Fertilizer International 514 May-Jun 2023
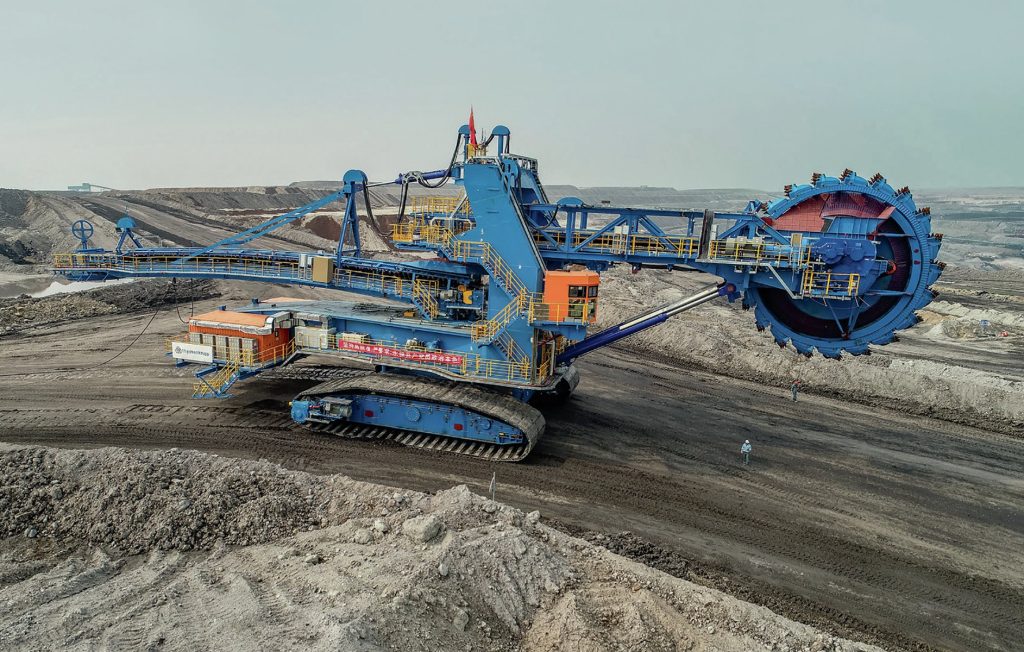
31 May 2023
FLSmidth completes thyssenkrupp Mining purchase
MINING, CRUSHING & TRANSPORT
FLSmidth completes thyssenkrupp Mining purchase
In September last year, one of the largest mining equipment and technology deals in history closed when FLSmidth finally completed its purchase of thyssenkrupp Mining. We look at the implications for the fertilizer sector and phosphate and potash mining.
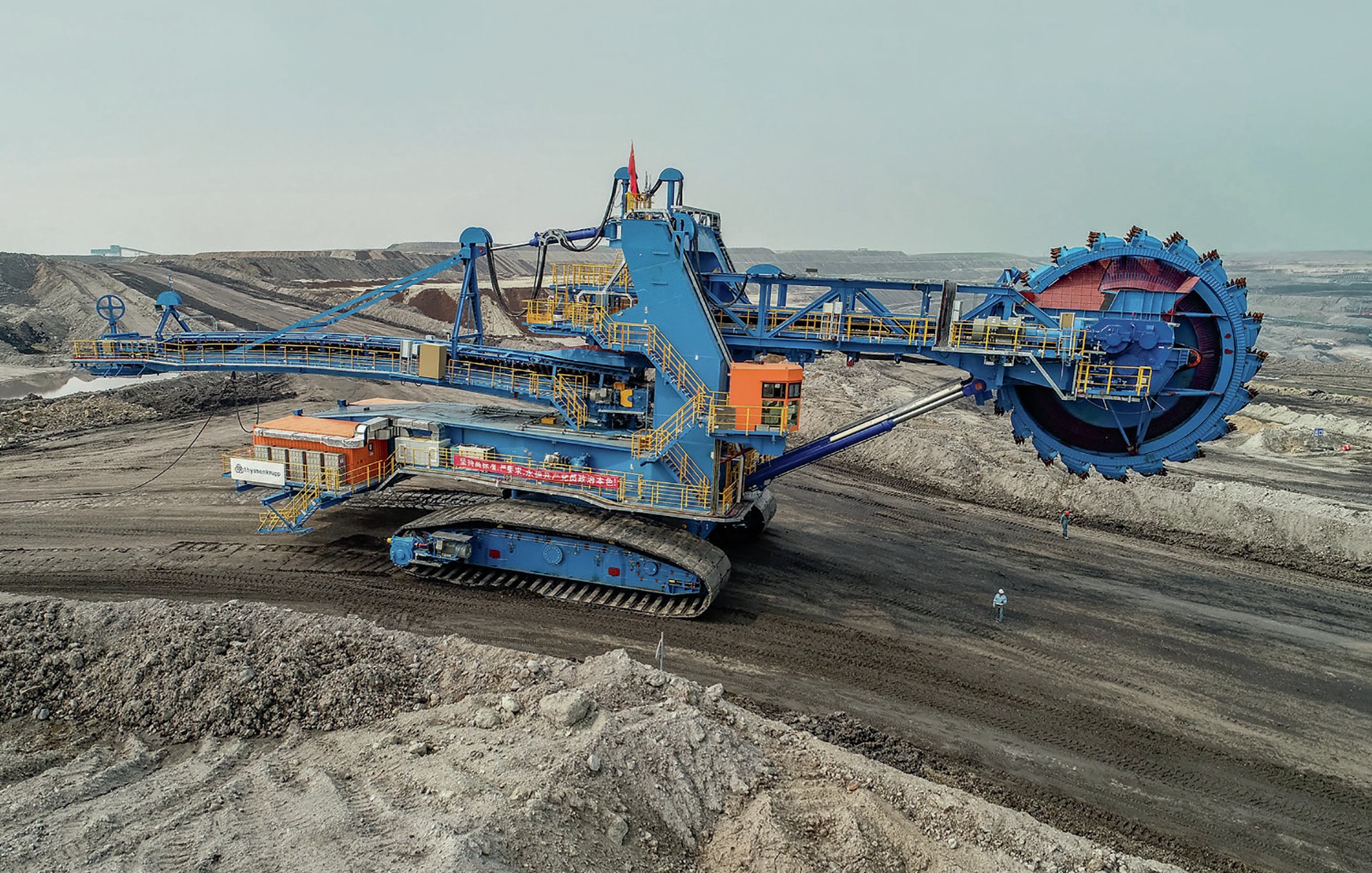
Mining mega purchase
thyssenkrupp Mining had a presence in 24 countries, with engineering and global service centres across the world, and almost 3,400 employees. The company generated revenues of e780 million in 2020.
Despite its strong identity and history, the name thyssenkrupp Mining was swiftly abandoned as a separate mining industry brand with immediate effect following its acquistion by FLSmidth. All its equipment offerings will now be sold under the FLSmidth marque instead.
The addition of thyssenkrupp Mining to FLSmidth creates a new business with a total annual revenue of e3.0 billion (2020 basis). The move should increase FLSmidth’s mining revenues by more than 50 percent and position the company as a top-tier mining industry supplier. Efficiencies and cuts to costs from the purchase are also projected to generate savings of e50 million this year.
The acquisition is expected to boost FLSmidth’s growth ambitions. These have a strategic focus on mining, which is likely to account for around 75 percent of company revenues in future.
“In addition to the competitive advantages of scale, FLSmidth will be able to offer a stronger value proposition to customers through combined competencies, a wider offering and a more extensive customer reach,” FLSmidth said in a statement.
A complementary offering?
thyssenkrupp Mining offers FLSmidth strong competencies in in-pit crushing & conveying (IPCC), high-pressure grinding rolls (HPGRs) and large mine conveyors (Figure 1). These capabilities also contribute to FLSmidth’s MissionZero sustainability strategy and its objectives:
- In-pit crushing & conveying (IPCC): Promotes mine electrification and reduces the need for diesel trucks.
- Overland/large mine gearless conveyors: These are the cornerstone of mine decarbonisation, offering significant power savings though electrification. thyssenkrupp’s conveyor offering also comes with excellent simulation capabilities.
- Crushers: thyssenkrupp’s eccentric roll technology further enhances mining operation efficiency.
- High-pressure grinding rolls (HPGRs): These significantly reduce energy consumption of energy-intensive grinding processes.
Commenting on the purchase, FLSmidth said1 : “The acquisition was identified as a good opportunity, as it allows us to strengthen our position as one of the leading suppliers for our customers in the global mining industry. The combined coverage of FLSmidth and thyssenkrupp’s mining business includes a strengthening of our pit-to-plant range of technology, equipment and service expertise, covering continuous mining, mineral processing, mining systems and material handling.
“thyssenkrupp Mining’s equipment offering consists of open-pit mining equipment and systems, mineral processing solutions and material handling solutions. Thyssenkrupp is primarily involved in crushing, conveying, grinding and processing, which we see as broadly complementary to our offering.
“We do have some overlap of technologies, but we see a clear complementary offering – especially in the areas of sustainability and digitalization. For example, thyssenkrupp mining has a strong in-pit crushing set up that is complementary to our existing offering, and in grinding, they have a strong position with HPGRs [high pressure grinding rolls], whereas we are one of the leading providers in other grinding solutions, such as SAG [semi autogenous grinding] mills.”
Acquisition closes
Mikko Keto, FLSmidth’s CEO, spoke to International Mining on the day the acquisition closed last September2 .
“It is important to emphasise that we are getting some big missing pieces into our portfolio – TK Mining was, and therefore we now are, the clear HPGR market leader in mining, both in technology and installed base, which they had built up over many years,” Keto said. “Another example is …the highest throughput, most challenging conveying projects, where again TK Mining has led the way – especially in areas like gearless driven conveying working with Siemens where they, and now we, are the clear leaders in the market.”
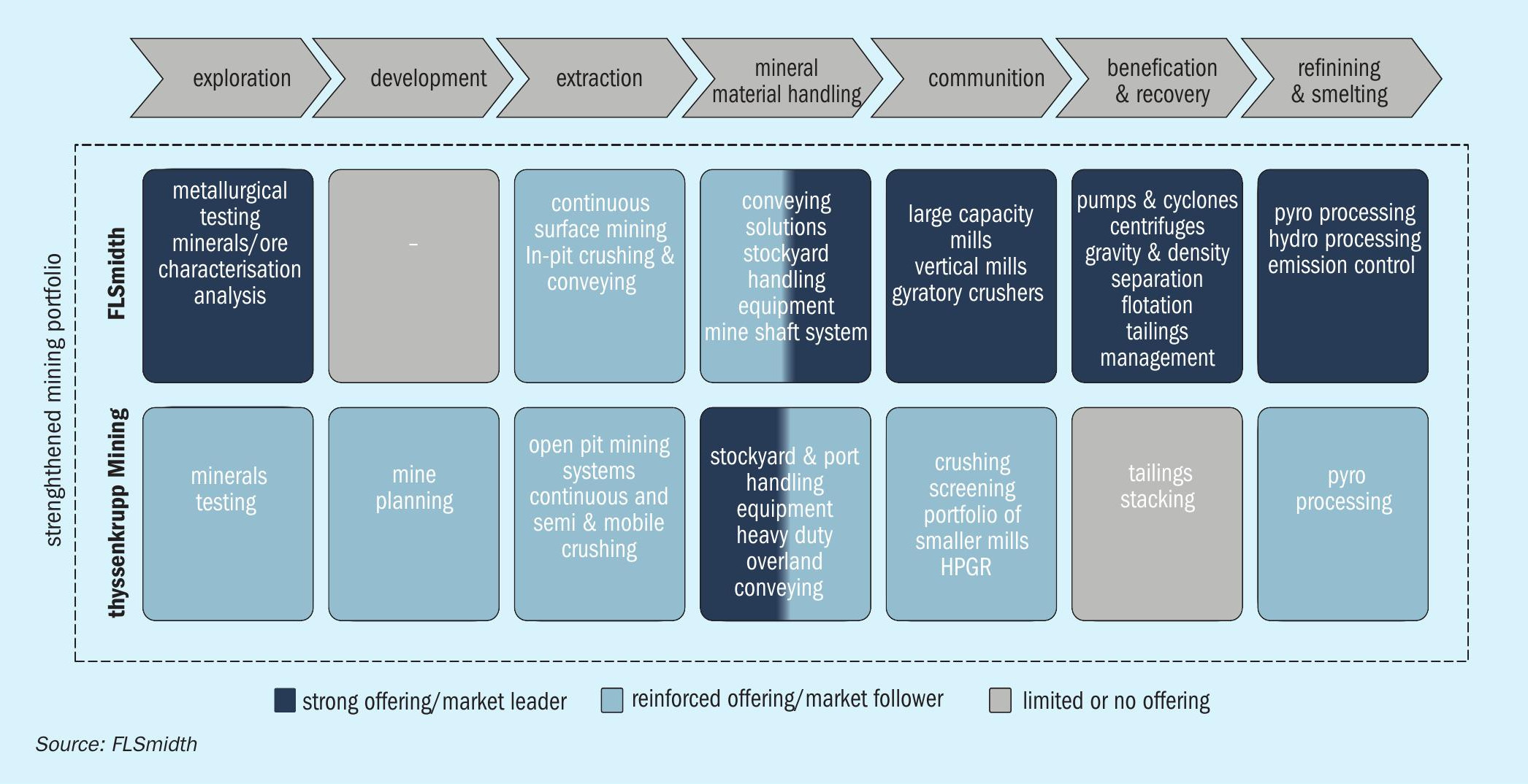
The purchase had been broadly welcomed by customers, according to Keto.
“The majority of the feedback we have had, including the major Tier 1 miners, has been very positive. It was no secret in the market that TK’s mining business was up for sale – and they had a huge installed base, especially in areas like primary and secondary crushers, mills including HPGRs, and within the IPCC space with conveyors and crusher stations. So there was concern as to who the new owner might be – and FLSmidth is seen as a welcome new parent, being itself a large and established player in mining technology, plus having a long term commitment to invest in and grow the business.”
In-pit crushing & conveying (IPCC), suggested Keto, was an area with opportunities for the new combined business.
“One area we are focussed on is further advancing a more modular approach to IPCC crushing stations. While IPCC projects are all bespoke to a certain extent, some standardisation of engineering helps reduce costs for both us and customers. Bringing the opportunities of IPCC to smaller and medium sized mines is also something we will continue to do. Of course, IPCC also brings huge MissionZero related benefits in terms of decarbonisation for miners.”
Keto said thyssenkrupp Mining’s Russian market exposure was under control.
“New business in Russia has been suspended and contracts with non-sanctioned customers are being finalised to the extent possible. The outstanding order backlog from Russian activities amounted to around e43 million by end July 2022 while other potential exposure and risks related to Russia remain subject to audit.”
Compact bucket wheel excavators
The purchase of thyssenkrupp Mining strengthens FLSmidth’s equipment offering for phosphate and potash mining. This includes the Barracuda range of bucket wheel excavators introduced in 2016 (Fertilizer International 495, p37). These compact mining machines use a larger number of teeth per bucket to cut materials with a compressive strength of up to 50 MPa.
The Barracuda’s innovative design allows harder materials to be excavated, including phosphate rock, potash and limestone, without the need for drilling or blasting operations. By combining ore excavation, loading and the transport within a single machine, the Barracuda can seamlessly replace a complex system of multiple machines with a single mining unit.
FLSmidth can now offer several versions of the Barracuda, each with different ore transport configurations. They range from a compact machine and conveyor – for a basic extraction process – to the advanced Barracuda C machine. This combines a compact bucket wheel excavator with a discharge boom operating in tandem with a conveyor system.
The Barracuda has three particular features that make it an attractive excavation option for mine operators:
- Streamlines ore transportation
- Offers predictable operational costs
- Able to eliminate pre-blasting.
In ore transport, integrating the Barracuda with continuous mining/conveyor systems widens the range of potential mine applications and also delivers major cost reductions in comparison to conventional truck transportation. The machine’s electrical drive can also reduce the carbon footprint of mining operations. One Barracuda machine, by potentially replacing more than 10 other mining equipment units, also streamlines both operations and maintenance efforts.
But is the elimination of pre-blasting that is the main overall factor which makes the Barracuda a leaner, more cost effective and safer mining process option. Conventional bucket wheel excavators are unable to cope with harder ore materials and – unlike the Barracuda – still require blasting to fracture rock in-situ prior to extraction. The need for pre-blasting can add more than $0.2 per tonne to extraction costs – a major cumulative cost for multimillion tonne mining operations.
The Barracuda, by removing the need for drilling and blasting, can therefore offer significant cost reductions, especially for mine expansions or new mine projects which require investment in new equipment anyway. The use of Barracuda mining machines also offers a more sustainable alternative to blasting, which is subject to increasingly stringent environmental regulations for noise, fumes, dust and vibrations.
In-pit crushing & conveying (IPCC)
thyssenkrupp Mining also brings to FLSmidth key capabilities for in-pit crushing & conveying (Fertilizer International 475, p54). The company’s market leading IPCC system is designed to limit truck haulage and has the following advantages versus a conventional system using diesel trucks:
- It is electrically driven with a higher efficiency than diesel motors
- Has a lifetime of up to 40-50 years with regular maintenance
- Significantly reduces operating personnel due to partial automation
- Increases mine safety
- Increases utilisation
- Reduces CO2 emissions, the amount depending on the origin of the electricity used.
Although the relative investment costs are generally higher for IPCC systems, opex reductions can typically generate a return on investment within 2-4 years.
In 2015, thyssenkrupp successfully installed an IPCC system at the Koashvinsky phosphate mine near the city of Kirovsk on the Kola Peninsula in northern Russia. This is operated by OJSC Apatit, a subsidiary of fertilizer producer PhosAgro (Fertilizer International 475, p54). The IPCC system designed for the Koashvinsky mine is a combined crushing unit with the capacity to handle up to 30 million tonnes of waste a year. The system needed to be able to accept materials with compressive strengths averaging 50-190 MPa up to a maximum of 320 MPa.
The hoppers installed have sufficient design capacity to accept trucks with a payload of up to 220 tonnes. The direct feed crushing plant is also equipped with a gyratory crusher designed to accept 6,200 tonnes of material per hour.
IPCC also replaced previous truck haulage of waste materials outside of the mine. Instead, these materials are crushed to a conveyable size and transported by a curved conveyor over a distance of around four kilometres to an external waste site. At the end destination, a crawler-mounted spreader with an hourly capacity of 6,200 tonnes then discharges material from the conveyor.
The IPCC system has substantially cut the Koashvinsky mine’s operating costs, maintenance costs and CO2 emissions. It also provides a higher level of operational safety.
References