Nitrogen+Syngas 383 May-Jun 2023
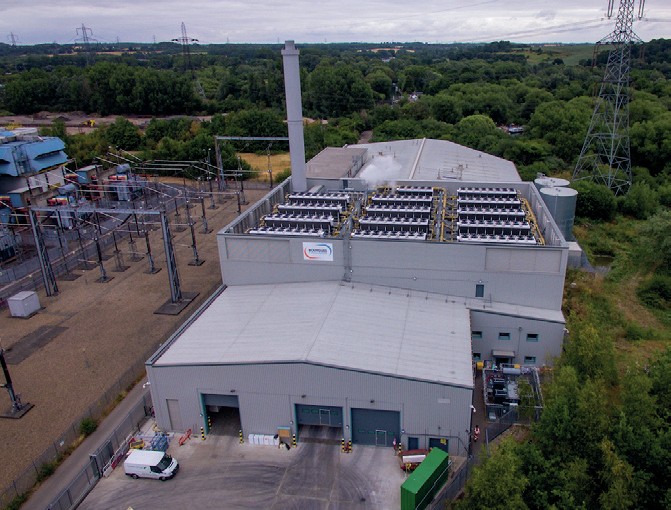
31 May 2023
Challenges for gasification technology
GASIFICATION
Challenges for gasification technology
Gasification, particularly of waste and biomass, is seeing interest as sustainable sources of syngas. But there are both technical and commercial challenges to wider adoption.
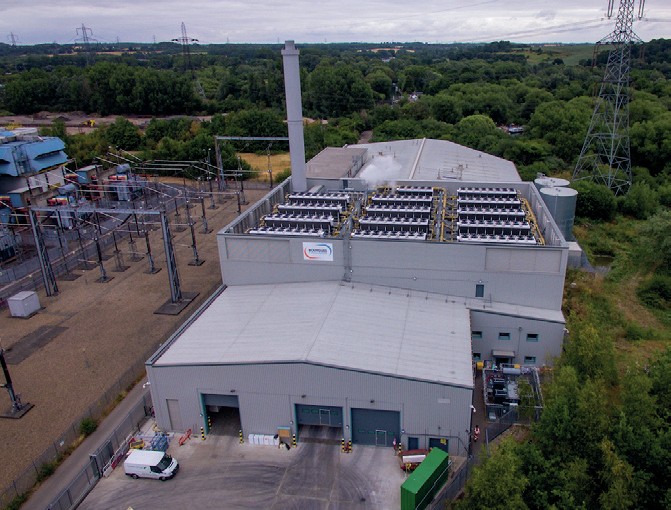
As the world seeks more sustainable ways of producing the everyday chemicals that we have come to rely upon, from fertilizers such as ammonia and urea to methanol, fuels and polymers, generation of synthesis gas from unconventional sources has become a particular area of interest. Many agricultural processes generate waste biomass, and major municipalities generate large volumes of domestic waste which cannot be easily recycled.
In both cases, gasification of these waste streams has been seen as a more sustainable alternative way to generate usable synthesis gas. However, waste and biomass gasification units have sometimes had an unhappy history with a number of failed and abandoned projects, especially in the UK.
Gasification
Gasification involves feeding finely pulverised waste material into a high temperature (>700°C) gasifier with a restricted oxygen flow to partially oxidise carbon components into CO and H2 over a catalyst bed. The catalyst bed may be fixed, or fluidised using the gas flow, or use an entrained flow where the feed and oxidant/steam are co-fed together into the gasifier, generally at higher temperatures (1,200-2,000°C). Fixed bed gasifiers are mechanically simple but suffer from poor mixing and heat transfer and are not widely used. Entrained flow gasifiers generate high quantities of ash which deposits on the gasifier walls depending upon the feedstock. Depending on the operating conditions of the gasification process, the molten ash deposits often solidify, causing plugging and the blockage of critical parts of the gasifier thereby hindering process efficiency. Fluidised bed gasifiers are the most efficient and widely used, but can produce high particulate levels which can cause erosion.
Fluidised bed gasifiers are operated at high pressure, which can result in operational complications such as defluidisation from particle agglomeration, particularly when agricultural crops and wastes are used as feedstock in the gasification process. This is because agricultural crops and wastes contain an increased amount of ash/alkali and, the alkali content of ash (sodium and potassium) can form low-melting mixtures with silica in the sand which is the most common bed material in an FBG process. Under this condition, agglomeration and sintering will occur, triggering the formation of a thin sticky substance around the bed particles with an instant loss of bed fluidisation. This can be avoided by using aluminium oxide or magnesium carbonate instead of silica, but this increases the cost of the process.
Gas cleaning
One of the issues with biomass and gasified municipal waste is the wide mix of components that can be found in the gasified waste stream including, but not limited to, ammonia, nitrous oxides, sulphur oxides and hydrogen chloride, BTX (benzene/toluene/xylene) and heavy metals. These can be treated by suitable gas cleaning processes. HCl, H2 S and SO2 are highly soluble and can be removed via water scrubbing. Ammonia can be decomposed using iron, nickel or ruthenium-based catalysts, but again these all add cost and complexity to the process.
Another major problematic component is tar. This is a mixture of polyaromatic hydrocarbons which exist as a gas at the high temperatures of the gasifier, but which at lower temperatures condense and can deposit in downstream equipment, blocking and fouling pipes, valves and turbines. Compared to a fixed bed gasifier, fluidised bed gasifiers, especially circulating fluidised bed reactors, have high gas speeds to keep the catalyst bed fluid, leading to shorter residence times for tar molecules in the reactor and lower conversion. Simple filtration of tar blocks the pores of a filter and creates a pressure drop. Tar also contains toxic chemicals, making its handling and disposal a health and environmental issue. The best way to tackle tar formation is to oxidise it to lighter components which remain as gases. This can be done via catalytic conversion. Different types of catalysts have been proven to be active for tar and ammonia decomposition. However, the utilisation of catalyst in the primary bed is problematic because it deactivates rapidly due to the fouling of ash and carbon on the surface.
Teething troubles?
Some of the initial enthusiasm for waste and biomass gasification has been tempered in the past few years by a number of high profile project failures, particularly in the UK, which had bet heavily on the technology. Both process and economic issues remain, with tar and ash formation remaining technical challenges still yet to be fully overcome. However, the technology continues to develop and has been operated successfully in some installations, and may yet hold the key to dealing with the volumes of waste that our society generates.