Nitrogen+Syngas 388 Mar-Apr 2024
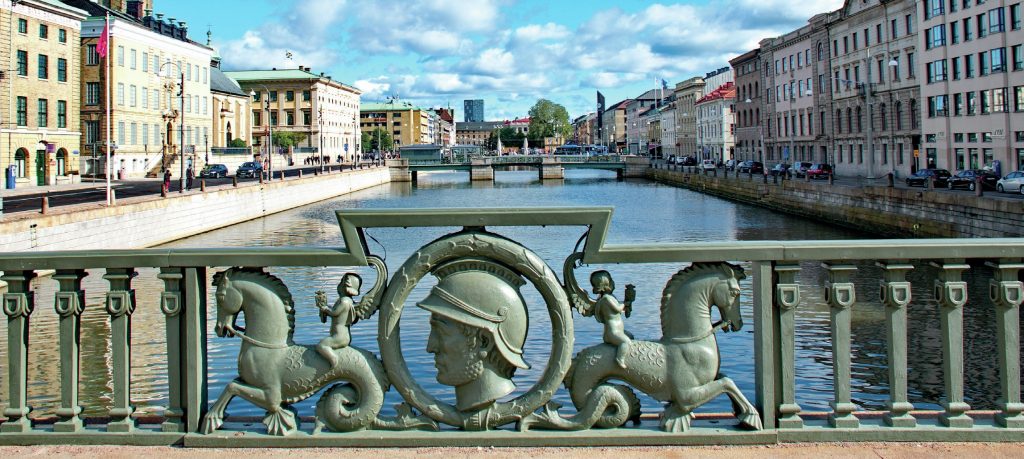
31 March 2024
Nitrogen+Syngas 2024
CONFERENCE REVIEW
Nitrogen+Syngas 2024
A summary of papers presented at CRU’s Nitrogen+Syngas conference, this year held at the Gothia Towers in Gothenburg, Sweden.
CRU’s Nitrogen+Syngas conference continues to provide a meeting ground for the nitrogen and allied syngas-based industries like methanol, combining market presentations from CRU’s own team of analysts with a large number of technical papers covering all aspects of the industry. Meeting at the Gothia Towers hotel and conference centre in the Swedish port city of Gothenburg once again this year, attendance was just under 600, and the accompanying exhibition was full with all 88 stands occupied.
Nitrogen markets
The first day was given over to a series of short technical showcase presentations in the morning, and a number of market and commercial papers in the afternoon. The first paper was of course the nitrogen market overview, this time presented by CRU’s new lead Mony Belon. Major gas benchmarks continue to fall, she said, and gas storage in the EU is at very high levels. There is more secure supply, and demand has fallen, leading to rising confidence in energy security in Europe. Ammonia prices are close to historical averages, back down after the spike following the Russian invasion of Ukraine. While up to 70% of EU ammonia capacity was shuttered in September 2022, this had fallen to 19% by September 2023, and while there have been some more closures bringing off-line capacity to 39% in January 2024, downstream nitrogen margins remain positive for ammonium nitrate production in the EU, and around zero for ammonia and urea for the next few months.
Most new nitrogen capacity additions are based on lower carbon supply – the pipeline for traditional ammonia production seems to be drying up, although some of the additional ammonia export availability in 2024 is coming from Russia as export becomes easier again. Incremental new merchant ammonia capacity is also coming onstream in the US (1.3 million t/a), Trinidad (600,000 t/a), and the Middle East (500,000 t/a).
On the downstream side, urea prices have followed the downward trend of gas and ammonia inputs. Russia remains essentially unhindered from exporting urea, with exports of 8.5 million t/a in 2023 and a similar figure likely for 2024. Another 4.7 million t/a of urea capacity is due to commission in 2024, mostly (3.2 million t/a) in China, as well as 0.8 million t/a in Russia. Indian imports continue to decline as new capacity comes onstream,. Indian production has risen 3.6 million t/a from 2022-24. Conversely, Brazil continues to rely heavily on imports and there is an optimistic outlook for crop production and urea demand. Brazil is becoming the largest global importer of urea, up to 7-8 million t/a. New urea import demand will come from Brazil, Argentina, Africa, Australia and the US.
Low carbon production
Marina Simonova, now with OCI, gave a producer’s perspective on lower carbon ammonia. The company is developing its new Texas Blue Clean Ammonia project, which will have a capacity of 1.1 million t/a when it starts up in the first half of 2025. OCI is also expanding its ammonia import terminal in Rotterdam to accept cargoes from overseas, with capacity rising from 400,000 t/a to 600,000 t/a and ultimately 2 million t/a. It is also doubling green methanol capacity to 400,000 t/a via a renewable natural gas pathway with green hydrogen from New Fortress Energy and biogenic carbon dioxide using biogas from the Beaumont City landfill site. At Beaumont, 95% of carbon dioxide will be captured and directed via a partnership with Linde and ExxonMobil for enhanced oil recovery in the US Gulf. OCI is also developing a low carbon ammonia value chain. It has signed a supply agreement with Rohm to supply low carbon ammonia for methyl methacrylate production, and is looking at ISCC+ certification.
Looking to the future, Marina saw demand for low carbon ammonia being driven by regulatory frameworks which are leading to use in power generation in Japan and Korea, demand for maritime fuel, and as a hydrogen carrier – Europe may need additional hydrogen volumes to meet its 2030 RePower targets. At present, global nitrogen trade (for all ammonia derivatives) stands at 115 million t/a ammonia equivalent, about half of this as urea. By 2030, the 19 million t/a of traded merchant ammonia may have nearly doubled to 18 million t/a of conventional ammonia and 15 million t/a of low carbon ammonia, and looking out to 2050, grey ammonia trade will be minimal and low carbon ammonia trade could reach 80 million t/a.
Eric van Dijk of TNO presented a different angle on low carbon nitrogen production, using carbon captured from steel production to make urea. The EU INITIATE project takes basic oxygen furnace gas (BOFG) from steel making – a mixture of carbon monoxide, nitrogen and water – and combines it with green hydrogen in a process called SEWGS – sorption enhanced water gas shift; a TNO development – which combines carbon dioxide separation with a shift reaction. The CO2 is then partly sequestered while the hydrogen and nitrogen are used in a Stamicarbon green ammonia converter using JM catalysts, then more CO2 is passed back to urea production. A 2.5 t/d pilot plant reactor is being developed, with the project aiming to ultimately make a bankable case for a 50,000 t/a demonstrator unit. The basic oxygen furnace is a batch process, leading to a dynamic feed to the reaction, and one of the INITIATE project goals is dealing with this dynamic feed composition.
Rob Stevens of Topsoe and Horisont Energi looked at some of the forecasts for green ammonia and methanol demand over the next 25 years. Increasing low carbon methanol demand is likely to run ahead of the ability to supply biogenic carbon to manufacture it. Topsoe is looking at alternative pathways, including green Fischer-Tropsch and green methanol production using captured carbon. Horizont Energi is developing the Barents Blue ammonia plant, which will capture 99% of carbon emissions. A final investment decision is expected late this year or early next, with production of 1 million t/a by 2029.
Oksana Melnyk of the German Society for International Cooperation (GIZ) highlighted the work of the German federal government in encouraging sustainable production and use of fertilizers. On the nitric acid side, it has encouraged the installation of nitrous oxide abatement technology via the Nitric Acid Climate Action Group (NACAG), as N2 O emissions offer a significant source of CO2 equivalent emissions (around 100 million t/a) which can be abated with relatively cheap technology (around 1-3 euros per tonne of CO2 equivalent). GIZ has supported nine nitric acid plants with grants totalling 20 million euros and abated 2.2 million t/a of CO2 e. There are also ongoing tender processes in Jordan and Columbia and work continues with Thailand, Georgia and Uzbekistan. However, it is also working on a range of other issues across green hydrogen, food security, ‘smart’ farming etc.
Production costs
CRU’s Charlie Stephen presented an overview of ammonia costs, beginning with a review of gas costs, especially in Europe, over the past few years. The average cost of ammonia production in Europe is expected to fall from its present level of around $390/t this year to around $350/t in 2028. Some of this fall is due to falling feedstock costs as new LNG export capacity worldwide, especially in the US, but also Qatar (and some – for the global market – from Russia) lowers the cost of gas imports. This will bring EU ammonia production costs below the level of Indian and Chinese producers.
Meanwhile, there is continuing pressure to reduce emissions and carbon taxes and trade schemes continue to proliferate. Chinese coal-based production remains the largest carbon emitter. The EU carbon dioxide price is rising as the number of free allowances decreases. By the 2030s, it could reach $160/t, and could add $165/t to the cost of ammonia production by 2028. However, delivered costs to the EU from the US will be lower than domestic European production costs even taking into account the carbon border adjustment mechanism (CBAM).
Low carbon ammonia applications could double the market for ammonia by 2050, but project announcements are not attracting finance and final investment decisions outside of the US where the 45Q tax credit has made a different. High costs for green ammonia means that additional incentives will be needed for a large scale uptake.
Pranshi Goyal of CRU looked at urea costs. The key exporting regions remain the Middle East, North Africa and Nigeria, Russia, China, and Southeast Asia. Europe, the largest regional importer, has been the marginal cost producer of urea since 2021. While costs have come down from their 2022 peak, they remain above the cost of Chinese coal-based production, which had been the marginal cost production capacity beforehand. Looking to the future, carbon costs will have an increasing impact on production costs, but Pranshi did not foresee a major change in trade flows due to Europe’s carbon border adjustment mechanism. Nevertheless, it seems that Europe may become a premium paying market for urea.
Technical papers
With more than 90 papers in three parallel streams across two days, it would be impossible to mention all of the technical papers, but the following is a sample. Of note were the continuing improvements in process control and the use of AI and machine learning systems to improve plant operation.
Ammonia technology
Perhaps unsurprisingly the ammonia technology session focused on green ammonia production, and specifically the challenges of dealing with a variable energy feed from wind or solar power when running a continuous process like ammonia conversion. Total and EREN have are developing a large scale green ammonia plant at Magellanes in Chile using local off-grid wind power. The plan envisages a hydrogen powered power generation unit to cope with periods of low wind energy.
Kinetics Technology meanwhile has been experimenting with compressed air storage of energy to balance peaks and troughs of energy production as part of their GALCES (Green Ammonia Liquid and Continuous Energy Supply) process, which incorporates Green Ammonia Technology from sister company Stamicarbon. The heat from compression is integrated into the process including the air separation unit for producing stoichiometric quantities of nitrogen for the reaction.
KBR has been working with electrolyser supplier SolydEra to develop its K-Green ammonia process. SolydEra’s stacks are used reversibly as electrolysers and fuel cells to balance power and hydrogen generation, which allows for more flexibility in operation and a reduction in the total investment cost of the plant by reducing the need for battery energy storage.
Topsoe looked at some of the problems in running dynamic ammonia synthesis. Lower flows of hydrogen mean that a recirculating synthesis loop must be used, but higher conversion rates can lead to lower pressure and stress fatigue from pressure changes. Topsoe’s green ammonia loop can dynamically adjust its load by 3% per minute and operate reliably over sustained periods with loads as low as 10% of nameplate capacity. This dynamic flexibility results in greater uptime and less need for costly storage solutions for reserve supplies of green hydrogen or renewable power.
JM and Fertiberia have been experimenting with a side stream feed to Fertiberia’s ammonia plant at Puertellano in Spain using hydrogen from a 20 MW electrolyser. The addition of hydrogen and stoichiometric quantities of air and the use of JM’s higher activity Katalco 74-1 promoted synthesis catalyst means that the reformer can be run at lower duty, reducing gas consumption. A new monitoring and control too, the AMMCON Dashboard, has also helped with integrating the ammonia feed and optimising plant operating conditions.
Air Liquide has been working with KBR and Clariant on an autothermal based low carbon ammonia scheme, and updated the conference on work showcased last year. Johnson Matthey likewise use either a standalone ATR or an ATR coupled with a gas heated secondary reformer for their Leading Concept for Hydrogen (LCH) process, and this was also presented.
Ammonia cracking
Ammonia’s potential use as a carrier for hydrogen means that it must be broken down back into its components at the other end of the supply chain, and several papers looked at this process, the first session focusing on the catalysts required to accelerate the reaction. Casale showcased their MACH2 (Mega Ammonia Cracking for H2 ) technology. It is open to the use of both nickel or ruthenium based catalysts – the former is cost competitive but requires high temperatures and higher capex, the latter can use lower temperatures but is more expensive. Catalyst choice is on a case by case basis. Casale is offering it in capacities of up to 1,300 t/d of hydrogen production.
Enercat is pursuing the ruthenium catalyst route, with alkali metals best as dopants, such as potassium or calcium oxide. A large megapore distribution leads to improved ammonia diffusion. Rare earth metal oxides such as cerium oxide as ruthenium carriers show promising benefits for the ammonia cracking reaction. Research work continues. Heraeus likewise has been experimenting with ruthenium catalysts and a number of different dopants.
KBR is developing its H2ACT process for hydrogen production up to 1,200 t/d, working with Clariant on the catalyst side. The process uses proven nickel catalyst at higher temperatures (>700°C).
Finally, Technip described a low intensity ammonia cracking process with recuperative high-grade heat recovery to sustain the cracking reaction. The design of the recuperative catalyst tube achieves higher throughput and higher heat recovery compared to a conventional pellet-packed tubular reactor layout.
Methanol
Toyo presented its g-Methanol (green methanol) technology, which uses direct synthesis from carbon dioxide and hydrogen. The Japanese government expects low carbon methanol to be used as a fuel and a chemical feedstock as part of its green transition strategy. At the moment there is a 10 t/d demonstrator plant for the process under construction in India, due for startup in 2Q 2024, using Toyo’s proven MRF-Z reactor. Toyo is targeting full commercialisation in 2026, with a proposed scale up to 300-600 t/d, and has a Methamaster program which can optimise grid feed, battery or hydrogen storage to deal with fluctuating feeds based on the lowest levelized cost of methanol for any given site.
Clariant are offering a promoted version of their MegaMax catalyst series, MegaMax 900 DCARB, with even higher activity, for methanol synthesis from carbon dioxide as part of green methanol plants.
Urea technology
Green feeds are typically smaller than the world scale plants that gas-based ammonia production can offer. So Saipem presented a smaller scale modular urea plant design optimised for green ammonia feeds, down to 100 t/d, or blue feeds using an enzyme-based carbon capture system.
Stamicarbon, conversely, looked to an ultra-low energy reactor for large capacity urea plants, expanding the existing ULE concept from plant sizes of 2,000-2,500 t/d up to 3,850 t/d.
Casale offered HYPER-U, a new high efficiency self-stripping urea process which lowers the demand on medium-pressure steam and cooling water. The main innovation consists of an additional carbamate decomposition step upstream of the conventional medium pressure section.
Nitric acid
Umicore discussed the recent spike in the price of rhodium and looked at ways of reducing rhodium content in nitric acid catalyst to reduce cost. The laboratory work also managed to increase selectivity to produce less N2 O and increase yield for ammonia conversion by 1%, leading to potential savings.
Heraeus presented two cases of back flow in nitric acid converters, in the first case from time delays in valve openings and in the second due to leakage from the superheater, and recommended strategies for mitigating these faults and cleaning contaminated gauzes.
Abu Qir experienced a pressure drop in their EnviNox tail gas treatment unit, increasing over several weeks following a restart. It transpired that long service had led to creep and elongation of bolts holding the catalyst basket, leading to leakage of catalyst from the basket and broken catalyst entering the expander. The basket was re-welded and the catalyst replaced.
Finally, NobelClad described their explosive weld technique for coating steels with thin layers of protective coatings for corrosion resistance, including tantalum and zirconium cladding and super ferritic 470LI steel with low nickel content which offers good performance in urea and nitric acid environments.