Fertilizer International 516 Sept-Oct 2023
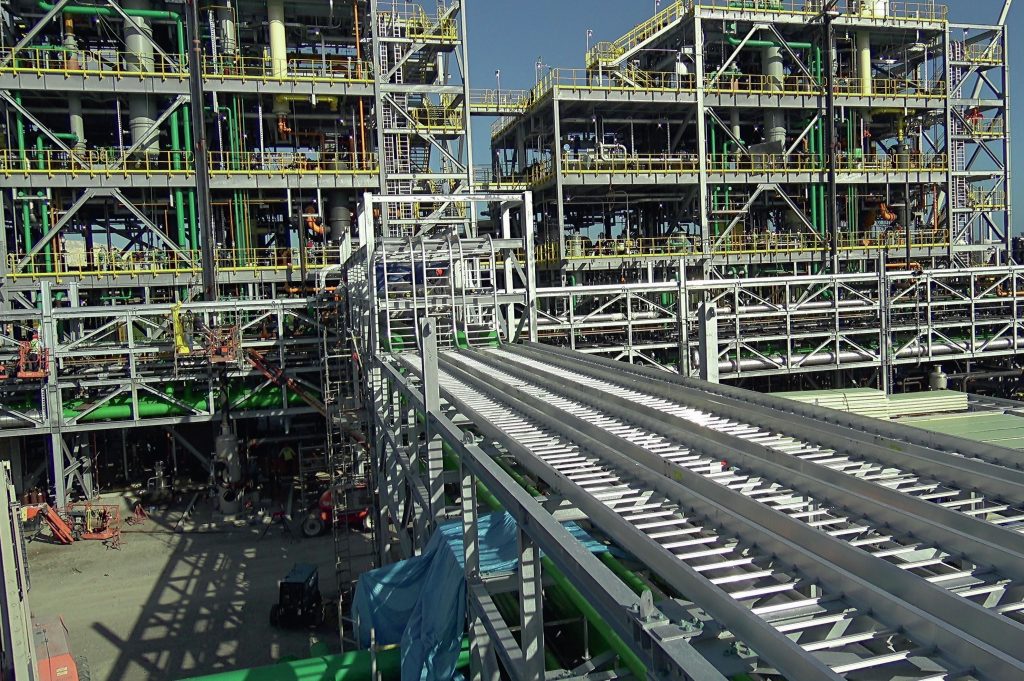
30 September 2023
Integrated and efficient phosphate production
PHOSPHATE PROCESS TECHNOLOGY
Integrated and efficient phosphate production
Leading companies such as Ballestra, Buss ChemTech, Elessent Clean Technologies (MECS) and Prayon Technologies are working together to solve the numerous production challenges facing the operators of integrated phosphate fertilizer production plants.
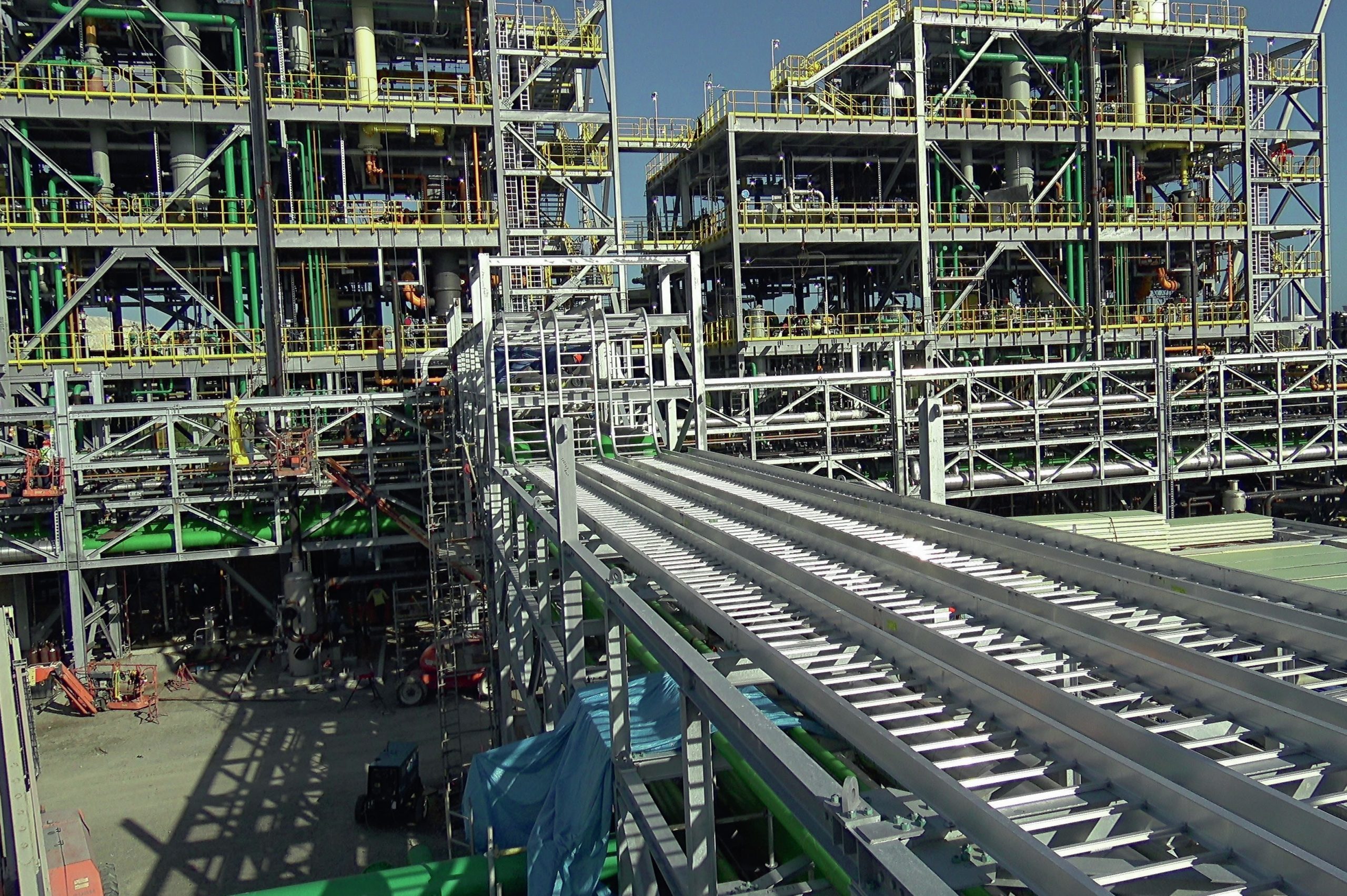
Cost reduction and revenue generation have become increasingly important imperatives in the manufacture of phosphate fertilizers. Greater resource efficiency has also risen up the industry’s agenda with the emergence of the circular economy and policies on waste prevention. This has seen plant operators turn to production methods that are able to consume low-grade phosphate rock and/or generate pure and saleable gypsum as a by-product.
Energy consumption is also coming under closer scrutiny. Phosphate production can be highly energy-intensive due to the cumulative energy demands from process steps such as mining, crushing, grinding, beneficiation, phosphoric acid production and product granulation.
There is also renewed interest in the commercial recovery of fluorosilicic acid (FSA), rare earth elements (REEs) and uranium during phosphate production. As well as improving process efficiency and reducing costs, the sale of such co-products can generate extra revenues for phosphate producers.
One company alone cannot hope to have the necessary expertise and experience to address all of these multiple challenges and opportunities. Instead, an integrated approach is required during the design, construction, operation and maintenance of phosphate production assets. This is now happening with leading companies such as Ballestra, Buss ChemTech, Elessent Clean Technologies (MECS ® ) and Prayon Technologies working together to collectively solve the numerous production challenges facing the operators of integrated phosphate fertilizer production plants 1 .
This has become necessary because:
- Phosphate rock, as a finite resource and the industry’s main feedstock, must be extracted and processed as efficiently as possible.
- The complete production process – from upstream phosphate rock mining to phosphate fertilizer finishing downstream – requires holistic problem solving to satisfactorily address multiple economic, technological and environmental challenges.
- The operability, profitability and longevity of production assets are determined by the overall design of the phosphate manufacturing complex and, critically, by the technology selection for the phosphoric acid and sulphuric acid plants.
- The ability to generate revenues from process by-products such as phosphogypsum and fluorine can deliver both environmental and economic benefits.
Milan-headquartered Ballestra has extensive experience in the design and supply of chemical plants. For the fertilizer industry, the engineering company offers production plants for sulphuric acid, merchant-grade and purified phosphoric acid (MGA and PPA), single superphosphate (SSP), triple superphosphate (TSP), potassium sulphate and granulated NPK compound fertilizers.
Ballestra is able to implement an integrated approach to phosphate production, offering both MECS ® technology for sulphuric acid plants and Prayon technology for phosphoric acid plants through its long-term partnerships with both companies. It also offers an economically attractive fluorine recovery process for phosphate plants through its ownership of Swiss-headquartered Buss ChemTech.
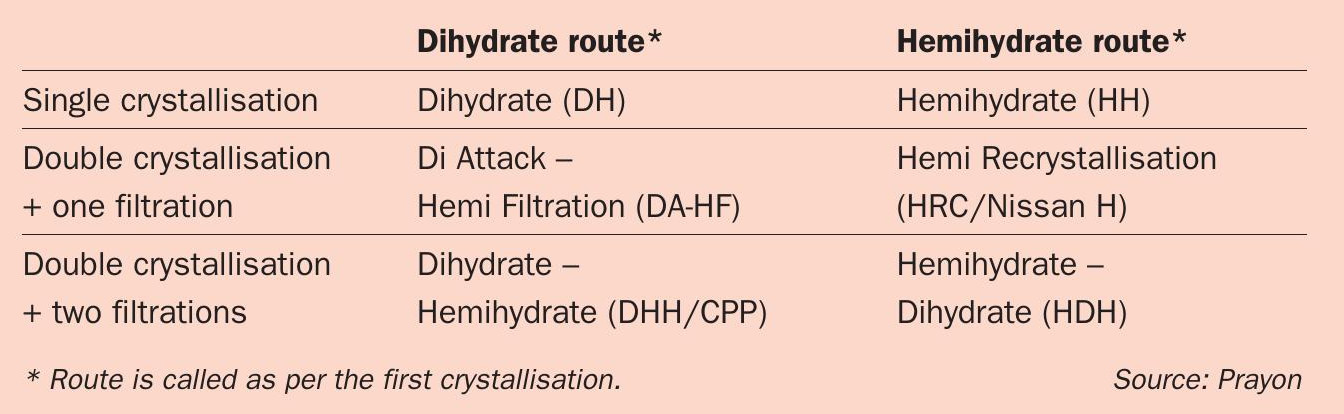
The rock quality challenge
In certain regions, availability, resource depletion and the long-term decline in P 2 O 5 grades are becoming issues for producers sourcing phosphate rock. Quality is a critical consideration as the presence of high levels of minor elements (Al, Fe, Mg) in phosphate rock can cause production problems, particularly at phosphoric acid plants. These elements are associated with high viscosities during filtration, gel formation during acid concentration and equipment scaling, for example 1 .
To address these challenges, Prayon Technologies offers two innovative chemical processes capable of beneficiating low-grade phosphate rock (Fertilizer International 500, p35):
- The EcoPhos process – an acquired technology based on the use of dilute hydrochloric acid
- The GetMoreP process – a similar technology developed in-house by Prayon based on the use of dilute sulphuric acid.
Both processes generate dicalcium phosphate (DCP). This flexible end-product can be used as a high purity feedstock (3941% P 2 O 5 and 32-34% CaO) for phosphoric acid plants, enabling the manufacture of a range of downstream phosphate products.
Sulphuric acid plant heat recovery
The standard wet process route for phosphoric acid production involves the digestion of phosphate rock with sulphuric acid. This is typically supplied by on-site sulphuric acid plants. The reliability, output and energy efficiency of these plants are therefore major considerations for integrated phosphate producers.
In the sulphuric acid process, the energy released through combustion and other exothermic reactions is easily recovered as high-pressure (HP) steam. In contrast, the recovery of low-level energy – such as the heat produced during SO 3 hydration – is usually uneconomic and is instead lost at the cooling tower.
However, with the MECS ® Heat Recovery System (HRS ™ ) from Elessent Clean Technologies, sulphuric acid plants can significantly increase their thermal efficiency by upgrading and recovering this low-level energy as medium-pressure (MP) steam. The amount of steam generated usually ranges from 0.4-0.6 tonnes of steam per tonne of acid produced. Typically, this steam can then be used to produce three megawatts of electricity per 1,000 t/d of acid capacity (Fertilizer International 508, p28).
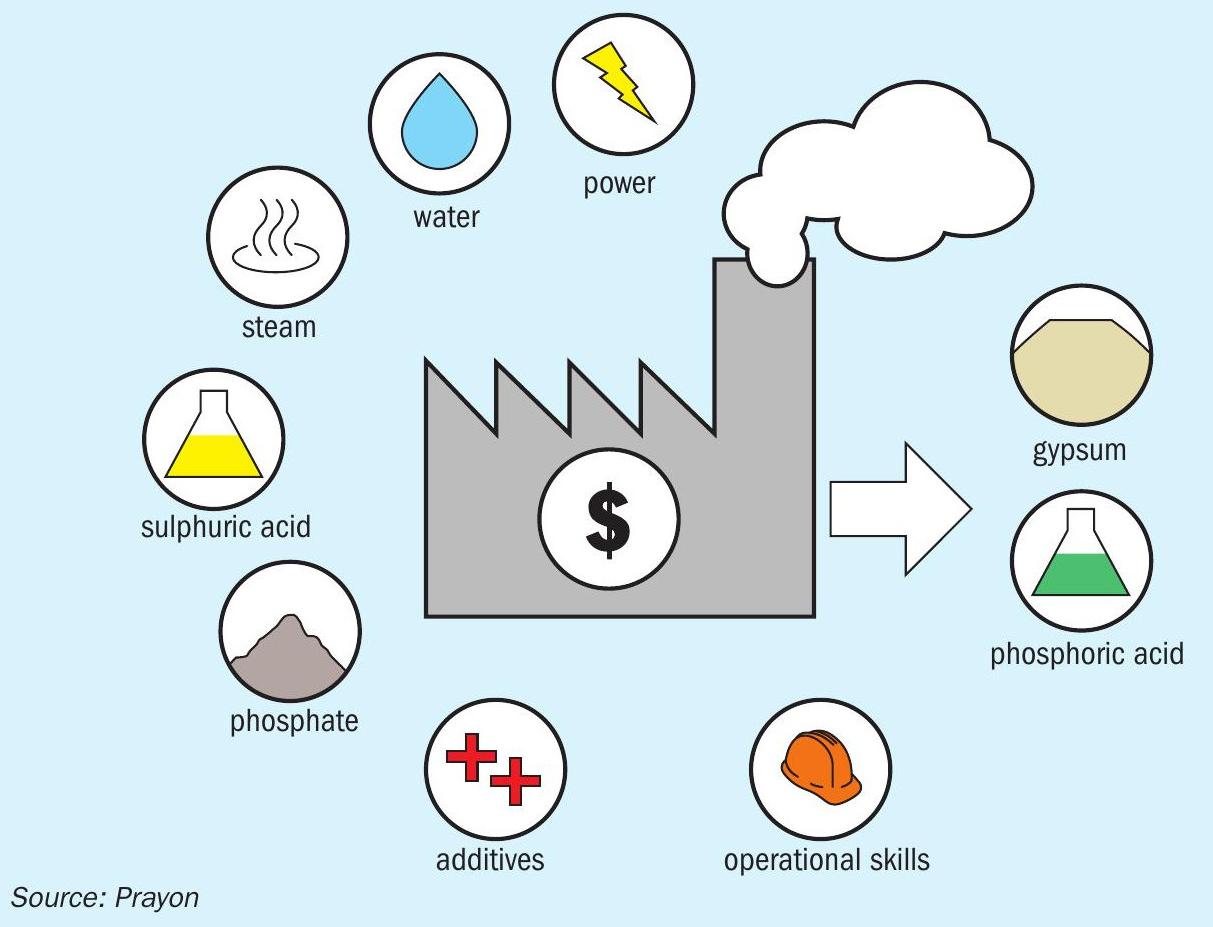
The longevity and reliability of equipment are also important cost factors in sulphuric acid production. Beneficially, MECS ® HRS ™ can meet these requirements too, being designed with durability and low maintenance in mind (Fertilizer International 508, p28).
HRS ™ technology has been deployed at sulphuric acid plants for around 40 years with over 100 units installed worldwide. It can also provide UN-accredited carbon-free energy for plant owners and neighbouring communities.
Elessent Clean Technologies is a major technology provider to the phosphates sector. More than 70 percent of the sulphuric acid produced using MECS ® technologies, for example, goes into phosphate fertilizer production.
Phosphoric acid process selection
The wet process is the most economical and widely-adopted method for commercial phosphoric acid production globally. Phosphate rock is attacked with sulphuric acid to produce phosphoric acid and a solid calcium sulphate by-product. These are subsequently separated by filtration (Fertilizer International 481 p49).
The six available wet process routes for phosphoric acid production have distinctly different characteristics. They vary according to whether dihydrate (DH) or hemihydrate (HH) calcium sulphate crystals form initially, and by the number of crystallisation and filtration steps involved (Table 1).
Prayon has developed commercial phosphoric acid production options for five of these six process routes, the one exception being the HRC (Nissan H) process (Fertilizer International 481 p49).
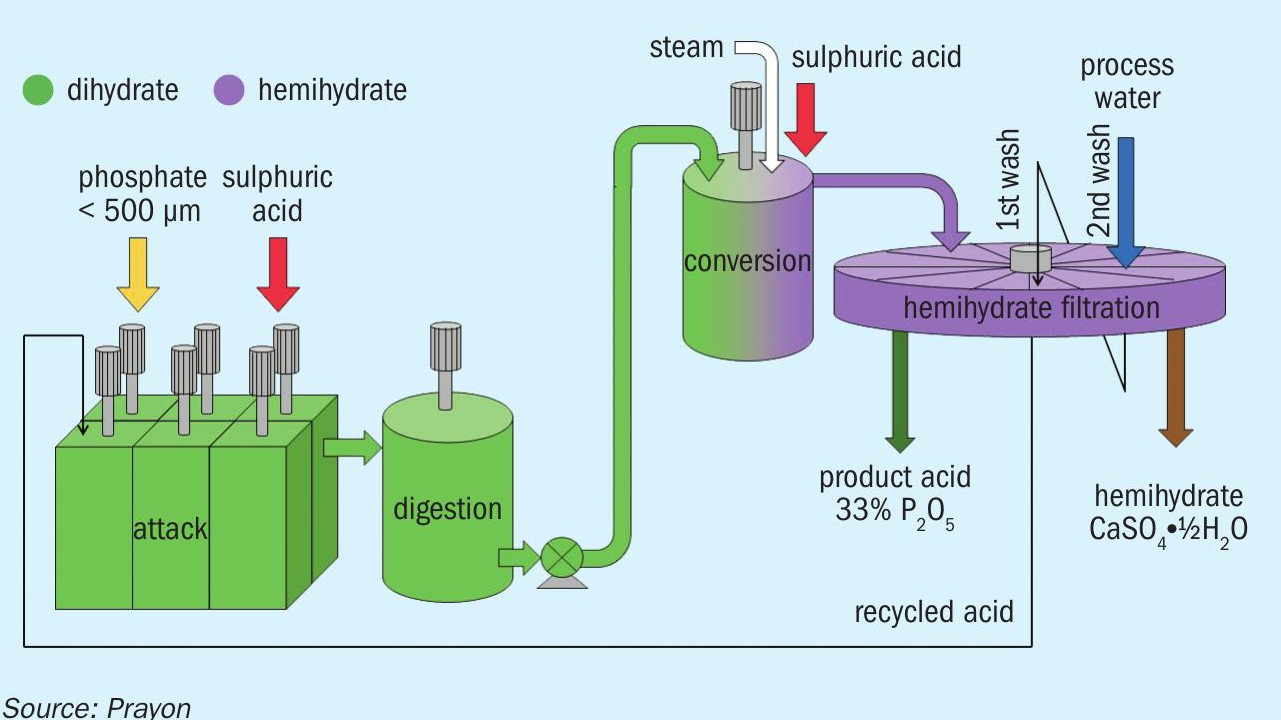
The company’s technology is used in more than 130 phosphoric acid plants in over 30 countries globally 1 .
In Prayon’s view, process selection, and the relative merits of each process route, can be assessed using the following criteria (Figure 1):
- Phosphate rock consumption and tolerance of impurities
- Quality and amount of sulphuric acid needed
- Steam, water and power consumption
- Additive usage l The quality/strength of the phosphoric acid product
- The quality of phosphogypsum by-product l Plant operability and ease of maintenance (opex)
- Sensitivity of the process to instability
- Investment cost (capex).
While investment cost is an important factor, it is vital to select the phosphoric acid process that best suits project circumstances and ensures the successful operation of the whole phosphate fertilizer complex, rather than opt for the phosphoric acid unit with the cheapest capital cost. That’s because a lower cost phosphoric acid plant, if undersized or inflexible, can perform poorly and make the whole production process uneconomic (Fertilizer International 481, p49).
While double crystallisation processes generally have a higher investment cost than single crystallisation processes, Prayon’s new DA-HF process (Figure 2) can offer valuable performance advantages at a reasonable investment cost 1 .
Grupa Azoty is currently operating the world’s first DA-HF plant at its Police production site in Poland. This was installed as part of a revamp of the company’s existing DH plant. The new DA-HF plant was engineered by Ballestra, who also helped commission the plant in 2019 in collaboration with a team from Prayon (Fertilizer International 496 p52).
The phosphogypsum challenge
As it expands globally, phosphate fertilizer manufacturing is generating ever larger volumes of phosphogypsum waste. Billions of tonnes of this material are currently being managed at great cost within giant waste stacks.
Nevertheless, phosphogypsum is finding increasing use as a co-product in agricultural, building and construction applications, particularly outside of the United States. This is a sign that the previously unwanted solid waste generated by the phosphate industry is becoming a valued resource (Fertilizer International 478, p58).
It is estimated that some 50-60 million tonnes of phosphogypsum are now being utilised worldwide (Fertilizer International 501, p45). Notable examples of commercial phosphogypsum (PG) use include:
- Belgium (Prayon): high-quality PG for the cement and plaster market.
- Brazil: most PG now goes to agriculture (5 million t/a) following its reclassification.
- Canada (Nutrien): PG for agriculture and for afforestation using man-made ‘anthrosols’ – PG mixed with soil in a 9:1 ratio.
- China (Wengfu Group): more than half of PG output is used in agriculture and construction, or recycled as ammonium sulphate/calcium carbonate.
- Kazakhstan (UN): large-scale remediation of saline/sodic soils.
- India: PG reclassified as a co-product, not waste, in 2008. Widely sold for construction, agriculture, soil additive, cement and as bagged fertilizer (Paradeep). Examples include afforestation for green energy (Coromandel) and road construction (Paradeep).
- Russia (PhosAgro): use of PG in agriculture, construction and road building
- Tunisia (GCT): PG for brickmaking, road construction, housing and for remediation and the return of land to productive use.
Nutrien, for example, has successfully established high yielding poplar and willow plantations (see photo) on top of waste stacks in Alberta, Canada, using artificial soils created from weathered phosphogypsum (Fertilizer International 501, p45)
“The tree plantations established at Nutrien are predicted to sequester 30 tonnes CO 2 equivalents per hectare per year,” Nutrien’s Connie Nichol told Fertilizer International. “Thus, in 20 years, the gypsum stack area reclaimed to date will sequester 12,000 tonnes of CO 2 . This same area is also predicted to produce 10 oven dry tonnes/ha/year of above ground woody biomass.”
Phosphoric acid process selection has a major influence on phosphogypsum quality and therefore use. Double crystallisation processes (HDH, DA-HF and CPP), for example, due to their higher resource efficiency, can generate higher quality phosphogypsum suitable for industrial applications as this contains much lower P 2 O 5 levels. This factor is critical for gypsum used in plaster and the cement market. Valuably, two of these processes (DA-HF and CPP) also generate hemihydrate, a self-drying gypsum product that offers significant energy and cost savings for the industrial end user 1 .
Prayon’s approach to phosphoric acid manufacturing provides a good example of how to manage and use phosphogypsum. The company has been successfully selling gypsum as a co-product for more than forty years. Currently, almost all of the phosphogypsum produced at its CPP phosphoric acid plant in Engis, Belgium, is sold for plaster and cement manufacture or for agricultural use (Fertilizer International 501, p45).
Prayon’s commercial customer Knauf established a plaster production plant close to Engis on the opposite bank of the River Meuse. Phosphogypsum from Prayon’s production plant is transported by conveyor belt across the river to a discharge point where it is temporarily stored. Over a period of several weeks, the phosphogypsum cures naturally in-situ, reverting from wet hemihydrate (HH) cake (18% free water, 6% crystalline water) to rehydrated dry dihydrate (DH, 5% free water, 19% crystalline water). The resulting gypsum product requires no further treatment prior to its shipment down river by barge to Knauf’s stucco plaster factory (Fertilizer International 501, p45).
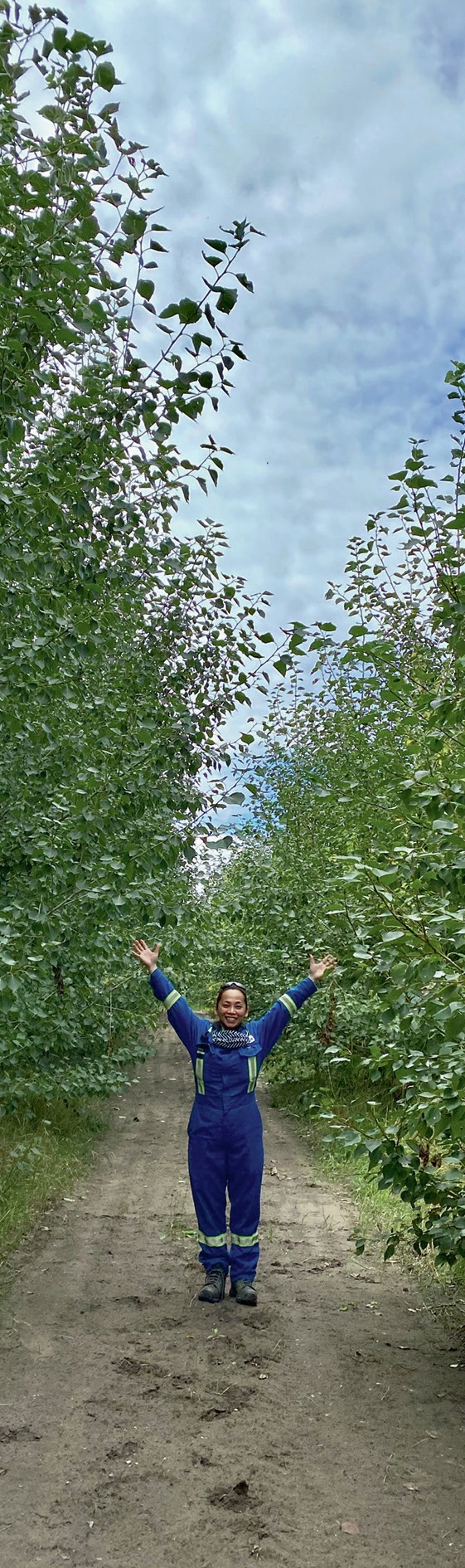
Fluorine – nuisance pollutant to revenue earner
The production of phosphoric acid (H 3 PO 4 ) and phosphate fertilizers creates silicon tetrafluoride (SiF 4 ) as a toxic off-gas. This originates from the natural levels of fluorine present in sedimentary (0.10-0.14 kg F per kg P 2 0 5 ) and igneous (0.06-0.08 kg F per kg P 2 0 5 ) phosphate rock. Currently, this problem is mainly tackled by absorbing SiF 4 in water to form fluorosilicic acid (FSA, H 2 SiF 6 ). The FSA obtained is then neutralised and either stored in ponds or disposed of into the sea (Fertilizer International 504, p44).
World phosphoric acid production, and by association FSA, is on the rise. Assuming phosphoric acid contains three percent fluorine on average, around 1.4 million tonnes of by-product FSA was produced globally in 2019, according to some estimates.
Although usage remains comparatively low, around 200,000 tonnes (fluorspar equivalent) of FSA is consumed annually in aluminium fluoride (AlF 3 ) manufacture, meeting some 11 percent of the global industry’s fluoride needs. Water fluoridation and fluoride salt manufacture consume a further 200,000 t/a of FSA by-product. Some FSA is also used during phosphoric acid production as a sulphuric acid substitute, reducing the latter’s usage by about five percent (Fertilizer International 504, p44).
Prayon offers a fluorine recovery system that can be installed during the concentration of phosphoric acid to 48-60% P 2 O 5 . This prevents fluorine being released to the atmosphere via the stack, or being sent back to the phosphoric acid plant where it results in scaling. This recovery system can simultaneously save on maintenance costs and increase revenues if the recovered FSA is sold for the manufacture of hydrofluoric acid or aluminium fluoride (Fertilizer International 504, p44).
The anhydrous hydrogen fluoride (AHF) process from Buss ChemTech (BCT) also offers the international phosphate industry a commercially attractive route for recovering FSA and creating added-value products. BCT’s technology, by manufacturing anhydrous hydrogen fluoride (AHF) from FSA, provides access to higher value markets such as organic and inorganic fluorochemicals or high bulk density (HBD) aluminium fluoride. The manufacture of AHF also creates indirect value, for the environment and the economy, by substituting for the large amounts of calcium fluoride (CaF 2 ) which would otherwise need to have been mined (Fertilizer International 504, p50).
BCT first commercialised FSA-to-HF conversion technology in the early 2000s. The company went on to successfully commission its first industrial AHF plant for Chinese phosphate producer Wengfu Group in 2008. This proved such a success that Wengfu now operates six BCT-constructed AHF plants (Fertilizer International 504, p50).
BCT recently completed the first AHF project outside of China for Nutrien at its Aurora plant in North Carolina. Arkema also took part in this project as the AHF consuming partner. BCT, which is owned by Ballestra, expects global capacity for FSA-to-HF technology projects to reach more than 200,000 t/a of AHF this year (Fertilizer International 504, p50).
Acknowledgement
This article is partly based on a presentation by Ballestra, Buss ChemTech, Prayon Technologies and Elessent Clean Technologies (MECS ® ) given at CRU’s Phosphates Conference & Exhibition in Tampa in March 2022 1 . This set out the case for an integrated approach to the design and construction of phosphate fertilizer production plants.
References