Sulphur 410 Jan-Feb 2024
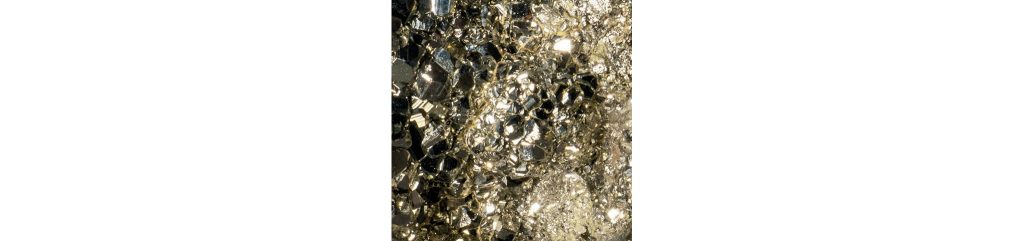
31 January 2024
The future of pyrite production
PYRITES
The future of pyrite production
Pyrite roasting as a source of sulphuric acid continues to be a significant, albeit minor sector of the overall acid market.
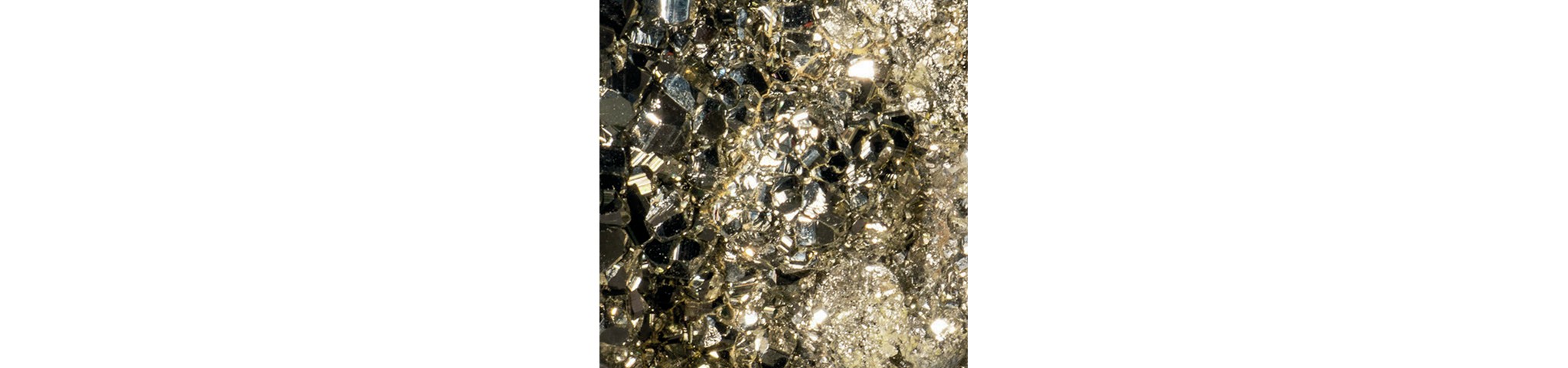
Iron pyrites (FeS2) are the most common sulphide mineral in the Earth’s crust. There are extensive deposits around the world, and prior to the development of Frasch mining, they were the dominant source of sulphur for sulphuric acid production, throughout the 19th and early 20th centuries. However, they fell out of favour as a source of sulphur, overtaken first by Frasch mining which began in 1895 in the US, and then by Claus sulphur recovered from oil and gas processing, which has come to dominate sulphur production, with acid derived from smelter off-gases the main secondary source of sulphur in all forms (SAF).
Global sulphuric acid production from pyrites reached a peak of over 30 million t/a in the 1970s, at which time it represented 22% of sulphur production in all forms. However, it has been in long-term decline since then, down to less than 7% of sulphur production in 2021. Production largely ceased in the United States in 1988, Brazil and Bulgaria in the 1990s, Albania and Spain in 2001, India in 2003, and Zimbabwe in 2008 with the closure of the Iron Duke mine. Nevertheless, some production continues in Finland, Russia, and particularly China, which now represents over 90% of world pyrite roasting acid production.
Production
The production of acid from pyrites is a pyrometallurgical process. The pyrite (pyrrhotite – Fe7 S8 – can also be used) rock is crushed or passed through a grinding mill to produce smaller particles with a larger surface area. There may also be a beneficiation step, using a process such as froth flotation, where chemicals are added to create a frothy mixture where the pyrite particles adhere to air bubbles and rise to the surface, allowing them to be collected and concentrated.
The crushed pyrite is then passed into a roaster. Metso uses an air blown circulating fluid bed system in its process. The pyrite is heated to a temperature of 600–1000°C, depending on the process, at which temperature the sulphide part of the mineral oxidises to sulphur dioxide and trioxide and the iron oxidises to a calcine mixture consisting of Fe2 O3 , Fe3 O4 , and FeSO4 , as well as oxides of any trace minerals in the pyrite (such as arsenic). The arsenic can be separated from the iron cinder in a two stage process with the arsenic volatilised in an oxygen free section before oxidation occurs, leaving it to be later recovered from the gas stream via a wet gas cleaning system. Waste hot gases pass to a heat recovery section such as a waste heat boiler to generate process steam. The sulphur oxide rich gas can finally be passed to a downstream conventional sulphuric acid plant.
Process economics
Pyrite was originally mined for its sulphur content, and as a convenient source of sulphuric acid. However, the recovery of large volumes of sulphur from oil and gas as a by-product and the recovery of sulphur rich off-gases from copper and other base metal smelting have collectively largely undercut the economics of pyrite mining for acid production, hence its gradual discontinuing in many of the countries that formerly used it, as noted above. Pyrite rock tends to be cheaper than elemental sulphur as a raw material, and the operating costs for a pyrite based acid plant can be lower or comparable, but the lower capital cost of a sulphur burning acid plant makes for faster payback in the medium term (though pyrite plants can be more profitable in the long term, depending on the price of sulphur).
In addition, the solid iron cinder contains around 30-60% iron. The production of 1 tonne of sulphuric acid usually results in the creation of 0.8–1.5 tonnes of iron cinder, and China produces more than 11 million t/a of it. The cinder is not very valuable, and sometimes is merely disposed of as tailings, but it can be used in the manufacture of cement or as ballast in road construction. And it can also be used a source of iron in steel manufacture, which has had particular application in China. China makes around 55% of the world’s steel, and the country imports large quantities of iron ore in order to do so. In 2023 China imported a record 1.18 billion tonnes of iron ore for steel manufacture. The iron calcine from pyrite manufacture can be used in lower grade steel manufacture and helps offset the process economics. Delivered costs of iron ore to Chinese ports are at present around $120/t c.fr, and even at a fraction of this the calcine still represents a valuable by-product. In addition, there are also often trace ‘impurities’ such as copper and gold in the calcine, and recovery of these minerals can also assist with the economics of the process.
There are however also additional drawbacks and costs associated with pyrite production, one of the foremost of which is acid mine drainage. When exposed to air, like in a mine, pyrite will fully oxidize in a matter of years. Microorganisms can also form on the mineral and speed up the reaction. In the presence of water this process generates sulphuric acid which can lead to environmental issues within and near the mine. As a result, modern mining practices prioritise the mitigation of environmental impacts associated with pyrite mining and processing, adding to the cost.
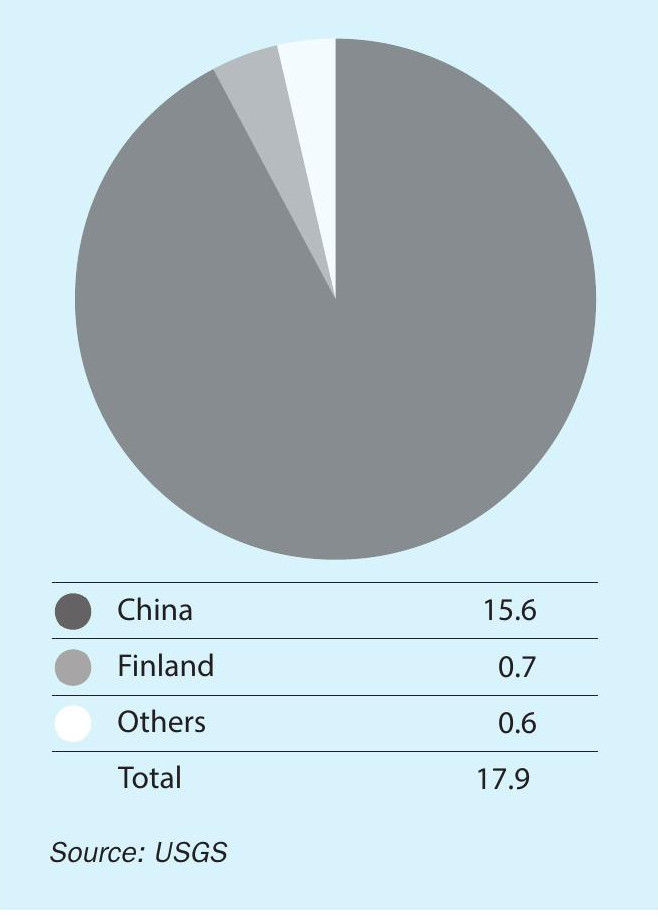
Acid production
After its long slow decline from its peak in the 1970s, global pyrite production has actually been at a fairly stable level over the past two decades. In 2021 it accounted for around 18 million t/a of acid production worldwide, most of this in China (see Figure 1). While production in several countries has been declining or ceasing, Chinese production was actually on an upward trend in 1990s and 2000s, with many of the smaller producers – there were over 350 producers of pyrite based acid in 2006 – closing at the same time that larger, more efficient and lower cost plants were completed. In 2006 Outotec completed the world’s largest pyrites roaster at Tongling Non-ferrous Metals, which produces 400,000 t/a of sulphuric acid, and Hunan Heng-yang started up a 300,000 t/a acid plant based on pyrites in 2008. Some pyrite roasters have converted their acid plants to sulphur burning, though the sulphur price spike of 2008 and continuing strong demand for both sulphuric acid and iron, continue to make pyrites roasting economical in parts of China. Chinese pyrite acid production peaked at 17.7 million t/a in 2010, but still amounted to 15.6 million t/a in 2021, representing about 17% of Chinese acid production that year.
Geographically, much of China’s sulphuric acid output is concentrated in Hubei and Yunnan provinces, with significant production also in Guizhou, Sichuan, Shandong and Anhui. Yunnan, Hubei, Guizhou and Sichuan are major fertilizer producing Others regions and capacity there is dominated by sulphur burning plants, while Shandong is a coastal chemical producing region, and Anhui has China a lot of smelter capacity. Pyrite-based acid production is concentrated in the eastern provinces of Guangdong, Anhui, Jiangxi and Liaoning (more than 75% of pyrite based production).
The future of pyrites
Outside of China, the next largest producer of acid from pyrites is Finland. Finland’s pyrites have mainly come from First Quantum Minerals Pyhasalmi mine, which produces the bulk of Finland’s pyrites. But this looks likely to come to and end soon. Underground mining at the site ended in 2022 when the zinc and copper deposits there were exhausted. FQM says that it expects to continue to produce 330-350,000 t/a of pyrite from pyrite rich tailings currently stored in one of the mine’s tailings ponds. However, pyrite recovery is not currently scheduled to last beyond 2025.
There have been predictions of the demise of China’s pyrite roasting acid industry for many years now, but the industry was kept alive via demand for iron and the burgeoning phosphate industry in China, which required ever-increasing amounts of sulphuric acid. However, China is now recovering increasing amounts of elemental sulphur from sour gas extraction in Sichuan and its increasing number of major oil refineries, and acid production has also been boosted by a large increase in copper smelting capacity, and pyrite-based acid must compete with both sulphur burning and acid offtake from smelters. In spite of this glut of acid capacity, China has continued building new pyrite roasting acid capacity, although this has been partially balanced by closures among older and less efficient capacity, and operating rates have slipped to around 70%. Nevertheless, there was still 21.2 million t/a of pyrite acid capacity in China in 2022, representing around 16.5% of total acid capacity. A stable or slow decline of this seems likely over the coming years, but the pyrite based acid sector will continue to be a small but significant part of China’s acid production.