Sulphur 406 May-Jun 2023
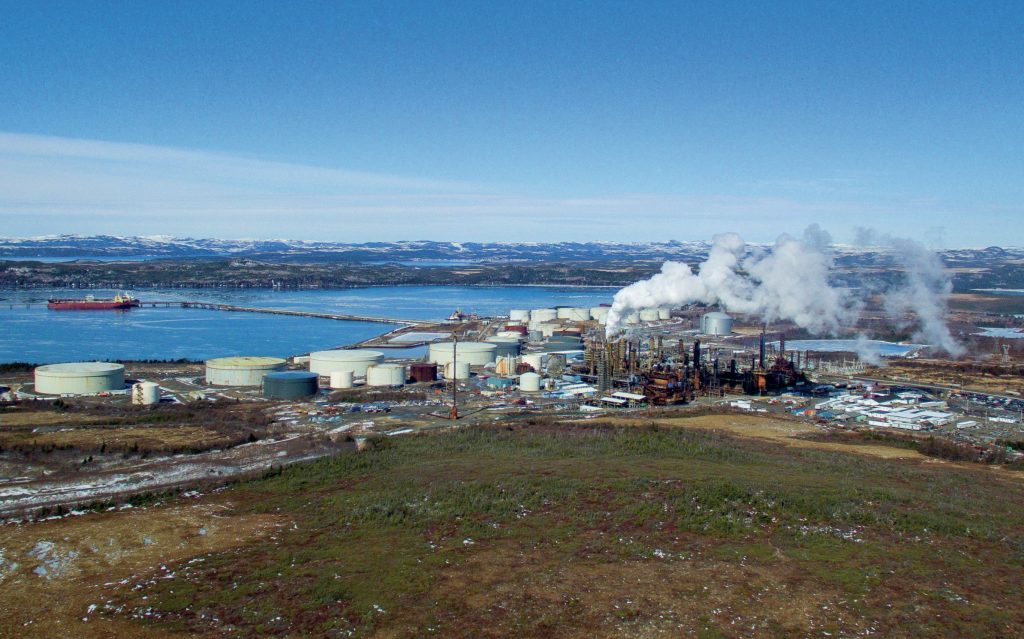
31 May 2023
Sustainable refineries
REFINERIES
Sustainable refineries
Liquid fuels will be with us for decades to come, but refiners will be pushed to decarbonise their activities, via greater use of biofuels, and green/blue hydrogen use.
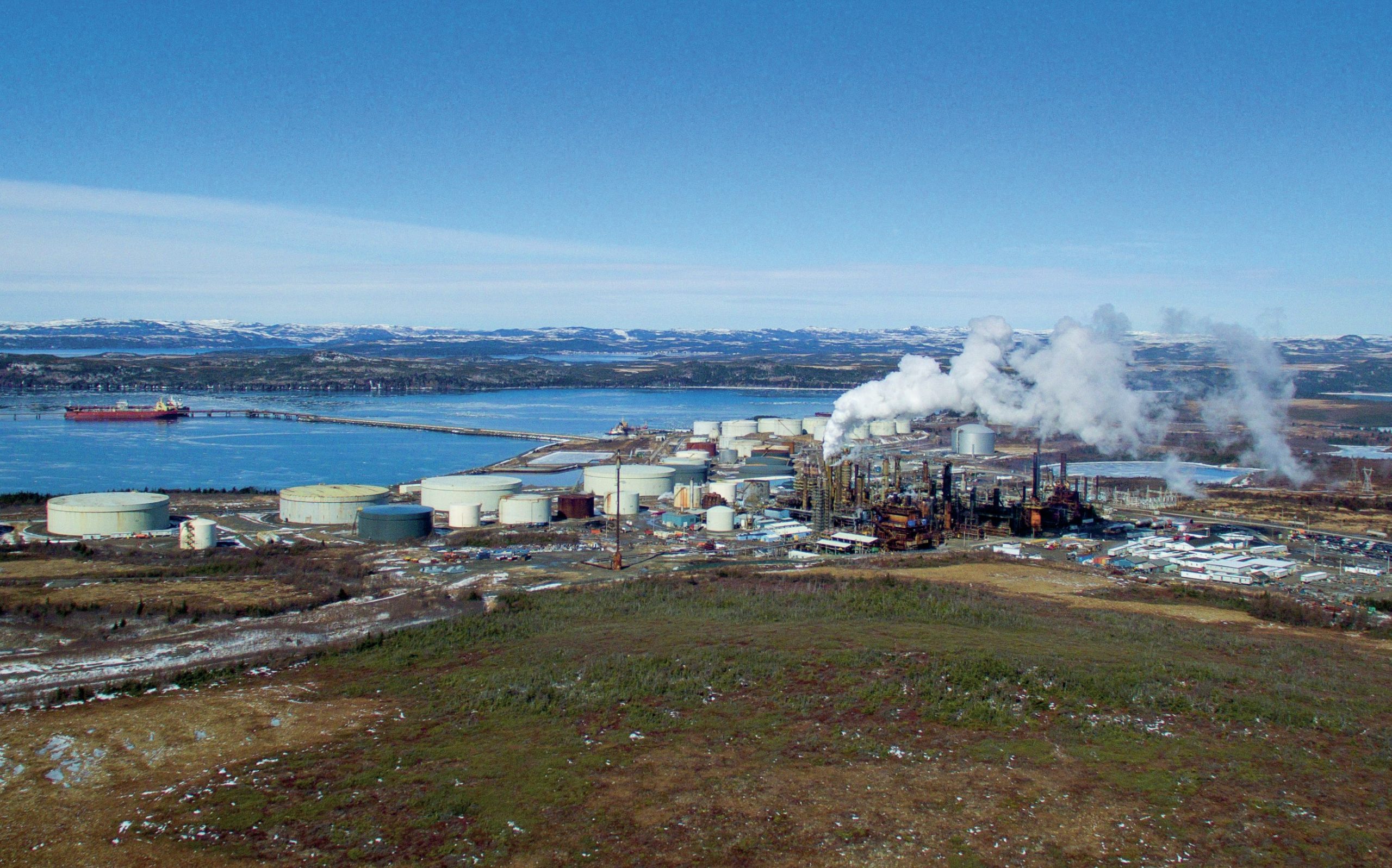
The refining industry, already battered by covid and the associated reduction in demand for refined products that saw 1.1 million bbl/d of refinery closures in the US and 0.8 million bbl/d in Europe, faces an uncertain future. Consumer demand for refined products is likely to peak during this decade, while an increasing use by governments of carbon pricing and other disincentives to production add costs to already squeezed margins. Production of electric vehicles is growing rapidly. Indeed, it is projected that EVs will form the majority of new vehicles sold globally by 2028. Demand for transportation fuels will thereafter decline by the equivalent of one major refinery per year worldwide. Concawe, the European refiners association, estimates that road fuel demand will decline by 31% between 2021 and 2035, from 343 million t/a to 232 million t/a. The pressure on capacity is likely to be strongest in North America and Europe, where operations are more expensive and EV takeup is fastest.
Low carbon operations
According to US EPA figures, the average refinery produces 1.2 million t/a of CO2 equivalent, with 95% of that coming from fuel combustion and catalytic cracking/ reforming. Refinery operations are likely to face increasing costs as carbon taxes and carbon pricing is imposed, particularly in Europe, where carbon prices are already approaching $100/t CO2 e. Reducing carbon emissions is likely to become a major factor in refinery operations to avoid these costs. Various strategies are available to the operator.
The least costly means of reducing carbon footprint, and the most effective, is to improve a refinery’s energy efficiency, via optimisation of operations and reduction of the gas, steam, and power needed to operate them. This can involve heat recovery systems, lower emission furnaces, thermal energy storage, and using digital tools to optimise operation.
Refineries can also offset their emissions switching to renewable energy sources, both to power their own operations and to sell back into the power grid. Other lower carbon fuel sources can also be used, including biomass, synthetic gas produced from biomass, biogas produced from other organic sources such as municipal waste and sewage sludge, and biomethane, which is produced by upgrading biogas.
Where operations are intensive in use of hydrogen, refineries can lower emissions by shifting from the production of hydrogen via steam methane reforming to green hydrogen made from entirely renewable sources of power. The cost of production has historically been high compared to gas-based production, but the cost of electrolysers and green electricity are both falling, and there are already over 800 green hydrogen projects announced worldwide, with a total capacity of approximately 29 million t/a, with financial incentives offered by governments, such as the US Inflation Reduction Act. IRA tax credits for renewable electricity and clean hydrogen can reduce the cost of green hydrogen production by almost half, falling to nearly $3/kg hydrogen for a project starting in 2023.
Finally, for large scale reduction of carbon emissions, there is the option of carbon capture, utilisation, and storage (CCUS). This can include production of so-called ‘blue’ hydrogen, using conventional steam reforming but capturing and using or storing the carbon produced, regarded as the more cost-effective option for large scale generators compared to green production, at least at present. CCUS does however require access to depleted oil and gas reservoirs, saline aquifers, basalt formations, or coal deposits that cannot be mined, or investment in downstream use of CO2 , such as chemical synthesis (including green methanol production), algae synthesis, etc.
Switching operations
Another option is to move away from refining altogether. Increasing integration with petrochemical production has been seen as an attractive way forward for some refiners. Many refineries already benefit from physical integration with a petrochemical plant and are co-located and operated as a single site. This integration leads to reduced costs of handling and moving exchanged streams; better overall optimisation of refining and chemical plant throughput; and scale-driven efficiencies in the cost of maintenance and operations support.
Biofuels
An option that has gained considerable traction in recent years is to switch the refinery operation to the production of biofuels. In Europe, there had already been significant production of biofuels as FAME (fatty acid methyl ester) biodiesel, using vegetable oils or used cooking oil combined with methanol. However, only a fraction of this has come from conventional refineries. The FAME biodiesel market has blending restrictions, and also overbuilt capacity in Europe. New production is mainly coming from hydrotreated vegetable oil (HVO), using a mix of both virgin vegetable oils and from waste and residues, as well as lignocellulosic and waste based feedstocks. This is proving an attractive option for European refiners. Around 75% of investment in European refineries is going towards biofuels production. Total has converted two conventional refineries at Grandpuits and La Mède in France which had been scheduled for closure into ‘biorefineries’ that able to produce bio-jet fuel, biodiesel, and bioplastics. Shell is looking at a huge 800,000 bbl/d facility in the Netherlands, and Eni is reportedly considering converting its 500,000 bbl/d Livorno refinery in Italy.
Renewable diesel and sustainable aviation fuel (SAF) plants are also proliferating in North America. Eight refineries have announced conversions to produce renewable fuels, with a combined capacity of 240,000 bbl/d, more than double US current biofuel output. In 2022, domestic renewable diesel and other biofuel plant capacity was just under 1.8 billion gallons per year, or 114,000 bbl/d, according to the Energy Information Administration (EIA). Government policy is driving change here, including tax credits and environmental regulations ranging from California’s low-carbon fuel standard to the federal Inflation Reduction Act (IRA).
Refinery conversions include Marathon Petroleum and Phillips 66, who are both in the process of converting refineries near San Francisco to produce renewable diesel, the former in partnership with Neste. HF Sinclair is adding a renewable diesel unit to its Navajo refinery in New Mexico, and there are also conversions in the US Gulf Coast. Valero Energy is engaged in a massive expansion of its Diamond Green Diesel facilities in Louisiana, a joint venture with Darling Ingredients. Fellow independent PBF Energy is adding renewable diesel capacity to its Chalmette, Louisiana refinery as well. In Alabama, Vertex Energy, a firm that specialises in processing used oils into products, is tweaking its Mobile refinery to produce renewable diesel. In Canada, Newfoundland’s Come-by-Chance facility is aiming to begin producing renewable diesel and SAF in the second half of this year.
Sulphur production
The impact of these changes will of course be a reduction in sulphur output. Although biofuel feeds contain some sulphur, it is often at very low levels, usually less than 150 ppm. At the moment the level of conversion has not had an appreciable effect on output; US refinery sulphur output actually increased in 2022 from 6.9 million t/a to 7.5 million t/a due to a combination of higher run rates and use of higher sulphur crudes. But towards the end of the decade these increasing conversions and closures will start to impact sulphur production, first in North America and Europe, but likely worldwide over the subsequent years.