Nitrogen+Syngas 388 Mar-Apr 2024
31 March 2024
Reducing emissions in nitric acid production with tertiary abatement
EMISSIONS REDUCTION
Reducing emissions in nitric acid production with tertiary abatement
To comply with environmental legislations, all new and most existing nitric acid plants must implement measures to reduce N2 O emissions to the atmosphere. This article explores the opportunities presented by Stamicarbon’s tertiary abatement technology for both existing and grassroots nitric acid plants to enhance sustainability and efficiency and discover the advantages of incorporating these technologies into a green fertilizer complex.
Like most industries, the fertilizer industry strives to reduce greenhouse gas emissions. Besides developing new technologies to achieve this, traditional technologies are evolving to cope with the climate goals to reduce environmental impact while meeting the latest emission regulations.
Existing greenhouse gas emissions regulations
The number of systems and initiatives for emission regulations worldwide is increasing as countries work to achieve the climate goals set in the Paris Agreement adopted by 196 parties at the UN Climate Change Conference in Paris. In the EU and several other regions of the world, Emission Trade Systems (ETS) are in place to regulate the amount of CO2 emitted by companies, but also other GHG emissions – specifically nitrous oxide (N2 O) and perfluorocarbons (PFCs). In countries with an ETS in place, carbon credits are awarded to companies, allowing them to emit a fixed amount of carbon dioxide or the equivalent amount of another greenhouse gas.
With the need to reduce emissions, abatement systems that remove hazardous gases from the exhaust stream of processes, are getting more important. Many existing plants do not have such systems and still need to comply with environmental regulations. A tertiary abatement reactor provides a solution by removing nitrous oxide (N2 O) and nitrogen oxides (NOx) from the tail gas produced by nitric acid plants.
Nitric acid technology
Nearly all industrially produced nitric acid is manufactured by the high-temperature catalytic oxidation of ammonia (the Ostwald process) in two main steps:
- the oxidation of ammonia (NH3 ) to form nitric oxide (NO), which is further oxidised to nitrogen dioxide (NO2 );
- the absorption of the nitrogen dioxide (NO2 ) in water (H2 O) to form nitric acid (HNO3 ).
Stamicarbon, the nitrogen technology licensor of the MAIRE engineering group, offers its proven mono- or dual-pressure design. In the mono-pressure process (see Fig. 1), oxidation and absorption sections operate at the same pressure level. Different pressure levels are used for the oxidation and absorption sections in the dual-pressure process (see Fig. 2). The oxidation section is operated at pressures between 4 and 6 bar(a), while the absorption section operates between 8 and 12 bar(a), combining the advantages of medium-pressure combustion with the efficiency of high-pressure absorption.
The main characteristic of both processes is a specific heat exchanger network downstream of ammonia oxidation. This configuration has several advantages. The heat exchanging network has specific process conditions selected to prevent corrosion and ensure that no proprietary materials are required for equipment manufacturing.
In addition to using standard stainless steel in place of special materials, another key advantage of Stamicarbon’s nitric acid technology is its high energy efficiency. The process is designed to minimise heat losses and maximise heat recovery from the process streams. This decreases the internal consumption of steam and lowers the operational costs.
Stamicarbon’s nitric acid technology is also designed with environmental concerns in mind. The technology incorporates measures to minimise emissions of greenhouse gases and other pollutants. The use of modern abatement technology allows for the reduction of nitrogen oxides and nitrous oxide, which can be reduced to almost zero, disposing of an environmentally safe tail gas.

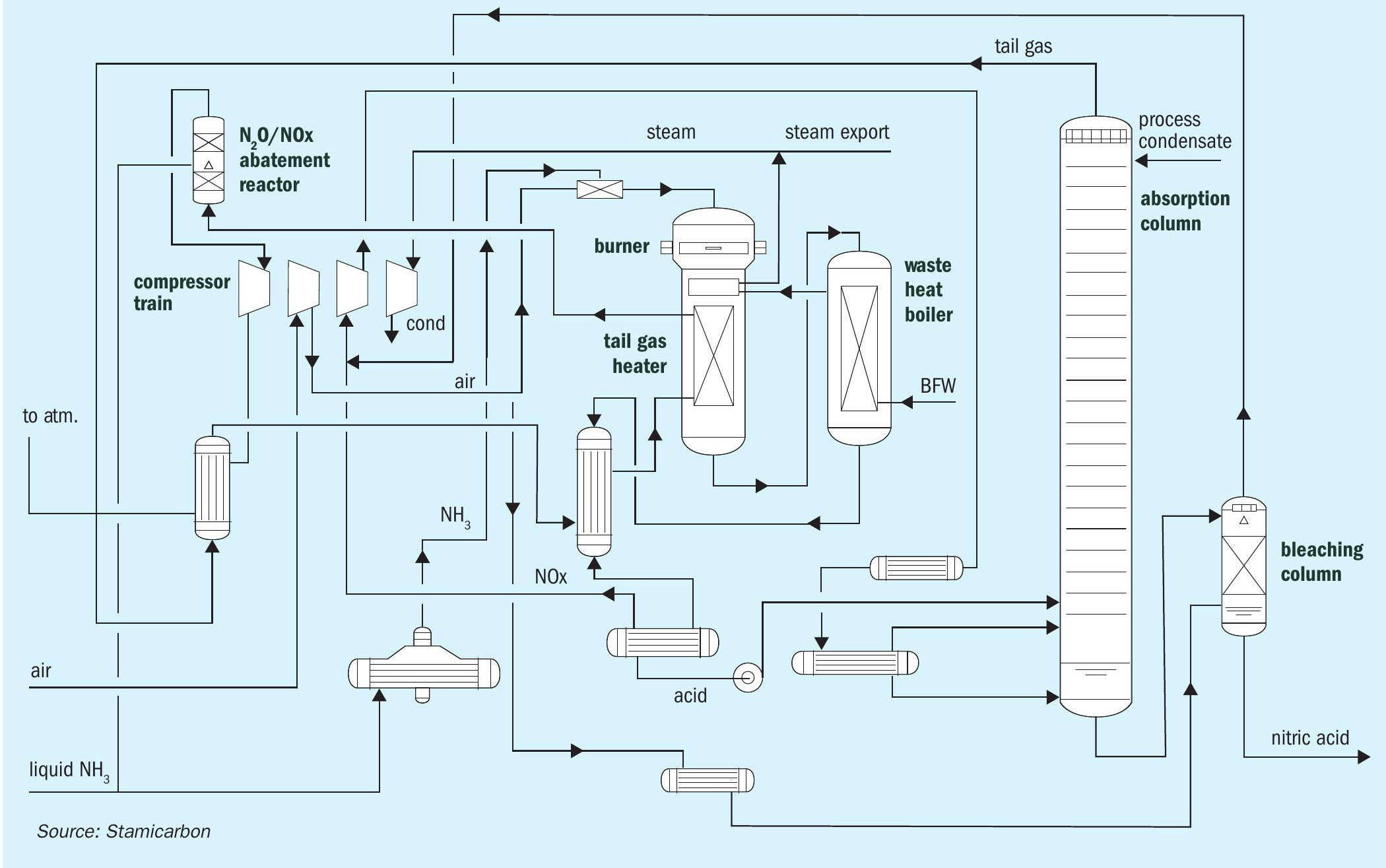
Emission control in nitric acid plants
The tail gas (off-gas) from nitric acid production mainly contains nitrogen, water and impurities, such as NOx and N2 O. NOx stands for nitrogen oxide and nitrogen dioxide, gases that contribute to air pollution, smog and acid rain. N2 O – nitrous oxide, commonly known as laughing gas – is a powerful greenhouse gas, estimated to be about 300 times more powerful than CO2 .
To comply with environmental legislations, all new and most existing nitric acid plants must implement measures to reduce N2 O emissions into the atmosphere. N2 O is formed on the precious metal gauzes of the primary catalyst package in the ammonia burner as a by-product of ammonia oxidation. There are several locations in the plant where N2 O could be eliminated. However, the tertiary abatement system is the optimal solution for removing both N2 O and NOx simultaneously. The process conditions at that location are suitable for reducing both components in a single unit, offering additional savings on capex and opex.
Stamicarbon offers a unique technology that ensures significant greenhouse gas emission abatement and an adequate mixing between ammonia and tail gas, thus eliminating ammonia carryover, and minimising the pressure drop across the catalyst beds. A key safety feature is the prevention of catalyst particles from reaching the downstream tail gas expander. In addition, the system’s design also allows for flexible catalyst selection based on the tail gas temperature for every nitric acid plant technology.
Tertiary abatement system for grassroots nitric acid plants
The system consists of a reactor with two packed beds holding an iron-zeolite catalyst. The first bed reduces the main part of the N2 O, while the second bed eliminates the remainder of the N2 O and the NOx. To achieve the latter, ammonia is supplied to the tail gas leaving the first catalyst bed.
6NO + 4NH3 → 6H2 O + 5N2
6NO2 + 8NH3 → 12H2 O + 7N2
2N2 O → 2N2 + O2
In the Stamicarbon nitric acid process, the tail gas temperature upstream of the expander is above 480°C. This temperature is reachable by a proper heat integration in the system, with the last tail gas heater placed inside the burner and close to the catalytic gauzes. Such high temperature of the tail gas maximises the energy efficiency of the process and provides several advantages to the abatement system:
- The high temperature increases the efficiency of the catalyst, reducing the catalyst volume needed.
- N2 O can be simply removed by thermal decomposition, which eliminates the use of natural gas or any other reducing agent in the first catalyst bed.
- There is no possibility of ammonia slippage, since at 480°C, ammonia is decomposed into N2 and H2 .
- It is possible to combine NOx and N2 O removal in one bed since the temperature is suitable for both reactions.
- Standard stainless steel is used as the material of construction for the tail-gas expander.
In other words, the tail gas temperature of 480°C represents the optimal conditions in terms of capex and opex: it reduces the amount of catalyst required, allows easy combined removal of NOx and N2 O in a single device without the addition of methane and allows the use of standard stainless steel as the material of construction for the tail-gas expander.
Upstream of the abatement system, the tail gas typically has the following concentrations:
NOx: 400-600 ppmv
N2 O: about 1000 ppmv
Downstream of the tertiary abatement, these figures are reduced to levels below 10 ppmv.
Acting as a one-stop shop for designing and delivering equipment and catalysts, Stamicarbon collaborates with leading catalyst suppliers to offer optimal and reliable tailor-made solutions, accommodating various process conditions and emission requirements.
What about non-Stamicarbon plants?
As mentioned, the Stamicarbon nitric acid process scheme is designed to have the tertiary abatement operating at favourable process conditions, which is beneficial in terms of capex and opex. However, to comply with current environmental regulations on emissions, existing plants also need to implement the removal of N2 O and NOx.
Stamicarbon can provide a tailor-made solution for any nitric acid technology, regardless of whether the tail gas operating temperature is higher or lower than that of the standard design. Through partnerships with suppliers worldwide, Stamicarbon offers advice on the type of catalyst, reactor design, and reactor location on a case-bycase basis to meet client requirements.
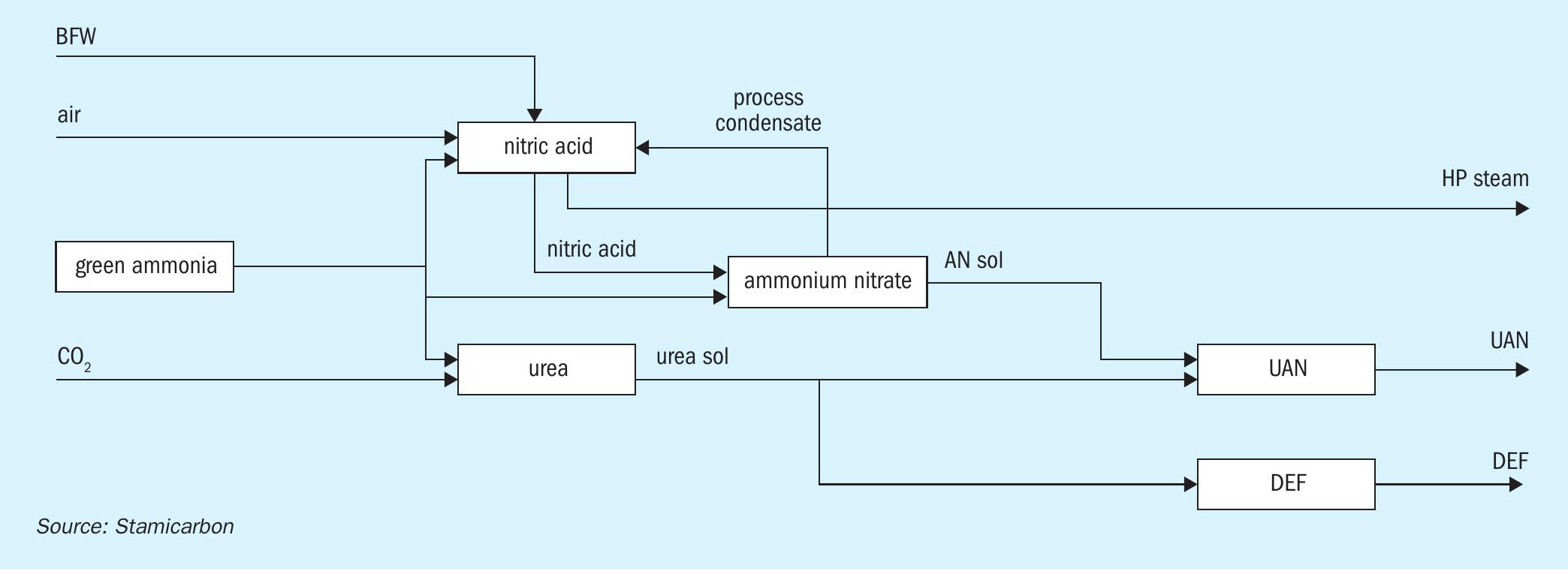
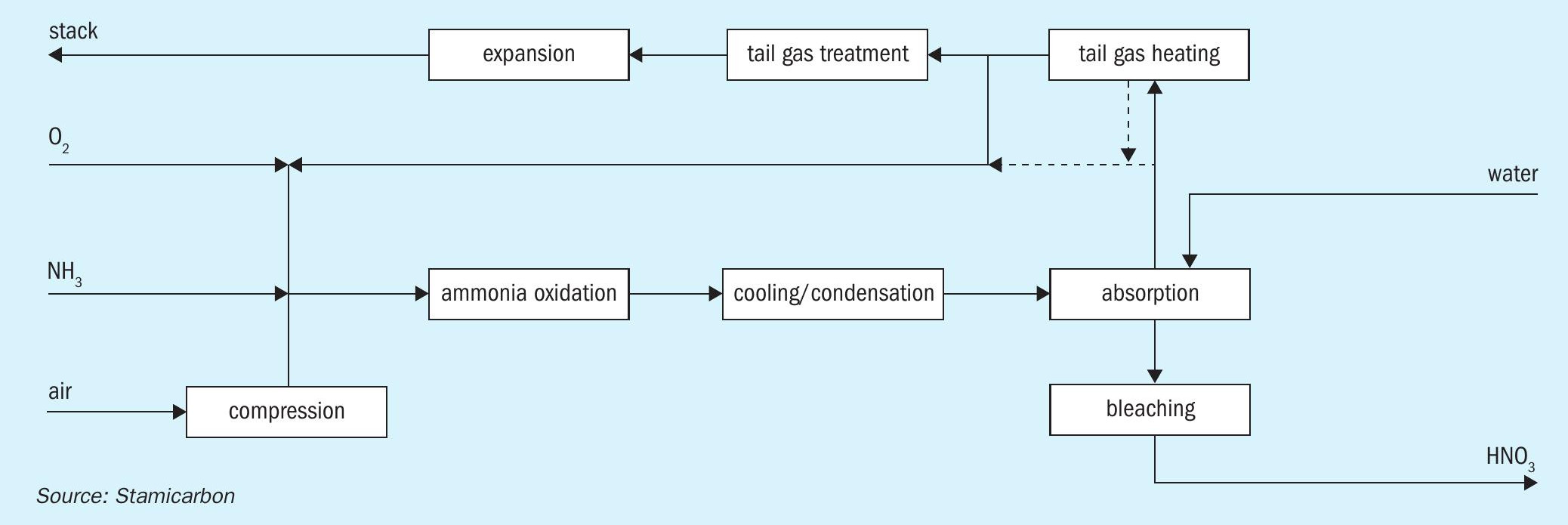
This approach aims to minimise the impact of this new unit on the rest of the production process while considering all constraints indicated by the producer.
Integration of technologies in a green fertilizer complex
Having a comprehensive portfolio of nitrogen technologies, including nitric acid, urea, green ammonia, and other processes offered by the MAIRE Group, Stamicarbon ensures integrated plant operations that make the entire complex economically attractive and environmentally friendly.
A nitric acid plant with tertiary abatement can efficiently be combined within a larger complex (Fig. 4) that may include a green ammonia plant to produce carbon-free feedstock for the downstream units, a urea plant to produce DEF through a carbon capture technology in which CO2 is recovered as a waste stream from an existing industrial process, and an ammonium nitrate plant to produce UAN via a mixing unit. In this case, oxygen from water electrolysis, in combination with the nitrogen from the generation unit, is effectively used in the nitric acid plant.
At the same time, to ensure that the mixture of ammonia and oxygen remains below the explosive limit upstream of the burner, additional nitrogen is required, and this can be sourced from recirculating the tail gas, as illustrated in Fig. 5.
This integration offers several advantages over conventional methods:
- There is a more positive power balance since compressor power is reduced, increasing steam production by more than 30%.
- Capex is reduced owing to the need for a smaller air compressor unit and expander.
- Conversion efficiency is increased by looping NOx gases back into the reaction (NH3 burner, the bleacher, or both).
Additionally, the total catalyst volume, which is necessary to achieve the same level of abatement, is significantly reduced, by up to 40%, due to the recirculation of a part of the tail gas stream, which reduces the total flow of tail gas to be treated and therefore the amount of NOx and N2 O in the off-gas.
Conclusion
The industrial emission of greenhouse gases into the atmosphere is a universally recognised problem addressed by the Paris Agreement. One of the most potent greenhouse gases is N2 O, which is emitted from the tail gas of nitric acid plants. The Stamicarbon tertiary abatement technology, with its unique process scheme, enables the ideal process conditions for N2 O and NOx removal without the need to import natural gas from outside battery limits. Offering an opportunity to retrofit any type of nitric acid plant with guaranteed performance, Stamicarbon’s tertiary abatement system is notable for its simple and reliable design.
Tertiary abatement plays a crucial role in the design of a green fertilizer complex. When integrated with other technologies to achieve efficiency with minimal investments and operational costs, it ensures the plant achieves a minimal
“Offering an opportunity to retrofit any type of nitric acid plant with guaranteed performance, Stamicarbon’s tertiary abatement system is notable for its simple and reliable design.” environmental footprint, making it an effective strategy for environmental sustainability.”
To accelerate the implementation of this highly efficient technology within existing nitric acid plants, Stamicarbon actively participates in the Nitric Acid Climate Action Group (NACAG) initiatives, a global project led by the German Government. This involvement enables nitric acid plants in partner countries to receive technical and financial support for implementing N2 O abatement technology. n
Resources