Nitrogen+Syngas 389 May-Jun 2024
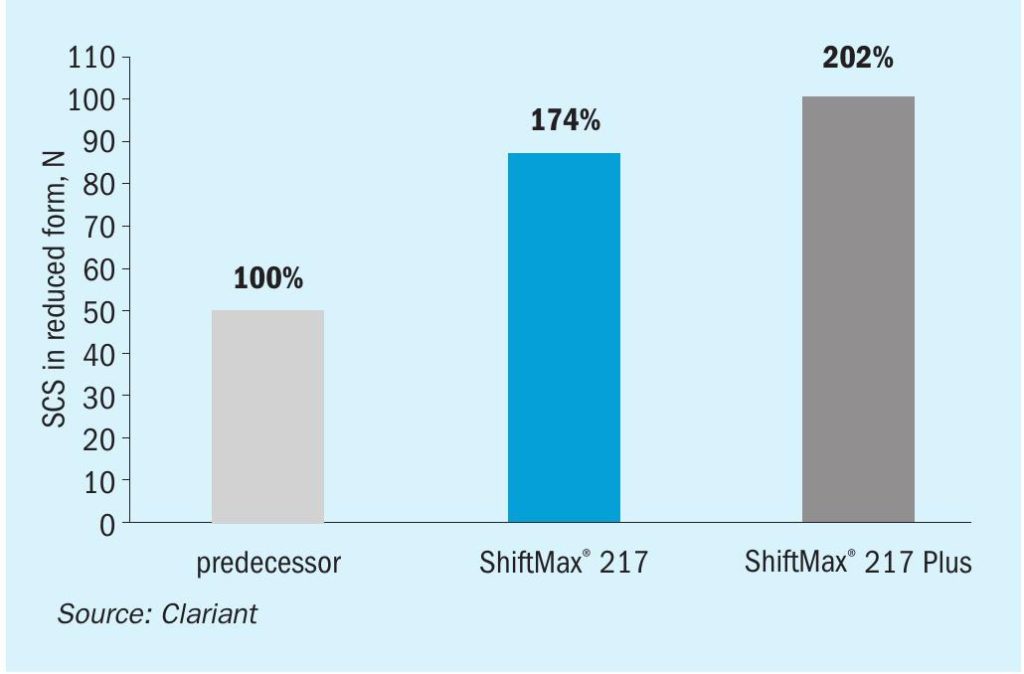
31 May 2024
A new low methanol shift catalyst
LTS SHIFT CATALYST
A new low methanol shift catalyst
Anton Kariagin and Stefan Gebert of Clariant discuss the benefits and commercial performance of the new low temperature shift (LTS) catalyst – ShiftMax 217 Plus. A case study demonstrates the benefits of this catalyst, providing ultra-low methanol formation resulting in increased ammonia production and/or energy savings.
Clariant is known for its commitment to innovation, and always puts the interests and needs of its customers as the target for continuous product development. High levels of investment in R&D are maintained every year to enhance existing products and develop new ones.
Ammonia production is one of the most complex processes in the chemical industry and also one of the most studied. There are hundreds of patents and developments in this process, and one might think that there are no more opportunities for further development. In recent years, however, Clariant has launched a new “Plus” catalyst series for ammonia production: ReforMax 210/330 LDP Plus for the primary and secondary reformers, ShiftMax 217 Plus for the low temperature shift and AmoMax 10 Plus for the ammonia synthesis section.
Clariant LTS catalyst
The copper/zinc-based LTS catalyst has a significant impact on the energy efficiency of the plant and consequently on its economics. Therefore, it is extremely important to have a highly active, stable and robust catalyst that ensures long life and high performance and to a certain extent can withstand various upsets during its lifetime, such as sulphur and chloride poisoning, condensation or high temperatures.
In an ammonia plant, a more active LTS catalyst decreases the inert concentration in the ammonia synthesis loop over a longer period of time, reducing purge gas losses and increasing the energy efficiency of ammonia production. As a rule of thumb, 0.1% more CO converted in the LTS means approximately 1% additional ammonia, especially in plants without purge gas recovery units.
Clariant already has one of the best LTS catalysts on the market – ShiftMax 217, which provides excellent crush strength in both the oxide and reduced states for increased robustness, as well as enhanced activity and selectivity for higher conversion at low temperatures and low methanol byproduct formation. Since its introduction in 2010, ShiftMax 217 has been used by more than 60 customers worldwide.
New LTS catalyst ShiftMax 217 Plus
With the recent trend to develop decarbonised ammonia as a transport medium for hydrogen, ammonia producers and licensors tend to harshen the operating conditions of new and existing ammonia plants, making the physical strength and thermal stability of the LTS catalyst more and more important. Additionally, the flow scheme of “blue” ammonia production is often based on a low steam-to-gas ratio concept for higher energy efficiency, resulting in higher methanol by-product formation.
With these existing and future customer needs in mind, Clariant has not stopped with the highly active and robust ShiftMax 217 but has developed ShiftMax 217 Plus, the next-generation LTS catalyst for ultra-low methanol formation and outstanding physical strength while keeping the same high activity of the well-proven ShiftMax 217. By introducing an optimised production process, ShiftMax 217 Plus exhibits a more homogeneous distribution of active metals and promoters within the catalyst matrix, resulting in enhanced catalyst selectivity and, consequently, lower formation of by-products such as methanol.
Lower by-product methanol formation
According to the reaction equation, by-product methanol formation consumes hydrogen, leading to hydrogen yield losses and/or lower energy efficiency and technological and environmental challenges such as VOC and COD emissions.
CO2 + 3H2 = CH3OH + H2 O + heat
Excessive methanol make will not only contaminate CO2 and process condensate but will also cause loss of ammonia production. As a rule of thumb, for every one tonne of methanol produced in the LTS reactor, 1.1 tonnes of ammonia are lost. Methanol formation is controlled by gas composition, operating conditions (similar to those required for industrial methanol synthesis), and catalyst type. Therefore, the methanol formation rate can be reduced by increasing the steam-to-gas ratio and/or using low-methanol catalysts.
In laboratory tests, ShiftMax 217 Plus demonstrated ultra-low methanol formation without compromising activity. Compared to the commercially proven version ShiftMax 217, the new catalyst provided the same high level of CO conversion but formed 40% less methanol, and provided increased mechanical strength, as shown in Figs 1 to 3.
The ultra-low byproduct methanol formation provides several benefits:
- increased ammonia production and/or energy savings;
- cost savings in the downstream treatment system, e.g., condensate system, solvent regeneration, etc.;
- helps to reduce VOC/COD emissions;
- mitigates capacity limitation due to VOC/COD emissions.
The following case study demonstrates the outstanding reduction of by-product methanol formation that helped the ammonia producer solve its issues with regulatory limits for VOC emissions.
Case study: 50% lower methanol in CO2 off gas
An ammonia producer in Europe has very strict regulatory limits for VOC emissions, which could result in a high penalty if exceeded.
In 2018, the producer installed the previous generation of Clariant’s “low methanol” catalyst ShiftMax 217, which greatly helped to decrease methanol formation and meet the regulatory limits. However, during the start-of-run period, the average methanol formation was still higher than the limits due to the high activity of ShiftMax 217.
It is well known that even with the “low methanol” type of catalyst the highest amount of methanol is formed at the beginning of the run because the activity of the fresh catalyst is high for both reactions during this period of the catalyst life: the targeted shift reaction and the by-product methanol synthesis reaction.
As a result, this ammonia producer still had issues with exceeding the regulatory limits in the start-of-run period after installation of the fresh “low-methanol” catalyst ShiftMax 217.
For the next charge in 2022, Clariant offered the new generation catalyst, ShiftMax 217 Plus, to solve the problem with methanol during the start-of-run period.
At the same time, due to high energy prices, the plant was looking for any opportunity to improve plant economics by increasing ammonia production while decreasing energy consumption, which can be achieved by increasing hydrogen production. Thus, the ability to avoid hydrogen losses by reducing methanol formation was another reason why the ammonia producer selected the ShiftMax 217 Plus catalyst for its LTS reactor.
Conclusion
The case story above shows that by understanding the needs of its customers, Clariant was able to launch a new generation of “ultra-low methanol” catalyst ShiftMax 217 Plus, that addresses the following needs:
- energy savings or increased ammonia production, which has a direct impact on the profitability of a plant;
- increased catalyst reliability and longevity;
- improved sustainability to meet new emission regulations for VOC and COD.