Sulphur 408 Sept-Oct 2023
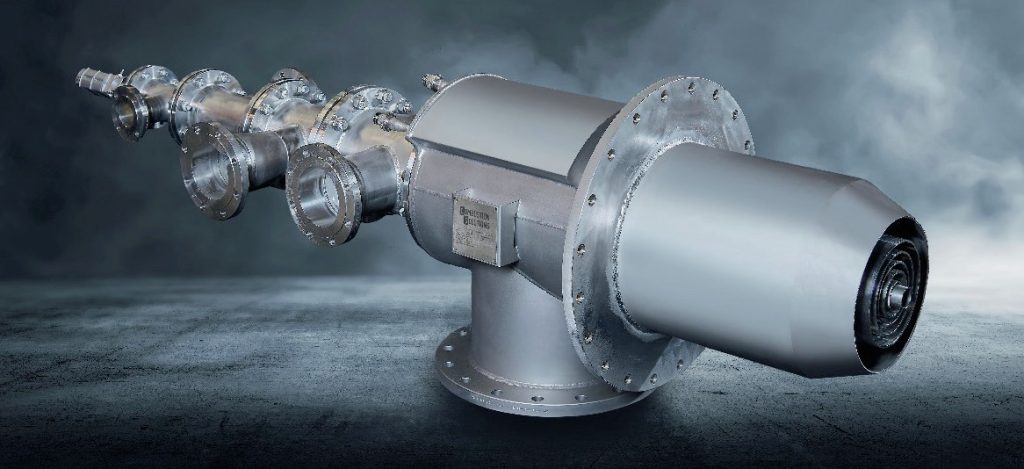
30 September 2023
A novel combustion solution
SPENT ACID REGENERATION
A novel combustion solution
A new burner design for the combustion of natural gas with either combustion air or pure oxygen as the oxidiser has been developed by CS Combustion Solutions. The new Oxijet® -Burner has been designed to perform both start-up and main operation functions with one burner. The key objectives, challenges, and burner design considerations are discussed.
The background to the development of the new Oxijet® -Burner started with a request for the supply of natural gas burners for a new greenfield spent acid regeneration plant for both the start-up process and the main operation. However, the main operation of this plant was to be designed as a pure oxygen firing case to increase the efficiency of the combustion process.
Initially, one start-up air burner and two main oxygen burners were requested. However, this setup would lead to complications during the main operation due to the startup burner not being in operation in the hot chamber (damage to the burner). Also, cooling the burner with air or removing it after the start-up process was not ideal, due to the loss of efficiency of the overall process and the potential danger to personnel working close to the hot chamber and sealing of the big opening after burner removal.
Challenges
The main challenges were:
- Dry-out and start-up process:
– maximum required heat input 11 MW;
– cannot be done with natural gas and oxygen as oxidiser due to wet flue gas;
– needs to be done with combustion air as oxidiser for proper dry-out.
- Main operation:
– maximum required heat input for main operation 32.8 MW;
– to be done with oxygen as oxidiser to maximise efficiency.
- Required space on front wall of chamber for burners to be minimised (number of burners and placement).
- Find a feasible solution with a dedicated start-up burner and two main burners or cover both operation cases with one or multiple burners.
- Ensure a feasible turn-down ratio for both operation cases, with at least 1:10 for the main operation case.
Aims
After brainstorming about the issues with a dedicated start-up burner, which would not be in operation during the main operation, CS discarded the idea, regarding it as not sensible for a new plant. The goal was therefore to design a burner system, which would be capable of operating with both combustion air and/or oxygen as the oxidiser for the combustion of natural gas.
A new burner design
In order to find the best solution, different burner designs were analysed and the operating conditions were reviewed.
The typical design of oxygen burners and air burners offered on the burner market are inherently different. Oxygen burners are typically jet-type burners with high nozzle velocities to induce the recirculation of flue gas back to the flame. Air burners are usually bigger and operate with lower nozzle velocities and often with swirl bodies to ensure good mixing of fuel and oxidiser. Operating an air burner with oxygen would not be sensible as oxygen reacts very fast with the fuel and would lead to unstable flame conditions and likely damage the burner. On the other hand, a jet-type burner operated with combustion air instead of oxygen would not be feasible due to flame instability and eventual blow out of the flame. However, finding a way to stabilise the flame would provide a viable design approach.
Designing the burner with only one fuel stage for both the start-up and the main operation case would lead to a poor turn-down ratio during the start-up case, but splitting the load and designing the burner with multiple stages would help to support a higher turn down ratio for both operating scenarios.
Lastly, deciding between one big central burner or multiple smaller burners was concluded by reviewing that jet-type burners have slim long flames, and it therefore makes most sense to spread out the heat load via two burners. In this way, proper heat distribution in the chamber can be ensured, while simultaneously minimising the required space on the chamber head.
CFD analysis of the burner design
Multiple CFD analyses were done to verify the dual-fuel stage design of the two burners. The images in Figs 1 and 2 show the temperature and SO2 distribution of the burner design at different sections of the chamber.
Close to the burners is the hottest part of the chamber with good recirculation of flue gas back to the burner flames. Secondary oxygen and spent acid are injected in the first part of this chamber from the top and sides, respectively. At the end of the chamber the temperature distribution is almost completely homogenous at around 1,100 °C.
The results
As a result of the burner design review and CFD analyses a completely new burner design was developed for combustion of natural gas with either combustion air or pure oxygen as oxidiser.
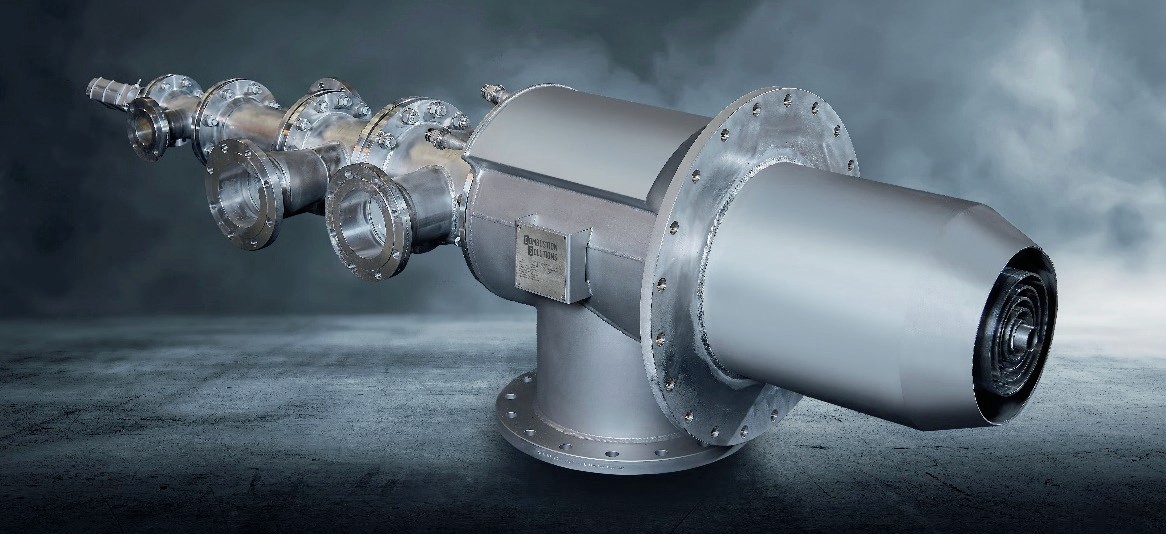
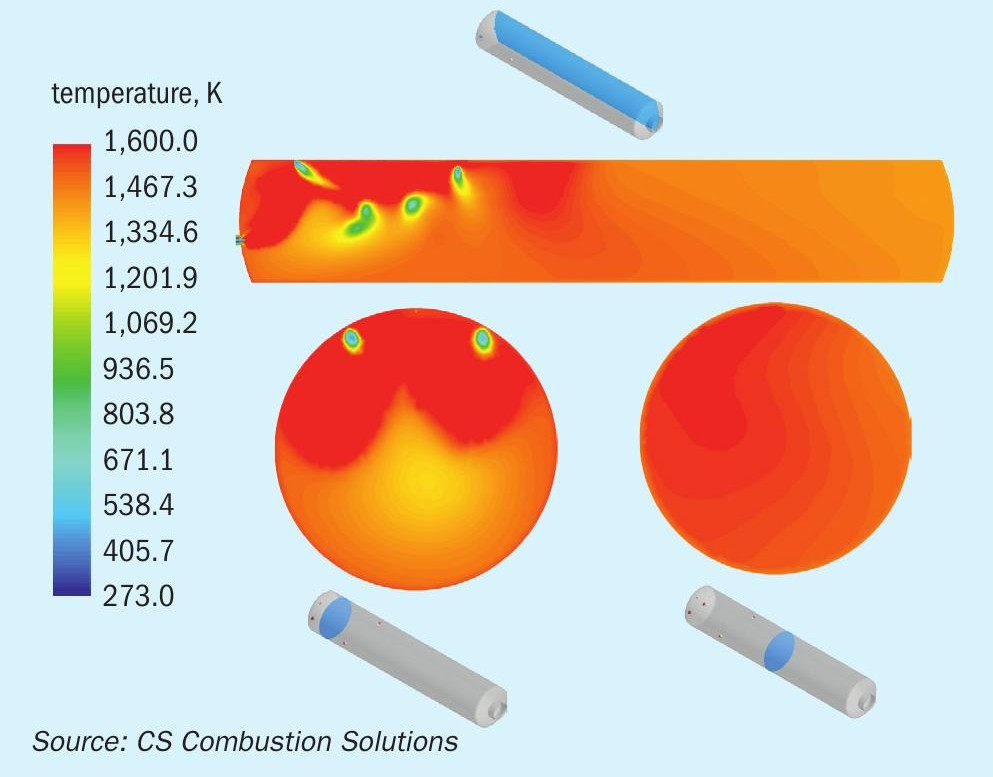
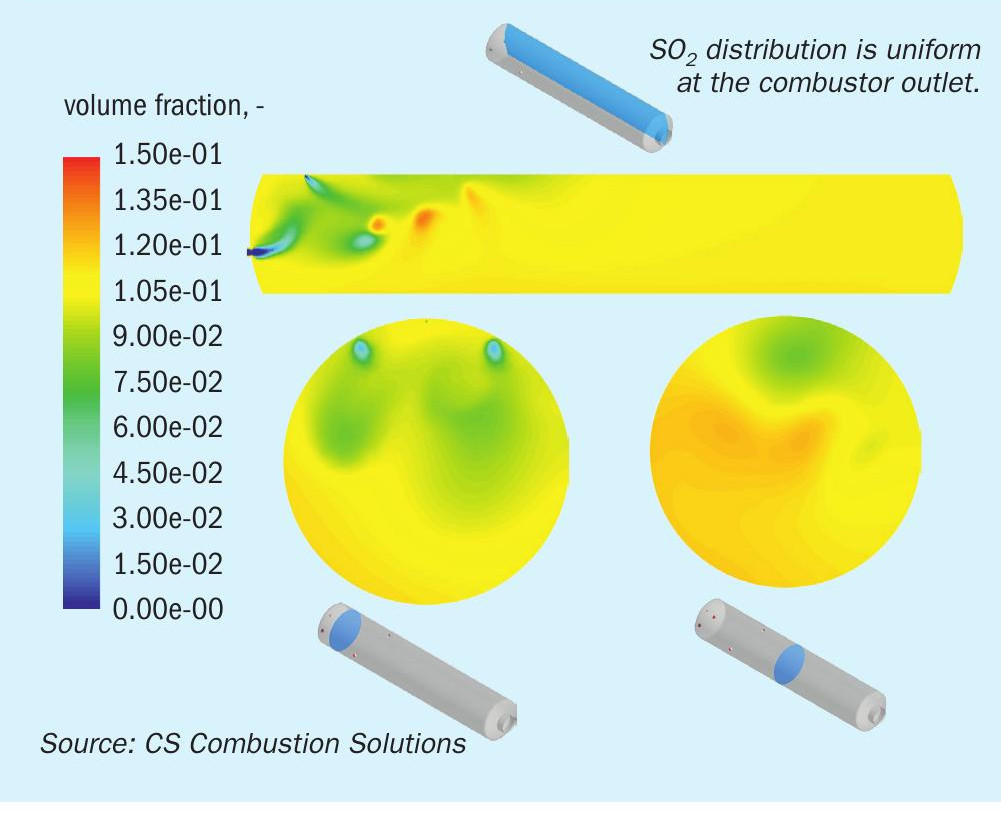
The burner can also be operated with enriched air, making it a viable solution for existing plants to reduce operating costs or increasing production capacity. Removal of the burner after start-up procedure is not necessary. The burner has a simple and low maintenance procedure with an exchangeable lance design. Flame monitoring is performed via three UV and IR flame scanners installed on the burner.