Nitrogen+Syngas 385 Sept-Oct 2023
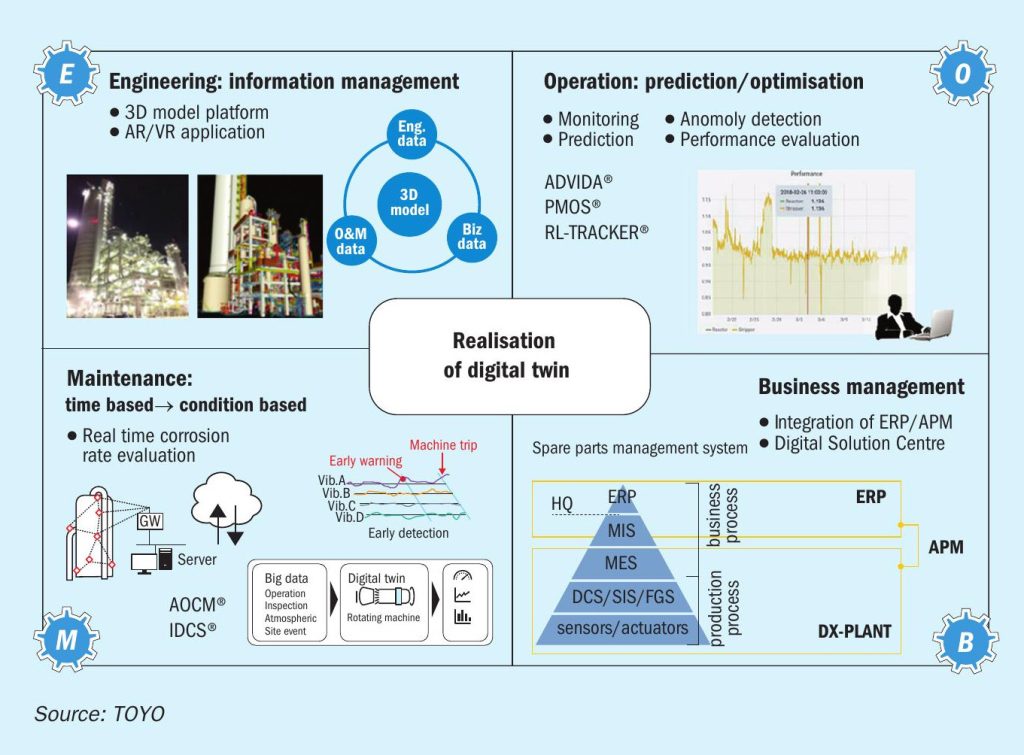
30 September 2023
A digital twin across the plant lifecycle
DIGITALISATION
A digital twin across the plant lifecycle
TOYO’s digital twin concept combines its unique digital twin at both the project execution stage and the commissioning stage, and when used in conjunction with its proprietary process simulator it can predict the whole plant lifecycle.
In 2016, Toyo Engineering Corporation (TOYO) launched a digital transformation service named DX-PLANT® in the field of chemical and industrial plants by leveraging IoT and big data analysis technology. Through the development of DX-PLANT® , TOYO has provided unique solutions featuring various fields and reported its progress in previous issues of Nitrogen+Syngas. In this article, TOYO addresses recent updates to TOYO’s digital twin concept across the total plant lifecycle for fertilizer plants.
TOYO’s service is characterised by the realisation of a comprehensive digital twin across the entire plant lifecycle spanning from the engineering, procurement, and construction (EPC) phase to the operations and maintenance (O&M) phase. In line with the “Advanced EPC Operation” strategy of its mid-term management plan, TOYO is working diligently to execute digital projects through the digitalisation of EPC operations. The EPC digital twin has been created for implementation of advanced work packaging (AWP) in projects.
The EPC digital twin is based on the EPC-hub that integrates data from various systems related to EPC execution. The EPC digital twin enables TOYO to optimise the project as a whole, to make project execution more resilient through agile replanning in response to unexpected irregularities, and to realise future predictions. As an EPC contractor as well as a urea process licensor, TOYO believes that it will be able to provide the EPC digital twin to its clients as an asset model as described in the following section.
TOYO’s digital twin in the EPC phase transitions and grows during various phases of the project, such as basic design, detail design, procurement/construction and commissioning phases, and after the project is completed, the digital twin created during the EPC phase will be handed over to the O&M phase digitally. TOYO has already developed its own DX-PLANT® , which is the digital solution for the O&M phase, and the EPC digital twin created during the EPC phase will be integrated into DX-PLANT® and utilised during the O&M phase (see Fig. 1).
The use and transition of the EPC digital twin in each phase is described below:
- During basic design, various process systems and components are digitised using an intelligent P&ID (2D) in which the process system information is set up as a digital twin to perform necessary studies and maintain design consistency.
- At the time of layout design during detail design, verification and examination are conducted on the digital twin (engineering 3D model), which is based on the basic design phase digital twin (intelligent P&ID) providing consistency.
- In the procurement and construction phases, the digital twin created in the design phase is further developed into a virtual construction model that is linked to the project schedule. In this digital twin (virtual construction model), the design document schedule, procurement schedule, and construction schedule are integrated into a so-called “4D model”, and study and verification of the plans are repeated virtually on the digital twin (4D model) for alignment.
- In the pre-commissioning and commissioning phases, the digital twin developed from the virtual construction model is used to plan, verify, and review test blocks, taking into account actual construction progress, which is not possible with 2D models.
- The digital twin data created through to project completion is then digitally handed over, reducing the end user’s cost and schedule for “information handover to operation”.
Structured in this way, the EPC project digital twin is utilised by TOYO as an integrated project management tool to optimise the project.
The structure and TOYO’s approach for the digital twin in O&M is as follows.
First, TOYO defines the digital twin as consisting of an asset model and an operation model, comprising a physical model and a data driven model.
The asset model manages the design information including the 3D models necessary for O&M and data such as maintenance records. The asset model is based on the digital twin created during the EPC phase, and further developed with e.g., maintenance records or information during the O&M period.
The operation model reproduces the plant operation virtually. It consolidates the operation data in a virtual space and then utilises the data with the physical model, which consists of a process simulator developed during the EPC phase. Using a process simulator enables remote monitoring support or performance monitoring. In the early stages of plant operation, insufficient operation data are available, therefore applications such as predictions from plant operation data cannot be developed.
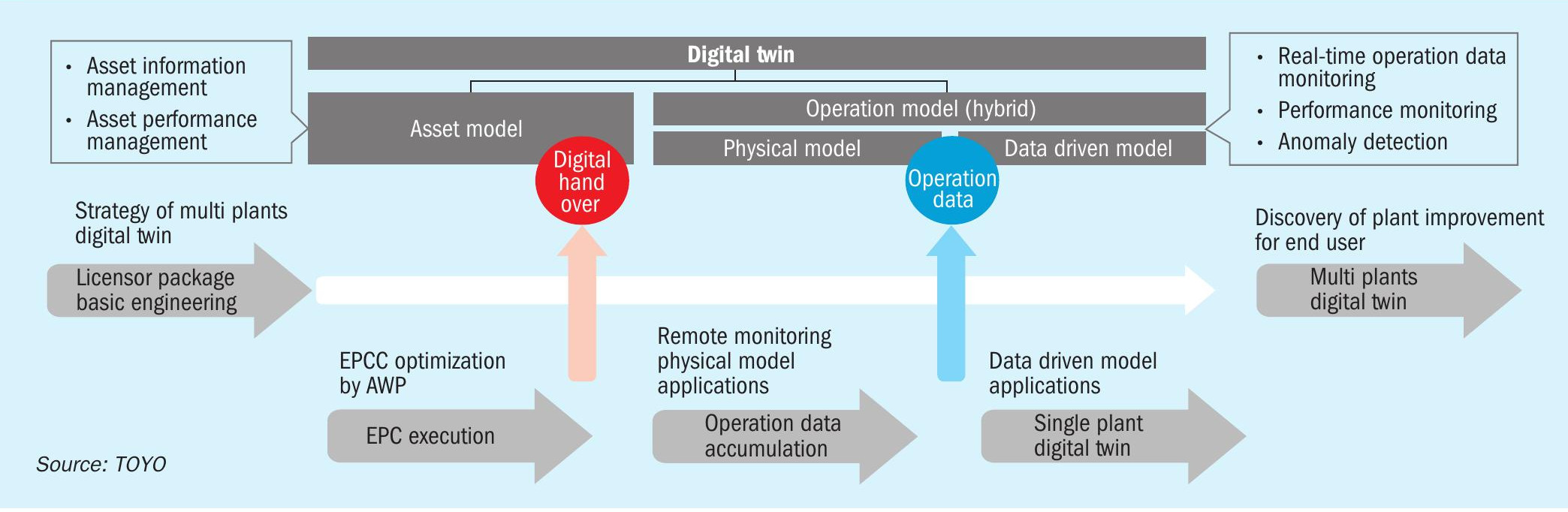
However, once sufficient operation data has been accumulated in the operation model, it is possible to create a data-driven model to fine tune the process simulator to fit the simulation to the operating plant, create an anomaly detection system and soft sensors. In other words, it is the completion of the operation model (hybrid) and digital twin.
It should be noted that TOYO tailors its proprietary process simulator for each urea plant as a result of the engineering. It can be used to trace plant conditions very accurately and enables a reliable digital twin to be handed over to the owner even when sufficient operation data is not available. After accumulating data, it can become the true precise digital twin.
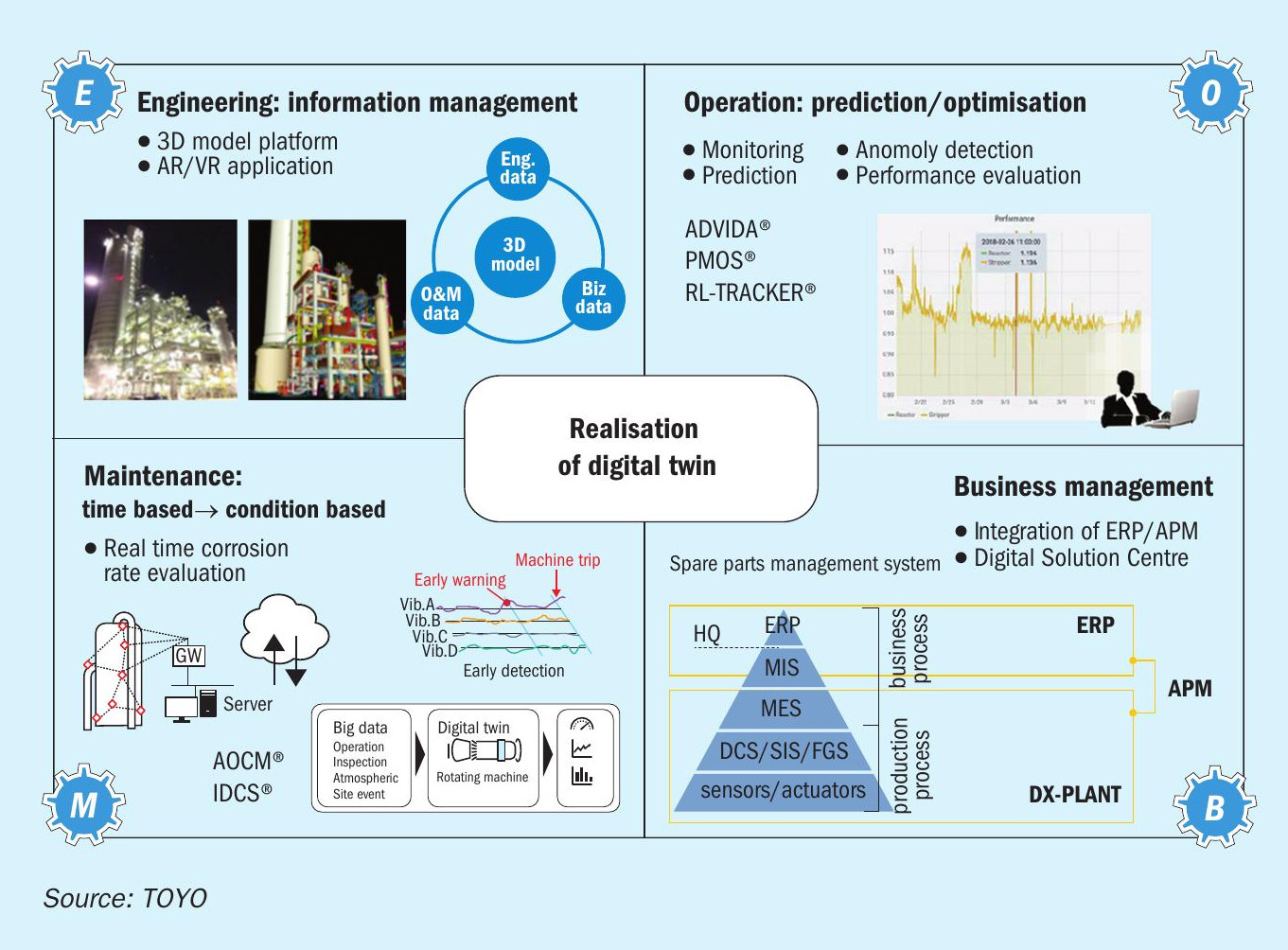
TOYO’s system can be used for single or multiple plants. By utilising TOYO’s digital twin for multiple plants, it is possible to compare the performance of a plant with others for its evaluation, identification of issues, and to make improvements in a shorter timeframe.
In this way, TOYO optimises EPC through the EPC digital twin, seamlessly handing over the digital twin to O&M, and realises O&M improvements using the digital twin as a process licensor.