Sulphur 404 Jan-Feb 2023
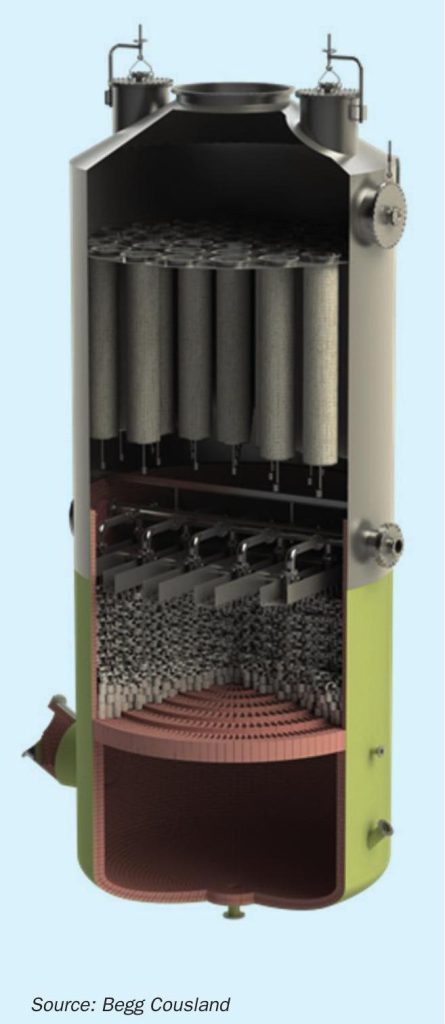
31 January 2023
The art of candle filter wetting
Candle filter mist eliminators are used widely in the sulphuric acid industry across the world. Located in the absorption towers as well as drying towers, they play a pivotal role in reducing air pollution as well as operational problems caused by the formation of sulphuric acid mists. Their successful operation is vital for achieving a plant’s operational capacity, protecting downstream equipment, and reducing the need for stoppages and maintenance interventions.
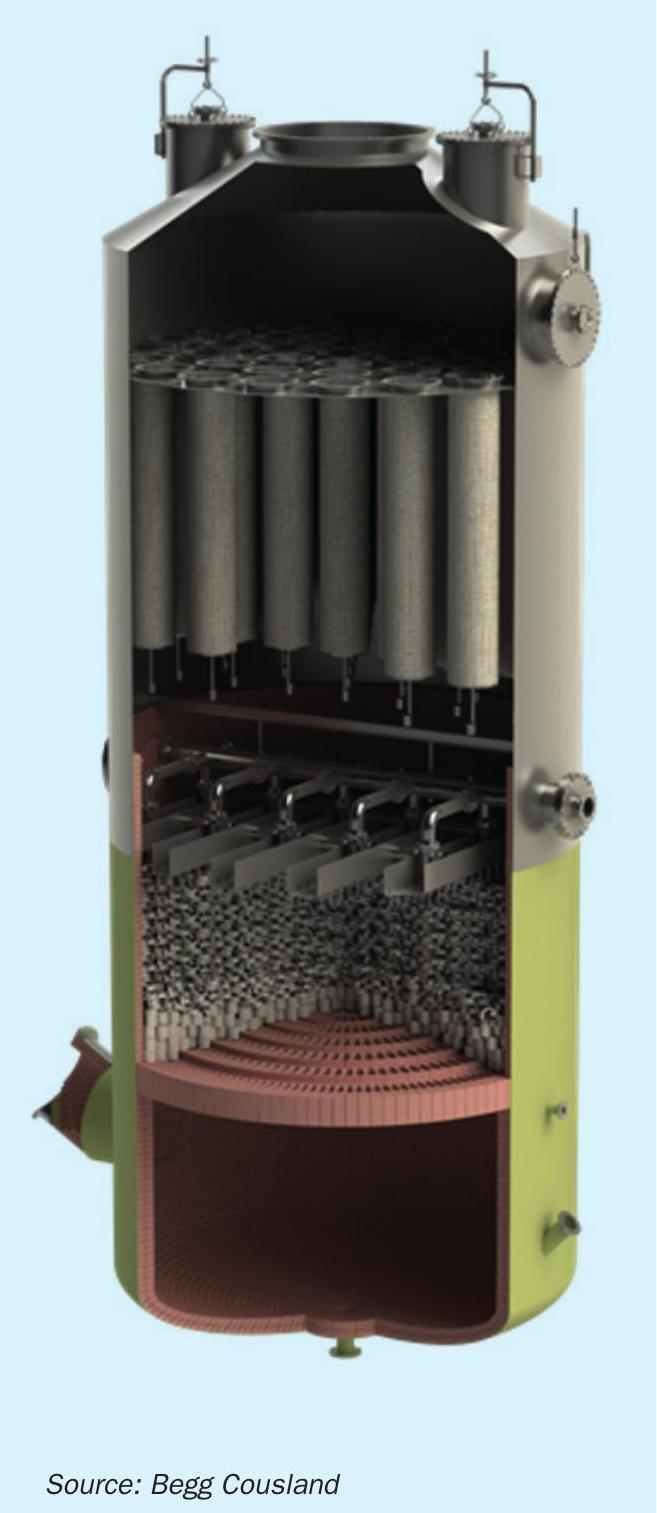
Fig. 1 shows a typical hanging type candle arrangement in an intermediate or final absorption tower.
Brownian diffusion mist eliminators are normally installed in the intermediate absorption tower (IAT) and in more recent times the final absorption tower (FAT) for achieving lower emission standards. Their use relies on the fibre media being sufficiently wetted, but what issues can arise when the candle filters are not sufficiently wet?
Case 1 – Free SO3
One of the main reasons for installing a wetting system in a sulphuric acid plant is in the event of free SO3 , which can cause a visible plume at the stack. This will occur:
- at sulphuric acid plant start-up;
- in cases where there is an interrupted power supply and stopping and starting of the plant;
- in plants that have oleum production.
The best solution is to irrigate the candle filters with sulphuric acid to ensure the fibre bed is sufficiently wet.
Case 2 – NOx (nitrous oxides)
Nitrous oxides can form nitrosyl sulphuric acid which will cause problems within the candle filter fibre bed (Fig. 2). It is dependent on the operating temperature and concentration build-up. This leads to operational issues, such as higher than expected pressure loss, loss of removal efficiency and product contamination. To solve this NOx issue, the following steps can be taken:
- irrigate the candle filters with fresh H2SO4 ;
- increase the tower temperature to above 73°C to dissolve the nitrosyl crystals;
- segregate the acid collected within the filter from the final product acid.
Case 3 – Free SO2
The final case is free SO2 , which can result in emission non-compliance. Begg Cousland’s experience has been with single contact wet sulphuric acid plants and the solution has been to irrigate the filters with a mixture of sulphuric acid and hydrogen peroxide to remove the SO2 .
How to wet a candle filter
Traditionally, candle filters have been wetted using spray nozzles. This can be done by spraying from beneath the installed filters using a series of spray bars and manifolds, or in the case of standing type filters, by fitting the spray nozzle into the top plate. There are some drawbacks to this method:
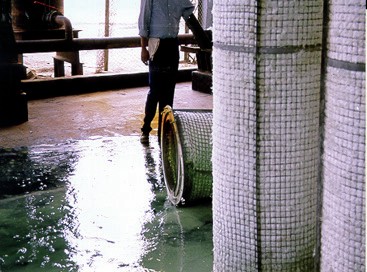
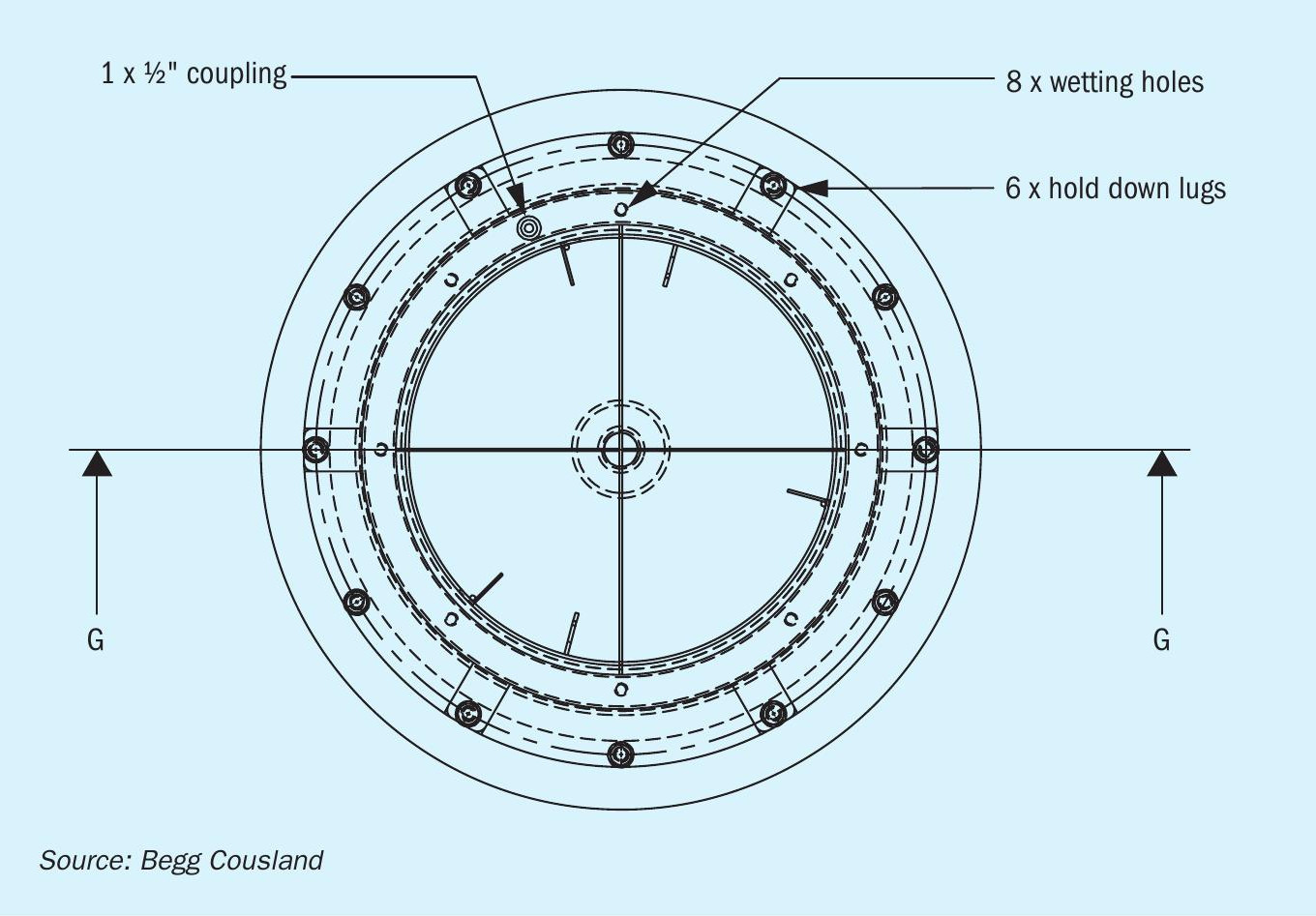
- A relatively high supply pressure (3-5 bar) is needed which may require a secondary acid pump, as the pressure supplied to the acid distributor is too low.
- These methods rely on the gas to carry the sprayed liquid into the fibre bed of the candle which does not always provide uniform coverage, particularly in the case of longer length filters. In some cases, spraying from below and above is necessary to solve this problem.
Improving the introduction of liquid to the fibre bed
Begg Cousland considered several options to improve the wetting of a candle filter and settled on an annular wetting ring solution fitted to the top of the filter (Fig. 3). The main advantages of this design are that it is a low-pressure liquid feed with fully controllable flowrates to suit the candle filter size. The ring allows the liquid to be fed directly into the fibre bed providing uniform liquid addition.
The optimal configuration for a wetting ring system is with the candle filters in a hanging type orientation to ensure easier access to the tubesheet above. In this case there is a series of circumferential manifolds and flexible hoses connected to the wetting ring. It is worth noting that the wetting ring system can be installed as part of a new supply of candle filters, but can also be retrofitted to existing candle filter installations.
Recent case studies
Case study 1: A Southern African customer having issues with free SO3 . This was an existing installation in a plant that was having issues with interrupted power, causing multiple restarts. Begg Cousland looked at how to retrofit a wetting ring in the final absorption tower and came up with a bolt-on solution where the existing candle filters were drilled with holes and retrofitted (Fig. 4). Following the wetting ring installation, stack emissions were improved significantly.
Case study 2: A North American customer having issues with stack opacity when producing oleum. In this case it was slightly more difficult as the customer had X-TRA FLOW candle filters with both an inner and outer fibre bed, meaning two sets of wetting rings had to be produced for each filter (Fig. 5). Again, the filters were drilled with holes to be retrofitted with wetting rings. Both the inner and outer fibre bed were fed from a central circumferential manifold feeding both rings.

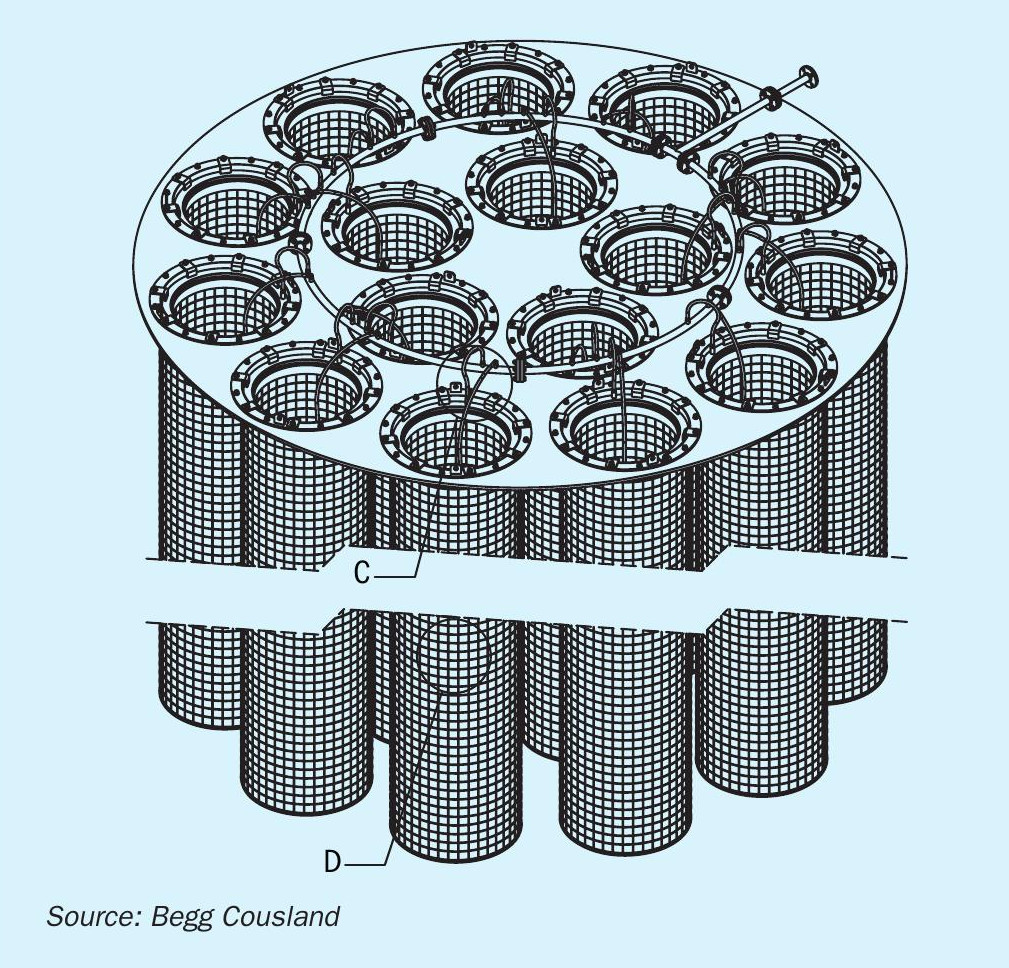
Case study 3: This was one of Begg Cousland’s first experiences of increased fibre bed pressure loss due to NOx in 2004 when a European customer changed the old set of candle filters, like-for-like. When the new candle filters went into operation the pressure loss was higher than the old set, which should not have been the case. The plant sourced zinc concentrate from the Century mine, which has high levels of NO. As shown on the pressure loss trend graph (Fig. 6) the use of some Century concentrate began in 1997-8, which led to an increase in pressure loss. A higher percentage was used from 2002, leading to another increase.
Nitrosylsulphuric Acid (NOHSO4 ) forms crystals below 73°C when insufficient H2 O is present to prevent (or to dissolve) them. The fibre, when removed, was hard to the touch and when sent for analysis high levels of nitrogen were discovered.
It was not possible to visually see the build-up of nitrosyl crystals in the tower/fibre bed as the crystals themselves are white. It only became apparent when the filters were removed from the tower, and they fumed an orange/brown colour.

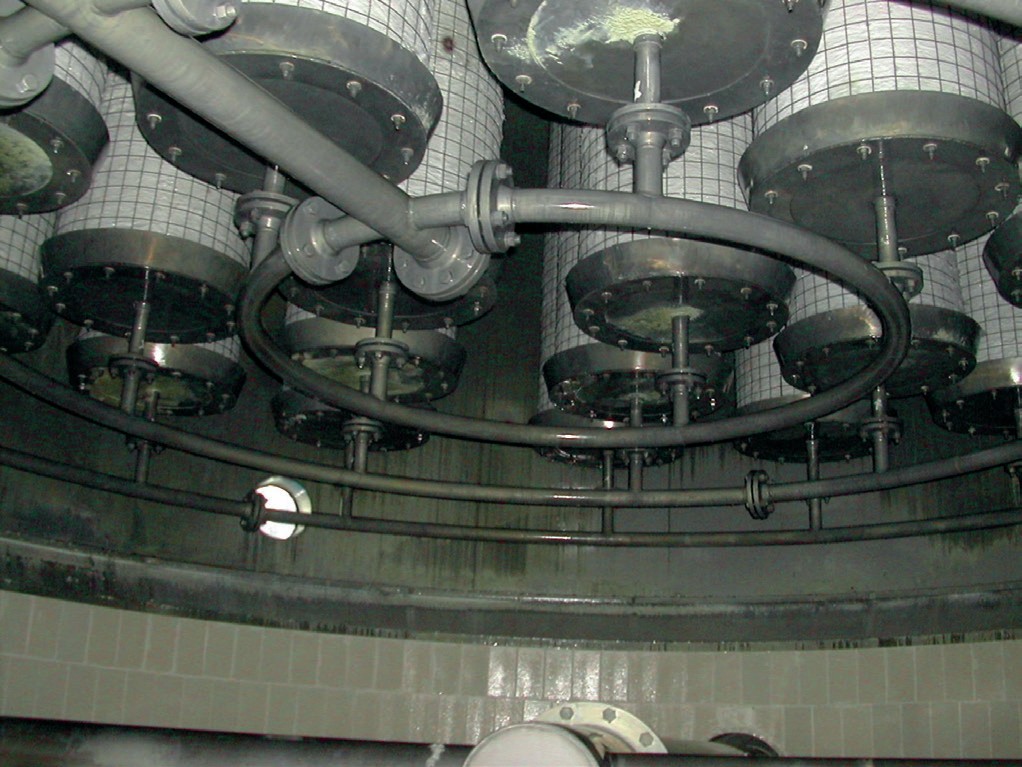
Where NOx is an issue, the tower needs to be operated at an elevated temperature (75-77°C) to solubilize the crystals. The use of a wetting ring is imperative, with the candles pre-wetted before start-up and continuous wetting in operation.
In the case of NOx, the high levels of nitrogen still remain an issue as the collected contaminated acid from the filters must be segregated from the final product acid. A flanged drain pipework can be introduced into a central manifold, as well as the use of a drip tray at the base to minimise NOx drips into the acid below (Fig. 7).
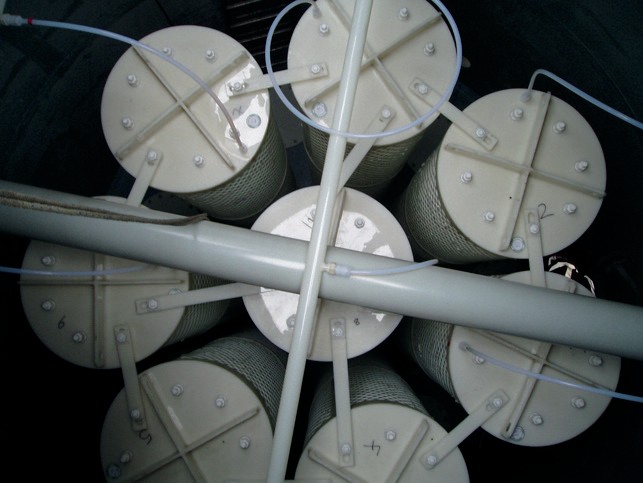
Case study 4: The reduction of SO2 in a European single contact wet sulphuric acid plant. In this installation, there were fluoropolymer candle filters in a standing-type orientation. The mixture of hydrogen peroxide and sulphuric acid was introduced using PFA flexible hoses and wetting rings at the top of the candle. Once again, the stack opacity was greatly reduced.