Sulphur 411 Mar-Apr 2024
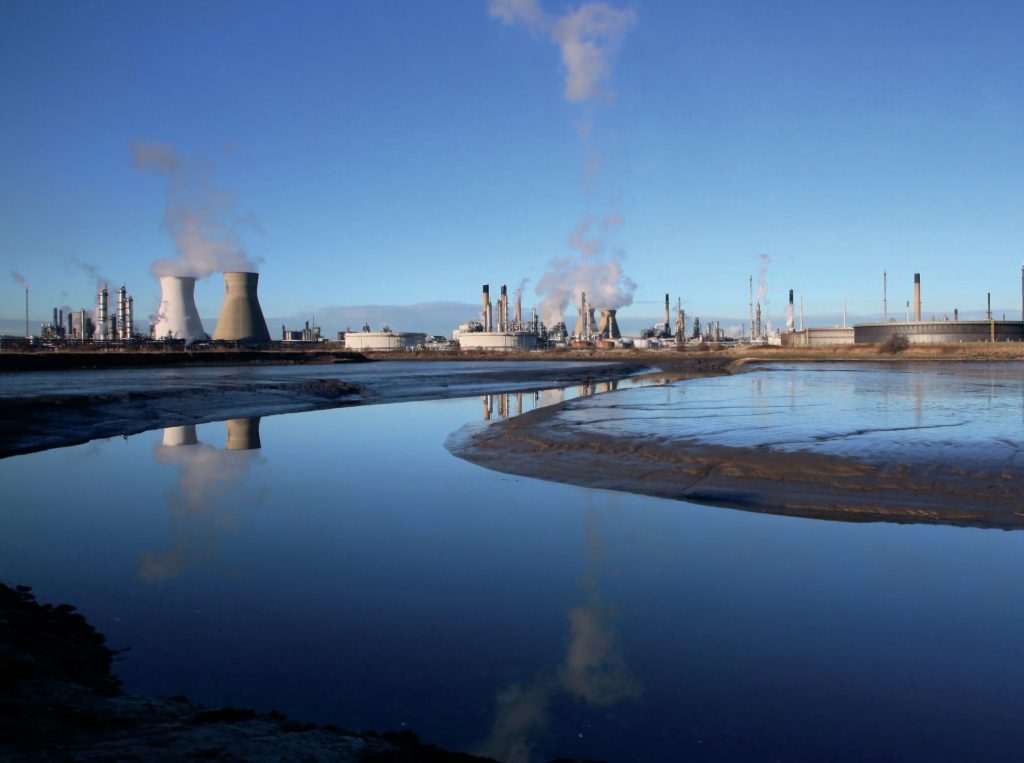
31 March 2024
Sulphur in Europe
EUROPE
Sulphur in Europe
Falling volumes of sulphur from refining and sour gas could turn Europe into a sulphur importer.
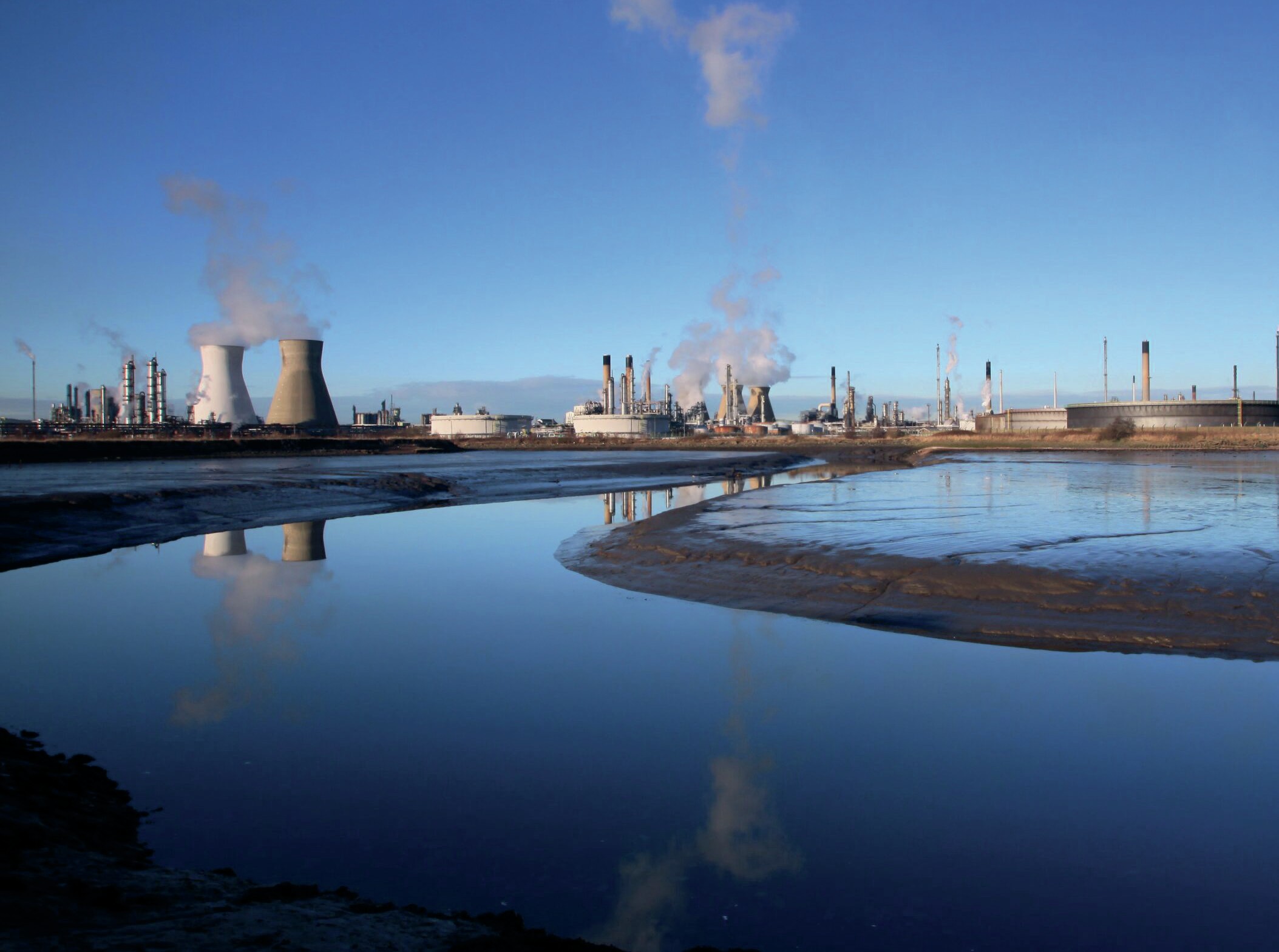
Europe’s supply of sulphur is falling, potentially turning the continent into a net importer and changing the dynamics of the market away from liquid sulphur. Traditionally, European sulphur output has come from three sources; refining, sour gas processing, and Poland’s sulphur mine. However, output from all of these sources has been in long term decline.
Refining
The European refining industry has seen a prolonged contraction. Since 2009, out of 100 operational refineries in Europe, 26 have closed, and another five have switched towards biofuels processing. The drivers behind this have mainly been falling domestic demand and cheaper imported products. European demand for refined products has fallen from a peak of around 15.2 million bbl/d in 20002005 to 12.7 million bbl/d in 2019, and then dropped by another 1.0 million bbl/d due to covid. Although there has been a bounce back after covid restrictions were lifted, the war in Ukraine has also had a major impact by restricting imports of Russian crude and – at the end of 2022 – banning it altogether, although there is now a growing industry in sanctions evasion by, for example, transferring oil between vessels to mix Russian crude with crude from other sources to disguise its origin. European refinery output in late 2023 was down by 600,000 bbl/d compared to the same period for 2022. Most of the decline in demand from 2005-2015 was not from reduced use of transport fuels, but rather the phaseout of electricity generation from oil and oil products, but now European refiners face a continuing fall in fuel demand from reducing consumption as more electric and hybrid vehicles are sold. Out to 2030, fuel consumption is expected to drop by about one third compared to 2018 figures, removing around 2 million bbl/d of demand for refined products.
Refinery margins are also back lower, after a year following the invasion of Ukraine when high fuel prices meant that refineries were making money for a while. The reduction in supply of diesel from Russia has also kept margins for that product good. Nevertheless, periods of loss making have dissuaded European refiners from investing in upgrading and modernising refineries, and also led to cutbacks in maintenance which have led to a spate of incidents forcing shutdowns in the past year or so.
There is also increased competition from cheaper refineries in other regions, including the Middle East such as Kuwait’s new 615,000 bbl/d Al-Zour refinery, and West Africa, with the 650,000 bbl/d Dangote refinery in Nigeria due to start up in 2024.
The expected weaker demand outlook for oil products, and an increased focus on emissions performance has prompted a wave of announcements by oil refiners to close or convert capacity to non-crude feedstock. Six European refineries have closed since 2020, mostly older, less complex refineries. This may reach eight following the decision by UK-Chinese joint venture Peotrineos to convert its 150,000 bbl/d Grangemouth refinery in Scotland into an import terminal, and the expected closure of Shell’s 147,000 bbl/d Wesseling refinery in Germany in 2025. Total loss of capacity between these refineries is around 935,000 bbl/d. Eni is also looking at converting its 84,000 bbl/d Livorno refinery in Italy to focus on base oils and biofuels and ending crude refining.
On the sulphur side, the restrictions resulting from the invasion of Ukraine have forced European refiners to replace Russian oil with lighter and sweeter crudes, particularly from the United States. This means a lower output from the refineries’ hydrocracking, fluid catalytic cracking and coker units, of potentially up to 7%.
Sour gas
At the same time, sulphur from sour gas processing is also continuing to decline. With the closure of the Lacq plant in France and its conversion to CO2 capture and storage, sour gas processing in Europe is now limited to the Grossenkneten gas field in Germany. Production here is expected to continue decreasing year on year as reserves are depleted. In 2010, sour gas processing at the Grossenkneten plant was about 12 bcm, but in 2022 that was 5 bcm, and sulphur production has dropped to below 400,000 t/a, as shown in Figure 1.
Based on reported proven reserves, the operation has a few years of production remaining, but there is a risk that it may prove uneconomical before reserves are fully depleted. The tight availability of natural gas in Europe stemming from the war in Ukraine and related trade issues means that the gas field is currently being strongly utilised, and this may shorten its life.
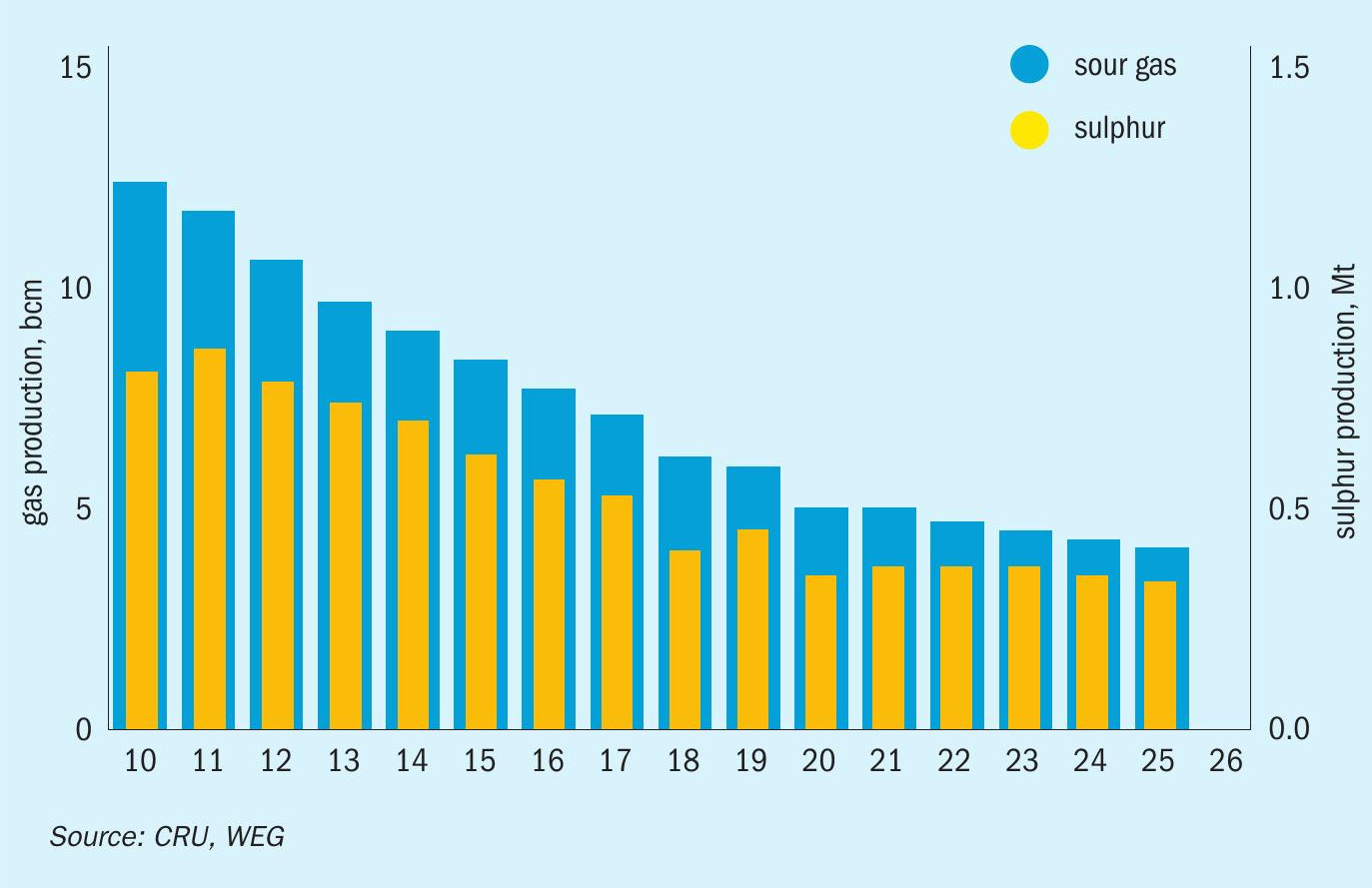
Demand
On the demand side requirements for sulphur have also been falling. The European chemical industry has faced issues with high feedstock and energy costs since the Ukraine war began, and there have been a number of closures or operators running at reduced rates. This was also true of downstream phosphate processing in Europe to produce fertilizers. Overall European sulphur consumption for 2023 was down nearly 30% compared to 2022, helping to more than offset the fall in production. As with other commodities, there are also issues with cheaper imports, in areas such as caprolactam and titanium dioxide, which have weighed on European chemical production. Falling energy costs should bring some of this capacity back, but it remains to be seen to what extent this occurs.
Remelting
Sulphur consumers in Europe are geared up to handle liquid sulphur cargoes. This limits their option to import and remelt solid sulphur, although small volumes of liquid sulphur are imported from the US. A few years ago, refinery closures and falling sour gas sulphur production led to increased interest in sulphur remelter projects to import solid granulated sulphur from overseas, providing supply flexibility in much the same way that Mosaic’s sulphur remelter in Florida has done.
In 2020, Saconix bought the assets of the Brake sulphur terminal as part of its plans for a terminal and melter there, which were announced in 2019 with planned capacity of 200,000 t/a. Aglobis also announced in June 2020 that it planned to build a terminal on the Rhine with 400,000 t/a of remelting capacity. However, as falling sulphur demand helped to offset production cutbacks, and refineries began running at high rates to take advantage of improved margins in 2022 and early 2023, so the need for these projects began to seem less pressing. But now the pendulum seems to be swinging once again, and there is renewed interest in possibly moving these projects forward over the next few years, in anticipation of tighter liquid sulphur markets in Europe, such as have been seen in early 2024.
Acid
There is a trade-off between sulphur and sulphuric acid demand in Europe depending on the relative prices of the two commodities. When sulphur prices are high and acid prices are low it makes sense for consumers to buy acid if they are able to handle it. This is complicated by export demand, however, with importers like Morocco occasionally in competition with domestic buyers. Europe is overall a net sulphuric acid exporter, with a number of base metal smelters providing surplus acid. European sulphuric acid prices dropped considerably from a peak in June 2022 following the Ukraine invasion due to a lack of demand from downstream consumers driven by high energy costs. Prices reached a low point in August 2023, since when they have risen back to around $50/t.
With European acid demand forecast to recover or even increase slightly over the next few years, and sulphur supplies continuing to fall, it is possible that Europe could turn to being a net sulphur importer over the next couple of years.