Nitrogen+Syngas 383 May-Jun 2023
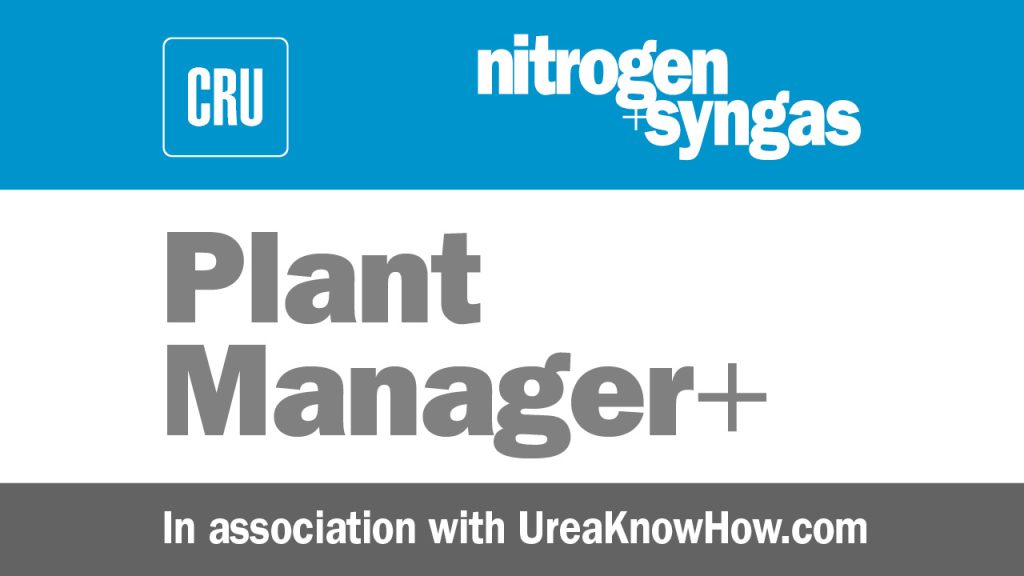
31 May 2023
Problem No. 67: Redrilling liquid holes in the ferrules of a CO₂ stripper
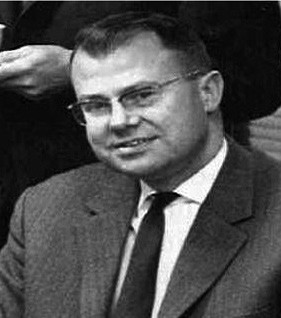
In 1967 Stamicarbon revolutionised the urea process by the invention of the high-pressure CO2 stripper by Petrus J. C. Kaasenbrood (pictures above). The high-pressure CO2 stripper led to the following benefits:
- the ammonium carbamate could be recycled at synthesis pressure so extra water needed to be added to recycle the unconverted ammonium carbamate from the reactor;
- a medium-pressure recirculation section was no longer needed;
- with the condensation of strip gases in the high-pressure carbamate condenser, low-pressure steam could be produced which could be used in the downstream sections approximately halving the steam consumption of a urea plant.
At the same time, however, the performance of the CO2 stripper has become possibly the most critical parameter in these urea plants. A new stripper that is properly designed will provide good performance (stripper efficiency). But during its lifetime fouling, passive corrosion and other corrosion failure modes impact the stripper efficiency in a negative way.
One critical parameter for the stripper efficiency is the size of the liquid holes in the ferrules. There are typically three holes per ferrule. The diameter and shape of these holes slowly change due to cross cut end attack corrosion. The diameter increases and the shape changes from round to oval as the rate of cross cut end attack corrosion differs depending on the rolling direction of the applied steel during its fabrication process.
For high stripper efficiency it is very important that the liquid holes of each tube ferrule have the same dimensions. This is checked by delta-P measurements of each ferrule: Air is blown through the three holes and the delta-P is measured. The range in the delta-Ps of all ferrules should be as small as possible in order to assure a high stripper efficiency.
Older strippers show a larger range than a new stripper and over time the diameter of the holes eventually become too big and the range of the delta-Ps become too large to realise a sufficient stripper efficiency. A low stripper efficiency in a Stamicarbon urea plant leads to higher loads/pressures in the low-pressure recirculation section and higher recycle rates of unconverted ammonium carbamate, reducing the maximum possible plant load.
Replacing ferrules is quite expensive and therefore many plants try to extend the lifetime of the ferrules by redrilling the liquid holes. Some experiences are discussed in this discussion.
Abdul Samad of Fauji Fertlilizer Bin Qasim Limited in Pakistan kicks off the discussion: As per recommended practice, we perform the delta-P check of all ferrules of the urea stripper during turn around and replace those that have failed the delta-P check as per Stamicarbon procedure. We intend to carry out the repair of used ferrules (with enlarged holes). Can anyone suggest the recommended method to repair used ferrules and what inspection checks need to be followed during and after completion of the repair?
Sunil Kulkarni of Mangalore Chemicals and Fertilisers in India replies: We have done this repair on stripper ferrules by drilling three different holes at 120 degrees apart and closing the old holes. This was with ferrules made of 2RE69 (Alleima 25-22-2) material.
Mark Brouwer of UreaKnowHow.com in the Netherlands asks some further questions: Would you be so kind to share with us your general experiences like:
- Was the redrilling exercise successful?
- How much time it did take?
- What delta-P range did you achieve?
Sunil replies: The exercise of redrilling the liquid holes of the stripper ferrules was successful and we used the redrilled ferrules for another 7-8 years. The delta-P after redrilling was in the range 400-450 mm WG. The whole drilling operation after blocking the old holes was done carefully with a new jig in a time period of about 10 days (1,680 ferrules).
Ali Azhar of Fauji Fertlilizer Bin Qasim Limited in Pakistan asks a further question: After welding the old holes, was the surface smooth inside of the welded area or was there any cavity left at the inner surface of the ferrules?
Ahsan Sarfraz of Fatima Fertilizer Ltd in Pakistan shares his experience with another solution: Another procedure we have done successfully at PAFL (Pak-American Fertilizer Ltd) is to measure the hole size of all holes of a single ferrule. Now close any of the holes based on the size so that the overall hole size across a single ferrule remains the same. This practice was also very successful, and we used these ferrules for three more years before overhauling the whole stripper as part of an upcoming plant revamp. The whole activity was completed in two days (1,846 ferrules). This is the simplest method requiring less time and accuracy and the results are also pretty good. In case you have replaced the ferrules with new ones you have sufficient time to redrill the holes.
Majid Khan of Pakistan follows up with another question: What happens if we shorten the length of ferrules due to corrosion in the lower part (fitted inside the tube)? I have come across a case study where shortening of the ferrule led to stripper flooding at high load.
Prem Baboo, Expert at UreaKnowHow.com joins the discussion: Please refer to my Technical Paper “Energy saving in Urea Plant by equipment modifications.pdf” available in the E-Library of UreaKnowHow.com.
Majid replies: I have gone through the paper. It clearly mentions that the ferrules were shortened and the liquid hole size was increased from 2.8 mm to 3.1. Why did you do that?
Prem responds: The thinned bottom portion of the ferrules are removed due to the adverse effect on making the heat transfer film. It is so thin that it can easily bend and disturb the flow of solution.
The tangential hole diameter was increased due to load limitation. 2.8 mm was designed for a plant load of 1,100 t/d. The plant load had increased to 1,500 t/d, hence the tangential hole diameter needed to be increased according to the load otherwise flooding would occur in the stripper tubes. The total area of the tangential holes needs to be increased by about the same ratio as the plant load increase or with 90% of plant load increase, e.g., plant load increase is 26%, then total tangential hole area increase should be 90% X 26% = 24%. 2.8 mm diameter with three holes per ferrule and 1,677 ferrules means a total tangential hole area is 30,962.8 mm2 . The hole area is to be increased by 30,962.8 X 1.24 = 38,393.9 mm2. The area of one hole = 7.63 mm2. Hence each hole diameter is 3.11 mm.
Wasif Qazi of Engro Fertilizer Pakistan asks a further question: Will the decrease in ferrule length have any impact on the stripper efficiency? If yes, how it can be improved?
Prem replies: No, the efficiency will not decrease.
Mark adds some further comments: The flow through the liquid holes is dependent not only on the hole diameter or hole area but also on the liquid height. With the same hole area the liquid height will increase with a larger plant load. There could be a moment when overflow of liquid of the ferrules occurs, which will obviously lead to a bad falling film formation and low stripper efficiency.
When the hole area increases, the liquid height will reduce at the same plant load. One must assure a minimum liquid height to realise that each ferrule receives the same amount of liquid taking into account that the stripper may not be installed perfectly vertical, the liquid may not be perfectly divided over the complete tubesheet surface and sufficient buffer capacity of the liquid should be assured. In practice this means that a stripper with larger liquid hole areas will have a higher turndown ratio than its original design.
This series of discussions is compiled from a selection of round table topics discussed on the UreaKnowHow.com website. UreaKnowHow.com promotes the exchange of technical information to improve the performance and safety of urea plants. A wide range of round table discussions take place in the field of process design, operations, mechanical issues, maintenance, inspection, safety, environmental concerns, and product quality for urea, ammonia, nitric acid and other fertilizers.