Nitrogen+Syngas 383 May-Jun 2023
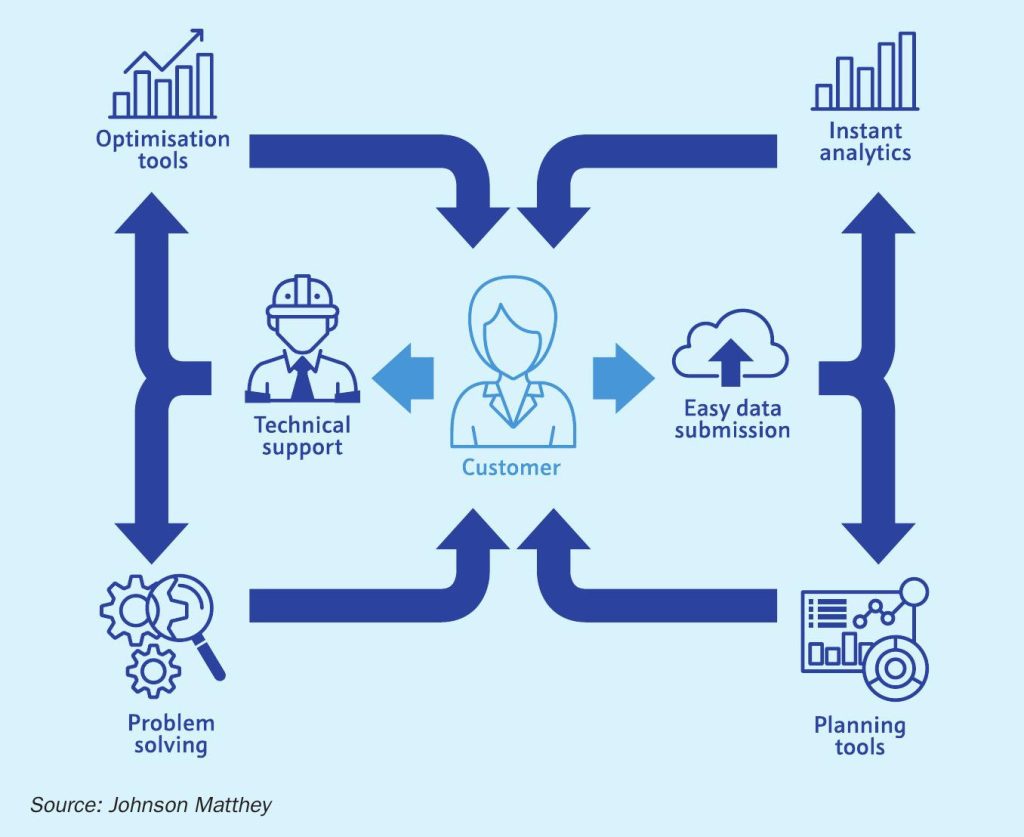
31 May 2023
Optimising methanol production
DIGITAL TOOLS
Optimising methanol production
Combining a deep scientific knowledge, engineering and field experience with state-of-the art technology, Johnson Matthey is proud to introduce its next generation of digital simulation tools via its JM-LEVO™ digital portals to further support customers in achieving their operational and sustainability targets.
Johnson Matthey (JM) is a global leader in sustainable technologies, catalysing the net zero transition. With over 200 years of sustained commitment to innovation and technological breakthroughs, JM improves the performance, function and safety of its customers’ products. JM’s science has a global impact in areas such as low emission transport, energy, chemical processing and making the most efficient use of the planet’s natural resources.
JM is known for its process technologies and catalysts, but it is its scientific knowledge and experience to ensure its products perform optimally in its customer plants that differentiates it. To enhance its technology and catalyst offer, JM offers a suite of services to ensure customer success and maximise plant performance. This includes asset life and reliability studies, reformer monitoring and surveys, reduction and start-up assistance, plant flowsheet designs and modelling capabilities1 . However, as markets evolve and operational performance and sustainability are at the forefront of everyone’s minds, the need for more agile digital solutions has become apparent.

Digital transformations can be used to solve some of the toughest problems that face the chemical industry today and as the world continues to transition to a net zero future, it is important to have the right tools in hand to support and adapt quickly to customer’s needs.
The JM-LEVO digital portal, is a plant model and communication tool that intelligently collects and evaluates operating data to enable real-time monitoring and provide detailed insights through automated data validation and analysis. The dynamic portal allows operators to identify opportunities to improve operation and maximise the utilisation of available feedstock, catalyst and equipment. With the introduction of enhanced digital services to JM’s portfolio, customers can share dynamic content with JM technical service representatives to support with unusual operating data. These representatives can then offer tailored recommendations based on 60+ years of experience. This is shown in Fig. 1.
A key priority for JM in building a digital product portfolio was to enhance existing services, help drive the implementation of customer sustainability goals, and enable customers to quickly pivot to changing priorities and business requirements. Building on JM’s experience in the catalyst and process technology markets, the company launched its first digital product, JM-LEVO Formaldehyde, in 2020 for its FORMOX™ catalyst customers.
The digital portal was developed with direct customer input to offer a unique solution to support specific customer and production needs. A machine learning tool has been developed to further supplement the technical support team’s knowledge bank. This approach has led to many customer successes and is a prime example of how digital tools can be leveraged to support technical services.
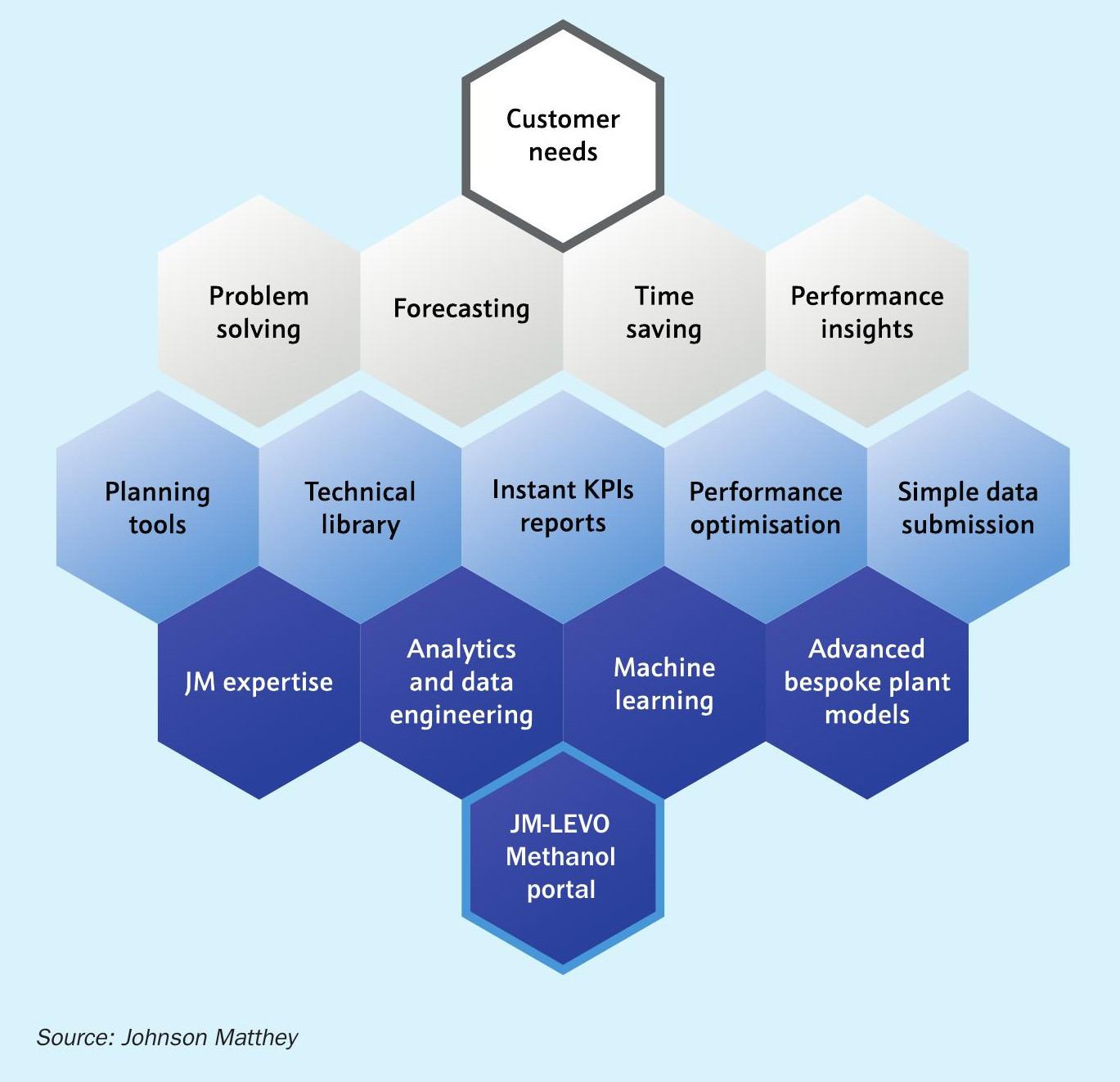
The JM-LEVO Formaldehyde portal set much of the groundwork for JM’s digital journey, demonstrating the value of the approach and providing a robust platform to expand the offering across other markets. Building upon this experience and customer input, a machine learning model has been developed that continually improves capabilities and functionality, helping customers deliver higher performance across reactors and plants. For example, the model is able to use historical data and customer insight to improve load comparison and compare larger data sets, thereby enabling customers to analyse larger volumes of data to support optimisation and make better-informed decisions.
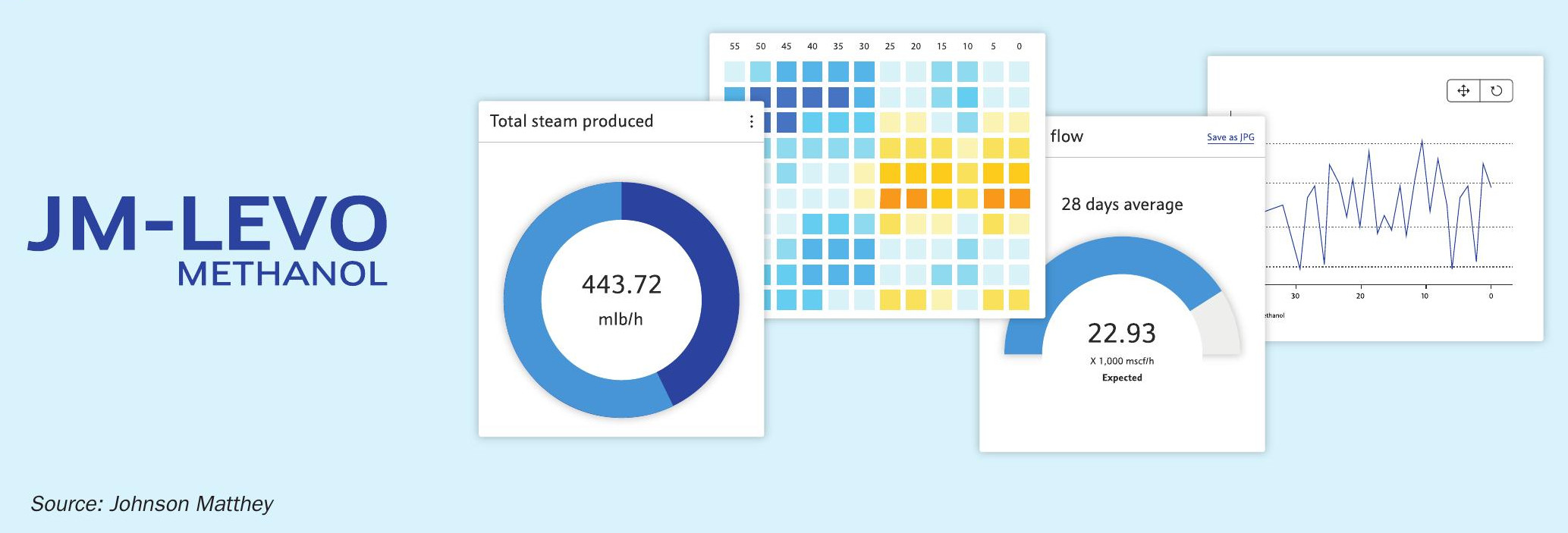
JM-LEVO Methanol
JM has been at the forefront of methanol technology (through ICI heritage) since it developed the modern ‘Low Pressure Methanol’ process in the 1960s, and is a world leader in the development of methanol technology and catalysts. With a background in methanol plant design, operation and optimisation, JM is uniquely positioned to deploy enhanced digital tools in this market to offer more reliable, sustainable customer-centric plant optimisations. The JM-LEVO Methanol digital portal was released last year with the first customers now onboard, benefitting from a new approach to reporting and communicating methanol plant operating information. The JM-LEVO digital portal can cut through the noise generated by vast data volumes from a chemical plant to offer clear and concise ways of filtering, evaluating, and storing valuable information, driving more efficient operation and lowering environmental impact. Additionally, the JM-LEVO portals simplify the retrieval of detailed reports and technical guidance from an online library, providing easy access to key information and JM technical expertise, whilst meeting the end-to-end security requirements.
The JM-LEVO digital portal allows more frequent assessment of plant performance, giving plant engineers the opportunity to identify areas of improvement earlier than ever before, and to achieve operating targets more consistently. The goal of the JM-LEVO digital portal is to optimise production and meet customer sustainability objectives, whether it be product yield, catalyst life, cost or capacity, as illustrated in Fig. 2.
Methanol plants today are highly optimised facilities, with fine margins separating good and great performance, whether this is measured by production, efficiency, or more complex indicators such as carbon intensity, the methanol industry is continually working to improve efficiency of production towards a net-zero carbon emission goal. In a world that is currently moving and changing at pace, the JM-LEVO digital portal can facilitate these objectives by giving better access to JM expertise to troubleshoot problems and find solutions quickly.
JM-LEVO digital portals are intended to complement existing technical services, providing an easy way to share data with JM and receive feedback and recommendations on plant operation. They are the basis for a new generation of technical service, processing larger volumes of data through more advanced models and analysis. This is a necessary step to open the opportunity to use technologies such as machine learning driven optimisation on all plants, not just those being designed today.
The portal’s dynamic charts, insights and valuable information, examples of which are shown in Fig. 3, can be easily shared with colleagues, and JM technical representatives, enabling benchmarking and performance monitoring across loads and reactors for multiple sites and plants. JM has access to the dashboards and reports, enhancing the support that JM can offer its customers using the JM-LEVO services.
Responding to customer feedback and market dynamics, JM has recently developed an automated data ingestion tool, offered as additional functionality via the JM-LEVO digital portal. This solution enables the JM technical service team to access up-to-date plant data direct from the customers to provide rapid reporting. The customer can control what data they make available to JM via the JM-LEVO digital portal.
With the success of the JM-LEVO digital portals for formaldehyde and methanol customers, JM is planning to develop this for other industries too including nitric acid.
Summary
With the success of its most recent digital portals, JM is at the forefront of offering digital solutions for chemical production in syngas markets. Leading this digital revolution, the JM-LEVO digital portal enables effective and efficient data integration to provide the insight customers require to maintain optimum high efficiency.
In conclusion, online analytics can help improve plant efficiency by: providing real-time data, allowing for proactive monitoring and control of the process; identifying areas of inefficiency; and providing insights into process changes and optimisation opportunities. By utilising online analytics, chemical plants can more effectively utilise their resources and operate more efficiently.
The JM-LEVO Methanol digital portal is available now, and is already supporting Johnson Matthey customers to improve production capabilities, maximise plant efficiency and achieve sustainability goals. n
References