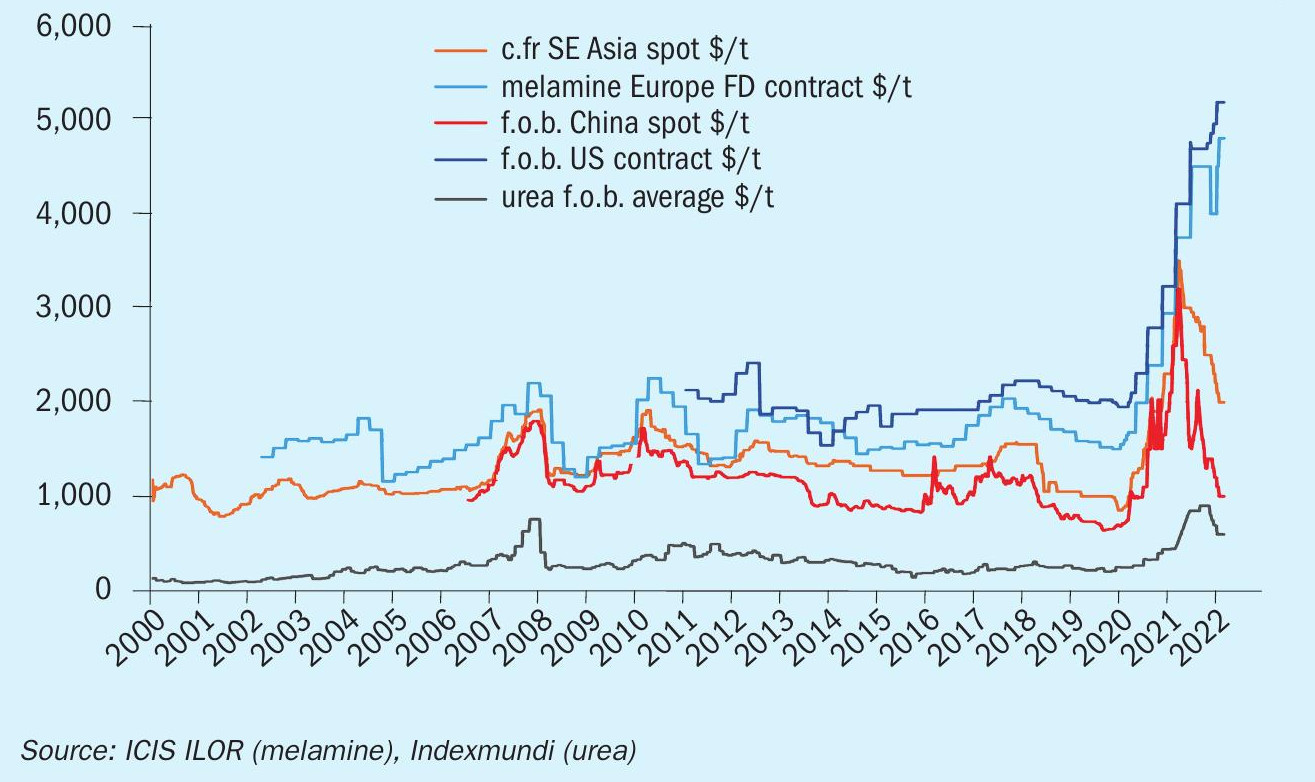
Melamine is also a high value product. This is reflected in the price, which was between $2,600 to $3,000 per tonne in 2021. Urea has been traded around $220/t for a long time and has reached peaks of $1,200/t in the recent past (see Fig. 2).
Because both urea and melamine tend to crystallise easily, an EP/C contractor, experienced in urea technologies, can transfer its knowledge to the melamine process, contributing to a well-working melamine plant. thyssenkrupp Industrial Solutions AG’s Business Unit Uhde (Uhde) has more than 60 years of experience building and revamping various urea melt and granulation plants and consequently is one of the most suitable EP/C contractors also when it comes to melamine plant erection. During its long-term involvement in urea, Uhde has developed its own solutions and advanced technologies within licensor designs. For example, Uhde has developed an emission-free vent stack within the urea melt plant, the application of self-regulating pumps, which cannot cavitate and are used for the melt delivery from the melt plant to the granulator, and melt flushing in the evaporation unit of the melt plant in order to dissolve any biuret deposits efficiently. All three examples contribute to reduced emissions and a higher availability of the plant. In addition, Uhde can provide information on the flushing of process lines and advice on tracing and insulation, which can be applied to boost plant performance, increase plant availability, reduce emissions, ensure plant safety or simply provide trouble-free operation of the plant. Uhde know-how can make a difference when it comes to plant safety, reliability and efficiency.
Combining this know-how with the latest generation of melamine technology provided by Eurotecnica SpA can help to protect the environment while providing a fast payback time for the end user
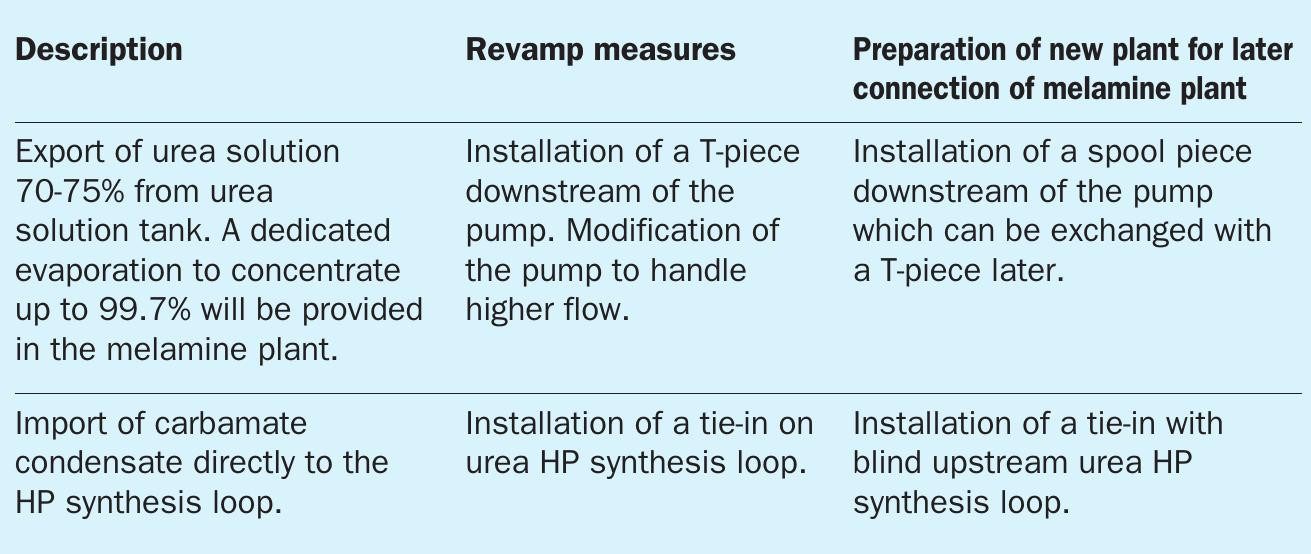