Fertilizer International 514 May-Jun 2023
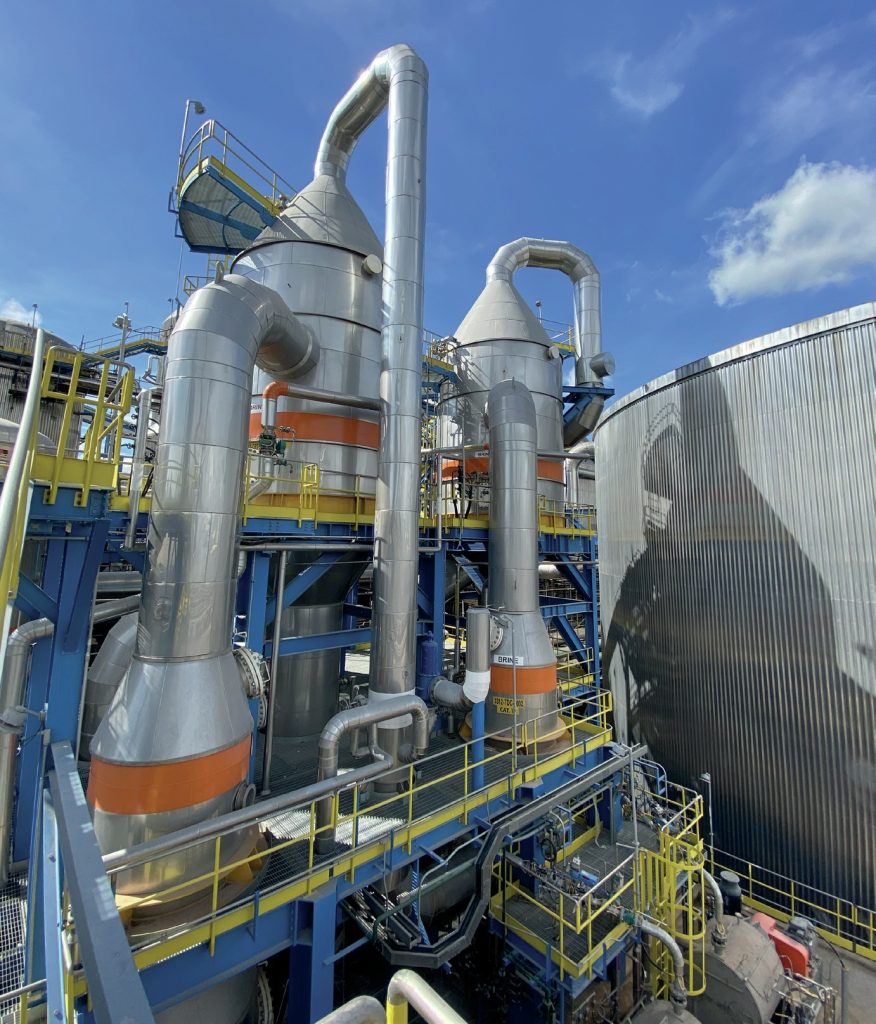
31 May 2023
Crystallisation and evaporation in fertilizer production
SUSTAINABLE PROCESS TECHNOLOGIES
Crystallisation and evaporation in fertilizer production
Evaporation and crystallisation are widely used throughout the fertilizer industry. These powerful production processes are helping fertilizer manufacturers diversify their product portfolios, improve profitability and meet sustainability goals.
VEOLIA WATER TECHNOLOGIES
Crystal clear advantages
Evaporation and crystallisation have many fertilizer industry applications.These include the manufacture of fertilizer products from primary raw materials (Fertilizer International 477, p56).
Their ability to economically recover by-products for fertilizer use – from other industrial processes or previously discarded waste streams – is also valued. This helps fertilizer producers control manufacturing costs and meet sustainability and circular economy objectives by increasing resource efficiency and improving waste management (Fertilizer International 496, p50).
Such advantages are clearly shown by the production of monoammonium phosphate (MAP), the most popular type of water-soluble fertilizer consumed globally. Crystallisation enables high quality MAP to be produced from low-grade phosphoric acid feedstocks. This is beneficial as poor-quality phosphoric acid, is classed as waste product and was previously unusable without costly purification.
It is vital that fertilizer raw materials should not go to waste, given their growing scarcity and the energy used in their extraction and processing. Fortunately, the adoption of evaporation and crystallisation by fertilizer producers now make this possible – due to the ability of these technologies to treat and recover waste streams and recycle low-grade feedstocks.
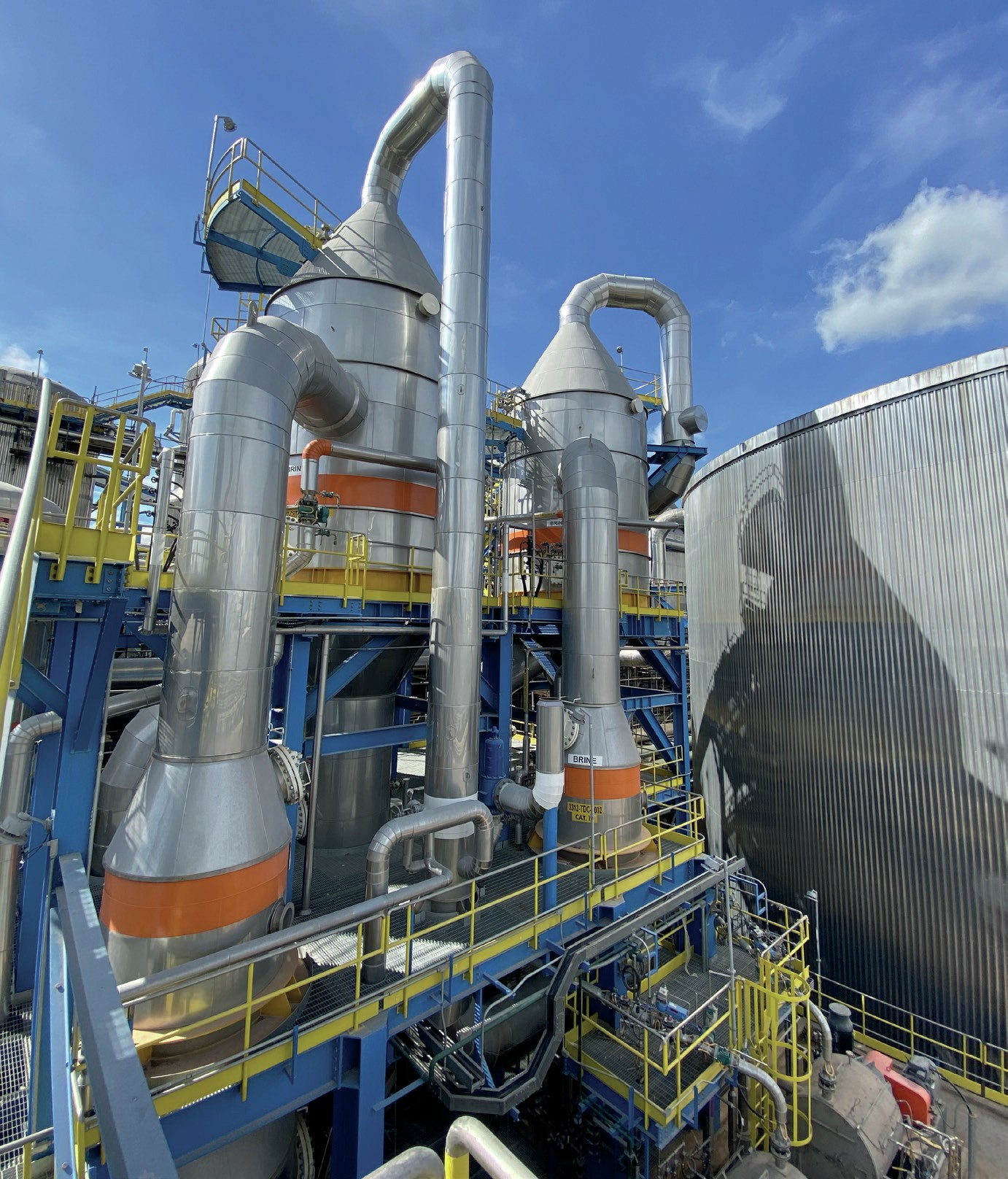
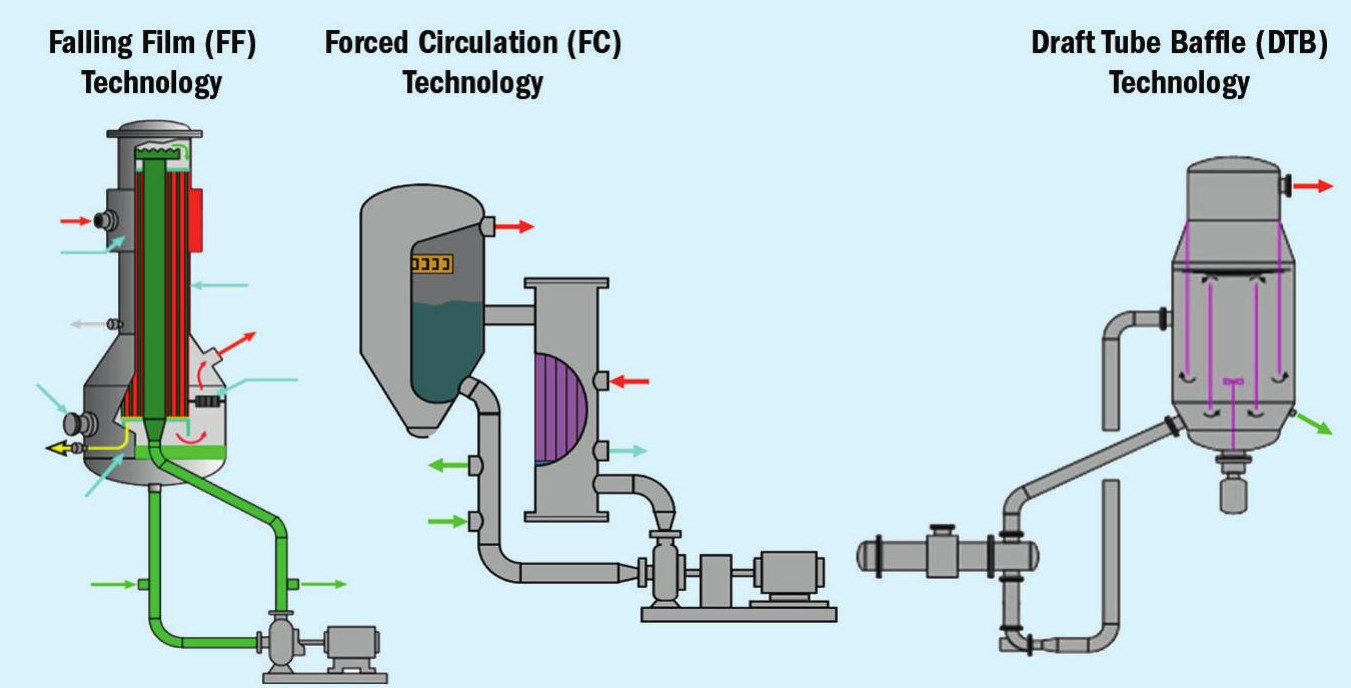
Process selection
Evaporation and crystallisation describe a range of different process options. These include:
- Standard evaporation
- Evaporative crystallisation
- Cooling crystallisation
- Reactive crystallisation.
Process selection is influenced by the type and physical behaviour of raw materials, the desired quality of the end-product, and project-specific criteria.
Evaporation and evaporative crystallisation: In this process, the objective is to increase the concentration of dissolved salts via evaporation. This involves the removal of a solvent (typically water vapour) to concentrate the solute (the desired product). Evaporation is generally used in the fertilizer industry to preconcentrate dilute streams prior to crystallisation.It is also widely used to concentrate phosphoric acid.
Cooling crystallisation: Compounds whose solubility is highly temperature-dependent can be easily crystallised in cooling crystallisers. Crystallisation occurs when a hot saturated solution is cooled until supersaturation is reached. This is generally achieved by flash cooling water vapour under vacuum. Crystallisation is largely initiated by cooling the solute, although some concentration also occurs due to the removal of water vapour. This type of crystallisation is prevalent in potash production.
Reactive crystallisation: In this process, a crystalline product is formed by the chemical reaction that occurs when two compounds are mixed together. This type of crystallisation is used to manufacture ammonium sulphate from ammonia (either gaseous or liquid) and sulphuric acid, for example, and to produce monoammonium phosphate and diammonium phosphate (MAP/DAP) by reacting ammonia with phosphoric acid. Relatively pure reactants are generally required – although there is increasing interest in using less costly and lower purity raw materials or waste streams instead.
Equipment options
The most common types of equipment installed in fertilizer production (Figure 1) are as follows:
- Falling film evaporators: These are typically used to concentrate a solution in non-scaling applications. They are often used to preconcentrate a stream prior to a separate crystallisation process – and can turn highly soluble salts such as calcium chloride into high concentration solutions.
- Forced circulation crystallisers: These are used for processes where large crystals grow easily or where the particle size distribution of the product is not critical. Forced circulation crystallisers are often used for sodium chloride crystallisation in potash recovery from sylvinite deposits. They are also known as a ‘mixed suspension, mixed product removal’ (MSMPR) crystallisers because the slurry is mixed uniformly throughout the system.
- Draft tube baffle (DTB) or HPD partitioned internal circulation (PIC™ ) crystallisers: These crystalliser types are in widespread use in the fertilizer industry – especially in those production processes requiring both a narrower crystal size distribution and a larger crystal size. Common applications include potash, ammonium sulphate and MAP/DAP production.
- HPD Growth™ crystallisers: Also known as Oslo type or ‘classified suspension, classified product removal’ (CSCPR) crystallisers, these typically involve the circulation of a crystal slurry and the classification of crystals according to size using a fluidised bed. The advantages of HPD Growth™ units have been demonstrated in many applications – and include the production of potassium chloride (high-purity and fertiliser-grade) and ammonium sulphate (highpurity and by-product manufacture).
Process plant configuration
There are many different ways to configure evaporation and crystallisation equipment (Figure 2) to ensure that project economics and process efficiency are both maximised. Among the design factors that must be considered are:
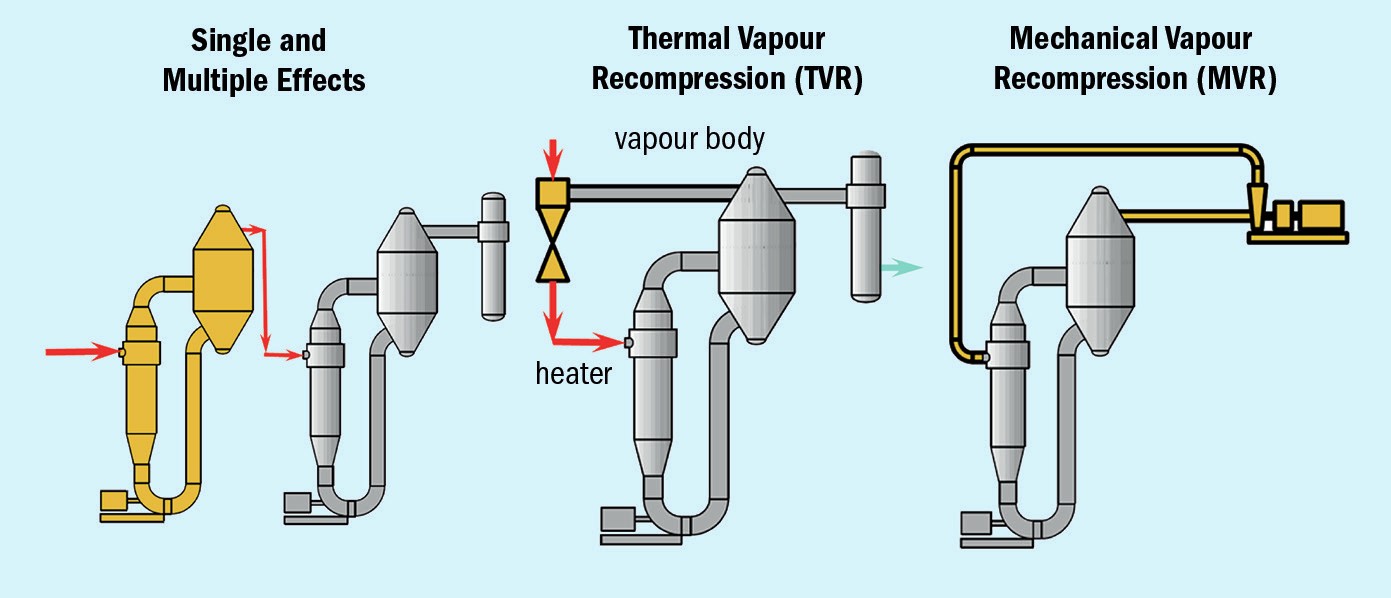
VEOLIA SUCCESS STORIES
Monoammonium phosphate (MAP)
Alkimia Group is a leading Tunisian chemical company specialising in the production of phosphate salts for industrial applications. The group has been able to diversify and generate new revenue streams from a new 25,000 t/a capacity monoammonium phosphate (MAP) plant (Fertilizer International 496, p50). The new manufacturing line exports this added-value fertilizer product from Gabes, Tunisia, to agricultural growth markets elsewhere in Africa.
Alkimia’s new MAP plant, designed and delivered by Veolia, integrates two crystallisation stages with centrifugal separation, drying, cooling, and screening systems. The plant consumes merchant-grade phosphoric acid (MGA, a relatively low-grade acid) and ammonia to produce fully water-soluble, high purity (99 wt % minimum) MAP crystals with very low insoluble content (below 0.2 wt %). A series of laboratory tests carried out by Veolia were used to simulate and develop the process flowsheet and determine the correct plant design.
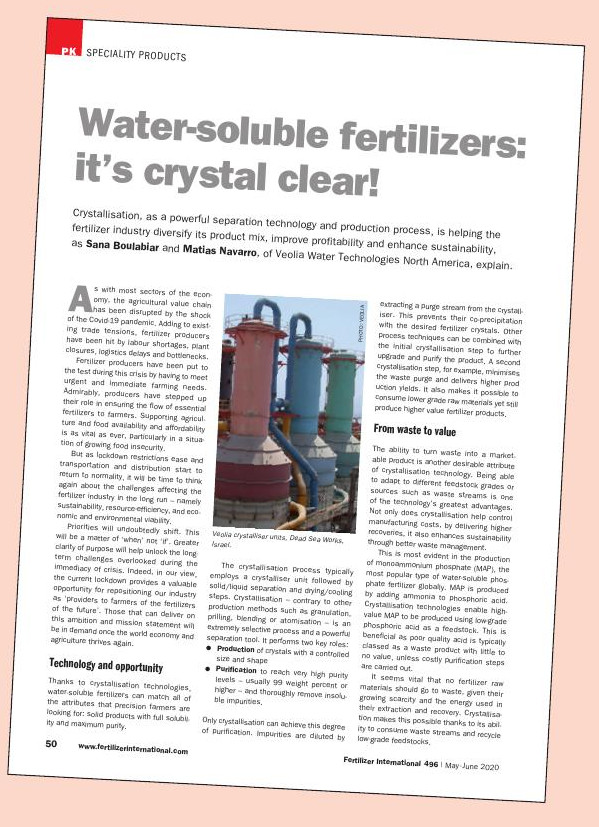
Potassium sulphate (SOP)
North American crop nutrient and salt producer Compass Minerals needed to expand potassium sulphate (SOP) production at its Ogden plant in Utah in the United States. Veolia successfully integrated its HPD® PIC™ draft tube baffle crystalliser unit into the existing plant (Fertilizer International 496, p50). This converts a brine feed containing schoenite into a high-purity SOP product, marketed by Compass as Protassium+® . Veolia simulated and developed the process at its research facility near Chicago before validating the design. The newly installed equipment also enabled Compass Minerals to significantly reduce its water consumption, being more efficient at recycling waster than the existing SOP plant.
High quality SOP from wastewater
Veolia’s HPD® crystallisation technology is capable of manufacturing high-quality water-soluble SOP from a range of different feedstocks. One innovative production option is to manufacture SOP from the wastewater generated at pulp and paper mills (Fertilizer International 510, p42).
In this process, glaserite (a double salt of SOP and sodium sulphate) is initially recovered via a black liquor ash treatment system and then converted into high-quality SOP crystals for fertilizer use. This two-stage crystallisation process uses Veolia’s ECRP™ system to recover the SOP from ash treatment purge. The system:
- Delivers rapid operational payback
- Reduces sulphate levels in mill effluent
- Returns potassium back to the forest via the production of SOP fertilizer – creating a closed nutrient loop
- Saves on the cost and usage of chemical consumables such as caustic and sodium sulphate.
-
Utility availability and costs (steam, power and cooling water)
-
The size of capital equipment
-
Installation costs
-
Metallurgy and process requirements
-
Environmental constraints.
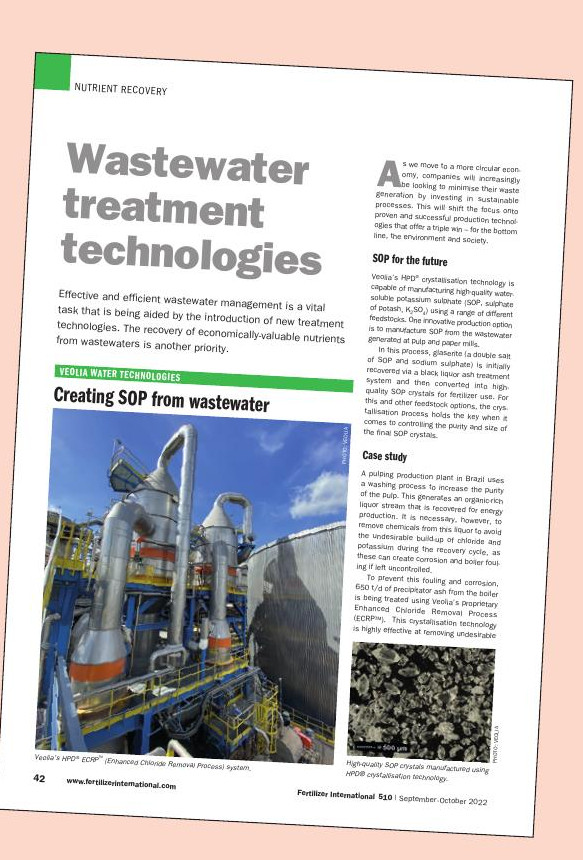
In steam-driven systems, the heat present in steam is used to concentrate a solution in heater tubes via evaporation. Energy efficiency can be improved with multiple-effect evaporation (MEE). This process uses the vapour generated as a heat source to evaporate additional water. Vapour generation occurs at progressively lower pressure in each additional effect. This configuration greatly increases the steam economy, i.e., the amount of water evaporated for each unit of steam used.
Steam consumption can also be reduced by using thermal vapour recompression (TVR). This configuration uses high pressure steam to compress the vapour generated in the evaporator to an intermediate pressure which is usable in the heater.
Mechanical vapour recompression (MVR) uses electrical energy to drive the evaporation in lieu of steam. The water evaporated is compressed using a mechanical vapour compressor. The resulting high-pressure vapour is then used in the heater to drive the evaporation. MVR has a much higher energy efficiency than a steam-driven system and is the most beneficial and practical option where steam or cooling sources are limited.
A multiple stage vacuum flash configuration is generally used for products that have an inverse solubility. These types of crystallisers use adiabatic cooling, i.e., evaporation under vacuum cools the liquor and the product precipitates as a result. This is the configuration typically used in KCl production.
Production objectives and process challenges
To develop or validate design parameters, bench or pilot-scale tests are generally an imperative. Ideally, these should be performed with the same feed solution that will be used by the full-scale commercial plant. The main process challenges in designing a commercial plant are:
- Production of high-quality product salts. Fertilizer products often need to meet specific crystal habit, size or purity requirements.
- Adaptation to environmental constraints, e.g., limitations on liquid wastes or other discharges to the environment, limited energy supply or cooling media supply etc.
- Valuable product recovery from waste streams or by-products.
- Heat integration and water balance optimisation. Some production processes, such as potash from solution mining, have large recycle flows and place very high energy demands on the system. It is vital for such systems to have a highly-integrated heat balance.
- Choice of construction materials. Because the feed or mother liquor is often at high temperature and contains high concentrations of corrosive compounds, a balance needs to be struck between the need for corrosion resistance and ensuring that the design remains cost-competitive.
Fertilizer production
The diverse range of fertilizers produced using evaporation and crystallisation technologies include:
- Ammonium sulphate: Crystals can be made from pure ammonia and pure sulphuric acid by reactive crystallisation or produced by evaporative crystallisation of a dilute ammonium sulphate stream.
- MAP/DAP: Monoammonium phosphate (MAP) and diammonium phosphate (DAP) can be made via reactive crystallisation using technical-grade phosphoric acid and pure ammonia. Opportunities also exist to make these products using less expensive green phosphoric acid or raffinate.
- Potash: Cooling crystallisation is used extensively in potash solution mining to generate potassium chloride (KCl, muriate of potash), and in conventional potash mining to improve potassium chloride grade. Many potash deposits contain sylvinite (a double salt of NaCl and KCl). Incorporating crystallisation equipment in processing plants – due to their ability to remove sodium chloride – can therefore be vital in potash recovery.
- SOP: Potassium sulphate (SOP) production methods often involve a crystallisation step. Interest in SOP production is rising due to unmet demand from cash crops such as tree nuts and tobacco. It also sells at a premium relative to potassium chloride.
- Nitrate fertilizers: Evaporation is used to concentrate ammonium nitrate and to produce products such as potassium nitrate and calcium nitrate.
- Phosphoric acid: Evaporation is used to concentrate dilute phosphoric acid into a marketable product or for onward use in phosphate fertilizer production.
Conclusions
Evaporation and crystallisation processes are prevalent in many commercial fertilizer production plants. New fertilizer production technologies continue to be developed in response to rising fertilizer demand and the decreasing availability of affordable raw materials. Evaporation and crystallisation play a key role in these emerging technologies. Research, bench-scale and pilot scale testing, and process development will also remain vital in bringing new applications to market.
GEA GROUP
Efficient and sustainable fertilizer production
- There is increasing market demand for water-soluble fertilizers (WSFs) for foliar applications, fertigation and NPK blends. For these value-added speciality products, the use of evaporation, stripping, crystallisation and membrane filtration units in manufacturing is ideal, as they can produce high-purity crystalline solids with the required shape and size characteristics (Fertilizer International 496, p45).
These production technologies can be harnessed to manufacture a wide range of fertilizer intermediates and end-products.
Evaporation and crystallisation – the essentials
Evaporation and crystallisation are chosen for a production process whenever:
- Removal of water or another solvent is required
- Concentration has to be increased
- Volume has to be reduced
- By-products or impurities need to be stripped or precipitated l Valuable, high-purity crystals are being manufactured.
The main process options include:
- Evaporation and evaporative crystallisation
- Cooling crystallisation
- Reactive crystallisation.
Equipment selection and plant design is influenced by many product- and process-specific factors. Customer requirements, notably site characteristics such as the energy source and its cost, play an equally important role in determining the process engineering design of an industrial plant.
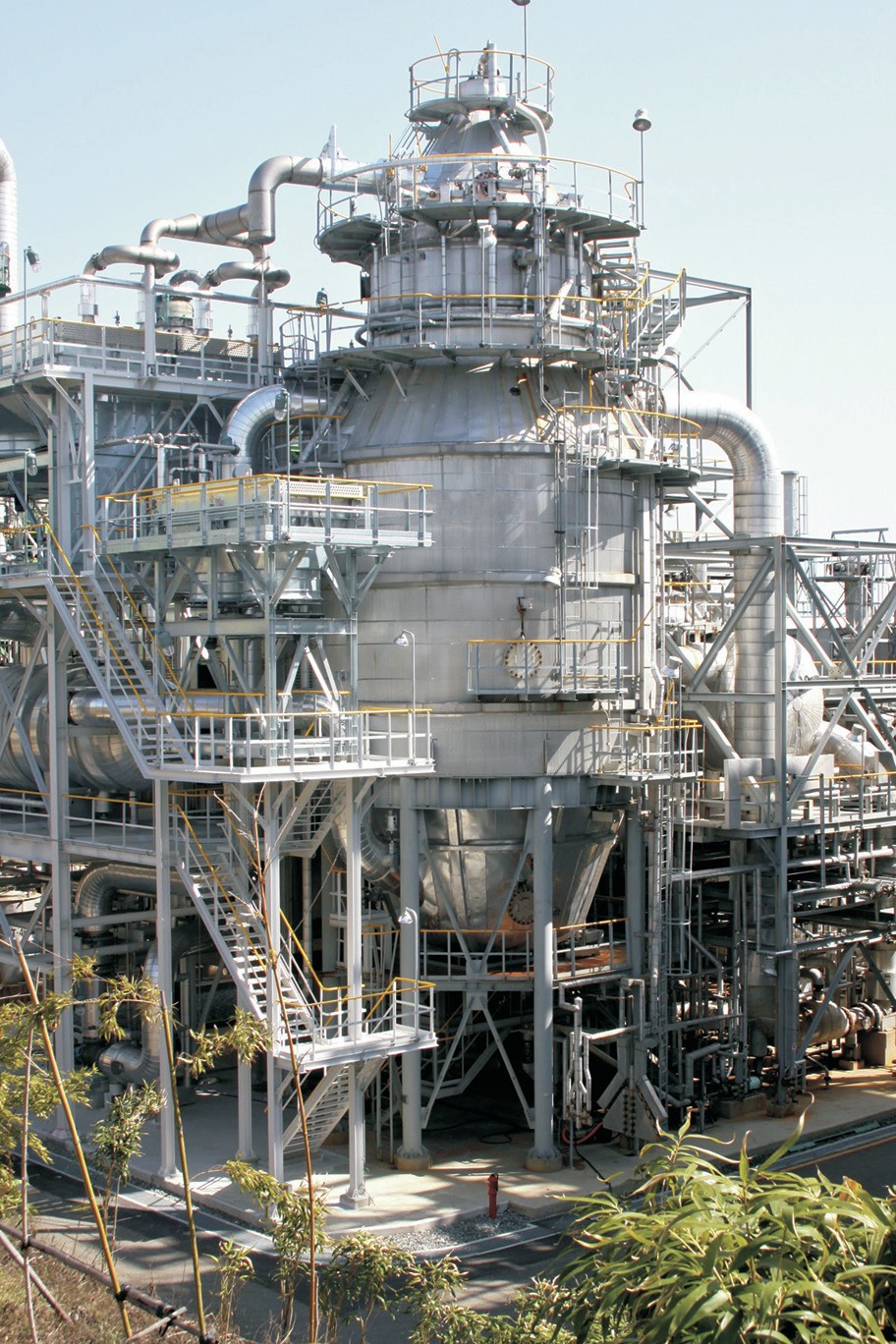
Crystallisation plants
Crystallisation plants need to be engineered to meet the customer’s product and process specifications (purity, particle size, operating time, etc.) while also minimising investment and operating costs. The crystalliser unit is selected from a wide range of available technologies (forced circulation, draft tube baffled, Oslo or flash cooling) to match individual product requirements. Achievable particle size can range from microns to millimetres, depending on the crystalliser type.
Evaporative crystallisation is usually chosen as a process when the solubility of the solute is largely independent of temperature, allowing supersaturation to be achieved by concentrating the slurry instead. A forced circulation system is often required to properly control supersaturation, suspension density and crystal breakage.
Vacuum cooling crystallisation, in contrast, is usually chosen when the solubility of the substance to be crystallised is strongly temperature dependent. Supersaturation is achieved by adiabatic cooling of the slurry under vacuum without a cooling surface and by avoiding encrustation.
For end markets with high quality standards, a recrystallisation stage can be added to improve the purity of the final product.
Evaporator types
Several designs of evaporators are available to satisfy a wide spectrum of process requirements. They include:
- Plate or tubular type falling film evaporators
- Plate or tubular type forced circulation evaporators
- Flash and multi-flash evaporators.
These evaporator types have different strengths and benefits. In each case, the most suitable type is selected by consideration of the main process parameters:
- Scaling tendency
- The product’s thermal sensitivity
- Required particle size
- Annual operating hours
- Accessibility for maintenance.
To ensure the longest operational lifetime, evaporation plants are made from the most suitable and durable construction materials. These routinely include carbon steel, stainless and duplex steel, high nickel alloys, nickel and titanium. For the most highly corrosive applications, graphite, rubber-lined carbon-steel and fiberglass reinforced plastics are selected.
Heating configurations
Evaporation and crystallisation processes consume a substantial amount of energy. Operating costs are directly linked to the type of evaporator and the heating configuration selected (Figure 1). The main options are:
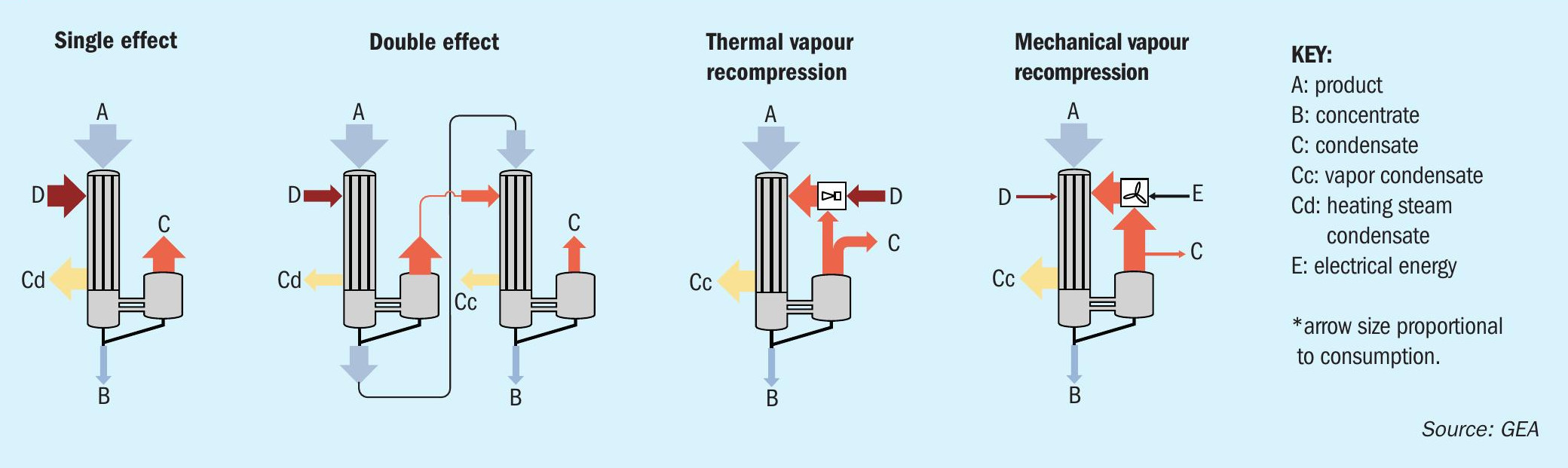
- Multiple-effect evaporators. Classical multiple-effect evaporation uses low-pressure steam for heating of the first effect and vapour for heating in the subsequent stage or stages. The number of stages employed reflects the relative importance of operating costs versus capital investment. These factors are linked to evaporation capacity and the boiling point elevation of the solution.
“Evaporators and crystallisers are widely applied in nitrogen, phosphate and potash production. This includes the large-scale manufacture of the fertilizer commodity potassium chloride and production of the process intermediate phosphoric acid.”
- Thermal vapour recompression (TVR) is used whenever steam is available at high- or medium-pressure. The flash energy of the steam is used to recompress part of the vapour given off, up to the pressure of the heating steam. This configuration, when available, achieves substantial savings in steam and cooling water at a relatively low cost.
- Mechanical vapour recompression (MVR). In this configuration, all of the process vapours are recompressed to heat the evaporator. Virtually no steam is required, apart from pre-heating when starting the process. The only energy consumption necessary is the power required to drive the compressors. These are usually centrifugal fans, with one or several stages of compression, or positive-displacement type compressors. In some applications, a scrubber is installed prior to the compressor to prevent corrosion from acid vapours.
Current energy costs make MVR a very attractive configuration for evaporation and crystallisation. Choosing this option also delivers a saving on cooling tower and boiler investment.
A new crystallisation and evaporation plant must balance energy costs with capital cost. This is achieved by finding the right compromise (in terms of the total cost of ownership) between the customer’s investment budget and operating cost, the latter being mainly linked to energy price levels. Existing production units can also be upgraded by reconfiguring and improving the existing heating configuration and/or by introducing more modern technology.
KEY FERTILIZER INDUSTRY APPLICATIONS
Potassium chloride (MOP) production
For brine sources, highly pure crystalline potassium chloride is recovered at multiple flash cooling crystallisation plants. Brines typically contain both sodium chloride (NaCl, sylvinite) and potassium chloride (KCl). This process is notable for:
- High efficiency heat recovery
- Temperature drop from 110°C to 45°C
- Heat recovery in four stages is usual with condensation in three re-cooling stages
- K2 O content adjustable between 58-62 percent by remixing condensate
- Crystal size of up to 1.2 mm.
Potassium chloride is also commonly crystallised from conventionally mined carnallite ores (containing KCl, MgCl2 , NaCl, MgSO4 and CaSO4 ). Additional purification steps are generally necessary to generate a product of the required commercial quality at an economically-acceptable yield.
Potassium nitrate crystallisation
Potassium nitrate (KNO3 ) can be manufactured via several process routes:
- GEA offers a direct conversion process for KNO3 using crude, natural sodium nitrate product (caliche) and fertilizer grade potassium chloride (MOP). This innovative process design provides a capital cost saving on the sodium nitrate rectification plant.
- The reaction of MOP with nitric acid is another KNO3 production method. This yields ammonium chloride as a by-product.
- Potassium nitrate can also be produced using an ion exchange and crystallisation process.
Ammonium sulphate manufacture
The industrial production of caprolactam (CPL), methyl methacrylate (MMA) and acrylonitrile yields large quantities of ammonium sulphate (AS) as a by-product. This route now accounts for 60-70 percent of AS production globally. Other sources of ammonium sulphate include:
- Purge gas washing, e.g., from large urea prilling towers
- Regeneration liquids from continuous ion exchange systems
- Production through reactive crystallisation of ammonia and (spent) sulphuric acid.
The heat generated by the reactive crystallisation of AS enables the evaporation process to be operated without any external energy source. While reactive crystallisation has an energy advantage over evaporative crystallisation, disadvantageously, it produces smaller crystals. Consequently, around 80-90 percent of AS crystallisers are operated in evaporative mode to produces larger size crystals. The market price of the larger crystals (2-3 mm) obtained can be up to three times higher than the price of smaller crystals (<1 mm) – a price premium that strongly favours the production of large crystals.
Water-soluble monoammonium phosphate
Highly pure and water-soluble monoammonium phosphate (MAP) can be manufactured from phosphoric and ammonia by a process with the following steps:
- Reactive crystallisation – the reaction of NH3 with H3 PO4 in a reactor
- Decantation
- Membrane filtration
- Forced circulation crystallisers with integrated scrubbers.
This produces MAP in highly concentrated form as white crystalline pellets. The demand for this type of water-soluble MAP – for fertigation or foliar application to crops – is growing globally.
Fertilizer production
Evaporators and crystallisers are widely applied in the production of nitrogen, phosphate and potash fertilizers (see box). This includes the large-scale manufacture of fertilizer commodities such as merchant-grade phosphoric acid (MGA) and granular muriate of potash (MOP, KCl). More importantly nowadays, evaporation and crystallisation are also used to produce value-added speciality products, especially water-soluble fertilizers (WSFs) such as monoammonium phosphate (MAP), potassium nitrate (NOP), potassium sulphate (SOP) and monopotassium phosphate (MKP).
GEA Group, with its expertise in evaporation and crystallisation, has developed and successfully installed numerous processes in fertilizer production plants worldwide. The company also has expertise in process design, gained from laboratory- and pilot-scale testing and process simulations carried out at GEA’s development centre.
Innovations and sustainability improvements
High-purity phosphoric acid is generally used as the starting product for MAP manufacture. GEA, however, has developed a ground-breaking process that produces high-quality water-soluble MAP fertilizer from non-purified, merchant-grade phosphoric acid (MGA) instead (Fertilizer International 496, p45). This eliminates the need to purchase or manufacture more costly purified phosphoric acid (PPA).
In a landmark fertilizer industry project, GEA has successfully implemented this process at a production plant in Eastern Europe. This allows the customer to manufacture highly pure and soluble MAP at a yield of up to 70 percent. The installed production unit has avoided considerable capital costs and operational expenditure, thanks to its ability to consume MGA rather than PPA, while still producing high-quality, water-soluble MAP, a premium fertilizer product with a high market value.
The company’s newly-developed MAP production process, as well as consuming lower grade MGA, incorporates a special ceramic membrane filtration (CMF) system that removes impurities (mainly struvite). The filter’s ceramic elements are abrasion resistant and provide a high level of temperature stability while removing crystalline impurities from the MAP solution.
GEA, by providing the industry with the ability to manufacture high-quality water-soluble fertilizers (WSFs) for fertigation, is also supporting sustainability by promoting efficient and responsible nutrient use.
Fertilizer producers are minimising energy usage and cutting energy costs – to increase their competitive advantage, cut carbon emissions and improve operational sustainability. With these objectives in mind, evaporation and crystallisation can improve energy consumption in several ways such as:
- Better use of hot condensates
- Use of vapour recompression l Installation of multiple-effect evaporators
- Heat integration between the evaporator and dryer
- Combining scrubbing or steam reforming with vapour recompression, when dealing with corrosive process vapours.
GEA is able to provide energy use audits and advise on all these options.
Water and product recovery from fertilizer production effluents is also becoming more important. Increasingly stringent wastewater regulations are creating growing interest in evaporation and crystallisation for waste reduction and treatment. As a technology, they offer customers a complete solution to water cycle management in industrial processes. The installation of evaporation and crystallisation equipment can deliver:
- Compliance with environmental regulations
- Recovery of distilled water
- Recovery of valuable chemicals l Profits from waste treatment
- Positive improvements in environmental, social and governance (ESG) performance.
The management of phosphogypsum ponds and raffinates remains a great challenge for the phosphates industry. Evaporation and crystallisation technology, together with membrane filtration and ion exchange, offer one potential solution due to their ability to recover both valuable products and water.
Summary
Evaporation and crystallisation technologies can be customised to manufacture a wide spectrum of fertilizers, allowing these to be produced both efficiently and sustainably.
GEA – with a team of 150 evaporation and crystallisation specialists and brands like Messo, Wiegand and Kestner – is a long-standing provider of innovative production technology to the fertilizer industry. Founded nearly 140 years ago, the company combines an extensive track record in industrial evaporation and crystallisation with strong research and development capabilities. Its wide experience of full-scale production plants is backed by strong process design capabilities and laboratory- and pilot-scale testing facilities.
Around the globe, GEA plants are producing industrial-grade, high-quality fertilizers – in locations ranging from the Atacama desert in Chile to Europe’s potash mines, and from the shores of Dead Sea in the Middle East to phosphoric acid plants in Asia and Latin America.