Sulphur 405 Mar-Apr 2023
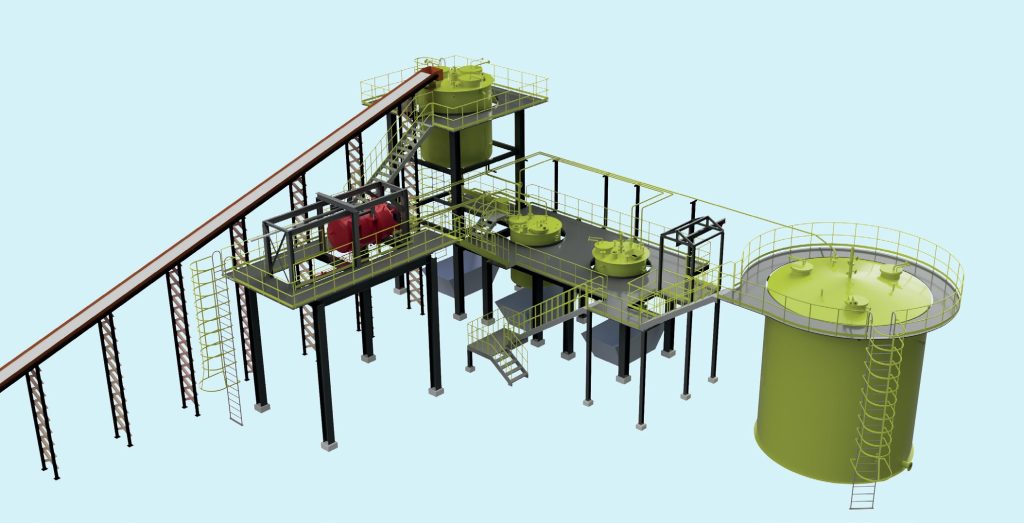
31 March 2023
Life cycle of a sulphur melting plant
SULPHUR PROCESSING
Life cycle of a sulphur melting plant
Mathijs Sijpkes, Nuria Pascual Vasco and Jan Hermans of Sulphurnet discuss the importance of a whole life cycle cost analysis at the conceptual design phase when making investment decisions about new sulphur processing facilities.
Sulphuric acid is one of the most widely used chemicals in the world, its main applications are the extraction of minerals in the mining industry as well as the production of fertilizers. Due to the increase in demand in these applications, the sulphuric a cid industry is set to continue to grow over the next decades.
An important part of the sulphuric acid plant is the sulphur melting and filtration facility. This is where the solid sulphur is treated and prepared as a raw material for the production of sulphuric acid. To keep the sulphuric acid plant running continuously and to keep costs under control, it is essential to feed high-quality liquid sulphur and have a reliable sulphur melting and filtration plant. Achieving this goal requires the expertise of a sulphur plant designer and a significant investment.
Sulphur in itself is a neutral non-corrosive product, but due to the presence of humidity, air, and the bacteria thiobacillus, elemental sulphur is oxidised into sulphates that react further with the moisture from the environment producing sulphuric acid derivatives. The solid sulphur then turns into a very corrosive product that will cause serious damage to the plant if it is not handled properly.
Besides corrosion, the exceptional properties of sulphur also require attention. Sulphur is liquid only between 125°C and 158°C, a temperature range that should be maintained at all times; its weight cannot be neglected; and its impurities need to be removed. Thus, it is fundamental to consider experienced designers that select appropriate materials of construction and instrumentation, and to consider the reasons for the required investment.
In general, the sulphur section has an exceptionally low priority in the financial budget when designing a new facility. However, there has been a shift in mindset with plant owners increasingly looking for sulphur processing facilities that demonstrate value for money over the long term, rather than simply opting for the design which leads to the least expensive solution. Returns on invested capital costs are essential in making decisions and a combination of knowledge of the potential investment, analytical skills, and the capability to draw conclusions from available data and experience are all important. For example, a major maintenance cost in the sulphuric acid plant is catalyst screening due to high pressure losses in the converter. These costs can easily add up to $2.5-3 million over a period of ten days. However, by investing much less than that in the sulphur section an acid plant can be in operation for more than 32 months before catalyst screening is required.
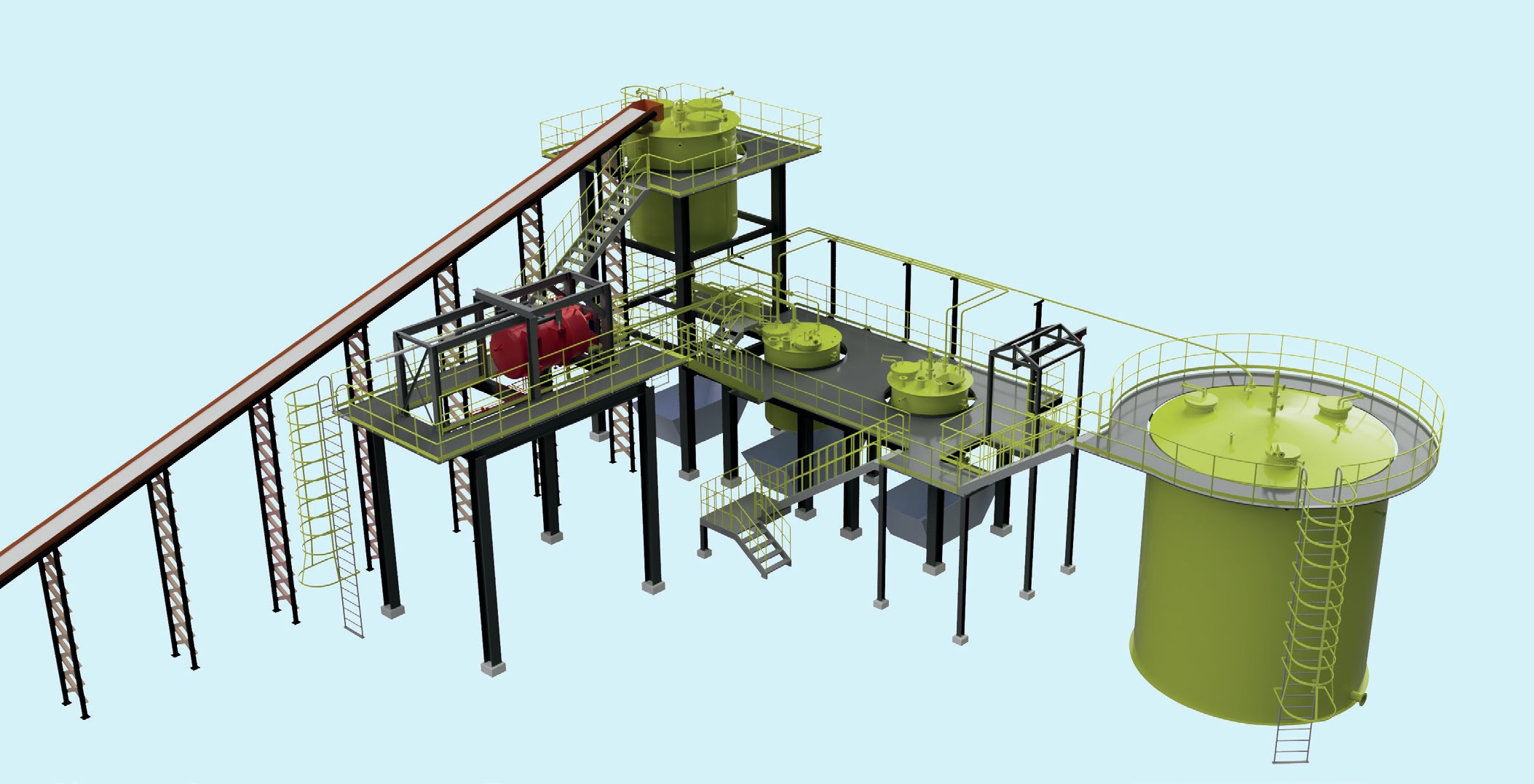
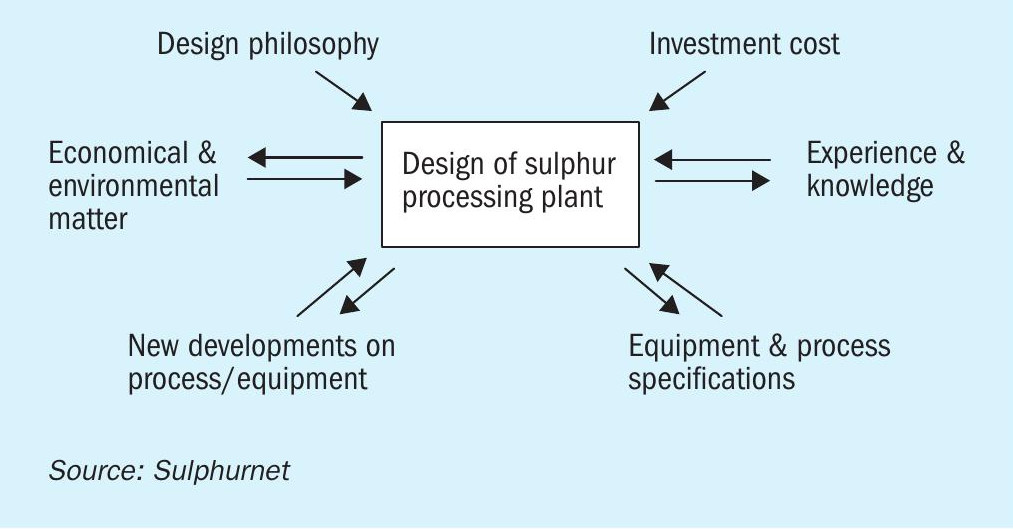
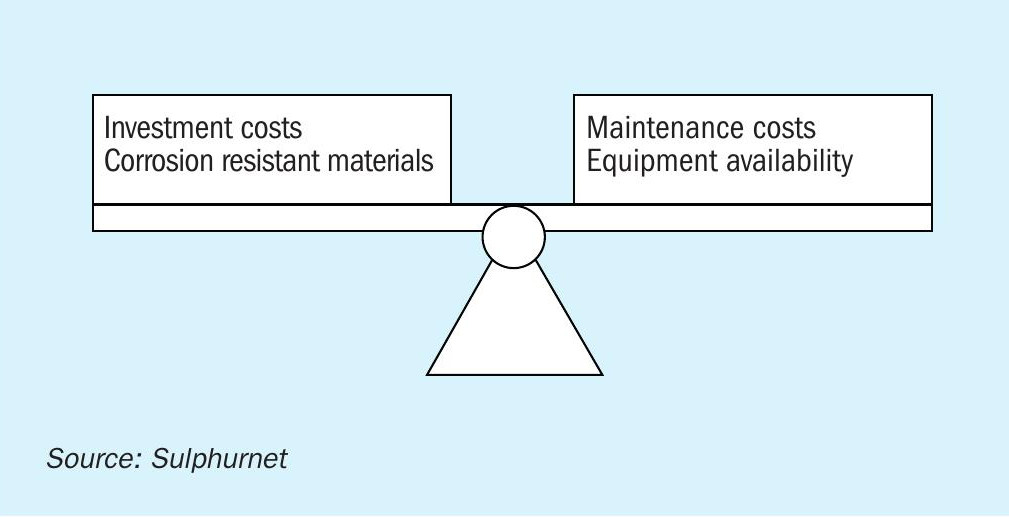
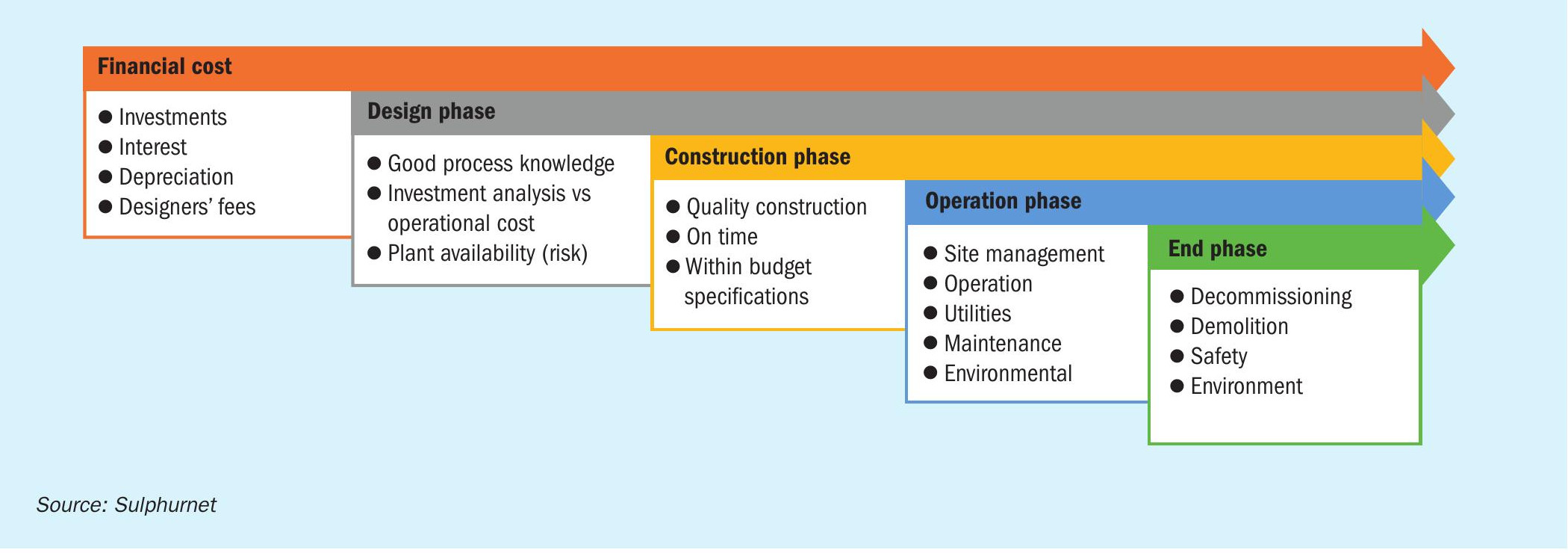
This change of mindset increases the importance of finding the maximum benefit of the investment. Thus, it is highly recommended to carry out a whole life cycle cost (WLCC) analysis as early as possible in the decision-making process, preferably in the conceptual design phase, where 70% of the WLCC can be examined and the design versus costing decisions can be justified.
The WLCC evaluates all costs in all stages involved in the operation of the sulphur melting plant, from design to decommissioning and disposal, together with the effects on the sulphuric acid plant. The ultimate goal is to construct the plant in a “build right first time” methodology while taking into account the long-term costs and economic performance of constructed assets. In addition, operator health, environmental legislation must be considered, as well as maintenance and operation issues.
The WLLC should be performed together with a risk analysis when evaluating a new sulphur melting project. During the risk analysis, internal and external risks and potential impacts are identified, the cause of those possible risks are analysed and evaluated in order to make decisions.
Design phase
The design stage, which starts with planning and engineering the sulphur plant, is the major phase of the project. Here the specific needs, requirements and specifications of the operation need to be defined. This may include determining the appropriate future needs and selecting the melting technology and filtration systems as well as implementing safety measures.
During the design phase, estimates must be made for the overall whole life cycle costing of the plant. This goes well beyond the technology of the process. Shortcuts in the design causes problems in operation and always results in high expenses.
During the design phase the following topics can be studied/evaluated:
Equipment selection
All viable options must be thoroughly analysed while evaluating the expected overall costs and benefits, i.e., investment cost versus operational benefits considering equipment lifetime and process availability. Risk management is an important task in this process. As projects continue to increase in cost, greater risk must be accepted.
In this context, various considerations should be evaluated, for example:
- Back-up equipment to assure plant availability will increase the investment but ensure almost 100% operation.
- Using corrosion resistant materials of construction to increase the plant lifetime implies higher investment costs but reduces maintenance cost.
- Melting sulphur requires a lot of energy in the form of steam to evaporate the water from the solid sulphur. This is generated in the acid plant but could also be converted to electricity.
- Should the solid sulphur warehouse be covered to protect it from rain or not? Under roof storage requires higher investment but ensures better raw material quality.
- Savings in the design of a sulphur melting tank reduces investment but increases risks and maintenance costs.
Construction phase
The construction phase includes the installation of equipment, such as solid handling equipment, various tanks, filters, and the construction of buildings and other structures. The quality of construction is important. A well-constructed plant using high-quality materials and equipment is likely to have a longer lifetime than one that is poorly built.
During this stage the plant should be built according to the design and within the time schedule and budget. Considering the tasks, material and personal resources, contingencies and costs involved in all the stages of construction during the design phase will always raise unforeseen topics and costs, help in the decision making and make the team better prepared.
Cost estimates during the operation phase
The operation phase includes various key factors:
Operating conditions
Analyses of the operational cost in various forms must be assessed. Some considerations for operating a sulphur melting plant include:
- number of operators required versus the level of automation;
- reliable recovery of steam/condensate and the requirements of other utilities must be controlled to minimise costs without endangering plants operation;
- effect of the quality of raw materials like solid sulphur on the operation (water content, acidity and organics will all affect the operation). Poor quality sulphur leads to difficulties in processing and is a potential risk for production losses, and creates extra waste.
Maintenance
Maintenance can be defined as regular programmed maintenance, or response maintenance e.g. in case of emergencies.
Scheduled maintenance will help to extend the lifetime of a plant by preventing equipment failures, wear and tear. Once the plant is operational, it will go through a period of production, during which it will melt and filter sulphur according to the needs of the operation. This stage may last for many years, depending on the lifetime of the equipment and the quality of sulphur used in the plant.
Emergency maintenance is needed when an asset or piece of equipment suffers an unexpected breakdown or situations occur that result in an immediate threat to health and safety or could cause serious property damage. Lack of commitment to a scheduled maintenance program, increases the probability of emergency maintenance. The cost of emergency maintenance is many times higher than the costing of scheduled maintenance. Only considering time as a factor, shutting down while waiting for spare parts to arrive on site leads to production losses.
Utility costs
Melting sulphur requires a considerable amount of heat in the form of steam, which is produced in the acid plant, were it could also be converted to electricity. Decreasing steam consumption and recycling of condensate is an objective. Minimising power consumption, plant air, and instrument air are further objectives.
Most of those topics can be studied to a good extent during the design phase of a project. For example, correct measures in the process design or in the selection phase of equipment can reduce the power consumption of rotating equipment.
Environmental load
Gaseous emissions occur during the sulphur melting process both in the form of H2 S, which is present in sulphur, and in the form of sulphur flour. Sulphur flour consists of fine sulphur particles and droplets that escape mainly through the stack of the melting tank and solidify on cold spots. These fines can cause serious corrosion and can result in reduced plant lifetime or increased maintenance costs. Design of the gas cleaning system requires an excellent knowledge of the chemistry and physical properties involved in the process and the technology required.
Site management
The responsibility of the site management team is broad. This cost centre is responsible for keeping the physical plant and its assets running. It includes the physical workplace of the people, the day-to-day plant operation, keeping plant changes updated, complying with the latest legislations, the organisation and planning of all the side works, maintenance, inventory of spare-parts and the study of potential future projects.
All things considered, site management is an essential aspect of any operational plant. When overall safety is a priority and regular maintenance is well executed and according to a defined schedule, the life cycle of assets, systems, and equipment is extended and personnel injuries are minimised. This reduces the company costs for emergency repairs or replacements for expensive assets, adding revenue to the bottom line.
Decommissioning phase
When the plant eventually reaches the end of its operational lifetime, the decommissioning phase starts. This may involve the removal of equipment, the demolition of buildings, and the clean-up of any contaminated soil or water according to environmental regulations. Site restoration is carried out to return the site to its original state.
Total financial cost
The total financial cost is built up through the whole life cycle of the plant in all phases of the project, which should include the decisions made as a result of the risk assessment. Other costs not specifically mentioned should also be considered. It all comes down to the predicted overall investment, operational and other costs versus benefits.
Conclusion
The construction of a reliable sulphur melting and filtration plant may require a higher investment cost, but making the wrong choices in the initial phase of the plant design will lead to high unexpected maintenance costs, production losses and poor safety, that at the end of the day will translate into higher operational expenses in the sulphuric acid plant. By performing a WLCC with a qualified partner at an early stage of the project, it is possible to anticipate these costs, and instead, get the right design and construction for the sulphur melting plant from the outset.