Nitrogen+Syngas 387 Jan-Feb 2024
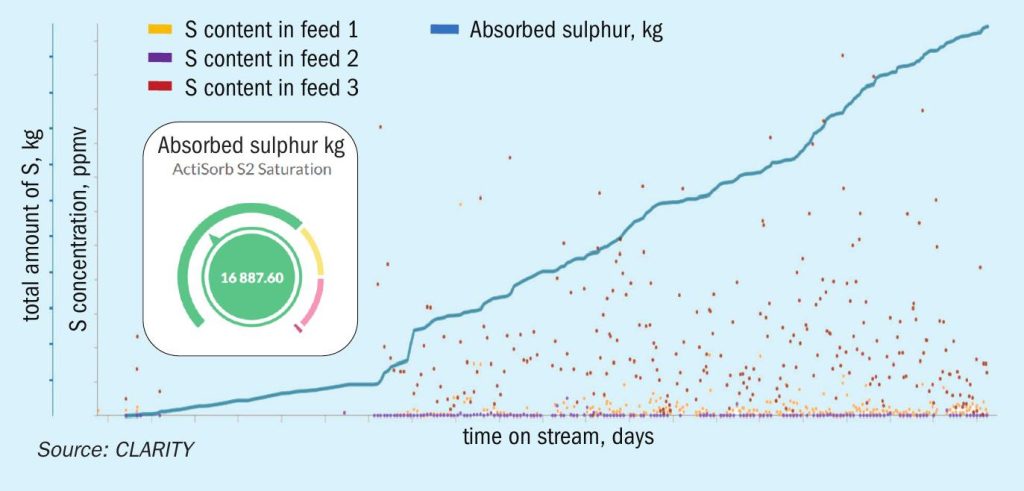
31 January 2024
Digitalised data to revolutionise catalyst operations
DIGITAL TOOLS
Digitalised data to revolutionise catalyst operations
Data has always been crucial for successful operations in the chemical industry, but the growing volume of data is only as good as our ability to analyse it. Now, the market is about to experience a step change in data assessment, and Clariant is fully on track, thanks to cutting-edge technologies for real-time data monitoring, visualisation, and information exchange.
Operation of chemical plants has long relied on control systems and thousands of sensors, amassing vast amounts of process and performance data over decades. However, drawing meaningful conclusions from this wealth of data to improve catalyst operations typically requires collaborating with catalyst providers who are well-versed in both the data and the catalyst. Additionally, plant operators depend on the technical expertise of the catalyst provider especially when troubleshooting issues or evaluating remaining catalyst lifetime. The relevant process data is usually not accessible to all stakeholders, so it gets shared through manual data workflows using spreadsheets and email. Manual data workflows are time-consuming, resource-intensive, and prone to human error. Deriving value from the extensive plant data is a major issue with these old-fashioned analysis and communication techniques.
Because data analysis occurs sporadically and retrospectively, rather than being continuously conducted proactively on an accessible shared platform, there are many instances where valuable insights from catalyst providers are missed. Implementing proper data visualisations and a collaborative approach could help reveal hidden opportunities to optimise plant operations that are currently being overlooked.
Chemical plants collect massive amounts of data to enable problem identification and reveal actionable patterns to prevent issues. At times however, the analysis itself may lead to faulty conclusions. Significant deviations in expected and measured catalyst performance can stem from offsets in analysers, especially after shutdowns. Evaluating catalyst performance is typically needed to pinpoint those measurement offsets. A collaborative data platform granting catalyst providers access to process data allows plant teams to rapidly catch such faulty readings.
Planning for catalyst replacements is also crucial for plant operations but is often constrained by budget and logistics limitations. Plant operators would benefit from more advanced evaluation of remaining catalyst lifetime to optimise their own replacement strategy. Rather than just identifying the right changeout timing, the ideal loading scheme and potential implementation of more suitable products can also be assessed based on prior catalyst cycle learnings. Then again, proper data visualisation can strongly contribute to identifying these key considerations for enhancement.
CLARITY™ : Bringing data to life
Clariant’s cloud-based service portal – CLARITY – is the solution for overcoming the limitations of current methods for managing catalyst operational data. The platform provides plant operators real-time access to catalyst performance data and advanced analytics tools via secure dashboards. By automating data sharing and visualisation, the service portal eliminates the need for cumbersome spreadsheet-based data handling.
CLARITY’s user-friendly interface connects plant operators directly to Clariant’s technical experts for optimisation guidance. Over 80 plants worldwide have already adopted the platform, with more than 380 active users in 28 countries. The platform features customisable, well-organised dashboards that present performance insights in an accessible manner. This enables users to easily monitor all critical parameters and extract key information to guide data-driven decision making for process enhancement.
The platform’s rapidly growing customer adoption is a testament to the substantial value it delivers. By pioneering innovative solutions that extract value from digitised data, CLARITY is establishing a competitive advantage in helping companies optimise catalyst performance.
As Lorena Oviol, Head of Applied Catalyst Technology at Clariant, stated, “CLARITY, together with Clariant’s catalysts experts, bring customer experience to a brand-new level. As competition continues to grow across industries, our state-of-the-art tools and data-driven insights will help our customers to stay ahead in their fields.”
Optimising plant performance
Turning complex data into impactful visualisations provides critical insights and uncovers hidden opportunities. Well-designed graphics and interactive visual analytics enhance decision making by highlighting key information and relationships. By bringing data to life, effective visualisation unlocks the full potential of digitised data, enabling better business decisions that drive success.
In ammonia plants, CLARITY allows for monitoring of critical data such as reformer tube wall and exit temperatures. Maintaining tube wall temperatures (TWT) within safe design limits is vital for ensuring long-term, reliable operation of the primary steam methane reformer (SMR). However, being too conservative risks missing opportunities for higher yields and profits. Uneven firing patterns in the SMR can cause damage to the tubes or reduce hydrogen output. Optimising performance requires operating closer to the limits while retaining a safety margin. CLARITY makes it easier for plant operators to maintain the right balance by providing an easy-to-understand visualisation of tube temperature data needed to optimise reformer output while remaining within safe parameters.
Case study A:
An ammonia plant customer experienced temperature deviations in the SMR outlet headers, signalling suboptimal operations. By using Clariant’s CLARITY portal, the customer gained insight into these deviations, uncovering hidden optimisation potential within the reformer. Leveraging CLARITY’s communication tools, the customer consulted Clariant experts on improving performance. Collaboratively, they adjusted burner firing to achieve more uniform operation and boost output: the customer implemented site changes while Clariant experts monitored performance until optimal conditions were achieved (Fig. 1). Reducing temperature variation widened the safety margin, enabling higher throughput and ammonia production. Ongoing monitoring allows continually optimised firing to capitalise on full capacity within safe parameters. The cooperative functionality of CLARITY streamlined joint efforts to fully optimise the SMR. This level of data-enabled collaboration positions the customer and Clariant to unlock the unit’s complete potential through partnership.
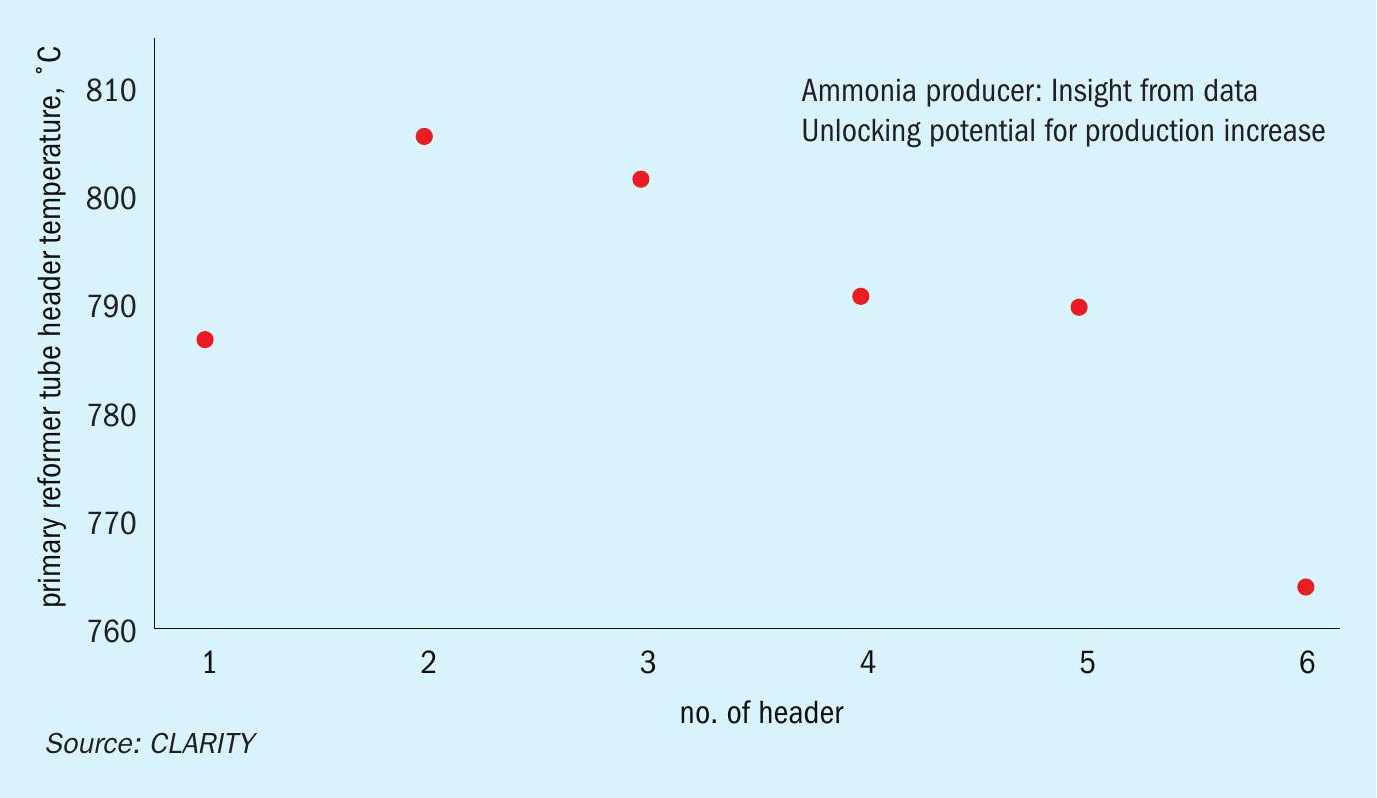
Accelerating repairs and reducing risks
Real-time data analytics and monitoring enabled by the CLARITY platform allows rapid identification, diagnosis, and resolution of plant issues. By providing data-driven insights, corrective actions can be taken immediately, and problems may be quickly resolved. This minimises costly downtime from disruptions and optimises the speed and efficiency of problem resolution. With the ability to detect and address risks in real-time, plant processes that previously required several days to fix can now be resolved much faster. The platform’s capabilities enable substantial time and cost savings.

Case Study B:
A syngas plant customer noticed a steady increase in methane leakage from a reactor after partial replacement of the catalyst in the secondary reformer. As they believed it limited their performance, the plant operators approached Clariant to determine the cause and find the optimal solution.
Through CLARITY’s dynamic visualisation tools, Clariant experts rapidly reviewed relevant plant data – temperatures, flows, analysers – to troubleshoot and check for root causes beyond the perceived poor catalyst performance. Simultaneously, CLARITY also enabled direct communication between the customer and dedicated Clariant experts for real-time collaboration. The portal automatically notified users of new advice and questions.
The Clariant expert quickly conducted correlation analyses in the tool by evaluating the values of different measurement points in the flow scheme (Fig. 2). This revealed that the measurement was incorrect since related trends diverged. A calibration check was recommended, which verified the Clariant expert’s conclusion: there was no issue with catalyst performance.
CLARITY’s integrated visualisation, seamless interaction capabilities, and instant expert access enabled and accelerated remote troubleshooting. This rapidly fixed an issue that would have previously taken much longer to identify, and could have resulted in an extended, unplanned, and unnecessary downtime.
Preventing costly shutdowns
In the case of ammonia, hydrogen, and methanol plants, zinc oxide (ZnO) sorbent is used to remove sulphur, which enters these plants with the natural gas feedstock. If sulphur passes through to the downstream catalyst reactors, it can poison the catalysts, dramatically reducing yields and catalyst life. Such catalyst poisoning often requires costly, unexpected shutdowns and early catalyst replacement. Therefore, close monitoring of the actual performance and loaded capacity of the ZnO sulphur sorbent is critical to preventing sulphur leakage and damage to the vulnerable downstream catalysts.
Among a multitude of data collected, CLARITY continuously monitors incoming sulphur levels and process gas flow rates to calculate total incoming sulphur. The cumulative sulphur value in an ammonia plant is compared to the expected saturation capacity of the loaded desulphurisation vessel sorbent (Fig. 3). The graphical display shows proximity to potential sulphur breakthrough and indicates whether sorbent replacement should be considered at the next available maintenance window.
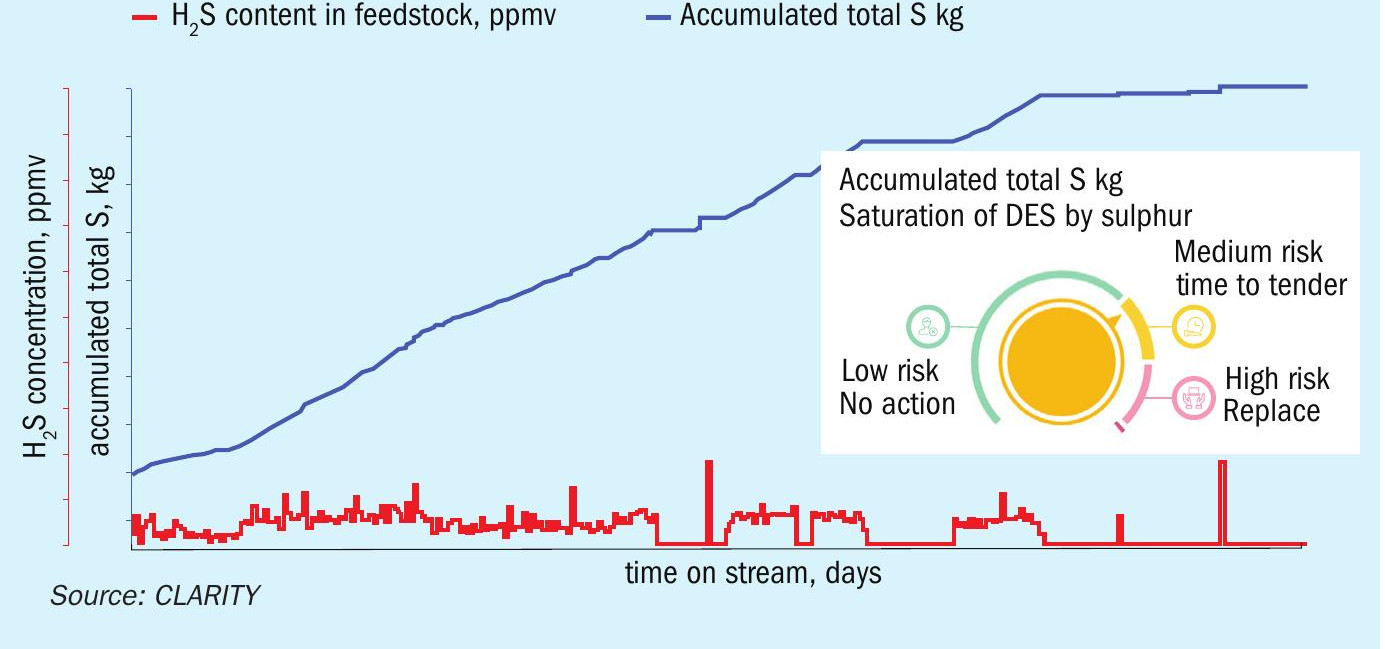
Case study C:
For a hydrogen plant with a two-bed desulphurisation system, the calculated, cumulative, sulphur pick-up capacity was 16,888 kg over approximately five years of operation. The CLARITY platform showed that given the loaded sorbent volumes and types, the estimated remaining sulphur capacity was enough to operate until at least the next turnaround for this plant at current inlet sulphur levels (Fig. 4). The continuous updates, based on actual incoming sulphur, provide increased accuracy in determining the remaining sorbent capacity.
Case study D:
Sulphur peaks can contain organic or inorganic sulphur species. With certain sorbent systems, organic sulphur may slip through during high inlet sulphur events. In such cases, an improved sorbent load capable of both sulphur hydrodesulphurisation and absorption is needed to minimise breakthrough. Without continuous monitoring via CLARITY, identifying peaks of organic sulphur as the root cause would be extremely difficult. The trending and visualisation features allow Clariant experts to review the situation before planned shutdowns and to recommend more suitable loading schemes or product combinations. This was implemented for an ammonia customer in February 2023 and despite similar high spikes in the incoming sulphur levels, the exit sulphur leakage was kept below detection limits – thereby better protecting the downstream catalysts and improving overall life and yields (Fig. 5).
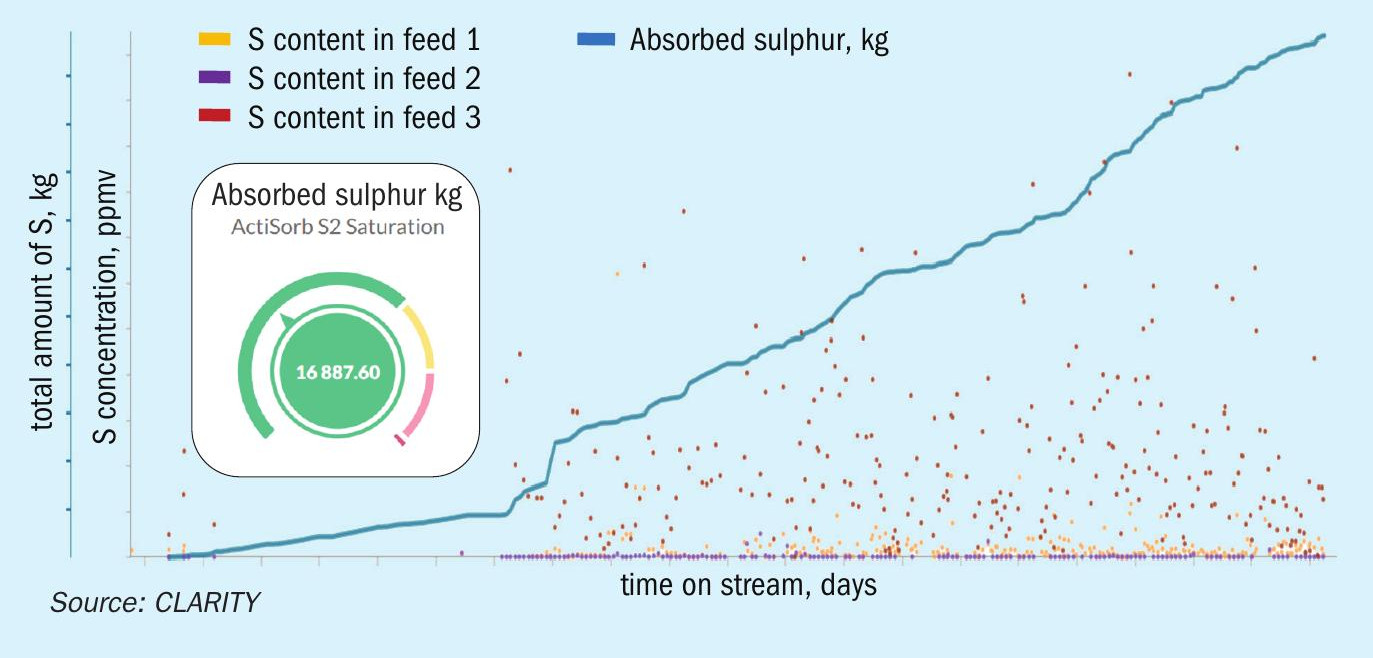
Driving continuous innovation
Clariant’s innovative CLARITY platform is transforming data utilisation in the chemical industry. By providing real-time analytics, visualisation, and collaboration tools, CLARITY not only facilitates efficient handling of process data but also enables plant operators to optimise catalyst performance, rapidly resolve issues, and prevent costly unplanned shutdowns. Numerous examples highlight the advantages of CLARITY for unlocking valuable insights from operational data. The platform’s ability to detect early signs of problems allows immediate implementation of corrective actions.
Overall, the digitalisation and automation of data analysis through CLARITY helps plant operators to achieve the best possible performance of Clariant’s catalysts, thus enhancing efficiency, productivity, and profitability of the plant. The rapidly growing adoption of CLARITY confirms that plant operators recognise the benefits of transitioning from conventional methods to leveraging advanced analytics and visualisation. As the article demonstrates, CLARITY can improve catalyst operations by facilitating communication between catalyst provider and plant operator.
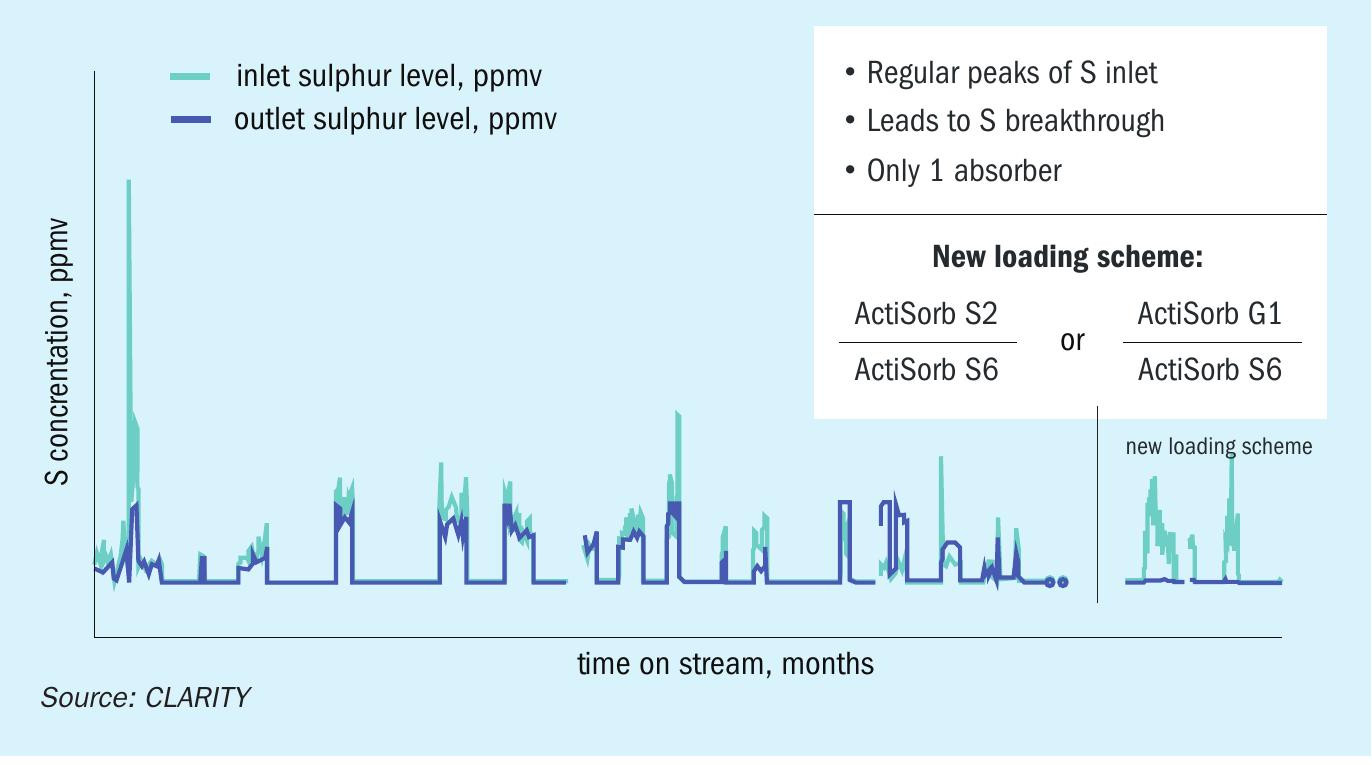
Going forward, Clariant is further advancing CLARITY’s capabilities by incorporating catalyst specific features like smart alerting and performance predictions that are supported by data science, artificial intelligence, and machine-learning tools. This next level of Clariant’s digital service will enable customers to optimise catalyst performance, both now and in the future, to support achieving the best possible lifetime efficiency. With this dedication to digital solutions, Clariant aims to directly contribute to increasing efficiency, sustainability and optimising its customers’ catalyst operations.