Sulphur 403 Nov-Dec 2022
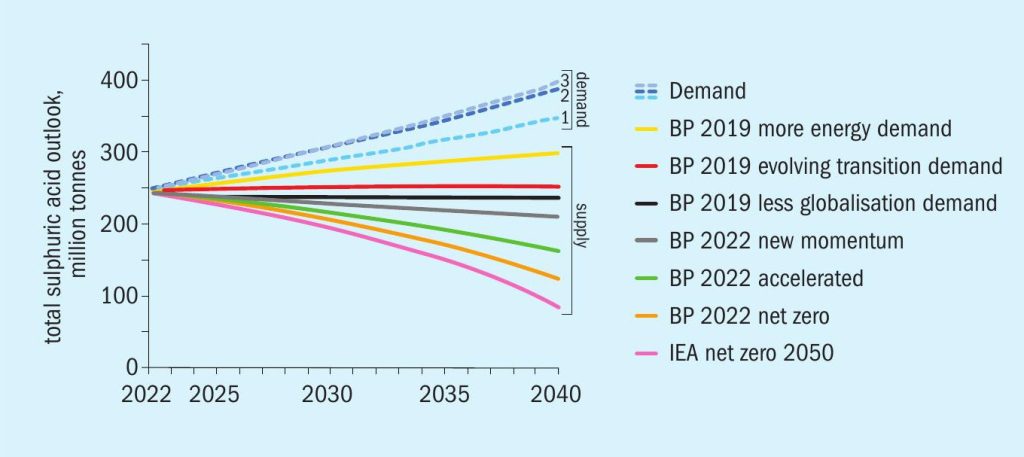
30 November 2022
Road to sustainability
SULPHURIC ACID INDUSTRY
Road to sustainability
The energy transition has already commenced and while sulphuric acid production is already virtually carbon free, there will likely still be impacts on the sulphuric acid industry resulting from this energy transformation. Hannes Storch, Shailesh Chandrol, Collin Bartlett and Jens Kleiber of Metso Outotec present their view on a roadmap to sustainability, preparing for energy transition in the sulphuric acid industry through permanent product development, digitalisation and new technologies.
The reality of climate change and the consequences of it are becoming visible; the average temperature of the globe is rising; ever more unprecedented weather events can be observed. In Fig. 1 the effect of greenhouse gas (GHG) emissions on global warming is illustrated for different scenarios1 . Even early action to the GHG issue will result in an optimistic view to a warming limit of 1.5°C and delayed actions predict dramatic increases in temperature.
At the moment the focus of greenhouse gas reduction certainly lies in building up a renewable infrastructure and pushing forward the decarbonisation of energy intensive industries, such as cement, steel and aluminium. It has to be acknowledged however that all commodities will be impacted by this energy transition and need to develop their own commercial and technical roadmap for the coming decades if the warming limit of 1.5°C is to be achieved.
The focus of this article is a holistic review of the sulphuric acid industry from a technology provider’s view and also highlights areas where Metso Outotec considers further development is required.
Energy transition
The key element to fight the climate change is an energy transition from hydrocarbon dominated to renewable energy sources. On this subject there are numerous studies and scenarios available which all include the same elements, however the timeline to achieve a “Net-Zero scenario” differs significantly.
One example, detailed in a recent report2 entitled “The Net-Zero Transition”, McKinsey & Company is detailed here. This article offered the scenario of primary energy production by 2050 based on Network for Greening the Financial System (NFGS) – refer to Fig. 2.
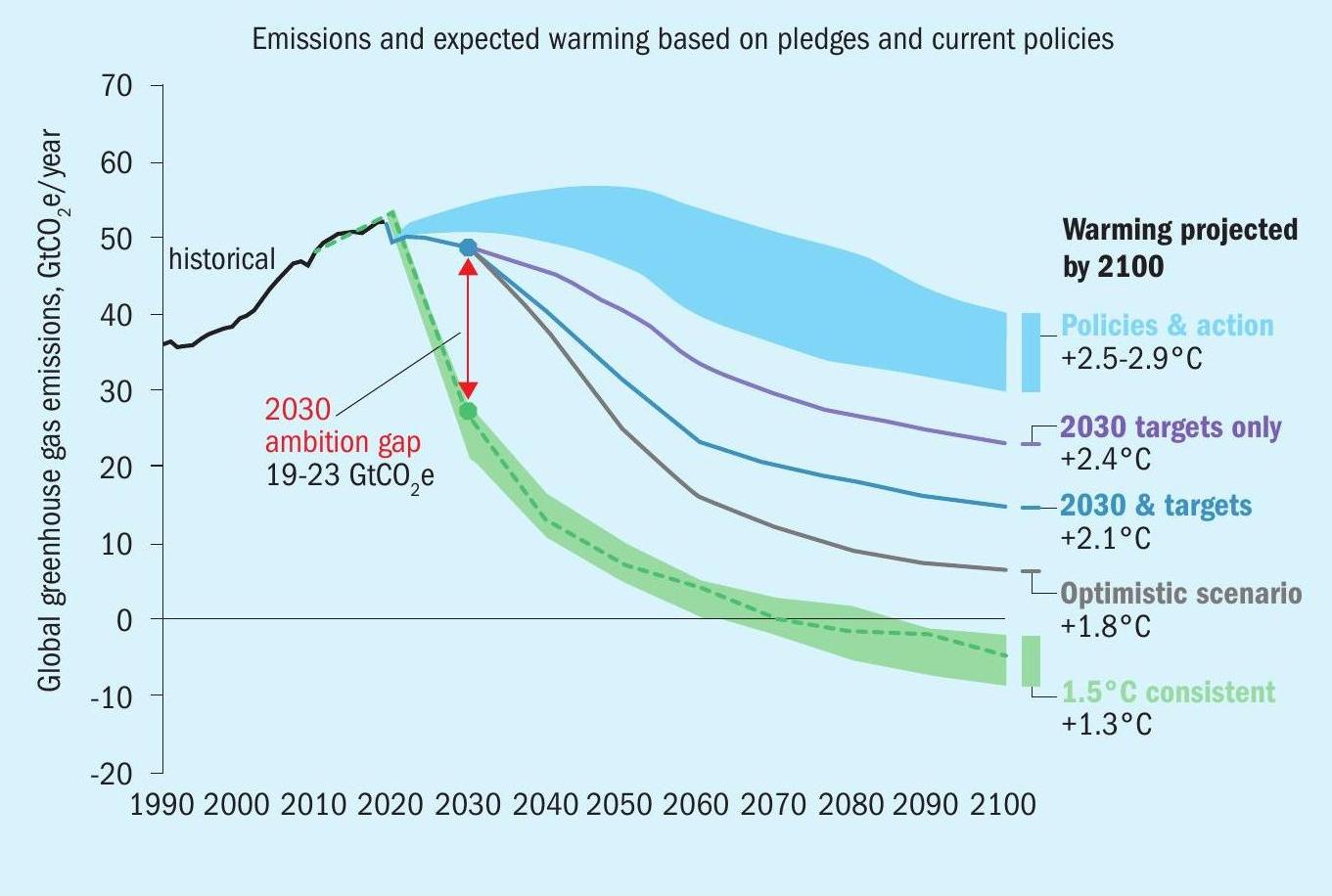
Fig. 2 shows a significant reduction firstly in the use of coal, followed by oil and gas in a relatively short period of time. In different regions and commodity industries it can already be observed that the process has already commenced.
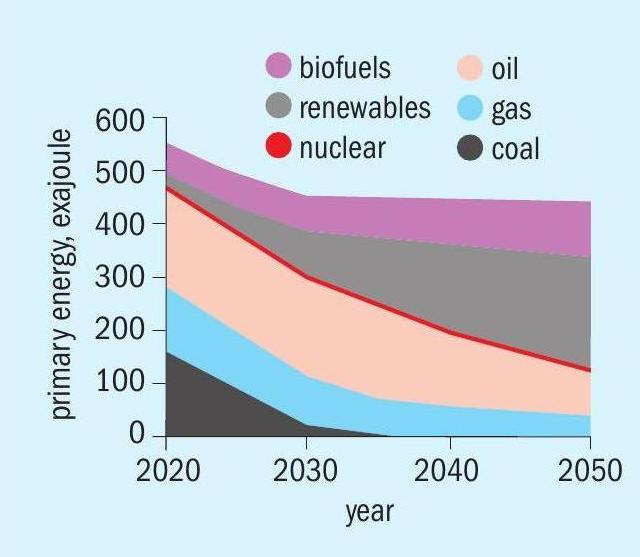
Implications of energy transition on the sulphuric acid industry
Although sulphuric acid production is already virtually carbon free, the energy transition may well have potential impacts on the industry:
- long-term global sulphur supply/ demand and availability dynamics from a reduced use of hydrocarbons;
- short- and mid-term requirement for more sustainable solutions to further increase operational KPI’s, i.e., kWh/t acid, m³ cooling water/t acid, etc.;
- regional/local requirements to shift to an alternative sulphur source, i.e. pyrite, natural sulphur, phospho-gypsum to bridge upcoming supply/demand shortfall.
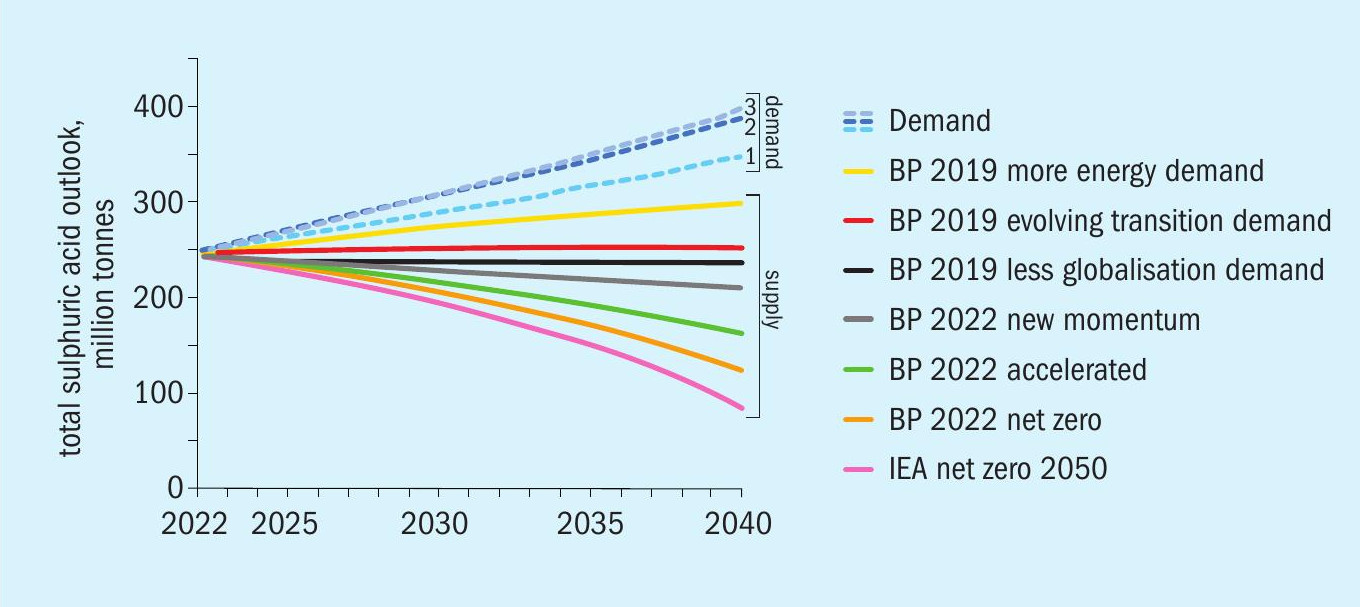
A recent report3 by Maslin et al. (2022) summarises the supply/demand gap for different scenarios on intensity of the energy transition. It indicates that “Sulphuric acid demand is set to soar just as sources are likely to shrink” and this is encapsulated in Fig. 3.
Road to sustainability in the sulphuric acid industry
Metso Outotec’s view, as a technology provider to the acid industry, is that energy transition and its transformational facets requires a roadmap today and this “road to sustainability” should consist of three areas to address and provide technologies and solutions to the industry at large:
- permanent product development;
- digitalisation;
- new technologies.
Permanent product development
Permanent product development is an ongoing process that focuses on improvement of safety, reliability and efficiency KPIs of acid plant technology and its products. Numerous products have been developed to address those key areas. However, the transition phase of energy transition requires further focus/re-thinking of specific operational key performance indicators (KPIs). Redefined KPIs in order to minimise specific energy consumption will support the use of equipment/technical solutions that are today not always considered as standard in the sulphuric acid industry, for example:
- Use of energy efficient equipment
– filter, packing
– VSD for blower, process pumps, etc.
– more conservatively designed process equipment
- Significantly more attention to maintenance
– Preventive maintenance supported by digitalisation
– Managing pressure drop increases during operation
– More catalyst screening, etc.
- Stronger focus on opex-based cost benefit analysis (CBA) over the plant’s lifecycle rather than front end capex optimisation.
Fig. 4 shows one example relating to cost development over pressure drop. Historically, optimisation of plant pressure drop took place considering stable low level energy pricing; due to increased energy prices and carbon taxation this will potentially change in future. In case-by-case analysis it should be evaluated if higher initial capex for lower energy consuming plants offsets the anticipated opex over the lifecycle of the plant.
Digitalisation – the next leap in efficiency
One key element to support the optimised operation of acid plants will be digitalisation. There are numerous applications supporting all phases of the plant life cycle. A few prominent examples of applications that have already been established in the wider sulphuric acid industry are:
- connectivity, data storage and transfer (big data);
- optimising the process with data analytics;
- remote expert support;
- digital twins;
- predictive/interactive maintenance;
- future use of digi-connected tools, i.e. 3D spares printing, etc.
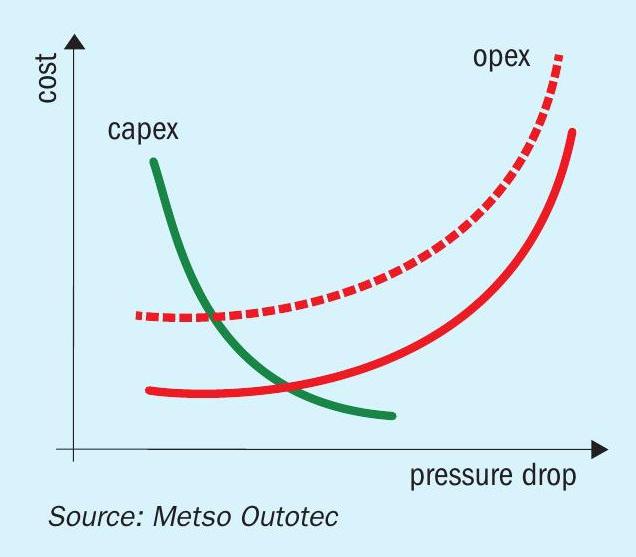
Metso Outotec has significant experience in the development and application of operating process optimisers and has a palette of references associated with a wide variety of industries. Such solutions are expected to have a place in the acid operators’ toolkit in future – refer to Fig. 5.
Today, many of these digital solutions can be considered as stand-alone, however in the future they will need to become an integral part of an integrated digital solution, encompassing the concept of the ‘mine-to-ship’ philosophy.
New technologies
Besides the elements of permanent process development and digitalisation, a review of different traditional and future feedstock is required. Table 1 shows some of Metso Outotec’s historical and current technology portfolio. Table 2 shows some of Metso Outotec’s ideas on future technologies to respond to the disruptive scenarios of energy transition.
For traditional feedstock materials, the overall maturity level can be considered as high, and the focus of developments remains more on permanent improvement in respect to energy efficiency, emission and impurity control. In the case of pyrite as feed material, developments to significantly increase throughput via new designs in combination with the use of oxygen have to be considered as relevant.
Potential alternative feedstocks, namely phosphogypsum, would require significant efforts in their development. Fig. 6 shows a simplified block diagram of one potential process to use phosphogypsum. In this process hydrogen and renewable energies (such as solar) are used to decompose the phosphogypsum and the SO2 gases are cleaned from impurities and processed in a sulphuric acid plant. The solid product of the process (CaO) is used in a separate process step for the production of CaCO3 , which can be used in different industries. The key characteristics of the process are:
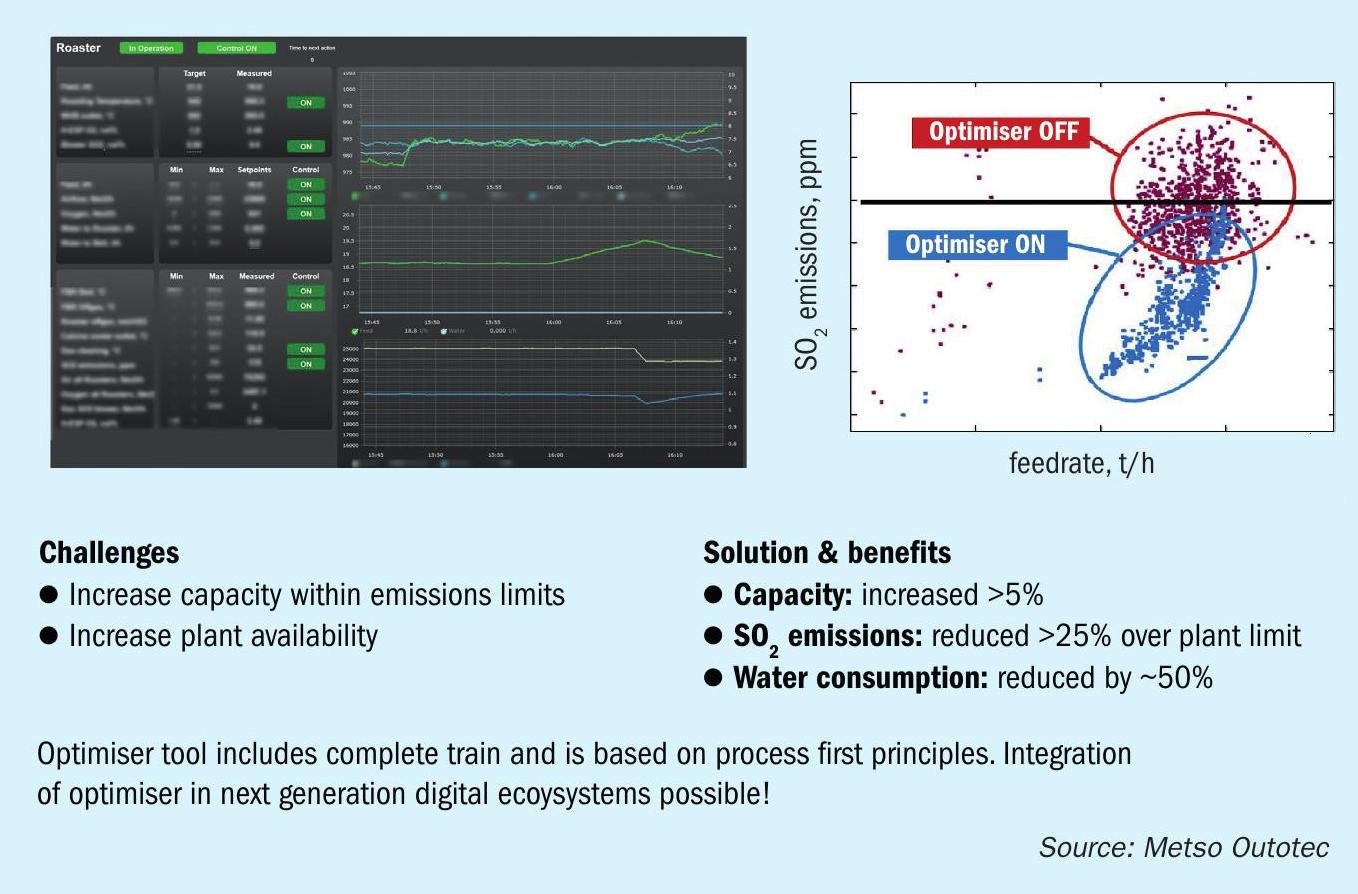
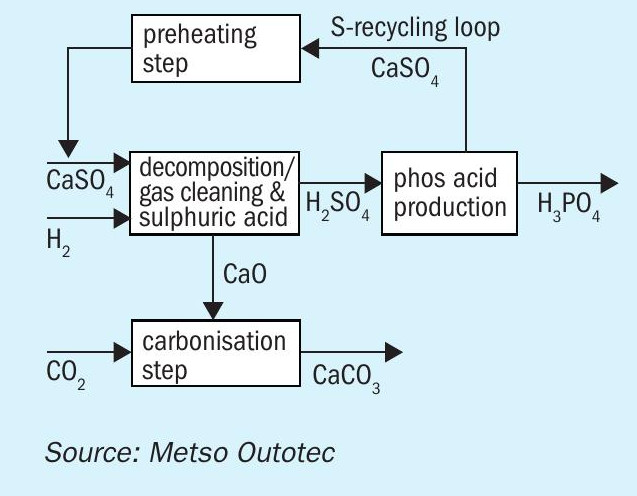
- use of hydrogen and renewable energy sources;
- development of a (local) circular sulphur economy by reusing phosphogypsum;
- carbon dioxide fixation;
- stabilisation of impurities;
- adaptation of existing technologies/ process steps.
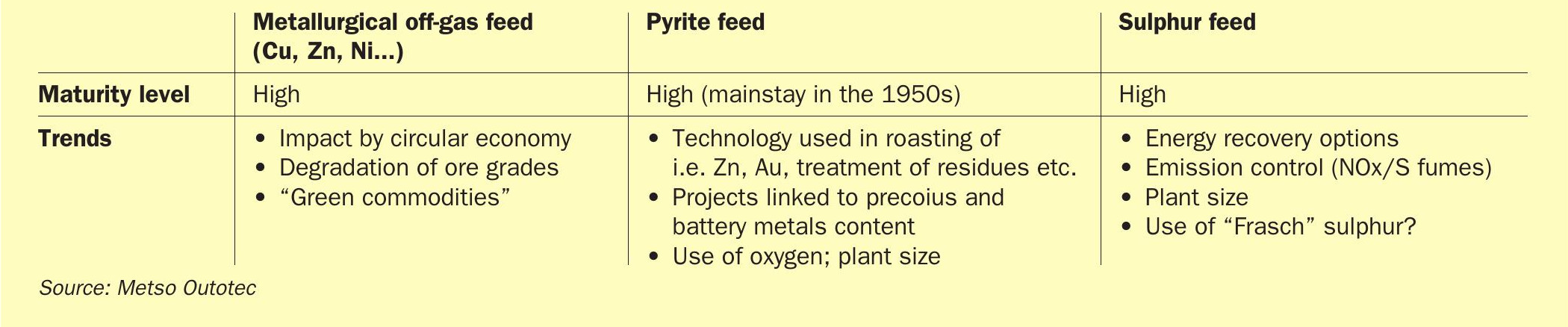
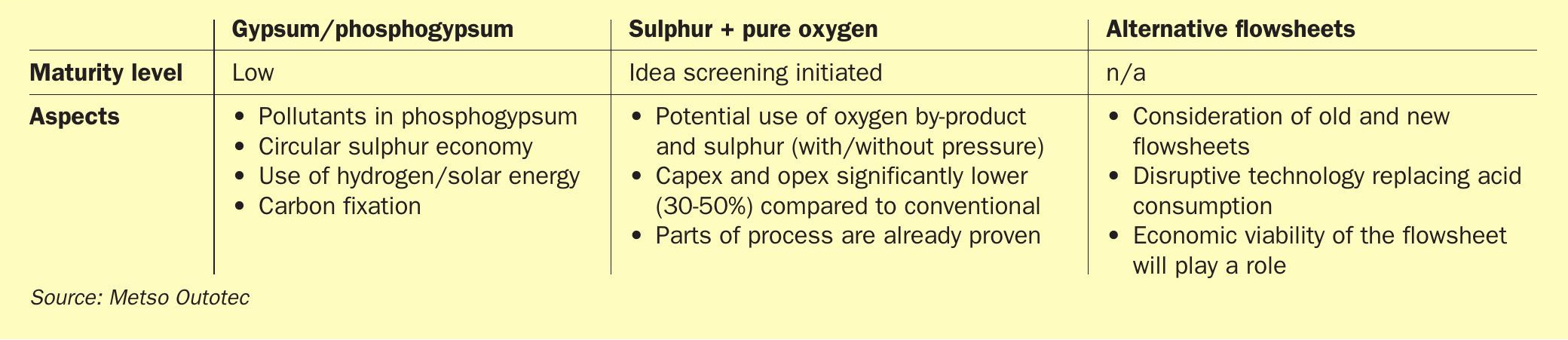
Other new concepts, such as the use of pure oxygen for the combustion of sulphur or processing metallurgical ores are already in use in industry and might see more relevance in the future and particularly once oxygen as a by-product from hydrogen production becomes more economic.
It is fully acknowledged that for all potential new process routes the maturity level has to be considered low and collaborative development initiatives between producer and technology provider will be required.
References