Nitrogen+Syngas 382 Mar-Apr 2023
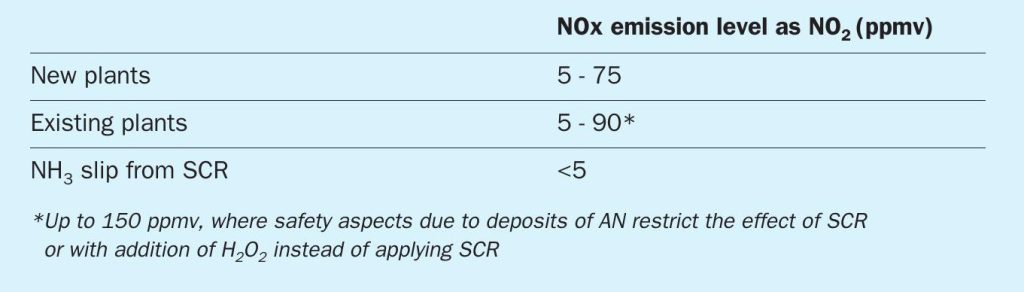
31 March 2023
Emission monitoring from nitric acid production
NITRIC ACID PRODUCTION
Emission monitoring from nitric acid production
Highly efficient N2O abatement technologies, coupled with the continually rising CO2e price/ tonne are the driving forces behind nitric acid plant operators looking for increasingly sensitive and precise measurements of the N2O mass emission. David Inward of Sick AG discusses new state-of-the-art emission monitoring technology which provides the measurements required.
The current intense focus on global warming and the need to transition to decarbonised production processes and carbon-free energy streams as a means to reduce the quantities of greenhouse gases being emitted to atmosphere can already point to a tangible success story from the fertilizer sector.
Nitrous oxide, (N2O), laughing gas, is a notable greenhouse gas with a global warming potential approximately three hundred times greater than carbon dioxide.
The main source of N2O release to the atmosphere relates to its generation as an unwanted by-product in the manufacture of nitric acid. The vast majority of nitric acid production is used by the fertilizer industry, where it is reacted with ammonia to produce nitrogenous fertilizers, such as ammonium nitrate (AN) and calcium ammonium nitrate (CAN).
In contrast to carbon dioxide (CO2), N2O is a more reactive molecule.
Significant progress has been achieved in reducing N2O resulting from nitric acid production, such that emitted concentrations of N2O below 10 parts per million (ppm) are now achievable. Measuring such low N2O concentrations, coupled with the need to report an N2O mass emission with a pre-defined measurement uncertainty < +/-5% is bringing new challenges to the continuous emission monitoring system used as the basis to report greenhouse gas (GHG) emissions.
These improvements are a result of optimisation of the fundamental nitric acid production technology to reduce the generation of this unwanted by-product as well as the employment of downstream abatement technologies located after the final nitric acid production step which are designed to convert any remaining N2O in the tail gas stream into nitrogen and oxygen.
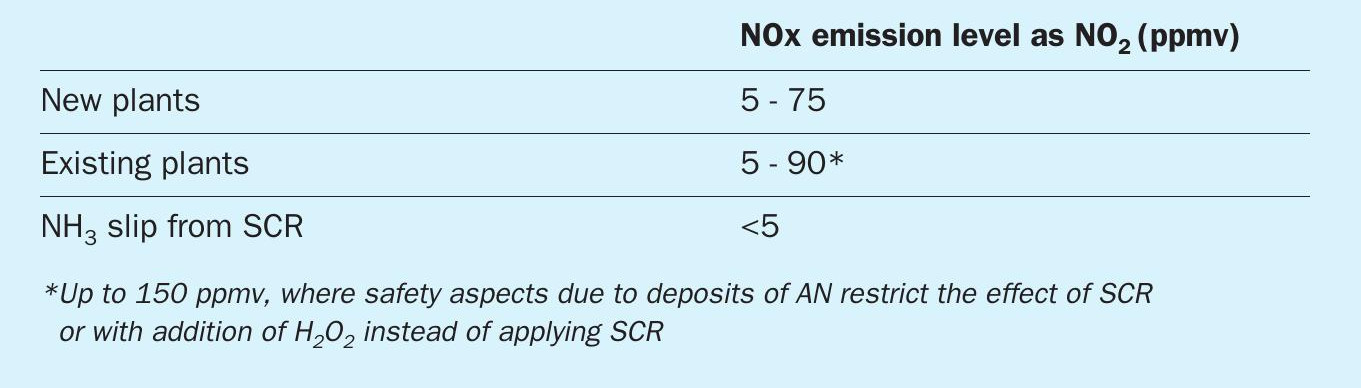
Implementation of commercial market drivers, such as the carbon trading scheme and Carbon Border Adjustment Mechanism in the European Union are the fiscal drivers, which will maintain a strong focus on minimising N2O mass emissions from nitric acid production.
Emission monitoring regulations – Emission limit values
Historically, the main focus in terms of monitoring and reporting emissions from the production of nitric acid was related to ensuring that emissions of “NOx”, comprising the sum of the concentrations of nitric oxide (NO) and nitrogen dioxide (NO2) was below a defined emission limit value.
Since the method to reduce NOx emissions is typically based on a selective catalytic reactor (SCR) or DeNOx unit, which doses ammonia to react the residual NOx to produce nitrogen and water, an ammonia “slip” emission limit value also applies.
In Europe, the Industrial Emission Directive (IED 2010/75) includes a series of industry-specific Best Available Technique Reference (BREF) documents, such as that for large volume inorganic chemicals, which comprises separate chapters that cover specific fertilizer production processes, such as nitric acid.
Table 1 shows NOx emission levels associated with the application of BAT for the production of nitric acid.
Published in the same year, the World Bank guidelines for nitric acid plants also sets guideline values for NOx (NO+NO2 ) and NH3 emissions (see Table 2).
Important to note is that emission limit values for NO/NO2 and NH3 are typically based on normalised conditions. This means that that the pollutant concentration value must be referenced to standardised conditions, with reference values set for temperature, pressure, water vapour and oxygen concentrations. This implies a need to also measure oxygen and either measure dry basis (after removing water vapour) or include a water vapour measurement if the sample is measured in a wet condition.
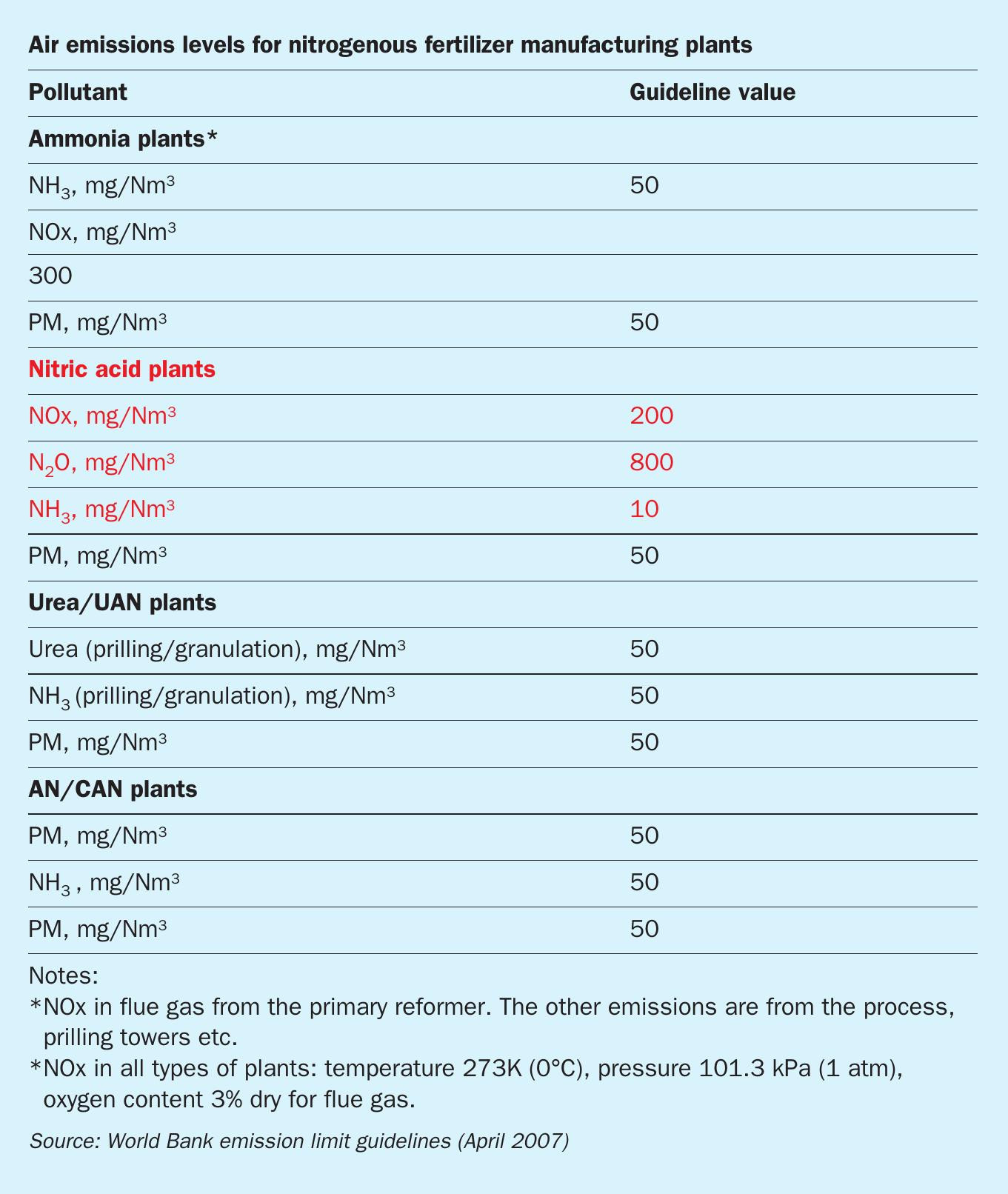
Emission monitoring regulations
In contrast, as described in EN 2066/2018, the reporting of greenhouse gases such as N2O is done as mass emission, by combining a concentration measurement with a volumetric flow measurement.
Since flow technology inherently measures in-situ, i.e. measuring the volumetric flow of gas out of the final stack in a “wet basis”, logically the gas analyser should also measure “wet basis” so that the N2O concentration and volumetric flow can be directly combined to report in the required units (kg/hour N2O).
Table 3 shows the European regulation for N2O emissions from nitric acid production (LVIC BREF August 2007).
Application challenges
The contrasting reporting regulations for emission limit values and greenhouse gas mass emission place a combination of differing requirements on the measurement technology. Furthermore, since the tail gas composition resulting from nitric acid production possesses some unique properties, it follows that applying a conventional emission monitoring technology may not be the best fit.
Cold extractive infra-red gas analyser
A conventional continuous emission monitoring system is based on a cold extractive analyser design (Fig. 1). The conventional infra-red analyser requires a completely dry and particle-free sample gas. Therefore, the sample system is based around two aspects, namely a gas cooler to chill the sample gas to condense out and remove water, coupled with a series of filter elements, which remove first coarse and then fine dust particles.
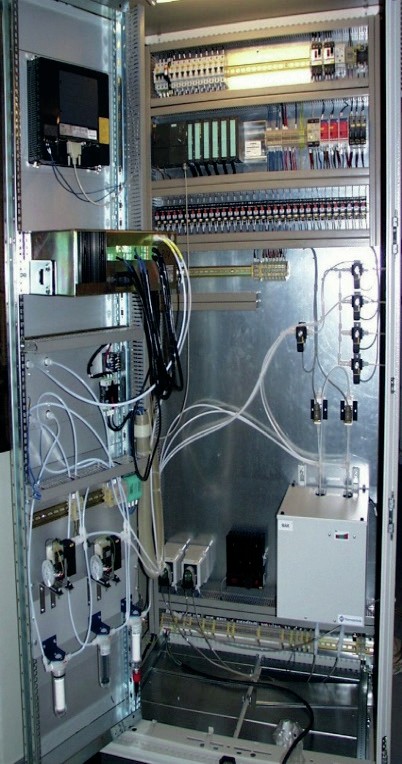
Conventional infra-red analysers are well suited to measuring NO, but are not sufficiently sensitive to directly measure NO2. To measure total NOx, (NO + NO2 ) in emission monitoring applications containing a small NO2 portion, a NOx converter is usually applied, which reduces NO2 to NO directly before the infra-red analyser. However, the tail gas from nitric acid production contains a uniquely high proportion of NO2 , which would rapidly exhaust the NOx converter catalyst charge. An analyser that directly measures both NO and NO2 therefore better suits the application requirements.
The next point to consider concerns the highly water-soluble nature of nitrogen dioxide (NO2), a physical property that forms the basis of nitric acid production. Since nitrogen dioxide (NO2) in the tail gas from nitric acid production makes such a significant contribution to the total NOx emission, cooling the gas to remove water vapour and ensure a dry sample gas brings with it concerns that a significant portion of the NO2 will be dissolved and lost in the cooler condensate.
Finally, the potential presence of ammonia in the sample gas brings major difficulties. Utilising an analyser technology requiring the sample gas to be cooled to dry it, introduces the threat that ammonia present in the sample gas will react with oxides of nitrogen at temperatures below approximately 150°C to form solid ammonia salts (ammonium nitrate, ammonium nitrite) which will cause severe blockages in the sample system. Ammonia slip from the use of SCR DeNOx units dosing ammonia creates a consistent threat of salt formation and blockages once the sample gas is allowed to cool.
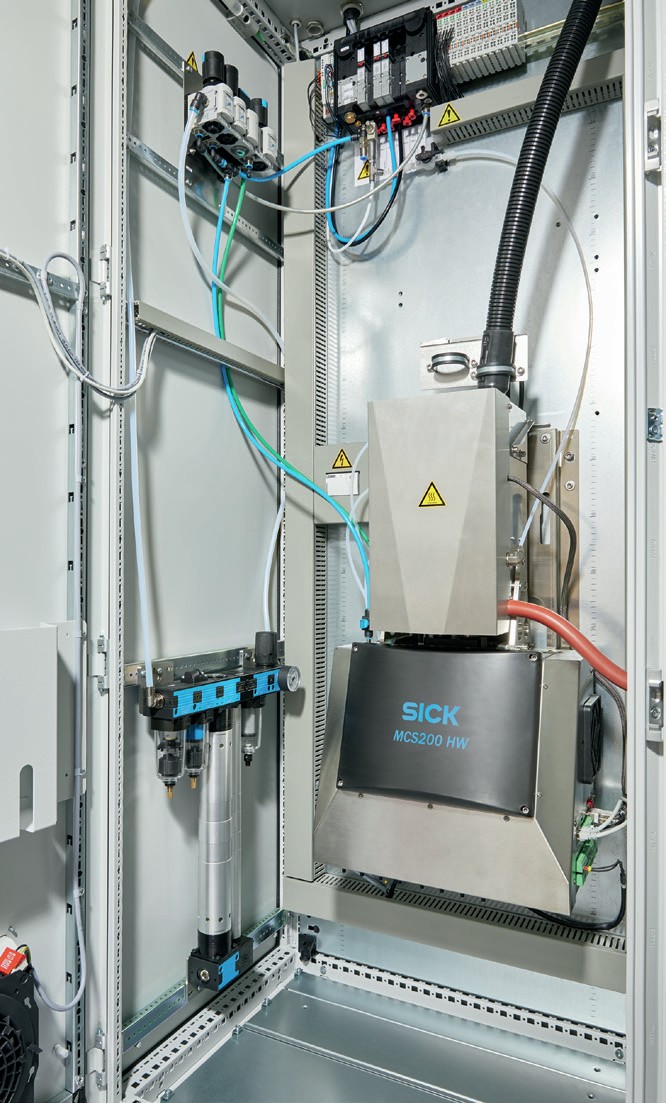
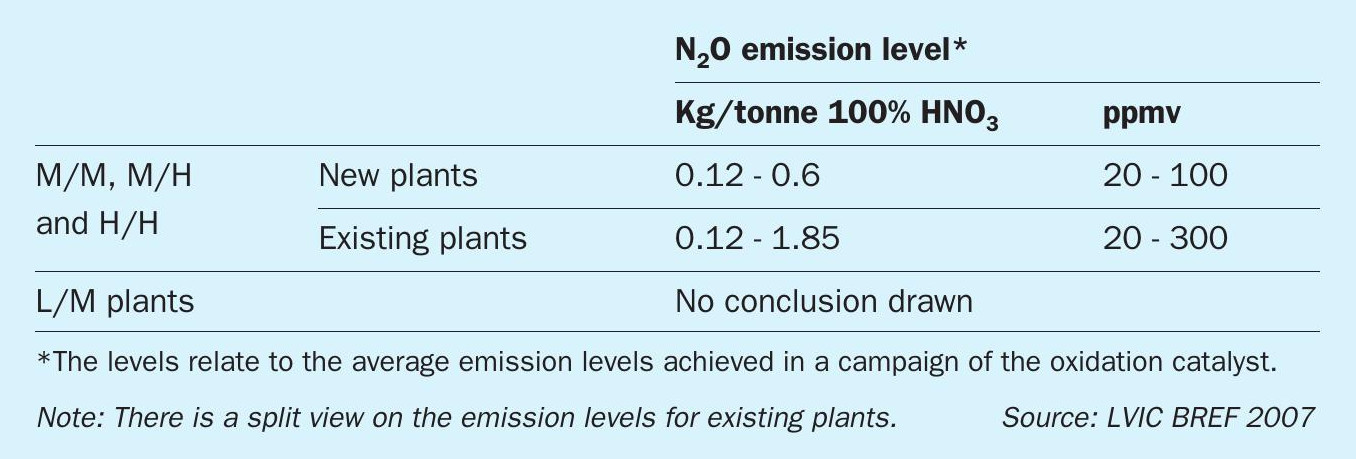
Hot extractive infra-red gas analyser
Hot extractive infra-red analysers (Fig. 2) have in recent years been broadly applied to the task of measuring emissions from nitric acid production. The fundamental design differs by maintaining the sample at an elevated temperature (200°C) across the entire sampling chain, i.e., from the sample extraction point to the measuring cuvette.
This design inherently avoids both solubility issues related to a proper and precise NO2 measurement, as well as any threat of ammonia salt formation. Therefore, the analyser can still measure emissions reliably behind an SCR DeNOx unit dosing ammonia and even during process start-up, when ammonia combustion in the primary furnace may not have reached stable combustion conditions.
Since the analyser measures the hot, raw sample gas, water vapour is not removed, but included as a measured component both to dynamically correct interferences to other target gases, as well as to allow the pollutant gases concentrations to be expressed dry basis.
The hot extractive infra-red analyser offers a powerful multi-component capability, which allows a single analyser to measure all required components, irrespective as to whether SCR or SNCR is applied. This includes direct measurement of both NO and NO2 as the basis for the NOx measurement.
A zirconium oxygen detector, another technology which perfectly fits a hot measurement design allows pollutant concentrations to be normalised to 3% O2 .
Table 4 shows MCS 200 HW hot extractive analyser certified ranges according to EN 15267.
Ultrasonic flowmeter
An ultrasonic flowmeter provides the volumetric flow measurement which when combined with the N2 O concentration gives the desired N2 O mass emission (kg N2 O /hour)
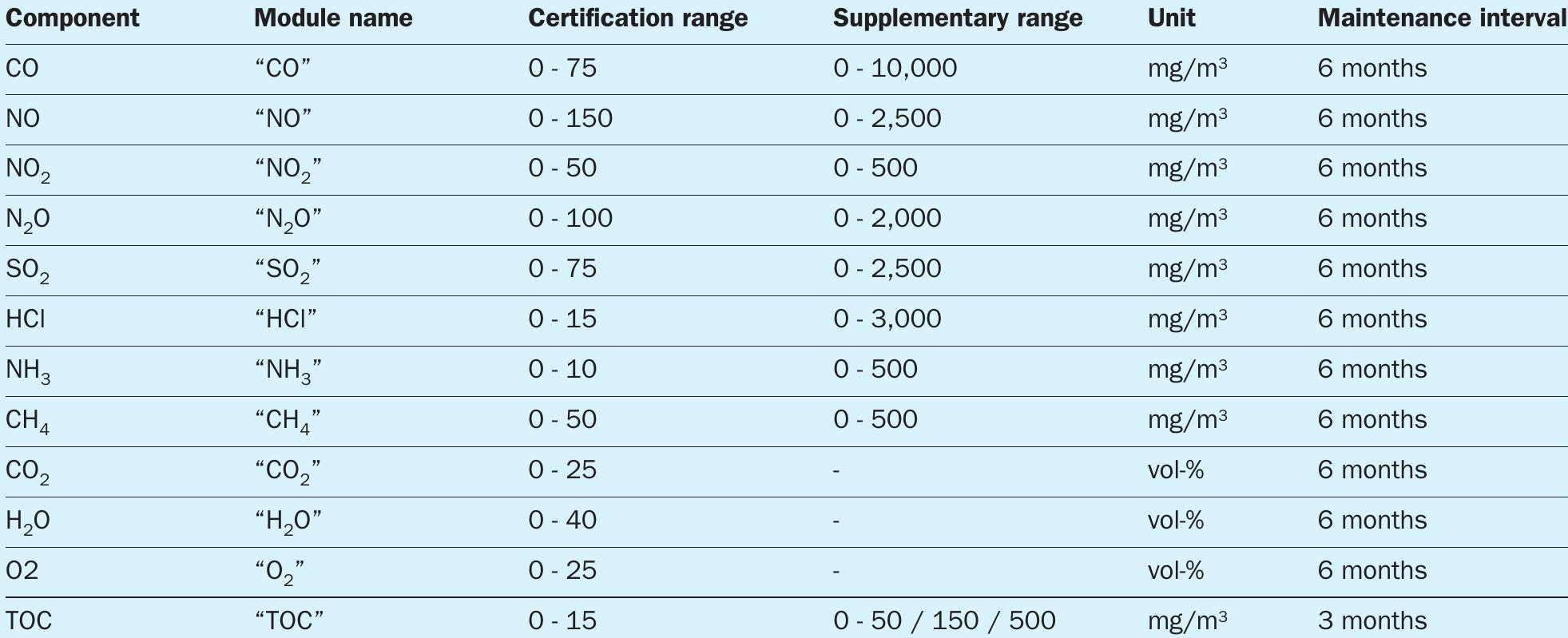
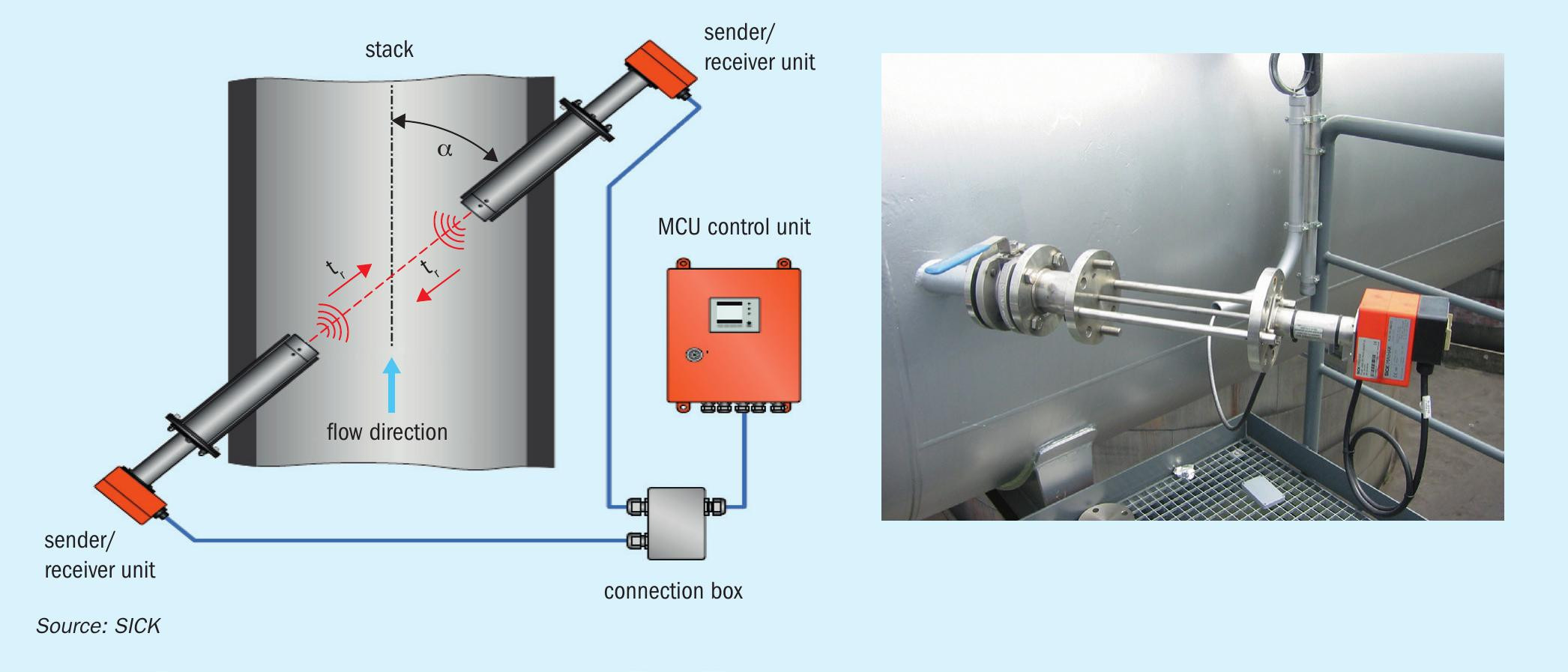
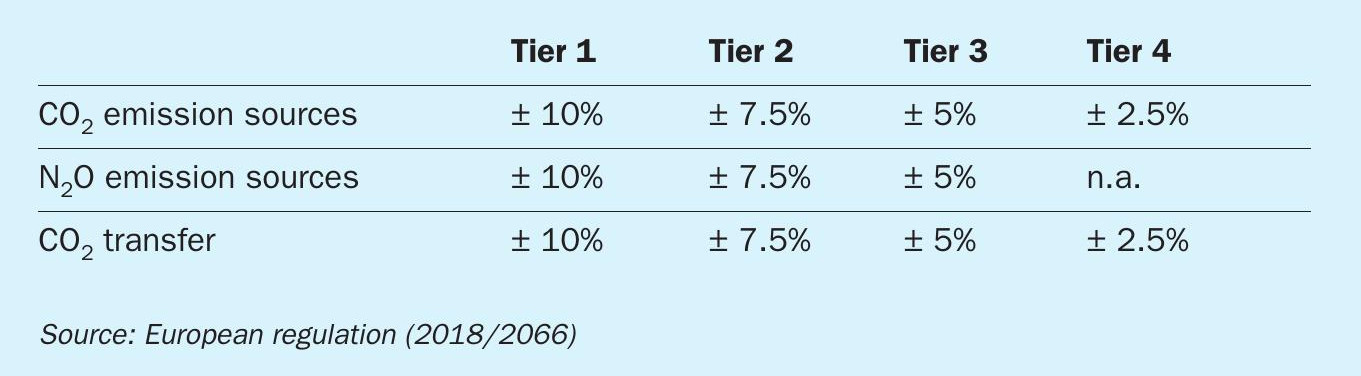
To capture the entire flow profile across the stack, the ultrasonic flowmeter is ideally mounted in a cross-duct design (Fig. 3). Ultrasonic signals travel both with and against the flow, the resulting time differential is the basis to precisely calculate the gas flow velocity.
This non-invasive volumetric flow measurement method offers a combination of best-in-class measurement uncertainty with minimal maintenance support.
Current and future requirements – N2O mass emission
The latest European regulation (2018/2066) sets out the requirements for emission monitoring technology for the purpose of reporting the N2O mass emission and establishes defined minimum performance requirements for the N2O mass emission measurement uncertainty, as well as defining how this uncertainty performance is to be defined.
The use of gas analysers and volumetric flowmeters with a valid QAL 1 certificate according to EN 15267 is a prerequisite.
The on-site “QAL 2” calibration procedure performed by a certified (EN 17205) laboratory, compares the emission monitoring system with manual sampling measurements and is the basis to define the measurement uncertainty of the N2O mass emission.
Table 5 shows the tiers for continuous emission monitoring systems (maximum permissible uncertainty for each tier).
Whilst the current reporting regulation sets out the minimum uncertainty requirement, commercial incentives are having an ever-stronger impact on current performance requirements.
The carbon dioxide equivalent (CO2 e) price per tonne has accelerated rapidly over the last three years, with almost a threefold increase in only the last two years (see Fig. 4). The current 2023 price has just touched e100/tonne and future projections anticipate ongoing increases.
The rising CO2e price increase acts as a strong incentive for plant operators to reduce their N2O mass emission, from which significant benefits on the trading of carbon credits can be reached.
State-of-the-art abatement technologies now require emission monitoring technology that can measure very low N2O concentrations (< 10 ppm). The need to achieve the best possible result on the N2O mass emission measurement uncertainty is relevant, since the uncertainty performance is included on the N2O mass emission calculation budget of the plant operator.
Greenhouse gas mass emission – field trial
When looking to optimise N2O mass emission uncertainty, the two main aspects are optimisation of measurement hardware combined with a calibration procedure that simulates the on-site conditions as precisely as possible. Sick AG already has in-depth experience of a field trial to establish mass emission uncertainty performance for greenhouse gas mass emission reporting. This was based around two complete CO2 greenhouse gas mass emission monitoring systems to verify uncertainty performance under field conditions.
A CO2 concentration analyser measuring “wet basis” i.e., without the removal of water vapour, was combined with the volumetric flow measured by an ultra-sonic flow meter.
Extensive experience in the field of fiscal flow metering of natural gas, supported the design considerations, since it is established that multi-path ultrasonic flowmeter designs and precisely simulated calibration procedures allow volumetric measurement uncertainty < +/0.1% to be achieved. Therefore, for the field trial a special dual path ultra-sonic flowmeter design was implemented.
The next focus was that of the site specific calibration. The following site-specific optimisations were targeted to drive down measurement uncertainty performance:
- special calibration of the analyser (optimise linearity at typical measured concentrations);
- establishment of exact flow profile in the stack by means of CFD (computational fluid dynamics);
- very precise flange toflange distance measurements on the stack at site (laser scanner) as the basis of the travel times for the ultra-sonic flowmeter signals (Fig. 5).
The resulting measurement uncertainty results for the duration of the field trial, expressed against the standard reference methods were comfortably lower than the requirements coming from the European regulations (2066/2018 MRR Annex VIII, Tier 3 +/5%).
Summary
Highly efficient N2O abatement technologies, coupled with the continually rising CO2e price / tonne are the driving forces behind nitric acid plant operators looking for increasingly sensitive and precise measurements of the N2O mass emission.
The greenhouse gas regulation (2066/2018) in combination with the value in trading carbon credits is bringing a strong fiscal aspect to how the technical requirements for an N2 O mass emission system are defined.
A hot extractive gas analyser is ideally suited to fulfilling the complete measuring task for reporting emissions to air from nitric acid production. This includes the ability to measure N2O concentrations < 10 ppm.
The combination with an ultra-sonic flow-meter offers a best-in-class complete solution to report N2O mass emission. The volumetric flow measurement is equally relevant as the N2O gas analyser in terms of mass emission measurement uncertainty.
The N2O mass emission measurement uncertainty result for any given plant will be site specific.
The defined N2O mass uncertainty will be strongly influenced by site specific calibration efforts.
A field trial for CO2 mass emission as a greenhouse gas indicates that an uncertainty performance exceeding that required by European regulations for N2O (Tier 3, +/5%) is achievable.
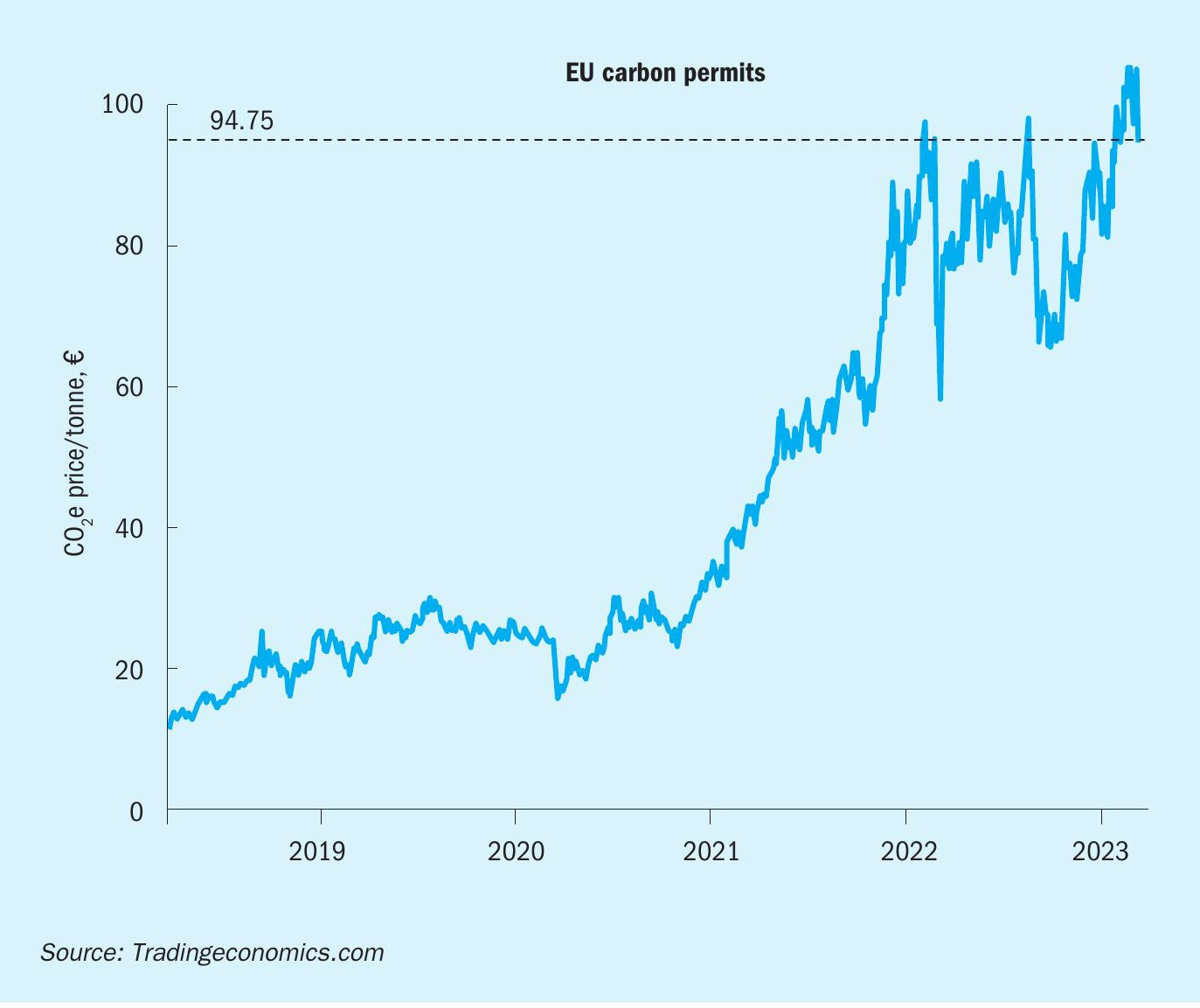
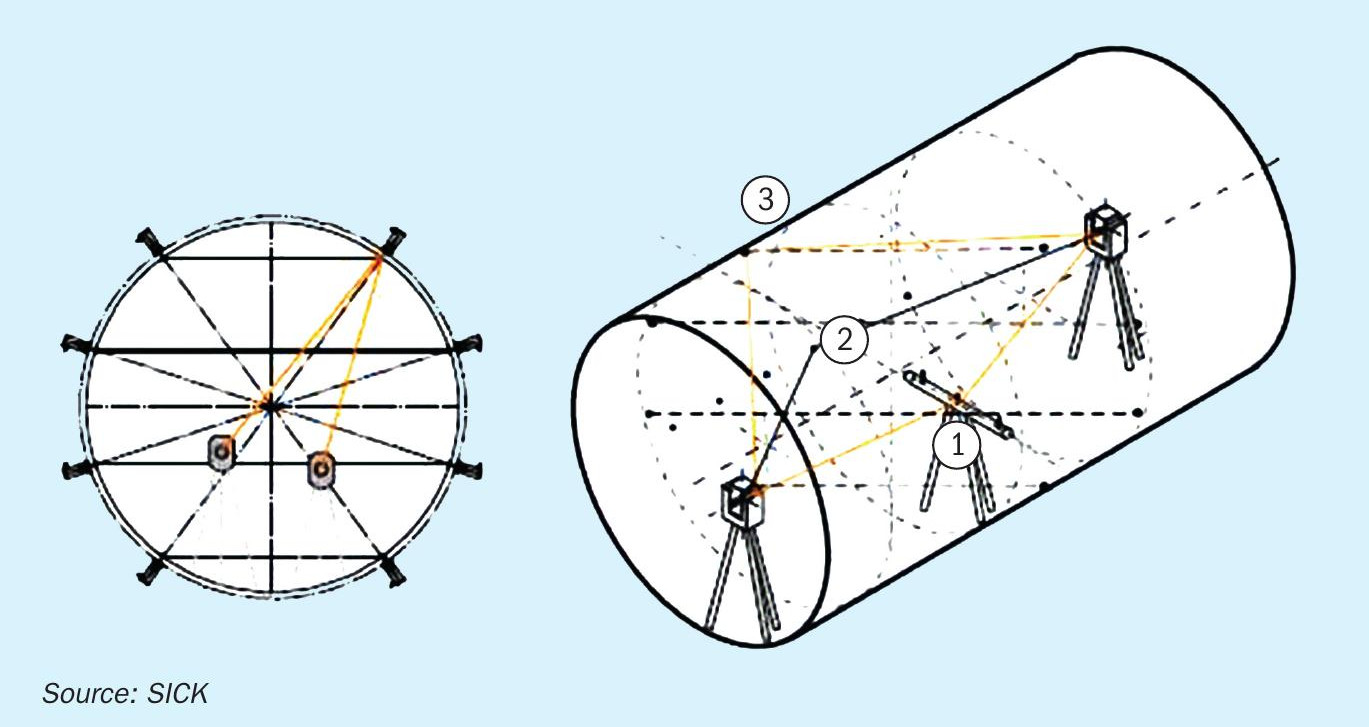
A field trial specific to nitrous oxide is planned to establish N2O mass emission measurement uncertainty according the Greenhouse Gas Regulation (2066/2018) with MRR Guidance Documents 4 & 7.
Sick AG is now looking to initiate a project at a European nitric acid plant to establish N2O mass emission performance based around applying bestin-class technologies for a complete solution approach. n
References