Nitrogen+Syngas 386 Nov-Dec 2023
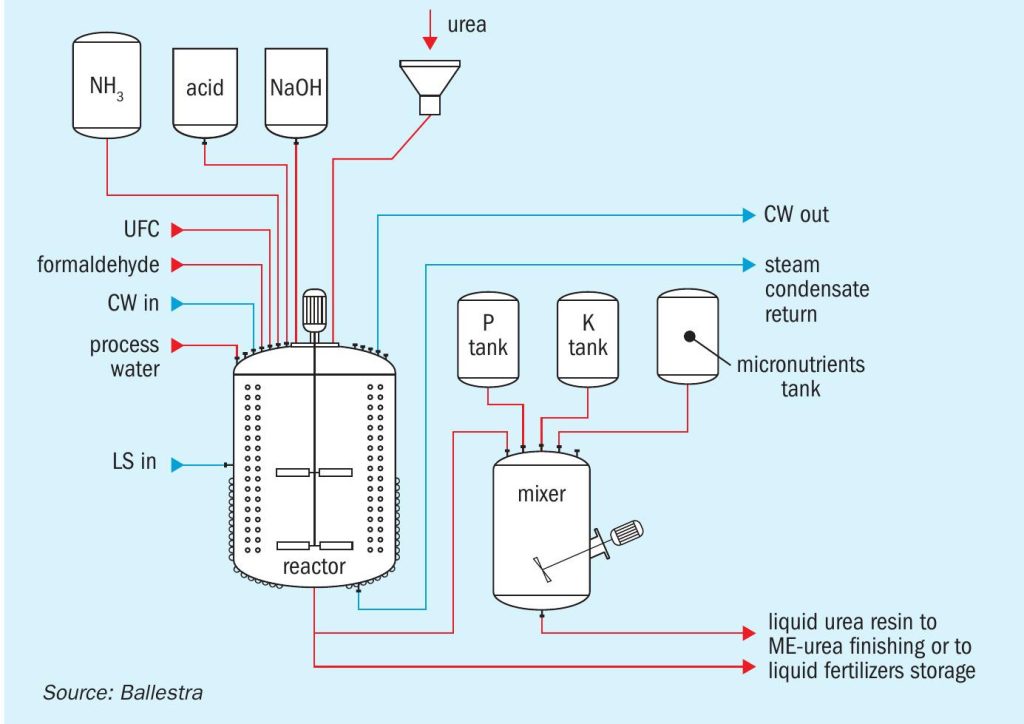
30 November 2023
Improving nutrient use efficiency with methylene urea
SLOW-RELEASE FERTILIZERS
Improving nutrient use efficiency with methylene urea
Ballestra is taking a new approach to improving nutrient use efficiency by moving methylene-urea production to the fertilizer industry. Massimo Gori and Svet Valkov of Ballestra discuss the technology and benefits of having a slow-release fertilizer that uses a product from within the fertilizer industry.
The fertilizer industry as we know it is set for a change. Arable land is limited, and world population continues to grow, but it is no longer acceptable to simply pour more fertilizer per hectare to feed more people. The capability of crops to absorb nutrients is limited and any surplus nutrients are leached away by rain and end up in rivers and seas as ammonia, nitrates, phosphates and potassium.
Improving fertilizer efficiency and increasing product value without changing existing plants and renewing investment has become the new focus of the fertilizer industry. Many different solutions have come to market that provide crops time to absorb the nutrients, avoid or reduce leaching by rain or irrigation and ultimately maximise the efficiency of fertilizers.
For nitrogen fertilizers, the main strategies that have emerged are:
- urease inhibitors which block or slow down the decomposition of urea into NH4+ ;
- nitrification inhibitors which block or slow down the conversion from NH4 + to nitrate;
- coatings which cover the entire surface of a fertilizer granule with a substance that delays contact with water;
- formulations, same as above, with substances intimately mixed with the mass of the fertilizer granule.
These solutions are made possible by substances like polylactic acid, polyurethane, N-(n-butyl) thiophosphoric triamide, dicyandiamide, sulphur, 2-chloro-6 (trichloromethyl) pyridine, 2-chloro-6 (trichloromethyl) pyridine, malic+ itaconic acid copolymer, etc., none of which are a product of the fertilizer industry. As a result, the fertilizer industry has to pay a third-party fee to achieve fertilizer efficiency that erodes, sometimes significantly, the margin from the added value of controlled and slow-release fertilizers.
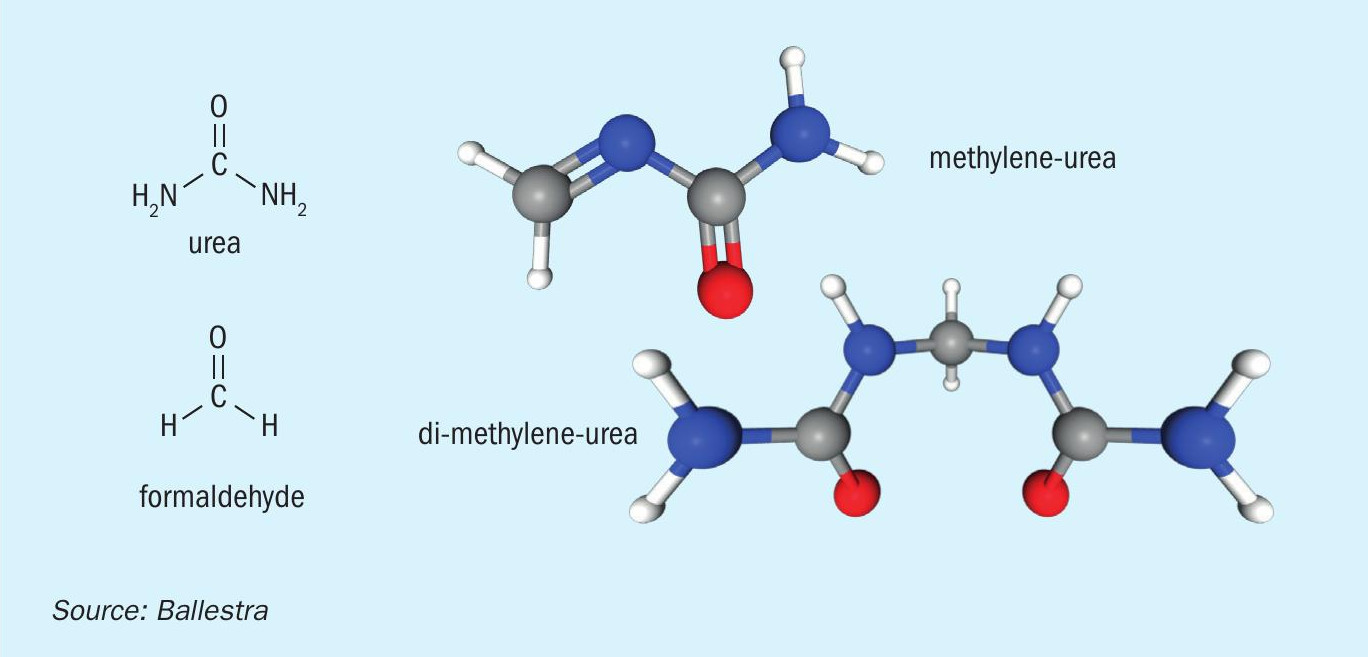
Taking a different approach, what if the means of delivering a step change in nutrient use efficiency was a product, methylene-urea, already available to the fertilizer industry? Currently, the production of this compound is limited by the small size of the resin industry that supplies it. Ballestra is therefore working to scale up methylene-urea manufacturing technology to allow the large-scale production of this slow-release fertilizer within the fertilizer industry.
Methylene-urea chain compounds
Methylene-urea (Me-urea) is obtained by condensing together one molecule of urea with one molecule of formaldehyde. If condensation continues, more molecules join together to form di-methylene-urea (Fig. 1). Proceeding further with polymerisation increases the chain length and a compound known as ureaform is then formed. The ultimate end product of this polymerisation process is a urea-formaldehyde (UF) resin made up of long reticulated molecular chains.
These types of compounds are already well known within the nitrogen industry. Urea-formaldehyde concentrate (UFC), for example, is an essential additive used to impart mechanical resistance and hardness to urea granules. There is also good awareness of formaldehyde as a product of the partial oxidation of methanol, a major basic chemical and close relative of ammonia.
Valuable slow-release properties
Urea is very soluble in water while UF resins are completely insoluble. The various methylene-urea chain compounds (Meurea, di-methylene urea and ureaform) sit somewhere in between these two extremes and are partly soluble. Generally, these compounds become more insoluble as their polymer chain length increases.
Urea, Me-urea, di-methylene urea, urea-form and UF resins are all excellent nitrogen carriers and can therefore be used as fertilizers. The slow-release properties of methylene-urea chains can be precisely engineered to dissolve and make nitrogen available within days, weeks, or months, according to the requirements of a particular crop. These compounds will resist water leaching depending on their polymer chain length, starting from urea (very soluble) and arriving at UF resins (insoluble).
Me-urea and longer chain ureaform (UF) fertilizers are available in both liquid and granular form and are considered safe for both humans and the environment. These slow-release nitrogen fertilizers, when applied as a foliar liquid, have been shown to be 4-5 times more efficient than conventional nitrogen fertilization, i.e. 4-5 kg of urea are needed to deliver the same yield as 1 kg of Me-urea. Granular Me-urea offers similar efficiency advantages and is widely applied in turf (e.g., golf courses) and ornamental markets as well as in agriculture. Both liquid and granular products do not result in crop burn as they have a low salinity and no nitrate content.
Low volumes, high prices
The valuable fertilization properties of Me-urea compounds are said to have been discovered when grass surrounding a urea-form tank grew greener and taller because of a leak. In reality, Me-urea is a well studied and well known product that has been sold and used for decades. It is a proven slow-release fertilizer that is attractive in the wider world market and can therefore command premium prices.
Currently, Me-urea is manufactured by the UF resin industry, a much smaller industrial sector compared to the fertilizer industry, with installed capacity limited to a few hundred thousand tonnes per year.
Interestingly, though, this compound is made from chemicals already found in fertilizer production processes. That opens up the possibility that the fertilizer industry itself could begin to produce Me-urea, rather than sourcing this externally. This would allow fertilizer producers themselves to deliver the necessary step change in nutrient use efficiency – without sharing added value and margins with third parties. Indeed, in this article, we explain how Me-urea manufacturing can be moved from the UF resin sector to the fertilizer industry where it belongs.
Methylene-urea production
Ballestra’s Me-urea production system (Fig. 2) closely follows the approach already taken by the UF resin industry. The process design guarantees a fully automated, safe and durable production system, with no volatile organic compounds emissions. Operators, by adding the recipe to the control system, are ready to go.
The core know-how behind Me-urea production is the process recipe. The use of a batch reactor allows this to be changed easily to deliver different product grades. UFC or formaldehyde are loaded with solid urea or urea solution into the reactor. Polymerisation via acid or basic catalysis is performed in closely controlled cycles with the conditions varied to obtain a specific polymer length (or mix of polymer lengths).
The product obtained can be stored as liquid nitrogen fertilizer or mixed with other nutrients and micronutrients to obtain a precisely formulated liquid NPK fertilizer. Both of these product types can also be sent for further finishing in a drum granulator.
Product finishing
Although Me-urea production technology is well defined, the finishing stage is where most existing plants fall short. This is also the reason why the production capacity of a single Me-urea line is generally limited.
Me-urea is actually a family of different products, not a single product based on well-defined commercial specification. Because of this, each individual process recipe will require a specific set of finishing parameters for the Me-urea product obtained. However, most available granulation technologies do not have the flexibility to cope with full the range of Me-urea product grades.
This is where Ballestra’s fluid drum granulator excels. Essentially, it consists of a rotating drum with a fixed table inside made of a perforated metal sheet (Fig. 3). The rotation of the drum lifts the granules onto the table, where they are kept in fluid bed conditions by air flowing through holes in the metal sheet. The perforated table is slightly inclined to one side. This allows dry granules from the fluid bed to fall back to the lower part of the rotating drum. While doing so, they pass through an incoming spray of fresh Me-urea, which creates a further layer of material.
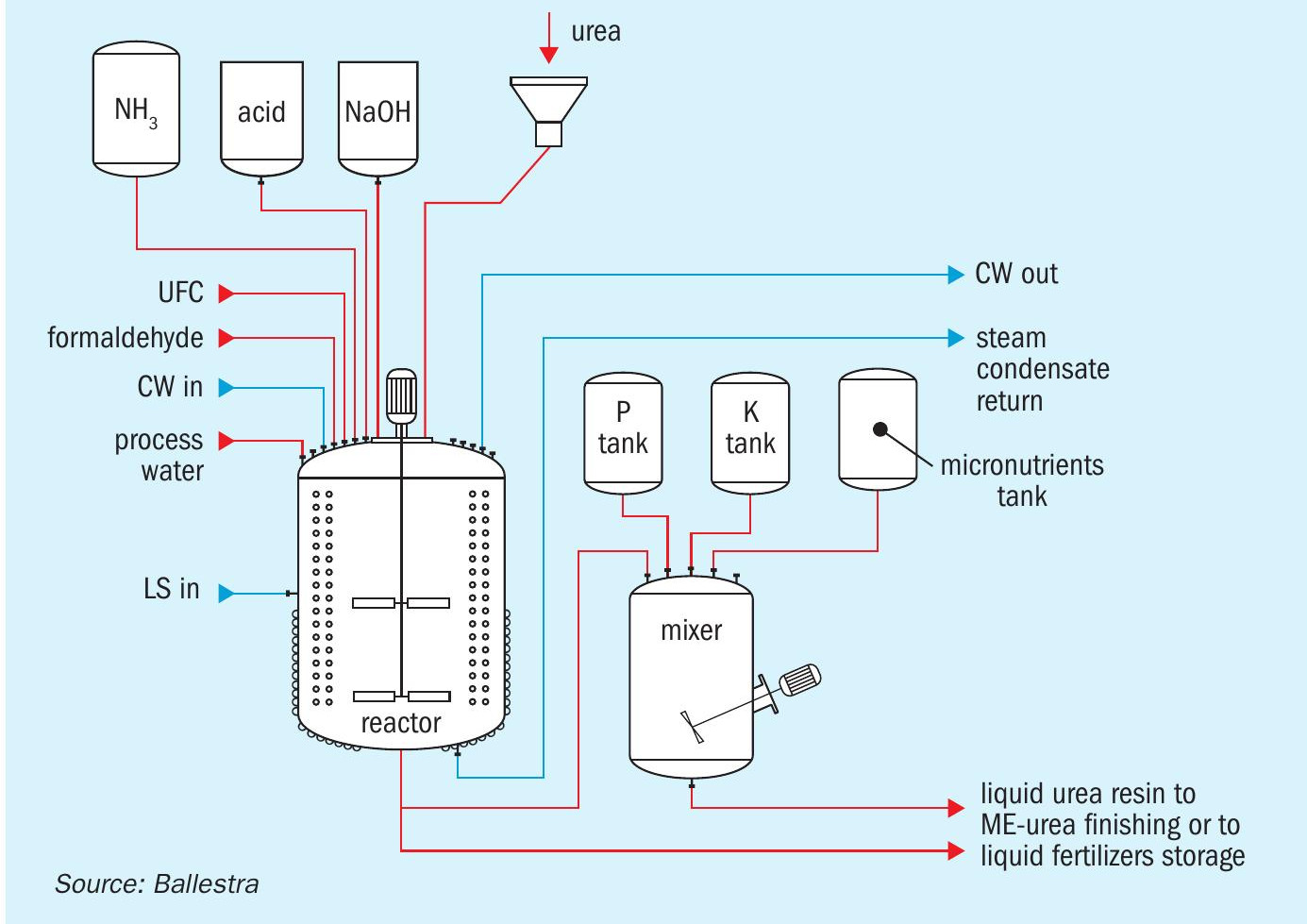
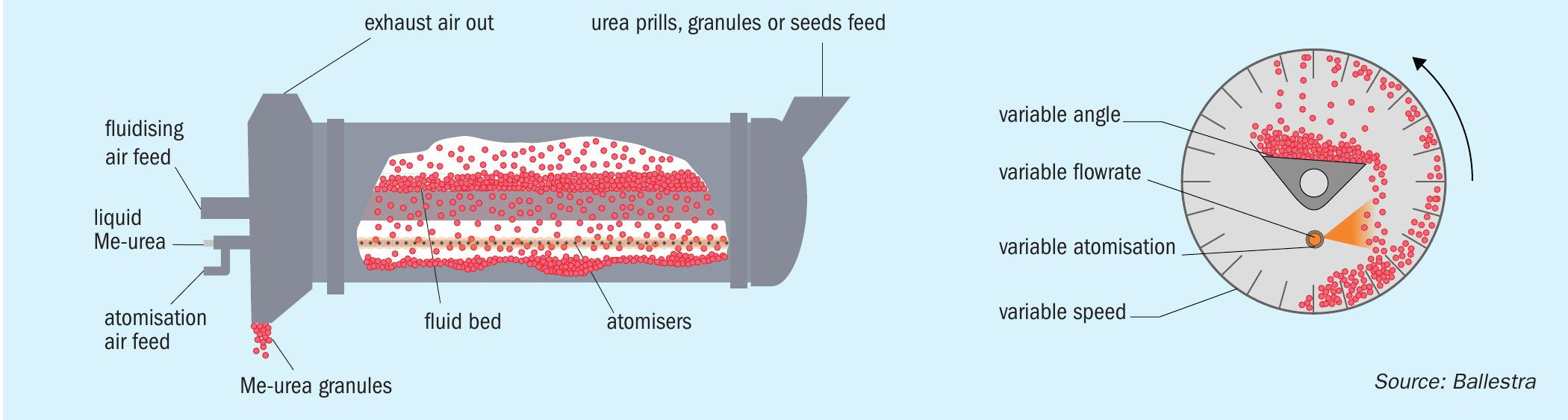
Everything in the design is about flexibility. The following parameters can all be carefully regulated:
- drum rotation speed;
- inclination of the fluid bed table;
- temperature and flow of the fluidising air;
- temperature of the freshly sprayed liquid.
Once the proper parameters for each recipe are defined, the result is granules with a solid, onion-like, layered structure and a hardness and mechanical resistance far greater than those of standard urea granules. A notable feature of Ballestra’s fluid drum granulator is that the fresh solution is sprayed into an area away from the fluidising air flow. This limits droplet entrainment, compared to a standard urea granulation process, and therefore reduces the duty on the downstream air cleaning section.
Setting aside these differences, the overall finishing scheme for Me-urea (Fig. 4) resembles a simplified urea fluid bed granulation process.
More products from the same plant
The finishing process described here is not limited to just Me-urea and ureaform production. Its flexibility also enables the production of other, more complex types of slow-release fertilizers.
Prior to finishing, Me-urea and ureaform, which are basically UF resins with shorter polymer chains, behave like a glue. Other nutrients can therefore be added as feed particles to the Ballestra fluid drum granulator and become evenly embedded within the solid and hard matrix of Me-urea granules. The resulting NPK and multi-nutrient granules have the same slow-release properties as standard Me-urea granules. This holds true even when the granule is broken as the added nutrients are still firmly fixed within the Me-urea matrix.
The fluid drum granulator can also be used as a quick and economical way of modifying the physical behaviour of urea granules and prills by, for example, improving their slow-release properties, surface resistance and bulk flowability. This is achieved by coated or fattening urea prills and granules fed to the Ballestra fluid drum granulator with a layer of Me-urea.
The resulting granules have a core of pure urea surrounded by an Me-urea coating. The release of the urea core to the soil can be carefully timed by regulating the thickness of the outer Me-urea coating.
Applying Me-urea coated urea granules to soils alongside seeds, for example, could provide a fertilization boost exactly when growing crops need it. Furthermore, supplying mixed granules with coatings of different thicknesses can provide a series of fertilization boosts at specific times. The end result is precision engineered fertilizer granules designed to deliver nutrients at specific times to closely match crop requirements.
Partners on a common journey
Ballestra invites partners to help them shift methylene-urea production away from the UF resin and laminates industry and embed production within the fertilizer industry where it can make a significant contribution to fertilizer industry sustainability and improve nutrient use efficiency.
As a company, Ballestra offers robust and scalable process and finishing technologies, as well as agronomic, marketing, and regulatory support, plus the expertise to deliver new fertilizer product recipes. By combining these strengths with industry partners who have the necessary feedstock availability, marketing push and innovative spirit, methylene-urea technology could be scaled up to meet actual market demand.
New products, intellectual property (IP) and applications could also be jointly developed. Achieving reductions in natural gas consumption during fertilizer production would be another worthwhile objective.
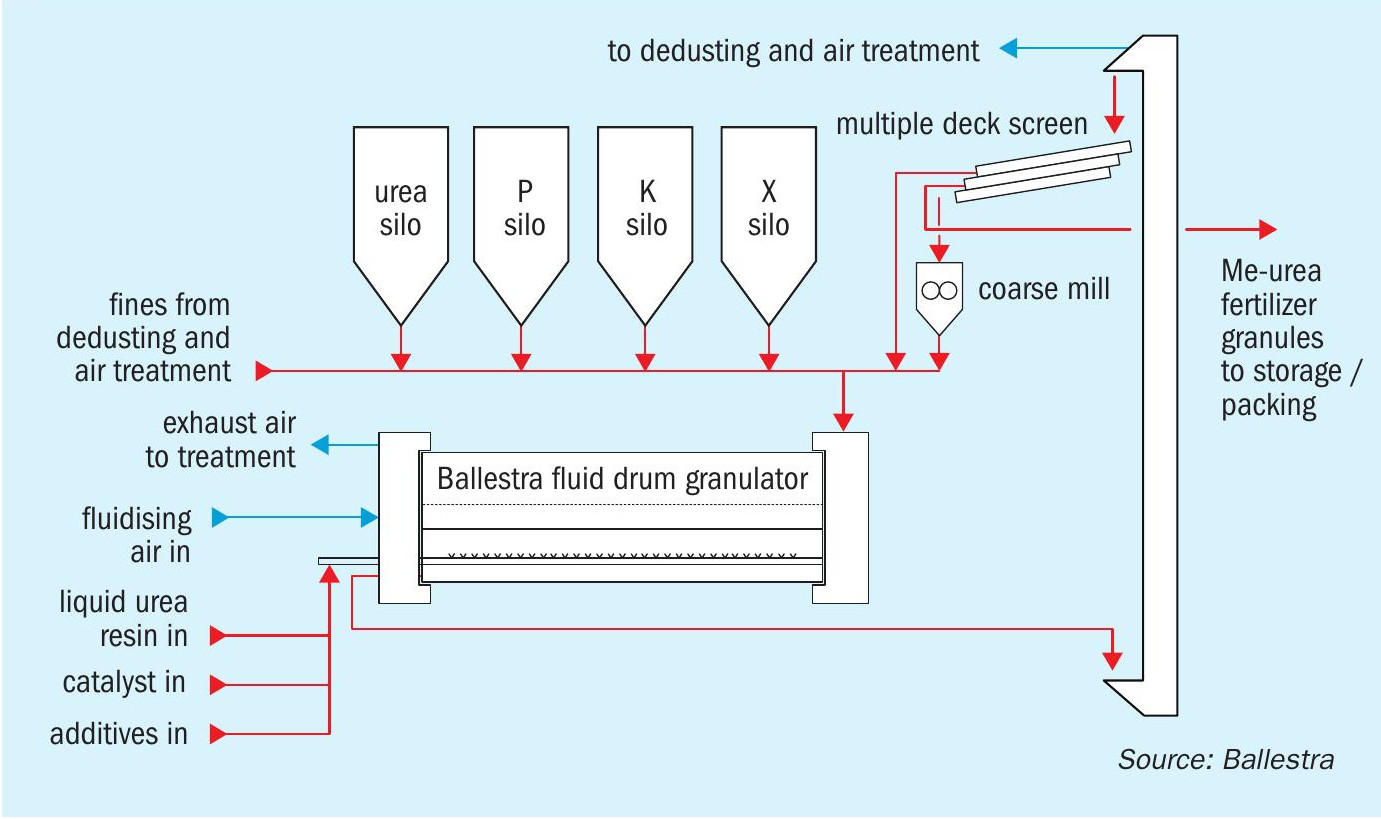