Sulphur 405 Mar-Apr 2023
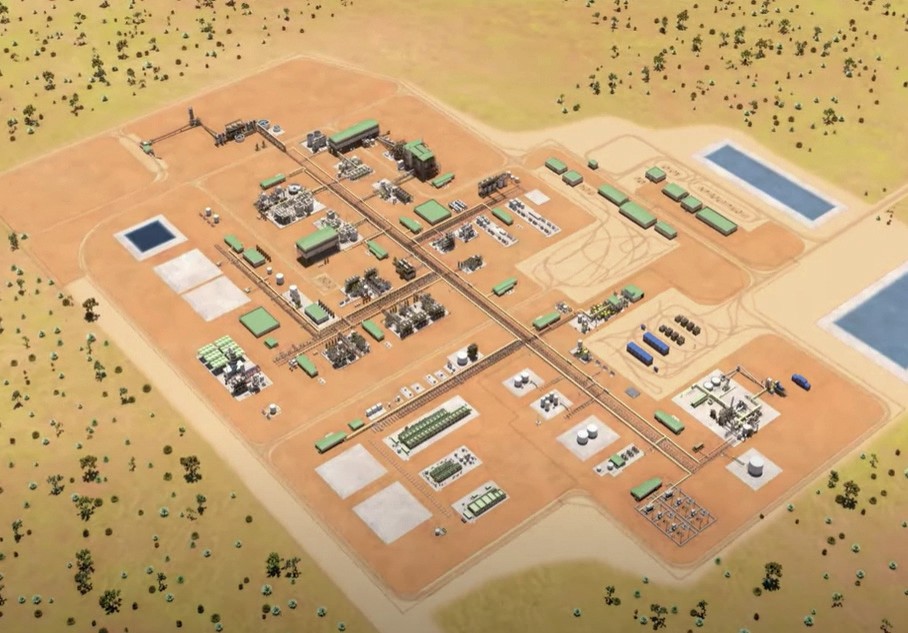
31 March 2023
Sulphuric Acid News Roundup
AUSTRALIA
Chemetics to provide sustainable acid technology
Arafura Rare Earths Ltd has awarded Worley subsidiary Chemetics Inc the contract to install Chemetics CORE-SO2™ sulphuric acid technology at its Nolans Project in the Northern Territory of Australia. The scope of the contract is to deliver the detailed engineering and supply of the sulphuric acid plant plus associated oxygen plant on a lump sum basis. The acid plant at Arafura’s Nolans Project will be designed to meet future emission performance and clean energy transition goals, utilising CORE-SO2’s high turndown capability and the potential to idle the plant while keeping the catalyst warm for extended periods of time, allowing the acid plant to operate with 95% reduced SO2 emissions when compared to traditional double contact double absorption (DCDA) plants. High pressure steam production within the process will allow CO2 – free electrical power to be generated. By removing the use of a diesel or natural gas start-up burner, further greenhouse gas emissions will be prevented.
Additionally, being 60% smaller in size than traditional sulphuric acid plants, the plant will low internal gas flows and fewer pieces of equipment, enabling modularisation. This will minimise construction and assembly work for the remote mine site at the Nolans Pro-ject, leading to increased workforce safety and improved cost-efficiency.
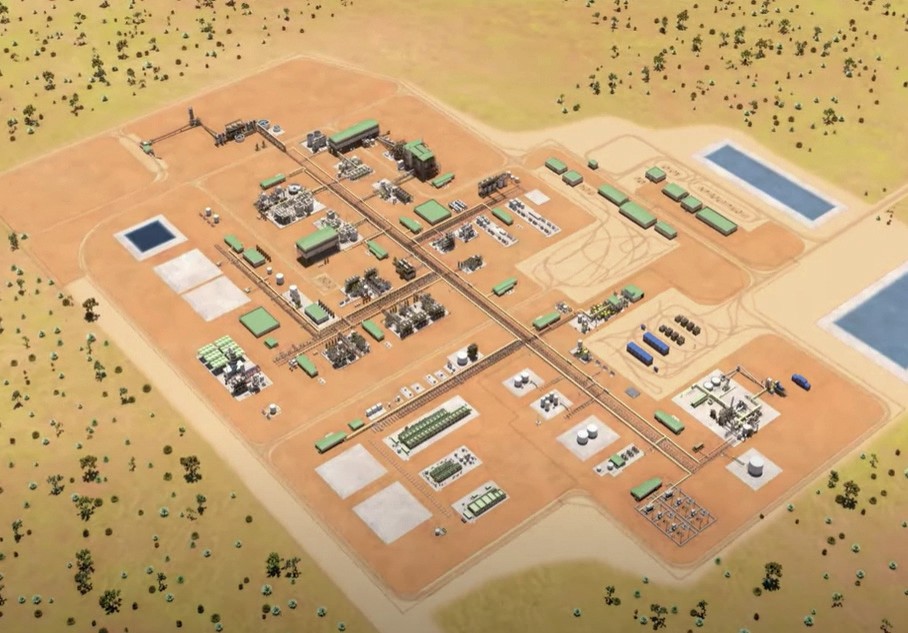
“With this project, we will assist in Arafura’s goal to be a trusted global leader and supplier of choice for sustainably mined and processed rare earth products. With each year of plant operation, more than 700 tonnes of SO2 will be converted to usable sulphuric acid rather than emitted into the atmosphere.” Chemetics Inc., President Andrew Barr said.
“Arafura Rare Earths is very pleased to be working with Chemetics Inc as a global leader that is able provide the Nolans Project with highly efficient, robustly engineered and low emission sulphuric acid technology. This sulphuric acid plant represents a key component in achieving our sustainability goals,” General Manager Projects, Stewart Watkins, said.
UNITED STATES
MECS wins two contracts for electronic grade acid production
MECS, a subsidiary of Elessent Clean Technologies, has been selected to supply propriety technology and equipment to clients in the US and Taiwan to enable production of high-purity electronic-grade acid for the global market. Governments from several countries around the world have implemented incentive programs for electronic-grade acid production. Tax credits, grants, and research and development investment are some of the ways in which acid manufacturers are being rewarded for contributing to the supply chain.
“The semiconductor industry is experiencing growth we have not seen in decades. Because of our robust history in the sulphuric acid industry, using MECS® technologies and equipment to produce high purity electronic-grade acid feedstocks provides assurances our competitors cannot replicate. We are at a critical point in high purity sulphuric acid production. With high demand around the globe, and the passage of the CHIPS Act in the United States, we are excited to help meet the needs of the expanding global marketplace and to assist the US in being more competitive within that space.” said Eli Ben-Shoshan, CEO, Elessent.
Work begins at Thacker Pass lithium project
Lithium Americas Corp. has begun construction at its 100%-owned Thacker Pass lithium project in Humboldt County, Nevada, following the receipt of notice to proceed from the Bureau of Land Management. Thacker Pass is targeting 80,000 t/a of battery-quality lithium carbonate production capacity in two phases of 40,000 t/a respectively. Phase 1 production is expected to commence in the second half of 2026.
EXP Global Inc. has been awarded the contract for the engineering, procurement, construction support, commissioning and start-up services for the project’s sulphuric acid plant. The plant will have a capacity of 3,000 t/d.
MECS, Inc. was awarded the contract for the technology license, engineering and equipment for their MECS® Heat Recovery System, to harness waste heat to generate steam which will subsequently be converted into carbon-free electricity for the processing plant.
“Starting construction is a momentous milestone for Thacker Pass and one we have been working towards for over a decade,” said Jonathan Evans, President and CEO. “We are excited about the prospect of generating economic growth in Northern Nevada and playing a major role in the domestic lithium supply chain for electric vehicles.”
MECS says that, when combined with more traditional means of energy recovery within sulphuric acid plants, HRS™ enables a plant to utilise up to 95% of the process heat it generates internally as steam, which can be converted to electricity that is either employed to power the facility or sold to a neighbouring industrial complex or the local power grid. Through the production of both high-pressure and intermediate-pressure steam, HRS™ technology can prevent up to the equivalent of 100 tonnes of carbon dioxide emissions over the course of a year for each t/d of acid that is produced by the plant.
The State of Nevada has become a critical supplier of lithium within the US as the nation’s leaders make plans to reduce reliance on imported lithium. As the pivot away from fossil fuels becomes increasingly urgent, consumers are buying more electric vehicles (EV) to support the energy transition which requires lithium, and other raw materials like nickel and cobalt, for the production of EV batteries.
“We are thrilled to be working with Lithium Americas and EXP on this project. It is very exciting to be part of such a monumental project in the United States that has the potential to make a global impact on the battery metal supply chain. Throughout the planning process our team has been cognizant of environmental preservation, and we want Thacker Pass to be the prototype for environmental stewardship for other projects of this nature. We have worked closely with Lithium Americas to ensure maximum efficiency so they can meet industry growth needs while prioritizing carbon reduction initiatives.” said Eli Ben-Shoshan, CEO, Elessent.
INDONESIA
New smelter off-gas acid plant
Indonesian mining company PT Amman Mineral Industri (AMIN) says that it will partner with Elessent Clean Technologies for the provision of a new smelter off-gas MECS® sulphuric acid plant equipped with DynaWave® wet gas scrubbing technology. The new plant will be constructed in Sumbawa, Nusa Tenggara Barat, Indonesia with anticipated start-up in 2024. Over the last few years, Indonesia has become a critical region for the battery metal marketplace. As the electric vehicle revolution sweeps the globe, consumers are procuring more vehicles to support energy transition. Battery metals are essential for the production of electric vehicles, as well as numerous other electronics, and producers are turning to Indonesian mining operations for access to materials.
“AMIN chose Elessent for their reputation in meeting environmental regulations and the high reliability of their technologies. Using MECS® acid plant design and its incorporated technologies, our new plant will expectedly meet site-specific environmental, cost and operational goals, as well as environmental requirements,” said Mr. Anil Upadhyay, Copper Smelter Project Director, AMIN.
BRAZIL
Award for sulphur-burning acid plant
Brazilian chemical maker Unigel RI, one of Latin America’s largest chemical companies and Brazil’s top manufacturer of nitrogen fertilizers, has contracted with the MECS subsidiary of Elessent Clean Technologies for the construction of a new sulphur-burning acid plant to displace the import of sulphuric acid for their downstream chemical processes. The new plant will be constructed in the coastal state of Bahia. With sustainability as a core value, Unigel’s new plant will also be used to generate utility steam that will provide reliable and carbon-free power throughout their industrial complex. Start-up of the plant at the Bahia, Brazil site is expected to take place in the first half of 2023.
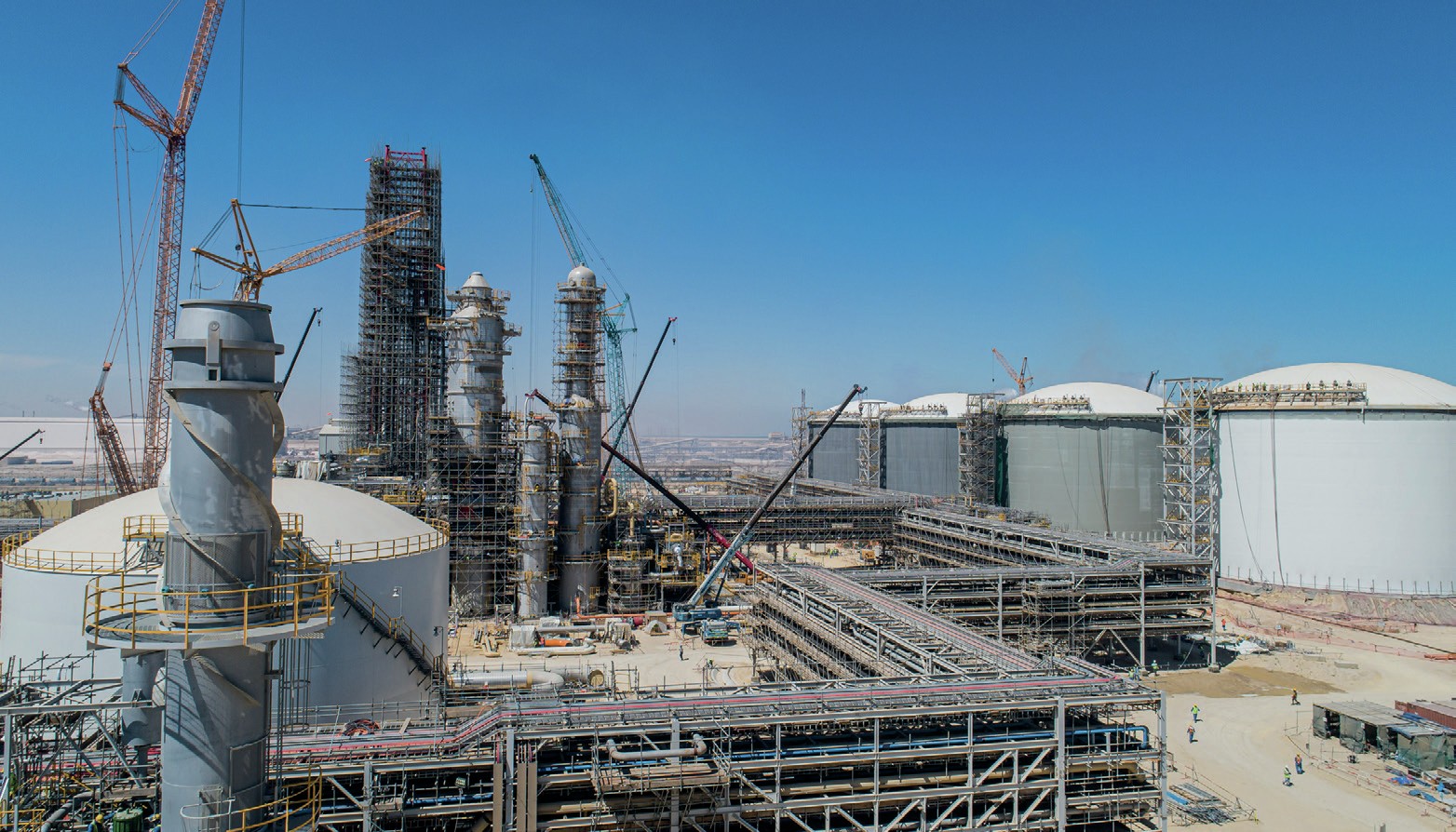
The project also contributes to the challenges of decarbonising the production chain, since the steam produced in the plant will be carbon free, reducing greenhouse gas (GHG) emissions. This is in addition to other environmental initiatives promoted by Unigel, including Brazil’s first green hydrogen plant which Unigel is pioneering.
The process design for Unigel incorporates state of the art products and technologies, such as GEAR® catalyst for ultra-low emissions and high conversion, Brink® AutoDrain™ technology for operational efficiency, as well as UniFlo® distributors, acid coolers and acid piping.
“The design and construction of this new sulphuric acid plant, the first for Unigel and the first for Brazil in over 15 years, is an integral step to enabling more streamlined operations and positioning Unigel as a key player in the widespread distribution of sulphuric acid to consumers. Unigel operates on four major pillars: sustainability, quality, safety and reliability; and we knew we needed the market leader for this project. The MECS® technology, products and equipment used in the plant’s design… will ensure our commitment to our customers while ESG practices are met.” said Unigel CEO, Roberto Noronha Santos.
SAUDI ARABIA
Metso Outotec signs MoU with Ma’aden for sustainable phosphogypsum processing
Metso Outotec and thyssenkrupp Uhde have signed a memorandum of understanding with Ma’aden for developing a novel circular concept to improve the sustainability of Ma’aden’s phosphate operations. The aim is to design a ground-breaking integrated complex for processing of phosphogypsum waste from phosphoric acid production, to reduce the amount of solid waste and allow the capture of CO2 emissions. The new circular process will be incorporated into Ma’aden’s phosphate operations to support the company in achieving their ambitious sustainability goals aligned with the Kingdom’s objectives.
“We are honoured to be part of this unique initiative. Decarbonisation and circularity are relevant for all industries, and the new concept to be developed for phosphogypsum processing will be a major step forward in the fertilizer industry, contributing to efforts limiting global warming,” commented Hannes Storch, Vice President for Metals and Chemicals Processing at Metso Outotec.
Ma’aden names Phosphate 3 project partners
Ma’aden has selected Worley and JESA International S.A. (JESA) as engineering and construction contractors for the initial phase of its Phosphate 3 mega project. The company issued a preliminary agreement (notice of award) to both partners on 1st February, covering engineering, procurement, and construction management (EPCM) services for phase 1 of the project.
“The parties expect to work towards a definitive agreement for the … EPCM contracts in the next few months,” Worley said in statement.
These EPCM contracts cover the design and construction of new process plants in the industrial cities of Wa’ad Al Shamal (WAS) and Ras Al-Khair (RAK) in Saudi Arabia. Both cities will form part of an integrated production complex that is expected to produce up to 1.5 million t/a of phosphate fertilizers, once operational. Worley will provide in-Kingdom services for the project from its offices in Saudi Arabia and India. JESA, meanwhile, will provide out-of-Kingdom services, executed by its offices in Morocco.
“We are pleased that Worley has been selected for providing services to Ma’aden’s Phosphate 3 development program that is expected to make Saudi Arabia one of the leading phosphate fertilizer exporters worldwide,” said Chris Ashton, Worley’s CEO.
FINLAND
Metso Outotec shareholders to vote on name change
The board of directors of Metso Outotec has proposed to the company’s upcoming Annual General Meeting that the current name of the company is changed to Metso Corporation, on the grounds that the integration of Metso and Outotec, which became effective on July 1st, 2020, is completed, and the company’s current strategy focuses on growing a strong unified company that builds on the long history and legacy of its businesses to create significant customer value.
CZECH REPUBLIC
Nuberg awarded sulphuric acid plant project
Nuberg EPC says that it has been awarded a 550 t/d sulphuric acid plant project on an EPC basis in Neratovice, Czech Republic. The project is owned by Spolana s.r.o, a leading chemical manufacturer located on the Elbe riverbank, and one of the largest chemical companies in the Czech Republic, the country’s only manufacturer of PVC and caprolactam, as well as ammonium sulphate and sulphuric acid. Nuberg will be executing this project based on the latest double conversion double absorption (DCDA) technology. The plant is expected to be delivered in three years. Acid pro duced by the plant will be used for petrochemical and fertilizer based applications. It will also be used in mining and processing of some ores and minerals, manufacturing batteries, and etching surfaces.
A. K. Tyagi, MD, Nuberg EPC said, “This undertaking illustrates Nuberg’s competency of combining intelligence and knowledge in terms of Engineering aspects. It is a pleasure that Spolana has chosen our EPC services for this project.”
CHILE
Copper output falls on higher input prices
A new report by state copper commission Cochilco indicates that direct copper mining costs in Chile increased from $0.134/lb in 3Q21 to US$0.169/lb in 3Q22 at 19 of the 22 local operations that represent 93.9% of national production. The biggest increases related to smaller operations, with the main drivers being price rises for diesel fuel of 85%, of electricity by 10% and freight for concentrates and insurance by 36%. The sulphuric acid price increased 142% due to the Russia-Ukraine war and the consequent oil refining stoppage and operational difficulties at Chinese smelters, Cochilco said. The average price of this key material for hydrometallurgical operations was $220-225/t last year. As a consequence, copper production fell 252,000 t/a to 3.6 million t/a. Collahuasi, controlled by Anglo American and Glencore accounted for the biggest drop, 11%, from 480,000 t/a to 428,000 t/a. Output at state copper miner Codelco’s El Teniente and Chuquicamata assets fell by 7.5% and 5.1% from 342,000 t/a to 291,000 t/a and from 239,000 t/a to 200,000 t/a respectively. Antofagasta Minerals’ Los Pelambres registered 4.9% lower output, down to 193,000 t/a from 259,000 t/a in 2021.
BULGARIA
Pirdop sees small fall in acid output
German copper producer Aurubis says that the cathode output of its smelter in Pirdop, 80km east of Sofia, Bulgaria, increased by 7% year on year to 58,000 tonnes in the first quarter of its fiscal year 2022/2023, which started on October 1st. Copper concentrate throughput at Pirdop decreased by 1% yearon-year to 369,000 tonnes in the October-December period of 2022, but in general the smelter recorded a strong performance similar to the previous year, Aurubis said in an interim financial statement. Sulphuric acid output at the smelter amounted to 367,000 tonnes in the review period, also down 1% on the prior-year first quarter.
SERBIA
Restart for Zijin Bor Copper after smelter overhaul
Zijin Bor Copper, the Serbian unit of China’s Zijin Mining Group, has restarted its flash smelting furnace following a $340 million overhaul of its production facility in Bor, according to the Serbian energy ministry. The reconstructed smelter will use clean natural gas instead of fuel oil, coal and other highly polluting fuels, and the concentration of powdery substances will not exceed five milligrams per cubic metre, bringing the smelter in line with EU environment protection standards.
“When the smelter starts working, we will produce 180-200,000 t/a of cathode copper of high purity, about three tonnes of gold and 700,000 t/a of sulphuric acid. The value of annual output will be more than $2 billion,” the ministry quoted CEO of Zijin Serbia, Djin Siming, as saying in a press release.
OBITUARY
Bo Levander, founder of ChemTrans, passed away on 5th February 2023. He worked in the sulphuric acid industry all his life, beginning in the late 1960s at Boliden in Stockholm. In 1971 he moved to Switzerland, where he was responsible for the Boliden office in Zug. Ten years later, in 1981, he left Boliden and struck out on his own, founding ChemTrans AG, also based in Zug. Two years later, the company sold its first parcel of sulphuric acid; 85,000 tonnes from Spain to Tunisia, and in 1987 it purchased its first ship, the 8,700 dwt MT CT Star. By 2005, the company had grown to be one of the largest shippers and traders of sulphuric acid, with 600,000 tonnes of acid shipped and a turnover of 73 million Swiss francs.
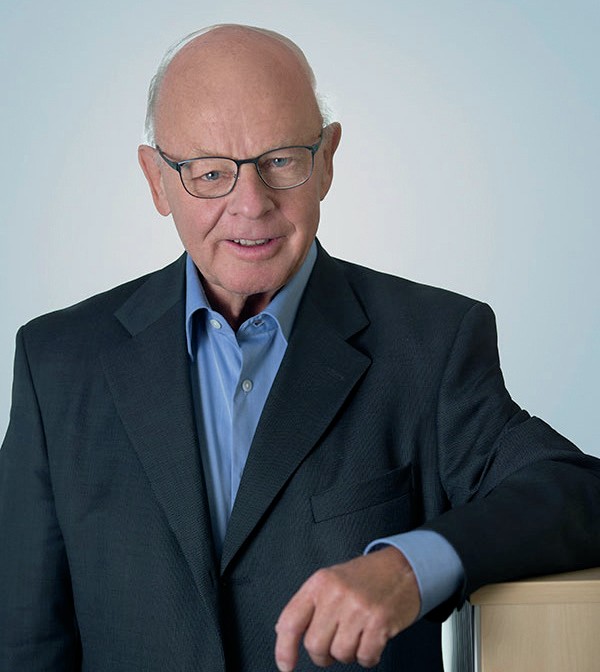
Bo is survived by his son Henrik, who has been CEO of ChemTrans since 1995. Henrik adds: “Bo was a very respected and esteemed person in the sulphuric acid world, and a light for all of us at ChemTrans. We will continue shining his light by carrying it within us in our own lives. Death means to say goodbye, but never to leave a loved one behind.”
GERMANY
Trafigura buys Ecobat Stolberg lead smelter
Swiss-based commodity trader Trafigura says it has completed its purchase of Ecobat Resources Stolberg (ERS) multi-metals processing plant in Germany, and plans to bring it online in the coming weeks to supply European battery producers. The Stolberg plant will be operated and managed by Nyrstar, which Trafigura owns, and the Stolberg business will be renamed Nyrstar Stolberg GmbH, Trafigura said in a news release. The plant was among several industrial sites damaged by massive flooding in Germany’s west and south last year and has suffered months of lost production. It has the capacity to produce 155,000 t/a of lead, and more than 100 different specifications of lead alloys as well as 130,000 t/a of sulphuric acid.
CANADA
First Phosphate looking at long term offtake agreement with Prayon
Canada-based First Phosphate Corp has entered into a collaboration agreement with Belgian producer and technology provider of purified phosphoric acid Prayon SA. First Phosphate and Prayon have committed via memorandum of understanding to explore the potential of a long-term offtake agreement for phosphate concentrate to be produced by First Phospahte in its Quebec mining operations. The agreement also allows First Phosphate to be able to toll process its phosphate concentrate to battery-grade purified phosphoric acid at Prayon’s facilities. The partners also plan to explore the development of a facility to produce lithium ferro-phosphate (LFP) -grade phosphoric acid and even active LFP cathode material in Quebec. Prayon’s technology is used to produce phosphoric acid at 130 sites worldwide. In addition, Prayon operates five of its own plants.
Commenting on the signing of the MoU, Marc Collin, Prayon’s Chief Technology Officer said: “We are excited to partner with First Phosphate and test our recognised technologies for the production and processing of high quality phosphoric acid to supply the LFP battery industry in North America. The opportunity to partner with First Phosphate is an important step in our global diversification initiatives.”
MOROCCO
Phosphate exports down 12% in 2022
Morocco’s phosphate and derivatives exports reached $11.3 billion last year, according to data from the country’s customs service. The number represents an increase of 43.9% compared to a year earlier, and the phosphate sector topped the list of Morocco’s best-exporting sectors in 2022, ahead of the automotive sector. However, the rise was mainly due to an increase in price of 74.4% over the year, and the actual physical quantity of phosphate fertilizer exported actually fell by 11.8% compared to 2021. Morocco holds 75% of the world’s phosphate rock reserves. OCP, which manages those reserves, announced a turnover of $8.32 billion throughout the first nine months of last year, up 55% on the same period of 2021. The group announced last year its plan to increase fertilizer input by 10% to meet the rising global demand for fertilizers. The company’s decision comes amid the Ukraine-Russia war, which created uncertainty in the international fertilizer supply chain.
INDIA
Reopening for Sterlite Copper smelter?
After almost five years of closure, the prospects of a reopening of the Vedanta group’s Sterlite Copper smelting plant in Thoothukudi look a little brighter. There has been a groundswell of popular opinion in the local community on behalf of villagers and business owners in the city badly impacted by the closure of the smelter, and even a protest in New Delhi. According to the Pro-Sterlite Plant Federation, 600 truck owners, and 13,500 truck drivers have been left with no source of income, as well as 5,000 workers engaged in repair shops, hotels, and tea and coffee shops catering to the lorry industry. Sterlite has also gained some credit from producing medical oxygen to assist local hospitals during the covid pandemic, and points out that rather than a fall in SO2 levels in the vicinity, there has actually been a rise since the closure, supporting Sterlite’s claim that the SO2 pollution it was blamed for is actually coming from local coal-fired power plants. The shutdown in 2018 followed violence that broke out among anti-Sterlite protests over alleged environmental degradation caused by the plant. Fourteen rioters were killed by police.
The plant’s capacity of 400,000 t/a of copper represented almost 40% of India’s output. The Indian Supreme Court is currently hearing Vedanta’s petition to overturn the Tamil Nadu state government order to close the plant.