Nitrogen+Syngas 389 May-Jun 2024
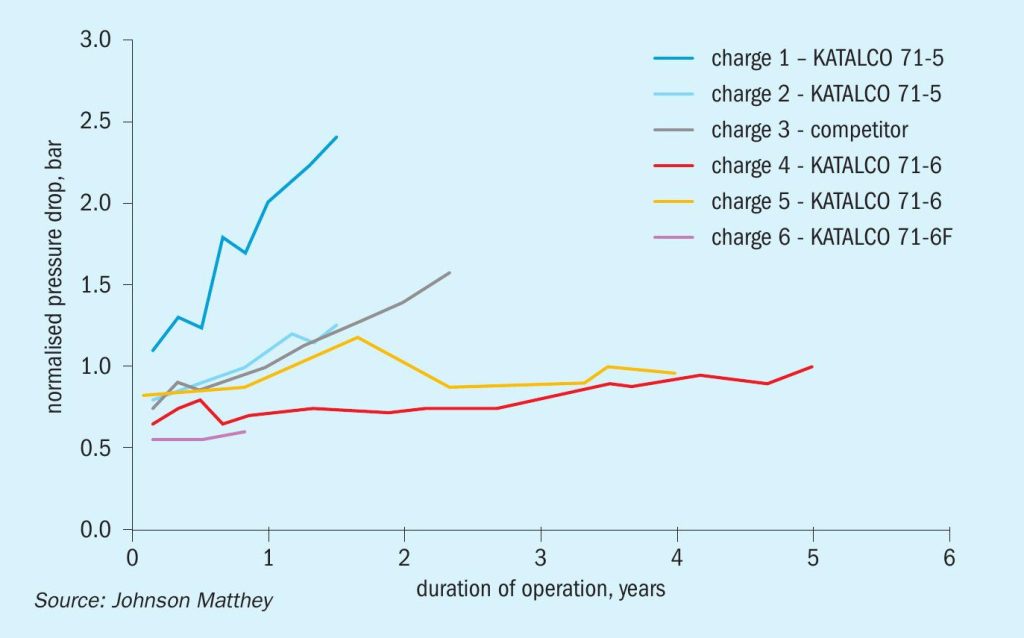
31 May 2024
A catalyst for the most demanding HTS applications
HTS SHIFT CATALYST
A catalyst for the most demanding HTS applications
Tim O’Connell and Emily Viney of Johnson Matthey introduce KATALCO™ 71-7F, the latest innovation in Johnson Matthey’s KATALCO 71 series catalysts for high-temperature shift (HTS) reactions. With its robust innovative ‘F’ shape providing lower lifetime pressure drop, JM expects KATALCO 71-7F will enable large-scale plants to increase ammonia production in the most demanding HTS applications.
Dedicated ammonia production using natural gas is the dominant route to make ammonia. Currently, most of the ammonia is converted to nitrogen-containing fertilizers. The established manufacturing process to make ammonia from natural gas comprises steam-methane reforming, water-gas shift, methanation, and ammonia synthesis. Steam-methane reforming converts natural gas into CO and H2 which is sent to the water gas shift (WGS) section. WGS catalyst converts CO into H2. After the WGS section, methanation removes the remaining CO. This sequence of reactions efficiently and effectively maximises the H2 generated. In the ammonia synthesis loop, H2 and N2 are reacted to produce ammonia. Reliable performance of the shift catalysts therefore maximises the hydrogen feed to the ammonia converter, contributing to ammonia yield from the plant, and therefore to the business success of ammonia manufacturers.
Johnson Matthey has developed KATALCO 71 series catalysts for high-temperature shift (HTS) reactions. Conventional cylinders and F shaped catalysts are available. The ‘F’ shape innovation provides lower lifetime pressure drop performance. Each of the catalysts in this series, provide a unique mixture of physical and chemical properties.
Improvements in durability of HTS catalysts benefits all manufacturers of hydrogen, and subsequent downstream manufacture of ammonia; however, these performance benefits are exaggerated in the largest plants. Johnson Matthey HTS catalysts have been exposed to the rigours of large ammonia plants with demanding duties, and the KATALCO 71-6 and KATALCO 71-6F catalysts have shown durable, high performance in these plants.
KATALCO 71-6 possesses superior strength over previous generation KATALCO HTS catalysts. The superior strength of KATALCO 71-6 has indeed shown greater durability in use, whilst delivering a reduction in the volume of catalyst due to its enhanced pore structure and activity.
Fig. 1 exemplifies these performance enhancements and the benefits achieved when KATALCO 71-6 and KATALCO 71-6F were installed in a large-scale ammonia plant. KATALCO 71-6 was the fourth charge of HTS catalyst installed in this plant, following significant pressure drop issues experienced with previous HTS installations, which had been KATALCO 71-5 and HTS catalyst supplied by another catalyst manufacturer. KATALCO 71-6 reduced the pressure drop and increased catalyst lifetime, allowing the plant to reduce the frequency of catalyst changes. For the latest charge, KATALCO 71-6F, pressure drop performance is even better, combining durability of KATALCO 71-6 with the advance shape of KATALCO 71-6F. KATALCO 71-6F has provided the most robust catalyst performance since this plant was commissioned.
Johnson Matthey’s experience within these demanding plants has driven the development of a new catalyst, KATALCO 71-7F, which extends the physical properties of existing HTS catalysts that Johnson Matthey have observed to be valuable for hydrogen production.
KATALCO 71-7F catalyst testing and performance
Johnson Matthey developed KATALCO 71-6, and subsequently KATALCO 71-6F, to enhance performance within HTS reactors with the sort of demanding duty which thermally ages HTS catalysts. The development of KATALCO 71-6 benefitted from an enhanced pore network which enabled improved transfer of gas through catalyst pellets compared to earlier generations. KATALCO 71-6 also benefitted from an improved intimacy between Fe3O4 active sites and Cr and Cu promoters which act to stabilise the Fe3O4 active species and the Fe active sites responsible for catalysing the water gas shift reaction. KATALCO 71-7F benefits from a further improvement in intimacy of Cr promoter location, further stabilising Fe3O4 active species within the catalyst. KATALCO 71-7F has a similarly robust porous structure to KATALCO 71-6F within catalyst pellets. KATALCO 71-7F maintains the enhanced catalyst shape developed for KATALCO 71-5F and KATALCO 71-6F previously, with improved geometric surface area: volume ratio of the catalyst pellets, which have been shown to have beneficial impact on HTS reactor pressure drop with catalyst ageing.
Johnson Matthey have investigated the strength of HTS catalysts KATALCO 71-5F, KATALCO 71-6F and KATALCO 71-7F and the results are shown in Fig. 2. Strength was measured before and after representative thermal ageing of the three catalysts – what might be considered as ‘regular’ durability for HTS catalysts. These results show that both KATALCO 71-6F and KATALCO 71-7F maintain catalyst strength after thermal cycling of the catalysts during ageing. KATALCO 71-6F and KATALCO 71-7F are stronger after thermal cycling than KATALCO 71-5F. Whilst KATALCO 71-5F suffers a significant change in strength during ageing, KATALCO 71-5F retains sufficient strength to perform well in numerous commercial settings.
Following the good strength result seen for KATALCO 71-7F compared to KATALCO 71-6F, both catalysts were tested for strength following ‘steaming’ ageing. This ageing is designed to represent more demanding duty cycles for HTS catalysts, in which the catalysts are exposed to steam during reactor start-up. In Fig. 3, both catalysts show good strength results after ‘steaming’ ageing. KATALCO 71-7F shows slightly higher strength after ‘steaming’ ageing than KATALCO 71-6F, also showing slightly higher strength than the test result for thermally aged catalysts.
Investigation of long-term durability was assessed using accelerated ageing conditions. KATALCO 71-5F, KATALCO 71-6F and KATALCO 71-7F were tested before and then after each subsequent ageing cycle; the results are shown in Fig. 4. These results show KATALCO 71-7F retains the highest performance following multiple aging cycles. Furthermore, these results show KATALCO 71-7F is an improved catalyst compared to both KATALCO 71-5F and at least equivalent to, if not better than, KATALCO 71-6F. Combining the performance results with the strength results shows KATALCO 71-7F matches and even exceeds the excellent performance of KATALCO 71-6F.
The strength and pressure drop advantages of KATALCO 71-7F, particularly after lifetime ageing, will enable large-scale ammonia plants to incrementally increase ammonia production. Johnson Matthey has developed a model to estimate the potential benefits for ammonia manufacturers. The absolute benefit of lower pressure drop in operation will depend on the cost of natural gas and the ammonia sales price. For a 3,300 t/d plant, with the following assumptions:
- Front end pressure drop: 18.6 bar
- On-stream factor of plant: 90%
- Gas usage: 35 million Btu/tonne of ammonia produced
- Other variable costs: $20/tonne of ammonia produced
- Shutdown time: 7 days per year
- Catalyst life: 4 years
Johnson Matthey calculates a pressure drop benefit of 0.10 bar, resulting in 8.9 t/d extra ammonia production. Table 1 shows the extra sales of ammonia enabled by durable HTS performance from the lower pressure drop within the HTS reactor.
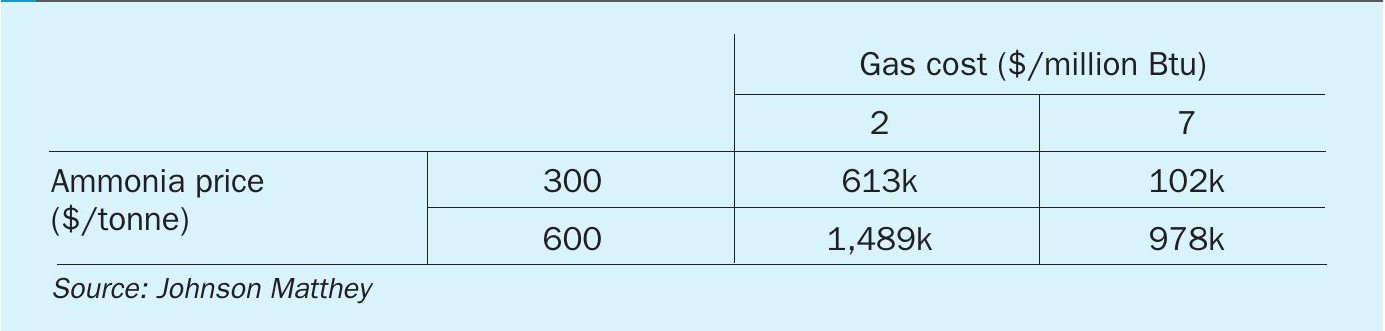
On top of the expected benefit from low-cost gas feed, and higher product sales price, lower pressure drop enabled by strong HTS catalysts with advanced shape design offers significant value to ammonia producers, up to $1.5m extra sales of ammonia annually.
Considering the KATALCO 71-series catalysts, Johnson Matthey predicts that for the most demanding duties, in which the HTS catalyst must be robust to severe and/ or frequent deactivating events (such as wetting or thermal stress events), KATALCO 71-7F will offer ammonia manufacturers the most durable performance over the catalyst lifetime. KATALCO 71-6F has previously shown excellent durability and performance in such plants. The results described above are summarised in Table 2. Table 2 shows that for more demanding duties, KATALCO 71-6F and KATALCO 71-7F offer ammonia manufacturers a benefit in strength and pressure drop performance compared to KATALCO 71-5F. Johnson Matthey’s test results suggest that the extra strength of KATALCO 71-7F will push the durability of this catalyst beyond the excellent performance delivered by KATALCO 71-6F. For plants with a lower frequency of events which damage the catalyst, or events which have less serious deactivating effect on the catalyst, each of KATALCO 71-5F, KATALCO 71-6F and KATALCO 71-7F may be used successfully by ammonia manufacturers – which is shown in Table 2 on the ‘regular’ duty line of the table.
Conclusion
Johnson Matthey has developed the KATALCO 71 series ‘F’ catalyst shape for HTS catalysts which benefits customers through lower lifetime pressure drop, as the nature of the ‘F’ shape increases voidage in the catalyst bed thereby reducing pressure drop, this offers the potential for increased throughput or efficiency increasing plant profitability.
KATALCO 71-7F has shown an unrivalled combination of strength and performance in testing, outperforming previous generation catalysts under conditions representative of HTS reactors.
Reference