Nitrogen+Syngas 386 Nov-Dec 2023
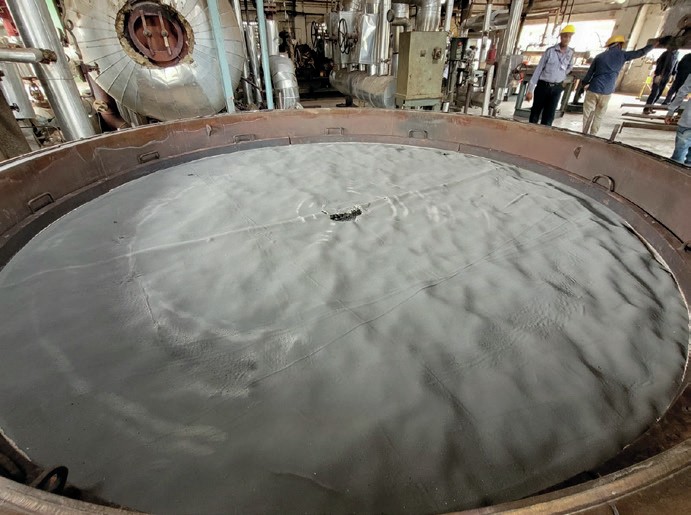
30 November 2023
Ammonia oxidation catalyst replacement
CATALYSTS
Ammonia oxidation catalyst replacement
Sumit Rao of Hindustan Platinum Private Ltd describes two recent start-up issues with catalyst gauze packs at a nitric acid plant, and their remediation to allow production to continue.
1a)
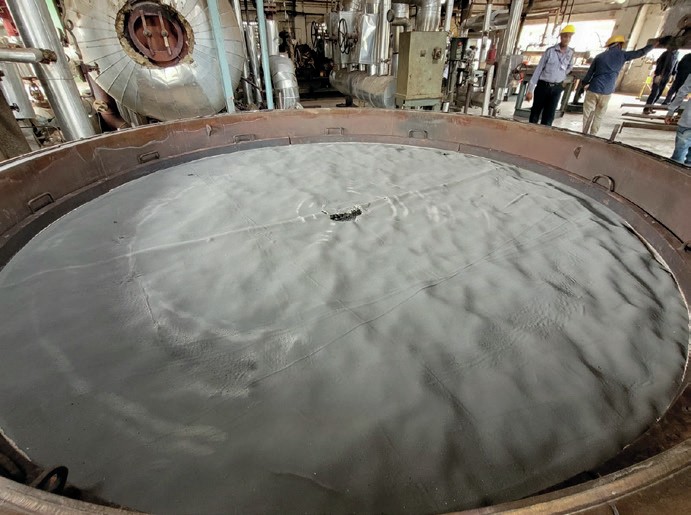
1b)
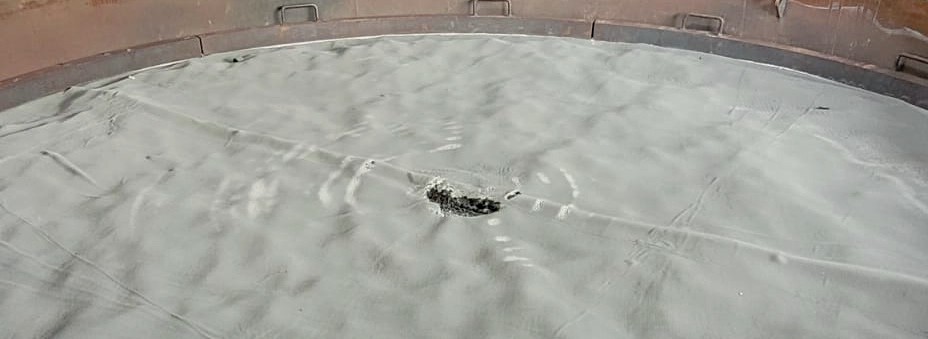
Mechanical failures in the catalyst pack converter are observed only infrequently, so this article describes a unique situation which deserves to be shared from the perspective of good corrective planning and implementation. Two failure occurrences were experienced one after another within 48 hours involving two different catalyst packs, but the plant restarted production within less than 36 hours of the second failure occurrence. The first failure was a result of a mechanical failure, while the second one was caused by a variance from the correct start-up procedure, resulting in catastrophic damage to the catalyst surface, rendering both packs inoperative. With no spare catalyst at hand, new catalyst supply at the site being at least two weeks away, and acid demand at its peak, a remedial measure was performed to get one of the catalyst packs up and running. We detail below the two failure scenarios and how plant production operations were restored within 36 hours of the second catalyst pack failure through teamwork and innovative restoration countermeasures.
2a)
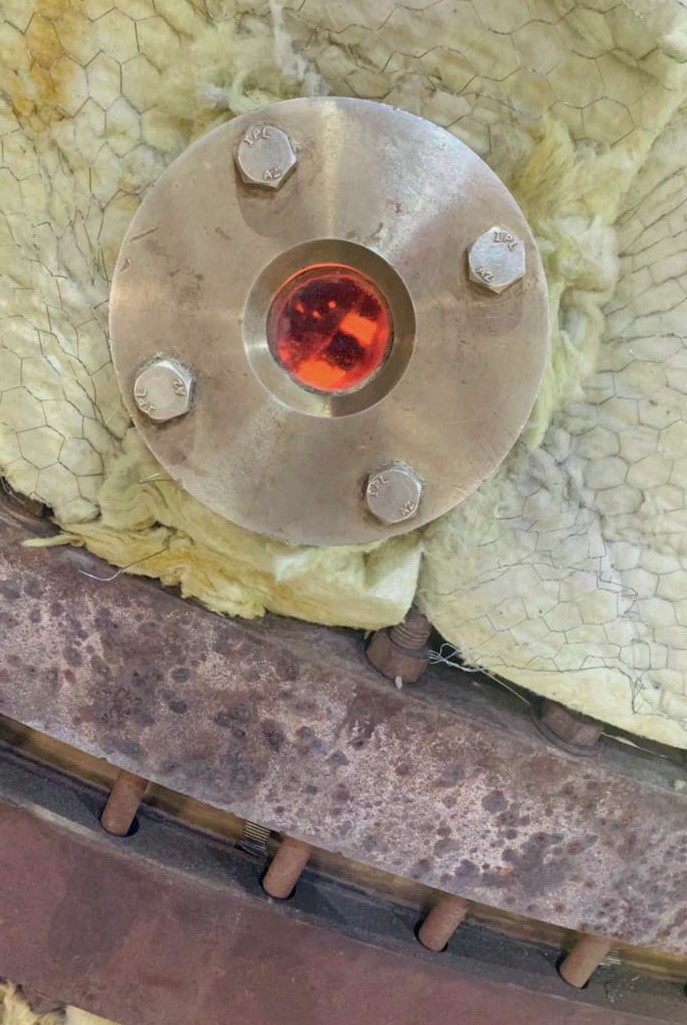
2b)
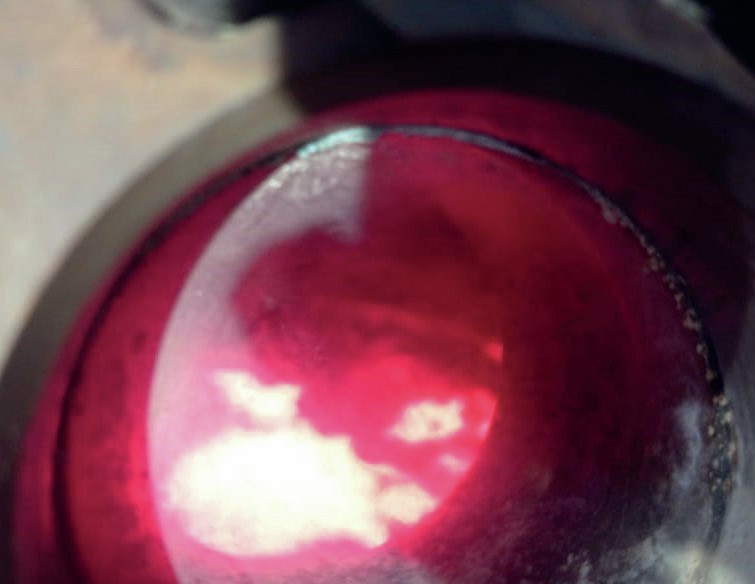
2c)
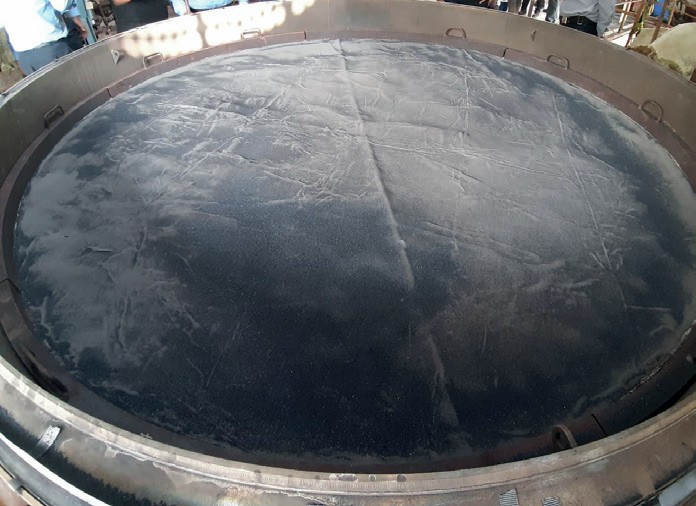
First failure
After operating the plant for about 90% of its anticipated production run, a mechanical failure in the light-up assembly caused damage and a tear to the gauze pack (Figure 1). The plant was stopped and an inspection carried out.
Second failure
The plant was restarted after replacing the damaged gauzes with a fresh set of catalyst gauze pack.
After the start-up of the newly installed catalyst pack, the plant team observed contaminants through the sight glass (Figure 2). The plant had to be stopped again due to the large scale contamination visible via the sight glass. After the removal of the burner hood, the degree of contamination was clearly visible, making the decision to shut down the plant a prudent one.
3a)
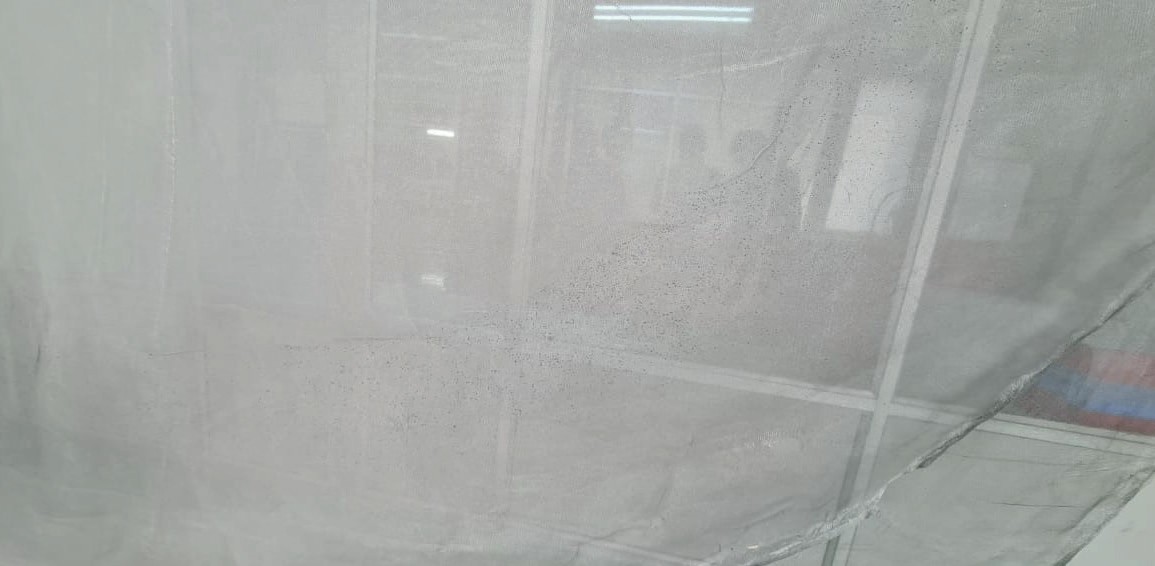
3b)
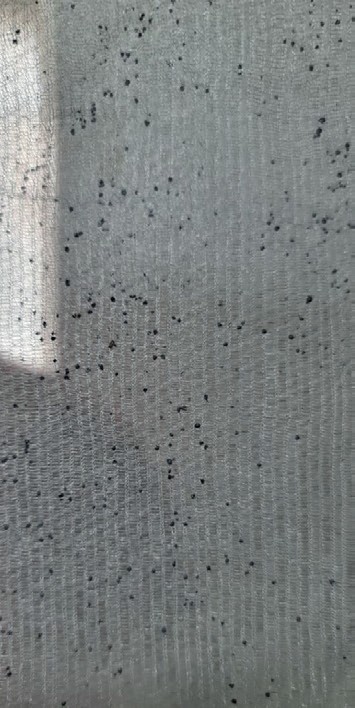
3c)
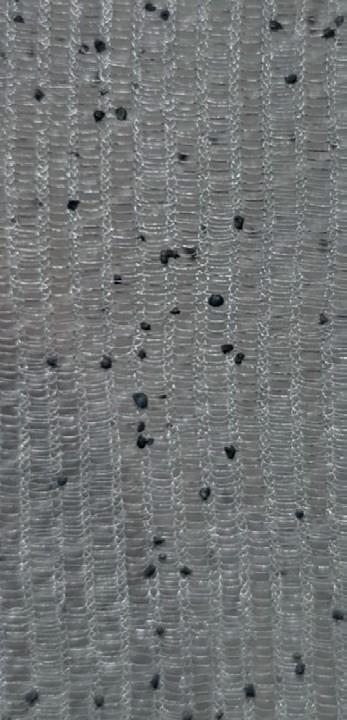
Root cause analysis
The contaminated gauze pack was transported to our Hindustan Platinum (HP) facility for inspection and assessment of the gauze surface. The bulk of the contamination was removed from the gauze surface by employing suitable mechanical operations. The gauze layers were separated from the pack and rolled onto the pipe hangers for inspection purposes (Figure 3-a). Fusion of the contaminants on the gauze surface was determined to be silicious and had coverage across the entire pack (Figures 3-b and 3-c).
The surface impurities resembled the material employed during upstream piping treatment and sand blasting operations. Insufficient blowing operations after sand blasting may likely have caused the retention of these contaminants in the u-bend piping, which eventually entered the convertor during the start-up process.
Remediation
Several checks and tests were carried out and the fused deposits could not be separated from the gauze surface, neither physically nor chemically, rendering the gauze ineffective for reuse. After joint brainstorming sessions between both the organisations’ plant production, manufacturing, technical services, and product management teams, it was jointly agreed to instead repair the damaged gauze pack from to the first shutdown.
The damaged pack (90% used) from the first failure was taken up for restoration (Figure 4). The motivation to take up this kind of solution arose based on past feedback from customers to safeguard critical production loss. While ideally it would be recommended to replace the pack, this is a temporary solution emphasising that the reconditioned product must be operated under strict supervision and regular monitoring to ensure safe operation.
4a)
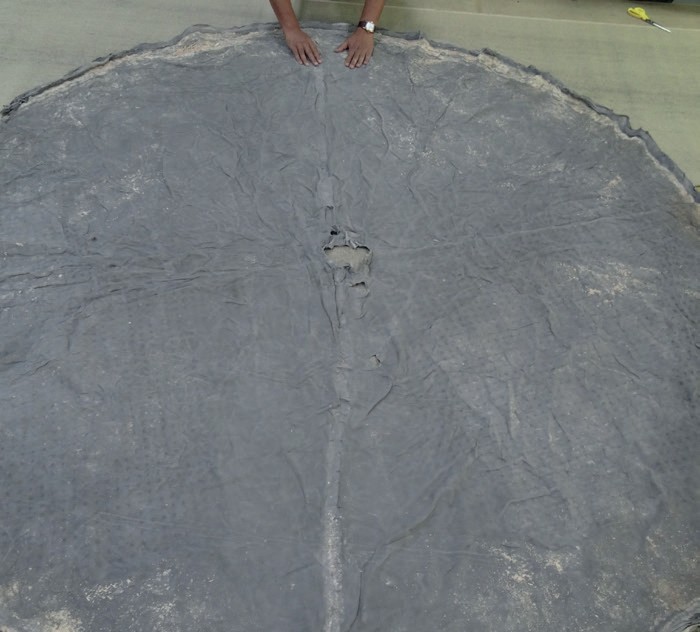
4b)
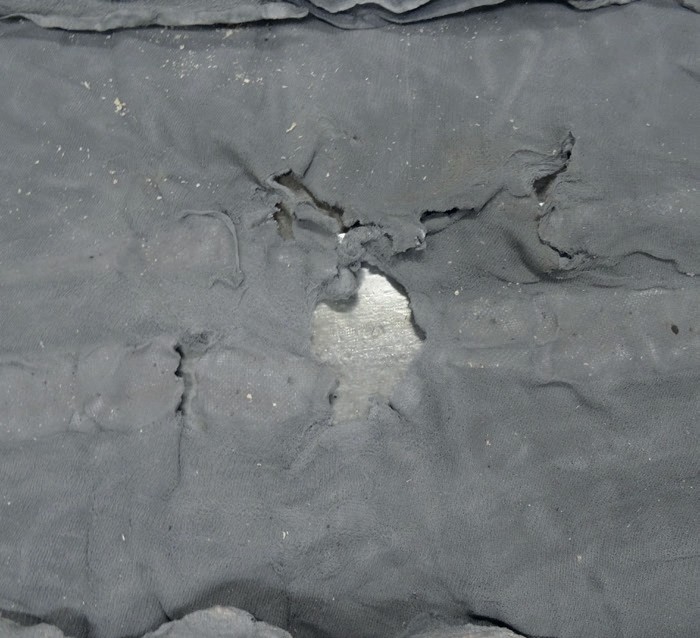
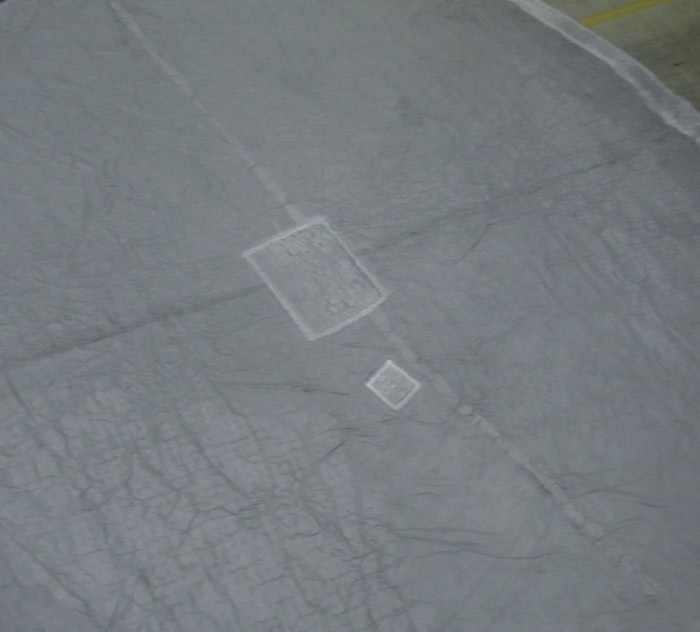
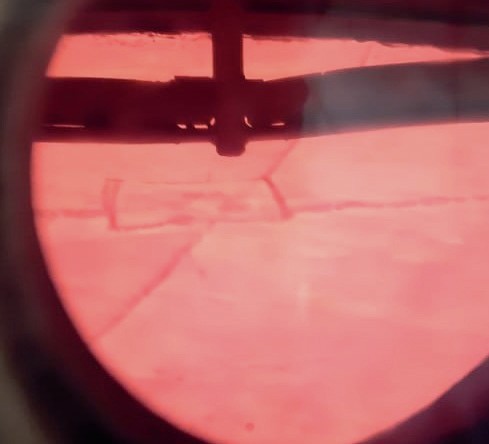
After several hours of deliberations and relentless efforts for the best outcome in the surface structure to enable continuity in the process for at least a month, a reconditioning process was taken up to revitalise the damaged catalyst pack by the production team at Hindustan Platinum, to restore each layer for operability and performance (Figure 5). The damage was: across the pack, through the centre, at the periphery, etc. It was a considerable feat to manage to bring back to life this damaged gauze pack.
Restored operability and performance
The renewed gauze pack was transported back to the plant site and installed within the catalyst basket. The plant was successfully restarted as per the normal procedure and normal observations were made in terms of its operability and performance (Figure 6).
The plant successfully restarted and operated for just under two weeks. Regular monitoring and evaluations were done during these two weeks’ timeframe to ensure that the gauze performance was within the normal and safe operating criteria, until a new supply of the fresh catalyst gauze pack arrived at the plant site and was installed.