Sulphur 403 Nov-Dec 2022
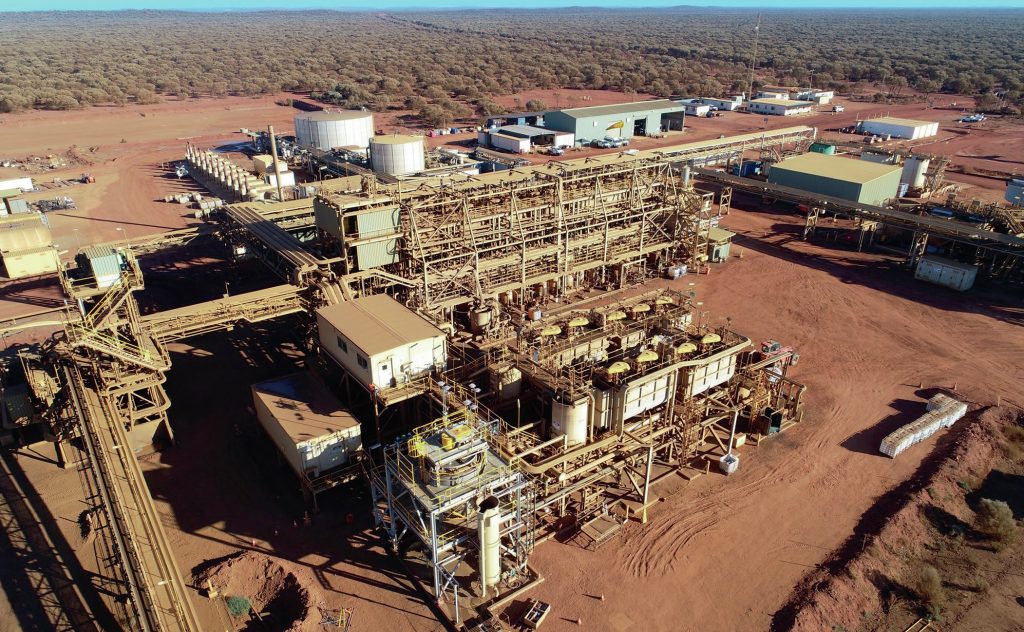
30 November 2022
Sulphuric acid in rare earths processing
RARE EARTHS
Sulphuric acid in rare earths processing
Global demand for rare earth metals is increasing, particularly for electric vehicle batteries and renewable energy devices, potentially leading to increased use of sulphuric acid in their extraction.
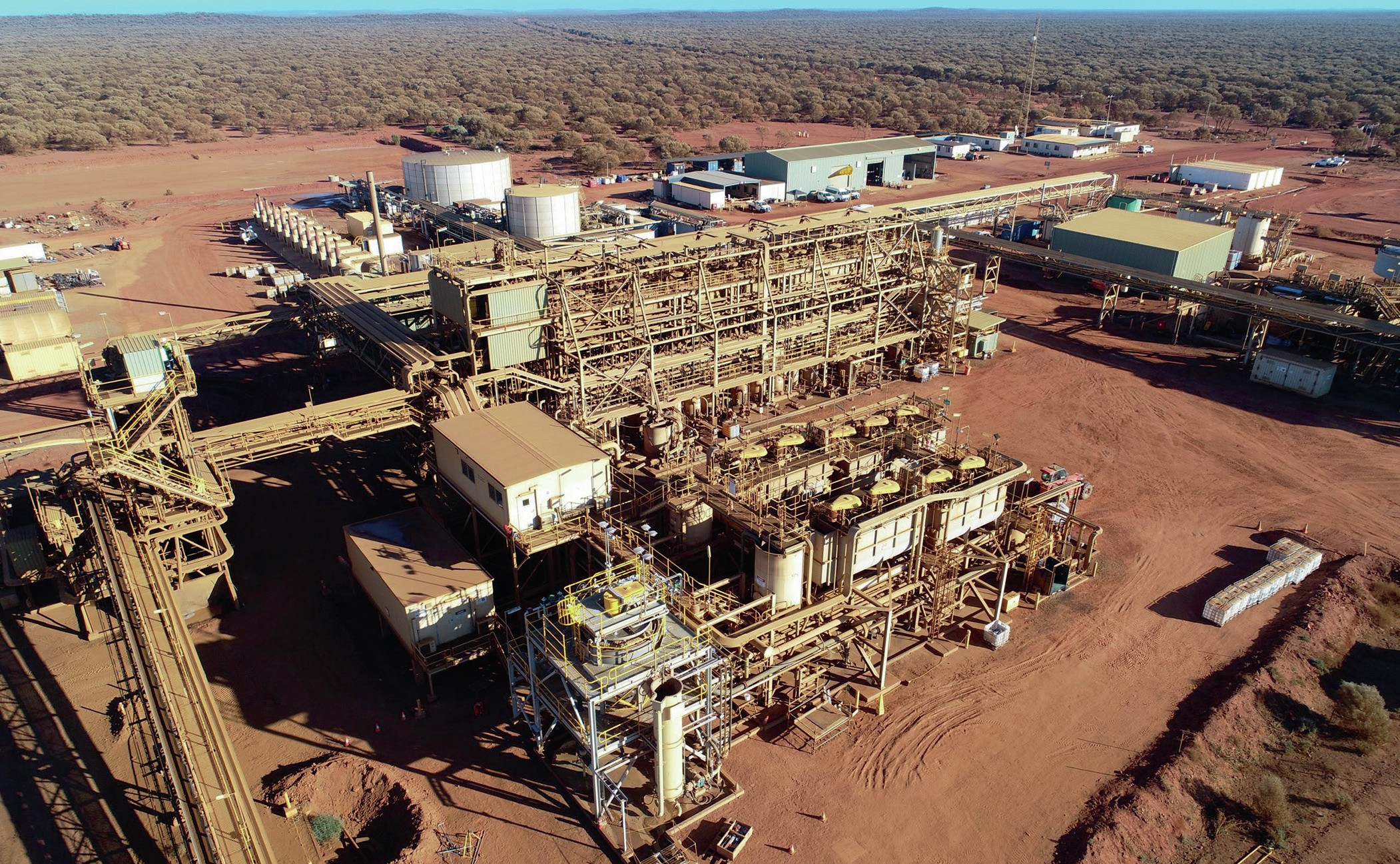
The ‘rare earth’ elements are generally considered to be the 14 lanthanide metals (see Figure 1), as well as yttrium, element 39, which sits directly above lanthanum in the periodic table. Scandium, which sits above yttrium, is also sometimes considered a rare earth element. They were first discovered in rocks found at an old quarry at Ytterby near Stockholm in Sweden in 1787 by chemist Carl Arrhenius, which is why the otherwise unremarkable village gave its name to four of the initially seven new elements found there – yttrium, erbium, terbium and ytterbium. In spite of their name, they are not necessarily particularly rare in terms of abundance in nature; there is actually more cerium, for example, in the earth’s crust than there is copper. However, they are not found as often in large deposits like transition metals such as cobalt and copper, which makes them harder to extract economically. The most common are yttrium, lanthanum, cerium and neodymium.
Their properties are varied, as shown in Table 1. Cerium, lanthanum and neodymium are important in alloy making, and in the production of fuel cells and nickel-metal hydride batteries. Ce, Ga and Nd are important in electronics and are used in the production of LCD and plasma screens, fiberoptics, lasers, and medical devices. Cerium and lanthanum are also important as catalysts, especially for fluid catalytic cracking (FCC). Neodymium is important in magnet production and it and similar metals are used in the electric motors of hybrid and electric vehicles, generators in wind turbines, hard disc drives, portable electronics, microphones and speakers. Overall, rare earth demand is expected to rise by about 10% year on year over the next decade, more than doubling from its present value by 2030.
Production
Rare earth metals occur in various minerals, but the most prominent are bastnasite, a fluorocarbonate ore with iron found Inner Mongolia; monazite and xenotime, both of which are phosphates, found in Mountain Pass, California, and Kerala, India; ion-adsorption clays formed by the weathering of rare earth rich volcanic rock; and minerals such as euxenite and gadolinite. However, over 95% of rare earths occur in the three ores bastnasite, monazite, and xenotime.
Processing of rare earth ores can be done by various means 3 , usually proceeding via beneficiation, decomposition of the mineral concentrate to extract the rare earth elements, and then impurity removal and separation of individual rare earths to produce purified saleable products. Bastnasite can be treated using a variety of decomposition methods. Mountain Pass uses a hydrochloric acid leach because it delivers a purer product, but the most widely used technique is sulphuric acid ‘baking’, which is used at Bayan Obo in China’s Mongolia region – the largest rare earth deposit in the world – and at Mt. Weld in Australia. Sulphuric acid baking in Mongolia was estimated to be responsible for more than 60% of China’s total rare earth production in 2015. The process converts rare earth salts to sulphates by reaction with concentrated sulphuric acid at elevated temperature (200-300°C) in a ratio of approximately 1-2.5:1 acid:ore. The sulphates are then dissolved in a water leaching step before separation.
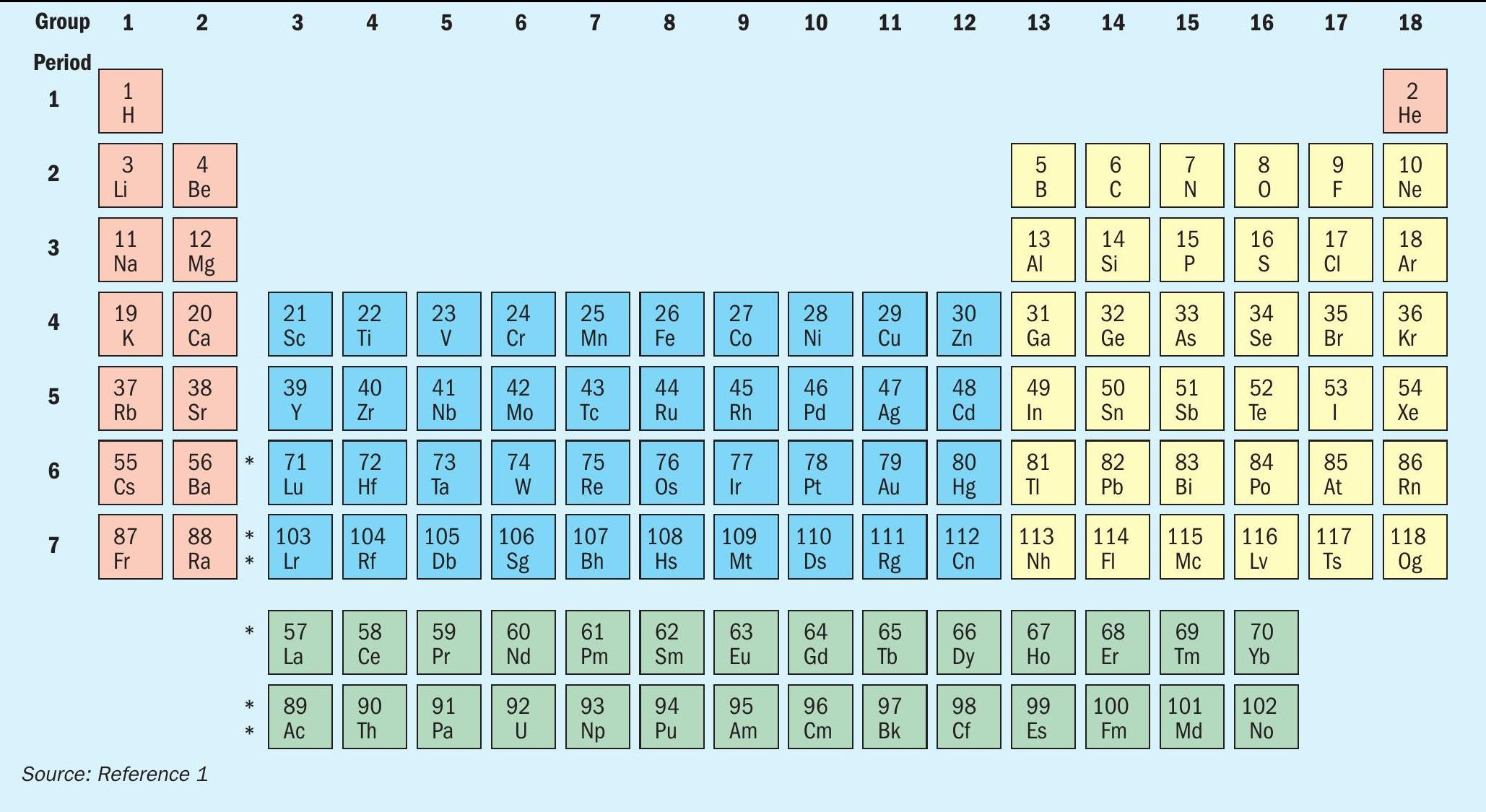
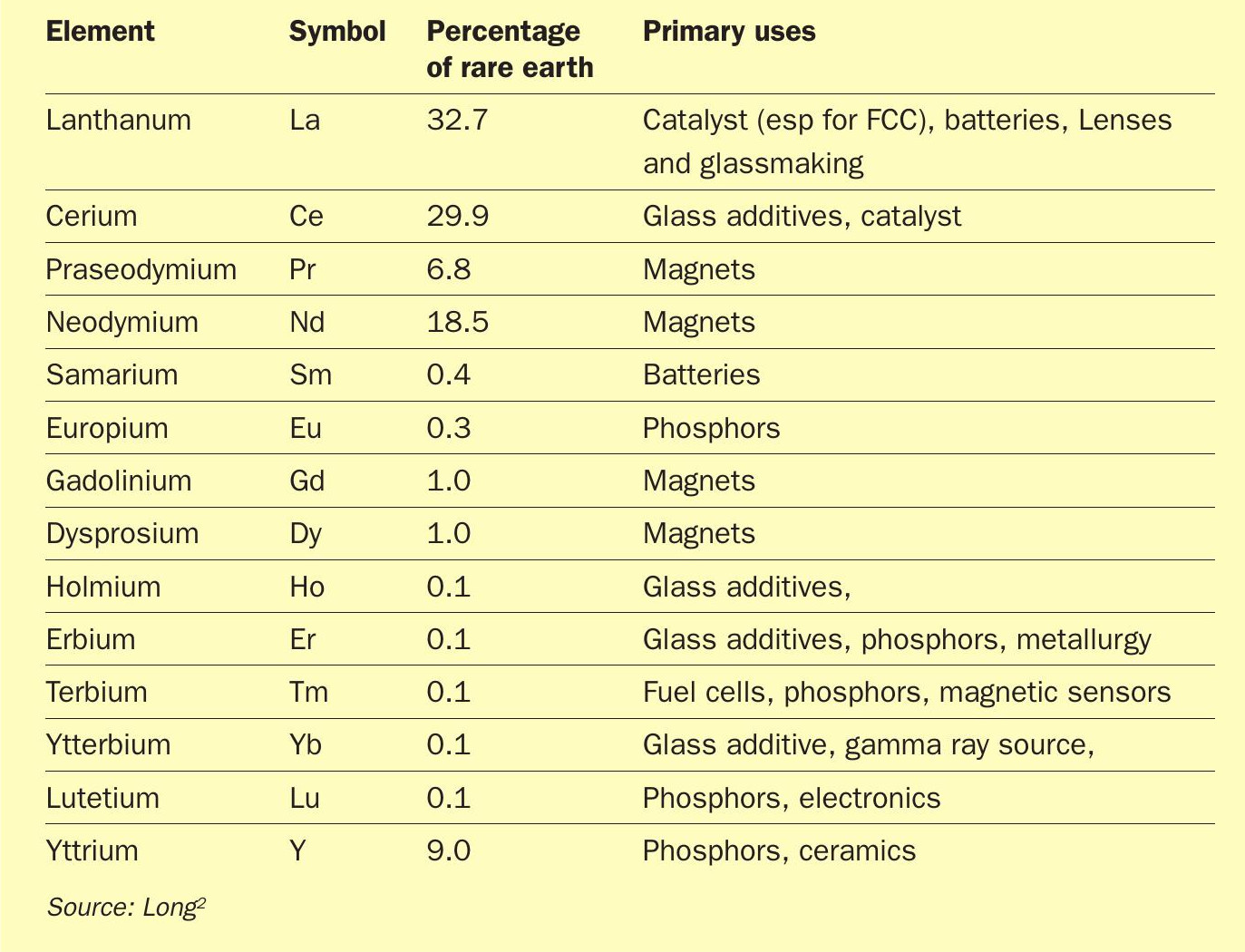
Monazite ore has in the past usually recovered using sulphuric acid, but the caustic route using sodium hydroxide has become preferred. The residue is then dissolved into hot acidic solution, either nitric or sulphuric acid, with subsequent solvent extraction using amines on the solution. Xenotime, effectively the yttrium version of monazite, is also almost always processed using a sulphuric acid bake.
Other extraction techniques
Phosphogypsum, a by-product of phosphate fertilizer production, mainly contains gypsum (CaSO 4 ) as well as impurities from the phosphate rock such as silicon, barium, iron, aluminium, titanium and uranium, but it also can contain small amounts (0.03-0.1% w/w) of rare earth elements. It has been estimated that the deposition of phosphogypsum stacks in Florida alone could incorporate up to 30,000 t/a of rare earth metals. Because of the low concentrations of rare earths, processing could be difficult and expensive. Nevertheless, methods have been proposed, including physical methods such as hydrodynamic sedimentation, flotation and high gradient magnetic separation, and use of various organic chemicals. But the most economically viable appears to be acid leaching. Though HCl and nitric acid have been shown in laboratory tests to be slightly more efficient at leaching rare earths, sulphuric acid would be preferred commercially because it is cheaper. Rainbow Rare Earths has a gypsum leaching project under development at Phalaborwa in South Africa, with first production anticipated in 2025.
It is also possible to recover rare earths from magnets or other devices containing them, though this can be costly to gather sufficient materials and large scale recycling is still in its infancy.
Supply
Until the 1950s rare earths were mainly extracted from alluvial deposits in Brazil and India, but the Mountain Pass mine in California, which began production in 1952, quickly came to be the dominant source throughout the 1960s-1980s. But beginning in the 1980s, China began mining rare earths on a large scale, and by the 1990s it had become the largest global producer. By 2000 China produced more than 90% of the world’s rare earth supply, and by 2010 that had become 97%. However, in 2010 China began to introduce export quotas in order (according to the government) to conserve resources and protect the environment. In 2012 three of the eight mines in China, representing 40% of supply, were closed down. This led to a spike in rare earth prices which galvanised the development of new mines elsewhere, in the US and Australia. As Table 2 shows, Chinese share of rare earth production now runs at 60% of world supply, though China also owns the rare earth mines in Myanmar and has invested in other production in southeast Asia. China’s production is concentrated in the provinces of Fujian, Guangdong, Hunan, Jiangxi, Shandong, Sichuan, Yunnan, Guangxi and Mongolia. The largest mining operation is Baotou Rare Earth’s Bayan Obo mine, which produces iron ore as well as bastnaesite and monazite as the main rare-earth minerals.
In Australia, Lynas Rare Earths Ltd began production at its Mount Weld carbonatite complex in Western Australia in 2011, and production has now reached 22,000 t/a, with a processing site in Malaysia. India has two small scale state producers, Indian Rare Earths Ltd. and Kerala Minerals and Metals Ltd. (KMML). The US reopened the Mountain Pass mine in California in 2012, operated by MolyCorp, but a glut of rare earths on the market led to production being idled there again in 2015. The mine was bought by MP Materials and production restarted again in 2017.
In addition to these, there have been a flurry of new project proposals, encouraged by the desire of countries such as the US and Europe to gain a degree of strategic autonomy in rare earths production, and be less dependent on Chinese supply. The Biden administration in the US has pushed domestic development of rare earths capacity. As a result there are new projects proposed in Australia, including Nolans Bore in the Northern Territory, Australian Strategic Materials at Dubbo in New South Wales, both of which are at the advanced feasibility study stage. Iluka Resources is developing a project in Western Australia at Eneabba, with a projected on-stream date of 2025. New project proposals in the US include Bokan Mountain, Alaska; La Paz, Arizona; Diamond Creek and Lemhi Pass in Idaho; Pea Ridge, Missouri; Elk Creek, Nebraska; Thor, Nevada; Round Top, Texas; Energy Fuels in Utah and Bear Lodge, Wyoming. There are also projects in Canada including Ashram, Buckton, Clay-Howells, Elliot Ridge and several others. Other project proposals include Greenland, Tanzania, South Africa, Madagascar, Kenya and Sweden.
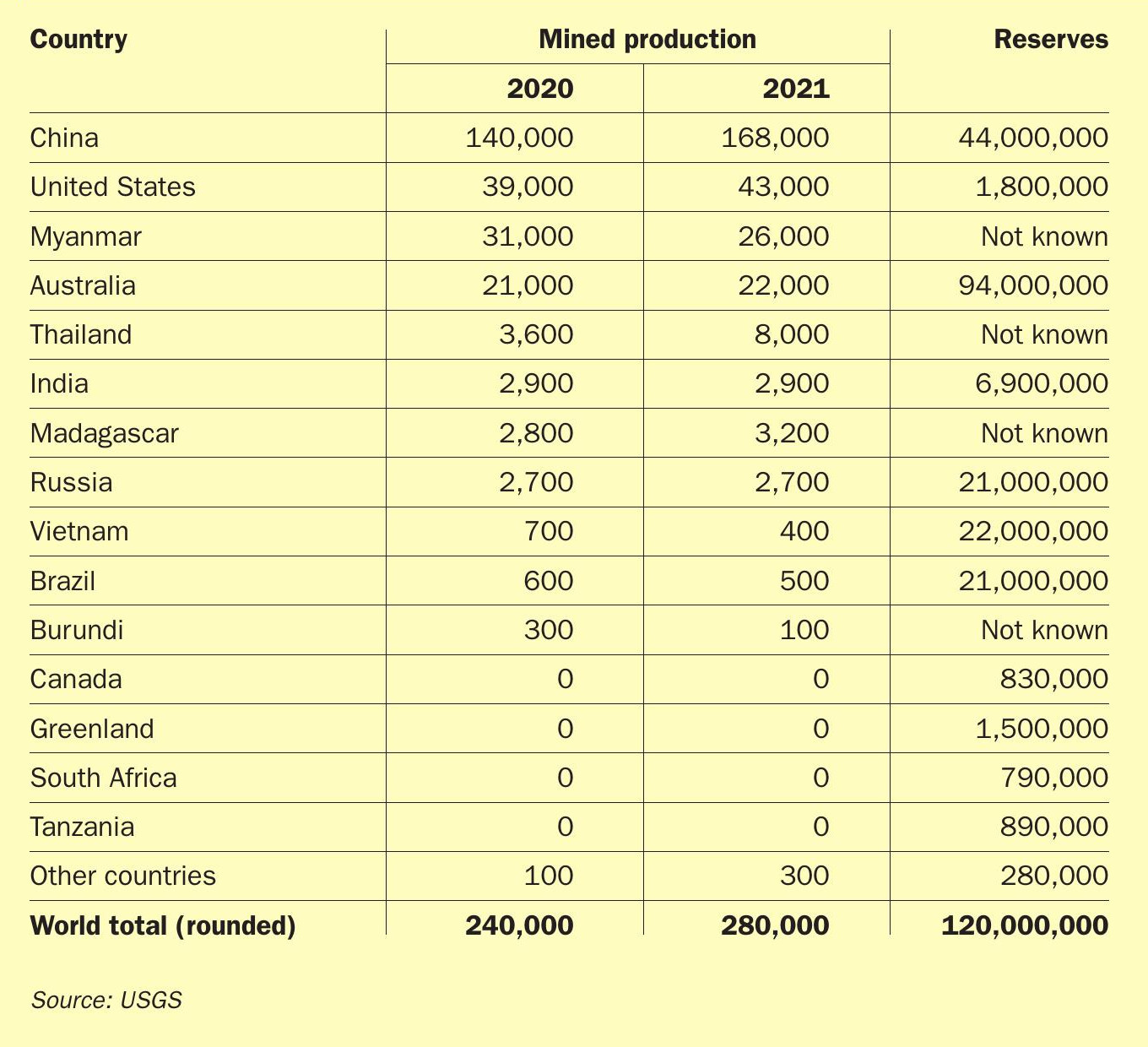
Acid consumption
Not all of these projects will come to fruition, and not all will use acid leaching, but given the small quantity of rare earth per tonne of ore, a great deal of rock must be processed in order to extract the 170,000 t/a of rare earths that are currently used, requiring perhaps 5-10 times the final amount of metal as acid. Downstream processing of rare earth concentrates is still by and large located in China and southeast Asia at present. Mountain Pass actually exports concentrate to China for processing.
Supply of acid can be crucial to the success of these projects. For example, Lynas Rare Earths is under pressure to close down its Malaysian processing site because of concerns about low level radioactive thorium residues from the leaching process, and is instead building a processing site in Kalgoorlie, Australia to handle ore from Mt Weld, which is due to become operational by 2025. The company is said to have reached a deal with BHP for supply of sulphuric acid from its nickel smelter at Kalgoorlie to run the plant. Overall, while rare earths processing remains a niche use for sulphuric acid, this rapidly expanding industry could be consuming another million t/a by 2030.
References