Fertilizer International 515 Jul-Aug 2023
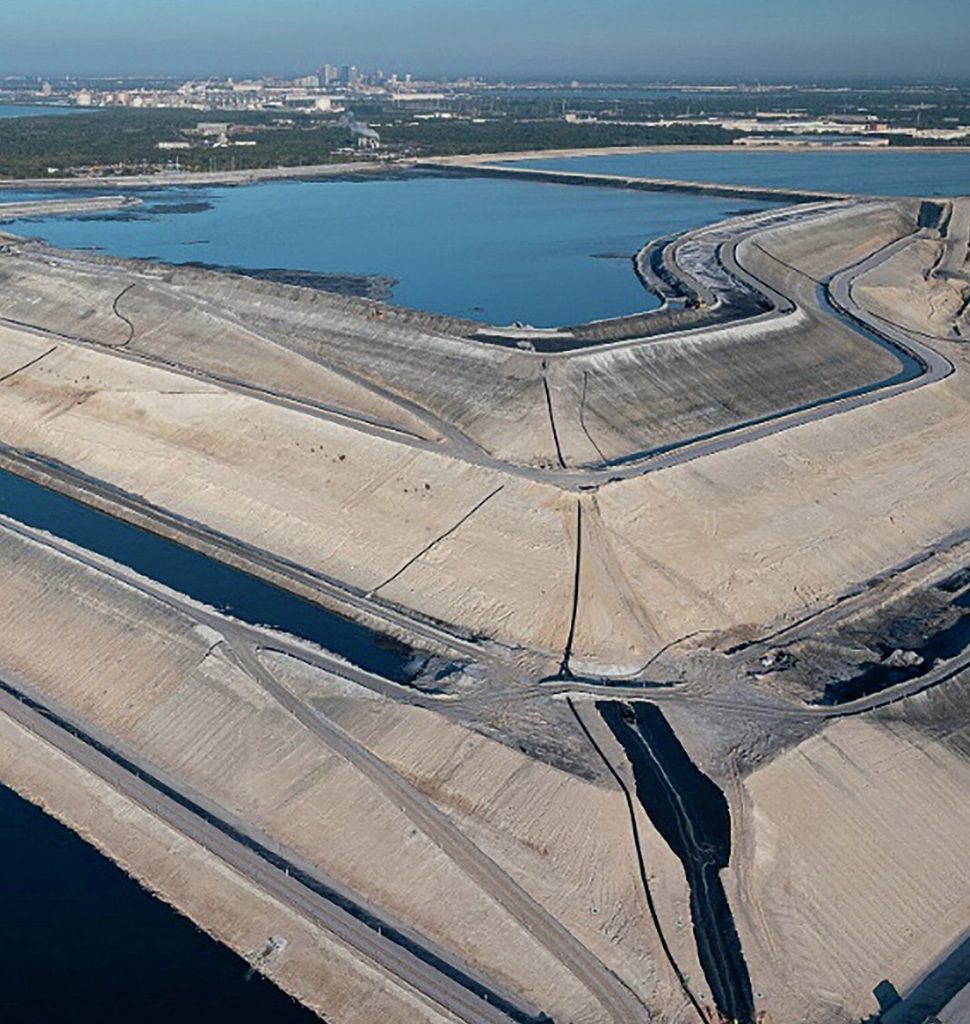
31 July 2023
Choosing the right phosphoric acid process
PHOSPHORIC ACID TECHNOLOGY
Choosing the right phosphoric acid process
In this review article, Hatch’s Jayden Ladebruk, Lyndsay Tran, Amelia Parrenin, and Edward DeRose outline the wide range of phosphoric acid production technologies, and discuss how industry challenges are influencing the choice of phosphoric acid process.
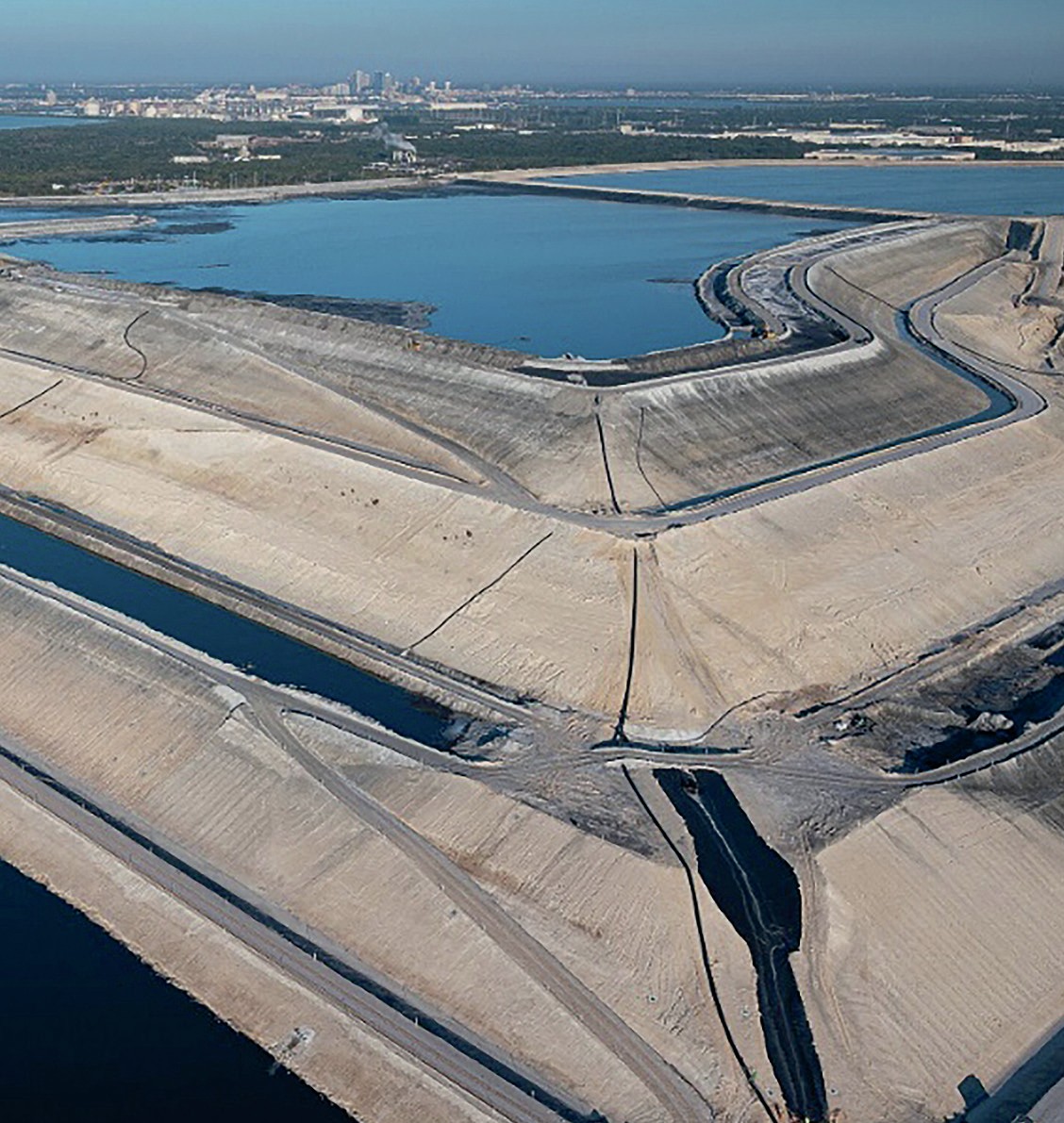
Phosphoric acid is a critical raw material consumed on a large scale globally for phosphate fertilizer production. Purified phosphoric acid is also manufactured for high-value food, feed, and industrial end-markets. Demand for phosphoric acid is also projected to increase in the future as it is a key ingredient in the production of lithium iron phosphate (LFP) batteries.
Over time, the industry has examined numerous alternative ways of commercially producing phosphoric acid in response to multiple challenges – such as evolving environmental regulations, declining phosphate ore grades, and tailings management.
Hatch has investigated the wide range of available technologies for phosphoric acid production to: firstly, understand the benefits of each process; and, secondly, help clients adapt to a constantly changing market and operating conditions. These technologies are primarily hydrometallurgical or pyrometallurgical processes.
This article summarises these investigations and in particular:
- Provides an overview of the main commercial process options for phosphoric acid production
- Highlights the various strengths and weaknesses of each production route.
The conventional production route
The standard wet process for phosphoric acid production is a hydrometallurgical method. Sulphuric acid is used to acidulate phosphate rock to produce phosphoric acid and a calcium sulphate (phosphogypsum) by-product.
The phosphogypsum (PG) generated contains different types and quantities of impurities, including radionuclides, due to the natural variations within phosphate rock deposits. While clean gypsum is a valuable by-product, commonly used in building materials, the presence of these impurities often prevents PG from being used or sold. PG therefore usually needs to be managed and stored as waste in phosphogypsum stack impoundments (see main photo).
Acidulation with sulphuric acid currently dominates the industry, accounting for nearly 90 percent of global phosphoric acid production 1 . This is due to the availability and lower price of sulphuric acid and the overall cost efficiency of the process.
Because this wet process route has been widely adopted and thoroughly investigated over many years, multiple process variations have been developed. Individual process variations are classified based on the calcium sulphate regime under which they operate – these being distinguished by their operating temperature and P 2 O 5 concentration.
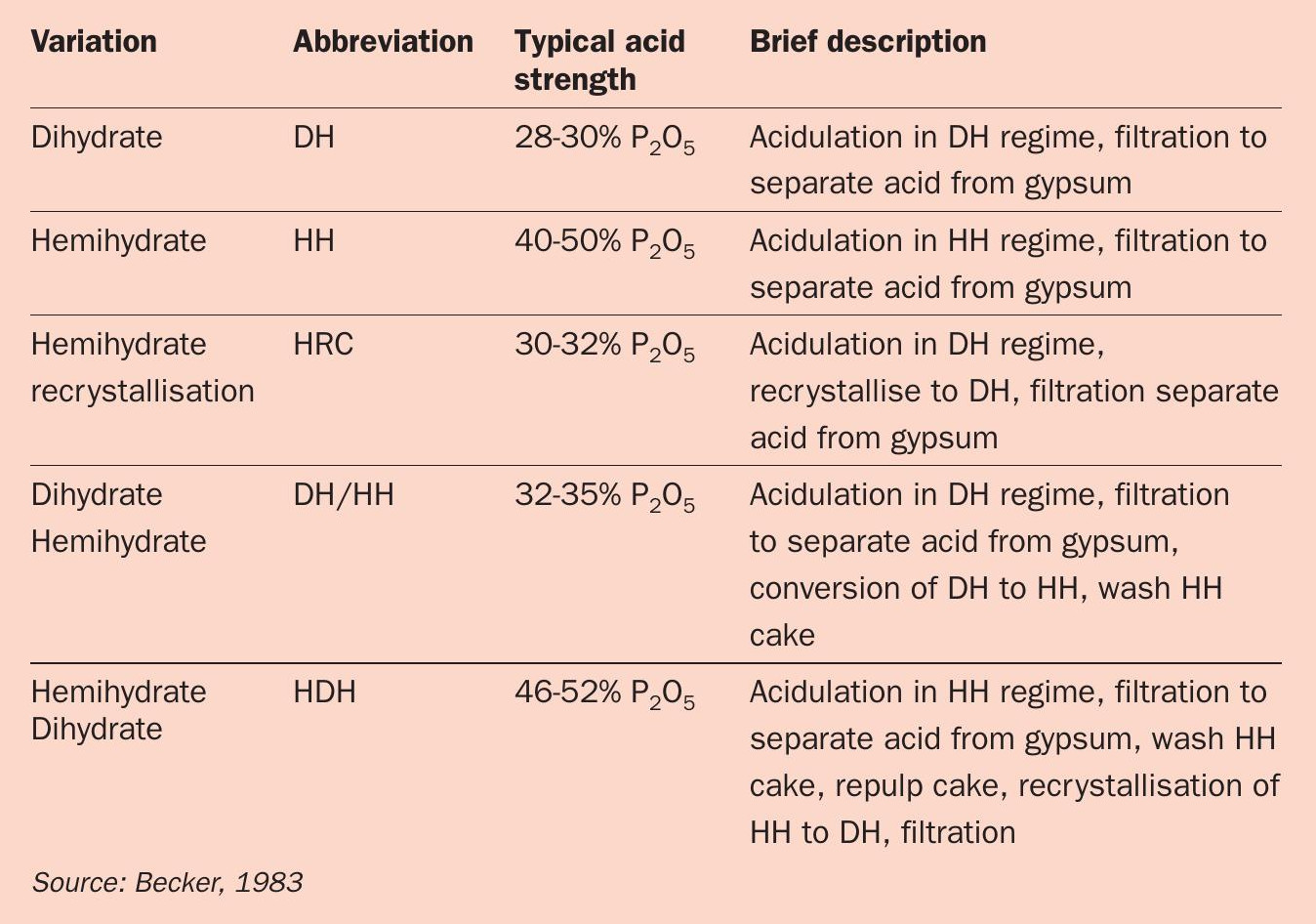
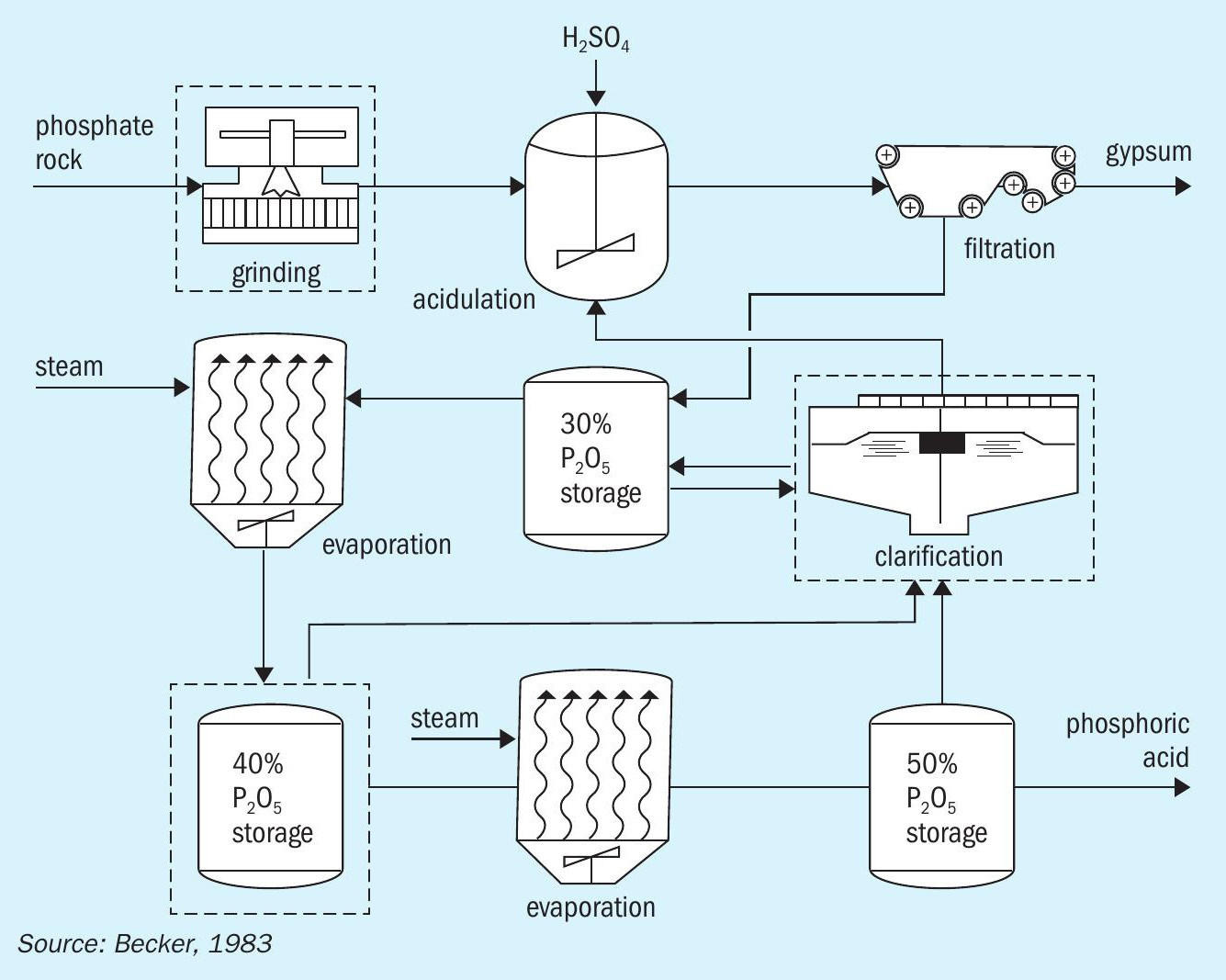
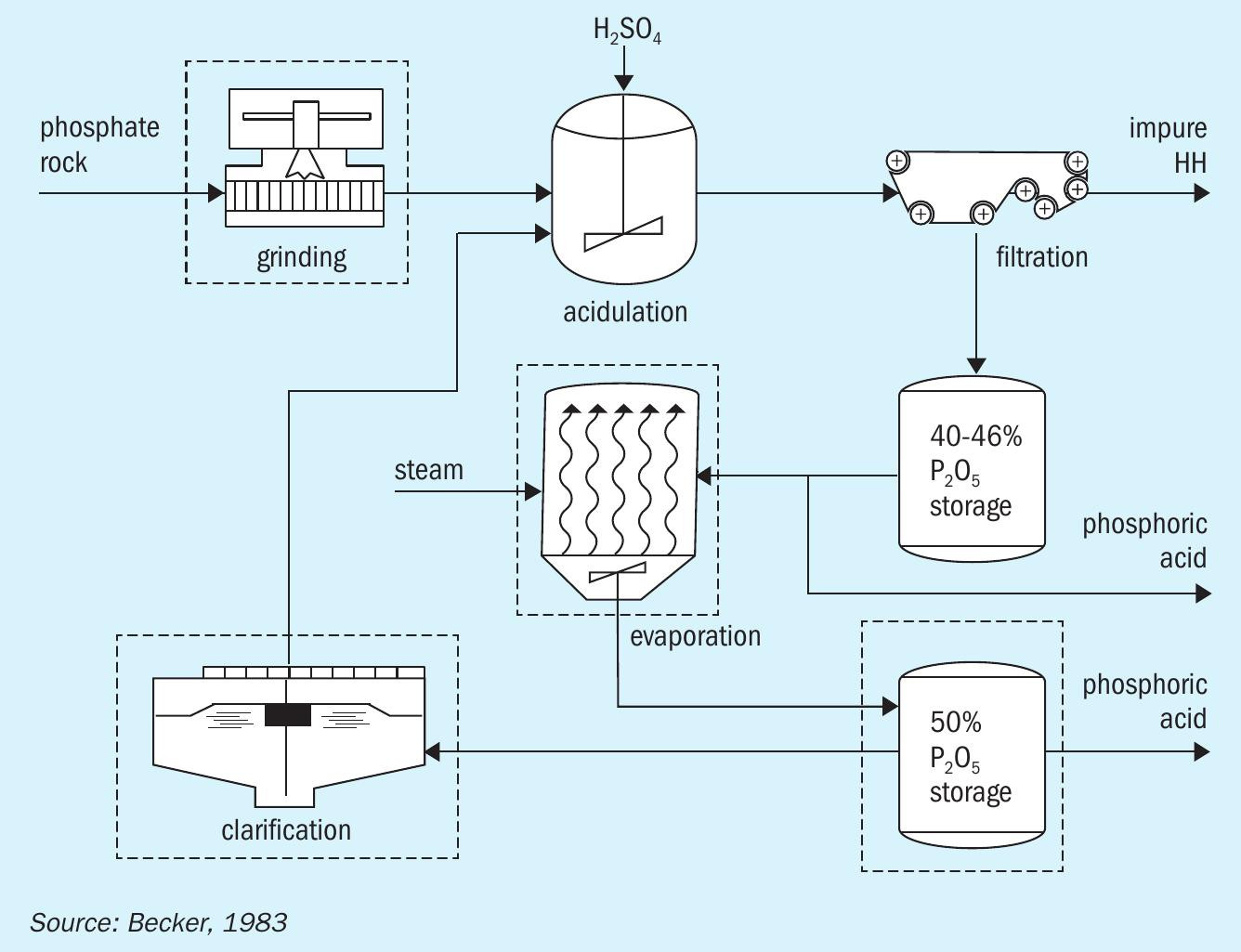
In general, processes operate under either a dihydrate or hemihydrate regime, with some processes alternating between the two.
The five most common process variations for acidulation with sulphuric acid, as summarised in Table 1, are:
- Dihydrate (DH)
- Hemihydrate recrystallisation (HRC)
- Dihydrate hemihydrate (DH/HH)
- Hemihydrate (HH)
- Hemihydrate dihydrate (HDH).
The DH route
The DH wet acid process involves acidulation under a dihydrate regime (Figure 1) and is currently the most common phosphoric acid production route. Acidulation is followed by filtration, clarification and, finally, multiple evaporation steps to achieve a stronger acid concentration.
“Acidulation with sulphuric acid currently dominates the industry, accounting for nearly 90 percent of global phosphoric acid production.”
The DH process has long been favoured due to advantages such as its:
- Simplicity of design
- Technological maturity
- Materials of construction – it only requires a lower grade of stainless steel
- Ease of operation.
Despite these advantages, the DH process generates the lowest strength acid, in comparison to the other process routes, typically accompanied by higher levels of aluminum and fluorine. This makes additional clarification steps necessary along with higher steam consumption for evaporation 1 .
Furthermore, the impure PG generated by the DH process requires relatively costly long-term managed storage within a lined impoundment.
The HH route
The HH process (Figure 2) has the following characteristics:
- Similar to the DH process in terms of its simplicity
- But generates a stronger (40-46% P 2 O 5 ) and purer acid (lower SO 4 , Al, and F)
- Can handle coarse rock, reducing both grinding requirements and power consumption
- Only needs a single filtration stage.
The HH process generally has lower evaporation and clarification requirements due to the high strength and purity of the acid generated. This reduces the overall capital cost by 20-25 percent versus the DH process. However, its higher acid strength means a larger filter area is required to avoid higher PG crystal lattice losses. Generally, higher temperature and acid strength conditions also make the HH process technically challenging to operate. The HH process, similar to the DH route, generates an impure PG by-product which requires stacking 1 .
The HRC route
The HRC process (Figure 3) involves acidulation in the hemihydrate regime followed by recrystallisation in the dihydrate regime. In comparison to the DH route, this process:
- Generates stronger acid at higher efficiency (97%) with lower reagent consumption
- Requires a single filtration stage with a lower filter area
- Produces a saleable PG by-product.
The HRC process does, however, require:
- A finer rock grind
- Sulphuric acid dilution
- A large recrystallisation volume
- Additional clarification and evaporation steps.
Furthermore, as its reaction stage is operated under the HH regime, the HRC process experiences many of the same operational difficulties as the HH process 1 .
The DH/HH route
The DH/HH process (Figure 4) involves acidulation in the dihydrate regime followed by filtration. The PG obtained is then recrystallised/dehydrated under the hemihydrate regime followed by another stage of filtration.
In general, the DH/HH route is:
- Highly efficient (98%)
- Technologically mature
- Flexible to different rock sources
- Produces a pure HH cake which can be used directly for plasterboard once rehydrated.
The main pitfalls of the DH/HH route are the need for 1 :
- Additional clarification and evaporation steps
- Two-stage filtration
- Optional rehydration of the HH cake to obtain clean gypsum
- Higher capital costs due to its extra processing steps and the use of sophisticated materials.
The Central Prayon Process (CPP) and Di-Attack Hemihydrate Filtration (DA/HF) process, both developed by Prayon Technologies, are two examples of the DH/HH route. A conventional DH plant can be upgraded to the DA/HF process (Fertilizer International 496, p52) by changing the plant digestion tank into a conversion tank with the addition of a steam sparger and sulphuric acid pipe 2 .
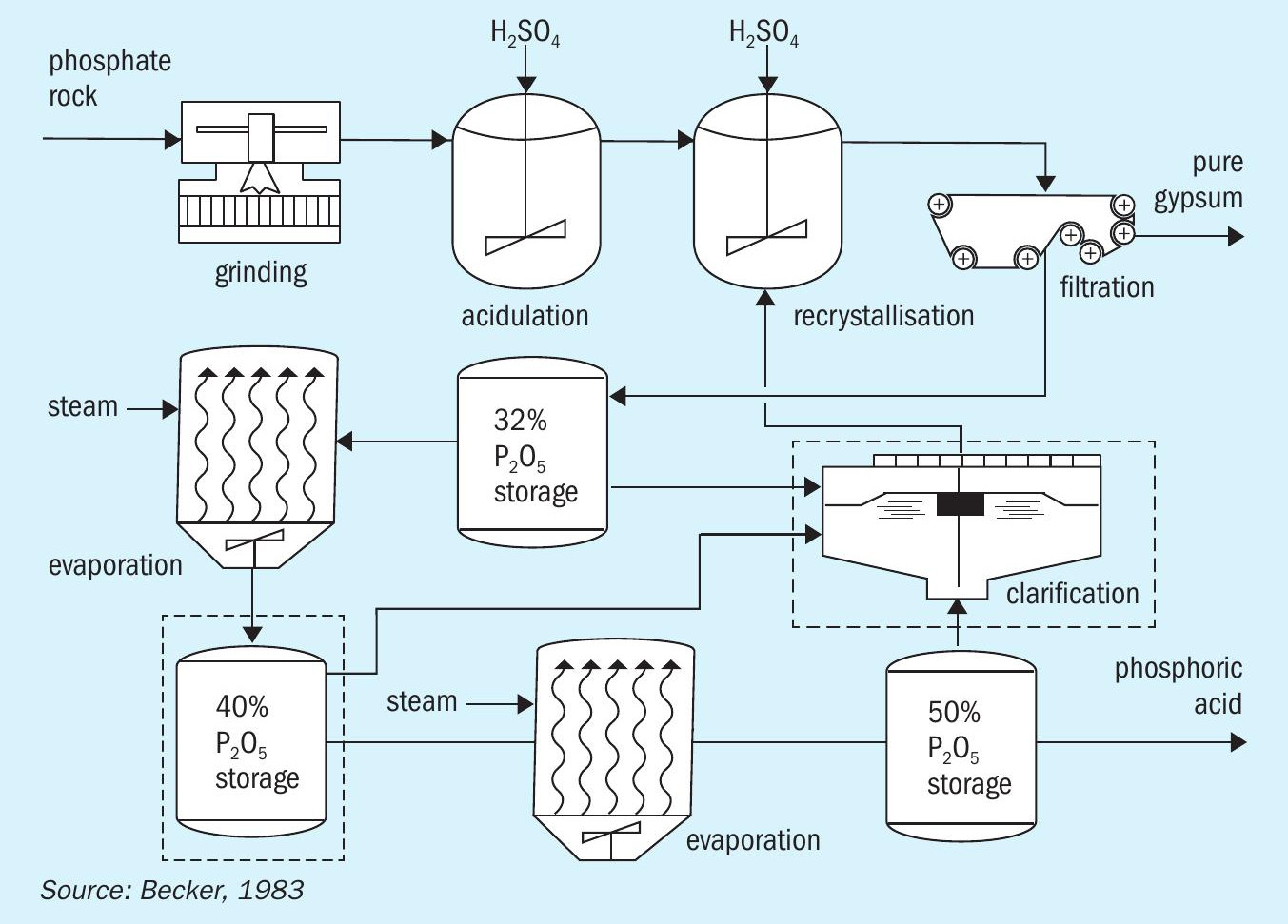
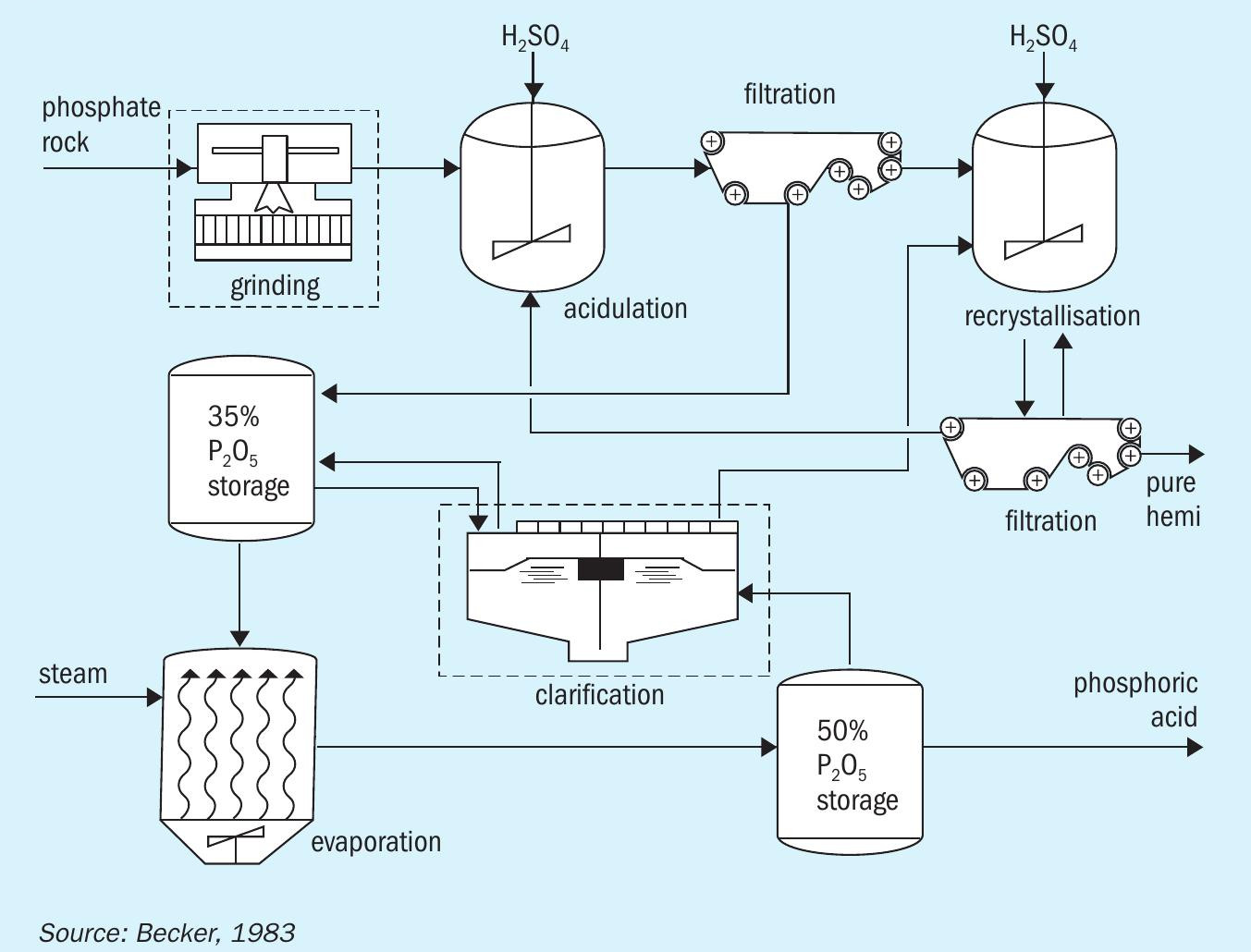
The HDH route
The HDH process involves acidulation in the hemihydrate regime, followed by filtration, then recrystallisation to the dihydrate regime, and finally another stage of filtration (Figure 5). The HDH route is notable for:
- Producing the strongest phosphoric acid concentration of all the sulphuric acid acidulation processes
- Its high efficiency (+98.5%)
- Its ease of operation
- Its low sulphuric acid consumption
- Generating saleable gypsum.
However, the HDH process also 1 :
- Requires two filtration stages
- Needs high-grade alloys
- Is technically challenging to design
- Has difficulty accepting igneous phosphate rock sources.
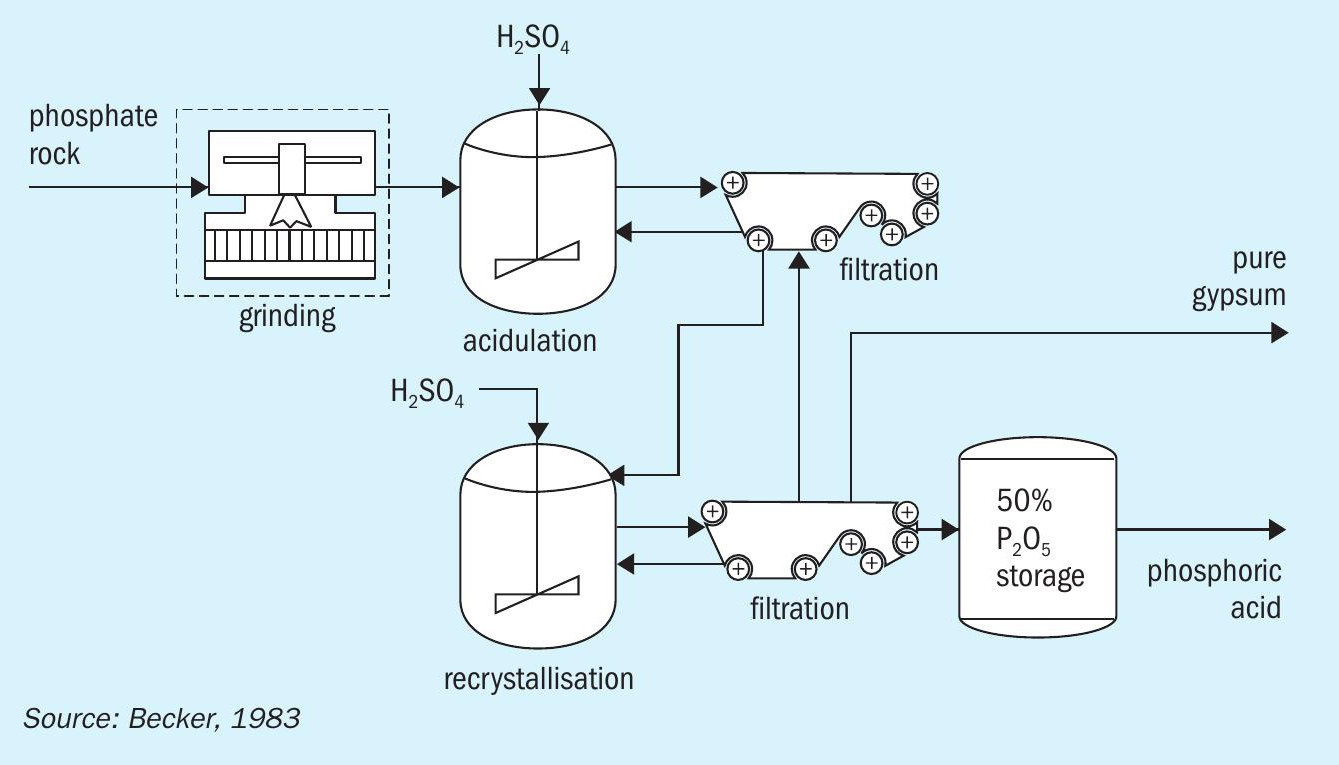
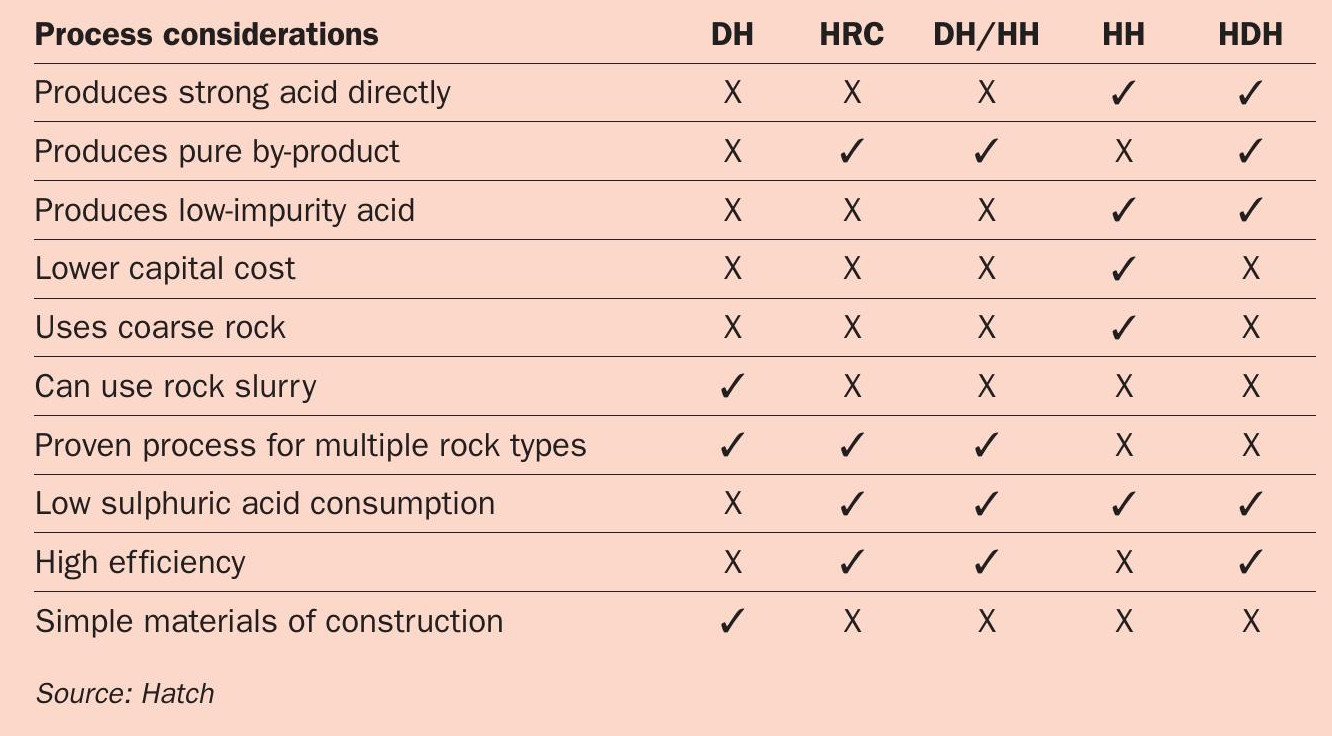
Sulphuric acid acidulation – process comparison
The five wet process routes each have their own set of advantages and disadvantages, as shown in Table 2. These factors must be taken into consideration and compared when selecting the right phosphoric production process for a given project and client.
Historically, acid strength, capital cost, and acid purity have been prioritised by phosphoric acid producers as determinants in process selection. Each client does, however, have a different set of process needs and requirements. Also, much more attention is now being given to the ability of a process to produce a pure and saleable gypsum by-product – due to cost pressures, increasingly stringent environmental regulations and land-use limitations.
Acidulation with hydrochloric acid
The acidulation of phosphate rock with hydrochloric acid is another commercial phosphoric acid production method. This offers several general advantages, including:
- The production of high-quality phosphoric acid
- Reduction in leaching time
- The ability to use lower-grade phosphate rock as a feedstock.
Acidulation with sulphuric acid produces large volumes of insoluble calcium sulphate. This then needs to be removed by filtration or other mechanical methods. The removal of soluble chloride-based by-products (mainly CaCl 2 ) generated by acidulation with hydrochloric acid, in contrast, involves very different treatment or extraction techniques. The hydrochloric acid route also requires the use of higher cost chloride-resistant construction materials.
The Israeli Mining Industry (IMI) process was the first hydrochloric acid-based technology to be developed commercially (Figure 6). This process digests phosphate rock with hydrochloric acid and filters the resulting slurry to remove insoluble compounds. The remaining liquor is then treated via a counter-current solvent extraction process. This selectively transfers phosphoric acid to an aliphatic solvent (e.g., isoamyl alcohol, n-butanol). The extract is then washed and distilled to separate the phosphoric acid from other components (water and HCl) which are recycled. The IMI process generates concentrated phosphoric acid (95% H 3 PO 4 , 69% P 2 O 5 ) as a final product 3 .
With ore grades declining, acidulation with hydrochloric or phosphoric acid is becoming valued as a pre-purification process that converts impure phosphate rock to either dicalcium phosphate (DCP) or monocalcium phosphate (MCP), respectively. Usefully, the addition of a pre-purification step can eliminate the need for beneficiation from the flowsheet.
Prayon’s Ecophos process is one example of a pre-purification process – and is the most widely adopted hydrochloric acid-based technology in the phosphates industry. With this technology, run-of-mine phosphate rock is digested by dilute hydrochloric acid. The resulting slurry is then filtered to remove any insoluble components. In the next step, the filtrate is neutralised with calcium carbonate or calcium hydroxide to produce DCP. This can be treated with dilute HCl or used as the feed for a dihydrate production plant to yield a relatively high quality phosphoric acid 4 . The hydrochloric acid from the process can be regenerated by treating the calcium chloride-rich cake with sulphuric acid.
Phosphoric acid acidulation
Acidulation with phosphoric acid can also be used as a pre-purification process. This is used to generate MCP via the acidulation of phosphate rock with an excess of recycled phosphoric acid. The P 2 O 5 acid to P 2 O 5 rock weight ratio can range from 8:1 to 15:1. This process can operate in any gypsum regime as acidulation occurs between 45-100°C 5 .
Prayon’s GetMoreP process is a leading example of an MCP pre-purification process. It generates a saleable gypsum product by removing heavy metals and radioactive elements 6 .
Patents for phosphoric acid acidulation generally exploit the fact that many impurities (metal sulphates, silica, fluoride, and iron and aluminium phosphates) have a low solubility in the MCP solution and can therefore be easily filtered out 5 . Some patents also incorporate an impurity removal step. These use reagents (KH 2 PO 4 /SiO 2 , barium salts) or flocculants to target and remove impurities such as fluoride, radionuclides, alkali metal ions and silicates from the MCP solution 7, 8, 9 .
Generally, by pre-purifying to MCP, patents claim that the subsequent wet production process should produce phosphoric acid at high concentration (35-55% P 2 O 5 ) and generate cleaner gypsum – even when using lower grade phosphate rock as a feedstock.
One of the main setbacks of acidulation with phosphoric acid is, however, its technological immaturity. Although this process has been researched over the last 50 years, no commercial-scale plants using this technology are operating currently. Additionally, large recycle volumes of phosphoric acid are needed to maintain excess acid in the acidulation step. This drives up the size of equipment and therefore capital costs.
Nitric acid acidulation
Phosphate rock can also be acidulated with nitric acid. The nitric acid route – generally known as the nitrophosphate process – dissolves the rock in 50-60 percent nitric acid to form phosphoric acid and calcium nitrate.
The calcium nitrate generated by the process must be removed due to its hygroscopic nature. This is typically accomplished via cooling crystallisation. Solvent extraction, although technically feasible as an alternative to crystallisation, has yet to be commercially adopted in the nitrophosphate process 3 .
The filtrate from the process mainly consists of phosphoric acid, some unreacted nitric acid, and traces of calcium nitrate. This mixture can be neutralised with ammonia to produce a compound fertilizer. The calcium nitrate obtained, while it can be upgraded to calcium nitrate fertilizer, is often converted to ammonium nitrate and calcium carbonate instead by treatment with carbon dioxide and ammonia 10 .
The main upsides of the nitrophosphate process are that, firstly, it does not produce large quantities of hard to manage phosphogypsum and, secondly, its by-products have value as fertilizers. However, the soluble calcium nitrate by-product that is generated, in comparison to insoluble gypsum, requires more costly and operationally challenging separation methods such as crystallisation or solvent extraction (Figure 7).
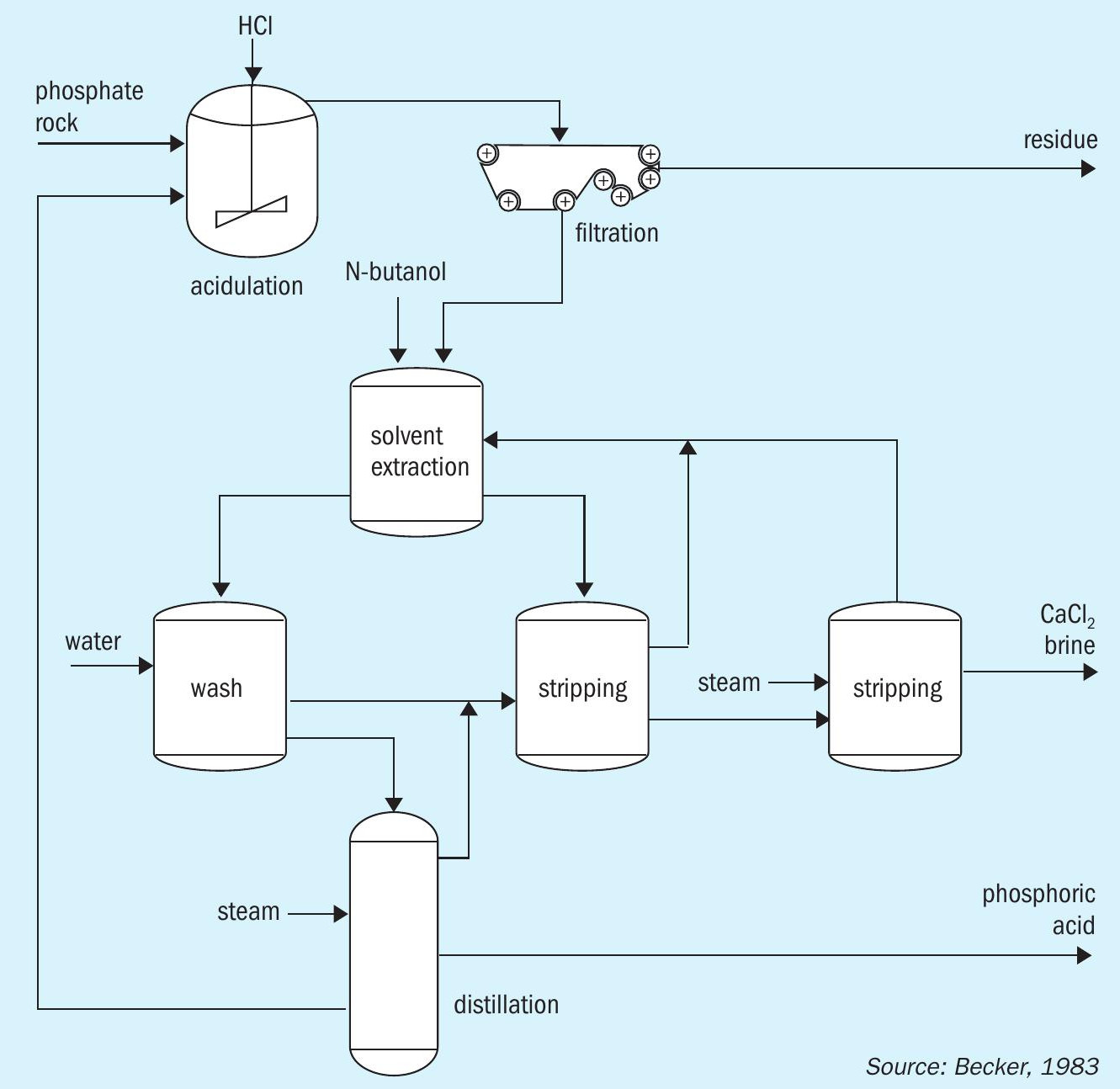
Thermal acid process
The thermal acid process was the original production method for phosphoric acid, being in commercial use from the 1930s to the 1950s. Thermal acid production subsequently went into decline, however, as the process could not compete with the lower operational costs of wet processes such as the DH route.
The process involves three major steps: combustion, hydration, and demisting. In the combustion step, phosphorus is oxidized in ambient air in a combustion chamber at a temperature range of 1,650-2,760°C to form phosphorus pentoxide. The phosphorus pentoxide is then hydrated with dilute phosphoric acid (H 3 PO 4 ) or water to produce strong phosphoric acid liquid. The phosphoric acid is demisted from the combustion gas stream, usually with high-pressure-drop demisters. The concentration of phosphoric acid produced from the thermal process normally ranges from 50-62 percent P 2 O 5 .
The thermal acid process can accept low grades of phosphate rock, and efficient plants can recover up to 99.9 percent w/w of the combusted elemental phosphorus as a phosphoric acid product. The product acid is much purer than acid produced by the wet process, and the waste slag from the furnace is relatively benign in comparison to wet process phosphogypsum. The thermal acid process is, however, very energy intensive and costly. With limited heat integration opportunities, an enormous amount of heat is lost to the environment.
Dry (electric-furnace) process
The electric furnace process uses electric resistance heating to generate elemental phosphorus vapour via a sustained reduction reaction from a mixture of phosphate rock, silica, and calcined petroleum coke. The reduction reaction takes place at 1,600°C and is highly endothermic. The phosphorus vapour generated is condensed to liquid phosphorus metal and is then oxidised in a phosphorus furnace to form P 4 O 10 gas. A hydrator finally converts this gas into highly pure and concentrated (52-62% P 2 O 5 ) phosphoric acid 12 .
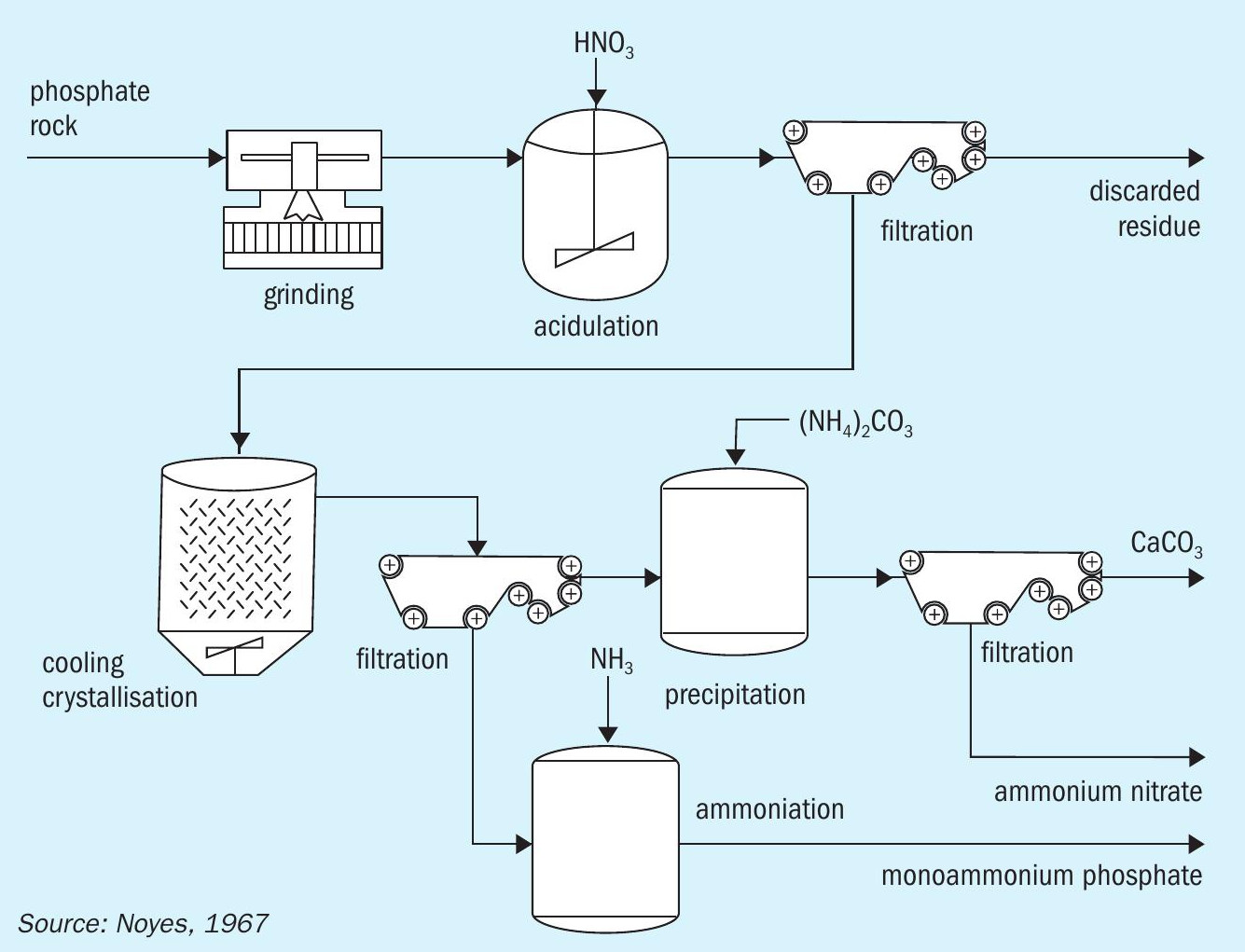
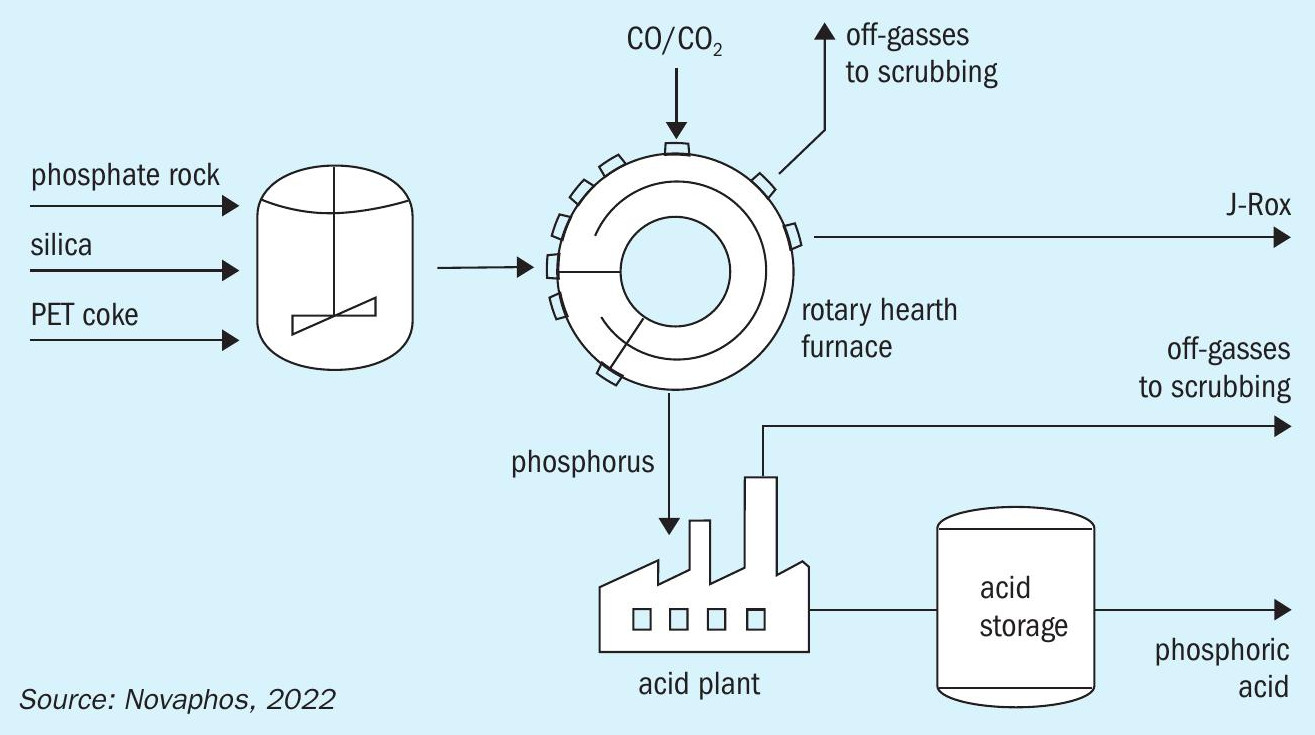
The phosphoric acid produced using the electric furnace process is of high purity and the primary waste by-product is inert slag. The furnace process can also accept low-grade phosphate rock, if the main impurity is silica, and the recovery of P 2 O 5 is also high – usually 86-92 percent of the furnace charge.
On the downside, the electric furnace process has a high capital cost and suffers from poor thermal efficiency. This is due to the lack of heat integration between the highly endothermic phosphate reduction reaction and the highly exothermic phosphorus oxidation reaction (to produce P 4 O 10 gas). Because of this, the electric furnace process is used almost exclusively to produce phosphorus and phosphoric acid for high value end-markets such as industrial chemicals, insecticides, detergents, and food or animal feed additives 13 .
Novaphos process
In the last decade, there has been renewed interest in dry phosphoric acid production processes spurred by new market uses for technical-grade phosphoric acid.
The Novaphos process (Figure 8) is one example (Fertilizer International 509, p52).
This thermal method produces phosphoric acid through the carbothermal reduction of phosphate rock with silica flux and petroleum coke in a rotary hearth furnace 14 . Elemental phosphorus gas is formed in this furnace, which is then re-oxidised and reacted with water in an acid plant. This generates high quality SPA (super phosphoric acid) grade acid at up to 68 percent P 2 O 5 . The design configuration used by Novaphos offers operational improvements and capital cost reductions compared to the previous dual-kiln technology.
Although the Novaphos process is an improvement on the original thermal acid process, it remains an energy-intensive and expensive process. Nevertheless, the process can accept low grade phosphate rock, including mine tailings and ore deposits that are too impure for conventional wet acid production processes.
Also, unlike the wet process, the Novaphos process produces a benign, saleable co-product known as J-Rox. This largely consists of calcium, magnesium, and iron silicates and has several valuable applications 14 including use as:
- A replacement for cement in concrete or as a supplementary cementitious material
- A porous, fine aggregate to help with internal curing
- A source of plant available silicon in fertilizers.
The acidulation of phosphate rock with sulphuric acid has been the conventional phosphoric acid production process for decades. It has been widely adopted in the phosphoric acid industry due to its relatively low capital and operating costs. The five main process variants (DH, HH, DH/HH, HDH and HRC) each have their own advantages and disadvantages – including (but not limited to) acid strength, by-product purity, and cost.
Conclusions
Other acidulation methods with alternative acids such as hydrochloric acid (HCl), nitric acid (HNO 3 ), and phosphoric acid (H 3 PO 4 ) are of increasing interest. These have the potential to produce cleaner and/ or stronger phosphoric acids from the filtration stage. Additionally, given that phosphogypsum (PG) stacking is becoming a land management and environmental concern for producers, chloride or nitrate-based processes are potentially more attractive as they produce an entirely different by-product altogether.
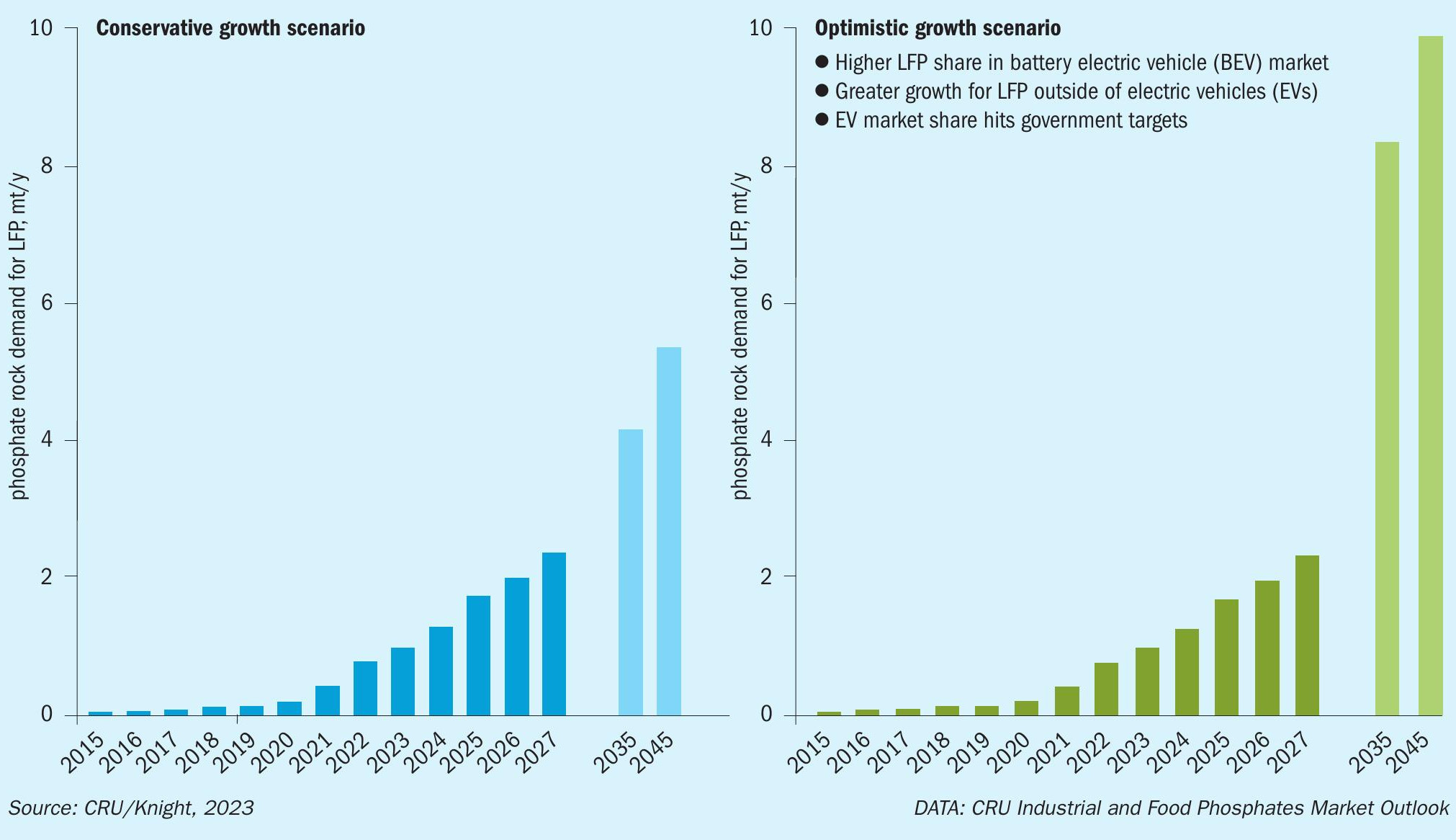
The choice of acidulation process is often determined on the local pricing, availability and/or sourcing of acids. HCl methods, for example, can consume excess HCl generated by sulphate of potash (SOP) or chlor-alkali production plants. Other producers, meanwhile, may already have access to sulphuric acid, which would make sulphuric acid and phosphoric acid acidulation methods more attractive. Moreover, existing NPK fertilizer producers are likely to have access to nitric acid (or its derivatives), making the nitric acid acidulation route an attractive production choice.
The potential to adopt pyrometallurgical processes for phosphoric acid production is heavily influenced by local energy pricing, and regional/national greenhouse gas (GHG) emissions regulations. Typically, thermal methods will be favoured for end applications where a high-grade phosphoric acid is required (e.g., pharmaceuticals or foods), or when elemental phosphorus is the desired product.
Another factor is the constantly shifting global market for phosphoric acid. Demand for phosphoric acid is projected to increase in future (Figure 9) due to the growing global need for fertilizers and the rapidly rising LFP battery market 15 .
The need to raise output and meet other industry challenges are forcing phosphoric acid producers to look at alternative H 3 PO 4 production processes. While some processes produce a cleaner or different by-product, and/or a higher strength phosphoric acid, the choice of phosphoric acid production method is ultimately driven by the needs and priorities of each individual producer.
Hatch is able to take its comprehensive baseline knowledge of all the different phosphoric acid production technologies – as described in this article – and support phosphate industry clients, as they adapt to the ever-changing market, by coupling this knowledge with its industry-leading expertise and track record in process design and engineering.
References