Nitrogen+Syngas 388 Mar-Apr 2024
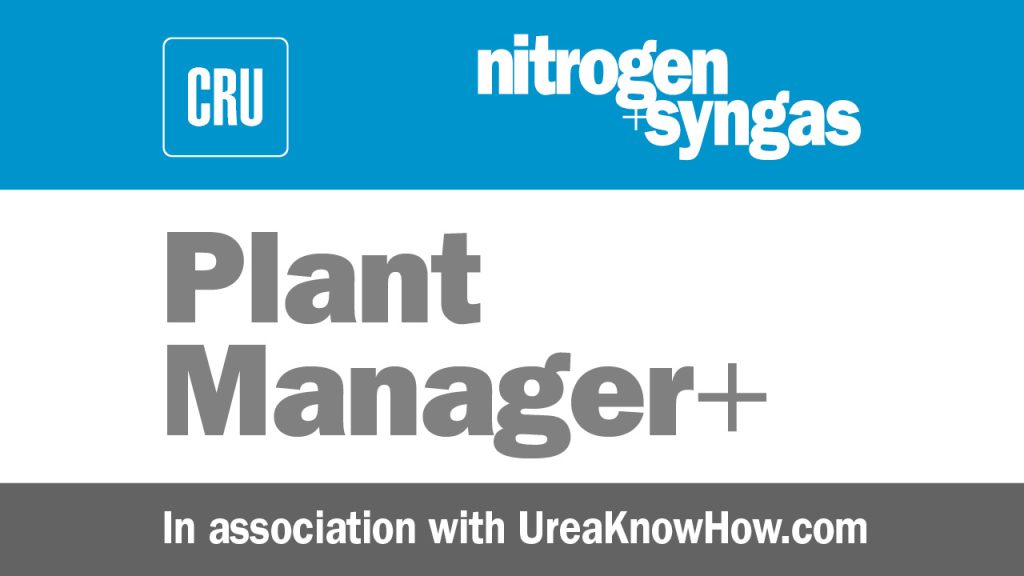
31 March 2024
Problem No. 72: Reuse of off-spec wastewater
Every urea plant is also a water plant as the overall reaction starts with two molecules of ammonia and one molecule of carbon dioxide resulting in one molecule of urea and one molecule of water. Further water is added to the process via the steam ejectors in the evaporation section. All this water, which is contaminated with ammonia, carbon dioxide and urea plus possibly other contaminants like formaldehyde, methanol, oil, etc is collected in an ammonia water tank and then sent to a wastewater treatment section. The purpose of the wastewater treatment section is to reduce the ammonia, carbon dioxide and urea levels to acceptable levels. First the wastewater is treated in a first desorber column, where LP steam is used to strip off the ammonia and carbon dioxide, reducing the ammonia content from approx. 6-8 wt-% ammonia to approx. 1 wt-% ammonia. Nothing happens with urea in the first desorber as temperatures are too low to hydrolyse the urea back to ammonia and carbon dioxide. This takes place in the next step, in the hydrolyser, which can be quite a large counter current column operating with MP steam at approx. 23 bar (Stamicarbon design) or a horizontal deep hydrolyser operating at approx. 33 bar (Saipem design, refer to figure). Downstream of the hydrolyser there is another desorber column to strip off the remaining ammonia and carbon dioxide. Nowadays, boiler feed water quality can be realised by modern wastewater treatment. But at higher plant loads the operating margin in the wastewater treatment can become too small leading to higher ammonia and urea levels during certain operating conditions…
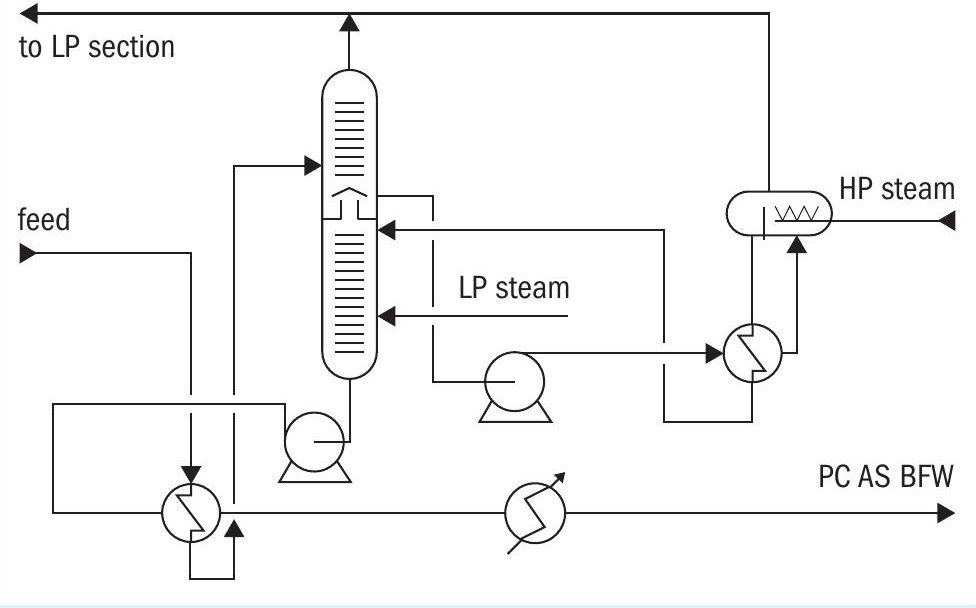
Niraj Nimje of RCF Thal in India initiates this round table discussion: In our Saipem plant, after the booster ejector and condensers in the vacuum section, we face problems due to a change in concentration of the wastewater section feed tank and off spec condensate is generated which is then wasted as effluent. What methods are available to treat this off-spec condensate to make it boiler feed water grade? I have heard of a polishing unit being used for such cases, but what is the maximum concentration of the contaminants that is permitted in such cases and what arrangements need to be in place to ensure a proper quality?
Prem Baboo, retired from NFL, India and Dangote Fertilizers, Nigeria shares his wide and valuable experiences: We have done the following modifications in the vacuum section:
- The crown flushing of 2nd stage vacuum separator (cone flushing) has been changed to 99.7% urea melt to minimise the water load and to minimise prilling diversion.
- The condenser flushing has been changed to wastewater (wastewater to distillation); a 2-inch line is taken from the distillation tower (desorber) feed pump for flushing, minimising the water load on the wastewater section.
- Water monitoring and a water balance is prepared in each shift.
- We take wastewater containing 1.0 ppm urea and 2-3 ppm ammonia to the demi water plant and this suitable for demi water production. We maintain the following parameters:
– Distillation (desorber) pressure 1.8 kg/cm2 g, temp in top 112°C and in bottom 132°C. Low pressure steam to distillation flow is 11.0 t/hr.
– Wastewater flow is about 80-82 m3 /hr at 3,500 t/d plant load.
– Hydrolyser pressure 34 kg/cm2 g and temperature 232°C. Steam to hydrolyser about 5.0 t/hr.
– Wastewater analysis is 5.5 to 6.0% ammonia and 0.9 to 1.0 % urea.
Nagaraju from Notore Fertilizer in Nigeria shares his experiences: The purified waste water from our 2nd desorber contains really high levels of ammonia and urea. In our plant (Stamicarbon) it is typically about 100 ppm urea and 50 ppm ammonia, how is that possible?
Prem replies: Wastewater with such a high concentration of ammonia and urea cannot be used as demi water. It means your hydrolyser is not working properly. The hydrolyser outlet urea should be less than 1-2 ppm. Please clarify your hydrolyser pressure and temperature and desorber temperature.
Niraj responds: We are already doing all you have mentioned and we are getting boiler feed water quality water without any polishing unit. Our hydrolyser and distillation units are working fine with 25 kg/cm2 and 1.8-2 kg/cm2 respectively but after crown washing, condenser booster ejector washing, or during any upset, the wastewater tank (V6) concentration changes (temporarily) and off-spec wastewater is generated. During these situations we increase the steam flows to the hydrolyser and distillation column. After a revamp our wastewater load also increased from 40 to 50 m3 /hr. So, it is sometimes difficult to maintain the quality of water generated after performing the activities mentioned above. As we don’t have a polishing unit, we are looking forward to it, and want to convert even small quantities of off spec wastewater into boiler feed water.
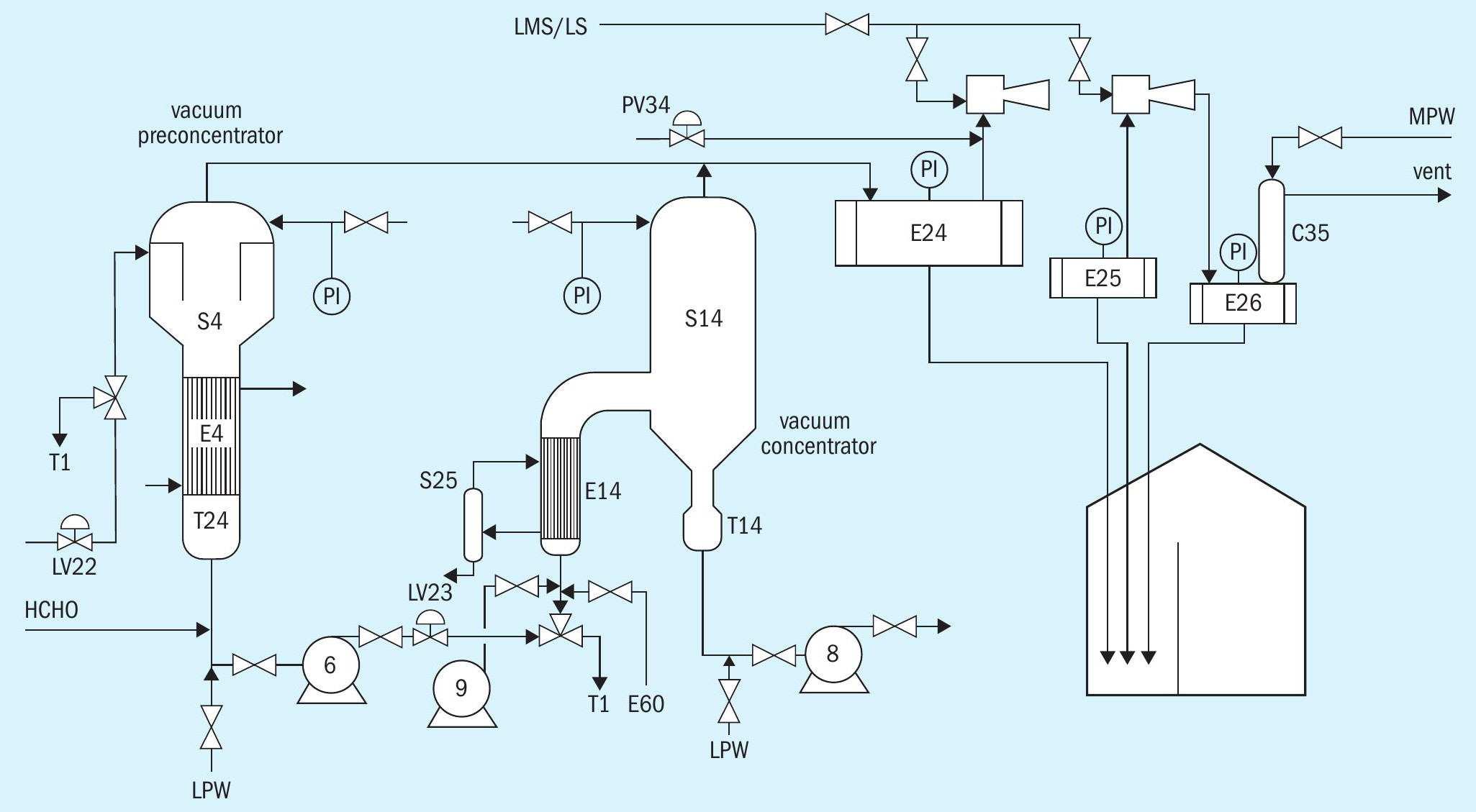
Mark Brouwer of UreaKnowHow.com, the Netherlands joins the discussion: I agree with Prem that water with ammonia and urea concentration 1~3 ppm is acceptable for use as boiler feed water after passing through a polisher.
@Prem Are you using this purified waste water in the boilers as boiler feed water directly? Did you observe any corrosion in the boiler or steam lines?
Prem replies: For boiler feed water, ammonia is not a problem because the ammonia is added anyway for raising the pH of the boiler feed water. The problem is the high urea content due to a problem with your hydrolyser. The hydrolysis reaction is a function of temperature: you cannot raise the temperature beyond 223°C at a pressure of 25 kg/cm2 . With the revamp you should be able to also revamp this section, either by increasing the residence time or raising the pressure. The residence time of the hydrolyser is reduced after revamp.
Phong of Petro Vietnam Ca Mau Fertilizer in Vietnam also joins this discussion: Our plant use Saipem technology for urea synthesis and Toyo technology for granulation. Our MMU section didn’t work well so we decided to stop operating the MMU section and feed formaldehyde directly to the P06 pump suction line (see figure above). In this case our wastewater after treatment still has presence of HCHO (more than 500 ppm). The parameters at the top and bottom of the distillation tower are 4.2 bar and 130°C (top) and 4.7 bar and 157°C (bottom). The condition in the hydrolyser is 31 bar and 230°C.
How does HCHO at concentrations above 500 ppm affect boiler feed water, and how do you treat it?
Mark replies: Formaldehyde will convert into formic acid in the hydrolyser. Depending how one reuses the purified process condensate one needs to take additional measures to avoid corrosion problems. For example, reuse as cooling water make-up may be possible without further treatment, while reusing is as boiler feed water for 40 bar steam will require further purification. One could send the purified process condensate to the inlet of the demi water section where the carbon filter and ion bed exchangers will take care of the formic acid.
Prem adds: The best answer was given by Mark. The formaldehyde and methanol are controlled by the ammonia plant: the formaldehyde formation is in the LT CO shift converter and the methanol is formed in the HT CO shift converter. Both come with the CO2 feed. Generally, the methanol is separated in the CO2 compressor interstage cooler with separators. In the urea plant itself there is nothing one can do except control the compressor inter stage temperatures so that maximum methanol / formaldehyde can be separated through separators.
Mark adds another suggestion: If you are injecting the HCHO as anti-caking agent for granulation/prilling section, it should normally be injected to the discharge of P8 and not P6, in this case you will have much less HCHO in your wastewater treatment section.
Nikhil Kamat from India also joins the discussion: What should the ammonia and urea content in the treated wastewater be if it is to be used as boiler feed water?
Prem replies: In our plant, the treated waste water contains about 2 to 3 ppm ammonia and 0.5 to 0.8 ppm urea. This treated water is directly sent to the demi water plant (cation/anion/mixed bed) and then used as boiler feed water. The turbine condensate and steam condensate are sent to the demi water plant for iron removal only i.e cation unit and then used as boiler feed water.